
6 minute read
Iscar – Machining at high RPM
from AMT JUN/JUL 2021
by AMTIL
High-speed machining (HSM) has not only led to a significant difference between machine tools, but it has also brought a greater awareness with regard to the high-speed spindle, which is perhaps the most important and central component of high-speed machine tools and a key factor in the success of HSM.
Operating a spindle with high rotation speed and gaining the optimal balance between the provided speed and torque is the main task of high-speed engineering. The spindle’s performance depends on a variety of different factors. One of the main factors relates to the design concept of a single- or combined twin-motor bearing system, seal components, and a tool retention method. When machining, the spindle is not in direct contact with the workpiece but interacts with it through another technological system – the cutting tool. This connection acts as a conductor and should transform the impressive capabilities of a high-speed spindle into improved machining results. Another element between the cutting tool and the spindle is the toolholder that is fitted into the spindle. A poor performance from this small assembly, consisting of the cutting tool and toolholder, may reduce the function of the spindle to zero. Therefore, HSM toughens the accuracy, reliability, and safety requirements for the assembly of the spindle extension. High-speed rotation generates centrifugal forces. In HSM, when compared with traditional machining methods, these forces grow exponentially and turn into a significant load on a cutting tool, which in turn determines the tool’s durability. In indexable milling, high centrifugal forces may cause insert clamping screws to break, inserts to loosen and a cutter body to fail. Formed fragments can not only damage a machine and a machined part but can also be very dangerous to the operator. In such conditions, cutting tool manufacturers are compelled to consider the design and technological means necessary to ensure appropriate reliability of their products. Hence, the focus on indexable milling cutters should include consideration of secure insert mounting and a robust body structure. Let us start with a clamping screw, the smallest and weakest element of an overall technological system, and one that may have a great impact on the system’s reliability. The same can be said about the clamping screw in relation to a highspeed indexable milling cutter. Applying dynamometric keys controls the tightening of the clamping screw (see Figure 1). However, ensuring the torque is tightened sufficiently is not enough to reliably operate the cutter. Intelligent design is directed to minimise the dynamic load on the clamping screw.
Figure 1 – Modular fixed torque keys provide effective options for reliable securing of indexable milling inserts.
Iscar’s HSM90S FAL-22 milling cutters are intended for efficient milling of aluminium at high-speed rates. They carry large-size inserts that enable a depth of cut of up to 22mm. The cutter insert pocket has a protruding ridge on the seat bottom surface, and the lower face of the insert has a matching groove which fits into a ridge when assembled (see Figure 2). This eliminates insert radial displacement due to strong centrifugal forces at high-speed milling, and improves the load distribution on the insert clamping screw. The cutter design facilitates reliable milling in a rotational speed range of up to 31,000 revolutions per minute. To reduce centrifugal forces, a cutter body should be axially symmetric and highly balanced. There are international and national standards and norms that specify tool balancing grades. When designing indexable milling tools intended for HSM, it is very important to ensure the mass distribution of the body is symmetrical with the body axis. As this theoretical balance relates to a virtual object, it cannot replace the physical balancing of a real body if needed but can substantially diminish the mass unbalance of a future product, making the “physical” balance much easier. It is known that the ambition of a tool design engineer is to make an indexable cutter body, and in particular, an insert pocket surface, as hard as possible in order to increase wear resistance. However, the higher the hardness, the faster the body of a rapidly rotating tool can break down. Hence, finding an optimal equilibrium between strength and wear is another important task in searching for effective HSM tool solutions. Solid tools feature higher accuracy and better axial symmetry when compared with indexable cutters. Typically, solid tools are less in diameter and naturally require higher revolutions per minute even for the same cutting speed. This explains why the majority of HSM tools are solid. Normally, such tools are made from coated cemented carbides, though in recent times cutting ceramics as a tool material has become popular for highspeed machining of high-temperature superalloys. Nevertheless, selecting a solid tool, especially milling cutters for HSM, may be difficult. Normally, the overhang-to-diameter ratio for solid carbide endmills is greater when compared with indexable tools. Such a feature, in combination with a flute shape that weakens a tool cross-section, demands specific attention to the vibration strength of a solid carbide endmill. To improve chatter stability, tool engineers often make a tooth angular pitch unequal, and a flute helix variable. This violates the principle of axial symmetry and may give a reverse result. Therefore, an optimal, intelligent design for solid carbide endmills requires engineer ingenuity and appropriate compromising (see Figure 3). Having highly engineered a balanced vibration-proof tool is half the battle. We have already mentioned the toolholder that is mounted on a high-speed spindle. So, what’s the use of an ideal tool if a far more massive toolholder is not suitable for HSM? In HSM, the dynamic characteristics of the tool cannot be separated from a toolholder. For example, balancing the tool should
Figure 2 – A rugged design of 90-degree indexable milling cutter ensures efficient milling aircraft components from aluminium at high-speed rates. The required tightening torque for an insert clamping screw and maximum revolutions per minute are necessary marking details.
be done in assembly with the toolholder – this is a single way to fulfil requirements of accuracy, reliability, and safety. Modern CAD/CAM systems ensure estimating the dynamic behavior of various products based on their 3D models. Providing such models for cutting tools, toolholders and various accessories is a typical feature of today’s serious tool manufacturer. In fact, we are proud to acknowledge that in recent years Iscar has significantly expanded the digital twin assembly options available in its e-catalogue. To conclude, high-speed machining has influenced the need for specific requirements of a cutting tool and toolholder. By meeting these demands, HSM has become a trusted highly engineered, highspeed spindle operation with maximum efficiency. www.iscar.com.au
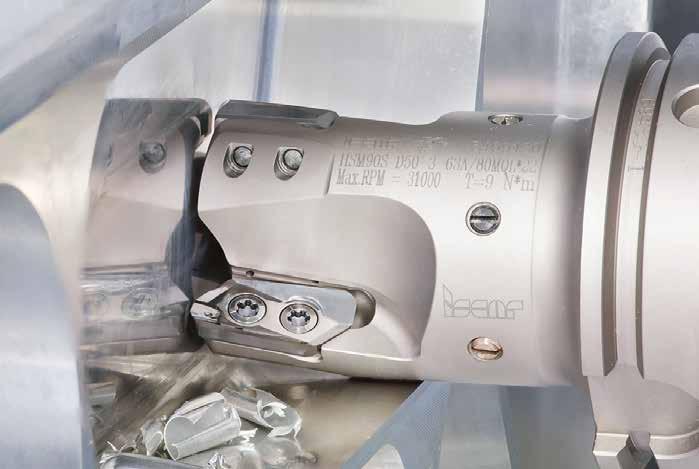
Figure 3 – Iscar’s seven-flute solid carbide endmill, intended for HSM, features different helix angles, variable pitch, and chip-splitting grooves on the cutting edges.

AMTIL DIGITAL BANNERS
60,000 ONLINE AD IMPRESSIONS 7,000 VISITORS
Figures quoted are average monthly statistics. Package dependent
25,000 PAGE VIEWS Call Anne Samuelsson for your FREE 2020 AMTIL Digital Media Kit on 0400 115 525 or email asamuelsson@amtil.com.au
1510AMTIL/V3
Keeping me up to date with our industry
As a member of AMTIL since its inception in 1999, M.T.I. Qualos appreciates AMTIL’s efforts in keeping the Australian manufacturing industry informed via AMT Magazine. This includes international news, the high levels of achievement of Australian manufacturers and initiatives to support our precision engineering sector. As a supplier of Precision Measuring Instruments, M.T.I. Qualos sees AMT magazine as an extremely valuable tool in reaching the key decision-makers. There isn’t a better or simpler way of reaching our target market.
Andrew Smith, General Manager M.T.I. QUALOS
APPROX 31,500
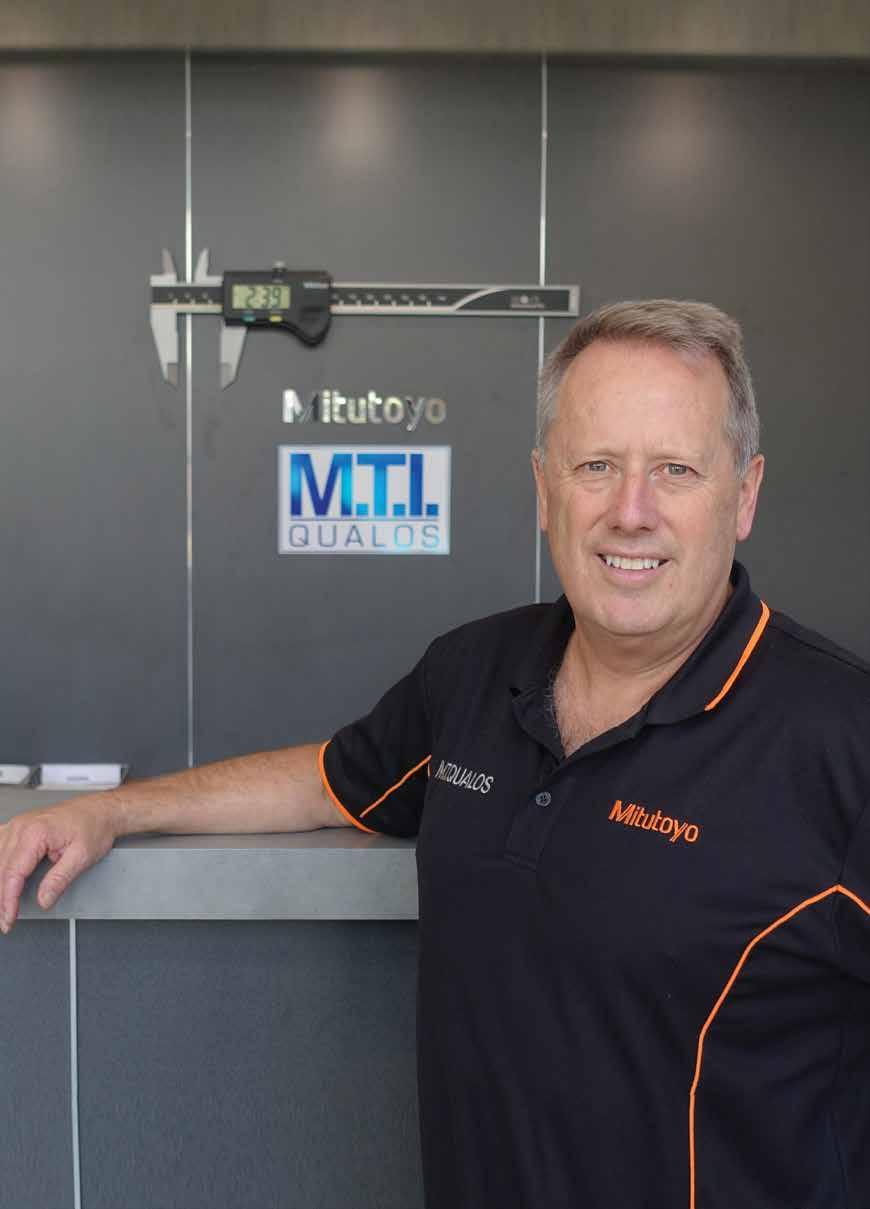