
28 minute read
VOICEBOX Opinions from across the manufacturing industry
from AMT AUG/SEPT 2021
by AMTIL
How Australia is unlocking the industries of the future
While Australian software darlings Atlassian, Culture Amp and Canva continue to capture headlines, there remains a common misconception that Australia shies away from hardware startups and advanced manufacturing. This couldn’t be further from the truth, writes Mike Zimmerman.
At present, exports from engineering enabled industries (excluding mining) total $92bn or 29% of total exports in Australia; we have five academic institutions ranked in the top 50 in the world for engineering and technology; and 2.61 million Australians work in engineering and engineering-enabled industries — around 22% of the job market. From LiDAR to robotics and satellite technology, Australia has a multitude of companies operating on a global scale and exporting our hardware innovations to the world. The Australian advantage
As we continue to manage the challenges of the pandemic, Australia has the opportunity to leverage existing strengths to enable the growth of world-leading engineering-enabled solutions, both for domestic and international markets. Historically, Australia has maintained a global reputation for strength in heavy industries including mining, construction, infrastructure and agriculture. Arguably, our energy and resource sectors have been major drivers of the economy for 30 years, and despite the effects of COVID-19, we have maintained our reputation as a consistent supplier of both. For instance, in the 2018-19 financial year, twothirds of Australia’s energy production was exported. Something perhaps less well known is the strength of Australian research institutions and universities across data-driven fields including artificial intelligence (AI), LiDAR, field robotics, and the Internet of Things (IoT). These fields present a huge opportunity for us to combine strengths and create the solutions that the world needs, especially today. These solutions fall into three broad categories: 1. Improved welfare of workers and consumers: Safer operations, improved training, tracking, and traceability. 2. Efficiency gains: Automation, speed and scale, better forecasting and supply management, and reduced waste. 3. Growth opportunities: Improved yields, new insights and services, trusted premium goods. A number of companies from our Main Sequence portfolio are already working with industry and leveraging world-leading IP to drive impact here and around the world. Not your typical LiDAR company, Baraja is building the future of autonomous vehicles by revolutionising the scanning technology that helps self-driving cars and other vehicles navigate their environment. The company has its own approach to LiDAR, Spectrum-Scan, that builds upon proven photonics and optical technologies from the telecommunications industry to completely rethink environment scanning for autonomous vehicles. Essentially, this approach sets a new benchmark in precision and reliability for autonomous mobility, creating precise images of the world through high-resolution point clouds at 200+ metres range, built to withstand real-world conditions in cars, heavy vehicles and more. Working to disrupt the IoT space, Myriota provides low-cost, low-power satellite connectivity for IoT sensors across industries including agriculture, mining, defence, logistics and management of vehicles. The company currently has seven mini-satellites in orbit — one of which was launched by SpaceX. Also a part of the portfolio, Advanced Navigation is building ultraprecise, AI-based navigational technologies and robotics used by multinational companies including NASA, Boeing, and Tesla. Emesent is a world leader in drone autonomy who’s flagship product, Hovermap, combines advanced collision avoidance and autonomous flight technologies to map hazardous and GPS-denied environments. While a small group of companies are already changing the way we operate our industries, we need to ensure that we are properly leveraging Australia’s inherent strengths by creating more of these companies to ensure we stay at the forefront of global problem solving. Building the next generation of industry pioneers
Building these companies “takes a village”. These are not mobile applications that a decent coder and a social marketing expert can develop over a weekend and turn into the next TikTok. These are solutions that have tangible value in our physical world and demand collaboration across industry sectors to build. To accelerate solutions there are four key ingredients needed, with each element chosen with precision to maximise the chance of success. The first is the research. Every problem you want to solve has at least the seed of a solution and it is happening right now in the research labs of the world. Research capability is needed to bring advanced systems and data science platforms to life, as well as to provide access to IP and the equipment and expertise to build trusted prototypes. The second piece of the pie is industry. Industry expertise bringing needs, trials and validation, and the business case to buy more. This is a company’s secret sauce to getting to market, fast. You need to understand customers and supply chains and be able to deliver the new solution straight to them. Thirdly (and arguably most importantly), you have the CEO, who brings the vision, passion and resilience necessary for the startup journey to commercialise that IP and bring value to the market. When it comes to finding the best executive leader, the election criteria includes a confidence around uncertainty, some advantage in the industry that this company will rise and the ability to synthesise thousands of idea streams into a path with momentum. And finally, you have the injection of capital. So — how do you pair all these ingredients for the perfect recipe? This is where the venture science model rears its head. Instead of hearing pitches from founders with an idea, venture science begins by identifying a challenge and global opportunity before assembling the science capability to address it, introducing a pathway to market, and injecting capital to create a brand new company. It’s this model that recently gave life to clean energy storage startup Endua and satellite space startup Quasar. At Main Sequence, we see ourselves playing a critical role in building more of these pioneering companies, functioning as a matchmaker between problem and opportunity. With deep experience in startup creation, helping set major company milestones, applying pattern recognition to mitigate risk, and of course risk capital. Now is the time to call the village. Together we can build more companies that harness the forces of entrepreneurship and science to deliver solutions at scale to the planet.
Mike Zimmerman is a Partner at Main Sequence. www.mseq.vc
New materials revolution makes more of waste
The Industrial Revolution brought enduring benefits to humanity, notwithstanding the social and environmental costs. More recently, the information revolution resulted in an explosion of digital tools and new technologies and businesses. Now, writes Professor Veena Sahajwalla, we are on the cusp of a new epoch: the materials revolution.
Community, government and international concerns around our waste and recycling challenges are converging, with a growing willingness across societies to embrace the issues we face. The materials revolution values the sustainability of all the materials we use from our planet, which are essentially finite in supply. Fast fashion and consumption have outpaced society’s ability to effectively deal with the consequences of a throw-away mentality, such as overflowing landfills, waste stockpile fires, and pollution of our waterways and atmosphere. A growing understanding about materials sustainability is juxtaposed against a consumption mentality for convenience and cheaper materials and products. We need to rethink our attitudes to the resources we rely on for our societies to function, and rethink our approaches to waste. The fact is that waste is, and should be treated as, a renewable resource. We need to add ‘reform’ as a fourth R to the three Rs of reducing, re-using and recycling unwanted products and materials, which we erroneously call waste. New technologies are emerging to demonstrate we can reform waste into new materials and products in ways traditional recycling does not. This is not so say that traditional recycling methods and processes are unwanted – they play a vital role in managing our waste. But what we need are new ways of recycling mixed and complex waste items like electronic waste (e-waste), to extract and reform the valuable materials they contain, like rare earths and metals. New government policies include rare earths as a national priority but we could introduce as part of that priority a requirement to harness more sustainably the material resources contained in e-waste. This reforming of many waste types will be a crucial step in the journey to create circular economies, where we keep materials in use for as long as possible. Another key step is that we need to start designing products and systems differently so that materials that are no longer wanted can more easily circulate back into manufacturing. This is why I see a strong alignment of recycling and manufacturing occurring in the near future. There are sobering reasons to get on with the job. The Government’s newly released National Waste Report 2020 shows our national waste increased to 74m tonnes a year. Of that, about 60% is estimated to be recycled, but Australia’s new waste export bans coming into effect from this year are expected to reduce the rate of recycling. This is below the national resource recovery target of 80% by 2030, set in the 2019 National Waste Policy Action Plan. Not being able to send a lot of our waste overseas adds another urgent reason to embark on the materials revolution with new technologies. Infrastructure Australia’s (IA) recent Priority List Report found that constraints on collection and processing, including product design and lack of sufficient demand, have led to recyclable waste ending up in landfill. The report lists as its highest priority the need for the nation to retool itself with waste and recycling infrastructure. It says current constraints include lack of space for transfer facilities, the inability of material recovery facilities to process co-mingled, highly contaminated waste (particularly in remote and regional Australia), and under-developed domestic reuse markets due to over-reliance on the export of waste. IA finds Australia must recycle an additional 650,000 tonnes of waste plastic, paper, glass and tyres onshore by 2024, putting further pressure on waste recovery and processing infrastructure. Limited landfill capacity and sorting facilities are increasing logistics costs as waste is transferred greater distances for disposal. I see a huge opportunity to not only address these challenges but also use our innovative smarts to create new technologies, supply chains and jobs. We need a materials revolution where there is a much closer alliance between scientists and engineers doing research & development, and governments, industries and communities that can benefit from new discoveries and technologies to improve sustainability. Recycling in new ways can be a foundation for the manufacture of high-quality materials and products made from waste resources. This new level of self-reliance can enhance sovereign capability in times of pandemic disruption, and lead to improved economic prosperity through the creation of new, and localised, supply chains. Recycling and reforming waste materials for completely new uses – for example isolating hydrogen from tyres or plastics to make green steel – should be at the centre of how we transform our sovereign manufacturing sector. UNSW’s Sustainable Materials Research and Technology (SMaRT) Centre is helping to create the much-needed alignment of recycling and manufacturing by introducing new technologies to business partners, community groups and just about any stakeholder interested. Our newly developed MICROfactorie technologies are increasingly being used outside our laboratories to reform waste into new, value-added materials and products. For instance, our Green Ceramics MICROfactorie module can transform materials such as glass, textiles and plastics not suitable for conventional recycling into new engineered products like floor and wall tiles, tables and other hard surfaces. Another module can reform e-waste plastics into filament as a feedstock resource for 3D printing. Companies like Mirvac are embracing the challenges of being more sustainable and in March featured many of our Green Ceramics in a display apartment at its Pavillions development at Sydney Olympic Park. Mirvac CEO and Managing Director Susan Lloyd-Hurwitz CEO says the “take-make-waste approach is no longer acceptable”. She and her team are working hard to find a better, more sustainable way to provide homes and office buildings that are kinder to the planet. My vision is for decentralised and modernised recycling and manufacturing in Australia. Increased funding from governments in this regard is extremely welcome, and while there is more to do we are making great progress. The second round of the Federal Government’s National Environmental Science Program has stepped squarely into this space, committing to fund for seven years a new Sustainable Communities and Waste Hub, which I will lead with a consortium of research institutions, industry and community partners. Enabling onshore waste processing, more sophisticated recycling, and reforming of ‘waste as a renewable resource’ as part of manufacturing must be central to the new materials revolution and Australia’s ongoing prosperity.
Professor Veena Sahajwalla is the founding Director of the Centre for Sustainable Materials Research and Technology (SMaRT) at the University of New South Wales. www.smart.unsw.edu.au
‘Green steel’ is hailed as the next big thing in Australian industry. Here’s what the hype is all about
While steel is vital to our way of life, production of the metal is a big contributor to global greenhouse emissions. However, new clean steelmaking processes are emerging involving hydrogen rather than coal, and for Australia the potential benefits are huge. By Jessica Allen and Tom Honeyands.
Steel is a major building block of our modern world, used to make everything from cutlery to bridges and wind turbines. But the way it’s made – using coal – is making climate change worse. On average, almost two tonnes of carbon dioxide (CO2) are emitted for every tonne of steel produced. This accounts for about 7% of global greenhouse gas emissions. Cleaning up steel production is clearly key to Earth’s low-carbon future. Fortunately, a new path is emerging. So-called “green steel”, made using hydrogen rather than coal, represents a huge opportunity for Australia. It would boost our exports, help offset inevitable job losses in the fossil fuel industry, and go a long way to tackling climate change. Australia’s abundant and cheap wind and solar resources mean we’re well placed to produce the hydrogen a green steel industry needs. So let’s take a look at how green steel is made, and the challenges ahead. Steeling for change
Steel-making requires stripping oxygen from iron ore to produce pure iron metal. In traditional steel-making, this is done using coal or natural gas in a process that releases CO2. In green steel production, hydrogen made from renewable energy replaces fossil fuels. Australia exports almost 900m tonnes of iron ore each year, but only makes 5.5m tonnes of steel. This means we have great capacity to ramp up steel production. A Grattan Institute report last year found if Australia captured about 6.5% of the global steel market, this could generate about $65bn in annual export revenue and create 25,000 manufacturing jobs in Queensland and New South Wales. Steel-making is a complex process and is primarily achieved via one of three processes. Each of them, in theory, can be adapted to produce green steel. We examine each process below. 1. Blast furnace
Globally, about 70% of steel is produced using the blast furnace method. As part of this process, processed coal (also known as coke) is used in the main body of the furnace. It acts as a physical support structure for materials entering and leaving the furnace, among other functions. It’s also partially burnt at the bottom of the furnace to both produce heat and make carbon monoxide, which strips oxygen from iron ore leaving metallic iron. This coal-driven process leads to CO2 emissions. It’s feasible to replace a portion of the carbon monoxide with hydrogen. The hydrogen can strip oxygen away from the ore, generating water instead of CO2. This requires renewable electricity to produce green hydrogen. And hydrogen cannot replace carbon monoxide at a ratio of 1:1. If hydrogen is used, the blast furnace needs more externally added heat to keep the temperature high, compared with the coal method. More importantly, solid coal in the main body of the furnace cannot be replaced with hydrogen. Some alternatives have been developed, involving biomass – a fuel developed from living organisms – blended with coal. But sourcing biomass sustainably and at scale would be a challenge. And this process would still likely create some fossil fuel-derived emissions. So to ensure the process is “green”, these emissions would have to be captured and stored – a technology which is currently expensive and unproven at scale. 2. Recycled steel
Around 30% of the world’s steel is made from recycled steel. Steel has one of the highest recycling rates of any material. Steel recycling is mainly done in arc furnaces, driven by electricity. Each tonne of steel produced using this method produces about 0.4 tonnes of CO2 – mostly due to emissions produced by burning fossil fuels for electricity generation. If the electricity was produced from renewable sources, the CO2 output would be greatly reduced. But steel cannot continuously be recycled. After a while, unwanted elements such as copper, nickel and tin begin to accumulate in the steel, reducing its quality. Also, steel has a long lifetime and low turnover rate. This means recycled steel cannot meet all steel demand, and some new steel must be produced. 3. Direct reduced iron
“Direct reduced iron” (DRI) technology often uses methane gas to produce hydrogen and carbon monoxide, which are then used to turn iron ore into iron. This method still creates CO2 emissions, and requires more electricity than the blast furnace method. However its overall emission intensity can be substantially lower. The method currently accounts for less than 5% of production, and offers the greatest opportunity for using green hydrogen. Up to 70% of the hydrogen derived from methane could be replaced with green hydrogen without having to modify the production process too much. However work on using 100% green hydrogen in this method is ongoing. Becoming a green steel superpower
The green steel transition won’t happen overnight and significant challenges remain. Cheap, large-scale green hydrogen and renewable electricity will be required. And even if green hydrogen is used, to achieve net-zero emissions the blast furnace method will still require carbon-capture and storage technologies – and so too will DRI, for the time being. Private sector investment is needed to create a global-scale export industry. Australian governments also have a big role to play, in building skills and capability, helping workers retrain, funding research and co-ordinating land-use planning. Revolutionising Australia’s steel industry is a daunting task. But if we play our cards right, Australia can be a major player in the green manufacturing revolution.
Jessica Allen is a Senior Lecturer and DECRA Fellow at the University of Newcastle. Tom Honeyands is the Director of the Centre for Ironmaking Materials Research, University of Newcastle. This article was originally published by The Conversation. www.theconversation.com www.newcastle.edu.au
Industry 4.0 is here and manufacturing stands at its centre. Using transformative technologies that now connect the physical world with the digital world, manufacturers can offer highly customised products to enhance the customer experience. By Matthew Weake.
New forms of human-machine interaction, as well as advances in artificially intelligence (AI) technologies, give manufacturers better connectivity between their customers and supply chains, as well as more flexibility to produce differentiated products to meet consumer demand. However, the amount of technological advancement that once occurred over a number of years is now happening in a fraction of that time. As technologies continue to accelerate and disrupt, the great differentiator won’t simply be a matter of quality or cost but how quickly one company can innovate over another. According to Austrade, over the next 20 years Australia’s manufacturing industry will evolve into a highly integrated, collaborative and export-focused ecosystem that provides highvalue customised solutions within global value chains. The sector will focus on pre-production (design, research and development) and post-production (after-sales services) value-adding, sustainable manufacturing and low-volume, high-margin customised manufacturing. To enable this vision, Australia’s manufacturing sector will increasingly rely on sensors and data analytics, AI technology, 3D printing, and virtual reality solutions. CADPRO Systems has identified five key technology trends for Australian manufacturers that will emerge over the next five years. Generative design
Generative design is software technology that lets manufacturers create highly optimised designs to meet pre-determined goals and constraints. Using shape synthesis algorithms and multi-physics performance analysis in the cloud, the software automatically generates thousands of design options from a single idea. This has huge potential for the Australian manufacturing sector, where one single idea can result in literally thousands of iterations in product design and capabilities. It can also lead to spin-off products that allow manufacturers to enter new markets. Additive manufacturing
Commonly known as 3D printing, additive manufacturing directly connects the digital world with the physical world by developing physical objects through depositing materials in layers based on a digital model. This technology is used to create literally anything from prototypes to produced products including engine parts, ecofriendly buildings, and medical implants. Additive manufacturing can incorporate new materials and integration that supports product innovation while reducing manufacturing cost and waste. It allows for much greater customisation of products, which meets the growing need for personalised, just-in-time manufacturing. Internet of Things
The Internet of Things (IoT) continues to be a top manufacturing trend due to its ability to seamlessly connect electronics, software and sensors to support communication between devices. This enables smart services that use real-time data gathered from internet-enabled devices on production facilities, transport fleets, networks, grids and more to provide specific services for design, production and delivery. Through IoT, advanced manufacturing software connects devices, gathers relevant data, and sends it to a centralised management console where business intelligence software converts the information into insights to drive better decision-making, or automatically updates manufacturing processes based on pre-defined rules. This helps to automate production and quickly overcome issues such as labour shortages. Robotics and automation
The use of robotics and process automation, powered by AI technologies that have machine learning capabilities, is becoming key to manufacturing operations. AI and robotic automation is perhaps the biggest economic opportunity that Australia has over the next 30 years. It is by far the largest source of productivity growth and could potentially add up to $2.2 trillion in value to the Australian economy by 2030. Due to the cost savings and efficiency gains from robotics and process automation, the manufacturing industry could achieve significant benefits from this technology. For example, automated workflows reduce human errors caused by repetitive tasks, which supports the efficient production of high-quality finished products, even for small-batch manufacturing. This allows manufacturers to deliver consistent, positive customer experiences. Data analytics software
Data has become core to doing business for all industries across Australia, including manufacturing. For example, data allows businesses to accurately measure what customers want and determine how customer demand will evolve over time. Advanced manufacturing software helps manufacturers seamlessly link data insights, processes and resources to meet customer needs. This improves plant efficiency, enhances the customer experience, and reduces manufacturing costs. Australian manufacturers have realised that customer experience now defines their industry, and they must take up the challenge of meeting increasing demand for high-quality, more personalised products on much tighter production schedules than have been experienced in the past. This involves the adoption of intelligent, automated technologies that make the business of modern manufacturing much easier, while delivering a consistent and enhanced customer experience.
Matthew Weake is a Senior Manager - Manufacturing at CADPRO Systems Australia. www.cadprosystems.com.au
BOQ FOREIGN EXCHANGE AND TRADE FINANCE
BUILT TO SUPPORT AUSTRALIAN BUSINESSES
Talk to one of our specialists today on 1800 343 939 or email financial.markets@boq.com.au to find out how we can support your business.
Australia: Grenfell - Never again! Non-combustible cladding
After the 2017 Grenfell Tower blaze tragedy in London which killed 72 people, Dr Kate Nguyen - a Melbourne engineer - teamed up with Envirosip to design lightweight, cost-effective cladding that will not combust. Dr Nguyen thought the way electrical cables are insulated might be part of the answer. “Instead of using a ceramic resin, which was very costly, I thought the plastic insulation around electrical cables that uses tiny ceramic particles could effectively do the same thing”. At high temperatures, the ceramic particles activate and chemically interact, forming an insulation. Subsequent experiments at RMIT led to the invention achieving the Australian combustibility standard AS1530.1:1994 and the international ISO1182:2010 standard. Envirosip is now commercialising the product, which is being further developed for a range of applications. The ceramic-like coating is made from industrial waste.
Engineers Australia
USA: Growing ‘metallic wood’ to new heights
Natural wood is a ubiquitous building material because of its high strength-to-density ratio. For the last three years “metallic wood” has been in development. Its name and useful properties come from its porosity (like wood’s). As a lattice of nanoscale nickel struts, metallic wood is full of regularly spaced cell-sized pores that radically decrease its density without sacrificing strength: it has the strength of titanium at a fraction of the weight and unique optical properties. Engineers have now solved a major problem preventing metallic wood from being manufactured at meaningful sizes: eliminating the inverted cracks that form as the material is grown from millions of nanoscale particles to metal films big enough to build with. Preventing these defects, which have plagued similar materials for decades, allows strips of metallic wood to be assembled in areas 20,000 times greater than previously. The enhanced colour changes also gives it the potential to be used as a sensor.
University of Pennsylvania
This strip of metallic wood is thinner than household aluminium foil but is supporting more than 50 times its own weight without buckling. Queen Maxima of The Netherlands at the opening of the bridge
Italy: First test with a natural gas/ hydrogen blend in steel forging
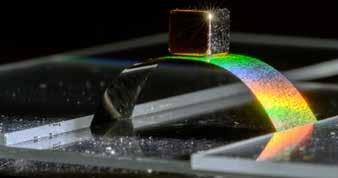
The world’s first test of a 30% natural gas/hydrogen blend in steel forging was successfully carried out by a collaboration in Italy. Used to power furnaces, the trial was successfully carried out after studies and tests lasting a year. Hydrogen is in a position to become the solution for decarbonising steelmaking as well as all hard-to-abate industrial sectors. This trial is a preparatory step to the gradual introduction of zero-emission hydrogen, initially blended with natural gas and then in pure form, in certain steelmaking processes. It is estimated that the permanent use of a 30% green hydrogen blend, fuelled by renewables, on the total gas consumed by the steel forging plants would lead to a reduction in CO2 emissions of 15,000 tonnes per year, equivalent to 7,500 cars.
Power Engineering Intl.
Amsterdam: 3D-printed steel footbridge unveiled
The world’s first 3D-printed steel footbridge has been installed in Amsterdam last month. Created by Dutch company MX3D, the bridge measures 12m in length and contains 4.5 tons of stainless steel forming a curved, flowing structure. The bridge will also be fitted with dozens of sensors – allowing monitoring in real time. Data will be fed into a “digital twin” to imitate its performance and behaviour, helping to inform future novel construction projects involving 3D manufacturing. Printing began in 2017, taking six months. The steel was printed layer by layer in four parts, plus four “corner swirls” that were manually welded together. News of the bridge’s opening follows a week after Knight Architects received approval for what is expected to be one of the busiest pedestrian bridges in London.
Archinect
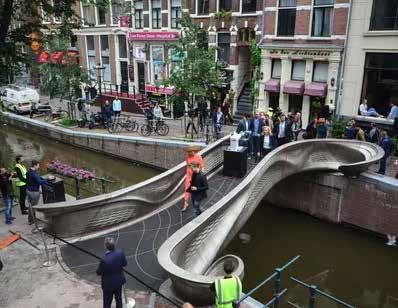
Germany: Safe human-robot collaboration
Range-finders on robots do not function when humans and machines stand close to each other. To increase safety, a webbased design tool – the Cobot Designer – has been developed, allowing companies to design their cobots to increase employee safety. Available as a free web application, users can combine different robots, hazard situations and tools, thus compiling and continuously expanding a catalogue. Ascertaining the robot’s speed to ensure safe collaboration, the tool is intended to replace measurement with a tester: preventing bad purchases and costly measurements (the robot must be programmed and built). The goal is to use computer simulation to dispense with measurements entirely. It is available for free on www.cobotplaner.de to anyone designing an HRC workstation.
Fraunhofer
Germany: Magnetic pulse welding
Aerospace companies face a storage challenge when storing hydrogen because the fuel must be cooled to -253 deg.C. Tanks and pipes accordingly must be absolutely tight. An innovative new welding process has been developed: magnetic pulse welding which demonstrates extremely resilient, metallic mixed joints for cryogenic applications. With this process, the magnetic pressure of a tool coil ensures a high-speed collision and the formation of a solid state joint as well as high stability and leak tightness. Creating tighter joints within just a few microseconds, these joints function reliably both at temperatures down to minus 270 degrees. Overlaps, which provide even more stability, are also created at the joints. The
method is not based on a high heat, but mainly on a high pressure between the joining partners - generating a high pressure on the joining surface and this ultimately welds the two metals together. The great advantage is that it can join combinations of metals that until now have been impossible or difficult to weld together.
Fraunhofer
USA: Robot’s soft touch beats Super Mario
Researchers have 3D-printed a soft robotic hand agile enough to play Nintendo’s classic game “Super Mario Bros” - and win! - demonstrating a promising innovation in “soft robotics” via this open source program. In the past, controlling the fluids that make these soft robots bend and move has been difficult. But now, the ability to 3D-print fully assembled soft robots with “integrated fluidic circuits” in a single step has been developed. Previously, each finger would need its own control line, but now, it can play the game based on just one pressure input (ie applying low pressure caused only the first finger to press the controller to make Mario walk, while a high pressure led to jumping). Guided by a set program that autonomously switched between pressures, the robotic hand was able to complete the first level of Super Mario Bros. in fewer than 90 seconds. Biomedical applications are being explored.
University of Maryland
Generally, plastics are processed at over 100deg.C, but enzymes cannot usually withstand these high temperatures. Researchers have now embedded enzymes in plastics without the enzymes losing their activity - creating enormous potential. To stabilise the enzymes, inorganic, highly porous carriers were used. The enzymes bind to these carriers by embedding in the pores. Although this restricts the enzymes’ mobility, they remain active and are able to withstand much higher temperatures. The stabilized enzymes had to be distributed as quickly as possible in the hot plastic melt - a balancing act which resulted in a process that is suitable for both bioplastics and for the conventional petroleum-based plastics. The carrier and technology remain enzyme-specific because no two enzymes are alike. The first functionalized plastic granulates, films and injection moulding bodies have already been produced.
Fraunhofer
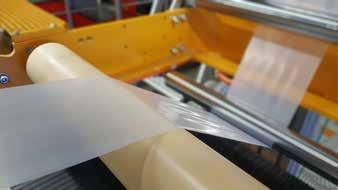
UK: Aircraft engines quiet as a hairdryer
An incredibly light new "meringue-like" material that can reduce aircraft engine noise has been developed. The graphene oxidepolyvinyl alcohol aerogel weighs just 2.1kg per cubic metre, making it the lightest sound insulation ever manufactured. It could be used as insulation within aircraft engines to reduce noise by up to 16 decibels - reducing the 105-decibel roar of a jet engine taking off to a sound closer to that of a hair-dryer. The extremely low-density aerogel was created by using a liquid combination of graphene oxide and a polymer, which are formed with whipped air bubbles and freeze-casted. Although the initial focus is aerospace, it could also be used to create panels in helicopters, or car engines.
University of Bath
USA: The robot smiled back
EVA is a new autonomous robot with a soft and expressive face that matches the expressions of nearby humans. At present, progress is hindered by the fact that each facial expression needs to be programmed. In order to adapt robot behaviour in real time to different situations, robots need to be able to train themselves, as well as make fast decisions and apply the acquired knowledge to diverse and new contexts. Researchers addressed this by designing an animatronic robotic face by developing a vision-based self-supervised learning framework for facial mimicry. While lifelike animatronic robots have been used for years, the team made two advances: EVA uses deep learning AI to “read” and then mirror the expressions on nearby human faces. And EVA’s ability to mimic a wide range of different human expressions is learned by trial and error from watching videos of itself. EVA’s internal neural networks learned to pair muscle motion with the video footage of its own face. The robot blueprints are open-sourced.
Columbia University School of Engineering & Applied Science
“Figuring out a simple way of eliminating inverted cracks has been a long-standing hurdle” James Pikul, Associate Professor at the Universityof Pennsylvania, in relation to “metallic wood” (a lattice of nanoscale nickel struts). An inverted crack is an excess of atoms – in the case of metallic wood – extra nickel fills in the nanopores. These cracks have been a problem since the late 1990s. A technique has been developed which allows for crack-free regions that are 20,000 times larger – with the ability to make previously impossible devices. The new approach allows the manufacture of porous metals that are three times stronger than before, at similar relative density and 1,000 times larger than other nanolattices. The material is already being used as membranes to separate biomaterials in cancer diagnostics, protective coatings and flexible sensors.
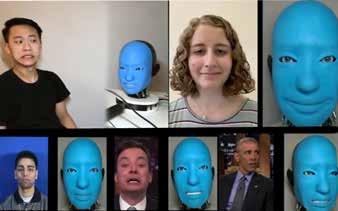