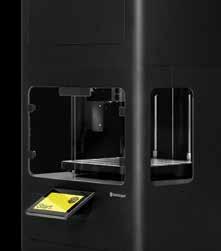
31 minute read
PRODUCT NEWS Selection of new and interesting products
from AMT AUG/SEPT 2021
by AMTIL
Markforged has announced three key additions to its Digital Forge additive manufacturing platform: the Metal X Gen 2, Next Day Metal, and the X7 Field Edition.
The new hardware and software releases are built to help manufacturers reinvent the way they overcome global supply chain challenges by producing parts efficiently and safely at the point of need. Whether on a factory floor or in the most remote areas of the world, these advances are designed to enable manufacturers to recover faster when parts break, operate with less onhand inventory, and minimise equipment downtime. The Metal X Gen 2 builds on the legacy of its predecessor, the original Metal X System released in 2017, by pushing the boundaries of what’s possible in printing complex, industrial-grade metal parts with key hardware developments that improve user experience and increase operator safety to make metal printing even easier. New features such as an external seveninch touchscreen, door position sensors and additional chamber insulation make the Gen 2 even more energy- and time-efficient than before. Markforged has also released Next Day Metal across its entire global fleet of metal printers. This over-the-air software update unlocks print speeds up-to twice as fast as before to produce high-quality, strong metal parts. Wash and dry times – an essential step in metal 3D printing – are now more accurate for smaller parts, shortening the required debind cycle time. These factors, combined with an approximately 17-hour small parts express run on the Sinter-2 post-processing oven, can give manufacturers the parts they need more quickly, and thanks to increased capacity on each printer, it allows them to scale their additive manufacturing operation. Supply chain and manufacturing challenges relying on The Digital Forge are not limited to the factory floor. The X7 Field Edition (X7 FE) allows Markforged technology to be deployed in the most demanding environments in every corner of the world, helping engineers, operators, and service members reinvent the way they tackle global supply chain challenges. The X7 FE is a ruggedised, field-deployable industrial 3D printer for tactical response to inventory challenges in remote locations, as utilised by the US Marine Corps XFAB program. The X7 FE is equipped with a rotomolded high-impact polyethylene Pelican case to protect it during transportation through harsh environments. The case contains all the tools, spare parts, and materials required for maintenance and repair operations in the field. Customers can drop the unit directly into harsh environments like combat zones and exploration sites and be printing in less than two minutes. “Manufacturers are up against many challenges in today’s market – from supply chain challenges like rising supply costs and shipping delay,s to increased pressure from the market to innovate faster and stay ahead of the competition,” said Shai Terem, President and CEO of Markforged. “Since Markforged shipped our first printer, we’ve been committed to quality and continuous improvement, always looking for simpler, smarter, and more robust ways to empower our customers to build anything they can imagine. The addition of the Metal X (Gen 2), Next Day Metal, and the X7 FE to our Digital Forge are important steps towards reinventing manufacturing today so that we are all more resilient tomorrow anywhere in the world.” www.markforged.com
Metalmaster: Welding fume extraction for all materials
Designed for mobile use in manufacturing or fabrication facilities, the European-made Metalmaster S-H13 Mobile Welding Fume Extractor is a compact fume extraction and filtering unit. It provides filtration of fumes from Mig, Tig and Arc welding on all materials that produce intense fumes.
A 3m-long, 160mm-diameter Exo-Joint swivel arm provides high-velocity fume extraction. This unique arm design delivers up to 56% more air flow efficiency with its low drag characteristics when compared to pleated hose arms that require internal support. The Metalmaster S-H13 can process a high volume of 1,300 cubic metres per hour combined with dual stage air filtering capability, featuring a class-leading 23sqm of filter media surface area to prolong the life of the filter and promote quiet operation of less than 69dBA. The extractor’s HEPA H13 filters are compliant with EN ISO 15012 W3 standards and produce fully respirable clear air. The filters are designed for contamination-free filter changing from the clean air side. For larger fume extraction requirements, the Metalmaster D-H13 featuring twin 3m Exo-Joint swivel arms processing 2,600 cubic metres per hour is the right choice. These compact, space saving mobile welding fume solutions are ideal for manufacturing lines, steel fabrication facilities, construction of transport vehicles and anywhere where welding is an integral party of operations.
www.machineryhouse.com.au
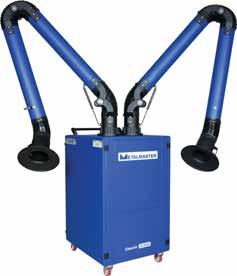
Guhring gets 222 groovy with new parting system
With the arrival of the new 222 System of turning and grooving tools, Guhring has extended its position as a supplier of full-line turning solutions that deliver productivity, efficiency and high performance.
N38 X1.0106 Y.5876 Z-4.5461 A-55.5607 B17.7803 F879.41 N39 X1.1572 Y.5857 Z-4.508 A-55.9513 B16.4387 F893.1 N40 X1.3037 Y.5839 Z-4.4698 A-56.3279 B15.0668 F904.19 N41 X1.4503 Y.5821 Z-4.4316 A-56.6898 B13.6653 F912.54 N42 X1.597 Y.5805 Z-4.3933 A-57.0362 AMT AUG/SEP 2021 03 F879. 41 N39 X1. 1572 Y. 5857 Z 4. 508 A 55. 9513 B16. 4387 F893. 1 N40 X1. 3037 Y. 5839 Z-4. 4698 A-56. 3279 B15.0668 F904.19 N41 X1 .4503 Y .5821 Z-4 .4316 A-56 .6898 B13 .6653 F912 .54 N42 X1 .597 Y .5805 Z-4 .3933 A-57 .0362 B12 .2349 F918.
7803 F879. 41 N39 X1. 1572 Y. 5857 Z 4. 508 A 55. 9513 B16. 4387 F893. 1 N40 X1. 3037 Y. 5839 Z-4. 4698 A-56. 3279 B15.0668 F904.19 N41 X1 .4503 Y .5821 Z-4 .4316 A-56 .6898 B13 .6653 F912 .54 N42 X1 .597 Y .5805 Z-4 .3933 A-57.0362 B12.234 7 B17. 7803 F879. 41 N39 X1. 1572 Y. 5857 Z 4. 508 A 55. 9513 B16. 4387 F893. 1 N40 X1. 3037 Y. 5839 Z-4. 4698 A-56.3279 B15.0668 F904.19 N41 X1 .4503 Y .5821 Z-4 .4316 A-56 .6898 B13 .6653 F912 .54 N42 X1 .597 Y .5805 Z-4 .3933 A-57.0362 607 B17. 7803 F879. 41 N39 X1. 1572 Y. 5857 Z 4. 508 A 55. 9513 B16. 4387 F893. 1 N40 X1. 3037 Y. 5839 Z-4. 4698 A-56.3279 B15.0668 F904.19 N41 X1 .4503 Y .5821 Z-4 .4316 A-56 .6898 B13 .6653 F912 .54 N42 X1 .597 Y.5805 Z-4.3933 A-57. A55. 5607 B17. 7803 F879. 41 N39 X1. 1572 Y. 5857 Z 4. 508 A 55. 9513 B16. 4387 F893. 1 N40 X1. 3037 Y. 5839 Z-4. 4698 A-56.3279 B15.0668 F904.19 N41 X1 .4503 Y .5821 Z-4 .4316 A-56 .6898 B13 .6653 F912 .54 N42 X1.597 Y.5805 Z-4.393 61 A-55. 5607 B17. 7803 F879. 41 N39 X1. 1572 Y. 5857 Z 4. 508 A 55. 9513 B16. 4387 F893. 1 N40 X1. 3037 Y. 5839 Z-4. 4698 A-56.3279 B15.0668 F904.19 N41 X1.4503 Y.5821 Z-4.4316 A-56.6898 B13.6653 F912.54 N42 X1.597 Y.5805 Z-4 Z-4. 5461 A-55. 5607 B17. 7803 F879. 41 N39 X1. 1572 Y. 5857 Z 4. 508 A 55. 9513 B16. 4387 F893. 1 N40 X1. 3037 Y. 5839 Z-4. 4698 A-56.3279 B15.0668 F904.19 N41 X1.4503 Y.5821 Z-4.4316 A-56.6898 B13.6653 F912.54 N42 X1.597 Y.58 6 Y. 5876 Z-4. 5461 A-55. 5607 B17. 7803 F879. 41 N39 X1.1572 Y. 5857 Z 4. 508 A 55. 9513 B16. 4387 F893. 1 N40 X1. 3037 Y. 5839 Z-4. 4698 A-56.3279 B15.0668 F904.19 N41 X1.4503 Y.5821 Z-4.4316 A-56.6898 B13.6653 F912.54 N42 X1.597 N38 X1. 0106 Y. 5876 Z-4. 5461 A-55. 5607 B17. 7803 F879. 41 N39 X1.1572 Y. 5857 Z 4. 508 A 55. 9513 B16. 4387 F893. 1 N40 X1. 3037 Y. 5839 Z-4. 4698 A-56. 3279 B15.0668 F904.19 N41 X1.4503 Y.5821 Z-4.4316 A-56.6898 B13.6653 F912.54 N42 X1.5 N38 X1. 0106 Y. 5876 Z-4. 5461 A-55. 5607 B17. 7803 F879. 41 N39 X1. 1572 Y. 5857 Z4. 508 A55. 9513 B16. 4387 F893. 1 N40 X1. 3037 Y. 5839 Z-4. 4698 A-56. 3279 B15.0668 F904.19 N41 X1.4503 Y.5821 Z-4.4316 A-56.6898 B13.6653 F912.54 N42 N38 X1. 0106 Y. 5876 Z-4. 5461 A-55. 5607 B17. 7803 F879. 41 N39 X1. 1572 Y. 5857 Z-4. 508 A-55. 9513 B16. 4387 F893. 1 N40 X1. 3037 Y. 5839 Z-4. 4698 A-56. 3279 B15.0668 F904.19 N41 X1.4503 Y.5821 Z-4.4316 A-56.6898 B13.6653 F912.54 N42 X1 N38 X1.0106 Y. 5876 Z-4. 5461 A-55. 5607 B17. 7803 F879. 41 N39 X1. 1572 Y. 5857 Z-4. 508 A-55. 9513 B16. 4387 F893. 1 N40 X1. 3037 Y. 5839 Z-4. 4698 A-56. 3279 B15. 0668 F904.19 N41 X1.4503 Y.5821 Z-4.4316 A-56.6898 B13.6653 F912.54 N N38 X1.0106 Y. 5876 Z-4. 5461 A-55. 5607 B17. 7803 F879. 41 N39 X1. 1572 Y. 5857 Z-4. 508 A-55. 9513 B16. 4387 F893. 1 N40 X1. 3037 Y. 5839 Z-4. 4698 A-56. 3279 B15. 0668 F904. 19 N41 X1.4503 Y.5821 Z-4.4316 A-56.6898 B13.6653 F912.54 N38 X1.0106 Y.5876 Z-4. 5461 A-55. 5607 B17. 7803 F879. 41 N39 X1. 1572 Y. 5857 Z-4. 508 A-55. 9513 B16. 4387 F893. 1 N40 X1. 3037 Y. 5839 Z-4. 4698 A-56. 3279 B15. 0668 F904. 19 N41 X1. 4503 Y. 5821 Z-4.4316 A-56.6898 B13.6653 F912.54 N4 N38 X1.0106 Y.5876 Z-4.5461 A-55.5607 B17.7803 F879. 41 N39 X1. 1572 Y. 5857 Z-4. 508 A-55. 9513 B16. 4387 F893. 1 N40 X1. 3037 Y. 5839 Z-4. 4698 A-56. 3279 B15. 0668 F904. 19 N41 X1. 4503 Y. 5821 Z-4. 4316 A-56.6898 B13.6653 F912.54 N38 X1.0106 Y.5876 Z-4.5461 A-55.5607 B17.7803 F879.41 N39 X1.1572 Y. 5857 Z-4. 508 A-55. 9513 B16. 4387 F893. 1 N40 X1. 3037 Y. 5839 Z4. 4698 A-56. 3279 B15. 0668 F904. 19 N41 X1. 4503 Y. 5821 Z-4. 4316 A-56. 6898 B13.6653 F912.54 N N38 X1.0106 Y.5876 Z-4.5461 A-55.5607 B17.7803 F879.41 N39 X1.1572 Y.5857 Z-4.508 A-55. 9513 B16. 4387 F893. 1 N40 X1. 3037 Y. 5839 Z-4. 4698 A56. 3279 B15. 0668 F904. 19 N41 X1. 4503 Y. 5821 Z-4. 4316 A-56. 6898 B13.6653 F912.54 N42 N38 X1.0106 Y.5876 Z-4.5461 A-55.5607 B17.7803 F879.41 N39 X1.1572 Y.5857 Z-4.508 A-55. 9513 B16. 4387 F893. 1 N40 X1. 3037 Y. 5839 Z4. 4698 A56. 3279 B15. 0668 F904. 19 N41 X1. 4503 Y. 5821 Z-4. 4316 A-56. 6898 B13. 6653 F912.54 N42 X N38 X1.0106 Y.5876 Z-4.5461 A-55.5607 B17.7803 F879.41 N39 X1.1572 Y.5857 Z-4.508 A-55.9513 B16. 4387 F893. 1 N40 X1. 3037 Y. 5839 Z4. 4698 A 56. 3279 B15. 0668 F904. 19 N41 X1. 4503 Y. 5821 Z4. 4316 A-56. 6898 B13. 6653 F912.54 N42 X1.59 N38 X1.0106 Y.5876 Z-4.5461 A-55.5607 B17.7803 F879.41 N39 X1.1572 Y.5857 Z-4.508 A-55.9513 B16. 4387 F893. 1 N40 X1. 3037 Y. 5839 Z4. 4698 A 56. 3279 B15. 0668 F904. 19 N41 X1. 4503 Y. 5821 Z 4. 4316 A56. 6898 B13. 6653 F912. 54 N42 X1.597 Y.5 N38 X1.0106 Y.5876 Z-4.5461 A-55.5607 B17.7803 F879.41 N39 X1.1572 Y.5857 Z-4.508 A-55.9513 B16.4387 F893. 1 N40 X1. 3037 Y. 5839 Z4. 4698 A 56. 3279 B15. 0668 F904. 19 N41 X1. 4503 Y. 5821 Z 4. 4316 A 56. 6898 B13. 6653 F912. 54 N42 X1. 597 Y.5805 N38 X1.0106 Y.5876 Z-4.5461 A-55.5607 B17.7803 F879.41 N39 X1.1572 Y.5857 Z-4.508 A-55.9513 B16.4387 F893. 1 N40 X1. 3037 Y. 5839 Z4. 4698 A 56. 3279 B15. 0668 F904. 19 N41 X1. 4503 Y. 5821 Z 4. 4316 A 56. 6898 B13. 6653 F912. 54 N42 X1. 597 Y. 5805 Z-4.3 N38 X1.0106 Y.5876 Z-4.5461 A-55.5607 B17.7803 F879.41 N39 X1.1572 Y.5857 Z-4.508 A-55.9513 B16.4387 F893.1 N40 X1. 3037 Y. 5839 Z4. 4698 A 56. 3279 B15. 0668 F904. 19 N41 X1. 4503 Y. 5821 Z 4. 4316 A 56. 6898 B13. 6653 F912. 54 N42 X1. 597 Y. 5805 Z-4. 3933 AN38 X1.0106 Y.5876 Z-4.5461 A-55.5607 B17.7803 F879.41 N39 X1.1572 Y.5857 Z-4.508 A-55.9513 B16.4387 F893.1 N40 X1. 3037 Y. 5839 Z4. 4698 A 56. 3279 B15. 0668 F904. 19 N41 X1. 4503 Y. 5821 Z 4. 4316 A 56. 6898 B13. 6653 F912. 54 N42 X1. 597 Y. 5805 Z-4. 3933 A-57.036 N38 X1.0106 Y.5876 Z-4.5461 A-55.5607 B17.7803 F879.41 N39 X1 .1572 Y .5857 Z-4 .508 A-55.9513 B16.4387 F893.1 N40 X1.3037 Y. 5839 Z-4. 4698 A 56. 3279 B15. 0668 F904. 19 N41 X1. 4503 Y. 5821 Z 4. 4316 A 56. 6898 B13. 6653 F912. 54 N42 X1. 597 Y. 5805 Z-4. 3933 A-57. 0362 B12.23 N38 X1.0106 Y.5876 Z-4.5461 A-55.5607 B17.7803 F879 .41 N39 X1 .1572 Y .5857 Z-4 .508 A-55 .9513 B16 .4387 F893.1 N40 X1.3037 Y. 5839 Z-4. 4698 A 56. 3279 B15. 0668 F904. 19 N41 X1. 4503 Y. 5821 Z 4. 4316 A 56. 6898 B13. 6653 F912. 54 N42 X1. 597 Y. 5805 Z 4. 3933 A-57. 0362 B12. 2349 F9 N38 X1.0106 Y.5876 Z-4.5461 A-55.5607 B17.7803 F879 .41 N39 X1 .1572 Y .5857 Z-4 .508 A-55 .9513 B16 .4387 F893.1 N40 X1.3037 Y.5839 Z-4. 4698 A 56. 3279 B15. 0668 F904. 19 N41 X1. 4503 Y. 5821 Z 4. 4316 A 56. 6898 B13. 6653 F912. 54 N42 X1. 597 Y. 5805 Z 4. 3933 A 57. 0362 B12. 2349 F918.07 Mastercam Australia | 0478 674 970 info@mastercam.com.au www.mastercam.com.au MILL LATHE MILL-TURN WIRE ROUTER Mastercam for SOLIDWORKS®
Work with confidence. Choose Mastercam. MILL SWISS LATHE MILL-TURN WIRE ROUTER Mastercam for SOLIDWORKS® DESIGN
www.mastercam.com
MULTIAXIS SWISS DESIGN
Incorporating an extensive line of indexable inserts and toolholders, the new 222 Series provides a productive and costeffective solution for all material types and applications. The 222 designation is derived from the two cutting edges with an effective depth of cut up to 22mm. The 222 System is available with both a toolholder or as a blade type to suit the demands of the end-user. The dedicated toolholder is nickel-plated to present extended tool life and longevity with three internal coolant supply channels to suit the specific set-up of the endusers machine tool and coolant supply configuration. High-pressure coolant delivery is supplied to the cutting edge via two channels that are positioned both above and below the cutting edge. This design extends tool life, performance and it also supports chip breaking and evacuation. The toolholders are available in left and right-hand designation with tool body dimensions from 12 by 12mm up to 25 by 25mm, making the new 222 System suitable for everything from small compact turning centres and sliding head machines through to large more robust machine tools. The impressive toolholders can be selected in overall body lengths from 108mm to 152mm depending upon the tool selected. Rigidity and performance are further assured by a tool design that also incorporates a new clamping screw design and insert support that guarantees maximum insert clamping torque and stability during machining. Like the toolholder designation, the nickelplated blade-type toolholder is available with and without through coolant facility with a blade length of 120 or 150mm, a height of 26 or 32mm and a width of 2.25mm depending upon the selected tool. The new blades are compatible with existing Guhring blade holding tools as well as industry-standard blades from alternate manufacturers. The pressed-to-size solid carbide indexable inserts are coated with Guhring’s innovative proprietary Fire coating technology that demonstrates outstanding performance and longevity. The insert grades provide stable and consistent machining on carbon steel, low and high-alloyed steel, cast steel and stainless. The double-edged inserts correspond with the toolholders with neutral, left and right-hand variants available. Guhring has developed the 22mm long and 3mm wide inserts with an optimal chip breaking design that creates a smooth cutting action and reduces cutting forces. www.guhring.com.au

SLM Solutions – The future floats
SLM Solutions has released Free Float, a new additive manufacturing software package that empowers the creation of metal components that were previously impossible to design.
People have long discussed the use of structures, methods and processes found in biological systems in the design of metal 3D-printed products. Now users can utilise the full spectrum of nature-inspired design, without the limitations of the manufacturing process. Free Float is being shipped with every new SLM Machine, and can be retrofitted on others for free. “The goal is to be relentless with innovation,” says Sam O’Leary, CEO of SLM Solutions. “It’s free because we want to empower our partners and customer base. Why should this remain an enablement for just a few when it can benefit all?” Additive manufacturing has created new opportunities for innovation in product design, but has always been restricted by the ‘45-degree rule’. If a new part requires printing at anything less than 45 degrees, it isn’t possible without the aid of support structures. Now it’s possible to print overhangs at 10 degrees on long-range geometry and 5 degrees on short-range geometry, depending on the geometry of the individual part design and the thermal capabilities of the material. Several key enablers of Free Float already exist in SLM machines, such as the optimised interaction of the laser beam with the powder bed, the gas flow and management of the gas flow system, and frictionless re-coating mechanism that is bi-directional. This is delivered through the platform to match users’ requirements to the specific part, even allowing you to adapt parameters during the build. Users can also leave out support structures while still delivering part quality, enhancing freedom of design for innovators and creators. Since the 1990s, support structures have been vital in 3D metal builds for various reasons. They provide support for overhanging sections; they play a vital role in the cooling process, absorbing and distributing excess heat away from the components; and they can help prevent part distortion under high heat conditions. However, they do put constraints on product development. Supports must be removed in post-processing; design freedom is limited as support structures have to be considered in planning; and the build takes longer and uses more material. With Free Float these limitations are reduced. “Today you can design bolder. Design freer. Design with fewer limitations,” says O’Leary. “Today you can work faster. Work more productively. Work better. Today you can go to the place that will take you to the next level.” As well as increased overhang capability, the new technology allows users to increase the diameter of internal cooling channels, create thinner walls and sharper edges with reduced peel-off. The finished surface is improved, reducing post-processing time, while higher density and reduced porosity can be achieved. The space where supports might have been allows for better part orientation, or for more parts to be printed and a great reduction in material usage. Free Float software is now ready to be delivered and shipped with every new laser system, with retrofitting available on most SLM Solutions machines. Builds in titanium and Inconel 718 have been the initial focus of the new software parameters, meaning industries such as aerospace, space and the energy sector will have an early advantage in 3D product design and development, though this will be the first of many more metals to join the portfolio.
www.raymax.com.au
Hypertherm – Major update for Robotmaster robotic software
Hypertherm has released Robotmaster Version 7.4, an update of its offline robot programming software containing several enhancements designed to further simplify robotic programming.
The latest version of Robotmaster includes a range of new features, including: • Major enhancements to Remote Tool Center Point (RTCP) that allow for an improved end user experience and exploit the full capabilities of any robotic cell. • Additions to the surface paths with added strategies and advanced tools for applications such as polishing, grinding, deburring and more. The surface paths are designed to tie-in perfectly with the enhancements to RTCP or traditional configurations for robotic finishing. • Faster processing times when saving, loading, and calculating jobs, plus improved real time feedback during simulation for faster part programming times. • Enhancement to the Robotmaster Interactive Simulation
Environment (RISE), delivering a more realistic simulation for external axes, along with tools to better control motion between the robot and external axes. “With Robotmaster V7.4 we’ve responded to our customer base with features and enhancements that we believe take a big step forward,” explains Garen Cakmak, leader of Hypertherm’s Robotic Software team. “Take the RTCP improvements as an example. These will allow users to realise more value from their robotic cell investment.” Building upon the redesigned V7 architecture, first introduced in 2018, Robotmaster uses integrated CAD/CAM functionality to make robotic programming easy and intuitive for everyone, even first-time users. The software is used by a wide range of industries to program robots for tasks that include surfacing, 3D milling, additive manufacturing, welding, painting, and more.
www.hypertherm.com
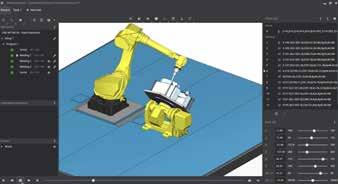
FARO launches all-new Quantum Max FaroArm
FARO Technologies has released its all-new Quantum Max ScanArm, an advanced portable measurement tool that features three purpose-built hot-swappable Laser Line Probes (LLPs).
Designed to meet a variety of small and medium-sized measurement needs, the LLPs – xR, xP, and xS – ensure that users are no longer forced to choose between speed, accuracy, or resolution. Value and productivity are enhanced by over 30% with the performance and scanning capabilities of the Quantum Max. Each LLP is enhanced with FARO CLR (Continuous Light Rectification) technology, which provides high-quality scan data on dark, translucent, and reflective surfaces, eliminating the need for sprays, time-consuming surface preparation, and cleanup while avoiding finished product contamination. “With the next-generation Quantum Max ScanArm, getting the inspection job done as fast and precisely as possible has never been easier,” said Ozan Ugurlu, FARO Senior Director of Product Marketing. “Changing probes is quick and easy in just seconds, with no need for recalibration so inspection can continue, virtually uninterrupted.” The new FARO LLP family features: • xR: Suited for high-precision tasks or areas on a part with tight tolerances to capture data with up to 30% better accuracy and resolution • xP: Offers a balance of the xR for resolution and the xS for speed so coverage and accuracy blend together for overall productivity • xS: Best for large parts or expansive surface areas when data collection speed is top priority — extra wide laser stripe delivers double the coverage in a single pass, allowing users to collect data over 65% faster Quantum Max further enhances speed and accessibility with its kinematic mount that allows each LLP to be interchanged with seamless ease. The portable measurement arm is fitted with a small, light end effector, allowing users to better access hard-toreach confined spaces while reducing operator fatigue. Quantum Max is fully compatible with FARO CAM2 software and its Repeat Part Management feature, which allows guided inspection routines to be pre-programmed. Operators can now perform the exact same inspection routine, minimising variability and maximising repeatability. “The new Quantum Max ScanArm exceeded our expectations,” added Clay Marsh, Managing Partner at Real Street Performance. “In our many years of industry expertise, we have learned that choosing the right LLP is not always a ‘one size fits all’ proposition. There are parts or specific features or areas on a part where you need the most accurate scan possible. For other parts or areas, getting the job done quickly to maintain production speed is most important. The Quantum Max ScanArm solves for both.”
www.faro.com

Kennametal HiPACS: Single-step aerospace drilling, countersinking
Kennametal has introduced the HiPACS drilling and countersinking system for aerospace fastener holes.
Designed to drill and chamfer holes in one operation, the high-precision tool meets the aerospace industry’s stringent accuracy requirements, while delivering increased tool life in machining composite, titanium and aluminium aircraft skins. “Most fastener hole tools used today are complex made-to-order tools with long lead times,” says Georg Roth, Product Manager at Kennametal. “HiPACS uses standard, off-the-shelf components for quick delivery and low cost per hole, by allowing the drill and chamfer insert to be indexed independently from one another. What’s more, it’s the only indexable drilling and countersinking system on the market that can hold the aerospace industry’s required fastener hole chamfer tolerances in just one operation.” Designed to be clamped in a standard hydraulic chuck, the HiPACS modular system consists of three components that are fast and easy to assemble: • A reducer sleeve with a built-in high-precision pocket seat. In conjunction with a standard hydraulic chuck, this component provides ultra-secure clamping and a runout of no more than 3µm, significantly increasing tool life and hole quality. • A PCD countersinking insert. This eliminates the need for expensive custom solution step drills, reducing manufacturing costs while meeting the industry’s accuracy requirements. • The two series of solid carbide drills —both diamond-coated and PCD-tipped—covering all material combinations found in a typical aerospace assembly. In addition, the straight shanked tools allow for length adjustments in increments of 10mm. The new HiPACS drilling and countersinking system can be utilised on all machines typically used for aerospace applications. In less stable conditions such as robot end effectors, the diamond coated carbide drills offer excellent tool life and hole quality. PCD-tipped drills, on the other hand, excel in stable conditions such as gantry machines. With an industry standard interface, HiPACS can be used on any CNC machine, and is suitable for a variety of drilling and countersinking applications.
www.kennametal.com
SAGE launches TilliT digital manufacturing spin-off
SAGE Group has announced the launch of TilliT, a new technology business that will deliver Software as a Service (SaaS) and associated Internet of Things (IoT) hardware solutions for customers across the broader manufacturing industry.
The move is part of SAGE Group’s strategic expansion aimed at meeting continued demand for agile software solutions and lightweight sensors amid the accelerating transition to Industry 4.0. “SAGE continues to invest in the evolution of our offering to clients, operating across the sectors that are shaping the world, to accelerate their digitalisation journey“ said SAGE Group Managing Director and CEO Adrian Fahey. “TilliT will be a standalone organization within the SAGE Group, bringing together two existing software products – TilliT Digital Operations and the Ailytic AI Scheduler – to enable us to continue focus on the development of smart manufacturing solutions.” The TilliT SaaS and IoT solution is a digital factory suite tailored to manufacturers of all sizes . It provides an integrated way to plan, execute and analyse manufacturing processes. It offers visibility of asset and manufacturing line performance, directs the execution of events, and orchestrates activities necessary to manufacture any finished good. It also handles quality checks, production scheduling and digital workflow with a focus on real-time visibility. Feedback from TilliT customers has been extremely exciting. TilliT was incubated within Nukon, a consulting company within the group. Nukon founders Alec Konynenberg and Rafael Amaral have decades of experience in understanding the challenges facing manufacturers in increasing efficiency, reducing costs and optimisig operations. This hands-on learning drove the development of an entirely new approach to digitalising production and removing paper from the shopfloor. Nukon remains a key implementation partner and represents the first of many distribution and implementation partners TilliT is targeting globally. Amaral moves across to TilliT as the Chief Technology Officer and will drive an accelerated roadmap to build on the current tech platform. SAGE recently announced the acquisition an Adelaide-based software company Ailytic. The Ailytic AI Scheduler is a modern, flexible and powerful tool for optimising detailed schedules in food
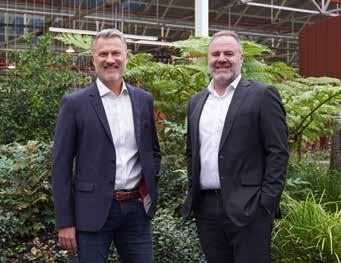
TilliT CEO James Balzary and SAGE Group MDand CEO Adrian Fahey.
& beverage, plastics, steel manufacture, electronics and other industries. The tool is already used by diverse range of Australian and global manufacturers. Ailytic founder James Balzary, will head up the TilliT business as Chief Executive Officer. “This is an exciting step for the team which will allow us to enter new markets, build new channel relationships and ultimately service current and future clients with an expanding portfolio of innovative software technologies” says Balzary. According to a 2019 report from LNS Research, 95% of Australian manufacturers are small to medium on a global scale and that 75% of their personnel and manufacturing equipment has no cloudconnectivity or detailed analytics or true performance. For this reason, IoT- and AI-enabled technologies such as TilliT are crucial to enable smart decision making, protect manufacturing profitability, and deliver the opportunity to thrive on a global stage.
www.goTilliT.com
Dormer Pramet – True 90° shoulder milling with TNGX
Dormer Pramet has expanded its offer for true 90° shoulder milling in various materials, delivering improved cost per edge with its new range of TNGX16 inserts and STN16 cutters.
The larger double-sided inserts have sixcutting edges, providing greater depths of cut (up to 10mm) and higher feed compared to its existing TNGX10 range. By offering low cutting resistance, the assortment improves the connection between passes, creating an excellent surface quality. This reduction in forces leads to smooth, quiet machining for additional process security. A positive geometry and through coolant offer improved chip evacuation across a wide range of materials, including steels, stainless steels, cast iron and non-ferrous metals. The TNGX16 assortment is available in radii from 0.4mm to 1.6mm and alongside a wide range of grades. It is supported by three geometries, F, M and FA. F is the first choice for low-to-medium carbon content steel. A highly positive geometry with narrow peripheral land makes it suitable for light to medium machining. The M geometry is for machining carbon steel, stainless steel and cast iron. Its positive geometry with medium T-land, makes it ideal for light to medium machining. Suitable for non-ferrous metals, FA is a highly positive geometry with a sharp cutting edge. Its polished insert face reduces sticking of machined material. Meanwhile, the STN16 tool holders provide a higher number of teeth for greater productivity, compared to the original assortment. Its differential pitch offers smooth machining in diameters above 50mm. Manufactured from coated tool steel to better resist corrosion and reduce friction, the cutter features large and strong clamping screws for easier handling and stability. A precision machined pocket design enables performance repeatability and security.
www.dormerpramet.com
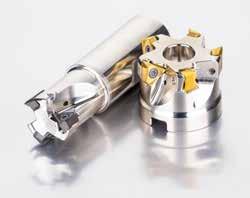
Leussink: Storage system complements Demmeler welding table system
Leussink has added the Demmeler Smart Toolbox to its large range of accessories for the Demmeler Modular Fixturing system.
Leussink Managing Director Jason Leussink says the new storage system is a convenient way to store the many Demmeler accessories: “The Demmeler system includes dozens of accessories like clamps, angles and bolts, and it makes sense to have a dedicated toolbox that fits neatly under the table. It means you always have your clamping accessories at hand.” The Demmeler Smart Toolbox is an under-bench cabinet with drawers made from sheet steel and is available in a two-drawer and a three-drawer model. Its maximum load capacity is 125kg, with each drawer having a recommended load capacity of approximately 50kg. While providing ample storage space, the Demmeler Smart Toolbox also protects tools and small parts from dirt and weld spatters. All drawers are equipped with a rubber mat as an anti-slip insert. This has a noise-dampening effect and protects the drawers from scratches. Additionally, the drawers have a soft-close system for quiet and jerk-free opening and closing, and they are lockable. The Demmeler Smart Toolbox is installed by attaching it to the underside of the Demmeler welding table, putting all the mostused Demmeler accessories within easy reach. It is easily installed using the table’s system bore-holes. The dimensions of the draws are 450mm x 500mm, while the drawer heights are 180mm (twodrawer version) and 80 mm/80 mm/180 mm for the three-drawer version. The Demmeler Smart Toolbox can also be fitted to other modular welding tables, to which Leussink can advise on how they can be fitted. German brand Demmeler first developed its 3D clamping system in the 1990s and it has gone on to become an international industrial standard due to the many possible applications and combinations. The Demmeler 3D workbench and welding table is a versatile jigand-fixtures system for all types of welding and fabrication work. Projects such as steel construction, sheet metal processing, robot technology, assembly and measuring equipment, laser welding, laser cutting, prototype construction, body construction, and many others can be set up easily and precisely. It can meet all horizontal and vertical requirements. “At Leussink we don’t just sell tables and walk away,” Jason adds. “We work with our clients to make sure the Demmeler Modular Fixturing System works for them by providing onsite visits and follow-ups.” www.leussink.com.au
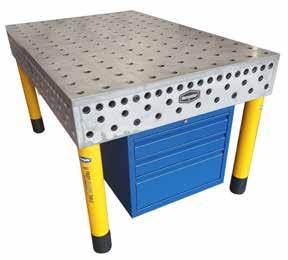
The Global Standard for Wireless Connection
Bluetooth®
Manage Measurement Data Centrally and Wirelessly on a Smartphone, Tablet or PC
The new U-Wave Bluetooth transmitter utilizes the popular Bluetooth 4.2 Low Energy Wireless Technology and allows a simple connection to smartphones, tablets and Bluetooth enabled Laptops and PC’s.
• A buzzer type and IP67 type with dustproof and waterproof specifications are available. • Up to 7 units can be connected to 1 Bluetooth enabled PC without a receiver. • New U-WavePak BLE for Android, iOS and
Windows available at no cost.
Available exclusively from Mitutoyo’s authorised national distributors
Walter launches micro drills for 12XD
When it comes to precision micro-drilling, Walter has established a strong reputation with its high-quality Supreme range of drills; now, the company has introduced two new additions to extend the portfolio for end users.
In a programme expansion, the new internally cooled Walter Titex DB133 Supreme micro drills have become successfully established around the world for machining precision parts. The series has been expanded with the DB133 Supreme solid carbide micro drill in dimensions of 5, 8 and 12XD. The through coolant DB133 Supreme features an AlCrN coating. The 5XD offering has WJ30EL full flute length coating applied. However, the longer 8XD and 12XD drills are WJ30ER with the coating only applied to the point of the drill and not the entire flute length, which further aids chip evacuation in deeper holes. The Walter Titex DB133 drills feature a 140-degree point angle to ensure positive engagement in the pilot hole that is produced by DB131. The DB133 Series starts at 0.7mm diameter, and increases in 0.05mm increments to the largest drill in the range, 1.984mm. The overall flute length of the 0.7mm diameter 5XD, 8XD and 12XD drills is 6mm, 8mm and 11mm and 17mm, 23mm and 31mm respectively for the largest 1.984mm diameter 5XD, 8XD and 12XD drills. The entire programme is based upon a 3mm diameter shank with all drills consisting of precision ground flutes and two coolant channels that maximise chip clearance and cooling performance. The new DB131 Supreme drill is a pilot drill for deep hole drilling operations. It features the WJ30EL (AlCrN) coating, which covers the complete flute length and it has a smooth surface offering secure chip evacuation. The point angle on the DB131 pilot drill is 150 degrees making it perfect for pilot holes up to 2XD prior to the deep hole drilling applications with the corresponding DB133 drill. The diameter ranges from 0.5 to 1.984mm with 0.05mm diameter increment increases, with common imperial equivalents also added to the program, and covering some small tap drill sizes. The flute length of the 0.5mm drill is 3mm and the overall length is 47mm and this proportionately increases to a flute length of 10mm and overall length of 57mm on the 1.984mm diameter drill. The result of a new flute design allows the chips to break, so that they are shorter, guaranteeing reliable evacuation from the work envelope. The new drills also incorporate a special cutting edge preparation that demonstrates outstanding surface finish and overall hole quality on the component whilst significantly improving tool life. With these new products, Walter has further refined the adaptation of the length to diameter (L/D) ratio to the required drilling depth. The result is a range of micro drills that ensures maximum stability when machining thanks to its broad scope and the optimised design. The drill and pilot drill can be used with emulsion or oil and are suitable for all ISO material groups. In addition to the watchmaking and jewellery industry and medical technology, the premium manufacturer cites general mechanical engineering, mwould and die making, the electronics and the energy and automotive industries as other specific areas of application.
www.walter-tools.com
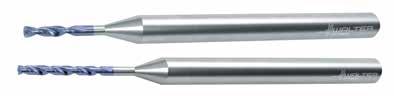
‘Manufacturing Mastery’: New podcast for Australian manufacturers
Newcastle-based manufacturing growth specialist Graeme Fitzgerald has launched a new podcast aimed at progressive Australian manufacturers who want to be more profitable, more sustainable and drive future growth.
The ‘Manufacturing Mastery’ podcast includes special guest speakers and will cover a wide range of industry-relevant topics. The content is intended to offer valuable insights and practical, real-world advice that manufacturers can apply to their business. Topics covered will include how to embed a planning framework into your business, marketing in Australian manufacturing, new approaches to innovation, the importance of culture, how to lead change, and navigating the new normal. “Manufacturing Mastery is my way of doing what I can to help create a forum where we educate and support manufacturers by sharing knowledge, experiences and lessons learnt in a format that’s in snack-sized bites for a busy world,” says Fitzgerald. “The podcast offers a unique opportunity to hear first-hand from practitioners what’s happening in all other areas of manufacturing and to listen to new ideas that may apply to their business, including emerging technologies – all from an Australian perspective”. According to Fitzgerald, the idea behind the podcast is to challenge thinking. Some listeners may not agree with everything that’s said, but that’s the intention. It’s designed to disrupt the status quo and create a forum for discussion. The first series of Manufacturing Mastery is anticipated to be released fortnightly and will run for eight to 10 episodes. Episodes will be available on the Graeme Fitzgerald website as well as via listeners’ favourite podcast channels. Recent episodes include ‘The Pursuit of Excellence’ with John Costly, and ‘Marketing and Australian Manufacturing’ with Jacqui Daley.
www.graemefitzgerald.com.au
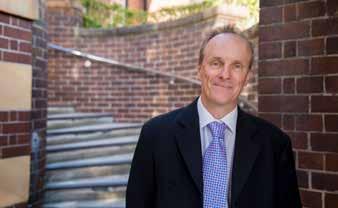