
5 minute read
Zip Water boosts its fabrication productivity
from AMT AUG/SEPT 2021
by AMTIL
Prompted by a redesign to one of its core product lines, Zip Water recently invested in an upgrade to its press brake capability, with the acquisition of an Amada HG1003ATC machine.
Zip Industries has been manufacturing and marketing Australian designed and made instant water systems since 1947. The company introduced the world’s first boiling water tap in 1970, followed in 1975 by the first on-wall instant boiling water heater. Today, Zip employs 160 people at its factory in Condell Park, in Sydney’s south-west suburbs,where it produces a wide range of hot and chilled, still and sparkling water-dispensing products that are exported to the world’s fastest growing commercial and consumer markets. The company’s flagship product, the Zip Hydrotap is also manufactured at this facility. The Hydrotap is an innovative multifunction touch tap that has revolutionised instant water dispensing and has recently made a successful debut in the huge US market. Michael Conyers, Director of Operations, Asia-Pacific at Zip, explains: “The Hydrotap is an appliance with heating and chilling functions and comprises many diverse parts. While our core competencies include sheet metal fabrication, manufacture of this product includes sub-assembly and final assembly of mechanical and electronic components. “Our second most popular product in the Australian domestic market, as well as the UK, is the Zip Miniboil, which is well known with a long history in the market. We have refreshed the functionality of this product, along with an updated design,” Conyers adds. Product redesign
In deciding to embark on a redesign of the small on-wall boiling unit, the process soon highlighted for Zip a need to upgrade its workshop’s press brake capability. It became clear that the company’s old machine was not up to the task, and a new machine would be required that offered the ability to produce the quality finish that was needed. David Smith, Manufacturing Manager at Zip, explains: “We analysed the performance of a number of press brakes. We needed an improvement in both output and quality. Bending accuracy had to be spot on, as was the ability to maintain the integrity of the powder-coated surface during the bending process. As well as a new machine, we needed special tooling that would let us maintain manufacturing parameters and tolerances that were required of the modern design.” The company investigated a wide range of
Members of the Zip Water team (from left): operator Charles Duarte; Michael Conyers, Director of Operations – Asia-Pacific; James Martin, Project Manager; and David Smith, Manufacturing Manager.
Zip Water manufactures and markets a range of Australian-designed and -made instant water systems.
press brakes before settling on their final choice. James Martin, Project Manager at Zip, says: “Some had a few of the features we needed, others had different features. The Amada HG1003ATC was the machine that gave us all the features and benefits we wanted, along with a complete package of local availability, installation, testing, commissioning and training.” Full list of features
Martin continues: “We particularly liked the press brake’s simulation panel that lets the operator preview the production process, graphically showing the final result that would be completed by the program. However, our decision to purchase the Amada machine was based on a package of reasons. These ranged from performance to very fast automatic tool changing, and – perhaps more importantly – the fact that Amada has a local presence with machines in stock and could provide full technical and engineering support.” Smith adds: “Access to technical staff was important to support the installation to enable us to get the machine up and running quickly. The Amada HG1003ATC ‘ticked all our boxes’ when looking at the parameters on which a decision was based.” According to Smith, the delivery and installation of the new machine took place very smoothly. “Within the first day we had all new programs loaded into the machine and producing parts,” he recalls. “We were productive from the first day. The set-up of the machine and the accuracy of the performance is a world away from what we were previously experiencing. Even our most experienced operators on the old machine were not able to achieve the same level of accuracy we are getting from the Amada. “In addition to us achieving the quality level needed, the greatest benefits are fast tool
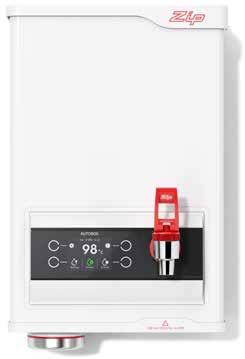
changing and a significant reduction of waste materials. Tool changes that previously would have taken up to 45 minutes are now performed in a couple of minutes. Automatic tool changes also preserve the quality of the tools, as there is less chance of damage than with manual tool handling.” Speed and precision
The new Amada press brake has overcome many of the problems experienced with Zip’s old machine, such as misalignments, which would result in the staff having to rework parts. In fact, according to Smith, the purchase of the new machine been a “game changer”. “The bending precision of the Amada press brake has enabled us to significantly some cases exceeding, 400 per hour. “Our productivity is vastly better and the quality is super accurate and consistent,” Smith concludes. “The new Amada HG1003ATC press brake has provided a massive improvement in production and a leap forward in technology.”
www.amada.com.au www.zipwater.com
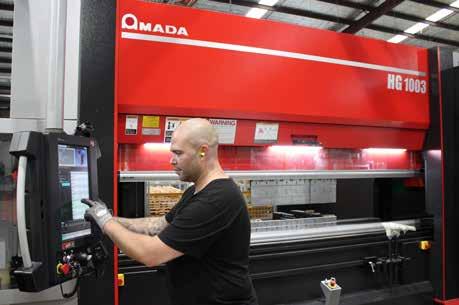
The new Amada HG1003ATC press brake has enabled Zip Water to significantly improve the quality finish of its products and improve overall workflow.
improve the quality finish of our product and improve our total workflow, both critical requirements in launching our new product,” says Smith. “Output quality, speed of tool change, rapid machine setup, reduction of effort and time compared with manual tool changes all add up to huge savings in labour costs. We are producing more than 300 different parts on this machine at a rate up to, and in
#1 IN IPG LASER SALES WORLDWIDE - OVER 2000 MACHINES IN 2020!
Automation Coming for Stock!
HSGs extensive Tube Laser Line-up

From simple manual load tube cutting to fully automated bundle feed systems. - Up to 12m in-feed and out-feed - Upgradeable to 5-Axis Bevel Cutting - Sigmatube Advanced Nesting Package
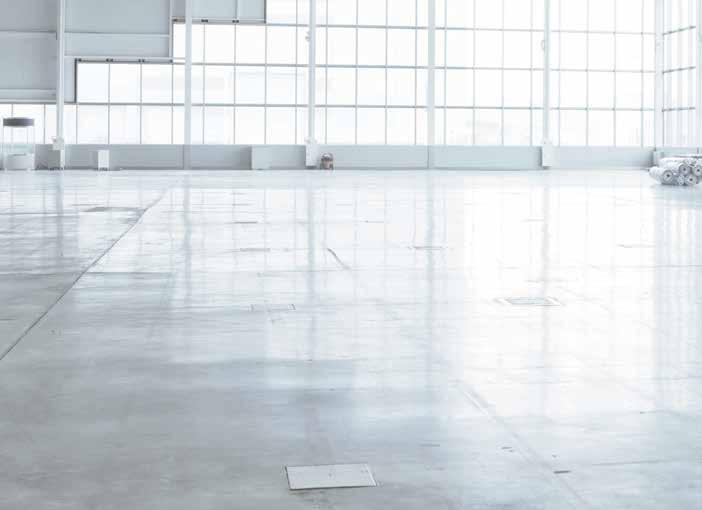
sales@capitallaser.com.au CALL US TODAY: OFFICE: 03 9132 5223 GREG COX: 0418 861 083

www.capitallaser.com.au Get in touch to find out more about our extensive range of automation systems!
HSG GH INDUSTRIAL FIBER LASER CUTTING MACHINE
- German Precitec Cutting Head - Quality imported German and Japanese components - Automation ready