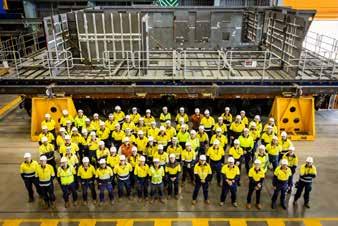
27 minute read
INDUSTRY NEWS: Current news from the Industry
from AMT DEC 2021
by AMTIL
Hunter Class Frigate Program rolls out first steel unit
Over 28 tonnes of Australian steel rolled off the production line at the Osborne Naval Shipyard in Adelaide in October with the completion of structural manufacture of the first steel prototype unit for the Hunter Class Frigate Program.
The 217sqm unit, which has a bigger footprint than the average Australian house, was moved from the shipyard’s primary manufacturing hall into the next stage of production, to be outfitted and consolidated (with the addition of three more units) into the first prototyping block. The prototype unit is one of four in the first representative ship block and is the first to have been blasted and painted, cut and constructed in the new Shipyard. This particular unit and block are located in the middle of the ship and would contain the Officer’s Accommodation. BAE Systems Maritime Australia Managing Director, Craig Lockhart said: “This is a significant production milestone for the Hunter frigate program and an important start towards establishing shipbuilding capability across the Osborne Shipyard. Osborne is one of the world’s most technologically advanced shipyards, a purpose-built modern manufacturing facility built for the digital age to deliver next generation anti-submarine warships by a highly skilled Australian workforce equipped to use Industry 4.0 technologies.” BAE Systems Maritime Australia will build nine of the world’s most advanced anti-submarine warfare frigates for the Royal Australian Navy. The prototyping phase commenced in December 2020 and program mobilisation continues at pace with more than 1,300 people now working across the program including 35 apprentices and 26 graduates. The Hunter program will create and sustain 5,000 jobs over the life of the program. Steel for the prototyping phase of the Hunter program has already been procured from Bluescope AIS at Port Kembla, NSW and structural steel from Infrabuild in Whyalla, SA. The Hunter program has already placed around 40 contracts with Australian businesses to support design and prototyping. Around 20 further contracts will be awarded to support prototyping, including ship outfitting, gaskets, wholeship eyeplates, insulation and deck coverings. Lockhart added: “Critically, the manufacture of the first unit has put into practice this step-change to shipbuilding programs of the past, as our employees test the full productive capacity of the yard maximising our ability to build high quality ships through our pulse line process utilising robotics that enable high quality welds and zero defects. This ensures an enduring and uniquely Australian sovereign industrial capability that supports Australia’s continuous naval shipbuilding strategy for future generations.”
www.baesystems.com
Calling all Manufacturing Mates
Mates in Manufacturing is a new suicide prevention program aimed at supporting the mental health of workers in the manufacturing industry.
Suicide affects us all. The suicide of a friend, family member or workmate can be devastating across the whole community and particularly at work. More than 3,000 Australians die from suicide each year; of these 75% are men. It’s a leading cause of death for people in the 25-39 age group. The pandemic has brought mental health issues into the forefront. Despite the devastating number of workers infected with COVID-19 in workplaces, Safe Work Australia has reported that nearly one in every five COVID-related workers’ compensation claims were generated on mental health grounds. In manufacturing, with many predominantly male or multicultural workers, there have been barriers to discussing mental health as openly as possible. Mates in Manufacturing has been set up to remedy the challenges of suicide ideation and mental health more generally. Bringing together employers and unions and drawing on the expertise of the Mates organisation, Mates in Manufacturing will deliver critical workplace training, building a peer-based program within workplaces and developing knowledge within the industry to address these problems. Funding has been secured from both the NSW and Federal Governments for research by Western Sydney, Deakin and Melbourne Universities, to ensure the programs are fit for purpose. Undertaken as a partnership between employers and unions in the sector, Mates in Manufacturing started its rollout in November ahead of its official launch on 10 December.
Members of the steering committee overseeing the project come from manufacturing industry leaders like Downer Group, OPAL, UGL, Stramit and Thales. They are joined by the Australian Industry Group, with workers represented by the Australian Manufacturing Workers’ Union (AMWU), the Australian Workers' Union (AWU) and the United Workers’ Union UWU. The partners recognise that suicide prevention and improving mental health support transcends traditional workplace issues and that by working together we stand a better chance of making positive change.
If you and your company operate within the manufacturing industry and want to get serious about confronting suicide and mental health challenges, as part of an evidence-based industry partnership through this workplace program, the Mates in Manufacturing program would welcome your involvement as part of this process.
To start a conversation, contact Dave Henry at matesinmanufacturing@gmail.com
Amiga Engineering lands order for 3D printing on SPARTAN scramjet
Queensland aerospace company Hypersonix Launch Systems has placed an order with Victorian manufacturer Amiga Engineering for the additive engineering build of the SPARTAN scramjet.
SPARTAN is Hypersonix’s fifth-generation scramjet. It is a fixed-geometry self-igniting hydrogen-powered scramjet capable of accelerating from Mach 5 to Mach 12. SPARTAN’s fixed geometry means it has no moving parts, so the design lends itself to 3D printing. This reduces both the cost and time to produce the scramjet, while potentially adding to reliability and performance. Additive manufacturing allows the creation of parts that have a complex design, and is perfect for light-weighting, which is essential for the space industry. SPARTAN uses green hydrogen for fuel, so creates no CO2 emissions. The hydrogen fuel also allows Hypersonix to utilise regenerative cooling on the combustor, in turn allowing the use of readily available high-temperature alloys in place of more expensive and complex high-temperature composites. David Waterhouse, Managing Director and co-founder of Hypersonix said: “The use of additive engineering to manufacture a scramjet engine will fundamentally disrupt the cost structure of scramjets and an important step in providing more affordable access to hypersonic flight. We are very proud of Australia’s world-leading heritage in hypersonics and the ability of Australian companies to work together to demonstrate of sovereign capability in this new space technology.” Additive manufacturing is one of the key elements mentioned in the Federal Government’s Modern Manufacturing Strategy, which among others includes priorities such as space, defence and clean energy. The SPARTAN scramjet is being manufactured under an Accelerating Commercialisation grant that the Federal Government awarded Hypersonix in August 2020. Under this grant, Hypersonix is building a flight-ready scramjet engine and fuel system. Hypersonix has been able to leverage the growing global hydrogen economy to repurpose off-the-shelf high-pressure composite hydrogen tanks. Hypersonix completed shock tunnel testing of SPARTAN in March 2021 and has completed the final design and thermal modelling of the scramjet. The project is on budget and in schedule and due for completion in March 2022. “In a demanding industry such as aerospace, additive manufacturing offers the cutting edge in component manufacture capable of creating very complex parts in some of the most exotic materials,” said Michael Bourchier, Managing Director and founder of Amiga Engineering. “With thousands of hours of research and development in every part, the aerospace industry settles for nothing but the best. We are extremely excited to work with Hypersonix Launch systems on the world’s first 3D printed fixed geometry scramjet engine.”
www.hypersonix.com.au www.amigaeng.com.au
It’s what you can’t see that is the biggest risk to your growth.
Get the visibility you need to efficiently control everything from bill of materials to production planning and inventory.
BusinessHub specialises in delivering MYOB Advanced: a cloud ERP (Enterprise Resource Planning) tool for manufacturing businesses like yours. Our expertise allows us to tailor a business solution to give you full control. With ongoing support and clarity, we’ll improve the efficiencies of all your key business areas: Inventory, Accounts, Customers and Production. Visit the BusinessHub exhibition during Australian Manufacturing Week at the The International Convention Centre Sydney (ICC Sydney) from 7-10 June 2022.
We’re here to set you up for success. phone 1300 733 071 � businesshub.com.au/AMTIL
ECU unveils new engineering labs
Boosting local manufacturing capabilities and finding new solutions for Australia’s green energy future are some of the exciting possibilities on offer with the opening of Edith Cowan University’s (ECU) three new engineering laboratories.
ECU recently unveiled the $10m state-of-the-art engineering facilities, which are designed to drive innovative research and strengthen Western Australia’s manufacturing, green energy, technology and mining industries. The facilities will deliver an enhanced focus on industry collaborations and discoveries, while offering real-world experience for the next generation of engineers. ECU Vice-Chancellor Professor Steve Chapman said the laboratories will provide exceptional new opportunities for industry partnerships: “Our facilities are aligned with both industry and the WA State Government's commitment to boosting local manufacturing and securing Western Australia's sustainable energy future.” The laboratories feature cutting-edge technologies and equipment, including Western Australia’s only GE Concept Laser metal 3D printing system in partnership with global mining company South32. “Combined with ECU’s world-class research and industry-focused expertise, these new laboratories aim to offer creative answers to our world’s most challenging and pressing questions,” said Chapman. “The laboratories reinforce our commitment to engaging with industry to provide remarkable outcomes for them but also delivering real-world experience and connections for our students.” The three laboratories include industry-grade tools and technology that will boost capabilities and research in a range of areas, including: • Advanced Manufacturing Hub. One of Western Australia’s leading facilities in 3D printing technologies and advanced additive manufacturing. The Hub will enable rapid prototyping and production of critical components in the manufacturing industry, lifting local skills and capacity. • Renewable Energy Lab. Featuring a comprehensive range of green energy infrastructure and grid control technologies, the lab enables frontier research into the integration and management of renewable energy sources to support
Australia’s green energy future. • Sustainable Energy and Resources Lab. With state-of-the-art technologies unique to Western Australia, the lab supports ground-breaking research into carbon capture and storage, and underground hydrogen storage systems to deliver solutions to the challenges facing the oil and gas industries. The laboratories strengthen ECU’s world-class engineering facilities, which have seen the School of Engineering ranked among the world’s best 175 universities in the 2022 Times Higher Education World Rankings. www.ecu.edu.au

Australia’s 11 best tech scale-ups crowned
Eleven of Australia’s best emerging technology companies have been crowned winners at the Australian Technologies Competition (ATC) national awards ceremony, held virtually from Melbourne on 26 October.
The ceremony was attended online by stakeholders in the innovation ecosystem from across government, private enterprise, the investment and scale-up community. This year’s winners included manufacturing company FormFlow, cybersecurity specialists Haventec, and telehealth solution provider Coviu, which also took the title of Australian Technology Company of the Year. Of the 11 winners, five – Coviu, iVvy, Plaetos, Goterra and Sound Scouts – were led by female founders, highlighting the growing representation of women in deep tech. Strong themes also included renewable energy, the circular economy, telehealth, bushfire resilience, emergency management, personal security and AI. This year’s winners were: • BlockTexx (NSW) – Circular Economy Award • Coviu (NSW) – Medtech & Pharma Award + Australian
Technology Company of the Year • FormFlow (VIC) Advanced Manufacturing Award • Goterra (ACT) – Food & Agribusiness Award • Haventec (NSW) – Cyber Security Award • iVvy (QLD) – Smart Cities Award • Microbiogen (NSW) – Energy Award • Plaetos (VIC) – Global Social Impact Award • Presien (NSW) – Mining Technologies Award • Sound Scouts (NSW) – Alumni Achievement Award • XDI Cross Dependency (SA) – Disaster & Emergency Award Patrick Mooney, Executive Chair of competition organiser Impact Tech Ventures, said: “We’re delighted to celebrate this year’s winners and also showcase Australia’s emerging diversity in tech. We aim to find the best Australian scale-ups, provide them with the best mentoring and growth support possible and connect them with relevant international partners. This year’s winners provide timely solutions to many of the most significant challenges and opportunities that Australia faces.” Entrants for the ATC go through a three-stage judging process, receive free mentoring, submit a concise business plan and take part in a highly rated International Growth Masterclass. They also have access to deep dive programs on key growth topics and key markets. The final step is a pitch in front of an independent panel of judges and a live audience. The 2021 ATC is sponsored by the Federal Department of Industry, Science, Energy and Resources, Victorian Departments of Environment, Land, Water & Planning and Jobs, Precincts & Regions, Accelerating Commercialisation, METS Ignited, the Australian Space Agency, IMCRC, AustCyber, FIAL, MTPConnect, NERA, NSX Australia and FB Rice. Partners include AMTIL, the CSIRO, SBE, LaunchVic, Cicada Innovations, MTAA, Heads Over Heels, HKTDC, WIT, NCTCE, Hatch Quarter, ACBC and AOEG.
www.austechcomp.com

ICN partners with Australian Made
Industry Capability Network (ICN) has joined up with the Australian Made Campaign as an Industry Partner, in support of a shared commitment to increased growth in Australia’s commercial and manufacturing sectors.
ICN provides manufacturers with connections, contacts and advice to help unlock opportunities across Australia and overseas. At its heart is ICN Gateway, which connects manufacturers to projects across Australia and New Zealand. A network comprising suppliers, buyers, government and market analysts, ICN Gateway helps Australian manufacturers access new opportunities. By creating a profile on ICN Gateway, Australian Made licensees can be listed on a publicly searchable database, search project opportunities and submit expressions of interest for individual projects. This database also provides a hub for project owners to identify potential suppliers, including Aussie manufacturers. With a number of ICN subscribers already proudly showcasing the green and gold Australian Made logo on their ICN Gateway business profile, the establishment of a formal industry partnership works to foster a stronger local manufacturing environment. Warren Jansen, Executive Director of ICN Limited, said ICN’s core purpose lay in its desire to provide manufacturers with opportunities to grow and expand: “Since being created over 30 years ago, ICN has helped local manufacturers find over $30bn worth of contracts to keep them working and growing. This partnership strengthens our work in fostering and supporting local manufacturers, ensuring the Australian manufacturing sector continues to be a driver of economic growth in Australia.” Ben Lazzaro, CEO of Australian Made, believes it has never been more important for Australian manufacturers to be supported, especially when venturing into new projects and markets: “With a renewed focus on bringing manufacturing back to Australia, the ICN Gateway provides local manufacturers with the opportunity to access new projects and expand their offering into new markets. Australian manufacturers produce products to some of the highest quality standards in the world. This partnership works to promote these Aussie makers and help them leverage their Aussie credentials both here and overseas.”
www.icn.org.au www.australianmade.com.au
IMCRC Design Robotics project wins Excellence in Innovation Award
The ‘Design Robotics for Mass Customisation’ team at the Innovative Manufacturing Cooperative Research Centre (IMCRC) has won the Cooperative Research Centre Association’s 2020 Award for Excellence in Innovation.
The award recognises outstanding research collaborations that address industry-specific problems for the benefit of Australian industry and the economy. With funding from IMCRC, Brisbanebased company Urban Art Projects (UAP) embarked on an $8m robotics research project in partnership with Queensland University of Technology (QUT) and RMIT University in 2017. By investing in robotic vision systems and developing smart user-interfaces, UAP streamlined its ability to manufacture bespoke artwork and architecture pieces in Australia. As part of the project, UAP also opened its factory to local manufacturing SMEs to share research outcomes and education on how robots and other emerging technologies can assist in manufacturing high-value products. This ‘open innovation’ approach led to the formation of the Advanced Robotics for Manufacturing (ARM) Hub in Brisbane. QUT Associate Professor Jared Donovan, who accepted the award on behalf of the Design Robotics team, thanked all participants: “In the IMCRC Design Robotics project, we set out to ‘Make Robots See’ – to combine the power of robotic vision and design-led manufacturing to enable highly custom and bespoke manufacturing. As a researcher, it has been an absolute honour to have worked with such a fantastic industry partner as UAP. I also want to thank the teams at IMCRC, RMIT and QUT. Without you this would not have been possible.” Matthew Tobin, Founder and Managing Director of UAP, said the project had been transformational for UAP: “The outcomes and cultural change that working with QUT, RMIT and IMCRC has delivered to UAP have fundamentally changed the way we think about manufacturing and will continue to influence our digital transformation in the years to come. We think about the University staff as explorers, and we think about the IMCRC framework as a discipline. Both those things add great value to our transformation journey.” David Chuter, CEO and Managing Director of IMCRC, congratulated the Design Robotics team on their achievement: “The Excellence in Innovation Award is a well-deserved acknowledgment of UAP’s bold move to break with design manufacturing tradition, and the Design Robotics team that pushed so many boundaries by pairing human creativity with the efficiency of robots. With many CRC projects, you only start to see the impact years later. The Design Robotics project is different; not only has it already helped UAP to achieve a greater competitive advantage, but also by being the catalyst for establishing the Advanced Manufacturing in Robotics (ARM) Hub where manufacturers can explore robotics and designled manufacturing.”
www.imcrc.org www.cooperativeresearch.org.au
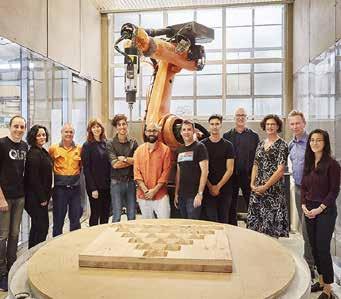
BOC and Redkite: A partnership that stands the test of time
AMTIL member BOC was the first corporate to partner with children’s cancer support charity Redkite, back in 1998.
Today the partnership is stronger than ever and has made a real impact on childhood cancer support in Australia, helping fund critical emotional and mental health support, financial assistance, and information and resources to help families throughout the long and traumatic cancer experience. Over the 23-year partnership, BOC has raised more than $2.4m for Redkite. “Redkite and BOC have always had a similar philosophy, based on providing practical help when it’s most needed, as well as a deep commitment to community and looking after families who are doing it tough,” said Monique Keighery, Redkite’s CEO. “BOC’s generosity over the years has helped us achieve significant change that has made a real impact on the lives of children and their families.” BOC offers an innovative employee giving program, Hero time, which allows team members to take leave and donate the leave pay for those hours to Redkite. Employees are also encouraged to take part in Redkite fundraisers, such as Redkite’s first national Sun-Up Challenge, for which BOC was headline sponsor. In 2020, during the COVID-19 pandemic, BOC implemented a virtual Wellbeing Event. Employees around the country pledged to complete a physical activity and BOC matched their entry fees and paid $5 for every kilometre completed. The Wellbeing Event was such a success that it ran again in 2021, this time with BOC paying $1 for every minute completed. BOC raised more than $25,000 for Redkite through this initiative alone. One particularly passionate employee is Melbourne-based Andrew Wesley, Reliability and Improvement Manager for BOC South Pacific. The keen triathlete and kayaker has undertaken some amazing personal challenges for a good cause, including the New York Marathon. “Life is about the memories and friendships you make along the way and fundraising for Redkite via the NYC Marathon has given me some of the very best,” says Andrew. “Not just the event but the people I met and interacted with along the way – people from Redkite, from within my local community, and within BOC, who have all been amazing in their generosity, support and sincerity. The fundraising gave me an additional purpose. It made me feel valued, appreciated, and filled me with an enormous amount of gratitude.”
www.boc.com.au www.redkite.org.au.
BOC’s Redkite team running the New York Marathon, with Andrew Wesley on the right.

G R E E N T E C H N O L O G Y F O R T H E WAT E R J E T I N D U S T R Y
only60AMP
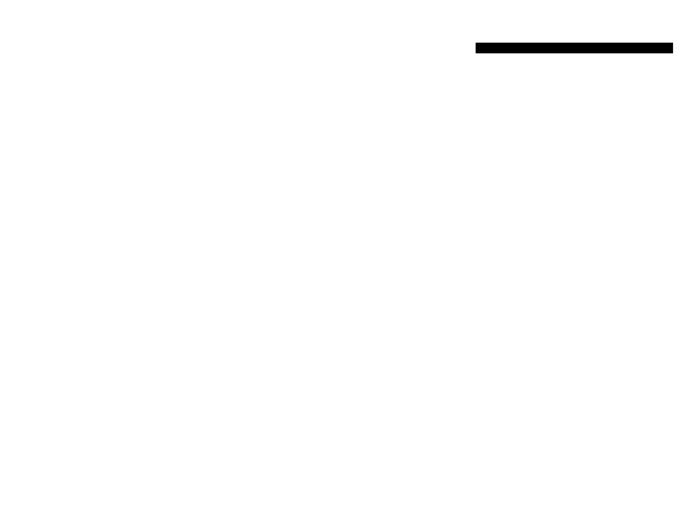
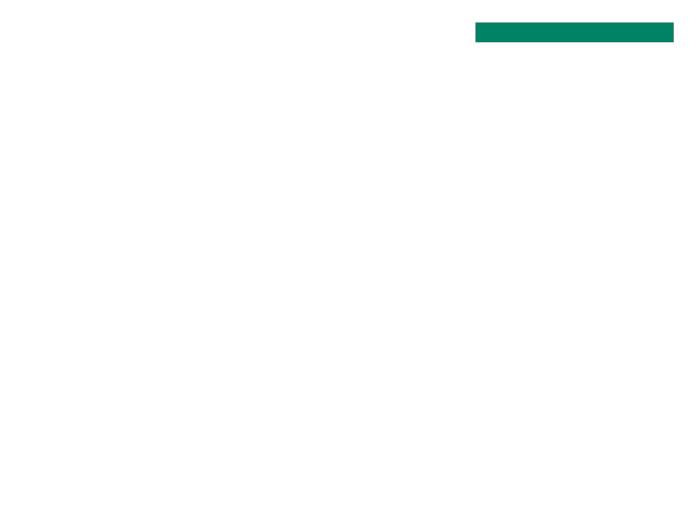
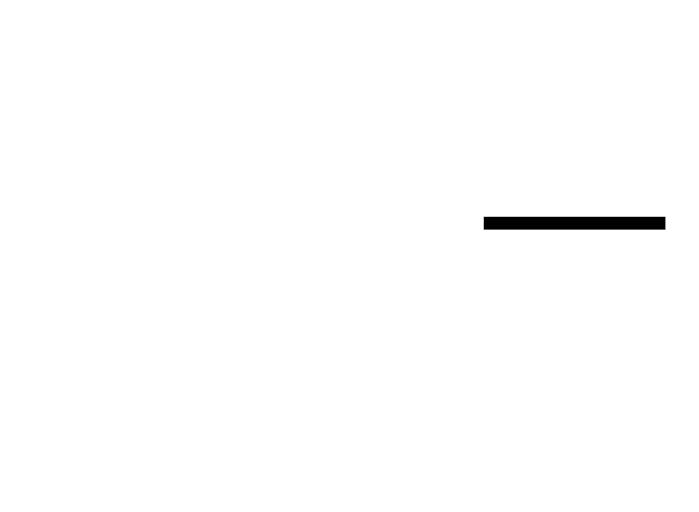
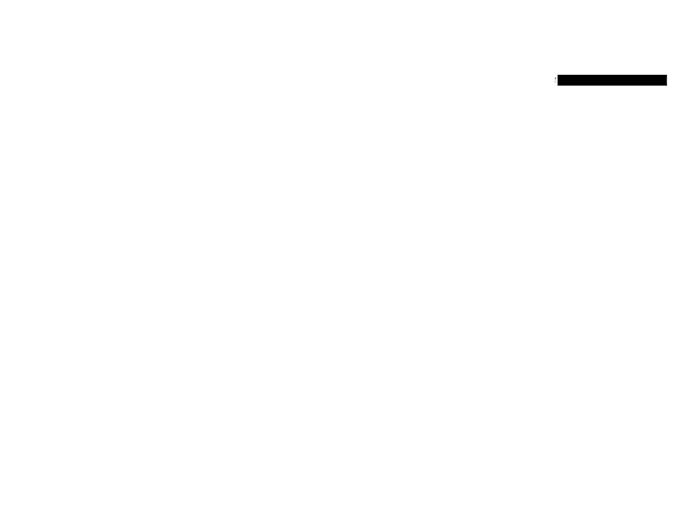
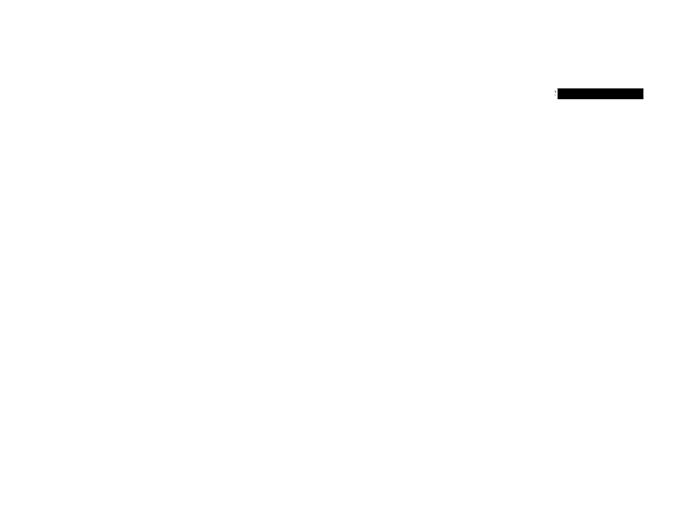
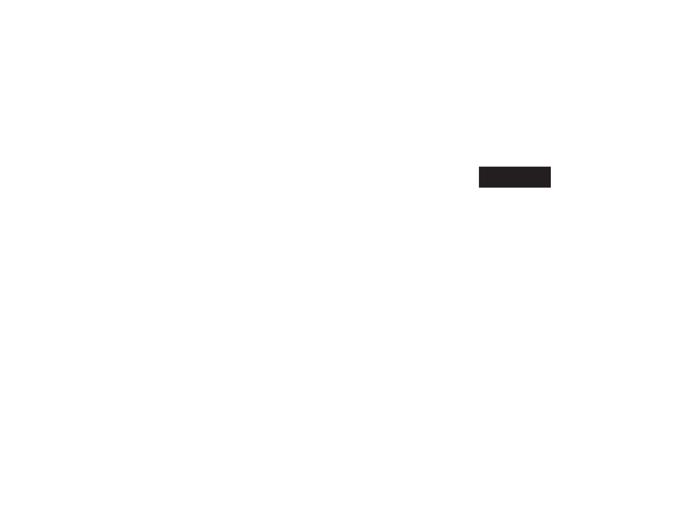
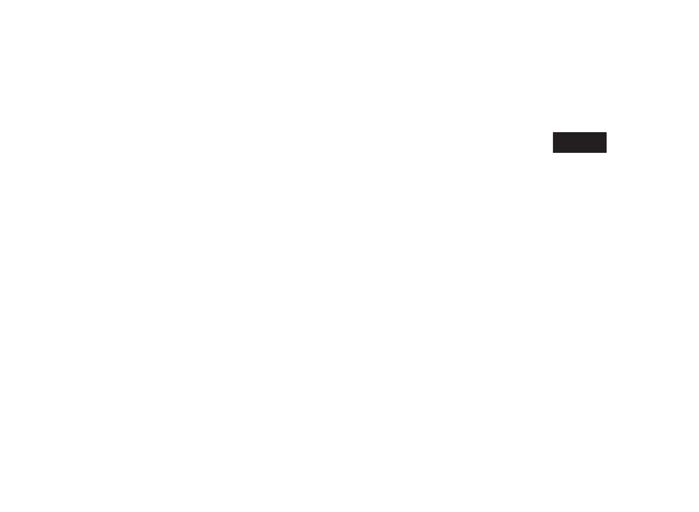
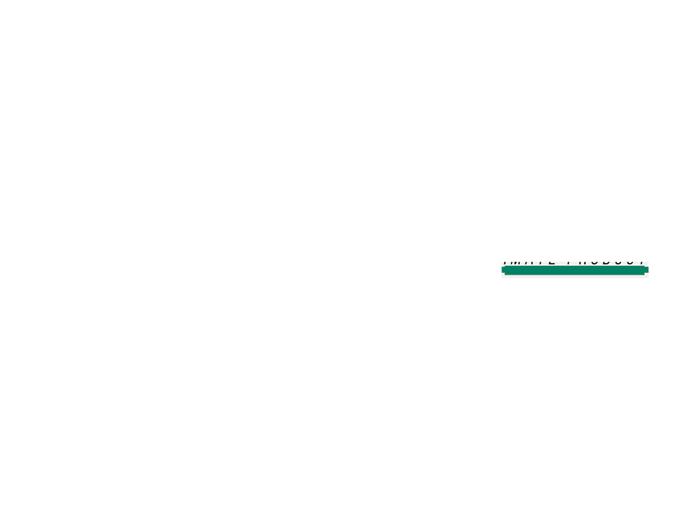
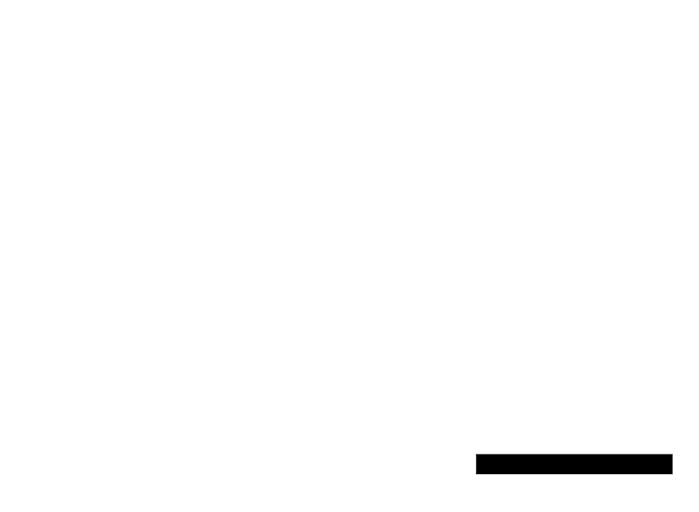

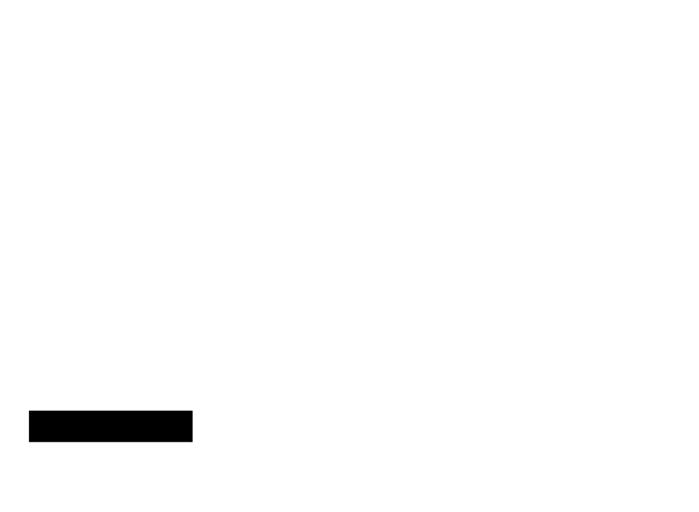
inletrequired
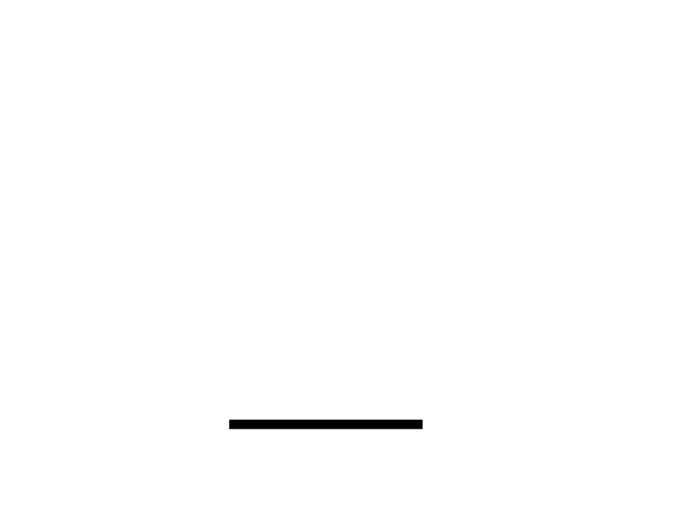
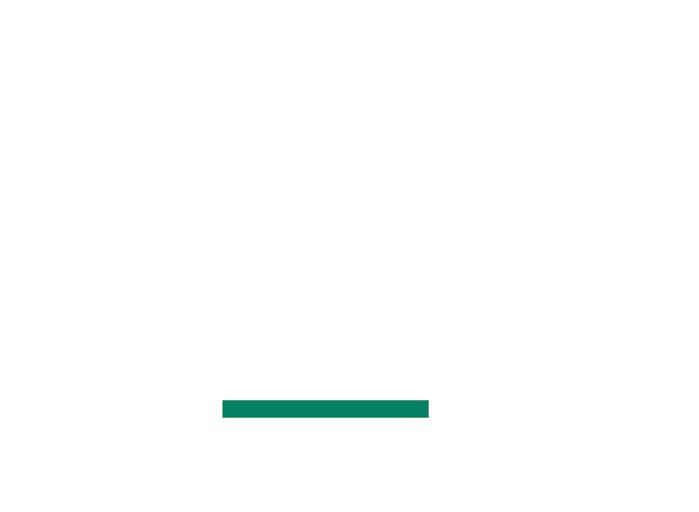
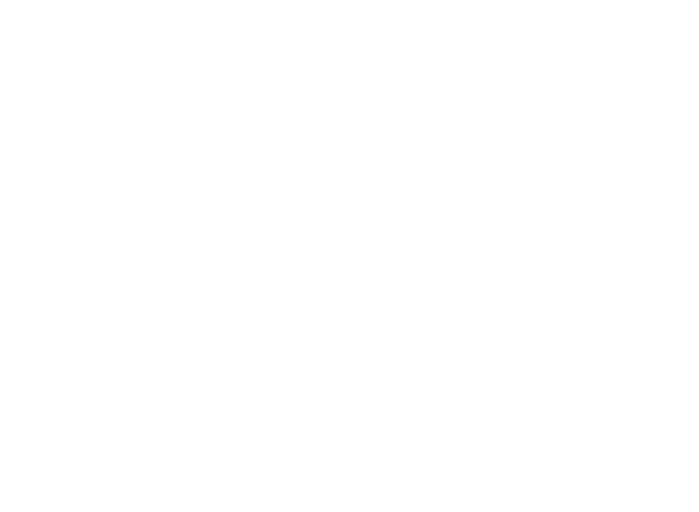
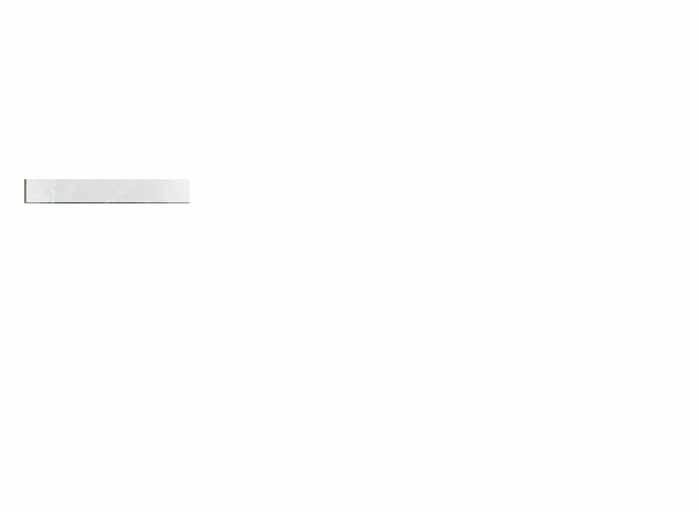
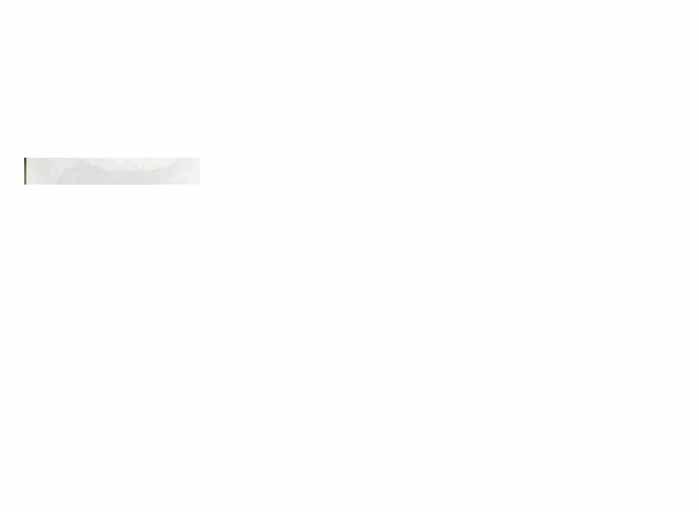

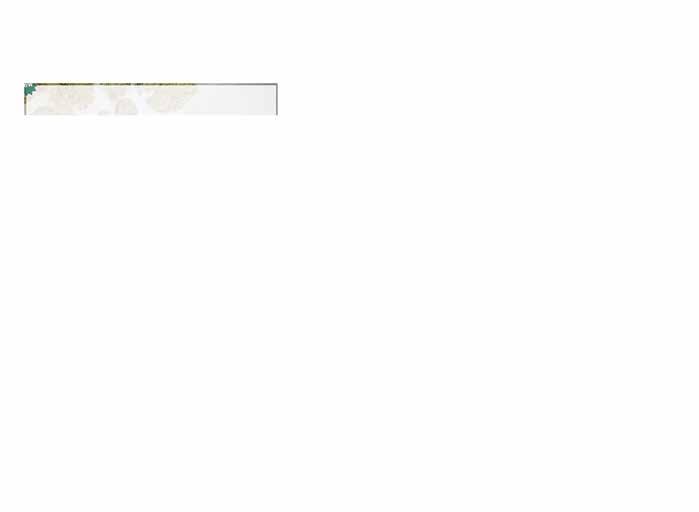
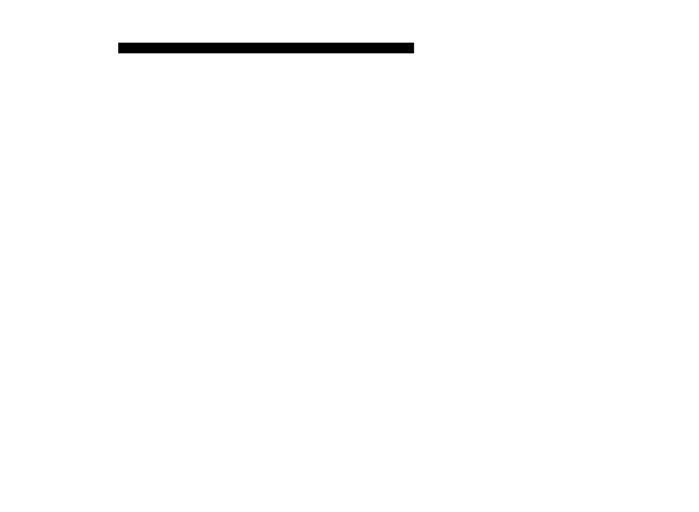
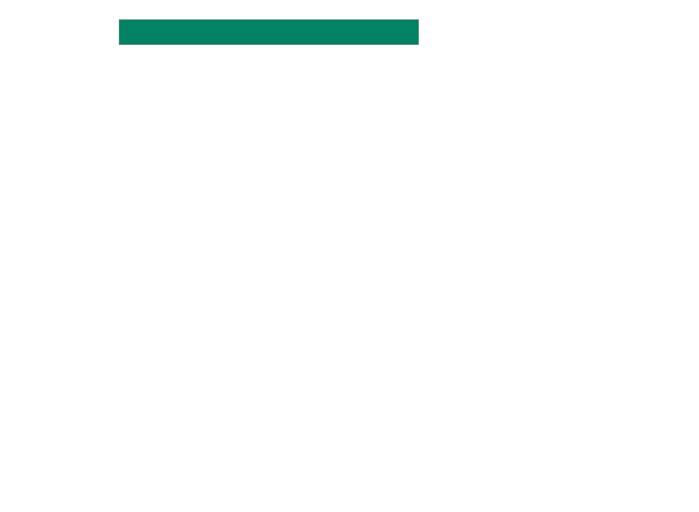
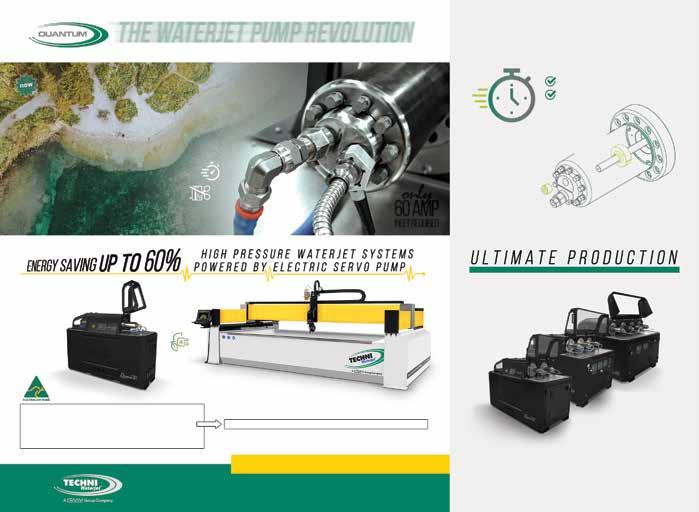
T O T H E S E A L A N D C H E C K V A L V E S
Access check valves in <1min Access seals in 10 min
Quick Change SEAL DESIGN
External Cartridge CHECK VALVES
Greatest lifetime of hyper-pressure components
D U A L T R I P L E Q U A D
Switch to electric pump technology for your exissng waterjet, or purchase a complete new Techni waterjet system.
Instant Asset Tax Write-Off
G O V E R N M E N T I N C E N T I V E VA L I D U N T I L 3 0 t h J U N E
CONTACT US TO GET A QUOTE
AVAILABLE IN 66,000 PSI AND 88,000 PSI VERSION MAX OUTPUT VOLUME from 6.0 LPM to 16.7 LPM
Victoria: Funding boost for defence industry’s digital future
The Victorian Government has unveiled new support for Victorian defence industry companies to transform their operations by deploying digital technologies.
Minister for Industry Support and Recovery Martin Pakula in October announced the $1.36m Smart Enough Factory program that will support small-to-medium-sized businesses in Victoria’s defence industry to modernise design and manufacturing processes. Delivered by DMTC Limited (formerly the Defence Materials Technology Centre), the Smart Enough Factory program will assist participating businesses to adopt digital technologies, overcome barriers such as costs, skill shortages or security vulnerabilities, and create opportunities to enter defence supply chains. With an aim to boost digital and Industry 4.0 capabilities, the program uses advances in data-driven production to enhance businesses’ operational performance and manufacturing productivity, leading to more efficient processes and significant cost savings. The pilot program is underway with Victorian small businesses Australian Precision Technologies, AW Bell, Ronson Gears, APV Corporation and Heat Treatment Australia. The fullscale program will run from the end of the year for an initial period of three years, with up to 20 Victorian defence businesses each year to reap the benefits of the program. The program will also take on up to eight undergraduate or postgraduate interns a year from Victorian universities through a scheme administered by the Defence Science Institute (Victoria) to provide technical support, offering them valuable work experience, defence industry exposure and possible future employment. By embracing advanced technology, the program will ultimately boost participating businesses’ prospects of participating in multi-billion-dollar defence programs, meaning more jobs and investment for Victoria’s defence sector. “We’re supporting our defence industry to become ever more responsive, adaptive and connected – ensuring we lead the way in advanced manufacturing, innovation and technology,” said Minister Pakula. “This program will help defence businesses to grow and transform, supporting jobs and economic growth and cementing Victoria’s status as the advanced manufacturing capital of Australia.” DMTC Limited Chief Executive Dr Mark Hodge added: “This program is not just about getting companies to the starting line, it’s about putting companies in a better position to compete and win work. It’s about tangible actions to put industrial capability in Australian hands.” Victoria’s defence sector contributes up to $8.4bn to the state’s economy each year, employing around 24,000 people in 6,300 businesses that manufacture equipment and provide services for defence activities.
Victorian businesses can express interest in the program at: dmtc.com.au.
Queensland: $7.1bn bid to become train building powerhouse
The Queensland Government plans to deliver the largest investment in train infrastructure in the state’s history to create jobs and rebuild the economy.
Premier Annastacia Palaszczuk on 20 October announced $7.1bn to boost the state’s train manufacturing industry and build and operate 65 trains, transforming Queensland into Australia’s rail manufacturing powerhouse. Delivering the Rail Expansion Program is projected to create up to 3000 jobs in construction and manufacturing across Queensland in the lead-up to the 2032 Olympics. “We’re investing in manufacturing to create long-term, secure jobs in regional Queensland,” said Palaszczuk. “At the election, we committed $600m to build 20 new trains in Maryborough. It’s now clear we’ll need a full complement of trains to cater for growth in years to come. That’s why we’re committing to build all 65 trains, right here in Maryborough. My government is making great progress on Cross River Rail - building Brisbane’s first underground rail system. Manufacturing the trains is the next step.” Treasurer Cameron Dick added that investing in Queensland-made trains would create long-term quality jobs for many years to come: “This investment in publicly-owned manufacturing facilities will support thousands of jobs well into the future. Importantly, this commitment will include minimum local content requirements, along with the best industry standards, meaning we’re supporting Queenslander workers.” Under the plan, the 65 six-car passenger trains will be built in Maryborough for use on the South-East Queensland rail network. The trains will be built in a $239m purpose-built manufacturing facility to be constructed at Torbanlea, north of Maryborough. Transport and Main Roads Minister Mark Bailey said the rail investment would lock in secure jobs and training opportunities for a generation of Queensland workers: “We are delivering a pipeline of work over the next decade that will support up to 800 construction and manufacturing jobs here in Maryborough. First, we will construct a purpose-built, publicly-owned train manufacturing facility at Torbanlea. Not only are we delivering trains, this $7.1bn investment includes new rail infrastructure in the South-East and ongoing maintenance of Queensland’s newest fleet.” Under the Rail Expansion Program, three train manufacturers are competing for the existing contract to build 20 trains in Maryborough and will have an opportunity to bid for the increased order for 65 trains. Those companies are train manufacturers Alstom, CAF and Downer Rail. A preferred supplier to build the 65 trains is expected to be named in the second half of 2022, with construction of the Torbanlea train building facility to follow. The investment will also mean Rockhampton will be part of the supply chain to build trains in Maryborough. Cross River Rail is on track for first services to begin operating in 2025. www.qld.gov.au
Western Australia – $1m boost for medical products manufacturing
A new voucher scheme from the MTPConnect WA Life Sciences Innovation Hub will see a major boost for medical products manufacturing in Western Australia.
Under the scheme, five Western Australia-based companies have been awarded a total of $450,000 to accelerate innovation projects requiring advanced manufacturing capabilities. Matched with cash co-contributions of $600,000, the initiative is injecting more than $1m into WA’s medical technology, biotechnology and pharmaceutical sector to drive job creation and economic growth. Awardees include: • OncoRes Medical Pty Ltd. With a focus on improving the accuracy of breast-conserving surgery, OncoRes Medical is driven by a mission to eliminate repeat operations after breast conserving surgery. OncoRes Medical is developing key preproduction manufacturing activities in WA, advancing their development of a novel diagnostic imaging system that guides surgical clearance of cancer in breast conserving surgery. • Proteomics International Pty Ltd. Established in 2001,
Proteomics International is recognised as a leader in the field of proteomics, developing and commercialising diagnostic tests for chronic diseases. The company is developing WAbased manufacturing capability of the PromarkerD diagnostic, which can predict the onset of diabetic kidney disease in patients with Type 2 diabetes. • SynGenis Pty Ltd. Perth start-up SynGenis was established in late 2020 and now operates a large facility in Bentley
Technology Park to manufacture high quality oligonucleotides (DNA and RNA) for the Australian and New Zealand market, and international customers. The company is seeking to expand their existing oligonucleotide manufacturing capabilities in WA to include ISO and GMP certification. • VeinTech Pty Ltd. VeinTech aims to eliminate the guesswork associated with cannulation, the most common invasive medical procedure. Their solution is a handheld ultraportable proof-of-concept prototype developed in partnership with a
WA-based manufacturer to assist with visualising veins. • VitalTrace Pty Ltd. Committed to empowering obstetricians and midwives to deliver the greatest outcomes for their patients, VitalTrace is developing a highly accurate biosensor to improve the safety for mothers and babies during childbirth.
The voucher will support key pre-production manufacturing activities in WA. MTPConnect Managing Director and CEO, Dr Dan Grant, congratulated the five successful companies. “Manufacturing medical products is a national priority so we’re supporting these promising projects to develop their medical devices and diagnostics,” said Dr Grant. “Each project is aiming to improve the health and wellbeing of Australians and if we can help them along the commercialisation pathway through our voucher initiative, these companies will also continue contributing to the state’s burgeoning innovation ecosystem.” The voucher initiative, announced by Health and State Development, Jobs and Trade Minister Roger Cook MLA, is being made available through the MTPConnect WA Life Sciences Innovation Hub, which is co-funded by MTPConnect, the University of Western Australia and the WA Government through the New Industries Fund. All projects are due to be completed by 30 May 2022.
www.mtpconnect.org.au
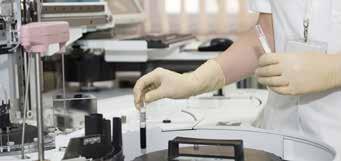
Tasmania – New space tech fund announced
The Tasmanian State Government is supporting local businesses to explore and enter the fast-growing space economy, which is set to grow nationally to $12bn and add 20,000 more jobs by 2030.
Michael Ferguson, Minister for Science and Technology, on 12 November announced the Tasmanian Space Technology Seed Fund, which will co-invest with businesses to adapt, extend or develop new technology and services for the space economy. Launching in the first quarter of 2022, the $500,000 fund will provide two rounds of competitive, matched grant funding to eligible Tasmanian businesses, including start-ups. “This is a great opportunity for Tasmanian businesses to enter an industry that captures the imagination like no other,” said Ferguson. Following the signing of an MoU with the Australian Space Agency in late 2019, the Tasmanian Government has strengthened its space research infrastructure capabilities in the fields of Space Domain Awareness, Space Medicine and Life Sciences through key partnerships with business and academia. The next step in the plan will seek to propel Tasmania’s industries into space by driving innovation, developing local space capabilities, increasing investment in R&D, and creating new STEM and highly skilled jobs.
Further details of the fund, including guidelines will be announced in the New Year. www.tas.gov.au
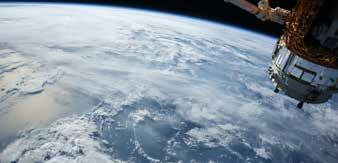
WHERE TECHNOLOGY MEETS INNOVATION
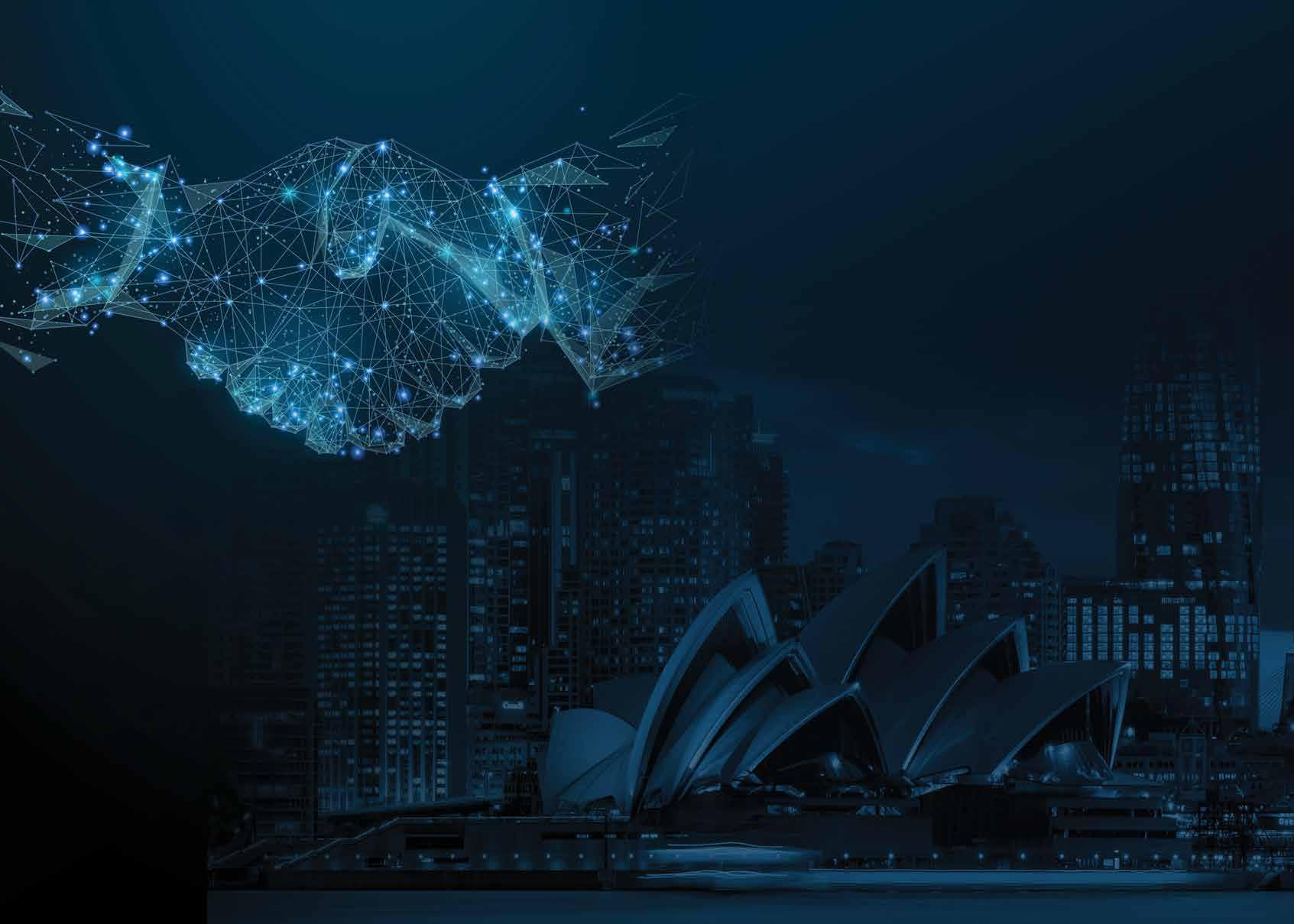
Australian Manufacturing Week is proudly owned and operated by AMTIL
www.amtil.com.au
AUSTRALIA’S PREMIER MANUFACTURING SOLUTIONS EVENT
SHOWCASING THE LATEST IN MANUFACTURING TECHNOLOGIES AND PROCESSES ACROSS 6 PRODUCT ZONES
AUSTRALIAN MANUFACTURING WEEK is the industry exhibition encompassing all aspects of manufacturing in Australia. AMW will showcase the latest in manufacturing technologies and processes, with a strong focus on innovation and digital transformation. AMW will be a week-long celebration of manufacturing in Australia today.
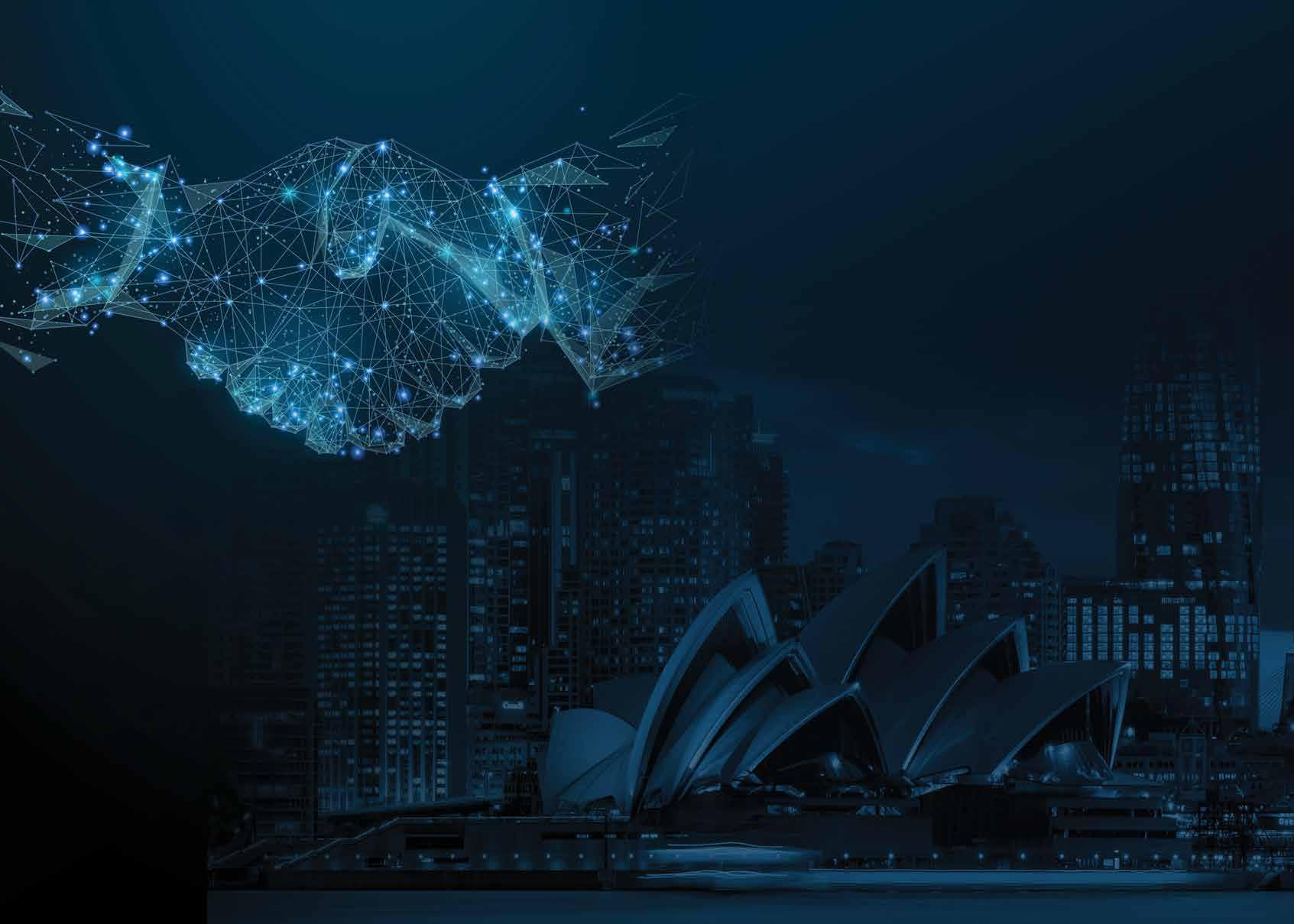
For more information visit WWW.AUSTRALIANMANUFACTURINGWEEK.COM.AU
SYDNEY: 7-10 June, 2022 INTERNATIONAL CONVENTION CENTRE SYDNEY
1585AMW/AMTDECJAN22