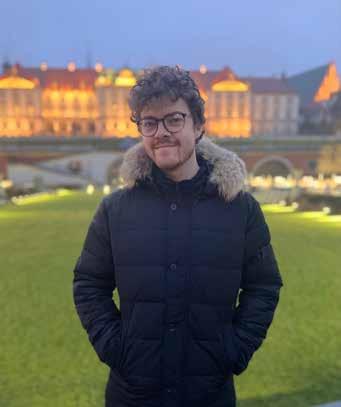
14 minute read
Where can F1 in Schools take students?
from AMT DEC 2021
by AMTIL
Where can F1 in Schools take students? A remarkable (young) Australian story
Thomas Agars lived and breathed the F1 in Schools Technology Challenge throughout his secondary education from 2008 to 2012. In 2012 he was a member of the World Championship winning team “Cold Fusion”, with whom he manufactured and raced the record-setting car.
At a very young age, Thomas knew he was born to be an engineer. Using the spare material found in his father’s shed, Thomas would construct anything and everything, using his ability to observe existing designs and recreate them. From remote controlled cars/ aircraft to bridges and everything else in between. There was always an ongoing project for him to work on. It therefore seems inevitable that Thomas would be drawn to the F1 in Schools STEM Challenge. Established by the Re-Engineering Australia Foundation (REA Foundation) in 2003, F1 in Schools is the world’s foremost student competition for Science, Technology, Engineering and Mathematics. Each year more than 17,000 schools in 51 nations take on the challenge of developing the world’s fastest miniature F1 car. “After meeting the head technology teacher, Stephen Read, during a Brighton Secondary School open day, I was immediately drawn towards the F1 in Schools challenge,” Thomas recalls. “I would stay at school, alone at first, for as long as I could, teaching myself how to use CATIA V5, designing ‘my first car’. I quickly picked this up and before long I was leading the design of cars competing in the national competition. “At first, it was a struggle, as the level of competition within Australia alone is phenomenal. After several years of near wins, I took away unique learning experiences each competition. Above all else this experience taught me the importance of teamwork and collaboration.” Among his peers in the 2012 champion team “Cold Fusion”, Thomas became known for pushing the limits within the competition, innovating, and approaching every problem with enthusiasm. As a testimonial to Thomas’ out of the box thinking, during his final year of competition he explored new ways to squeeze every ounce of performance out of the car. One innovation was to exploit a loophole within the regulations to include an articulated nozzle towards the rear of the car to maximise forwards acceleration. At the time, this had never been seen in the competition, and improved the lap times significantly. In the following years, other teams from all around the globe successfully implemented them, synonymous to the KERS (Kinetic Energy Recovery System) technology used in real F1 cars. For several years, teams developing KERS repeatedly broke speed records, a team from Brighton Secondary School being the current world record holders. “I believe I can speak on behalf of all F1 in School alumni that this learning experience isn’t easy to convey via traditional textbook teaching,” Thomas adds. “However the F1 in Schools challenge nails it on the head.” F1 in Schools – A significant value proposition
Through his success in the F1 in Schools challenge in 2012, Thomas was awarded a full scholarship to complete a Masters of Aeronautical Engineering at the City University. He was one of the first Australian recipients to take up this scholarship, traveling halfway around the globe as a 19-year-old to set up a new life in the UK. As a freshman student at City University, he was picked out by the leaders of the Formula Student team ‘City Racing’ to assist with the manufacture of their car. On top of Thomas’ talent, he also proved
Thomas Agars is now seeking fresh opportunities in the aerospace industry in Australia.
to be resilient in character. To sustain the significant living costs of London, he worked night shifts at the local pub. Later in his degree he was able to support himself by working as a research assistant within the university’s transonic wind tunnels. “By far the most valuable learning experience during my studies was actually just the act of living independently abroad with all of the challenges that presented me,” Thomas remarks. “It provided the catalyst to which I developed my character and multi-cultural perspective on the world. Because of my time abroad, I have made friends from all over the world. “It was about this time, 2015-2016, that I started really taking notice of the developments made by SpaceX, successfully vertically landing their Falcon 9 rocket. I was absolutely awestruck, I knew that this is where I wanted to end up, working in the aerospace industry. Thankfully, my trajectory within my education was nominal and on course to this goal. “However, I also wanted to expand my problem-solving ability by learning essential programming skills within Python, Arduino and MATLAB. I did this through a series of self-lead projects, and implemented custom AOA sensors within my work at City University. In addition to my formal education in aeronautical disciplines, I found myself absorbed in orbital mechanics and space vehicle design.” Thomas graduated in 2018 with first-class honours, topping his class. In his final year, his exceptional design and CAD skills became very apparent when he successfully led the design of a fixed-wing unmanned aerial vehicle (UAV) to compete in the British Model Flying Association (BMFA) competition. The UAV is now on display within the aeronautical labs at City University to set a topquality example for future students.
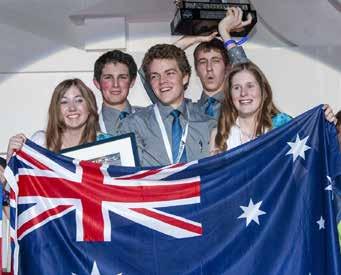
Thomas (centre) with F1 in Schools World Championship winning team “Cold Fusion” in 2012.

The F1 in Schools STEM Challenge sees teams from schools all over the world compete to develop the world’s fastest miniature F1 car.
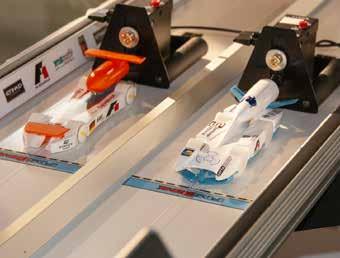
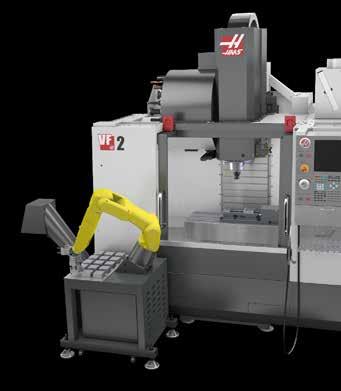
Thomas maintains that all these accomplishments had their origin in his participation in F1 in Schools: “For starters, the opportunity to study abroad was only possible because of my involvement with F1 in Schools. Moreover, the technical and collaborative foundation the challenge provided has shaped my development ever since.” Fast forward two decades and Thomas’ childlike curiosity and need to learn remain one of his core qualities. Since completing his tertiary studies, he has spent two years working in the UK for a clean-tech start-up called Gyrotricity, developing renewable and rapid electric vehicle charging technology. “I consider myself very fortunate to have had all these opportunities, the last two years being no exception,” he says. “I have been able to seriously expand my professional skillset at Gyrotricity. Embracing the start-up mindset, starting from nothing, building up core technology from the conceptual phase right through to manufacture and commissioning, I have been involved in all steps along the way. There is something so exciting about being dropped in the deep end and rising to the challenge.” Thomas is now back in Australia seeking fresh opportunities in the country’s rapidly growing aerospace industry. “Long-term my goal is to become an industry-leading engineer in the 21st Century space boom,” he concludes. “With so many new aerospace initiatives within Australia, I am confident it is the place to be right now. I cannot wait to see what the future brings, and I hope to be a part of the success I am sure Australia will experience in the space industry.” www.rea.org.au
Everything you need to start automatically loading & unloading parts –in a couple of hours, not days.
Plug-and-play capabilities to: • Haas small vertical machining centers • ST-10 through ST-25 turning centers
Haas Robot Package-1 The Haas Robot Package-1
An all inclusive, 7 kg robotic automation solution for your Haas machine.
The fully integrated HRP–1 system includes:
• FANUC LR Mate 200i D, 7 kg cap., 6-axis robot arm • Base stand and parts table • Robot electrical interface box • CE-compliant safety guard fencing • End-of-arm parts gripper
(single gripper standard; double gripper available) • Part spring pusher
✓ No complex connections ✓ No third-party integration ✓ Direct Haas Control
Visit haas-australia.com, or call 1300 20 12 30 for more information.
A Division of Alfex CNC Australia
Configure and price the perfect Haas solution for your shop today at www.haas-australia.com
Deakin’s new vehicle simulator – from virtual prototyping to virtual testing
Deakin University aims to accelerate Australia’s vehicular technologies into the future with the world’s most advanced Next Generation Motion Simulator and automotive design and testing platform.
Opening in the first half of 2022, the Simulator will provide compelling virtual worlds for vehicle development engineers and expert drivers in test and evaluation of new vehicle designs. Additionally, the associated infrastructure will allow advanced virtual vehicle prototyping design and testing, driver training, and automotive research and development. Deakin Vice-Chancellor Professor Iain Martin and Deputy Vice-Chancellor for Research Professor Julie Owens welcomed the announcement of $5m in funding from the Victorian Government for the new platform. Professor Martin said the Next Generation Simulator will provide the first dedicated and most advanced research infrastructure for driver-based and autonomous mobility technologies in Australia. “This is an exciting initiative and a powerful demonstration of what can be achieved when academia works collaboratively with government and industry partners,” said Martin. “This crucial infrastructure project will position Geelong as a global leader in the industry and make a substantial contribution to Deakin’s deep commitment to the economic and social development of regional Victoria.” Professor Owens said the Next Generation Simulator will help build a highly skilled Victorian-based workforce in advanced mobility technologies through the creation of new markets and export opportunities: “Deakin is a local university with global impact. Together with our partners, we translate our research into commercial, economic and social outcomes that help improve the future opportunities of our communities. “The platform will be an important addition to the world-class motion simulation facilities at Deakin’s Institute for Intelligent Systems Research and Innovation (IISRI) on our Waurn Ponds Campus, and will offer a unique asset to researchers, manufacturers and students in Victoria and Australia more broadly.” According to Professor Saeid Nahavandi, Director of IISRI and the Next Generation Simulator project leader, IISRI is the ideal home for this development: “IISRI has a proven track record of developing strategic partnerships including with over 500 business, industry and government agencies around the world. In addition to cost-effective virtual vehicle design, test and evaluation by automotive experts, we’re pleased to provide internship opportunities and bespoke motion technologies training for higher education students and industry partners alike.” Existing Deakin partners including Ford, Qantas and smaller technology providers are expected to use the facilities to expand their skills in simulation, generate IP and develop next generation prototypes. This will anchor further jobs in Geelong as the facility will assist Ford Australia to become the global vehicle design, test, and evaluation hub for multinational Ford Motor Company. Furthermore, small and medium enterprises (SMEs) will be offered access through a dedicated engagement program to the cuttingedge simulation technologies, consulting and expert services, and engineering support to expediate their growth into internationally competitive businesses. The new facility is expected to extend motion simulation technology-based research and innovation into new applications from road safety to shipping, helicopters and fixed wing aircraft. www.deakin.edu.au

Kinetic to bring all-electric buses to Melbourne
Melbourne-based company Kinetic has been awarded a $2.3bn contract that will introduce 36 electric buses to the Melbourne’s public transport network.
Kinetic will introduce 36 fully electric buses to the network by mid-2025, including five by June next year to jumpstart the State Government’s pledge for all new public transport buses to be zero emissions from 2025. More than half of the franchise fleet, 341 of the 537 buses, will be replaced with low- or zero-emission vehicles over the term of the franchise. The new environmentally friendly electric and hybrid buses will be made at Volgren’s Dandenong South facility, supporting jobs, boosting the local economy and helping to build Victoria’s engineering, design and manufacturing expertise in these emerging technologies. A minimum fleet target of 60% local content will apply to the electric and hybrid buses. Learnings from the early introduction of electric buses will add to the findings of the State Government’s threeyear, $20m Zero Emissions Bus Project which will start early next year. “We are jumpstarting our push for a zero-emissions bus fleet in Victoria to benefit the environment and help build our engineering, design and manufacturing expertise in these emerging technologies,” said Public Transport Minister Ben Carroll. “The roll-out of 36 electric buses early on in this partnership will accelerate our pledge for all new buses from 2025 to be zero emissions and, importantly, will contribute to the learnings of the three-year Zero Emissions Bus Project.” Kinetic, which operates SkyBus and runs local bus routes across Australia and New Zealand, will operate a third of Melbourne’s metropolitan bus network under the new contract. Kinetic bought SkyBus in 2014 and now operates urban, regional, school and airport bus services across Australia and New Zealand. Adam Begg, Co-CEO of Kinetic, commented: “With a leadership team that has grown up catching buses in and around Melbourne, this is an incredibly exciting announcement for us to partner with the Victorian Government to modernise the city’s bus experience and deliver benefits to the whole community.”
www.wearekinetic.com
Demmeler unlocks creative possibilities for renowned car restorer
Renowned car restorer Brian Tanti uses his Demmeler table system from Leussink Engineering in numerous ways, including holding and fixing, as well as for hammer forming parts.
“It allows me to be really creative,” explains Tanti. “The more I use it, the more uses I find for the Demmeler table. For me, it’s the product that keeps on giving. As well as holding and fixing, I also use the matrix of the table to help with design. It enables me to 3D print tools and then copy them into the matrix of the table. I’ve also used it as a makeshift milling machine by clamping a magnetic welder to it.” Tanti first discovered Leussink’s Demmeler table system several years ago when he was setting up a workshop for his then-employer Lindsay Fox. When he parted ways with Fox in 2018 after 30 years, he contacted engineering company Leussink to assist with the setup of his own workshop in the Sydney suburb of Artarmon. Brian Tanti’s Workshop, as his business is now known, was looking for a versatile fixturing table system to hold and fix parts in place, and called on Leussink to assist. Brian Tanti’s Workshop restores old cars that can be valued up to $9m, so Tanti’s work requires him to produce parts and repairs of a very high standard. All of the work is completely bespoke. Tanti creates replacement parts from scratch using wooden formers, which he designs the structure around. As such, he needs tools and equipment that are accurate and dependable. Before he discovered the Demmeler table system, Tanti made do with the equipment that was available, including a rudimentary table that was designed for use in the automotive smash trade. Tanti is also a qualified coach builder, a trade that harks back to the days when wealthy people commissioned the building of a coach to be pulled by a horse. Tanti uses his coach building skills in hand-making parts for cars. “The Demmeler system holds the metal sheet in place while I give it form,” he says. “Back in the 1950s, 60s and 70s, there were a lot of handmade cars, so it’s quite authentic to be producing parts in this way. “From my experience of Leussink, they don’t just sell products and step away. The engineers at Leussink provide problem-solving capability and personal insights for my business. Their advice is really rich. They’ve also helped me with the digitising of 3D objects and then generating new parts. They recently assisted with the restoration of an old German power hammer, which adds a layer of authenticity when I’m restoring vintage German cars. “Many fellow car restorers who visit my workshop think that the Demmeler system is totally beyond their budget, but the basic table is really affordable for most situations and is so versatile that it pays for itself.”
www.leussink.com.au www.briantantisworkshop.com
LESS INPUT. MORE OUTPUT.
MITSUBISHI‘S 5 YEAR WARRANTY
AGR-eco
Mitubishi‘s exclusive AGR-eco technology reduces Nitrogen consumption by up to 90%, drastically cutting costs while maintaining processing speeds.
AI Assist Cutting
Mitsubishi’s AI automatically finetunes the cut conditions during processing by reading multiple cutting-head sensors, ensuring peak performance with no additional training or operator involvement.
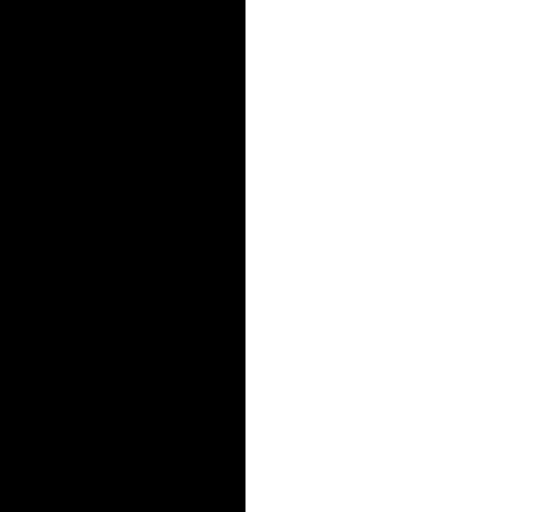
Conventional fiber laser processing systems
Running costs Profit
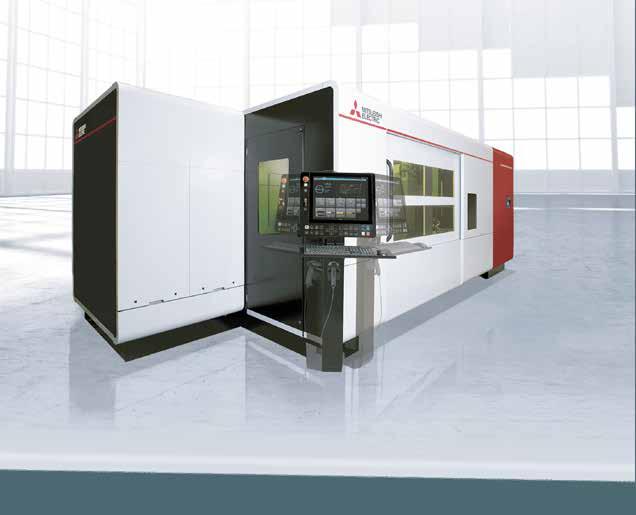
Productivity
Mitsubishi Electric’s GX-F ADVANCED Series
Running costs Profit
Productivity Real-Time Tracking of Electrical and Assist Gas Consumption
Custom Eco Modes
Advanced Gas Reduction (AGR-eco)
Mitsubishi Bar Code Scanner
The use of a unique job barcode and scanner allows anyone on the factory floor to begin job processing. Minimise additional costs associated with operator training and machine downtime with Mitsubishi.
CALL US TODAY: (03) 9115 1444
sales@kaizenmachinery.com.au www.kaizenmachinery.com.au