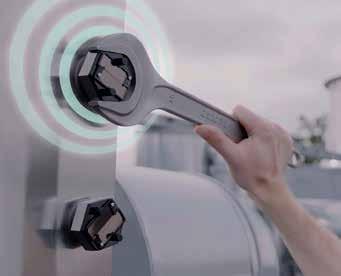
26 minute read
TECH NEWS: New and interesting technology
from AMT JUN/JUL 2022
by AMTIL
Germany: Smart screws keep infrastructure safe
Screw connections on critical infrastructures are exposed to major stresses and must be checked regularly. Researchers have developed a technology - The Smart Screw Connection - that allows the stability of the screw connections to be checked at any time by remote monitoring. It is a fully integrated, self-powered IoT device for determining the preload force. The data is transmitted wirelessly and is designed as a flexible, retrofittable system for DIN screws of various sizes. It comes with a screw fitted with a washer that is equipped with a piezoresistive DiaForce® thin film. When the screw is tightened, the pressure-sensitive sensors register the preload force at three points. Any change in the preload force changes the electrical resistance. When a screw comes loose, the resulting change in resistance is reported to a radio module located on the screw head. The radio module, in turn, sends the data to a base station. It can be adapted for a wide variety of applications.
Fraunhofer
The Smart Screw Connection is a fully integrated, self-powered IoT device for determining the preload force.
UK: Rail sensor goes ultrasonic to grease the wheels
Engineers are working on an ultrasonic sensor for the rail industry that can detect sections of track where vital lubrication has been worn away. The sensors will be embedded in the wheels of trains and will allow track conditions to be almost continuously monitored. In curved track, a special type of grease is applied between the wheel and rail to reduce wear but also the risk of derailment, whereby in some circumstances the wheel can climb up and over the railhead. This new measurement technology will provide an automated vehicle-mounted system that will communicate the presence of lubrication, and critically, locations where it is absent, thereby reducing maintenance costs and improving railway safety. Embedding ultrasonic sensors into the wheel provides the opportunity for continuous monitoring of lubrication effectiveness and allows preventative measures to be applied before problems arise.
The Engineer
US: How to print a robot from scratch: Combining liquids, solids
A team has established a strategy for using currently available printers to create materials that meld solid and liquid components – envisioning a future where a robot or stretchy electronic devices could be 3D printed via the press of a button. The researchers first designed a series of computer simulations that probed the physics of printing different kinds of materials next to each other. One of the big problems was how to keep droplets of solid materials from mixing into the liquid materials. The team established a set of rules to help them do that. The surface tension of a liquid can be used to support solid material, but it is helpful to pick a liquid material that is more dense than the solid material. Next, the researchers experimented with a real 3D printer in the lab. They loaded the printer with a curable polymer, or plastic (the solid), and with a standard cleaning solution (the liquid). Their creations were impressive: The group was able to 3D-print twisting loops of liquid and a complex network of channels.
University of Colorado at Boulder
A network of capillaries 3D-printed using a newly developed technique.
USA: Waterless dust removal for solar panels
The accumulation of dust on solar panels or mirrors is a significant issue — it can reduce the output of photovoltaic panels by as much as 30% in one month. But cleaning solar panels is estimated to use about 10 billion gallons of water pa. Attempts at waterless cleaning are labour-intensive and tend to cause irreversible scratching of the surfaces. Now, a team has devised a way of automatically cleaning solar mirrors in a waterless, no-contact system that could significantly reduce the dust problem. The new system uses electrostatic repulsion to cause dust particles to detach and virtually leap off the panel’s surface, without the need for water or brushes. To activate the system, a simple electrode passes just above the solar panel’s surface, imparting an electrical charge to the dust particles, which are then repelled by a charge applied to the panel itself. The system can be operated automatically using a simple electric motor and guide rails along the side of the panel.
MIT
USA: Heat engine with no moving parts as efficient as a steam turbine
Engineers have designed a heat engine with no moving parts. Their new demonstrations show that it converts heat to electricity with over 40% efficiency — a performance better than that of traditional steam turbines. The heat engine is a thermophotovoltaic (TPV) cell, that passively captures high-energy photons from a white-hot heat source and converts them into electricity. The researchers plan to incorporate the TPV cell into a grid-scale thermal battery. The system would absorb excess energy from renewable sources such as the sun and store that energy in heavily insulated banks of hot graphite. When the energy is needed, TPV cells would convert the heat into electricity, and dispatch the energy to a power grid
MIT
USA: Tumours partially destroyed with sound don’t return
Noninvasive sound technology called histotripsy has broken down liver cancer tumours in rats with millimeter precision, spurring the immune system to prevent further spread. By destroying only 50% to 75% of liver tumour volume, the rats’ immune systems were able to clear away the rest, with no evidence of recurrence in more than 80% of animals. Where a typical ultrasound uses sound waves to produce images, engineers have pioneered the use of those waves without the harmful side effects of radiation and chemotherapy. The transducer delivers high amplitude microsecond-length ultrasound pulses — acoustic cavitation — to focus on the tumour specifically to break it up. Traditional ultrasound devices use lower amplitude pulses. The microsecond long pulses generate microbubbles within the targeted tissues — bubbles that rapidly expand and collapse. These violent but extremely localised mechanical stresses kill cancer cells and break up the tumour’s structure.
University of Michigan
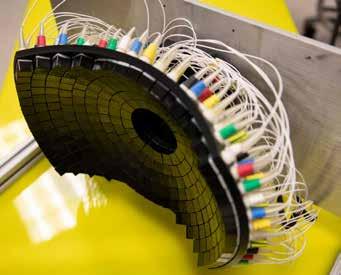
The 700kHz, 260-element histotripsy ultrasound array transducer
Australia: Insect wings inspire new antibacterial packaging
Inspired by the bacteria-killing wings of insects, scientists have developed a natural antibacterial texture for use on food packaging. The lab-made nanotexture from an Australian-Japanese team kills up to 70% of bacteria and retains its effectiveness when transferred to plastic. Dragonfly and cicada wings are covered by a vast array of nanopillars. When bacteria settle on a wing, the pattern of nanopillars pulls the cells apart, rupturing their membranes and killing them. The team developed their nanotexture by replicating this and developing nanopatterns of their own. To assess the pattern’s antibacterial ability, bacteria cells were monitored at RMIT’s worldclass Microscopy and Microanalysis Facility. Until recently, it was difficult to find suitable technology to reproduce this nanotexturing on a scale suitable for manufacturing. But now technology exists to scale up and apply antibacterial properties to packaging, among other potential applications, like PPE.
RMIT
USA/Germany: 3D-printing glass microstructures
Researchers have developed a new way to 3D-print glass microstructures that is faster and produces objects with higher optical quality, design flexibility and strength - expanding the capabilities of a 3D-printing process they developed three years ago — computed axial lithography (CAL) — to print much finer features and to print in glass. They dubbed this new system “micro-CAL. The CAL process is fundamentally different than today’s industrial 3D-printing processes. CAL 3D-prints the entire object simultaneously. Researchers use a laser to project patterns of light into a rotating volume of light-sensitive material, building up a 3D light dose that then solidifies in the desired shape. The layer-less nature of the CAL process enables smooth surfaces and complex geometries. This study pushes the boundaries of CAL to demonstrate its ability to print microscale features in glass structures - printing objects in polymers with features down to about 20 millionths of a meter (1/4 of a human hair’s breadth). For the first time, this method can print not only into polymers but also into glass, with features down to about 50 millionths of a meter.
UC Berkeley
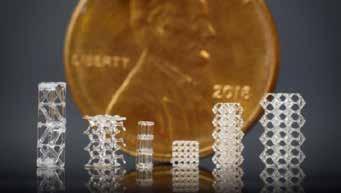
Australia: Breakthrough opens door to low-cost green hydrogen
In a clean energy breakthrough, researchers from the UOW and ACES have developed new electrolyser technology that brings cost-competitive renewable, or green, hydrogen closer to reality via the “Capillary-fed electrolysis cell” which enables production of green hydrogen from water at 98% cell energy efficiency. This productivity is superior to other existing technologies, and is well above the IRENA 2050 target, enabling an affordable hydrogen production cost that can match the production costs of fossil fuels. A UOW spin-out company, Hysata, was formed last year to commercialise the breakthrough. Electrolysers have existed for 200 years, however the large amounts of renewable electricity required to produce green hydrogen and the overall cost of electrolysers has prevented large-scale uptake of green hydrogen. Hysata’s overall electrolyser system has been designed for ease of manufacturing, scaling and installation, delivering 95% overall system efficiency, equivalent to 41.5 kWh/kg, compared to 75% or less for existing electrolyser technologies. This will significantly reduce both the capital and operational costs to produce green hydrogen -enabling hydrogen production of below US$1.50/kg per kg by the mid2020s, meeting Australian and global cost targets much earlier than generally expected.
University of Wollongong
“3D printing a liver or heart could take hundreds or thousands of years” – Mark Skylar-Scott, Ass. Prof. of Bioengineering, Stanford University. Even if 1000 cells per second are printed, organs contain many billions of cells. The team is working to speed up the printing process by laying down dense clumps of cells called “organoids.” Genetically modified stem cells are put in a centrifuge, generating a paste-like substance. A large number of cells are printed simultaneously into a gelatinous 3D structure. Each line of stem cells are genetically engineered to respond to a specific drug, allowing them to differentiate into specific cell types. But scaling-up will be a big challenge.
Battisti & Co. and Kaiser Compressors come along for the ride
Maintaining its position as one of the best luxury vehicle repairers in Australia has meant a long-term commitment at Charlie Battisti & Co. to continuously investing in the latest and most efficient technology. Kaeser Compressors has been on hand for over two decades now, ensuring their team of highly trained refinishing, repair and painting experts have access to a reliable and efficient supply of quality compressed air on demand.
When it comes to repairing prestige vehicles, Charlie Battisti & Co. has over 30 years of experience under its belt. Melbourne’s finest smash repairers, Charlie Battisti is one of only a handful of body shops Australia wide, that is a Porsche Certified Collision Centre, an Accredited BMW Body Shop and Mercedes Benz dealer recommended. Accident repairs, detailing and windscreen replacement are just a few of the services Charlie Battisti offers to its customers. However, regardless of the job at hand the focus is always the same - to ensure that the customer is 100% satisfied with all repairs undertaken and to maintain the vehicle's original build quality, strength and integrity. To meet these goals Charlie Battisti invested some years ago in a state-ofthe-art and purpose-built vehicle repair facility. Built with vehicle manufacturers specifications in mind, this modern facility in Nunawading houses all the latest approved repair, chassis alignment and measuring systems to ensure that all repairs meet the most exacting industry standards. To maintain its position as one of the best luxury vehicle repairers in Australia, the company continuously invests in the latest technology - not least the compressed air system. Compressed air is an essential utility at the facility that is used extensively. From powering the air tools - such as the sanders and polishers - to providing air to the dedicated paint refinish facility, the highly trained refinishing, repair and painting experts at Charlie Battisti require a dependable supply of high-quality compressed air. To meet these requirements back when Charlie Battisti first moved into the new facility, they opted for a Kaeser AS 31 series rotary screw compressor. Renowned for quality, reliability and efficiency, Kaeser was the ideal choice. After 15 years of reliable service, it was time to once again upgrade the compressed air system and invest in the latest and most efficient compressed air technology available. To reliably and efficiently meet the compressed air requirements of the facility, Kaeser recommended and subsequently installed an ASK 28 rotary screw compressor complete with air treatment. True class leaders when it comes to performance, the ASK series of rotary screw compressors deliver more compressed air for less energy. At the heart of every ASK system lies a premium quality screw compressor block featuring the energy saving Sigma Profile rotors. Kaeser airends are equipped with flow-optimised rotors, which contribute significantly to the overall system’s classleading specific package input power. Efficiency is further enhanced with the inclusion of a Premium Efficiency IE3 drive motor, which complies with and exceeds prevailing Australian GEMS regulations for three phase electric motors. Furthermore, the internal Sigma Control 2 controller always ensures efficient compressor control and monitoring. The ASK series also combine ease of use and maintenance-friendliness with exceptional versatility and environmentally responsible design. In addition, the soundproofed housing keeps operational noise to a minimum. Normal conversation can take place right next to the compressor, making the ASK series ideal at point of use. Seven years on and the ASK 28 continues to reliably and efficiently meet Charlie Battisti’s compressed air requirements, with the AS 31 remaining onsite as the back-up, when for example the ASK 28 is being serviced. “As a prestige vehicle repairer it’s always been important for us to invest in high quality equipment and Kaeser certainly ticks that box,” said Shane Perry, Paint Shop Manager of Charlie Battisti says. “We’ve been more than happy with the performance of the Kaeser compressors over the years. Moreover, the after sales and service support we’ve received from Kaeser over two decades now has been great.” The standard ASK series of rotary screw compressors from Kaeser Compressors are available with drive powers of 15 to 22 kW and produce flow rates from 1.93 to 4.45 m3/min, pressure 6 to 13 bar.
au.kaeser.com
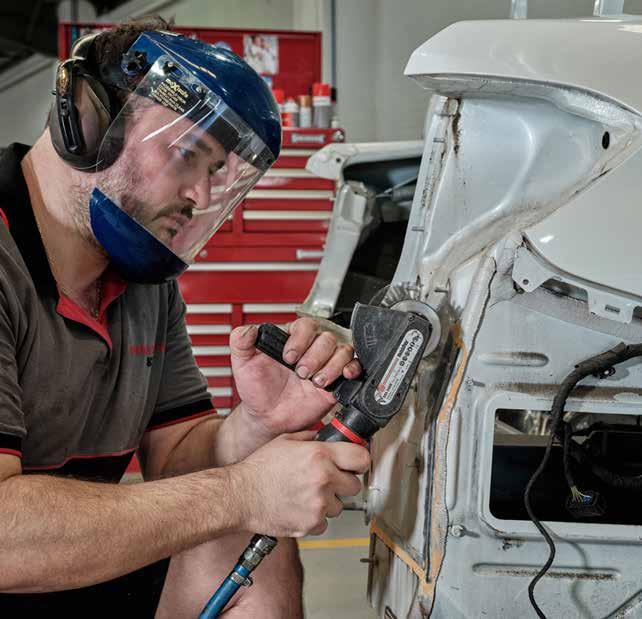
University sets up Industry 4.0 Technology Hub with Demmeler cobot system
In September 2020 during the COVID pandemic, the University of Wollongong (UOW) opened a new industry hub at its Shoalhaven campus in Nowra featuring Industry 4.0 technology.
This new Industry 4.0 hub includes a working demonstration unit of the Demmeler 3D table system supplied by Leussink Engineering with a cobot (collaborative robot). The Hub has several goals: Support local and regional industry (for example SMEs in manufacturing, agribusiness, defence industry) with the awareness and adoption of Industry 4.0 technologies Engage with schools and community to educate around Industry 4.0 and generally promote interest in STEM (Science, Technology, Engineering and Mathematics) Strengthen connections between UOW researchers and local industry. The innovative Hub showcases numerous Industry 4.0 Technologies, including cobots, virtual and augmented reality (VR & AR), as well as additive manufacturing (3D printing). “The equipment is used to demonstrate and showcase resources to industry partners looking to adopt new technologies. Equipment can also be accessed and used by students and the community through ‘makerspace’ activities,” said Evan Brown, Research Engineer, UOW Industry 4.0 hub. “Once the COVID lockdown period ended last year we had pent-up demand for people wanting to visit the Hub which is great. “HMAS Albatross, the largest operational Naval establishment and the Navy’s only Air Station is based in Nowra with many supporting businesses, so there are plenty of locals who want to see the Industry 4.0 technologies in action. It allows people to see how new technology could improve their business, and how they can adopt the latest equipment,” added Brown. Evan and his team worked closely with Leussink to set up two Demmeler tables to mount the collaborative robot welding system. Cobots are designed to operate close to humans as they perform their tasks, and unlike fully-fledged robots, they are an affordable solution to automate processes to support employees. In the UOW Industry 4.0 Hub, the cobot is set up on a Demmeler table system to undertake welding tasks. The Demmeler system plays a dual role. It holds the cobot firmly and accurately in place, and it also holds the workpiece securely and precisely while the welding is taking place. “The two systems demonstrate great synergies and visitors can see how this system will work in their business,” said Brown. Unlike traditional industrial robots, cobots are responsive to human touch and the environment around them, and therefore do not need to work behind large safety screens because they pose little risk of accidents occurring. Humans provide the direction to the cobot, and the cobot provides the precision steering and control. “One of the key advantages which we can demonstrate is how quickly it can be setup and programmed for just a few welds, before moving on to the next. Operators do not have to be experts in computer programming or welding to be able to operate the Demmeler cobot system,” said Brown. The Demmeler welding and fabrication system, distributed exclusively in Australia by Leussink Engineering, is the ideal partner product for a cobot. The main reason Demmeler tables and cobot systems were chosen for the Hub was to meet the objective to support local and regional industry (manufacturing, agribusiness, defence industry) with the awareness and adoption of Industry 4.0 technologies. As a consequence, the Business Development Manager and acting lead of the Industry 4.0 Hub works closely with groups like the Shoalhaven Business Chamber and local industry as well as attends industry events to spread the word with local businesses and those further afield. The Demmeler 3D workbench and welding table is a versatile jig and fixturing system for all types of welding and fabrication work. A cobot can be anchored and fixed to a Demmeler table system to ensure accuracy and versatility. The cobot can return to the same position every single time. Working in partnership with robotic experts, Leussink develops cobot-based systems for clients in a range of industries, enabling them to meet many different requirements. Leussink has extensive experience in the design and production of a wide range of bespoke equipment and solves engineering problems for companies across a wide range of industries.
leussink.com.au
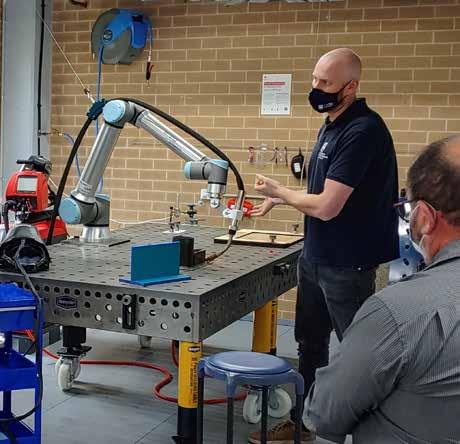
Evan Brown demonstrating the Demmeler table and cobot at UOW.
Lightweight Australian ingenuity solves heavy rooftop challenges
Industry pioneer and leader Con-form Group broke the mould for roof-mounting mechanical equipment in 2014 and has not looked back since.
Not that you would have noticed, because as Con-form Group Managing Director Nigel Cro says, “People will drive along on a highway overpass and there are a lot of things on roofs that you see; now if you don’t see those things, that’s because we’ve done a good job – that’s our goal.” Industrial HVAC systems are heavy and often noisy. Con-form Group provide an engineered solution for the structure to cater for the weight on rooftop installations and additionally deliver acoustic solutions to minimise environmental noise. Con-form Group’s lightweight aluminium plant platforms and screens are now found on industrial, commercial and public infrastructure roofs right around Australia. The Bathurst-based business was established more than 20 years ago and employs approximately 35 staff. In 2014, the Conform Group team developed an industry leading lightweight roofmounting platform system for mechanical equipment. “It was painful to see large structural steel sections getting craned onto roofs laboriously day after day, piece by piece and the danger and the logistics involved,” says Cro. “I remember just looking at that and saying, ‘There just has to be a better way.’ Why can´t we go to a lightweight structural system that removes a lot of this pain?” Cro explains that from his perspective, roofs and aluminium are something that go together very well. Aluminium is lightweight but can be engineered as part of a structural solution. Aluminium is an inherently non-corrosive material, well suited to Australian roofs subjected to harsh environmental conditions. The Con-form Group team pride themselves on being able to innovate and rapidly develop bespoke solutions for their clients. Employing a skilled team of engineers, draftspersons, fabricators and installers and encouraging a culture of excellence and innovation. “Your employees are your biggest asset – that is true. That will never change, it doesn't matter what sort of building you operate from, or what sort of machinery have. Your biggest asset, your most valuable asset will always be your team. So we´ve gone through very, very carefully and picked our team. Those individual people absolutely have to share the same culture and the same values that we as business owners do,” Cro says. Nigel Cro describes the agility of his team as being unprecedented. “I can go to our structural engineer who can do up a preliminary design sketch, send that through to the CAD team to draw it. It goes down to the machinery, which is fully automated, and I can have a sample on my desk within an hour. It´s as quick as that and that is very, very rarely seen.” Equally important to Con-form’s business and success are strong industry partnerships with key suppliers. Nigel emphasises the importance of cultural fit and the significance this plays in selecting suppliers Con-form Group will partner with. “We're very proud to be an Australian manufacturer. In years gone past we, like a lot of companies, purchased a lot of things from offshore. But as we realised what the importance to our customer is in timing as well as value of getting things local, we´ve brought a lot of things in house,” says Nigel. Capral Aluminium is a key supplier to Con-form Group providing regular supply of standard and exclusive aluminium sections along with aluminium sheet and mesh products. Custom extrusions are a key element in the solutions Con-form create, and Capral works hand in glove with the Con-form team to assist in the development of exclusive extruded sections and ensure the business receives consistent and regular supply to its regionally located manufacturing site. For Nigel Cro, the value of a strong partner like Capral is not limited to reliable material supply, “We get more value than a pallet of aluminium from Capral. That´s really where we’re at, and that comes back to the culture again. What can we exchange as industry colleagues between each other, rather than simply being a supplier that a truck comes in and it drops off something and you pay for it. That´s not what we´re about. We need to exchange data between ourselves so that we can grow together as industry partners.”
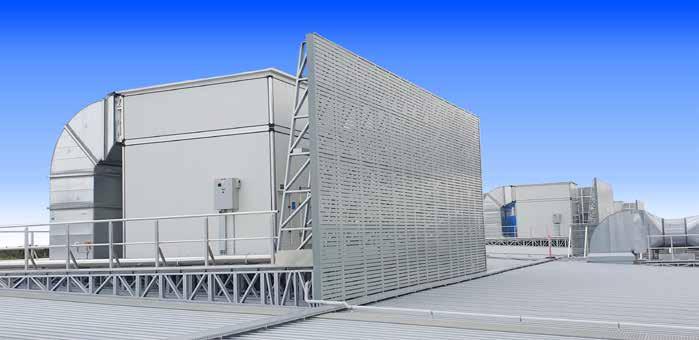

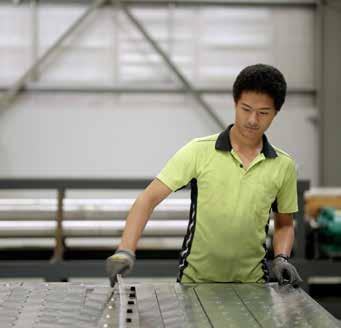
There have been significant changes within the Australian aluminium industry over the past 24 months as many Australian manufacturers grapple with material import issues and supply shortages not to mention turbulent aluminium pricing and LME fluctuations. These changes are significant for manufacturers like Con-form who rely heavily on their ability to procure aluminium to manufacture and satisfy customer needs in a timely fashion. Capral’s NSW Industrial Market Manager Mark Murray works closely with the Con-form team to ensure their needs are being consistently met and they are abreast of changing industry dynamics. “Mark came out to visit us today, and that´s always great because things are changing so fast in the industry, extremely fast. Quicker than we can almost keep up with. Mark, he´s just a wealth of knowledge so I really took that time to try and draw out a lot of things out of him that I really didn´t know, and that really helped us as a company,” says Nigel, emphasising the value of this supplier partnership for his business. Con-form Group stands out in the market for its solution focus and as a regional Australian manufacturer using Australian materials, ingenuity and labour. But more importantly, what they nail every minute of every day is their focus on what the customer is trying to achieve rather than simply responding to an order. ʺAny roof, any pitch, any weight, anywhere,” Nigel says, “that’s our promise, we will create the solution our clients need, and we are glad to have partners like Capral to support us.” capral.com.au
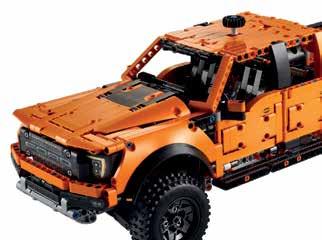
WIN
a Ford F-150 Raptor
See detalis below
Take control with ECI
ECI serves manufacturing businesses across the globe, offering a range of growth boosting features helping to:
Deliver more orders with less resource through streamlined order processing. Intelligently manage supply and demand to increase job profitability. Effortlessly manage any job scheduling challenges with built-in flexibility. Access insightful dashboards, providing visibility you can trust. Eliminate manual data entry to ensure accuracy across the business.
Visit us during Australian Manufacturing Week on Stand MT83 to find out more and be in with a chance of winning a (lego) Ford F-150 Raptor. Or visit ecisolutions.com/au
How business gets done
At-Home Toolholder assembly program
Building toolholders at home is a new direction in Innovation.
Lockdown has been tough for everyone, but the people at Integra Systems recognise they have been luckier than many due to the continuity of their work. For those in the local community who haven’t been so lucky and may have lost their income and/or sense of purpose, Integra found a way to help them through these difficult times: an at-home program for assembling toolholder kits. The program idea came from their Director of Innovation, Russell Hughes, who adapted it from a traditional German cottage industry model used by the cuckoo clock trade. In the Black Forest region of Germany, the villagers would get snowed in during the winter, so, to combat this issue, families focused on specific parts of cuckoo clock production, such as woodcarving, so they could generate an income during their isolation across the colder months. The Integra at-home program works in a similar way to these cuckoo clock creators in Germany. “We create kits at our facility in Melbourne’s North and then send these kits out to members of the community,” explains Hughes. “These are families, students without work, single people, anyone who puts up their hand for it – who then assemble these kits into toolholders from their lounge rooms, garages or kitchen tables.” Georgia Hughes and Nick Hardy, part of the team at Integra System, have been in charge of running this at-home program, packing their cars to the brim daily to deliver kits directly to the doors of workers as early in the morning as possible. Each kit comes as a set of components – screws, grub screws, final bags, final boxes, tools and parts ready to be assembled – that equate to 200 tool-holders per kit. Workers are paid per toolholder so, the more kits they can get through, the more money they make. The completed toolholders then go to Integra’s client where they are distributed to major retail centres for tool merchandising displays. “Providing kits to homeworkers in exchange for earning money is not a new initiative at Integra Systems,” explains Hughes. “The programs have had varying levels of success in the past but, with COVID and more people than ever working from home, or stood down from work, this initiative has worked extremely well.” “The idea is to provide workers with a continuous supply of toolholder kits and incentivise the workers to make the toolholders by paying them for their hard work,” Hughes continues. “To run effectively, the program must involve simple processes that require few specialty tools. When the toolholders are picked up and kits are dropped off regularly, we’ve found that the home workers feel highly valued; that they are doing something productive and contributing to the supply chain.” The Integra at-home toolholder kit program has been running since August, with a total of 18 families currently assembling toolholders on a regular basis. By the end of 2021, the home workers had assembled 25,000 tool-holders. “We’ve got a family of workers – the Cleeve family,” explains Hughes. “They decided not to keep the cash themselves but, instead, are a great example of paying it forward at a time when people are doing it tough. They’ve been using the money they’ve earned to purchase coffee cards for the frontline workers at the Austin Hospital.” “People have joined this program for so many reasons, whether it’s to take some pressure off themselves or to help others. Either way, it’s a win-win situation for everyone who’s involved, including us here at Integra Systems.” integrasystems.com.au
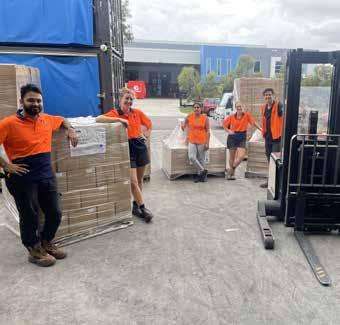
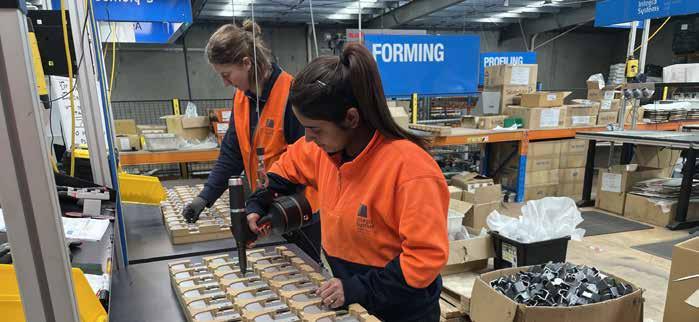
Veolia launches The Barrel
Veolia Water Technologies launches new disruptive technology for desalination and water reuse in the Asia Pacific.
Veolia Water Technologies, a subsidiary of the Veolia group and leading specialist in water treatment, announces the Asia Pacific launch of the Barrel, an integrated plug-and-play reverse osmosis (RO) technology. With increasing demand and rising concerns over scarcity of fresh water in the Asia-Pacific region, the Barrel meets the challenges and expectations of the desalination market while producing fresh water complying with all water quality standards. It is also suitable for wastewater reuse and low-pressure RO applications. The Barrel was selected as a key technology for the first experiment in Europe in wastewater treatment for the supply of drinking water through the Jourdain programme, in France’s Vendee region. The technology has also been in use at the Oman Sur desalination plant since 2019. The Barrel is a multi RO element vessel that is designed to be a plugand-play system. The carbon steel pressure vessel is manufactured and tested off-site, and is delivered as a single unit, so installation on-site can be fast-tracked and project schedules shortened. In addition, the modular design of the Barrel makes it highly scalable, offering varying capacities from 400 m3/day to 50,000 m3/day per unit. It can also be used in place of existing RO membranes and nanofiltration skids for a more economically viable, sustainable, and innovative alternative. Compact and suitable for outdoor installations, the Barrel offers a footprint reduction of up to 25% and does not require a controlled environment. The sustainable solution also provides a reduction in electrical consumption in the range of 0.05 kWh/m3 of fresh water produced. Beyond sustainability, the unique design of the Barrel also significantly reduces the number of high-pressure piping connections down to just two — the seawater inlet and the brine outlet. This design feature makes it safer for operators and minimises risks on-site during the maintenance and operation phases. Corrosion is less likely to occur as seawater leakage sources found on the multiple high-pressure connections of traditional RO skids are reduced. The Barrel also has a built-in digitalisation system with smart connectors providing real-time status updates on each membrane’s condition. In fact, their performance can be monitored automatically and accessed remotely — helping operators to make better decisions, whether to shut down, rotate, or replace membranes.
veolia.com
