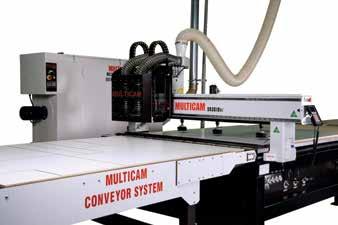
30 minute read
AMW 2022 – Where technology meets innovation
from AMT JUN/JUL 2022
by AMTIL
056 PREVIEW Multicam CNC routing machinery
Multicam CNC routers have been used in various engineering industries since inception. We are excited to be able to demonstrate how Multicam CNC routers can be a solution for Engineering companies in the plastics, metal and composite products industries at this years’ event. Multicam Heavy Duty CNC Routing machines are proudly made in Australia. Designed for profile cutting sheet product and extrusions including metals, plastics, composite materials, and timber products, they are used in the manufacture of Aluminium boats, Aerospace components, Truck body parts, Caravan & Motor Home components, Kitchens, Furniture or any other flat sheet product. They are used extensively in the ACM and HVAC industries and include many unique design features aimed specifically at making the processing of ACM cladding and ducting and insulation materials easier and more efficient. Other specialist features ensure that Multicam machines are an excellent alternative to Plasma and Laser machines that typically have higher running costs and greater servicing demands. Multicam CNC routers are available in a range of sizes with process areas starting from 2400mm x 1200mm with larger and custom sizes available. Multicam machines can be supplied with a variety of accessories including vacuum hold down beds, fully automatic tool changers, automatic loading and unloading attachments, mist cooling/lubrication system, chip extraction, multiple drill heads, tangential-oscillating knife attachments and more. Multicam Systems has over 30 years of experience in the manufacture of flatbed CNC routing machinery and has been providing CNC routing solutions through our offices in Newcastle, Melbourne and Brisbane. Multicam CNC routing machines are backed up by a highly skilled team of factory trained technicians ensuring the best possible level of advice and service. The ability to link with software programs such as Fusion360, Mastercam, SoldiCAM, Surfcam, Rhino, Pytha, ARTCam, Enroute and numerous other products makes Multicam CNC routers an obvious addition to any engineering company.
Multicam CNC Routing Machinery Stand MT22 multicam.com.au
Providing the right gas is just the start of the journey. Air Liquide’s ambition is to lead its industry, deliver long term performance and contribute to sustainability.
A world leader in gases, technologies and services for Industry and Health, Air Liquide is present in 80 countries with approximately 66,000 employees and serves more than 3.6+ million customers and patients. Oxygen, nitrogen and hydrogen are essential small molecules for life, matter and energy. They embody Air Liquide’s scientific territory and have been at the core of the company’s activities since its creation in 1902. Air Liquide’s ambition is to lead its industry, deliver long term performance and contribute to sustainability. The company’s customercentric transformation strategy aims at profitable growth over the long term. It relies on operational excellence, selective investments, open innovation and a network organisation implemented by the Group worldwide. Through the commitment and inventiveness of its people, Air Liquide leverages energy and environment transition, changes in healthcare and digitisation, and delivers greater value to all its stakeholders. Air Liquide Australia Limited provides innovative, responsive and customer focused services to our product range, which improves the performance of our customers while helping protect the environment. Air Liquide goes beyond simply selling molecules of gases. They believe in learning the customers' businesses to provide them with true value. They ask key questions and listen to the answers. That dialogue continues throughout the business relationship with their customers as they seek to contribute ideas to help them improve their operational processes, both business and manufacturing, while improving their own business process. They commit themselves to understand and fulfill the customers' requirements and expectations. Air Liquide also carries out their activities in a manner which uses the ISO 9001 Quality Standard to verify the quality and continuous improvement of their policies, procedures, work instructions and management systems, and ensures that their products and services satisfy the highest standards, through the application of best practices.
Air Liquide Australia Ltd Stand WT12 industry.airliquide.com.au
Panel benders look to the future
The panel bender is the machine which more than any other, represents the Salvagnini spirit. This unit is a solution able to combine cutting-edge technology with productivity, autonomy and flexibility.
The Salvagnini panel bender confirms its place as the undisputed protagonist in the world of smart manufacturing. The unit is fully automated and adaptive, with 11 different models available. Over 4,000 installations in 76 countries, the world’s largest panel bender manufacturing plant and over 40 years of experience and competence speak for themselves: Salvagnini is an authority on ‘panel bending 4.0’, a flexible process the likes of which have never been seen before, with application boundaries now extending to sectors and environments that have always been considered poorly suited to this technology. At the Australian Manufacturing Week in Sydney, Salvagnini is proposing its compact P2-2120 panel bender, one of its most successful models, which is able to natively combine productivity and flexibility, producing an average of 17 bends per minute. The P2 doesn’t need re-tooling, because the upper and lower blades, the counterblade and the blank-holder, are universal tools, able to process the whole range of thicknesses and machinable materials. The automatic blankholder adapts the tool length according to the size of the part being produced in-cycle, without machine down-times or manual retooling. But the P2 also automatically adapts to changes in material. “The Salvagnini panel bender is an automatic machine in every aspect, and as such is ideal for a modern smart factory,” explains Nicola Artuso, Salvagnini Product Manager for bending technologies. “The P2 we are presenting today, in addition to its consolidated features such as the maximum height and length of the bend, which reach 203 and 2,180mm respectively, or the overall footprint of less than 35m2, also has several interesting innovations such as MAC3.0.” MAC3.0 is a set of integrated technologies – sensors, formulae and algorithms – to make the P2 even more intelligent. MAC3.0 allows the P2 to adapt to the material being folded by measuring the tensile strength in real time and comparing it to the reference values of some of the most common materials on the market. If the mechanical characteristics of the material being machined are within ±25% of the reference value, compensation is fully automatic. MAC3.0 reduces the risk of obtaining faulty parts and eliminates rework-ing and material waste – a highly significant detail in the current economic situation, where each kilogram of raw material saved represents a considerable economic benefit. “The functions of MAC3.0 do not end here,” Artuso continues. “If necessary, MAC3.0 also makes it possible to define new materials simply and intuitively. This new material can then be called up in a few clicks: the panel bender adapts the bending force as necessary to keep working within the parameters. These newly defined materials can also be used as the starting point for new adjustments and new materials. This is an extremely interesting solution and is particularly relevant in today’s raw material supply chain where sourcing difficulties, along with the dynamism of the market and the need to comply with set delivery times, force companies to accept compromises on sheet metal quali-ty, risking significant increases in waste.”
Salvagnini Italia S.p.A Stand MT79 salvagninigroup.com

058 PREVIEW Applied bringing the Yawei pressbrake at AMW
New handheld fiber laser welder one of several products Applied will be exhibiting at Austech as part of AMW.
Applied Machinery will again be showcasing a diverse range of machines at Austech. Taking centre stage on the Applied stand will be a 9-Axis Yawei CNC pressbrake. Yawei pressbrakes offer manufacturers access to affordable, precision CNC bending. With a range available from 35 ton up to 3000 ton there are virtually no limits to what can be bent. The Yawei pressbrake on display is a PBH Series with a 160-ton bending capacity. It features a Delem DA-69T Controller, 6-axis CNC backgauge and a servo driven hydraulic system. An automatic tool clamping system, CNC bending help and robotic integration are amongst the additional options that are available. Over the past decade Yawei has built a loyal following; establishing an enviable reputation for quality, performance and outstanding value for money. In addition to pressbrakes, Yawei has an extensive range of fiber lasers, turret punch presses, guillotines, and smart-factory automation solutions. Also on the stand will be a Weber grinding and deburring machine. Weber is a German-based company with an impressive 100 years’ experience in grinding machine manufacturing. Weber grinding machines grind, round, deburr and descale lasered, punched and nibbled parts, to ensure a consistent, brilliant surface finish for either final use, or preparation for additional processing. One of the most innovative products that will be on the Applied stand is the new Fanuci handheld fiber laser. Handheld laser welding machines are increasing in popularity for the many benefits they offer compared to conventional welding. The Fanuci fiber laser welder provides high speed welding coupled with a far superior, smoother weld line. It features low heat input, small deformation, large penetration depth and good repeatability. The unit offers low energy consumption and is virtually maintenance free. “There has never been a more important time to support Australian manufacturers. We’re proud to be able to play our role by supplying high quality, value for money products that boost productivity, improve quality and allow companies to expand their market offering,” Mr Fisher concluded.
Applied Machinery Stand MT46 appliedmachinery.com.au
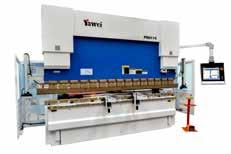
Machinery Forum has been supporting Salvagnini's customers for decades

Latest and best Salvignini Panel Benders and Cutters will be on display.
For over 50 years, Salvagnini have been offering innovative technologies that allow for automatic and flexible solutions to transform sheet metal into a great variety of products for daily use. The Salvagnini Group designs, manufactures and sells flexible machines and systems for sheet metal processing, punching machines, panel benders, bending machines, fibre laser cutting machines, FMS lines, automatic warehouses and software. The P1 is the electric Panel Bender that Salvagnini offers as an alternative to traditional folding designed to occupy only eight square metres, designed to consume three kW and equipped with patented kinematics. The P2 produces a great variety of pieces in a short time and automatically without machine stops, without waste and with reduced consumption. The P4 has for 40 years has been the flagship of the Salvagnini brand. Fibre Laser Cutters L3 and L5
The L3 Fibre Laser Cutter is a productive versatile solution. The L3 utilises the mechanical compass system making it possible to cut at high dynamics with high quality over a wide range of thicknesses. Brake Presses B3 and Roboformer
B3 designed by combining the features and benefits of electrical and hydraulic solutions with in-depth automation software, mechanical and electronic skills. The B3 is the ideal brake press for dynamic production. From two to five metres and from 60 to 400 tons. Roboformer is a non-traditional solution that combines the dynamics of the press benders with the intervention of a robot designated to manage work activity in complete autonomy. Punching Machines S1 and S4
S1 implements numerous innovative and original elements which make it a solution with a wide field of application that is more extensive than simply a punching machine. Laser cutting is integrated. S4 is a multi press head for multiple and independent punching. An integrated shear for kit production and an automatic manipulator for precise intervention and optimised control. FMS FlexCell and S4 + P4 line
FlexCell combined features of a panel bender and brake press and represents a unique solution on the market to obtain the maximum value from bending. S4 + P4 line. For more than 30 years has represented the most efficient flexible manufacturing system on the market. One of Salvagnini's most successful solutions. Industry 4.0 indicates the use of cyber-physical systems (CPS) and digital technologies (Cloud, IoT, Big Data) to improve working conditions and to increase the productivity and production quality of the plants by creating collaboration between all the players involved in the production process ie. operator, machines and tools. In 1985 the first automatic factory (AIS) operating with the lights off with built consisting of 12 interconnected systems and communicating with the MRP. Today AIS indicates a set of Salvagnini systems orchestrated by the OPS process software for intelligent integration between the machines and the customers ERP. Machinery Forum has been supporting Salvagnini and Salvagnini's customers in Australia and New Zealand for several decades. Machinery Forum has highly-skilled service engineers. For nearly 60 years, Machinery Forum has been in full support of local manufacturing and has made a significant contribution over it's many years of operation towards that goal.
Machinery Forum (VIC) Pty Ltd Stand MT79 machineryforum.com.au
Achieve innovative motion control solutions with ANCA Motion’s tubular linear motor technology
A new interactive linear motor demonstration will be live at ANCA Motion’s stand at this year’s Australian Manufacturing Week in Sydney.
The new demo showcases how ANCA Motion’s innovative linear motor technology can solve multiple very challenging issues in food and packaging industries, such as throughputs, flexibilities and harsh operating environments. It also shows how easy it is to build a full-feature user interface with ANCA Motion’s Commander software. Smart motion solutions consider the control of the flow and speed factory operations as well as the requirements of various industries. Using magnetic flux to create motion, ANCA Motion’s LinX motors offer a higher performance linear motion system at lower cost. Adapt as production needs evolve with flexible and accurate positional control
Modifications when required are simple, the setting of LinX can be changed by simply editing the parameters within the drive configuration, directly by the operator, saving valuable time and cost. Sensor-based sorting functionality, as displayed in the new demo is sought after by industry-critical applications in food processing, integrated post-harvest solutions, distribution, packaging, mining, recycling, waste management, chemical, and plastic industries. Simplicity in machine design leads to unlimited possibilities
Compared to traditional automation systems, the streamlined design of LinX® avoids the need for additional belts or screws, complex pneumatic air systems or bearing components. This translates to tangible benefits such as low maintenance and ownerships costs and it is retrofit friendly. At AMW, the team’s V-structure robot demo highlights the beauty, efficiency and creativity that can be achieved using tubular linear motors. The twin LinX M-series motors join to create a V-shape parallel robot, revealing that the uses for this technology are only limited by imagination. Suitable for harsh environments and washdown applications, ANCA Motion’s linear motors have an IP66 or IP67 rating and a fully potted body. With no contact between the forcers and shafts, grease or lubricant contamination is eliminated. The solution is ideal for clean environment applications such as in the food, beverage, and pharmaceutical industries. Tried and tested technology
ANCA Motion specialises in high precision control solutions for CNC and automation. Australian owned and operated, the company offers local design and manufacture with experience spanning over 45 years. The passionate team’s global network of 125 engineers create custom solutions, partnering with customers across a range of industries on bespoke technology solutions to meet individual needs.
Anca Motion Pty Ltd Stand RA72 ancamotion.com
CIVAN – a new high power laser for better welding
Manufacturers are increasingly replacing traditional mechanical machining and thermal welding systems with laser processing tools. Compared to traditional thermal welding processes, laser-based techniques require less heat input due to the beams’ high energy.
All welding methods involve melt-pool formation and subsequent rapid solidification, which can alter the properties of the welded metal. The high energy of laser welding, however, not only melts the material but also evaporates it, creating a vapor capillary in the material called a ‘keyhole’. This gives laser welding the advantage of a very high aspect ratio, defined as a high ratio of penetration depth to weld seam width. Compared to thermal welding methods, which generally provide wider and shallower weld seams, laser welding’s high aspect ratio translates into potentially lower part distortion. To meet the demands of modern manufacturing CIVAN has developed a High Power Single Mode Laser with dynamic beam. This innovative product enables different beam shapes, beam steering, and fast movement of the focal point, all electro-optically controlled with no mechanical movement. For example, CIVAN’s unique beam shaping allows uniform penetration in aluminium welding with constant depth and very low porosity. Inbuilt software allows beam shaping design in minutes, while beam steering with a small dynamic spot makes for clean fast cutting, efficient welding of a large gap or welding dissimilar materials. In this highly sophisticated laser system Coherent Beam Combining, of CBC, provides advantages for welding applications making available a whole new set of parameters for laser welding to meet the needs of to-days welder. The new Dynamic Beam Laser provides countless new applications for materials processing, an opportunity taken up by Valeo one of the world’s largest car battery suppliers. This European company designs innovative solutions for vehicles with a particular focus on reducing CO2 emissions and turned to CIVAN for a laser system to improve production. Due to the growing demand for an increase in the travel range of electronic vehicles, Valeo wanted to improve their battery cooler manufacturing process in order to make larger battery coolers. Valeo had been using a brazing method to join parts and were looking for a system which was more environmentally friendly system, more cost effective, with reliable strong welds and, importantly, produce no leakage of the large sealed cooling plates. Using the new Dynamic Beam Laser their processes were tested in CIVAN’s application lab. By answering the latest market challenges, CIVAN’s technology opens new horizons for better material joining control, new applications and welding new materials previously not possible.
Raymax Applications Stand MS35 raymax.com.au
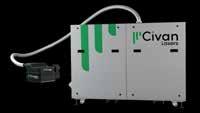
Bosch bringing the future of robotics and automation to their stand at AMW
As the manufacturing industry continues to evolve, new technologies, competition, and opportunities arise. This change is creating a new set of challenges for manufacturers.
Bosch Australia Manufacturing Solutions (BAMS) provides 135 years of Bosch quality and expertise to Australian manufacturers. Offering custom machine building, engineering, manufacturing support, and consulting services for Australian manufacturing operations, BAMS is helping to elevate Australian manufacturing. Based in Clayton, Victoria, BAMS has over 100 engineers and support staff servicing Bosch plants locally. Over the past five years, BAMS has become one of the country’s leading factory automation companies, working with a diverse array of blue-chip, mid-tier and start-up manufacturers to automate their manufacturing. In 2021, BAMS opened a new Manufacturing Automation Centre at the Bosch headquarters in Clayton, a purpose-built facility to house the growing automation business. With over 65 years of lean manufacturing DNA, Bosch Australia Manufacturing Solutions is a leading partner for manufacturers, ready to collaborate and navigate in these challenging times. BAMS combines its proud heritage and relentless innovative spirit to deliver premium quality machines and services and produce efficient and reliable solutions for our customers. Bosch Australia Manufacturing Solutions are the preferred supplier to help manufacturers scale up their business. To assist their clients, BAMS provides an array of solutions and services: • Robotics & Automation: extensive experience in designing and building a range of robotics and automation applications including automated assembly, packing, palletising, labelling, vision, welding, grinding, polishing and high precision mechanical assembly. • Production Line Systems: providing complete end-toend solutions including logistics (stock movement and management), complete IT, ERP and MES systems. • Test & Measurement Systems: testing equipment built to be fully integrated, ensuring the manufacturing achieves maximum value with minimal disruption.. • Machine Servicing: specialised services including mechanical design, process engineering, electrical and software design, robot programming, I.40 consultation, test systems, tailored training, and collaboration. • Consulting Services: customised lean manufacturing consulting services including lean assessment, design for manufacture and assembly, value stream mapping, and lean line design. • Factory of the Future: Bosch are a global provider and user of I4.0 Solutions, focusing on technology that allows the organisation to work smarter not harder. Industry 4.0 paves the way to the factory of the future and in doing so also makes new business models possible — for industries and companies worldwide.
Robert Bosch Australia Stand MT71 bosch-manufacturing-solutions.com.au
062 PREVIEW Workholding and clamping answers from Romheld Automation
Romheld Automation is pleased to present some of the latest developments in workholding and clamping from leading European, American and Japanese manufacturers.
These days, batch runs are generally smaller so set up and changeover times become proportionally more expensive, to the point where they can make a job uneconomic unless volumes increase. Add to the mix the current supply chain issues being experienced worldwide and the ability to be more flexible becomes a priority. At the same time the need for repeatable workholding raises additional challenges. To grow in the current manufacturing climate you need fast and accurate setups and changeovers, so enabling smaller production runs. Originally based entirely in the automotive industry, Romheld Automation understands the requirements of modern manufacturing. “Before the car industry shut down we moved into industrial automation, mainly supplying end of arm tooling (EOAT) for packaging and machine tending,” says Peter Hope from Romheld. “This experience enables us to offer a wide range of tooling suitable for both machining and robotic processes.” Hainbuch Gmbh manufacture precision collet chucks easily capable of 15 second collet changes without any clocking up required. Now, Hainbuch offer a full range of accessory tooling that is simply bolted into position, again without clocking up. These accessories including expanding mandrels, two and three jaw chucks, magnetic chucks and face drivers. With changeover times of two minutes or less you can be more competitive on both long and short runs. Roemheld GmbH manufacture world class hydraulic clamping equipment. Hydraulics can be problematic when machining carbon fibre and other composites, so Roemheld developed electronic swing clamps to eliminate the risk of oil contaminating the product. These clamps are fully self-contained with a built in brushless 24V DC motor with gear drive to actuate the swing and clamp movements. The control is integrated within the clamp, requiring only two cabes. IO link is available as an option. We will show an example of an electric swing clamp, as well as our very popular hydraulic Bore Clamps for ID gripping. The Roemheld group also manufacture Stark zero-point clamp tooling which provides extremely accurate, fast changeovers of fixtures and stationary clamping tools using springs to clamp, and air or hydraulics to unclamp. The group also offers Hilma precision machine vices and mould/die clamping and handling tooling, some of which will also be on display.
Romheld Automation Stand MT45 romheld.com.au

Sheetmetal Machinery Australia
Sheetmetal Machinery Australia to showcase the all new EvoBend long length folder at upcoming AMW.
Sheetmetal Machinery provide the latest leading-edge solutions to remain competitive in today’s market. Sheetmetal Machinery prides itself on commitment to customers, as such exceptional sales and service is offered on the range of machinery supplied. Sheetmetal Machinery is supported by a team of qualified in-house service engineers throughout Australia and New Zealand. Engineers receive regular OEM training and certifications, combined with a comprehensive inventory of spare parts to ensure the best possible support. Australian Manufacturing Week will be first Australian exhibition to showcase the all-new long length folder from EvoBend. The product line features up/down folders (D300, D400, D600, D800) utilising a patented folding technology combined with unique operator safety system. The patented double bending system enable unrivalled freedom of bending with a maximum capacity of 2mm mild steel and 3mm aluminium. Unlike most long length folders, the Evobend is completely electric. The absence of hydraulics provides several advantages in terms of energy consumption, accuracy, reliability, speed, maintenance, and noise. In terms of energy consumption, you can expect a reduction of up to five times less than a hydraulic long length folder. Operator safety is paramount for any machine, this is an area where the EvoBend excels without compromising speed and performance. A first glance you will notice that the folding beam does not pivot or swivel towards the operator, but rather “rolls” around the material. This allows the Evobend to utilise complete machine covers reducing the number of potentially dangerous intervention points. In addition, modern mobile safety fences are used in combined with laser finger protection at the clamping point to create a flexible solution for operator safety. A inherit feature of all electric machines is their speed and performance, there is no requirement for additional servo valves, double hydraulic pumps or the like. Simply put, the EvoBend provides the fastest possible bending speed available on the market. Evobend has re-defined the traditional long length folder and delivers a cutting-edge product line with significant benefits. If you would like to learn more, our highly skilled team are available throughout Australian Manufacturing Week. Also on display and for demonstration: • Q-Fin Advanced set F1200 + WES6000 • SafanDarley Press Brake
Sheetmetal Machinery Australia Pty Ltd Stand MT50 sheetmetalmachinery.com.au
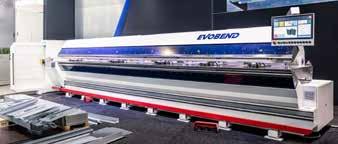
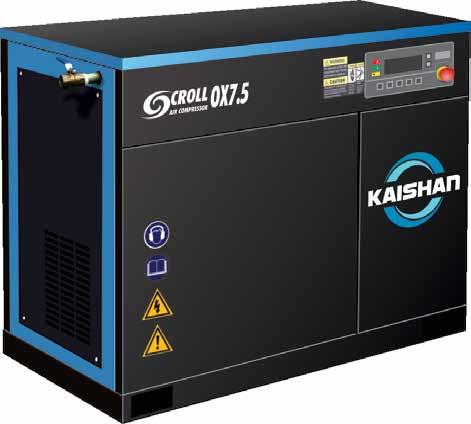
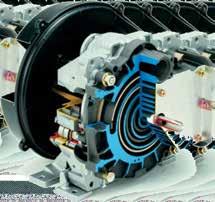
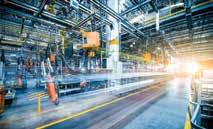
064 PREVIEW Dimac for workholding
Dimac Tooling is Australia and New Zealand’s leading supplier of accessories and workholding solutions for CNC milling and CNC turning machine tools.
Dimac will again showcase the leading productivity solutions for owners and users of CNC machine tools. On show will be the latest releases in workholding from the industry innovator, Lang (Germany) for secure and flexible holding of workpieces in your machining centres. Also see demonstrations of rapid and accurate tool setting and pre-setting with ability to directly communicate with your CNC controller from Zoller (Germany). With live demonstrations you will see how to keep your coolant filtered, clean and healthy with the rugged and portable coolant cleaning system from Freddy (UK). On show will be the standard and custom Top/Soft Jaws from Dimac’s design and manufacturing facility in South East Melbourne that can solve just about any workholding challenge on your CNC lathe. Dimac is motivated to continually finding more effective, safe and productive ways to hold and machine workpieces. They manufacture Soft Jaws, Hard Jaws and Custom Jaws in their own CNC equipped machine shop and this capability, coupled with over 30 years experience doing so, ensures they will provide the right workholding solution for you. When you visit Dimac’s stand, you also can discuss automation solutions to overcome production and skill shortages where you can start with very simple and basic tools and devices through to full turn-key solutions. Dimac looks forward to welcoming you to the Dimac stand.
Dimac Tooling Pty Ltd Stand MT06 dimac.com.au
Integra Systems still riding high
The last time Integra Systems appeared at Australian Manufacturing Week in 2019, the team was riding high as finalist for the Leader in Industry 4.0 category at the Victorian Manufacturing Hall of Fame Awards. Now, they’re keen to show us their progress in the digitisation of manufacturing with an eyeopening display at this year’s event.
While dealing with the disruptions caused by a global pandemic, Integra Systems took the opportunity to hatch a dream that was three years in the making: their K4.0 Kiosk concept. The concept was so successful it’s been commercialised so other manufacturers can now revolutionise their enterprises with this fully customisable, fully digitised system. Designed to meet the goals of the circular economy, the K4.0’s operational design replaces mountains of manual tasks and paper trails with integrated digital workflows, completely reimagining traditional manufacturing processes. It comprises a series of easyto-use and customisable kiosks that can function as virtual ‘job bags’ for industrial applications operated via touchscreen or even touchless ‘gesture’ control. The K4.0 Kiosk will feature on Integra’s stand at Australian Manufacturing Week where other manufacturers can see how to take the evolutionary leap into Industry 4.0. Having functioned as their own guinea pigs, Integra is eager to share their expertise and help you benefit from the increased appetite for Australian manufacturing while successfully transitioning into the industry’s next new, exciting phase. Along with the K4.0 Kiosk design, Integra will showcase two standout examples from their WorkSMART Collection: AeroSMART Industrial workbenches and BioSMART Mobile workstations. Given today’s strict OH&S compliance in workplaces, WorkSMART Collection overcomes ergonomic challenges while significantly increasing user satisfaction. From office to factory floor, these two designs offer a new way of working that is fully adjustable for maximising productivity and minimising risk. Furthermore, they’ve been designed and created according to the reduce, reuse, recycle and redeploy principles of circularity, similar to the K4.0. While AeroSMART, BioSMART and the K4.0 will be demonstrated on the Integra stand, bear in mind, what you see is not necessarily what you have to get. That’s because everything Integra creates is fully customisable in the truest sense of the term – you ask for it, Integra builds it. Based on their past appearances, we’re positive Integra Systems will have something for manufacturers to get really excited about at this year’s Australian Manufacturing Week. As well as their Industry 4.0 innovations, the team is ready to chew the fat with you about industry challenges and support you to help ‘Make Your Vision Real’ – as their tagline goes – with bespoke product development and advanced manufacturing services.
Integra Systems Stand MP45 integrasystems.com.au
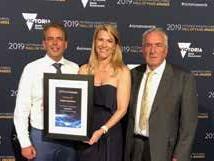
Ultimate LED shining a light
Demonstrating continuing improvements of the LED Workplace Safety Halo System.
Ultimate LED is an Australian Family Business established in 2012 in Coffs Harbour, NSW. Director Warren Hodder has always been in the motor vehicle and transport industries. The company is consistently looking outside the box for special safety products to pro-vide a safer workplace. Back in 2016 Warren developed the LED Workplace Safety Halo System, since then he has improved the performance of the LED red line beam and through some special help created a safe class 2 Laser red line beam for workplace safety. This is the first of its kind in the market globally. Pushing the boundaries of where lights can be shone, LEDs have long life, are incredibly energy-efficient, resistant to vibration and moisture incursion. LEDs are easy to install and are much faster to reach full intensity than standard light bulbs. This translates into an added safety benefit for using LEDs for your trailer's stop lights. Standard stop lights take a quarter of a second to reach full intensity whereas their LED counterparts take less than half this time.
Ultimate LED Stand MS87 ultimateledlights.com.au
066 PREVIEW Power Machinery brings in the sawing machines
Power Machinery is excited to be back on home turf at such a fantastic venue. Darling Harbour Exhibition Centre is a great location, not just for the show but also for visitors and exhibitors after hours. The restrictions opening means that our friends from MEP in Italy can join us again, which is good news. And since it has been a few years since our last show, we are excited to have a new range of Metal Cutting Bandsaws and the opportunity to chat with old customers and new ones. Produced in Pergola, Italy, since 1964, the product range includes Metal Cutting Bandsaws, Metal Cutting Coldsaws and aluminium Cutting Saws. There are a few reasons why it might be time to upgrade to a new Sawing machine. • Improved reliability • Increased capacity • Improved safety • Improved repeatability Or perhaps it is because as much as you love your old MEP saw, 25 years of faithful service has finally taken its toll. Power Machinery has partnered with MEP in the Australian market for over 25 years. We have factory trained engineers ready for service and a full complement of spare parts available for even some of the pre-2000s machines. They are our most active and dynamic supplier. MEP is continuously looking to evolve and innovate and never resting on its laurels. The recent acquisition of the American Saw manufacturer added another string to their bow and gave the group new capacity in the over 300mm market. The range of MEP saws is comprehensive, covering everything from 200mm handoperated saws to massive fully automatic hitch feed saws with 1000mm capacity. Any fabricator that has used a MEP Shark Saw, whether a manual CCS version, a Semi-Automatic SXI or Automatic AX or NC Evo, is unlikely to be satisfied with any other brand. The unique combination of traditional cast-iron structures and the latest technology makes MEP saws the market leaders. On display will be a range of Sawing machines.
MEP Shark 230NC 5.0 is a straight-cut double column automatic metal cutting hydraulic bandsaw. A “Full In Box” design with cast iron bow and band wheels. The protective guards fully comply with the latest machinery directive AS4024 and EN13898/2007. This model is highly robust and capable of continuous cutting at maximum capacity of 230mm solid bar. It can also automatically feed material until only 70mm of material remains. Operation is by a 180mm touch screen control. It is simple to use and program with a Windows CE based CNC that manages all cutting parameters and functions in real-time. The MEP Shark 331-1 NC 5.0 Spider is an automatic hydraulic bandsaw built in a cast iron construction to cut from 0-degree right to 60-degree left. The metal cutting saw is a compact design with a minimal footprint with a 180mm Touch Screen control. It is simple to use and program. The Windows CE based CNC manages all cutting parameters and functions in real-time. The cutting head and feeding vice can also be positioned manually by the joystick control. The Bar feed is by ballscrew and stepper motor. You can program different lengths and batch numbers on one length of material. There will be three Semi-Automatic versions. The Sharks 282SXI,382-1SXI and 512SXI. All models cut from 45° right to 60° left with four modes of operation; Manual, Dynamic, Semi-Automatic and Cycle Down Up. Each with a centralised control panel provides all information required by the operator, including alarms, diagnostics, pieces cut, cutting time and blade tension. We will also have one saw fitted with the latest programmable length stop from Arostop.
Power Machinery Stand MT38 powermachinery.com.au
Two sides to every business
Acra Machinery successfully bringing the new and refurbished machinery into the Australian manufacturing sector
Acra Machinery provides an array of metalworking machinery to the Australian manufacturing industry including, but not limited to, sheet metal, fabrication, defence, construction, transportation and healthcare sectors. They assist and consult businesses, both small and large, in advancing in their machinery and automation technologies to promote growth of manufacturing capabilities throughout the whole of Australia. Established in 1977 with a team of fully qualified, full-time service engineers, they have been able to create and maintain a reputable name throughout the industry as a premier supplier of capital equipment with a top-tier level of aftersales service and support. Acra Machinery is a certified dealer of high-quality European equipment with full support from their international partners. In 1986 Acra Machinery bought the manufacturing rights from Leeton Steel Works for all Acra products, including spare parts. It was about that time Acra Machinery became a company with the intention of continuing to build Acra Machines in Australia, however economic reality at the time made this dream impossible. However, the second-hand side of the business was growing larger each year, and Acra still needed a supplier of quality new machines. Acra traveled to Europe and America several times looking at all the machines available until they finally partnered with a previously unheard-of Manufacturer in Turkey, Durmazlar in 1994. Since then, Durmazlar has grown to be the largest Press Brake manufacturer in Europe and the second largest in the world, spanning an impressive 155,000 square meters of factory. They are now manufacturing over 5,150 high quality machines annually. Going forward ACRA are committed to the further expansion of our range to cater for the Australian sheet metal, machine tool and steel building industry.