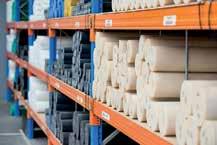
3 minute read
Wearable power generators whip up watts while walking
from AMT JUN/JUL 2022
by AMTIL
customised shape and even functionality is important, for example, medical devices such as hearing aids and prosthetics. The ability of 3D printed electronics to manufacture different components using the same equipment, and the associated decoupling of unit cost and volume, could also enable a transition to on-demand manufacturing. The challenges for fully 3D printed electronics are that manufacturing is fundamentally a much slower process than making parts via injection moulding since each layer needs to be deposited sequentially. While the printing process can be accelerated using multiple nozzles, it is best targeted at applications where customising offers a tangible advantage. Ensuring reliability is also a challenge since with embedded electronics post-hoc repairs are impossible – one strategy is using image analysis to check each layer and perform any repairs before the next layer is deposited.
Comprehensive analysis and market forecasts
The new IDTechEx report “3D Electronics/ Additive Electronics 2022-2032” assesses the competing technologies that will enable PCBs to be replaced with integrated electronics, saving space, weight and reducing manufacturing complexity. It covers electronic functionality to 3D surfaces, in-mould electronics (IME), and fully 3D printed electronics. The report includes multiple company profiles based on interviews with major players across the different technologies. There are 10-year market forecasts for each technology and application sector, delineated by both revenue and area. It also forecasts the gradual decline of LDS and growth in extruded paste for consumer electronic antennas, and increased use of extrusion and aerosol, especially for automotive applications. The most substantial growth is predicted for IME, which is predicted will be widely adopted in car interiors and the control panels of white goods. IDTechEx.com
Wearable power generators whip up watts while walking
Researchers from Loughborough University in the UK and the University of Moratuwa in Sri Lanka have developed a new, scalable manufacturing technique to create wearable fabrics embedded with small power generators known as triboelectric nanogenerators (TENGs).
The technique, detailed in the journal ACS Applied Electronic Materials, enables the creation of energy-generating textiles using established methods such as yarn coating, dip coating and screen printing to apply triboelectrically active solutions. The wearable, TENG-containing fabrics are similar in texture to knitted materials used to make jumpers and T-shirts, but can produce electricity to operate low-power electronics using our natural body movements. TENG devices collect static charges, like those that make a balloon stick to a wall when rubbed against a jumper. Once attached to the human body or clothing, TENG devices ‘slide’ or ‘vibrate’ with movements to create an electrical signal through a process called electrostatic induction. The new technique overcomes these issues by combining new conventional textile materials and carefully engineered TENG device designs. These devices display improved electricity generation and meet most of the comfort and durability requirements for textile products — a balance that has been very difficult to achieve so far in TENG research. The 4x4cm, lightweight TENG textile the researchers created produced over 35V using mild artificial movements that replicated slow body movements, which could potentially power low-power health sensors, environmental sensors and electronic devices in the near future. Study leader Dr Ishara Dharmasena, from Loughborough’s School of Mechanical, Electrical and Manufacturing Engineering (MEME), said the technology will be “massively beneficial for future smart textile and wearable electronic applications” and could support the global shift to remote health monitoring. “This work will lead to further research on how we can convert the common textiles into energy-generating clothing for various future applications including health care, communication, sports and personal electronics,” Dharmasena said. Dharmasena and his team are now looking at practical applications of TENG technology and are keen to hear from industrial and academic collaborators in the areas of smart textiles, health sensing technologies, nanotechnology and fabrication.
lboro.ac.uk
The one stop online shop for engineering plastics Wide range of engineering plastics Free delivery nationwide for orders over $150.00+ gst 24 hour operations for live orders Best business to business pricing
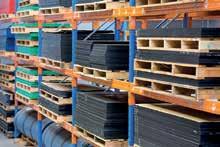
Acetal Cast nylon 6 HDPE PTFE UHMWPE Poly Carbonate – AR2 abrasion resistant 2 sides PEEK
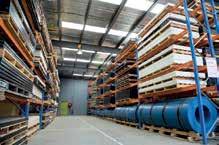