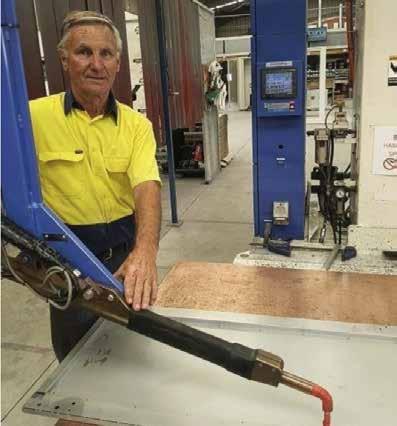
3 minute read
The special spot welding solution from Queanbeyan
from AMT JUN/JUL 2022
by AMTIL
Precision Metals Queanbeyan adopts a special spot welding solution
Based in a regional area of NSW, Precision Metals Queanbeyan has developed into a successful business by providing high level services and products to their customers across the nation.
Started in 1984 to support a fledgling electronics business with metal brackets and enclosures, demand from local small businesses for bespoke metal work increased rapidly over the next few years, and as growth continued, Precision Metals Queanbeyan realised the need to invest in technology if they were to meet the demand. As early adopters of CNC equipment, they were able to compete for larger contracts throughout Australia, supported by their highly trained staff to provide first class sheet metal products to all sectors of industry. Today, Precision Metals Queanbeyan continues to develop highly skilled tradesman, via their constant apprentice intake, and providing them with advanced tools that include some of the best equipment available, including CAD, CNC laser cutting, CNC folding, and all the welding and finishing equipment usually found in a sheet metal fabrication business. But it was an unusual investment that has really made a standout contribution to capability and productivity. Bob Campbell, founder of Precision Metals Queanbeyan, remembers the first time he saw the MySpot Table Spot Welding Machine at the Austech exhibition at Sydney in 2006. MySpot can be described as a machine with a large flat copper table, which is also the lower electrode and a free moving articulated arm as the upper electrode, guided into place by the operator to the exact weld position required, and then performing the perfect spot weld. That was a standout of the machine! I clearly remember, the quality of the weld, it was so impressive. “I was initially thinking that this type of machine wouldn’t be able to do any of our parts.” The concept is the opposite of what we do on a traditional type of spot welder, holding the workpiece between the electrodes while trying to keep it in place and level, while many times unable to know exactly where the weld will take place because the welding position was facing away towards the machine. Some parts were particularly heavy and awkward in shape, hard to handle, and then the distortion and surface finishing, dressing the electrodes, it was all hard work, and not everyone was able to do it properly. It was time consuming, and a lot of rework was required constantly. “However, once I understood the MySpot concept, we invested in the model with the largest table available. Instantly we realised that most of our existing spotwelding work could be done faster and better on the MySpot. The table provides a perfect location to assemble and weld the components together. The distortion is gone, the weld quality is exceptional, and surface finishing before powder coating is now rarely required. And no more rework! The MySpot Table Spot Welder is now one of the most trusted machines in our shop. So much so, we purchased a second machine featuring a vertical gun as well as the horizontal gun to provide us with additional capability. Any of the team can use our machines due to the MySpot Touch Screen Controller that provides access to programs to weld all the materials and thicknesses we need to weld. “All welding parameters including tip pressure are assured, just select the material and then the thickness, and start welding. The upper electrode system consists of a long horizontal gun that allows access into deep parts, and the vertical gun that can reach into items not suitable for the horizontal gun. The machines are supplied with a variety of shanks and consumable caps, that are easily changed over if required. The cap system is actually very good as the water cooling goes right to where the welding happens, keeping the cap cool to touch. This not only improves the weld result and consistency, it also extends the life of the electrode. “Dressing is done by the supplied pneumatic tip dresser at predetermined intervals as set on the controller. Overall, by introducing such a unique machine we have been able to improve our spot welding on existing parts, as well as attract new customers due to the productivity achieved, and by being able to assist in the designing of their projects to include spot welding rather than MIG and TIG welding wherever possible. This not only improves turnaround time, but it also greatly reduces the input costs of labour. “ MySpot enables Precision Metals Queanbeyan to compete for work against competitors based in larger population centres despite the disadvantage of being regionally based. Our MySpot machines were locally supplied by the Australian and New Zealand Agent Jim’s Machines and Accessories.