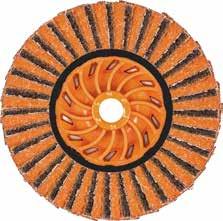
4 minute read
Getting the most out of your flap disc
from AMT JUN/JUL 2022
by AMTIL
Get the most out of your flap disc
Selecting the right shape of flap disc will help operators get the job done faster, allowing them to achieve a smoother and more uniform finish without gouging the workpiece.
Whether you are looking to grind down or remove welds, deburr, bevel, or prepare a paint-ready finish, flap discs are most likely your go-to solution. Metalworkers rely on them for their comfort, versatility, high productivity, quality finish and long product life. Enhance both quality and productivity when working with heat sensitive metals by using specially formulated flap discs. Each task and applications have their own unique challenges. Having the right tools for the job can help manufacturers, metalworkers, and welders achieve significant time and cost savings. Using the wrong abrasives can lead to a poor removal rate, affecting the surface finish, as well as the wheel being discarded before it has been fully used. A long, unproductive process can also result in increased operator fatigue. When considering a flap disc, the operator must consider three main factors: • Productivity • Quality finish • Safety and comfort Maximise productivity
Flap discs come in a variety of abrasive materials. Opting for a flap disc made from zirconia alumina will result in a long product life and provide the lowest overall cost of use when factoring in the longevity of the products. It allows the operator to save time and money due to the fewer disc changes and high removal rate. If you are looking to maximise your productivity, flap discs with premium self-sharpening ceramic grain provide a faster removal rate, which makes them ideal for heavy-duty applications. Discs that are made with cold-cured glue that is air dried at room temperature have a longer service life as the abrasive flaps’ properties are not altered during the heating process. Selecting the right shape of the flap disc, flat (type 27) or conical (type 29) will help you get the job done faster. For blending, finishing and general applications on flat surfaces, using a type 27 will lead to the best performance. If you are looking to remove a lot of material quickly, type 29 flap discs are ideal for contoured and edge work, as well as other finishing applications. They provide a high stock removal given their increased angle of attack. Trimmable flap disc backings made from less dense wood fibre composites are designed for easy and safe trimming. It also extends the life of the disc by allowing fresh cloth to be exposed to the workpiece, which again gives you a fresh new cutting edge. Although most flap discs with a plastic backing can be trimmed, it does not mean that all discs can be trimmed safely. Trimming a plastic backing not marked trimmable could cause failure. The WALTER flap discs specially marked “Eco-trim” for trimming have a special blend for the backing material to gradually shear rather than chip or break away. Remove material faster and achieve a smooth finish in fewer steps with the ENDURO-FLEX 2-IN-1 TURBO. The low heat generating sanding flaps are designed for cool cutting and high removal rate. Blendex flaps offer surface conditioning materials that blend scratches without smearing or contaminating the workpiece, allowing you to blend and finish the surface in one step. Flap discs allow operators to achieve a smoother and more uniform finish without gouging compared to a grinding wheel. What sets flap discs apart from bonded abrasives is their layered construction. These flaps can either be made from a single material such as cotton and polyester or from a combination of two different materials (sanding and Blendex flaps) — making them ideal for blending down welds and finishing a workpiece at the same time. For a quality finish, ferrous-free abrasives guarantee that there are minimal traces of iron, sulphur or chlorine to meet quality control objectives in sensitive operations. You may already know what finish you can expect from different grits (i.e., 40, 60, 80, 120, etc.), but certain premium flap discs offer a unique dual grit 36/60, which removes the material quickly but leaves a finer paint-ready finishing, saving you a valuable step in your finishing process. Premium flap discs also offer specific and specialised solutions designed for stainless steel, aluminium and non-ferrous metals. Integrating those specialized solutions in your processes will guarantee a consistent finish without discoloration and avoid clogging. Backing pad designs are also important as they can contribute to ventilation, improve discs durability, and reduce discolorations. By funnelling in air, it minimises heat transfer to the surface which keeps the workpiece cooler and increases the disc life. Experience safe and comfortable blending

Metal shops are recognising the importance of workers being able to do their jobs more efficiently, comfortably and with less fatigue. Flap discs are quieter and create less vibration and dust, making them more comfortable for operators to work with, which reduces the requirement for rework. To ensure the safety of the operator, make sure the flap disc is balanced and complies with ANSI B7.1 standard. This will guarantee vibrationfree weld blending leading to greater performance and operator comfort.
walter.com Courtesy of Fabricating & Metalworking fabricatingandmetalworking.com

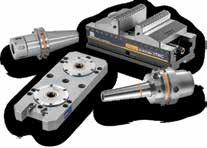