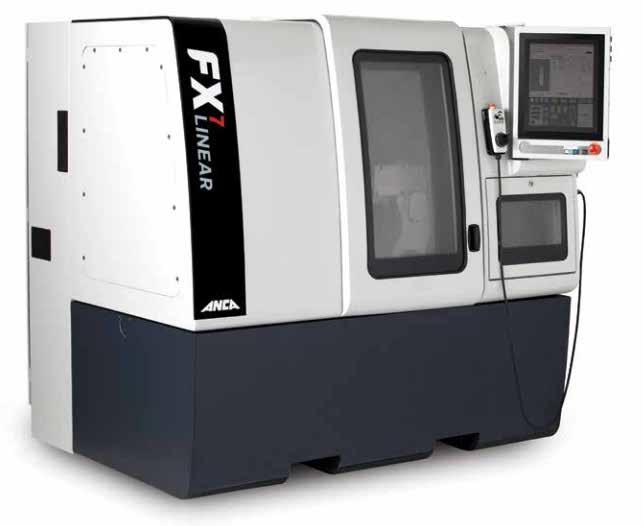
3 minute read
Foxy at Sutton Tools
from AMT DEC/JAN 2023
by AMTIL
Foxy
The ANCA FX7 Linear CNC grinding machine.
Australian manufacturing is in the process of a making a large pivot. With the state the world is currently in; recovering from the covid pandemic, and growing tensions between the West and East, supply chains are being rethought. The increasing need for sovereign capability and low cost but high quality product is becoming more and more evident. This is also the case for not only defence related products, but supply chains for the DIY enthusiast. Finding good quality product within a reasonable time, is almost impossible when it is made internationally. The US and Australia are becoming less reliant on international suppliers and relying far more on each other for manufacture and supply of goods. The type of products required are of high precision and tolerance, requiring significant machine investment to service such critical and large volume orders. With current abilities many manufacturers are struggling to meet the requirements of the newly found volume of Production with the current machines. At Sutton Tools there is a significant push to increase not only quality, but volume and capability. With that said, we introduce the newest member to the Sutton Family; FOXY. FOXY is an ANCA FX7 Linear CNC grinding machine. The pinnacle of flexibility and automation when it comes to tool grinding. ANCA’s new FX7 Linear CNC grinding machine is positioned at our Carbitool manufacturing plant in Moorabbin alongside ANCA MX7 and RGX machines. We use the FX7 to regrind cutting tools, as well as assist with the manufacture of high-performance cutting tools. Its latest software, linear rails, laser tool checker, tool loader and rigid spindle place CBT at the forefront of technology so that we can continue to improve our cutting tool manufacturing. But the power of FOXY doesn’t end there. The newly installed tool management system uses Radio Frequency Identification (RFID) that works with the Schunk Collet Changing facility, allowing us to grind tools of varying diameters and types without a human being present. Furthermore, FOXY was retrofitted with dynamic tool loading hardware and software, making it easier to operate. As an industry leader, ANCA promises its customers tailored, diverse, and quick setup options. The ANCA FX7 provides more flexibility and capability for unattended production of wood tools. FX7 is versatile enough to handle very different types of tools. They also offer the ability to automatically change production between different tool blades and solid round shank tools such as routers and drills used in the production of furniture and cabinetry. This is accomplished by offering a choice between two types of work holding: the blade chuck and the PremierPlus collet chuck. It takes only a few minutes to switch between the two systems because they use the exact same pull stud mechanism. A tool carrier containing an RFID chip is paired up with all the information that pertains to the tool (tool grinding file, grinding wheels, loading process, and collet diameter) before this “magic” can take place. A network-connected scanner pairs tools to chips in their carriers off the machine. We can load up to 88 tools in the loading station carriers per session. Upon loading the tool into a carrier, the Fanuc robot carries it to an internal scanner. Through its internal scanner, FOXY can read the chip and know precisely what is required for grinding the tool. In addition, the Fanuc robot will assist in changing collet sizes if necessary, changing wheel packs when needed, moving the tool from load station to collet, and returning home after grinding is complete. FOXY and Fanuc robot are always one step ahead in preparation for the next tool to be ground and will keep grinding until they run out of tools. This ANCA FX7 Linear is the second machine in the world to have this gamechanging technology. Robotic automation allows for easy transition between profile blades and round shank solid carbide tools, such as spirals, compression routers and drills, without changing grippers or retraining the robot. Simply change over the pallets to suit the tool type and size, and you are ready to start unattended production. In addition to a reduced turnaround time for tool regrinds, we look forward to many hours of unmanned machine time. suttontools.com
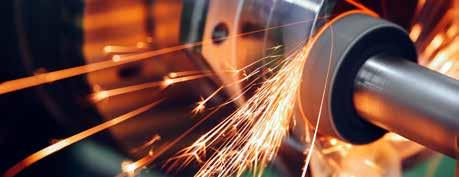