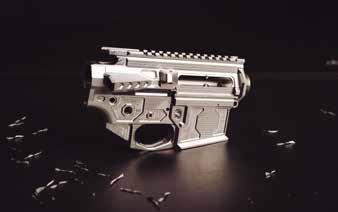
7 minute read
Boss Tooling
from AMT DEC/JAN 2023
by AMTIL
OKUMA machines Boss Tooling
Industry passion strongly evident at Boss Tooling.
To visit Boss Tooling in Melbourne’s manufacturing heartland of Dandenong South, is to witness a team with an outstanding passion for the industry, high integrity in performance for the customer and an unbelievable work ethic that will ensure success for this growing business. Boss Tooling was established in 2013 by Partners and Directors Simone Kramer and Brian Cogley. Located in a small building within a business complex, their original purchase was a second hand Okuma machine at auction and this was ultimately upgraded to 4 axis. From one machine Brian and Simone purchased another second hand machine privately in a brand that Brian had been familiar with during his training and with business continuing to expand, an additional new 4 axis Okuma Machining Centre was also commissioned early on. Prior to the pandemic the company experienced a quiet period which was of concern to the young couple so a rather nervous and inexperienced salesman Brian, set out on a sales mission to drum up business and expose the company’s capabilities to industry. His technical knowledge soon shone through and after a face to face call of some two hours discussion with a potential customer, new business was assured. This cold call turned out to be a catalyst for the continued growth of Boss Tooling with this business now a key customer for the fledgling company. Servicing clients in a range of industries Australia wide, the company specialises in highly sophisticated intricate products in shorter runs such as components for firearms, medical, oil rigs, specially designed cutting tools, etc. Boss Tooling has also invested in the latest 5 axis CAM/CAD software. To meet the demands of the expanding business, to expand their capabilities and fulfil customer expectations, Boss Tooling has recently commissioned an additional new OKUMA GENOS M460V-5 axis Machining Centre. The new generation 5-axis OKUMA Vertical Machining Centre is specifically designed to manufacture high precision parts and deliver impressive metal removal rates in a compact design. Its solid double-column structure, full 5-axis simultaneous control and thermal stability performance gives it the reliability to easily cut a variety of materials. “From day one with a second hand machine,” describes Cogley, “Okuma engineers have supported us with technical expertise and assistance particularly when upgrading our first machine. If it’s not a personal call from a technician their technical assistance by phone is just excellent,” he said. ”Time permitting we plan to take advantage of the ongoing training offered by Okuma but with just three of us in the team at present, including Simone’s sister, Melanie, the workload does not allow us much spare time.” “The new OKUMA GENOS Machining Centre provides us with even greater capabilities for intricate work, it is quick to set up and the cycle times are greatly improved,” said Cogley. “With such high levels of support from Okuma we plan to grow the business with this company going into the future.” Expansion plans are certainly on the agenda for Boss Tooling and given the tight working conditions within the present building with four operating machines, a new factory will ultimately provide much needed space for further development and growth. “The Boss Tooling work ethos fits perfectly with Okuma with each having a passion for the industry and service for our clients,” said Mark Richards, Branch Manager – Victoria & Tasmania for Okuma Australia. “It is exciting to see young people like Simone and Brian with such passion and obvious skills, developing a successful business going forward as a team and we look forward to working with them to meet their objectives,” he said.
bosstooling.com.au
Boss Tooling team L-R Simone Kramer, Brian Cogley, Melanie Kramer.

Aluminium Council
Australian Aluminium Council Welcomes Mission Possible Partnership’s Aluminium Transition Strategy.
The Australian Aluminium Council (the Council) has joined with its Members and other industry leaders in welcoming the Making Net Zero Aluminium Possible: A Transition Strategy for a 1.5° C-compliant Aluminium Sector (the Strategy) developed by the Mission Possible Partnership in collaboration with the International Aluminium Institute, released today at the New York Climate Week. The Strategy is an ambitious but achievable decarbonisation roadmap for the global aluminium industry. Aluminium is a critical material in the context of the global energy transition. It is anticipated that global demand will increase by almost 80% (from 2020 levels) to 179 million tonnes per year by 2050. The Council’s CEO Marghanita Johnson said “This work has brought together companies across the global industry, including those operating across the value chain in Australia. The Strategy recognises that it is possible to meet rising aluminium demand, reduce emissions from the sector to net zero by 2050, and align with a 1.5°C target.” The Strategy highlights that a global investment of approximately US$1 trillion will be required for the aluminium sector transition, including significant investment to supply the required zeroemissions electricity. Ms Johnson added “The Strategy outlines not only actions the industry needs to take, but also actions required by Governments to support this. In particular, developing policy which is predictable, stable and transparent will enable businesses to confidently plan for this substantial investment.” Governments also have a vital role to play designing electricity markets to support the transition and minimising the risks of carbon leakage. Decarbonising electricity supplied to aluminium smelters globally by 2035 is a key milestone for the industry in the Strategy. Ms Johnson observed “The owners of Australia’s four smelters have signalled their desire to recontract renewable electricity at the end of their current terms(2025-2029).” Over the longer term, smelters play a key role in being more flexible users of power to help balance variable generation grid systems. The Strategy notes that aluminium smelters in Australia are providing a leading role in already delivering this flexibility. Ongoing collaboration within the sector and partnerships with government will be a key enabler for the Strategy. “While Australia’s alumina industry already has some of the lowest emissions in the world, new technologies will be needed to decarbonise the alumina refining process. Alumina research headquarters for Alcoa, Rio Tinto and South32’s Worsley Alumina are all based in Australia, helping develop new technologies for the global industry”. We welcome the support already shown by the federal and state governments for that research, while noting the scale of the challenge ahead. The Strategy indicates that for the “digestion” phase of the refining process, while a range of solutions will likely become commercially available in the late 2020s, their suitability depends on local conditions, particularly the availability of zero-emissions electricity. Access to this zero-emissions electricity could be the rate-limiting step for deployment of these new technologies. “As noted in the Strategy, the deployment of inert anodes in smelters and electric or hydrogen calcination at refineries, are not expected to be ready for large-scale deployment before 2030. Both also remain contingent on sufficient supply of zero emissions electricity and green hydrogen. “Decarbonisation of Australia’s electricity supply is the single biggest opportunity to decarbonise the vertically integrated domestic aluminium industry in the coming decade.”
aluminium.org.au
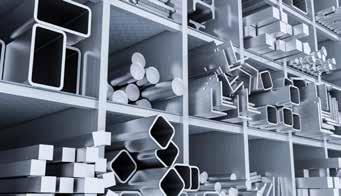
Titanium alloy
Monash engineers create the highest specific strength titanium alloy using cutting-edge 3D printing techniques.
Monash University engineers have created an ultrastrong titanium alloy, the highest strength-to-weight ratio among all 3D-printed metals to date, creating unprecedented mechanical performance. A world-first study led by Monash University engineers has demonstrated how cutting-edge 3D-printing techniques can be used to produce an ultra strong commercial titanium alloy - a significant leap forward for the aerospace, space, defence, energy and biomedical industries. Australian researchers, led by Professor Aijun Huang and Dr Yuman Zhu from Monash University, used a 3D printing method to manipulate a novel microstructure. In doing so, they achieved unprecedented mechanical performance. This research, published in Nature Materials, was undertaken on commercially available alloys and can be applied immediately. “Titanium alloys require complex casting and thermomechanical processing to achieve the high strengths required for some critical applications. We have discovered that additive manufacturing can exploit its unique manufacturing process to create ultrastrong and thermally stable parts in commercial titanium alloys, which may be directly implemented in service,” Professor Huang said. “After a simple post-heat treatment on a commercial titanium alloy, adequate elongation and tensile strengths over 1,600MPa are achieved, the highest specific strength among all 3D printed metal to date. This work paves the way to fabricate structural materials with unique microstructures and excellent properties for broad applications.” Titanium alloys are presently the leading 3D printed metal components for the aerospace industry. However, most commercially available titanium alloys made by 3D-printing do not have satisfactory properties for many structural applications, especially their inadequate strength at room and elevated temperatures under harsh service conditions. The findings in this work are expected to lead to fundamental insights into the principles of strengthening and dislocation engineering in the field of physical metallurgy. Professor Huang led the research titled: ‘Ultrastrong nanotwinned titanium alloys through additive manufacturing’ with Dr Yuman Zhu from the Monash Centre for Additive Manufacturing.