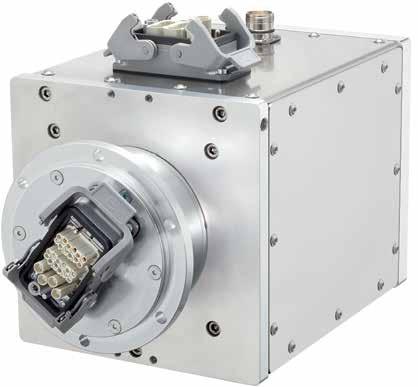
2 minute read
MEGA torque wrench
from AMT AUG/SEP 2023
by AMTIL
Digital MEGA torque wrench for precision milling.
If you need to achieve milling precision, the new Digital MEGA Torque Wrench from BIG KAISER is the best way to achieve the secure and accurate tightening of collet chucks. This new wrench has a user-friendly digital interface and interchangeable head sizes for the secure and accurate tightening of collet chucks.
The BIG KAISER torque wrench has multiple settings to ensure the right torque is applied to the clamping of cutting tools. The recommended torque for each compatible BIG KAISER collet chuck model is pre-set, and the correct tightening torque is easily available by simply choosing the model to be clamped. With a clear display, the torque wrench is easy to use and it combines a four-digit digital display with a high-precision five-level LED bar graph. When tightening is complete and the recommended torque is reached, the wrench vibrates and emits a warning beep, to alert the user. “Having correctly clamped tools is extremely important for all collet tool holders. Precision and holding force can only be guaranteed with tools that have been clamped with the right torque setting,” said Giampaolo Roccatello, Chief Sales & Marketing Officer for Europe at BIG KAISER. “Additionally, manual assembly holders have a far longer lifetime than heat shrink holders that wear out a little every time they are clamped. This means they are better for the environment and cheaper for the user.”
The Digital MEGA Torque Wrench provides a cost-effective alternative to expensive torque measurement machines. It is a
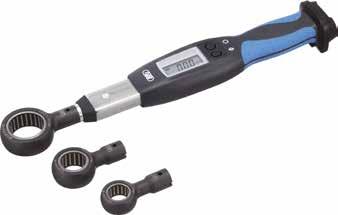
Kübler slip ring
much more flexible option than regular torque wrenches that have a very limited clamping range. Historically, a customer would require many wrench sizes to cover the entire range of MEGA6 to MEGA20 collets – this is no longer the case. The new torque wrench is also a better choice than typical freewheel wrenches that do not have any torque indicator, which results in the tool easily being clamped too much or too little – a factor that can significantly impact precision.
The torque wrench is powered by a built-in lithium battery that provides up to 4,000 tightening operations from a full charge. The battery takes three hours to recharge and has a lifetime of approximately 500 recharges. The Digital MEGA Torque Wrench is designed for use with cylindrical nuts up to 46mm and can be used with MEGA Micro, MEGA New Baby, and MEGA E chucks. The wrench has a torque range from 5 to 50Nm.
bigdaishowa.com
Slip ring with integrated sensor system ready for Industry 4.0 applications.
Kübler continuously shows how slip rings can be used as Industry 4.0 enablers in future applications and Industry 4.0 concepts. In addition to the reliable transmission of current, signals and data with Kübler slip rings, further data such as temperature, service intervals and with integrated sensors, speed and position are now also recorded. All this data is available for condition monitoring, lifetime histograms or electronic nameplates. Predictive maintenance is then achieved in line with Industry 4.0 and maintenance of the slip ring is therefore carried out early or on time due to its condition. The result is high system availability and perfect use of the Kübler slip ring. Thanks to the innovative contact technology, the slip ring is particularly low-maintenance and durable. The high degree of protection IP64 and optional IP67 also contribute to maximum reliability.
The smart slip ring SRS250 transmits up to 600V/100A as well as Industrial Ethernet communication and analog signals (0 ...20 mA, 0 ...10 V, Pt100 and thermocouples) reliably and trouble-free. Each Kübler slip ring is an individual solution and they stand for maximum adaptability. Various connection options as well as the modular and robust design ensure maximum integration in the plant/machine. The electronic name plate of the slip ring is used for simple commissioning of the slip ring and later for asset management. kuebler.com/iiot
Slip ring with integrated sensors for industrial 4.0 applications. In addition to the transmission of current, signals and data, other status variables are recorded and made available for condition monitoring.