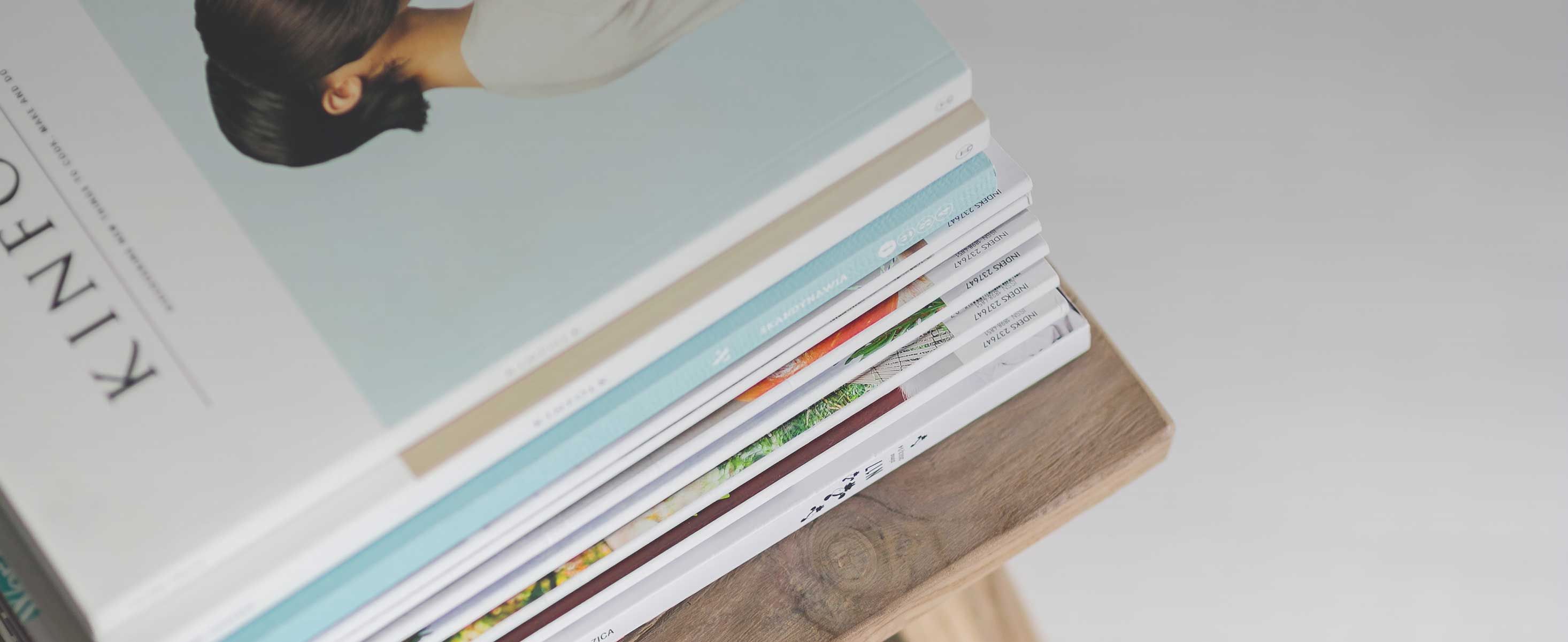
1 minute read
Raymax coaxworks
from AMT AUG/SEP 2023
by AMTIL
Laser welding heads for laser wire deposition, 3D metal printing and repair cladding. various advantages such as clean machine conditions as well as visualisation by camera technique, with wire spools able to be stored safely for long periods.
Due to the demand in laser wire welding, Raymax Applications Pty Ltd is now offering laser wire welding heads from coaxworks GmbH. Two product series for different power levels are available. The industry established wireM with flexible configuration options, is suited to processing in the laser power range of 4kW. The latest wireXL was introduced in 2023 and is suitable for efficient processing in the power range up to 10kW. Both laser wire welding heads are based on the coaxial 3-beam design with centric wire supply. With this direction independent functionality, they are highly suited for cladding processes like metal coating, repairing and generative manufacturing (3D).
Three coaxial laser beams melt the wire continuously, creating a round melt pool. Regardless of the direction in which the laser welding head moves over the workpiece, the weld seam maintains the same shape. In addition, horizontal and upward welding positions are possible providing additional flexibility. With 4kW of laser power, up to 2.5kg/h deposition rate is achievable using steel wire. Unlike welding with metal powder, a real advantage with the laser wire process is stability achieving 100% material utilisation during deposited. As the energy of a laser beam can be focused very specifically, the area around the weld seam is hardly affected as the temperature-related distortion is lower than with other welding methods. The use of welding wire as a filler metal offers
The wireM coaxial laser welding head is an interchangeable solution for use with a robot or CNC laser processing machine. Robust, compact, and simple to operate they are suitable for Laserline high power diode lasers or fitted to a disk or fiber laser. An optional shielding gas nozzle can be integrated into the wireM reducing oxygen in the atmosphere and preventing the welding material reacting to air particularly when welding stainless steel and titanium alloys. By using the SGC500 shielding gas chamber a fully inert atmosphere with a residual oxygen content of 20ppm, will prevent oxidation and tarnish during the work process.
Launched in 2023, the new innovative wireXL laser head from coaxworks, is a high-performance solution for both wire cladding and wire-based additive manufacturing. With a range of 10kW laser power and new digitalised functions, a deposition rate of up to five kg/h is possible for steel wires using the unique directionindependent three-beam concept. Other materials such as nickel, titanium, copper and cobalt alloys extend the application range. This flexible addition to welding and repair cladding is available with advice, support and training for local customers. raymax.com.au