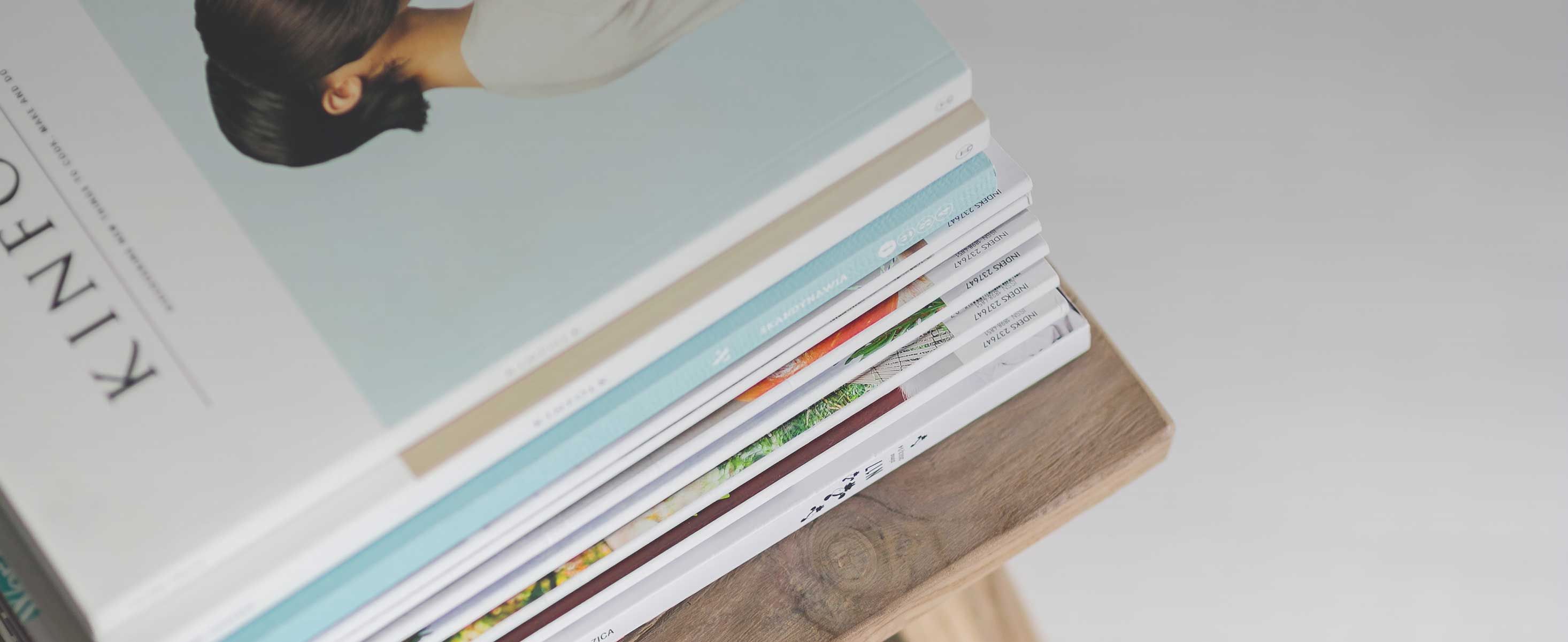
4 minute read
Kübler on Industry 4.0
from AMT AUG/SEP 2023
by AMTIL
of Industry 4.0, and tackle the unique challenges and opportunities that each customer faces as they embrace it. We want to help make smart industry, simple."
Telstra's Industrial Automation capability offers holistic solutions, spanning private networks, internet of things (loT), IT/OT convergence, cybersecurity, analytics and Al, cloud and edge, and professional and managed services. Burns said the combination of Telstra's expertise and technology had the potential to make a big difference for Australia's heavy industries, particularly for their workers. "One of the big opportunities we see is in increasing the safety of workers and automation in our heavy industries. For example, we've been working with Newcrest and Ericsson to trial underground private 4G and 5G networks at their Cadia gold mine - one of the largest gold operations in Australia - on the back of the fully operational above-ground 4G network."
"This can enable high-bandwidth, low-latency communications essential for the next generation of mining automation, including new networks of sensors monitoring everything from air quality to structural movement, and ultimately protecting Newcrest's biggest asset - its people,” Burns said.
"With the combination of deep-domain expertise, an extensive ecosystem of specialised partners and the latest technology and quality networks, we're excited to deepen our partnerships with our heavy industries to unlock value, grow their business and create better outcomes for people and the environment,” Burns concluded. telstra.com.au/industrialautomation
Kübler encoders and slip rings for Industry 4.0 concepts ready for applications.
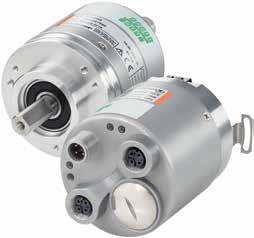
Networks and intelligent products are basic requirements for industry 4.0. These units are able to report about their surroundings. "Who am I, Where am I, How do I feel?” Industry 4.0 opens new perspectives and new business ideas. Compared to the current automation world, which is mainly device-oriented, Industry 4.0 offers a holistic system view. In addition, the technology enables manufacturerindependent access to device data, additional standardised services and simplified device administration. Sensors such as encoders and slip rings play a decisive role here. Kübler will use various use cases to demonstrate which additional tasks can be performed by slip rings in addition to the pure recording of speed and position by rotary encoders as well as the transmission of power, signals and data. Connectivity, Identifications, Diagnostics and Adaptability - these are features that Kübler believes an industry 4.0 product should bring with it.
Kübler encoders - Industry 4.0 ready
Which Industry 4.0 functionalities an encoder needs to be "industry 4.0 ready" depends on the overall concept. The decisive factor here is the role assigned to the encoder. Either as an independent industry 4.0 object (asset) or as a part of it. This determines whether the encoder must have its own management shell or be integrated into an existing management shell. in encoders with their own management shell not only has functions at the “field level”, but also at the “control level” and even up to direct edge communication. In the highest configuration level, for example, one speaks of an Industrial Ethernet encoder with integrated web server and additional OPC UA protocol. As a use case, the commissioning of a drive axis with Industrial Ethernet encoders, for example, can be simplified thanks to the electronic name plate. All information about the operating range, maximum speed, maximum temperature and the installation location of the motor and encoder is available and can be called up here.
Kübler slip rings - Industry 4.0 enabler
Slip rings are highly integrated components of complex machines. They can provide a great deal of reliable information about the condition of the machine and maintenance requirements. Kübler uses the slip rings as an "Industry 4.0 enabler" and has integrated sensor systems into its smart slip rings without taking up any additional valuable installation space. The precise measurement and monitoring of axis movements, vibrations and temperature, coupled with the storage of lifetime histograms, provide all the necessary information for condition monitoring. As a user case, the slip ring is available as a product-as-a-service. In this case, the slip ring is offered as a service or Kübler ensures that reliable transmission of power, signals and data is permanently guaranteed. Thanks to integrated sensors, additional status variables are recorded and used for condition monitoring and lifetime histograms. This ensures a high level of system availability, as this is detected in good time in the event of maintenance. kuebler.com/iiot
Cobots welding
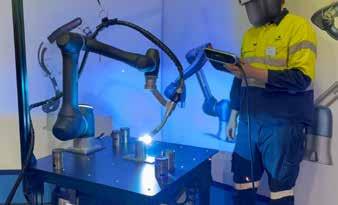
How collaborative robot welding can solve the welding labour shortage.
Welding practices have dramatically evolved over the last 60 years. In 1962, the concept of robotic welding was made a reality with the first real-world spot-welding application being implemented into the assembly line of General Motors, enabling the full-automation of this dangerous task.
This became a fundamental addition to the manufacturing space as the use-cases for robotic welding – and in this case, fully-isolated industrial robots working in human-free zones – started to quickly become ubiquitous across the industry in the decades to come. The ability for these robotic welding systems to increase the overall efficiencies of manufacturers skyrocketed the output capabilities of manufacturers that could justify the significant investment required – both from a financial and factory space perspective.
Fast forward to 2022: industrial robotic welding systems are as ubiquitous as ever – still requiring the significant aforementioned investment – but a new problem has emerged to perturb the abilities of manufacturers; and that is the availability of skilled labour. Weld Australia reported to ABC in 2022 that a range of fabricators in Queensland are working at about 50 per cent capacity due to this world-wide (not just Australia, unfortunately) skilled labour shortage and that this is to the direct detriment of meeting demand from the renewables sector (Margolis & Waterson, 2022).
Where 60 years ago industrial robotic welding began the automation of certain welding tasks, another evolution is occurring this year with the introduction of collaborative robotic welding specifically addressing the skilled labour shortages. The new addition to the manufacturing capabilities space for welders is collaborative robot