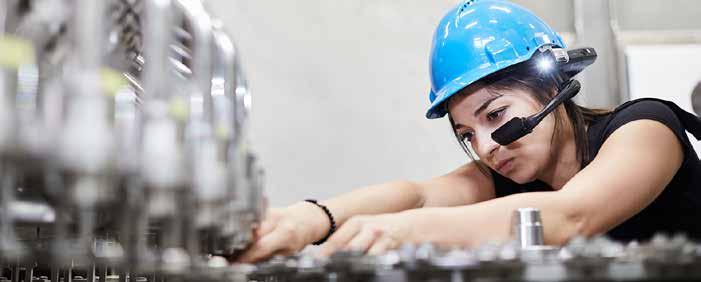
3 minute read
Augmented reality
from AMT AUG/SEP 2023
by AMTIL
The solution for Australian manufacturers’ skills shortage and ageing workforce could be right in front of our eyes. Sojung Lee, President – Asia-Pacific, TeamViewer.
Australian manufacturers have faced enormous challenges over the last few years, including experiencing a widespread skills shortage the likes of which has not been seen in nearly 50 years. Job vacancies in Australia peaked at a record 480,900 positions in 2022 and employers are still experiencing difficulties finding experienced workers to fill talent gaps. At the same time, the sector is also facing the challenge of an ageing population. In fact, by 2050, those over 55 will make up around 40% of the workforce. As older workers head towards retirement, they will take important skills with them, which means, finding ways to transfer these skills to younger workers is essential.
To mitigate these mounting challenges, manufacturers need to take their digital transformation to the next level and embrace new intelligent technology, such as augmented reality (AR), to better support frontline workers. Many enterprises are already leveraging the benefits of AR to improve productivity and safety, and tackle the skills gap. These benefits include quality control, maintenance and repair, streamlined workflows, and remote onboarding and training.
The rise of the smart factory
Due to greater business demands and the power of data, the fourth wave of industrial revolution, otherwise known as Industry 4.0, is in full swing. Technology such as AR will be a driving force behind a future of connectivity, automation and ultimately efficiency. While this can be glimpsed already, it will be seen clearly in factories of the future. There is incredible potential for AR to be deployed to support frontline workers on factory floors along the value chain and regardless of the industry, for example, in logistics, manufacturing, or quality assurance.
In logistics, AR solutions can help workers operate hands-free, faster, more safely, and with on-the-spot training and the ability to resolve issues in real time to ensure better accuracy. For example, a warehouse picker can wear AR glasses to see order details in real time so they can optimise their performance. Gamification can help make warehouse workers even more efficient by adding a fun element that rewards them for faster, error-free processing.
Manufacturing also benefits from this type of technology by providing step-by-step instructions to workers. This lowers error rates, making assembly and manufacturing more streamlined with less waste. It replaces the need for unwieldy manuals and lets workers use both hands for the activity. This lets them work faster with fewer interruptions and better ergonomics.
Efficiencies are also augmented by AR’s ability to maintain quality control. Minimising the natural rate of human error is essential. AR can aid in quality control processes by using smart glasses with cameras and sensors that compare the real-world product that’s being assembled with the ideal digital model in real time. Any discrepancies can be immediately identified, allowing for instant corrections, and thereby improving the overall quality of the output. By combining AR technology with artificial intelligence (AI), organisations can use image-based information to help employees comply with health and safety requirements, improve their skill level with dynamic feedback, verify that processes are being completed correctly, and more. These AI-enabled AR solutions can also provide real-time safety information to workers. For example, they can highlight hazardous areas, detect warning signs, provide safety instructions, or guide workers through emergency evacuation routes.
Enhanced training capabilities
Manufacturers can also use AR to support their workers with enhanced training. This is essential for an industry that regularly sees new members joining its labour force. For example, Australian Bureau of Statistics (ABS) figures reveal that new opportunities in manufacturing are booming, with 80,000 more jobs at the start of the pandemic. For stretched management teams who may have limited capacity to provide comprehensive training to new staff, smart glasses equipped with AR solutions can aid onboarding and deliver unrivalled learn-on-the-job experiences.
It’s also an excellent way for more experienced employees to share their skills with new staff members. AR solutions can support a personalised, one-on-one experience through video calls and AR annotations, even if mentors and mentees are based in different regions or different manufacturing floors. As an organisation’s most experienced staff members approach retirement age, they may be able to prolong their working life by becoming trainers and troubleshooters, using AR solutions to work from home while feeling as if they’re working side-by-side with their less-experienced counterparts. With Industry 4.0 being commonplace, now is the time for companies to look to the future and invest in solutions like AR to help deliver exceptional experiences for their frontline staff. AR can help support staff in various departments while simultaneously improving productivity, tackling skills gaps, and minimising errors. teamviewer.com