
2 minute read
The Kaeser Way
from AMT AUG/SEP 2023
by AMTIL
This is a set of basic steps a business can take to maximise the efficiency of its compressed air generation.
Kaeser Compressors describes this process as being capable of reducing the total energy requirement by up to 90%. The steps cover analysis of the business’ current compressed air station, suggestions for improvements to the existing system, such as leak mitigation, or updates to more modern equipment such as a master controller, energy recovery equipment. Final steps include purchase and servicing options that can be tailored, so that a business only pays for the compressed air used and can rely on fixed price, scheduled servicing.
Using Kaeser’s latest iteration of the Air Demand Analysis (ADA) and Kaeser Energy Saving System (KESS), a portable interface that simply clamps into the existing system, a trained Kaeser technical salesperson can measure, then analyse a business’s compressed air needs with a minimum of time and disruption.
Armed with this information, Kaeser Compressors can then recommend system solutions with maximum efficiency, based on the specific requirements. It may be as simple as identifying leaks and checking correct dimensioning of the current compressed air piping. Leaks are one of the biggest sources of inefficiency in a compressed air system and therefore, can be a huge drain on energy costs.
Other system solutions may be more involved, depending on the nature of the business, such as purchase of new equipment. Mr Peter Eckberg, Managing Director Kaeser Compressors Australia, said, “Our machines are some of the most energy-efficient and dependable on the market. Based on the results of our analysis, we can use our simulation program to create a tailor-made system in accordance with the customer’s requirements.
“For example, energy savings of up to 30% for compressors and 50% for refrigeration dryers are not unusual,” Mr Eckberg said. “Not only that, around 96% of the energy supplied to a compressor can be recovered and reused for heating purposes, whilst around 76% can be used to heat water up to 70°C.”
Another significant step of ‘The KAESER Way’ is to team the energyefficient Kaeser equipment with a SIGMA Air Manager 4.0 (SAM 4.0). SAM 4.0 allows the user to maintain intelligent control of the overall air system. For example, it is often possible to reduce the discharge pressure of the compressors, contributing even further energy savings. A decrease of just 1 bar pressure equates to a reduction in energy costs of 6 to 8%. A further advantage is that by decreasing the network pressure, wear and leakage losses are also reduced. Finally, Kaeser Compressors offers tailor-made monthly contracts, so a business need only pay for the compressed air used. Kaeser supplies and commissions a system for the customer, then scheduled maintenance is taken care of via Kaeser Air Service. The agreement also means that the equipment is serviced in line with the current maintenance schedule and therefore is always energyefficient. kaeser.com
After installation, Kaeser Service Technicians can perform a risk assessment to ensure that the system meets the statutory Occupational Health and Safety requirements. We recommend carrying out an annual leakage check, since new leaks can occur in a compressed air system over the course of time.
All Kaeser compressors impress when it comes to the question of sustainability. Not only do they operate extremely economically, but they are produced in Germany to the strictest quality standards and requirements. Exceptional durability means they can serve a company for many decades to come. Should it ever become necessary to replace them, many of the components used in their manufacture are recyclable.
When it comes to compressed air supply, ‘The KAESER Way’ represents positive steps a business can take regarding the environment, as well as the bottom line.
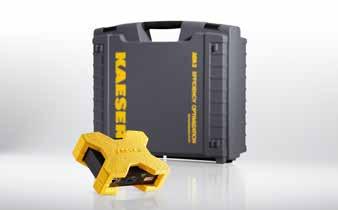