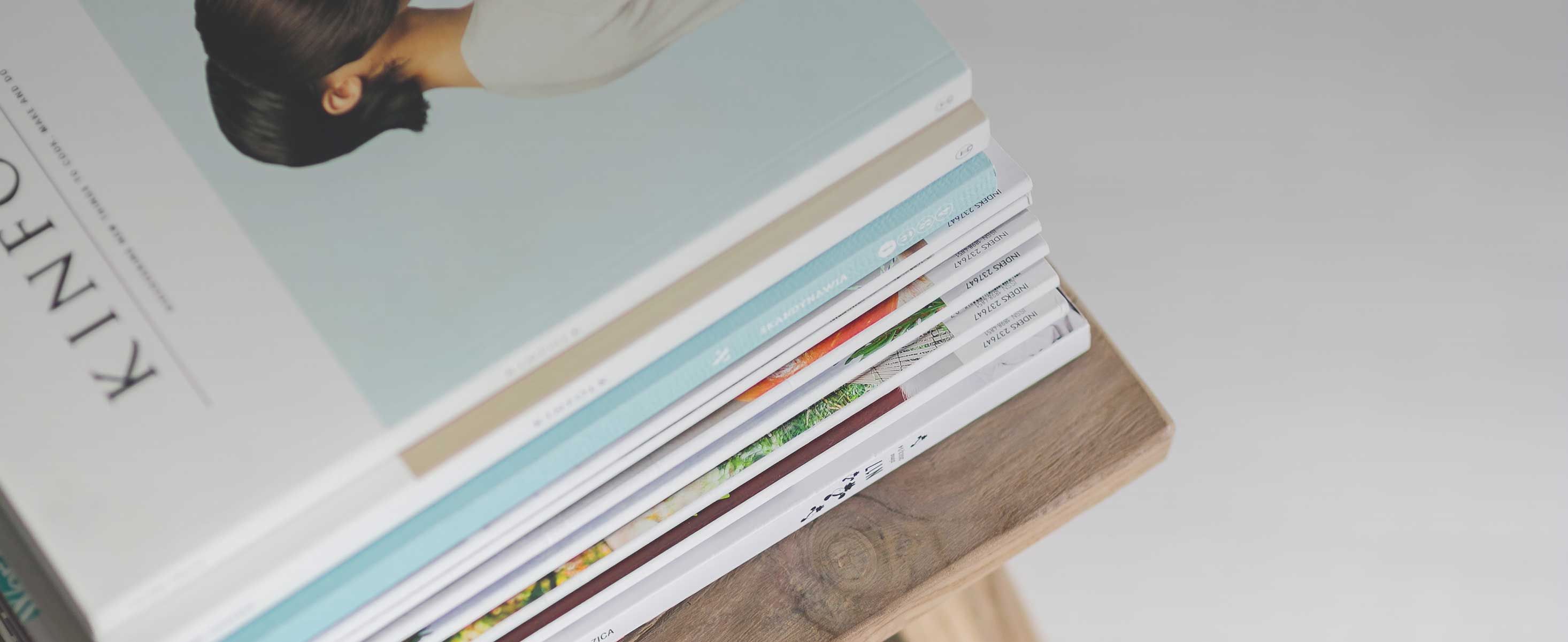
3 minute read
Airstroke actuators
from AMT AUG/SEP 2023
by AMTIL
Stroke of genius enhances hygiene and reliability in conveyor actuation.
A weakness of diverse conveyor and materials handling systems for the processing and packaging of food, pharmaceutical, and hygienic products can be presented by the need to lubricate and protect the actuators used for high-repetition and production automation tasks.
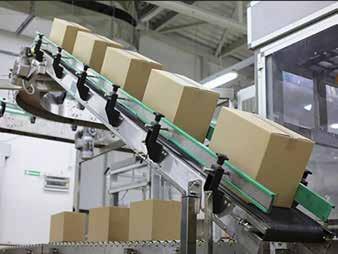
Sticky lubrication can expose traditional shaft-type actuators to buildups of hard grit and greasy grime during operation, during their successive extension and retraction strokes, posing wear issues to the actuators themselves and hygiene issues to the products being processed, transferred, or packed.
“Issues can also occur in areas requiring frequent washdown, as occurs in many food applications, including processed goods and meat, fish and livestock, and agricultural product washing and processing,” says pneumatic actuation and isolation specialist James Maslin, the Technical Product Manager for Air Springs Supply.
Key areas of concern include actuators for lift gates, drive tables, transfer sections, belt tensioners, belt centre guides, waste scrapers, tilt tables and friction brakes – all areas that can accumulate grime, debris, and waste, and can disrupt the seals and shafts of conventional pneumatic and hydraulic cylinders.
“Because conveyor breakdowns can compromise safety and cost money in terms of production losses, operations managers and process engineers can benefit from ways to make conveyor actuation simpler, cleaner, and more reliable.”
“Working on the reasoning that fewer moving parts are better and less prone to wear, one excellent solution for simplicity and reliability can be to employ Airstroke actuators, which have no seals, shafts or internal moving parts,” says James Maslin, who has more than 15 years’ experience in engineering actuation solutions using the Firestone Airstroke® range of actuators and functionally identical Airmount® isolators for which Air Springs Supply is Australian distributor.
These enormously tough rubber and fabric actuators are, in effect, balloons or bellows engineered to suit specific tasks. They are rapidly inflated and deflated, to provide the actuation and retraction required by modern high-speed conveyor components employed throughout industry.

Supplying actuation forces that range, from a few dozen kilograms up to 40,000kg a unit, Airstrokes’ single, double, and tripleconvoluted and rolling sleeve designs are made the same way as the air springs used as suspension springs in heavy vehicles, such as semi-trailers. The compact, but powerful, actuators are every bit as tough as the Airmount isolators found under giant semi-trailers, hauling heavy grimy loads day after day, year after year, says Maslin. The Airstroke range – ranging from the largest (one metre diameter) models down to palm-sized Polyactuator actuators for delicate jobs requiring a clean actuator that does not need lubrication and can cope effortlessly with high-repetition tasks. Eliminating lubrication eliminates another sticky surface for waste adherence.
“One of the beauties of this form of actuation is the inherent flexibility of the actuators when they meet their working surface,” says Maslin. “Being made of rubber and not having any rods or seals to damage, they allow maintenance-free deflection on a continuous basis. Their flexibility also makes them ideal for applications, such as belt takeups or roller friction applications, where they may be applied against an oscillating surface,” he says.
“They can also stroke through a radius without a clevis, thus eliminating both complexity and cost when you need to actuate through an angle. Their ability to soak up shock without damage, while delivering high-repetition strokes, means they are highly applicable to conveyor transfer, gate and lift sections.”
Air Springs Supply’s growing Airstroke range offers a wide range of force capacities and actuation strokes, ranging from Polyactuators’ 45kg with a 12.7mm stroke at 3.5 bar through to more than 300mm for triple-convoluted models that are used as both actuators and isolators in heavy industry. The largest, 940mm diameter Airstroke, will expand from a very compact 140mm to lift weights of approx. 40,000kg per unit.
The world-class Firestone Airstroke and Airmount ranges – widely used across the US, Europe, Asia, and Australia – may also cross over with other air spring actuators incorporated globally by OEM manufacturers of equipment used in industries such as food and beverage, agricultural processing, metal forming, materials handling and process and resources engineering.
“We don’t say Airstrokes are the ideal solution for all actuation needs – every professional knows that each case needs to be considered on its own special needs. But we do know, from a generation of experience, that they can save a lot of time and money over a vast range of applications because we have installations that have completed millions upon millions of cycles with outstanding reliability,” says Maslin. “If safety, reliability, flexibility and repetition are engineering issues, then this technology offers many advantages.” airsprings.com.au