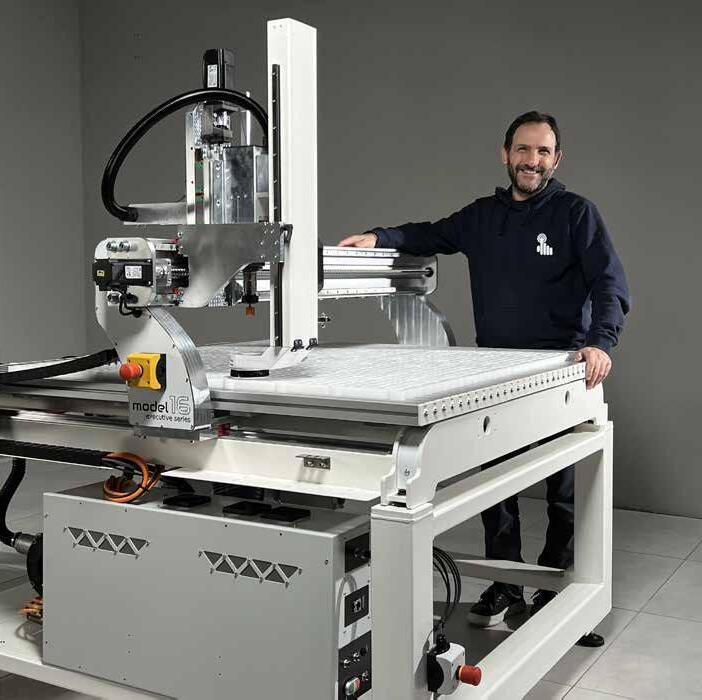
5 minute read
One machine, multiple purposes
from AMT AUG/SEP 2023
by AMTIL
What’s the next big move in the CNC routing end of the industry? Barry Grogan thinks he found a niche.
In collaboration with his university colleagues, Barry Grogan has spearheaded the creation of an exceptional solution for companies grappling with the challenges of outsourcing smaller-scale jobs. Frustrated by the prolonged lead times, frequent delays, and subpar quality that often accompany outsourcing, Barry and his team present the innovative 5.0 Robotics CNC Router. This cutting-edge router boasts minimal setup time, uncompromising adherence to specifications, tolerances, and speed, and incorporates renowned components such as Delta, Siemens, and Tekno Motor. Introducing the 5.0 Robotics Model 8 CNC Router—a user-centric marvel poised to revolutionise your operations.
As a newly qualified Mechanical and Manufacturing engineer from the Trinity College Dublin, like his former classmates, Grogan found there wasn’t much work in Ireland when he completed his degree in 2010.
“I didn't stay on to do a PhD,” Barry added. Grogan came to Australia, started working as a Project Engineer, managing projects in stainless steel fabrication and automation in food, dairy and beverages, then moved into a process engineering role in pharmaceuticals. “I was always more hands-on, more mechanical, more engineering, less management corporation. It just didn't suit me.”
To make ends meet, he imported and sold light professional CNC router systems from Taiwan as a distributor, as suggested by an industry friend back in Ireland. These came in effectively factory-built and would sell through up to 150 units a year, forming BG Precision. “We would do a full-on check through the machine to make sure they were ready for the customer. Making sure every nut and bolt was tight after transport,” Grogan said. “It is a reasonably priced product for the performance coming from it.”
“The Taiwanese company weren't that interested in changing specs too much though because it would narrow down their market,” he added. “So that led to us three years ago asking ourselves, why don't we design a machine from scratch at a highend level. So we did.”
5.0 Robotics
There's a lot of big industrial machinery out there but finding an operator to run that specific machine can be difficult. Grogan can see there’s not as many people wanting to get into that industry because of the demise of the automotive sector. “What we found is people needing to see maybe lower cost machines that are still as capable but more flexible to do smaller, different kinds of jobs. When you spend $300,000 on a machine to produce one component, it only makes sense when you are producing ten million of those same components per year.
The team renamed the business 5.0 Robotics, formerly 4.0 Robotics, just on one year ago. Industry 4.0 was technology driven, we have the technology with the Exec CNC Router, but Industry 5.0 is -user and -value driven and 5.0 Robotics is here to empower the people. Grogan thinks scaling down to smaller jobs with the CNC router has found a ready market. Not just for the smaller operators, but also the larger companies on smaller jobs with smaller runs. He knows this is a step ahead from Industry 4.0. “We know there's an industry 5.0 coming,” added Grogan. “The difference is, you went from mass production, running enormously expensive machines producing a million of the same component, down to a new dispersed market not needing as many of the same piece. What 5.0 Robotics and the new Model 8 is doing is bringing the people back in and empowering them with the right tools to produce the work.”
Another entrepreneur, based out of Tallinn, Estonia said he wanted to get involved. He convinced the two partners the HQ of 5.0
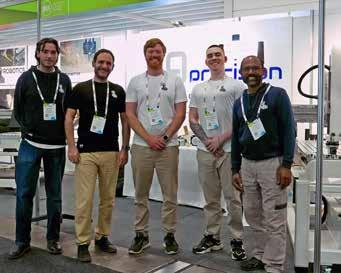
Robotics should be in Tallinn because of the perfectly centralised European location. Estonia is a very small country with only about 450,000 population, but they have great government incentives in manufacturing available there. “The partner in Ireland and I are engineers who don't want to get our heads out of the toolbox,” said Grogan. “The partner in Tallinn is a bit more mature in terms of the business side of things, already had contacts in Tallinn University, works closely with Siemens and also with some government officials there that kind of helps boost the brand off the ground.”
These three engineers put their heads together to revolutionise the manufacturing sector with 5.0 Robotics. And the industry was supporting the change in manufacturing in Australia. Where they need higher-end, lower cost, flexible solutions. 5.0 Robotics now find themselves exploring markets in the Middle East, USA and the Scandanavian countries.
One machine, multiple purposes
CNC routers are basically for machining non-ferrous materials. Aluminum, plastics, composites, timbers, even copper and brass. People come to 5.0 Robotics with pain points. They may be in industry, have a big industrial mill and never used CNC before. But they don't have a hundred thousand dollars budget. From there, some of the markets Grogan hears about are as surprising and inventive as the solutions that can be devised for them on these small CNC routing machines.
The machine as standard is a 3-axis CNC router. “We can add more automation to it, like clamping jigs that are pneumatic controlled sensors which ensure things are in place before you hit go,” suggests Grogan. “You can fit different types of cutting tools. We can automate the tool changing process. They’re optional add-ons if you like thereafter.”
“Industry 5.0 is as a leap into being empowered to do your own work. When someone buys one of these units, after two or three hours of familiarising, they’ll be starting work, producing products and making money.”
All these machines have a relatively small footprint, and they run on a simple 10A single phase point. When designing the 5.0 Robotics router, they had an acute awareness of energy bills, power consumption and a sustainable future. “These units can also fit inside a transit van running solely on battery power, so they’re drawing no more than 2,200 watts of power when the machine’s fully running,” Grogan said. “There is a market in outback Australia, also out in the Middle East countries where power isn’t 100% stable. But you could make a couple thousand dollars a day producing aluminum components in the middle of the desert, running off batteries or straight off solar power, it is very possible.”
Over the first three years of business, his company 5.0 Robotics and their CNCs has had success processing car windshields (glass) in central Europe for one of the big names in automotive, removing microchips from electronics boards for silicon recovery because of the global chip shortage, milling, foiling and embossing dies in the printing industry as Australia phases out acid etching of magnesium, relieving 5-axis robots and operators in the plastics mould manufacturing in Australia as skilled labour in 5-axis machines becomes hard to find.
“That’s where I think we differentiate a CNC router from a CNC milling machine,” he qualifies. “A milling machine is configured very differently. It’s a lot more rigid, has a lot more torque and power, and is complex in setup and operation, where these CNC routers are higher speed, faster moving, bigger tables allowing for faster material removale rates of material of any size in just a few steps across multiple applications and industries.”
Education
The Model 8 is a very turnkey solution to drop and play. In some workshops, and certainly in education, they offer a custom-built safety enclosure. All manufactured and assembled here in Australia. “These are large safety-rated panels on all sides too,” added Grogan. “In the large industrial milling machines, you've got a small viewport window you have to step up to look in on the work. With this smaller footprint, and these large transparent panels, it's just smart thinking with the user in mind.”
“If you've never used the machine before, you want to make sure you can see around the machine. The first step is education. With this unit, with the ‘education safety enclosure’, you can get a 360-degree view of what's going on, so it gives you confidence to give it a go. This can be used anywhere. Home, school, industry, and it's all enclosed.”
50robotics.com linkedin.com/company/50robotics/ BGPRECISION.com.au