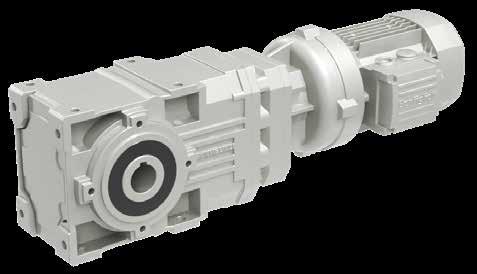
9 minute read
Bonfiglioli WA
from AMT AUG/SEP 2023
by AMTIL
Bonfiglioli’s collaboration with Vector Lifting yields smart train jack system for Perth Transport Authority.
Late last year, Vector Lifting and Bonfiglioli collaborated on a 15-monthlong installation for the Perth Transport Authority (PTA), successfully meeting the PTA’s deadlines and delivering a highperformance lifting solution.

The PTA introduced a new fleet of trains to the network and opened a new maintenance facility in Peth, requiring the installation of 24 lifting jacks for the Perth Metro Network. Vector Lifting was awarded the tender for the supply and installation of a turnkey jack system, which elevates the train body off the track so that the chassis and wheelset can be inspected, repaired, or exchanged.
“This a new train with new requirements, and the PTA required a large number of jacks for the maintenance facility,” says Clinton Capelli, Mechanical Engineer, Vector Lifting. “Our jacks are synchronised and run through a controlled PLC system to lift all 24 jacks at the same time, same speed and to just the right height.”
“One of the reasons we were selected for this project – besides the fact that this is a highly specialised application – is that we are local specialist manufacturer who are price-competitive,” adds Capelli.
A robust, reliable jack system
To complete the jack system, Vector Lifting sought gearboxes from its long-time supplier, Bonfiglioli. “We have developed a good relationship with Bonfiglioli because we believe in their product – it is robust and reliable. Their short lead time and rapid manufacture of custom gearboxes is ideal. They always offer us very good product and technical support, and understand the pressures of our business,” explains Capelli.
Bonfiglioli supplied Vector Lifting with 24 A Series, helical gearboxes, delivered via single consignment, ensuring that Vector Lifting would meet the PTA deadlines in spite of the challenges imposed by the COVID-19 pandemic. "Bonfiglioli offer local stock and assembly, and in the case of large orders which may require an import, they achieve a quick turnaround because of their wide international footprint and manufacturing setups,” elaborates Capelli.
“The A Series is best suited to the jack system design, and required minimal adaption,” explains Fred Whalley, State Sales Manager, Bonfiglioli. These helical bevel gear units offer a wide torque range and high efficiency, in a compact and durable design. They enable smooth, easy handling of goods, even under the most demanding conditions. “We have a large local stock holding but in the case of larger orders we are able to bring them in from Italy in a very short period of time”.
A formidable partnership
Vector Lifting and Bonfiglioli have collaborated for over 22 years. “Theirs is a tried and tested model – they always order the right product for the application,” says Whalley about the Australian job crane specialist. “They boast a professional engineering team, well-versed in the principles of mechanical engineering. We enjoy working with them”.
The pairing with Bonfiglioli has benefited Vector Lifting, in return. “Customers choose our products because we collaborate with Bonfiglioli and other suppliers who help us deliver a good product that can stand the test of time,” adds Capelli. “We feel that Bonfiglioli mirrors what is important to us in their own company ethos and how they interact with customers. This is important to us, to deal with like-minded people. Bonfiglioli also helps us support our product”. He points to the gearbox supplier’s comprehensive customer support offering, which benefits Vector Lifting customers. vectorlifting.com.au bonfiglioli.com
This is a prolific partnership, with plans underway for further collaborative projects. One such initiative is the roll-out of specialised winches (fitted with Bonfiglioli gearboxes) across several West Australian mines, to provide functional and safety enhancements. “We are also in the process of designing specialised lifting equipment for other international rail operators,” concludes Capelli.
Vector Lifting is an Australian manufacturer of and supplier of a variety of jib cranes (one of a limited number of specialists, worldwide), offering custom design consultancy as well as after sales support.
Ergonomics and design for safety
The how and why of ergonomic, human-centred design will minimise biomechanical injury.
The relationship between ergonomics and human-centred design is a complex but ultimately far more synergetic approach to design and manufacturing. As Nick Restall, Design and Development Manager at Integra Systems, explains, it’s defined by the biomechanical working in harmony with the psychological.
“On one hand,” he explains, “you're designing for a human movement and, on the other, you’re designing for the emotive side of the spectrum. But they work hand-in-hand so you're actually designing for that whole human interaction. That's how I see it. They work in conjunction, but they are two halves that form a whole.”
You might be thinking this sounds like common sense – a design approach that looks to make the office environment friendly, livable and aesthetically appealing while prioritising the health and wellbeing of the people in that same workplace. Not surprisingly, though, there’s a bit more to it than just that, with factors like essential ergonomic design parameters, the inclusiveness of the design and –at Integra Systems – considerations for driving the circular economy taken into account.
Let’s look at these factors in detail.
Designing for ergonomics
When you're talking about designing for ergonomics, you're designing to minimise biomechanical injury from either sustained sitting, or twisting or awkward movements that could lead to an injury, explains Ken Ambrose, Business Development Manager at Integra Systems. “One of the fundamentals of ergonomics is promoting blood flow within your body,” he continues. “It’s the reason why sit-stand desks were made. It’s the reason why the very first ergonomic chair went from being a fully upholstered chair to a mesh back because it allowed your body to breathe. All those different things come into calculations when ergonomic factors are taken into account.”
Ergonomic design then has specific parameters around heights, distances, effects on eye strain, body strain, RSI, the length of time a person should be standing, or sitting, or moving. Nick continues on from Ken’s examples explaining how extensive consultation with external ergonomists plays a huge role in their design process.
“With BioSmart, for instance, we had a full ergonomic review, so we knew exactly how far the monitor needs to be away from the eyes, exactly how high the monitor should be set on the shaft and so on,” he details. “We know exactly what the articulation requirements are for each of those, and as many kinds of customisable or moving parts as possible to work in with an individual's biomechanical requirements.”
Designing for inclusivity
For Nick and his team, when designing from an ergonomic perspective, the primary consideration is to solve a problem.
“You’re designing from a place of need; understanding that there’s a potential issue, or problem, or gap,” he explains. In filling in these gaps, the designs not only need to meet the ergonomic parameters, but they also need to hit an inclusivity sweet spot.
“These designs need to eliminate problems, but we also need to make sure we’re designing for inclusivity so we're maximising their potential,” he emphasises. “It's like a height-adjustable desk –you're designing so it can be used by everyone, not by 80% of the population. It's about trying to include everyone and be an enabler for all physical needs. You have to make sure that inclusiveness and diversity is maximised.”
Designing for circularity and sustainability
Designing for circularity and sustainability has always been part of Integra Systems’ DNA. According to Nick, meeting the challenge of designing ergonomic and human-centric products that drive circularity actually makes processes simpler. “If you're not designing for circularity as a habit, then it could introduce a level of complexity because designing in a circular manner means you're eliminating costly or manual processes,” he says. “But what makes Integra different is that circularity is part of how we operate and how we think. So, for us, designing in those circular elements with the ergonomics and with the aesthetics – the human-centric considerations – is a natural thing, and makes it simpler in the long-term.”
The sustainability component of ergonomic and human-centred design is equally important. It forces engineers to consider the design elements in recycled materials and modularity.
“There's the ergonomic side of it and there's a circular economy side of it that we're designing into all our modules. That's part of people being proud of their workplace, especially with sustainability being a core factor.”
This kind of design thinking isn’t limited to office furniture; it extends to equipment used across the business, such as the Lune waste separation bins that Integra manufactures under digital licence from their Dutch creator. The bins provide separation at the source, adds Ken Ambrose, or, in simpler terms, putting bins close to the office kitchen, rather than bins at every workstation, so everyone can get up and walk around.
“It's an opportunity for staff to stretch their legs, get the blood flowing and move the body when they're used to sedentary conditions,” Ken says. “So, if a workplace hasn't incorporated an ergonomic desk, like a height-adjustable desk system, at least they can incorporate other movement-based processes within the workplace through separation at the source, not waste at the desk.”
How it all comes together at Integra
Human-centred design with a focus on ergonomics is a core principle of Integra’s design methodology, so it’s no surprise this philosophy can be seen across their offices and production facilities. From a business point of view, Commercial Director Erika Hughes is of the firm belief the incorporation of human-centred design into their workplace has been a fundamental cog in establishing Integra Systems as an employer of choice. She explains how it’s helped create a working environment that staff want to turn up to each day, and that inspires them in their day-to-day work. It’s helped improve productivity, minimise staff turnover and drive down absenteeism, which are key KPIs in workplaces in any industry.
“Retaining good people is part of a robust business model and, as a business, you want your people to be happy, productive and safe,” Erika explains. “So, in order to do all of those things, the ergonomics and the user-centric design elements need to be factored into the whole process of providing them with a workplace that's healthy, enjoyable and maximises energy. And then that just increases their happiness and reduces their fatigue.”
Ken agrees that the safety element inherent in ergonomic design contributes significantly to a productive and happy workplace.
“I've been in ergonomics for a number of years, and I know from when I was doing chair trials that you can see people re-energise when they think there's going to be something new purchased and it's going to benefit them. I think, if staff feel they're safe at work, they're more likely to come and enjoy their workday, and to feel safe and be more productive.”
As an organisation committed to incorporating ergonomic and human-centred design into everything they do, the Integra Systems’ workplace is a great case study for the success of ergonomics and human-centred design.
As Nick explains, Integra has fitted out their workplace—both the office and the factory area—with their own products, like the AeroSMART height-adjustable industrial assembly workstations: “Our assembly teams are using an ergonomic solution day in and day out; they get that buy-in, and they reap the benefits of our focus on ergonomics and human-centred design.”
Alongside Integra’s BioSMART mobile, constant review is a major part of ensuring their products are ergonomically state-of-the-art. “We tap into the regulations and standards, and get the advice of ergonomists to ensure we’re meeting the technical specifications that are required,” Erika reveals. “But I think the feedback from people who are using it on the job is so very, very valuable. The ergonomics is all fine from a physio-therapeutic and biomechanical point of view, but the user-centric design that taps into the human psyche, and what makes us want to do things and be better at doing things, I think, is what our design team are so very talented at achieving.”
“We like to get that feedback from the production staff around what they like to see. That's what plays into that human-centred design approach,” adds Nick. “We get the feedback from the users and then we iterate and make improvements on the work stations to suit them and continue that human-centred design cycle.” Erika, Nick and Ken agree it’s rewarding for their designers and engineers to see what actually happens with their designs in a real-time environment. “It's really rewarding for the guys who are creating them in the factory and putting them together,” Nick points out. “They're seeing how the products they're putting together are being used on a daily basis.” One of the key differentiators of Integra is their willingness to be their own guinea pigs. As Erika puts it, “If it doesn’t work for us, there is no way we would recommend our creations to others. This real life testing of the products, as if we are our own customers, is critical to their commercial success and customer satisfaction.”
“For us,” she concludes, “it's important that our products represent who we are, and that our clients and customers reap the rewards. We can actually prove what those rewards are, and we can talk about them with our customers. That helps our customers have faith in whatever it is we’re building with them.” integrasystems.com.au
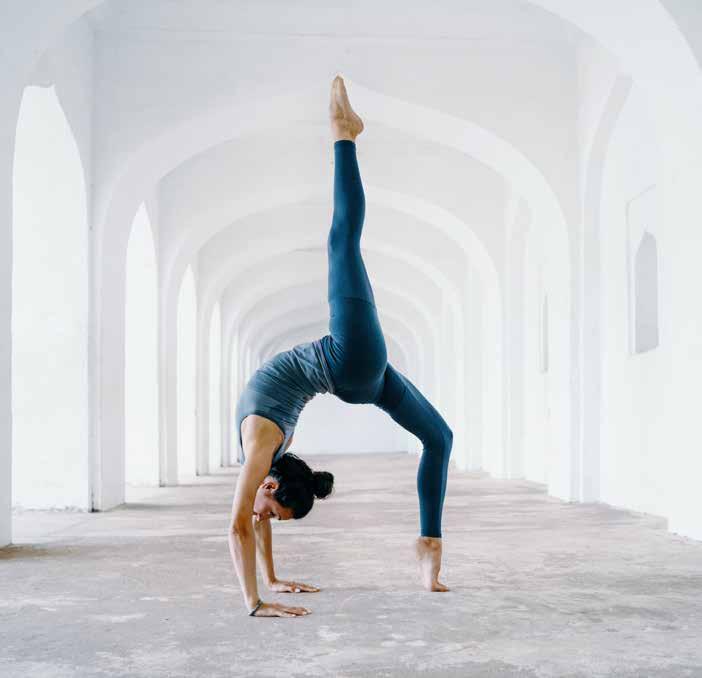