HangingMycelium:
UseofGravitationalFormFindingtechniquestouniformlyshapeModular MyceliumSheetswithoutFormwork.
AnnLomshekandNicoleReimertBurró
DepartmentofArchitectureatKansasStateUniversity
ARCH715:MycoMatters
AssistantProfessorJonathanDessi-Olive
November28,2021
Abstract
This research paper attempts to further sustainable practices of myceliumform-givingin order to reduce the waste generated by frameworkandformsthataretypicallyusedtocreatethe final form of any unit of mycelium. This research proposesanexplorationofform-givingthatis directly derived from form finding through hanging that was popularized by the Swiss engineer Heinz Isler1 as a way of creating unitized forms with precise dimensions without a need for molds or traditional formwork. Isler’s proposal, according to Baghdadi and Kloft, stated that forms that were hung and worked under tension could be flipped over and would support structural loads in compression at a precise scale that involved size and material thickness (p. 493). Through a series of experiments involving plaster and mycelium, the research team was able to achieve uniform shells that performed well under compression at thescaleatwhichthey were hung. The purpose of these particular hangs was to create unitized forms that could be stacked in order to form a non-load bearing partition screen. The final result proved that this process of hanging is efficient in creating mycelium forms thatallowavarietyofconfigurations fordifferentendproducts.
1 Baghdadi&Kloft,“StructuralassessmentofremodelledshellsofHeinzIsler,”491-502
1. Introduction
This experiment focuses on finding ways to grow mycelium as flat surfaces and determining their final shape without needforformwork.Ideally,thesebuildingmaterialswould be modified to a degree in which they couldbestackedasmodularunits.Forthepurposeofthis research paper, the aforementioned term, “building materials,” isn’t exclusively applied to the material once it is used in construction, rather, it discusses the processes of manufacturing materials and their byproducts as an important factor. Due to the nature of the class, the task presented to the group was to design a manufacturing process for mycelium that addressed this particularaspectofconstruction.
The research team uses the term mycelium to define the end product that occurs when fungal spores are allowed to grow in a sterile environment surrounded by substrates made of natural materials such as hemp. The spores branch out and form hyphae, or terminations, that present the unique capability of binding to the hyphae of other strands to form a unitized structural web. In mycelium growth, the hyphae is allowed to grow until it has completely engulfed the substrate that was previously sanitized and determined by Ecovative, the company that provides the material at a commercial level.2 Once the growth of hyphae issatisfactory,the mycelium can either be dehydrated or baked in order to stop further growth of branches and potential flowering into fungi. The researcher’s chosen course of action for preventing growth wasairdryingthroughhanginginordertotakeadvantageofgravitationalformfinding.
By working minimally yet effectively with available materials familiar to residential or commercial agriculture, the researchers considered how compatible the mycelium with hemp substrate would be with sisal,burlapandfinerthreads.Myceliumwould,intheory, consumethe bio-based threads and the remainder of the threadwouldbetheperfectaidforhanging.Urgency was also placed on the efficiency of stable, stacked forms thatcangrowindenseconditionsand stillbeabletodryinthree-dimensionalforceswhentheytakecompression.
1.1 Form Definition
Ecovative’s website3 served as one of the many inspirations the team took in assessing the current market and manufacturing for mycelium products. From the research, the team determined that the bulk of commercially available mycelium is typically grown as small modular units in prefabricated molds. The team felt there was a niche opportunity to explore growing mycelium as flat surfaces in a way thatwascompletelyfreeofanyformwork.Theidea was conceived from analyzing Mylo UnLeather’s manufacturing plant4 , in which they grow mycelium on racks stacked on top of each other before sending them to final production. The team inferred that this process would not only aid in waste reduction, but it would also be spatiallyefficient.Simplificationofmanufacturinghasambitionsforconsideringhowtoadvance “MycoSheets”atacommerciallevel.
In the context of this research, it is essential to clearly outline the difference between mycelium textiles (leather) and “Myco Sheets.” Mycelium textiles are commercialized textiles
4https://wwwmylo-unleathercom/ 3 https://ecovativedesign.com
such as Mylo Unleather that use pure mycelium or mycelium with a fabric substrate that are exclusively usedastextilesanddonotpossessanystructuralcharacteristics.MycoSheetsarethe name given to the material of this study In order for a material to qualify as a Myco Sheet, it must be grown at the final dimensions they will have. This means that, unlike other existing fabrics, the material must not be pressed orstructurallymodified.MycoSheetsaregrowntofull maturity andhungimmediatelyafterwardssothattheycanbedriedintotheirfinal3dimensional form. Materials such as mycelium textiles, floor tiles, slabs, or other architectural elements do not meet the requirements to be considered Myco Sheets because, while they can be grown to their final shape, they are not dried in a position that exploits gravitational form finding. The process of air-drying alone is not enough for a material to be considered a Myco Sheet in this research; materials must be hung in a matter that mimics Isler’s gravitational form finding studies5 .
Treating MyloUnleatherasaprecedentforlargermanufacturingpossibilitiesinspiredthe team to grow mycelium in the form of flat surfaces, whichbenefitedarangeofexperimentation in thicknesses, sizes, pressures, formwork types, and arrangements that allow arrays of form. Further considerations that will be discussed are how the final product could be modified and how changes in scale of the discrete form could allow for prefabricated units of dissected three dimensionalforms.
A key precedent used to analyze the behavior was MycoTEX by Aniela Hoitink from NEFFA. Hoitink’s study studied the growth of mycelium in petri dishes in conjunction with a
variety of textiles and non-fabric substrates to determine where mycelium would grow best and how it would affect the flexibility of garments.6 Hoitink’s design takes the formofseveraldiscs that lay on top of one another as though to grow instead of using stitches to bind the discs together The inspiration behind this, according to Hoitink, was in “observing a range of soft-bodied organisms that growbyreplicatingthemselvesoverandoveragain,”(NEFFA2020). According to MycoTEX, this created a piece of fabricthatwasrigidenoughtonotbetornwhen pulledandthatkeptflexibilitythroughout.7
The interest in Hoitink’s study for this team lies in herpreviousexperimentation.Before determining if her discs would be made out of pure mycelium, Hoitinkandherteamstudiedthe growth of mycelium with a variety of different fabrics and fibrous substrates. The resultsofher research, according to NEFFA, indicate that mycelium thrives on fabric that is very porous and has a very loose knit pattern (NEFFA 2019). Tightly woven fabricsandsyntheticsarenoteasily consumed by mycelium, which inherently makestheunitweaker.Theresearchteamworkingon Myco Sheets found that this was useful information because it indicated fabric characteristics that could be better membranes to host mycelium, such as linen, would actually hinder the growthofmyceliumandweakenthestructureasawhole.
1.2 Objective
6Nai,C.,&Meyer,V.,“Thebeautyandthemorbid:fungiassourceofinspirationincontemporaryart,”2.
7Morby,A,“AniellaHoitinkcreatesdressfromMushroomMycelium,”2016
The team hypothesized thatthesimplicityofgrowingdirectlyonasurfacethatmycelium can not consume would be both timeandspacesavingifcreatedwithapreciseform.Asdefined previously, “sheets” are the fully grown planes that are shaped from flatsurfacesatthegrowing stage (around 5 days, depending on state of inoculated material) and successively hung using predeterminedpointsappliedwithprecedentoftheHeinzIslergravityformingmethodaswellas foresight with experimentation of hanging pure mycelium like a sheet. The main goal of observing the sheets as they grew was to understandthecapabilities,andthereforefeasibility,of creating objects with tensile function in one stage,andconvertingtoanobjectincompressionin thefinalstageofafullygrownmyceliumsheet.
Since the purpose of the experiment was to test the flexibility and tensile capabilities of mycelium without a need for formwork, the research team believed that gravity would be the best way to test the aforementioned limits.Withthisinformationinmind,theteamhypothesized that the flexibility of mycelium sheets depended greatly on the ratio of thickness to length and width. However, itwasalsoclearthatmyceliumwouldbehaveverydifferentlytoothermaterials that are used for form finding, such as burlap or cotton fabric. Despite these shortcomings, the team assumed that the sheets would not only be structurally sound and stand upright, but that theywouldbeabletostackontopofeachothertoformalargerstructuremadeofmodules.
2. DevelopmentofForm
2.1 Gravitational Form-Finding
The first step in understanding gravitational form finding was to create a grid-like structure from which pieces of fabric could hang in a calculated manner The team fabricated a gridfromchickenwireandawoodenframe.Thechickenwirewas5feetlongby2feetwideand the grid boxes were an inch square. The entire unit was suspended 3 feet from the ground with sawhorses on opposite ends. Hanging occurredbysubmergingpre-cutpiecesofburlapinplaster and fixing thecornerstothegridwithziptiestoform“feet”.Thefeetwereindirectcontactwith the grid and the distance between the feet was determined by counting the number of squares between each point and making each point equidistant. The first series of hangs were purely exploratory, as though to understand what the process involved, and only a few of the forms that were originally hung werepresent infuturerounds(Image1).
With the previously mentioned tests, the team reaffirmed their theory of the importance of material thickness for structural stability Those pieces of burlap that were not submerged in enough plaster were not thick enough to sustain the loads imposed by their own weight when flipped over. This lesson was directly applicable to future mycelium practices in regards to
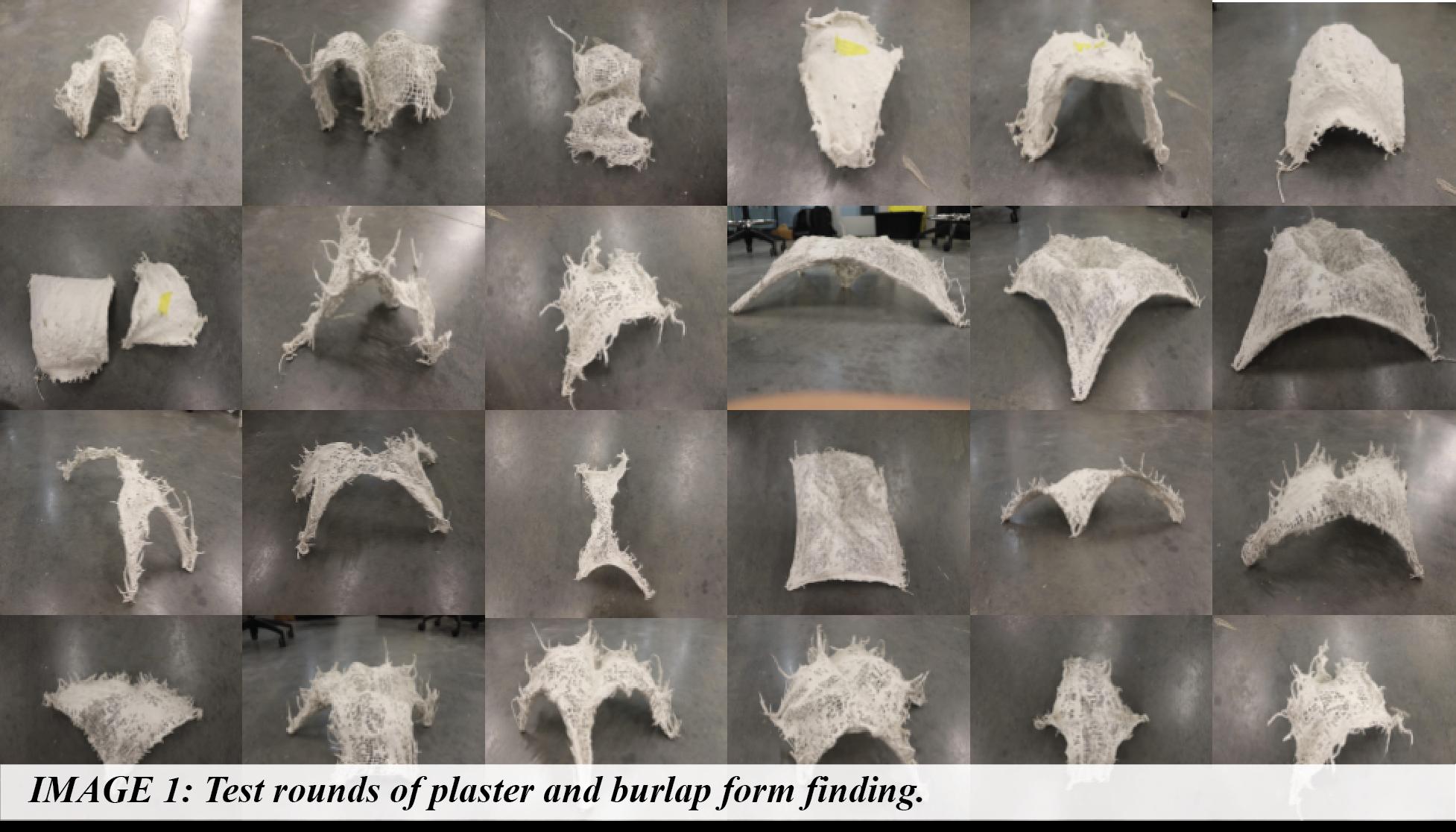
understanding the importance of structural cross-section in keeping elements upright and resistingoutwardthrust.
The team conducted 40 different hangs with burlap and determined that continuing to work with a material like burlapwouldnotbeinformativeincomparisontomycelium,asasolid sheet. Burlap behaved very differently from a solid sheet, so the team moved to using recycled bedding sheets as the fabric forexperimentation.Thebenefitoffabricinthisscenariowasthatit clearly outlined the folds and curvature of hanging forms in a way that the team couldcompare tomyceliumafterwards.
These initial exercises were to perfect the practice of form-finding through hanging.
Team members learned how to precisely dimension the distance between feet and how to take proper measurements for comparison. In addition, the practice of experimenting with zip ties, wire, burlap, and sisal helped the team to understand how differenttyingelementsmightimpact the fabric and the mycelium that would grow into or around the tie. This lesson was helpful in thefutureindevisingawaytohangmyceliumfromagridwithoutharmingthematerial.
2.2 Initial Mycelium Experimentation with Catenaries
The team proceeded to inoculate 0.12 cubic feet of mycelium for the initial experiment. The inoculation carefully followed the steps provided by Ecovative’s website8 . The directions state that 3 cups of water and 4 tablespoons of all-purpose flour are enough to activate the dormant mycelium in the bag. These ingredients were mixed in a sanitized pitcher and poured
into the bag, which was then sealed and vigorously shaken for2minutes.Immediatelyafter,the bagwasstoredinasanitizedblackcontainerfromMarch9,2021toMarch15,2021.
On March 15, 2021 the team re-opened the bag, which was now visibly white and fully covered by mycelium, and dumped all of the contents of the bag in a previously sanitized and dried container The researchers used gloves to ensure that no bacteria from their hands transferred on to the mycelium and also sanitized the gloveswithamixtureofisopropylalcohol and boiled water. To separate the threads of mycelium thathadgrown,theteammembershadto manually tear the mycelium apart until only the substrate was visible. Thisprocesswasusedin allgrow-stagesoftheInitialandFinalexperiments.
While this was occurring, other team members set up the surface on which the sheets would grow For this, the team used a fold-upplastictableandcovereditinpreviouslysanitized black tarp. Theythenlaiddownunsanitizedburlapwithanoverhangof2inchesoneverysideof the table, the purpose of tryingunsanitizedburlapwastoseeifinfutureexperimentsitwouldbe necessary to fullydisinfectthefabricorifmyceliumwasstrongenoughtocompetewithbacteria living inthefabric.Myceliumwaslaiddownin3differentsizes;onesheetwasaround18”X12”, another was 17”X11”, and the last was 11” X 8”. The team intended each sheet to be ¼ inch thick and was not very careful with edge treatment astheyassumedtheywouldcutthesheetsto size once they were dried. Once the team was satisfied with the shape of the sheets, they sprinkled water and a quarter of a tablespoon of flour on the sheets. The whole setup was then coveredinblacktarptoallowforfurthergrowthofhyphaeforfivedays.
The resultant material was in good condition after the growth stage. There was no visible external molding or infection. The initial formwork for these was created with attachment of the burlap to 2”x4” wood planks on parallel sawhorses (Image 2). The sheets were hung as barrel vaults, following precise measurements designed with Rhino3D catenary function. After drying for 5 days each form was cut down and flipped over Some shapes were skewed due to variability in the thickness in the sheet at the end of the growth stage. This could be accounted as human-error or simply as a variable behaviorofthemyceliumtogrowupwardswhenitisaflatcondition.
Post-modification was done to cut off the ends of burlap used for hanging, as well as to test the level of difficulty for modifying future forms (Image 3). The myco-material cut easily with scissors whichgaveitacleaneredge,however the skew in the catenary remained an ultimate implication as it could not be reshaped by further bending. Thebeautyofusingburlapinthisinstance was a texturized gridded surface that mycelium filled in. It did not visibly consume the burlap, as was anticipated to some degree, perhaps due to the
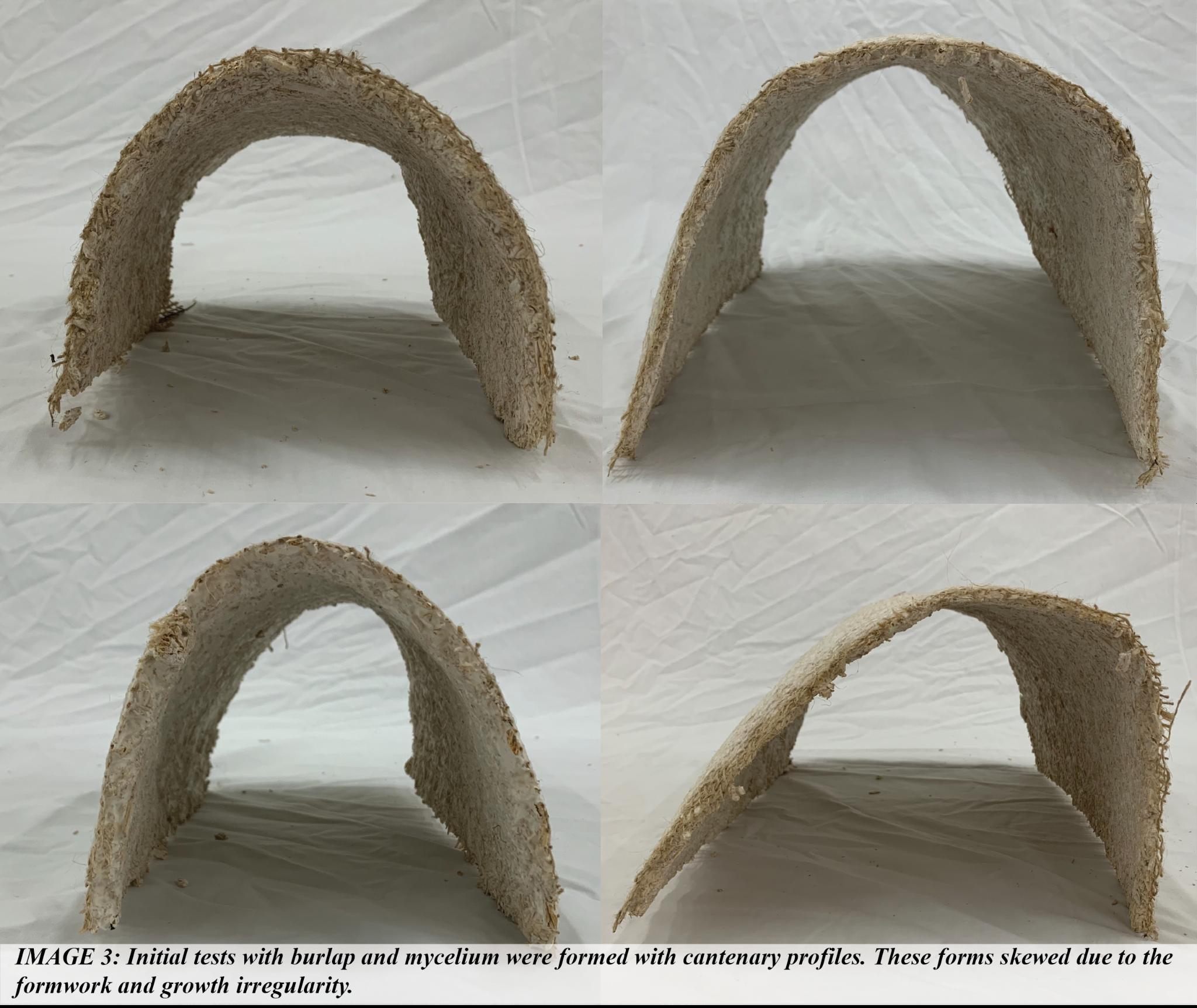
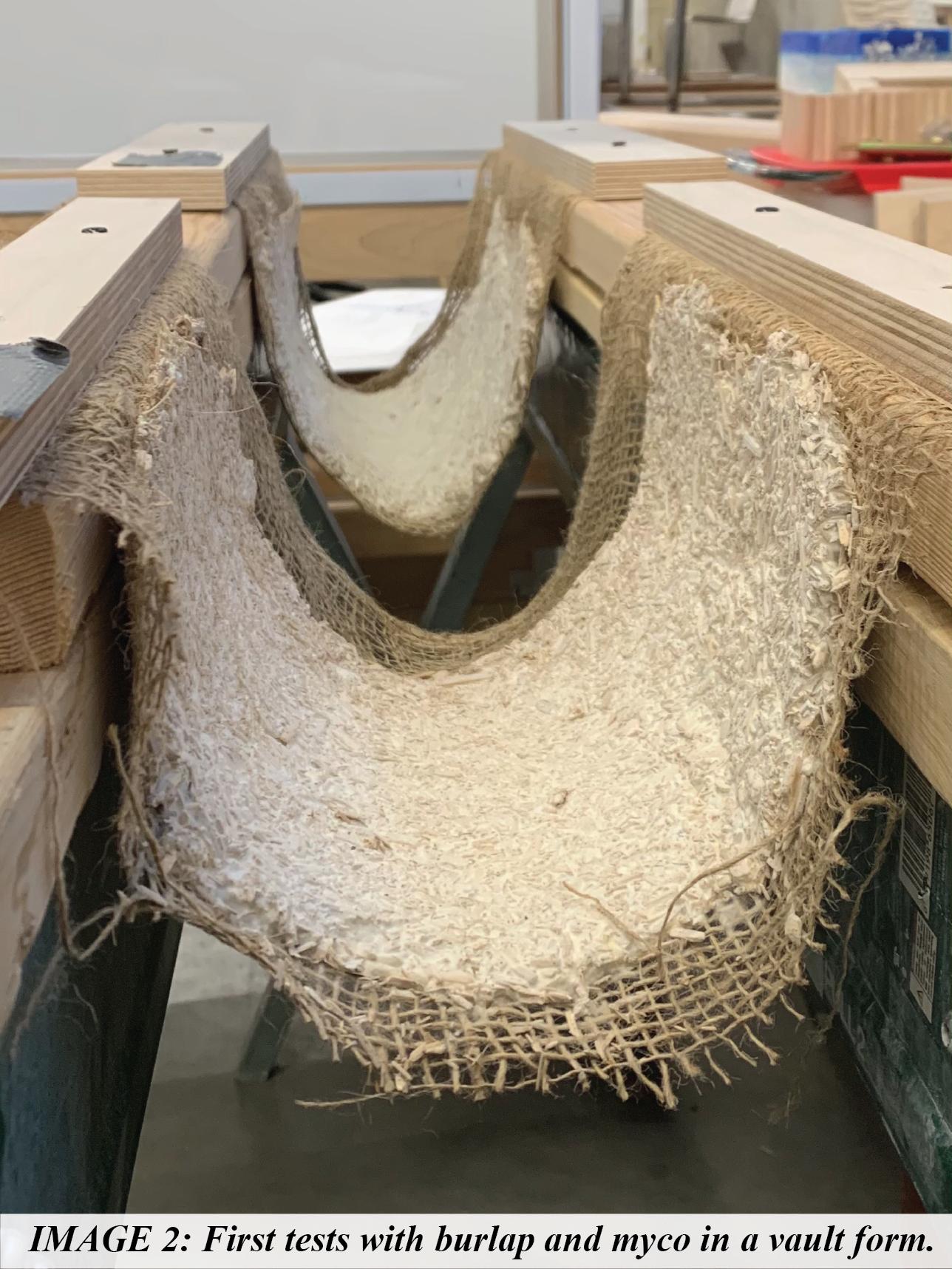
longevity of the growth period before hanging. Forthissubject'spurpose,makingthevaultswas apriorityoverobservingatwhatstagethesheetwouldbecomepuremycelium.
Once this initial test was conducted, the research team decided to scale up the size of sheets in order to better understand how thicker and heavier material would behave whenhung. This experiment would also assess different assembly configurations by varying the ratio between burlap to mycelium and the order in which it wasassembled.Thiswouldhelptheteam understand to what extent the fabric was aiding or hindering the flexibility of the sheets. The configuration of growth, in this scenario, was achieved by stacking tables on one another. The sheets at the bottommost tier would receive the least amount of oxygen and the highest amount ofpressure,whichtheteambelievedtobeawaytocontroltheheightexpansionofthematerial.
Six (6) bags of material were inoculated and grown in the same manner as before. The first set was achieved by laying unsanitized burlap underneath an application of 34”x70”x1/4” mycelium, following another layer of burlap. This amount of material came from 2 bags of Ecovative GIY kits, amounting to 0.24 cubic feet. The name given to this group was “Burlap-Myco-Burlap” due to its composition (Diagram 1). The sheet was then sprinkled with flour and water, which was expected tohelpcontinuegrowth.Theassemblywascoveredwith clear cling wrap and punctured for air flow to the fungal skin. The team members then covered the sheet in black tarp and laid a fold-up table, face down, on thetarptoaddpressure.Placedat thebottommostlevel,thissheethadthepressureofthreetablesandtheirsheetsontop.
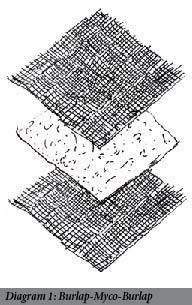
The next layer of mycelium was made of two (2) bags as well. In this case, the assembly was inverted from the first: one layer of mycelium, one layer of burlap, and one final layer of mycelium. The name given to this group was “Myco-Burlap-Myco” (Diagram 2). On a table of the same dimensions as the first, the team laid down two 34” x 34” x ¼” sheets. Just as with the previous test, the members covered the assembly in punctured cling wrap and covereditintarp.Thefold up table was placed on top of the other tables housing the first roundoftestsand,oncemoreanadditionaltablewaslaidfacedownontopofthetarp.
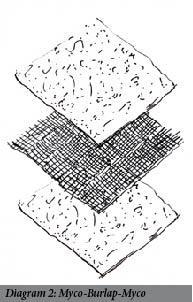
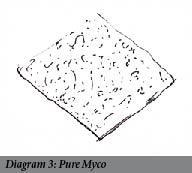
The final test, using the last 0.24 cubicfeetofmycelium, was conducted with no added fabric. For this reason, the team chose to call this group “Pure Myco” (Diagram 3). In this case, the growth process was the same, but the sheetswerelaidonthe sterilized surface with no burlap. These sheets, measuring 34” x 18”, were covered inclingwrapandtarp,followingthepreviousprocedure,andwerelaidontop of the table assembly with no added surface on top. These sheets had no pressure on them and weremeanttoactasthecontrolgroupforthisseriesoftests.
All sheets grew for 7 days, with constant moisturizing of the sides once a day with previously boiled water. At the end ofthegrowthcycle,theteamnoticedthatallsheets,withthe exception of the Pure Myco, had mold growth happening towards the center. The groups
Myco-Burlap-Myco and Burlap-Myco-Burlap had to be discarded as they were unusable for
hanging purposes. The team hypothesized that this occurred because the sheets were at the bottomlayersandhadnoaccesstooxygen,whichgavewayforinvasivebacteriatogrowinstead ofthehyphae.Thishypothesiswasfurtheraffirmedsincethepreviousroundincludedburlapand no infection had occurred. Additionally, Pure Myco thrived in an environment where it had accesstooxygen.

Since the only viable results were the Pure Myco control group, the team decided to try four point hangs with the three sheets (Image 4). For this, a larger grid was constructed from the same materials as the original. The grid was suspended 3feetoffthegroundbytwo(2) sawhorses placed under the short ends of the grid. The first module was hung by cutting the tarp around the sheet and piercing the tarp withsanitized16gasteel wire. The four points were placed at a distance of 11 inches from each other ina squareformation.Theteamfoundthatthis wasaninefficientwayofworkingbecause the sheets would slide down the tarp and the final form was warped. This informed
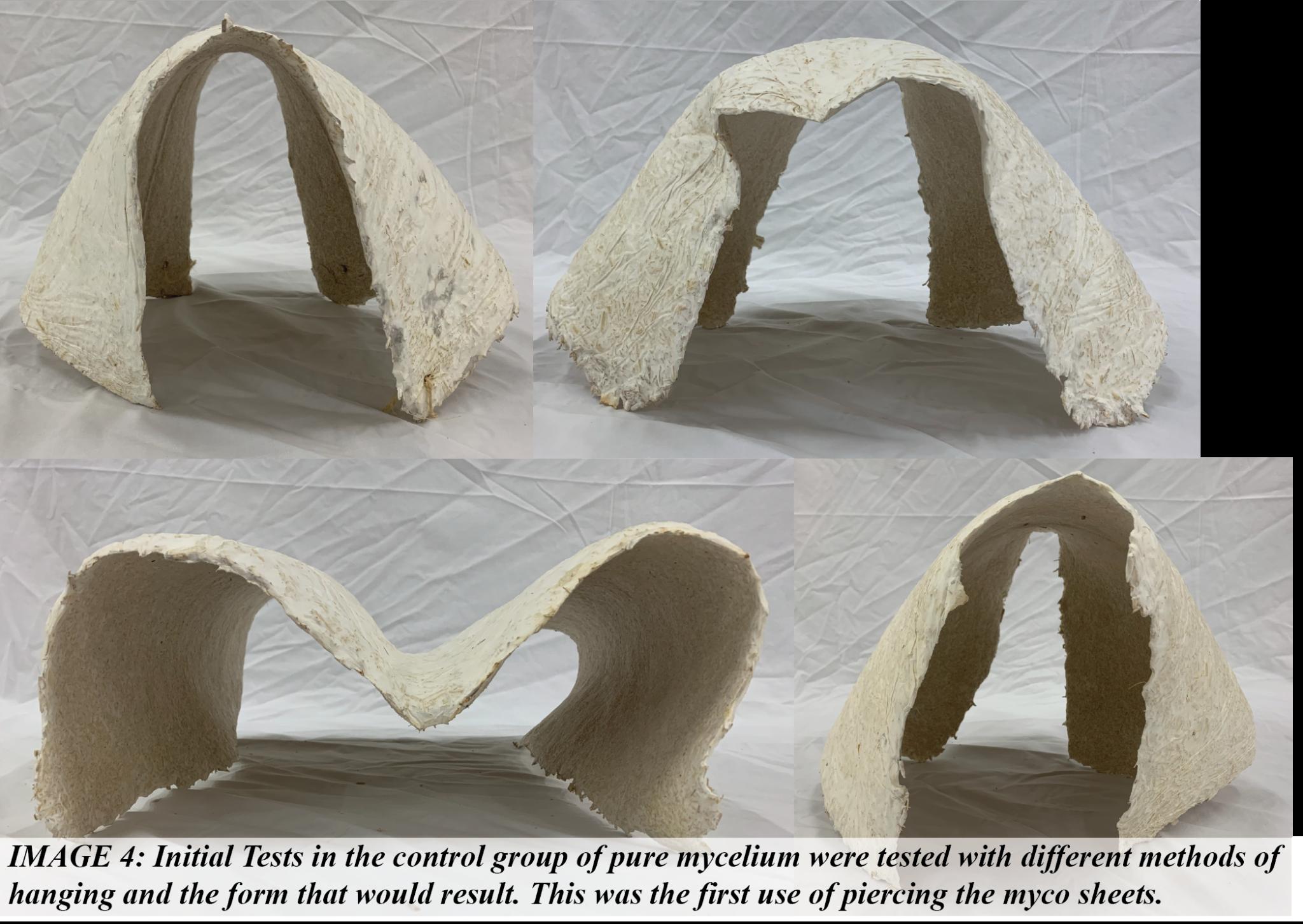
the next hanging procedures, in which the team experimented withpiercingthesheetswithsisal (Image 5). The following two sheets were hung in this manner and in this process the team discovered that sisal was not the best option because it unraveled and destroyed much of the structure of the sheet as it was too thick to be efficiently pierced. The sheets were hung, with some damage to the corners, and the research team experimented with creating indentations in the sheet with added sisal. The damage to the corners occurred when the team attempted to pierce the piece on only onepoint,astheweightofthepieceonthestringwouldriptheedgesof thepiecesoff.Becauseofthis,theteambeganpiercingontwopointsparalleltothecorner.
The sheets were drywithin24hoursandtheteamwasabletodismountthem.Whilethey did stand once flipped upside down, the cross-section was too thin and the sheets were easily warped. With any added pressure, the sheets couldlosestructuralintegritydespitebeingdryand theycouldnotholdtheweightofothermyceliumsheetsontop.
3. ActualizingHangingandMaterialsforModules
3.1 Updated Gravitational Form-Finding
The researchers extracted key lessons from the previous test rounds that informed the final form of the hung mycelium. The first change that needed to be implemented was growing mycelium free of pressure and with proper air circulation to preventinfection.Thesecondpoint wastogrowfreeofanysubstratesothatthemyceliumwasn’tcompetingwithanyotherbacteria. As a third point, the team also set out to thicken the sheets to ¾” and upto1”atthecornersfor greater structural integrity. The fourth, and last, modification was to pierce the sheets with a
needle and cotton sewing string for greater precision and less breakage of the mycelium structure.
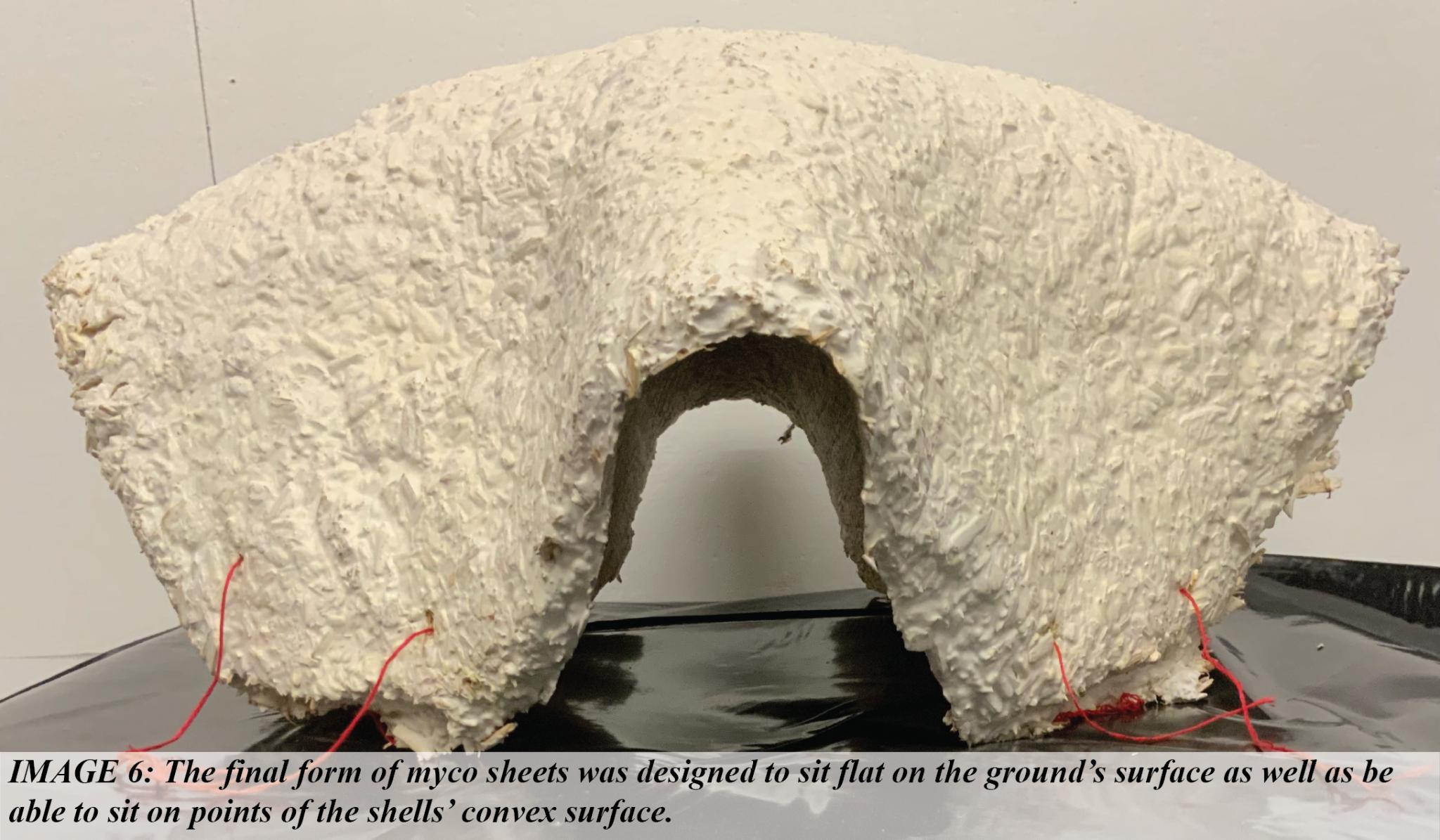
3.2 Final Form Selection
With this information in mind, the researchers chose to present their final form in the shape of a screen wall. This would be an effective way to showcase the stacking and modular properties achieved through hanging without pushing the limits of material property. The team decided to mimictheresultantformfromthefourpointhangasitprovedtobethemoststableof all the tested configurations.Beingonfourpointsgavethesheetmorepointstodistributeloadto and would be easier to modulate in a partition screen setting, as thefeetofeachsheetcouldrest ontheapexofeachvault.
Three (3) bags of 0.12 cubic feet were available for the final procedure. The team chose to divide this into 24 sheets of 18” x 18” x ¾” as though to have enough pieces to create a partition system. To ensure that the feet met the ground at a line, rather than at a point, the team chose to chamfer the corners oftherectangular shape the mycelium would grow in by 3” x 3”. This created a final form that would be able to layfirmlyonthegroundoncedried.(Image6)
3.3Modulating Forms into Final Form
With 24 sheets available, the challenge wastofind the best way to stack them to showcase the benefit of the chamfered “foot” and the sheets’ modularity A single sheet’s feet would need two sheets beneath it to stack vertically, with the orientation of the top sheet being rotated 45 degrees from the orientation of the bottom sheets (Image 7). With these considerations in mind, the team came up with a three tiered grid that started from a 3x2, moved up to 2x1, and landed on a single sheet atthe top(Image6).Theremaining15sheetscouldbestackedin a 3x3 bottom layer, 2x2 mid layer, and a singular sheet at thetop.
4. ProductionofModules
4.1 Environment and Sanitation
As stated throughout, the researchers followed Ecovative growing instructions and steps for sanitizing. Control of infection was prevented by cleansing gloves, surfaces, tarpandtablesthat were in contact with the mycelium. The room was kept dark and the growing areas were concealed further from light and heavy air flow by draping opaque black tarps. During the growthperiodwaterwassprayedontheplasticandnotthesheetstokeepahumidenvironment.

4.2 Sheet Growth
The inoculated material was first filled to the perimeter of the module size, then the sides were packed to a straight edge tool. One person controlledtheconsistencyformoldingtheedgeand corner conditions which were prone to crumble or spew past the perimeter shape (Image 8). Precaution was taken to check the edges after the tables were transported since the movement, plastic wrapping, and tarpwereallsubjecttocause variation in the shape. A few sheets closest to the wall, where there werenoplastictarps,were less grown in, which could be attributed to why there was a higher magnitude of fragilitywhen movingthosesheetstoitsformwork.
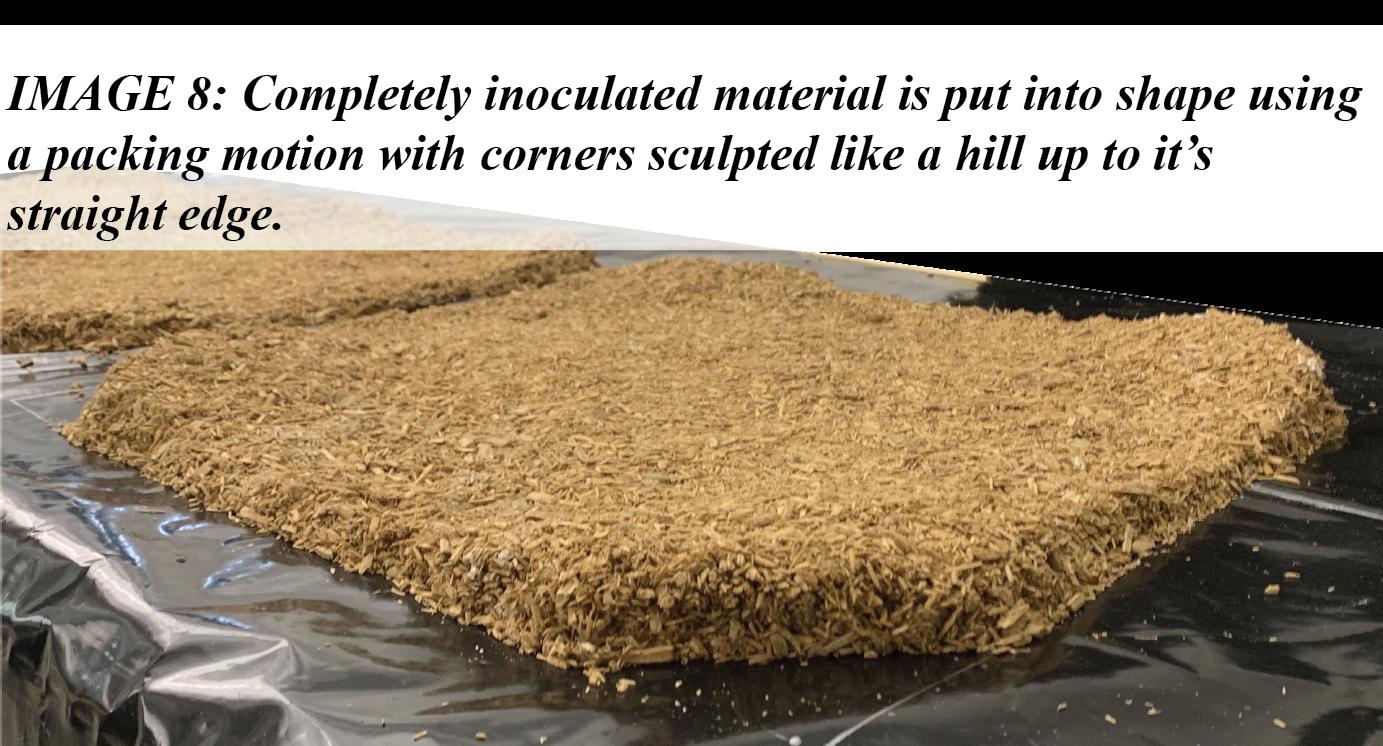
4.3 Hanging Procedures
After the growing period, the sheets were laid face down in order to be pierced through the plastic andmyceliumattwopointsontheiredgesusingsewingthreadandaneedle.Thesepoints were tied to strings that were secured in 10” squares along the wire grid. Fastening with string and wire allowed adjustment to makethepointslevel.Thesameprocedurewasusedwithlonger strings to hang a second row of sheets directly below the top row
Measurements were taken between hanging pointson the top level and accounted for on the

second level by tying a boundingedgetothelongerhangingstringsthatextendedfromthesame pointsaslevelone(image9).Duringthedryingtimetheplasticwrappingremainedonthesheets as secondary support on the convex side to control the variability that some sheets may dry quickerifnotcovered.Tarpswereagainplacedtogivethesheetsamorecontainedenvironment.
4.4 Variations
Upon moving the sheets to the formwork some were found to have torn so the team used stitching to reattach parts that would otherwise have torn further and been unusable to hang. These instances are attributed to the fragility of a thin, live material and human error during the move from growing flat to bending into a concave shape(Image10).
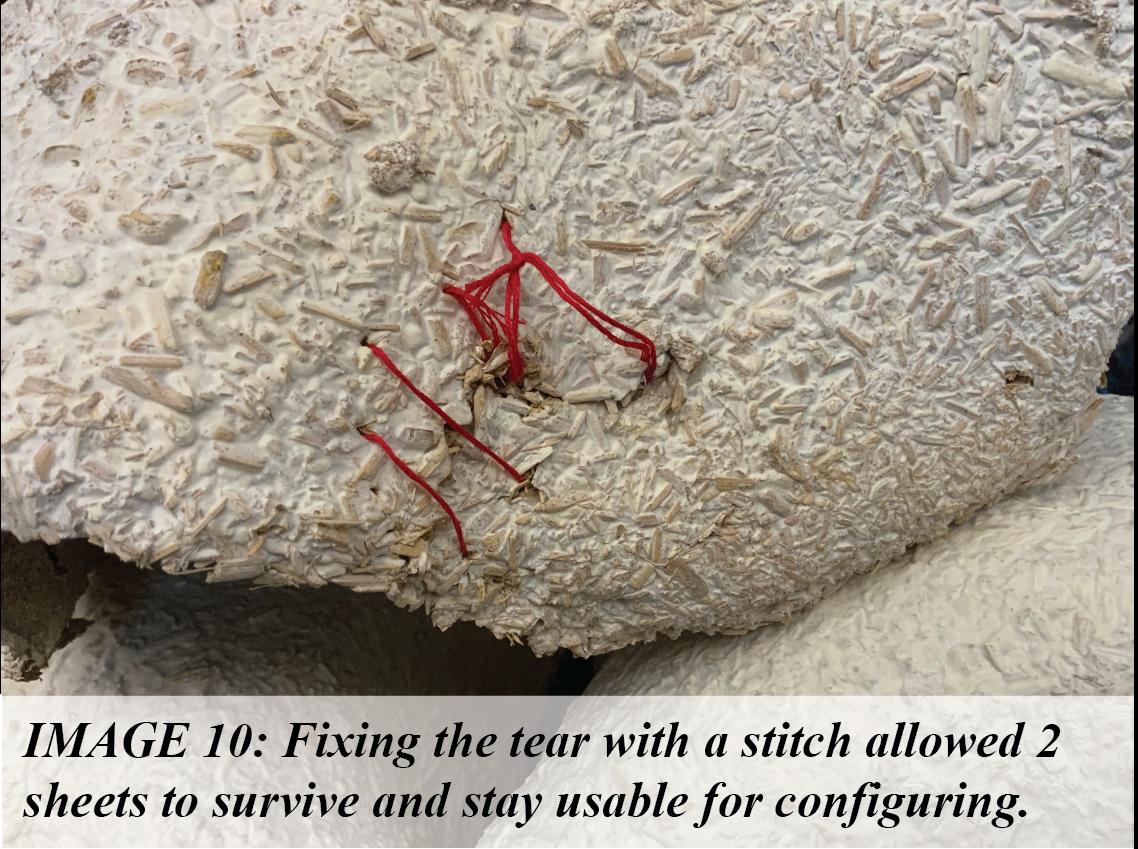
5. Results
5.1 Final Form
The strings holding the cut sheets were carefully removed from the grid and flipped around so that they would stand on their feet. Due to the careful hanging procedures, the variation between modules wasminimal,butstillnoticeable.Thegreatestvariationthatoccurred in the pieces that had to be sewn together, as theydeviatedfromtheverticalandhorizontalaxes
in the drying process. Out of the twenty-four (24) sheets, two (2) were not viableduetosignificantdeformation.The remaining sheets, however, stood on their feet with no issues andwereabletolayontopofeachotherwithoutany wobbling or need for manipulation. Sincetwoofthesheets were not viable, theteamhadtoadjustthefinalmodulation of the partition wall. The team chose to use the first partition proposal with a 3x2 base. The remaining sheets could be stacked singularly to showcase the 45 degree rotation and the possibilities of a single row of sheets (Image11).
The thickness of the feet compared to the membrane of the shell was instrumental in keeping the sheets standing without deformation once the weight of other sheets was placed on top. In addition, it also provided enough stability so that when a sheet was placedatoptheapex of a piece below it would have enough grip not to slip down the curve.The24 sheets were able to be swapped with each other, despite their irregularities, and the overall piece maintained structural integrity, confirming the modularnatureoftheunit(Image12).
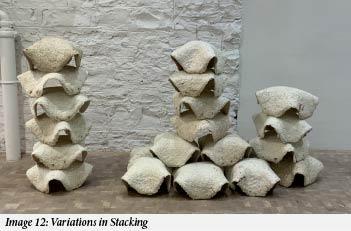
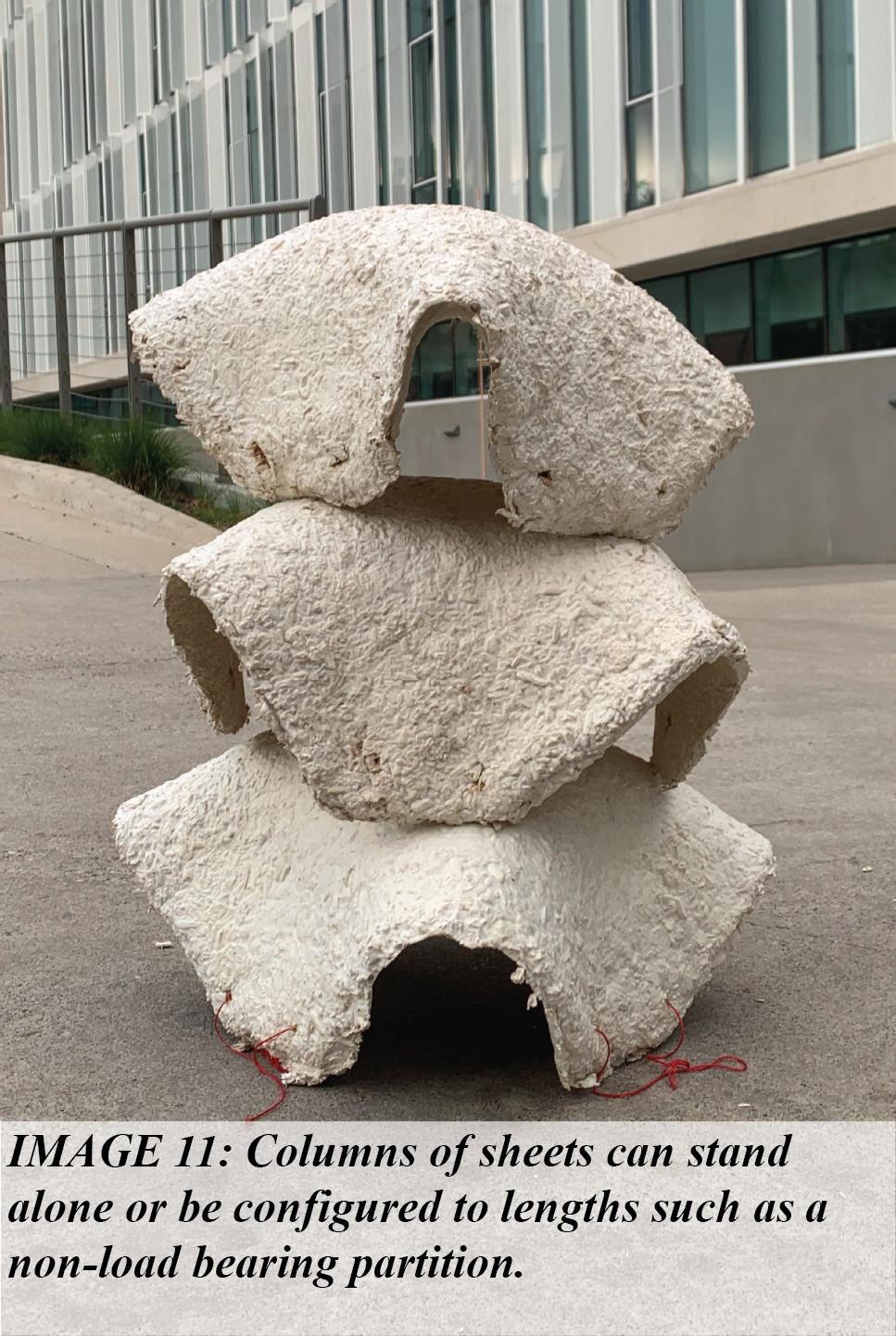
6. Conclusion
6.1 Discussion
This research sets the base for future experimentation on the flexibility of sheets while being formed solely with gravity Additionally, it proved that the integrity of the mycelium structure is strong enough to bepiercedandhungwithoutsignificantdamage.Theteambelieves that moving forward, it would be important to study what the optimum maturity state of sheets forhangingis,thethicknesstoperimeterratio,andthepossibilitiesofsewnpieces.
The team hypothesizes that the reason why some sheets were not viable is because the areas where breakage occurred were not fully grown. Meaning, the sheets would require more time so that the hyphae could fully consume the substrate. This would prevent future deformation that occurs when the pieces of the sheet are stitched together and would allow for mass production of uniform pieces. While stitching did not produce optimal results in uniform shell shape, it provided opportunities in the realm of hanging and post-production. The team hypothesizes that, were there a matrix thatpreventedgrowthintheformofpunctureholesinthe sheet, the hanging process could be more controlled to produce pieces with a smaller marginof variation. Additionally, thosepunctureholescouldbedesignedtoprovideapassageforthreadto jointwoormoredriedsheetstoeachotherortootherstructures.
Future investigation is still necessary on whether or not the thread should be inserted in the growth and maturity process so that the hyphae can consume the thread andformastronger bond. Much like the burlap tests, it might aid in reducing breakage and provide a measurement tool to decrease variation betweensheets.Itisalsonecessarytoinvestigatetheratioofperimeter
to thickness to determine what the optimal thickness would be to increase the sheets’ load bearing capacities. The thicknessproposedbytheteamisdenseandfunctional,butnoadditional experimentation was conducted to test if a thicker sheet with the same perimeter would be strongerandifitwouldbeasflexibleastheoriginalsheet.
A concern in regards to thickness is resultant weight. If apieceistooheavy,itmightnot be able to hang following the same procedures as this researchproposes.Thesheetsusedbythe team were pierced in two points to distribute the weight of the piece on the string and prevent ripping, as mentioned previously. In thicker, larger sheets, it might be beneficial to pierce in morethantwopointstodistributetheweightfurther.
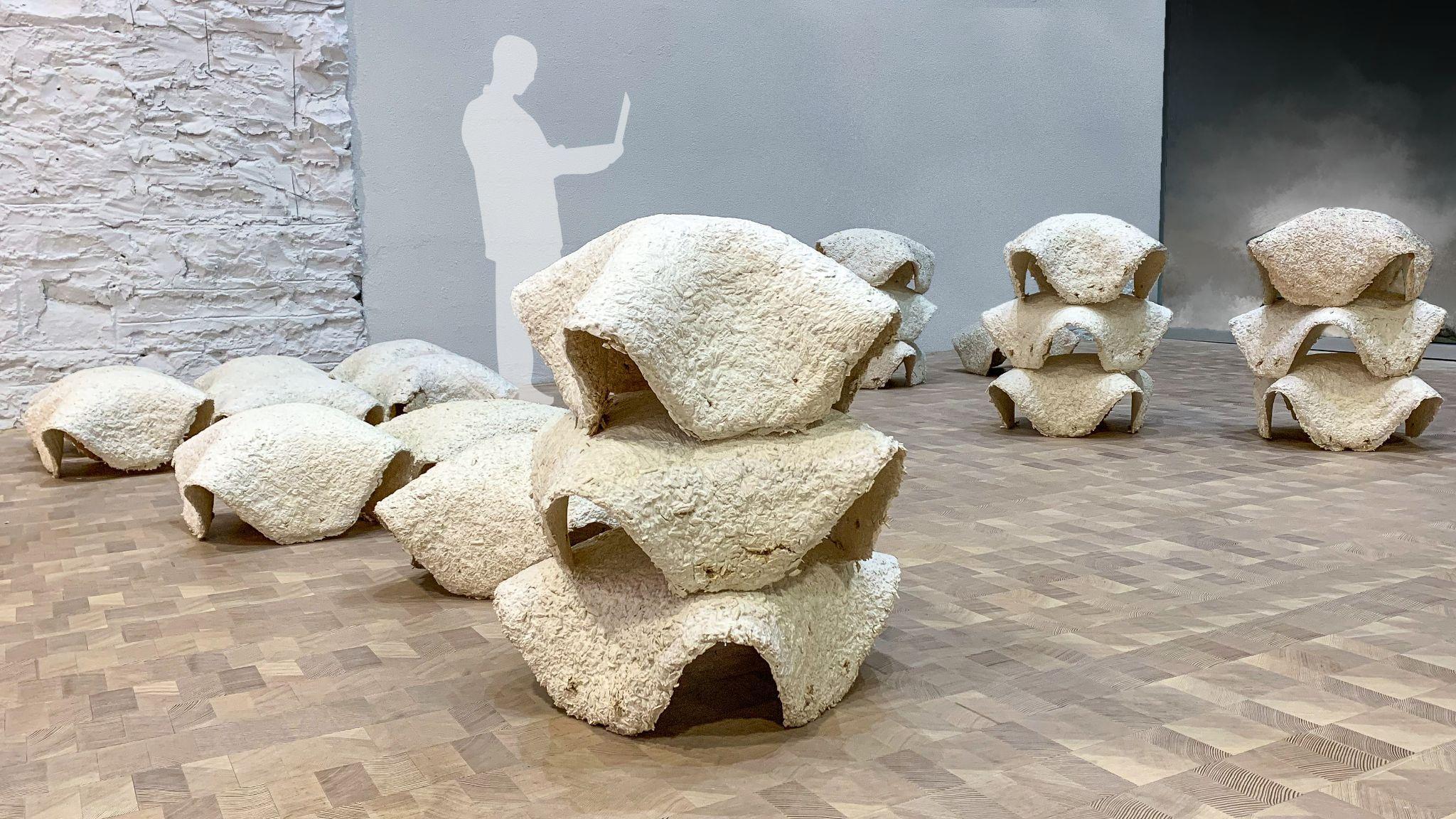
Bibliography
Baghdadi,A.,Heristchian,M.&Kloft,H.(2019).Structuralassessmentofremodelledshellsof HeinzIsler Int J Adv Struct Eng 11,491–502.
https://doi.org/10.1007/s40091-019-00248-4
“MycoTEX.”NEFFA,October22,2020.https://neffa.nl/mycotex/.
“MycoTEXproof-of-concept.”NEFFA,October22,2020.https://neffa.nl/portfolio/mycotex/
Nai,C.,&Meyer,V.(2016).Thebeautyandthemorbid:fungiassourceofinspirationin contemporaryart, Fungal Biology and Biotechnology,Vol.10,1-5.