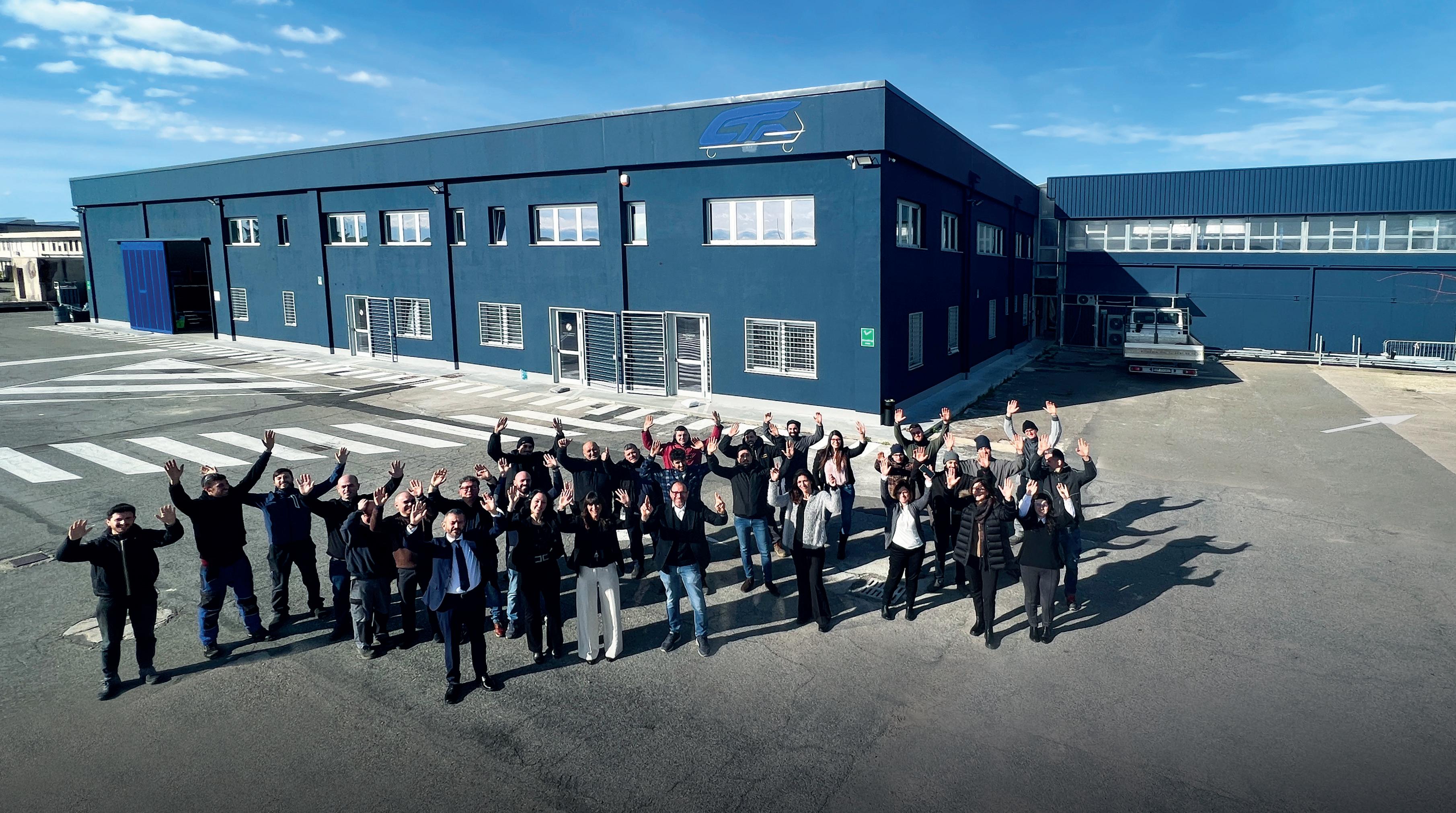
3 minute read
CTA revolution
CTA’s new production site is up and running, propelling the company’s operations into the future
Words and photo Andrea Cattaneo
CTA’s new production site has been in operation since 2022 and is now working at full throttle, marking a milestone in the Italian company’s growth. We at Aboutcamp BtoB went to visit the new facility and met the CTA team. The factory covers an area of 10,000 square metres, almost half of which is under cover. The buildings house the production department (3,000 sqm) and the warehouse (1,200 sqm), but there are also administrative offices and the technical department.
“After forty-five years in business and steady growth over the latest period, the time had come to scale up and look to the future,” explains Dario Bellezze, the founder’s son and current CEO of the company, “which is why we invested not only in a large new building, but also in state-of-the-art machinery and production processes. Lean-oriented manufacturing strategies enable a significant boost in production, but also increase production flexibility and decrease lead times. There has been a significant investment in terms of human resources and staff training: over forty people now work in the company, a number that has practically doubled in three years. The technical department has been implemented and we have a new production manager, Alessandro Ferrara, who already has ten years’ experience in Operations inside the company”.


Digital transformation
CTA has set itself a clear goal: to streamline all processes with the focus on customer satisfaction. With this mission always in mind, the company is aiming to increase production while maintaining high product quality, meeting the increasingly demanding requirements of the market in terms of numbers and costs. A pivotal figure in the development of the new production site is Alessandro Polidoro, an engineer and external company advisor, who has considerable experience in digital transformation projects, Industry 4.0 and quality improvement in innovative contexts.
“My role in the company is that of Programme Manager,” says Alessandro Po- lidoro, who is also a member of ISIPM, the Italian Institute of Project Management, “in other words, Project Manager for all the innovation projects. All the innovation projects have been managed through programme management methodologies”.
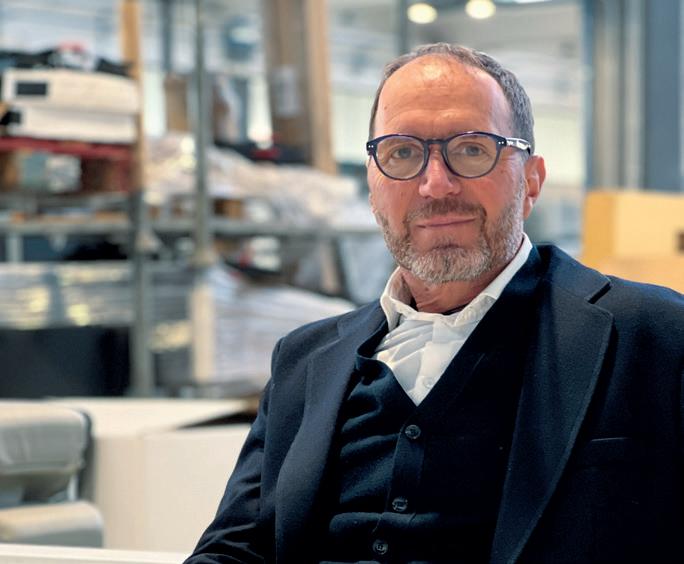
Activities in collaboration with Alessandro Polidoro (PHD in Industrial Innovation Engineering) are continuing into the future: as part of its Digital Transformation process, CTA has in fact been chosen as a partner of the innovative start-up iMetho (www.imetho.com) to apply the latest innovations in data analytics and artificial intelligence (specifically process mining, machine learning and deep learning) in its sector, aiming to maximise customer satisfaction, increase productivity and optimise consumption.
In recent years, CTA has expanded as a result of market growth, but by also broadening what it has to offer. All investments and strategic choices have been made in an optimal customer-centric manner, to better respond to customer needs.
“Over the last four years we have greatly diversified our range,” explains Ursula Scalia, CTA’s Sales & Marketing Manager, “both for our OEM customers, by also proposing solutions for the growing Minivan category such as the new swivel seat models and the Dinette Sleep, and by introducing solutions that better respond to the needs of the aftermarket. Today we are partners with the leading distributors of accessories and components, operating in most European countries and also in the United States. We are now also starting to penetrate other markets, such as Japan. Behind this development activity is great attention to the needs of the end customer and the distribution needs of our wholesale partners, for whom we have customised some of our core products created for original equipment, in order to make them easier to distribute and more usable for both the fitter and the end customer, also through specific marketing material such as brochures, assembly instructions, and available optional extras. One example among many: our seat belt anchorage structures, which have always been CTA’s core business for original equipment, have now become “Smart Kits”, with everything you need to install a professional and tested product according to current regulations”.
Automated and flexible production

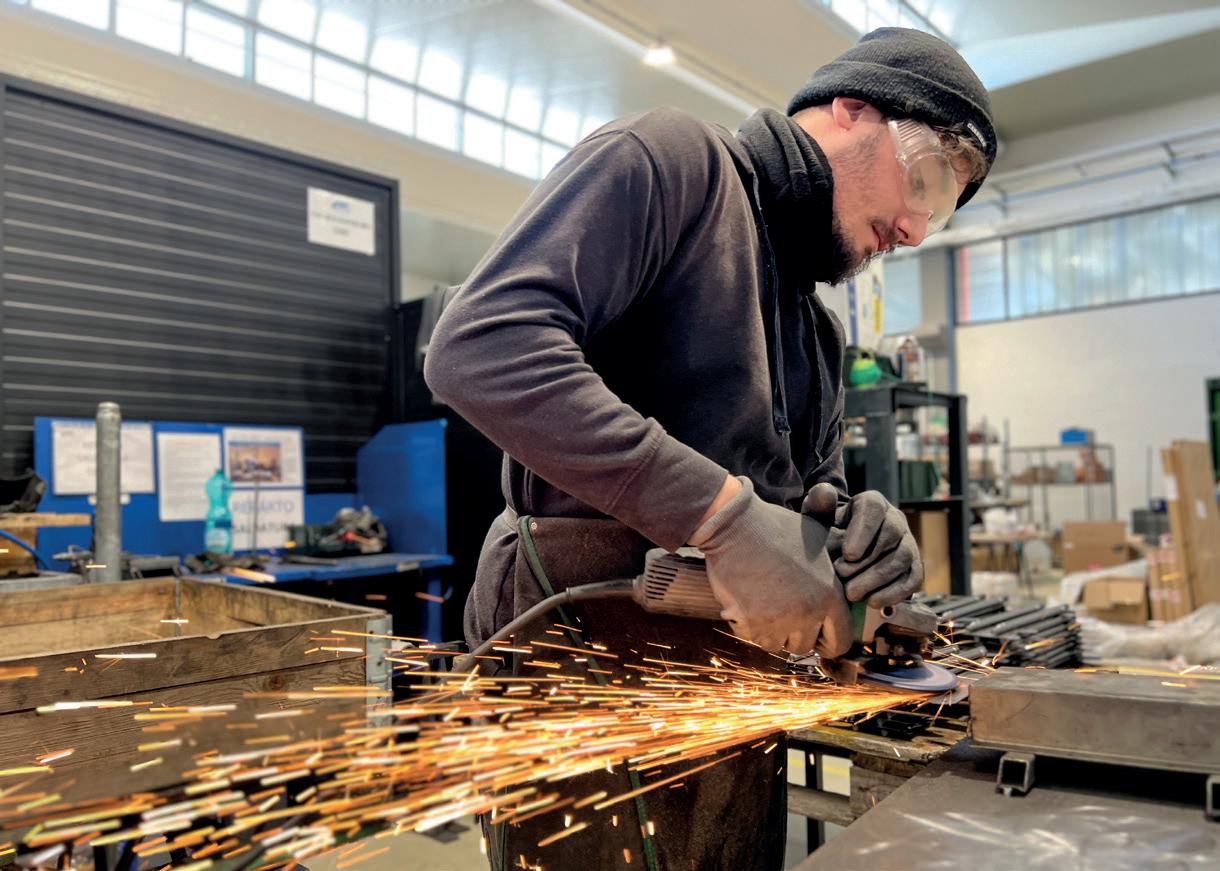
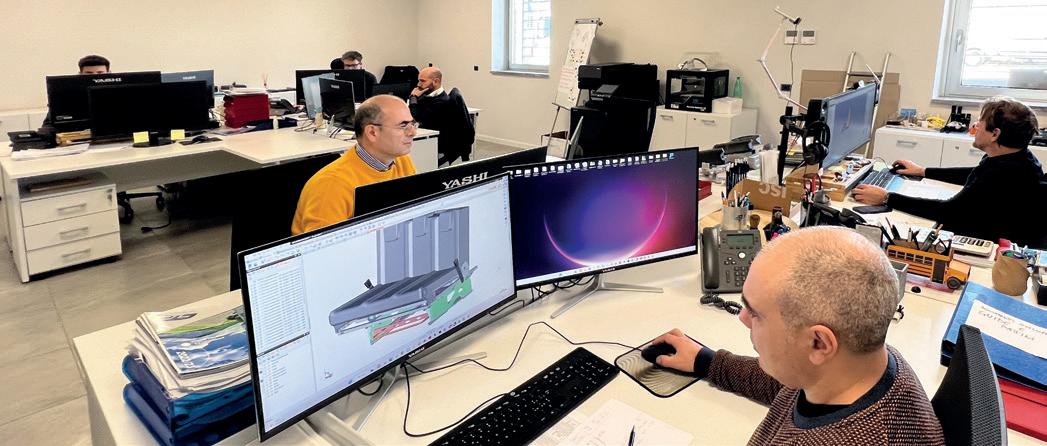
State-of-the-art, interconnected machinery has been installed in the new production department. Versatile and flexible work islands have been created, according to the type of production. For laser sheet metal cutting, there is an automatic loading and unloading system, which allows the machine to work around the clock.
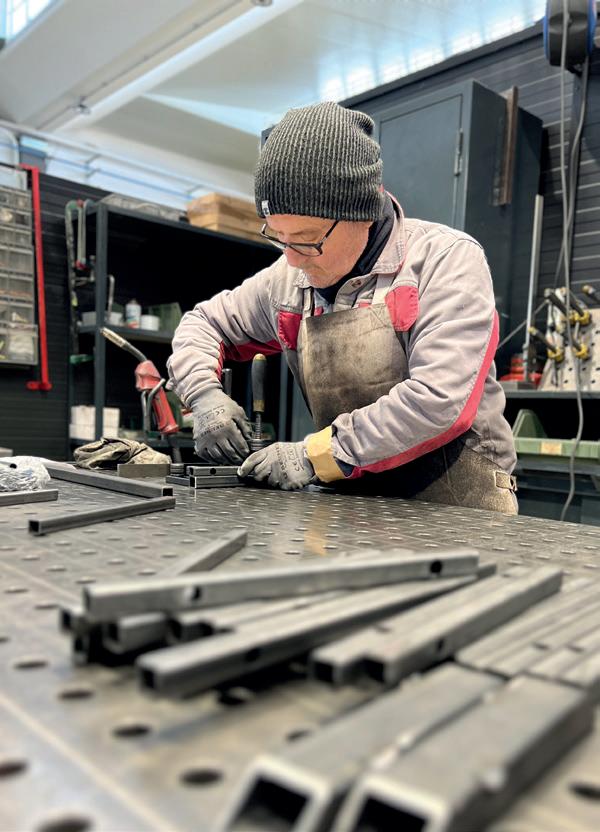
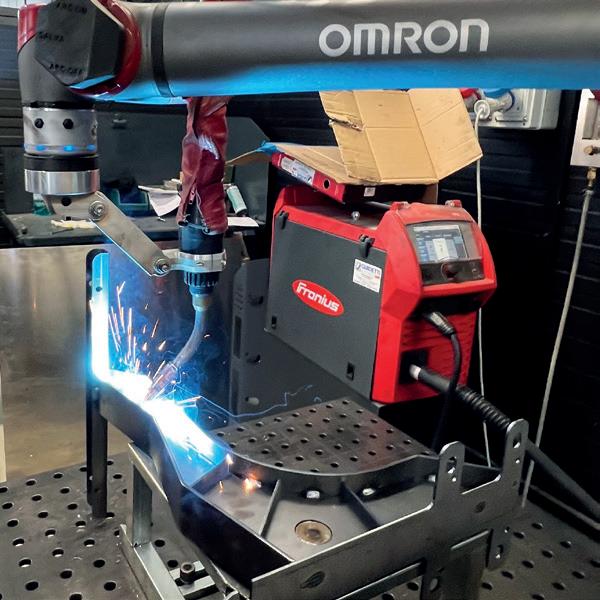
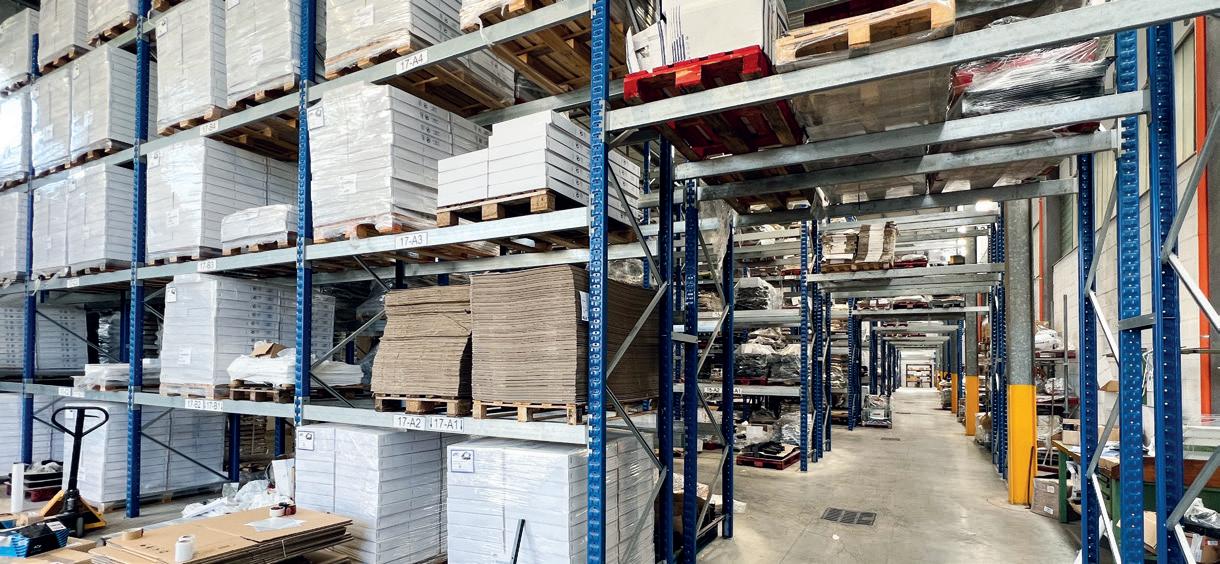
“The layout is optimised for flows,” explains Alessandro Ferrara, CTA’s new production manager, whose role is to optimise all the manufacturing processes. “We have six bending machines, one electronic and five hydraulic, two with seven axes and 150 tonnes, the other three smaller ones with 80 tonnes and four axes. The Cobot can be reprogrammed in a matter of minutes, offering unrivalled versatility and unparalleled flexibility. The production of the Cobot is managed directly through the internal software, so we always know what it is doing”.
