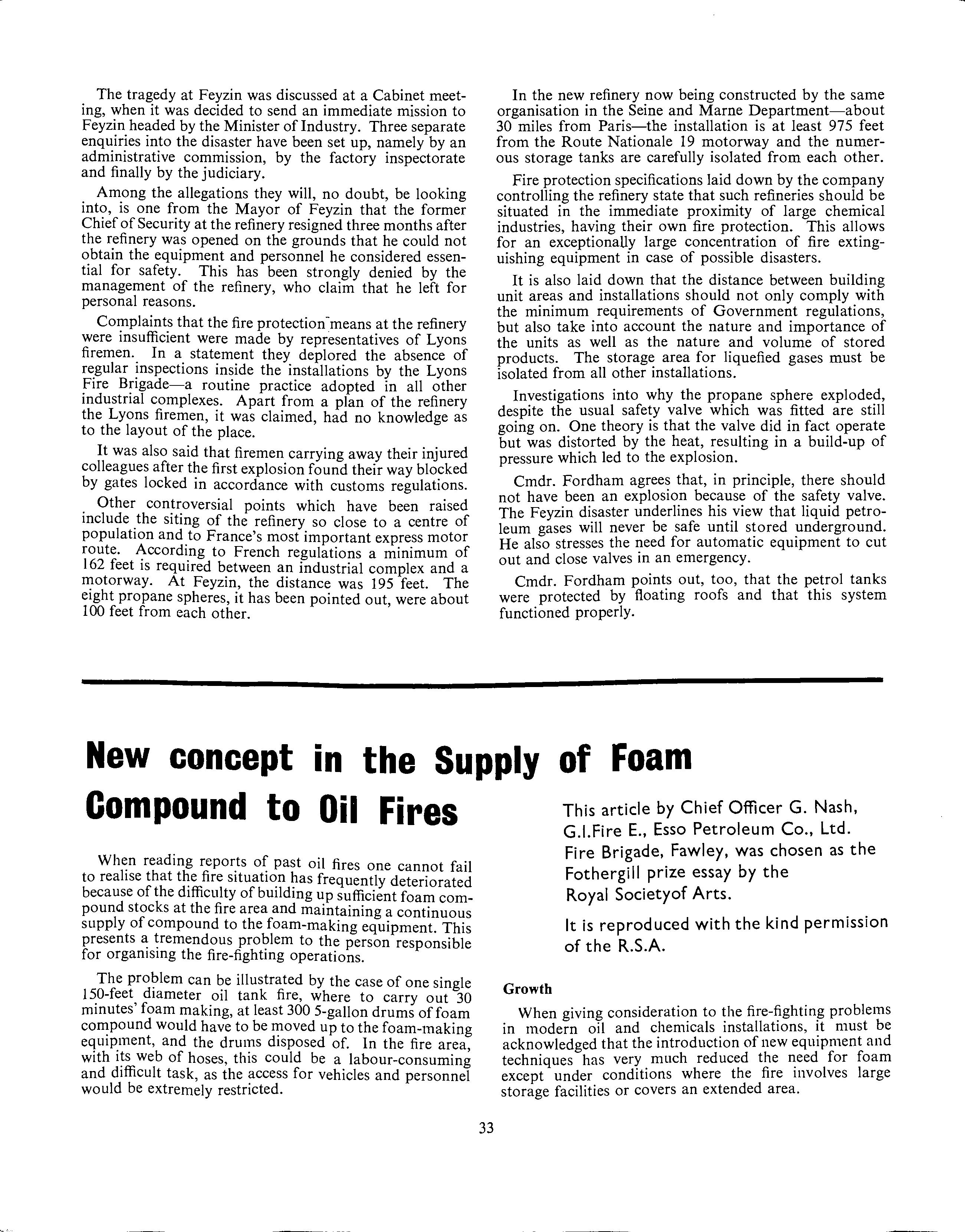
8 minute read
FIRES-G. NASH
from The Bulletin – April 1966
by apeauk
The tragedy at Feyzin was discussed at a Cabinet meeting, when it was decided to send an immediate mission to Feyzin headed by the Minister oflndustry. Three separate enquiries into the disaster have been set up, namely by an administrative commission, by the factory inspectorate and finally by the judiciary.
Among the allegations they will, no doubt, be looking into, is one from the Mayor of Feyzin that the former Chief of Security at the refinery resigned three months after the refinery was opened on the grounds that he could not obtain the equipment and personnel he considered essential for safety. This has been strongly denied by the management of the refinery, who claim that he left for personal reasons.
Advertisement
Complaints that the fire protection-means at the refinery were insufficient were made by representatives of Lyons firemen. In a statement they deplored the absence of regular inspections inside the installations by the Lyons Fire Brigade-a routine practice adopted in all other industrial complexes. Apart from a plan of the refinery the Lyons firemen, it was claimed, had no knowledge as to the layout of the place.
It was also said that firemen carrying away their injured colleagues after the first explosion found their way blocked by gates locked in accordance with customs regulations.
Other controversial points which have been raised include _the siting of the refinery so close to a centre of populat10n and to France's most important express motor route. According to French regulations a minimum of 162 feet is required between an industrial complex and a motorway. At Feyzin, the distance was 195 feet. The eight propane spheres, it has been pointed out, were about 100 feet from each other.
In the new refinery now being constructed by the same organisation in the Seine and Marne Department-about 30 miles from Paris-the installation is at least 975 feet from the Route Nationale 19 motorway and the numerous storage tanks are carefully isolated from each other.
Fire protection specifications laid down by the company controlling the refinery state that such refineries should be situated in the immediate proximity of large chemical industries, having their own fire protection. This allows for an exceptionally large concentration of fire extinguishing equipment in case of possible disasters.
It is also laid down that the distance between building unit areas and installations should not only comply with the minimum requirements of Government regulations, but also take into account the nature and importance of the units as well as the nature and volume of stored products. The storage area for liquefied gases must be isolated from all other installations.
Investigations into why the propane sphere exploded, despite the usual safety valve which was fitted are still going on. One theory is that the valve did in fact operate but was distorted by the heat, resulting in a build-up of pressure which led to the explosion.
Cmdr. Fordham agrees that, in principle, there should not have been an explosion because of the safety valve. The Feyzin disaster underlines his view that liquid petroleum gases will never be safe until stored underground. He also stresses the need for automatic equipment to cut out and close valves in an emergency.
Cmdr. Fordham points out, too, that the petrol tanks were protected by floating roofs and that this system functioned properly.
New concept in the Supply of Foam Compound to Oil Fires
reading repor.ts past oil fires one cannot fail to realise that fire frequently deteriorated because of the difficulty of bmldmg up sufficient foam compound stocks at the fire area and maintaining a continuous supply of compound to the foam-making equipment. This presents prol;>lem to the person responsible for orgamsmg the fire-fightmg operations.
The problem can be illustrated by the case of one single 150-feet diameter oil tank fire, where to carry out 30 minutes' foam making, at least 300 5-gallon drums of foam compound would have to be moved up to the foam-making equipment, and the drums disposed of. In the fire area with i!s web of hoses, this could be a labour-consuming and difficult task, as the access for vehicles and personnel would be extremely restricted. This article by Chief Officer G. Nash, G.1.Fire E., Esso Petroleum Co., Ltd. Fire Brigade, Fawley, was chosen as the Fothergill prize essay by the Royal Societyof Arts. It is reproduced with the kind permission of the R.S.A.
Growth
When giving to problems in modern oil and chemicals mstallat10ns, 1t must be acknowledged that the introduction of new equipment and techniques has very much reduced the need for foam except under conditions where the fire involves large storage facilities or covers an extended area.
33
Storage and transportation facilities have grown tremendously over the past few years; for example, marine tankers in excess of 100,000 tons capacity, and storage tanks of 200 feet diameter, are today commonplace. Although serious fires in such installations are not frequent, when they do occur, the demand for foam compound is increased proportionately; a Super Foam Monitor uses 40 gallons of foam compound or eight 5-gallon drums· each minute. These factors alone make it obvious that we must move away from the 5-gallon and 40-gallon drum complex.
Obstacle
At Esso Refinery, Fawley, this was recognised as a major obstacle to the mounting of an early and sustained attack on any fire situation which required the application of large quantities of foam. Our study and pre-planning to deal with a major incident at our Marine Terminal accentuated this fact.
The obvious answer to this problem is to mechanise the process, and the easiest method of moving a liquid from point A to point B is to pump it, either through fixed pipework or through temporary flexible hose lines.
The ability to use foam compound direct from a pressurised source into mobile and portable foam making equipment, most of which is developed from the principles of the inductor, was a factor, which to the best of our knowledge, had not previously been overcome.
A number of factors had to be considered: (i) Additional equipment to be used must be simple, compact and portable. (ii) It must be economical and usable with existing foam-making equipment. (iii) It must be completely flexible in its application.
The "Constaflo" and "Marie" control valves which are designed to give specified fluid flow regardless of inlet pressures varying between 15 to 200 psig (1.0 to 13.5 atu) are achieved by orifice variation. This is accomplished in the "Constaflo" by means of a flexible diaphragm and a fixed orifice. The diaphragm is the only moving part. When flexed into the fixed orifice, it compensates for increased pressures. The "Marie" valves use a flexible synthetic rubber ring to achieve the same objective. A fixed rate of flow is assured, as flow is regulated in direct proportion to the inlet pressures exerted against the diaphragm or rubber ring. An added advantage of this system is that an operator does not have to rely upon 100 per cent efficiency of the inductor incorporated in the foam-making equipment.

Direct
These valves met the need of our new design concept. We could now divorce the supply of foam compound from fire-fighting operations. Foam compound can now be delivered into the fireground through fixed or flexible pipelines, right up to the point where it is required, i.e., (i) directly into foam-making Monitors, Branchpipes or inline inductors; (ii) directly into the storage tanks of Foam Tenders operating on Tank laterals.
The foam compound required by each piece of foammaking equipment is automatically controlled with regard to both volume and pressure; there is thus no imbalance at the venturi of the inductors. The imbalance at the venturi of foam-making equipment has been the reason why the principle of pumping foam compound into the fire area has not been previously used with success.
This new concept will simplify the work of supplying foam comp~und into the fire area: (i) Only a minimum of manpower and mechanical handling equipment is required. (ii) Because the system is simple it can be brought into operation quickly. (iii) The problem of disposal of empty containers from the fire area is eliminated. (iv) The supply operation is conducted in an area remote from the fireground and by an officer who is not involved in firefighting problems. (v) The volume of compound delivered at any particular point is strictly controlled by the foam-making equipment actually in use. (vi) Most i~portant of all, the supply of foam compound m volume and over a wide area can be accomplished in a minimum of time and sustained for long periods, depending only upon availability of foam compound stocks.
We have estimated that a fire at No. 5 Berth of our Marine Terminal could involve foaming operations which would use foam compound at the rate of 150 g.p.m. Because. of the restricted approach and the distance ~nvolved, 1t would have been completely impractical to bmld up a successful foam attack in sufficient time to have achieved success in fire-fighting operations.
The new concept of foam compound supply will enable us to start full scale_ foaming operations within a half an ho~r of a .fire startmg, and to sustain operations for. a penod of time dependent only upon the volume of available foam compound stocks.
ASSOCIATION PUBLIC A TI ONS
The following documents on recommended practice are available from the Hon. Secretary, Mr. L. A. Cave, Dudley, at a cost of 2/6d. for the set of five. (1) General requirements as to the storage of Petroleum Spirit in underground tanks other than at bulk storage and distributing depots ; (2) Ge.n~ral requirements as to the storage of Petroleum Spmt or Petroleum Mixtures above ground (other than bulk storage) ; (3) Genera~ requirements as to the storage of Carbide of Calcium ; ( 4) E!ec~rical installations-Minimum requirements w1thm the hazard area on petrol station forecourts; (5) Report Form - Examination on electrically operated petrol service pump.
34