1983
Journal of the Association for Petroleum and Explosives
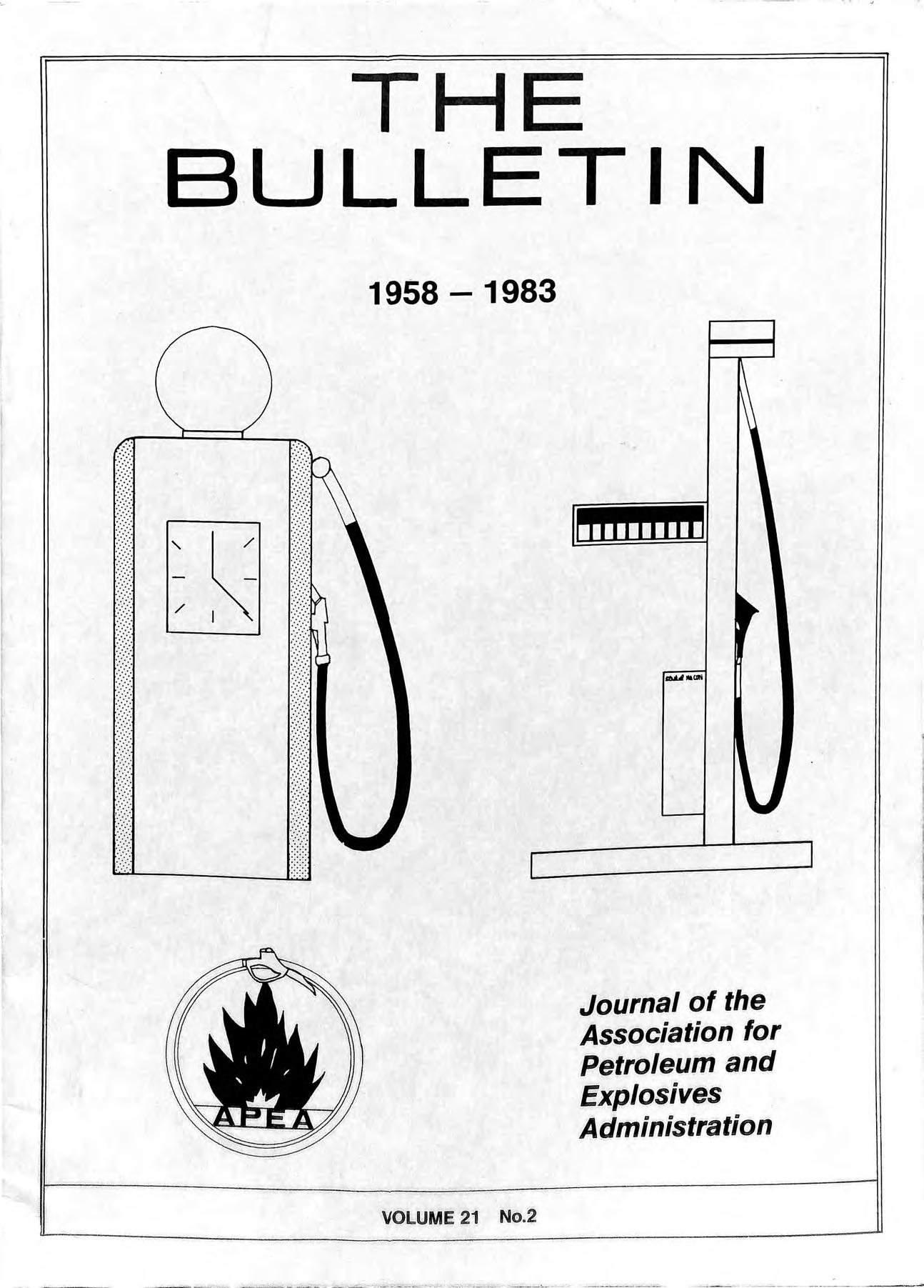
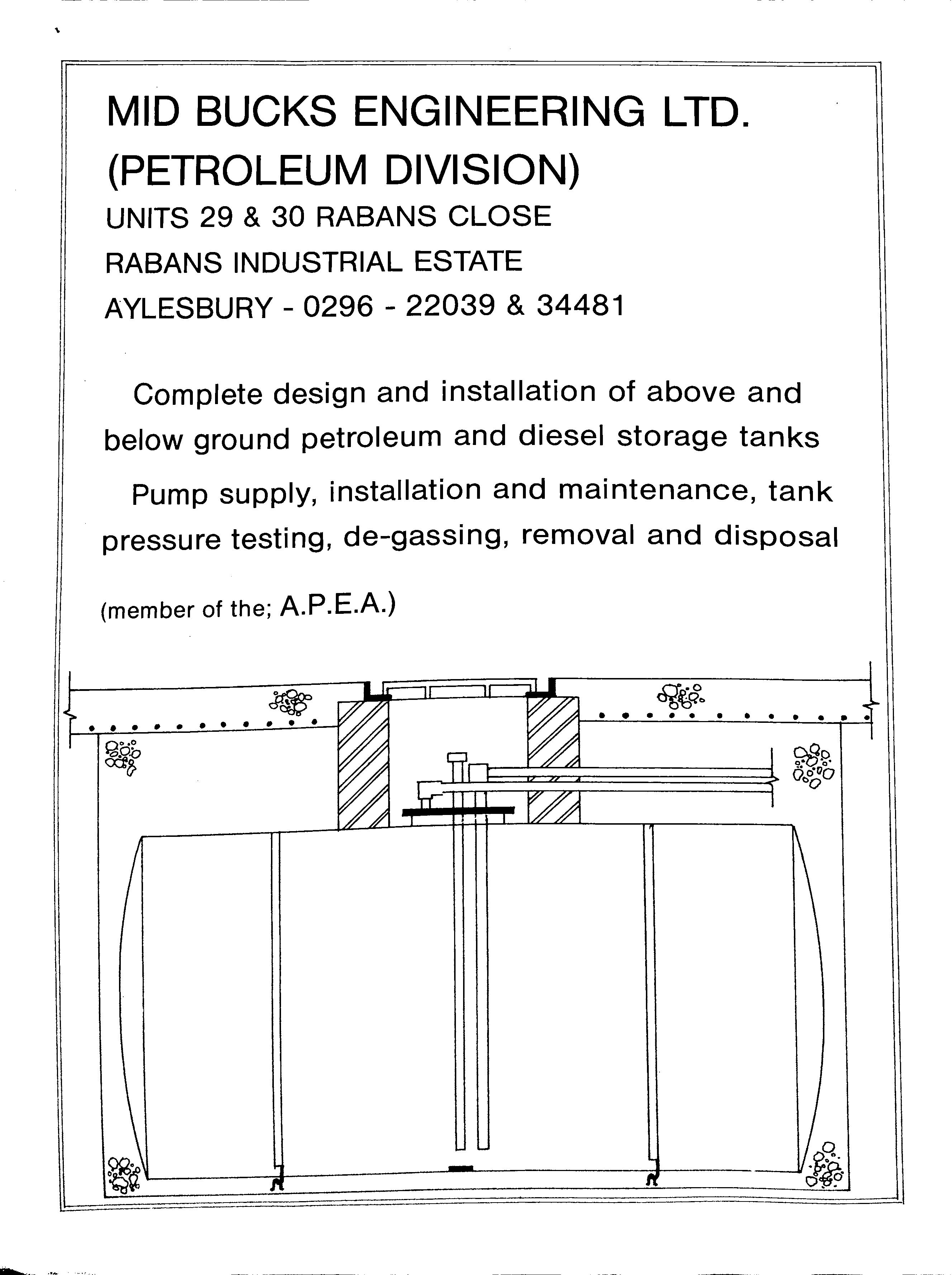
If you run a fleet of petrol engine vehicles, the last thing you want is expensive petrol.
Especially when there's a cheaper, better alternative Calor Autogas. Autogas is a liquefied petroleum gas. The big difference between it and petrol is 40 pence or more per gallon.
Put another way, you could save over £ 1 for every three gallons of Autogas you use.
And that's only the start of it. Autogas is a cleaner burning fuel. So the engine, the plugs and the oil stay cleaner, longer. Oil life, for example, can be as much as four times longer. Think what that means in reduced maintenance costs.
With Autogas, you don't need the to make a cold start. So costly petrol Isn t swamped into the engine to wash away the protective oil film
It's pilfer proof.
You. can have your own pump installed for f uelllng your fleet. Autogas is also avadable at a growing number of points the country currently over 300, including some Motorway and self service sites and can be bought on a Calor Autogas credit card.
And converting your fleet to run on Autogas doesn't eliminate petrol operation: you can even switch from one fuel to the other while on the move. So you have the back-up of petrol should you ever need it More miles per £1. More miles between plug and oil changes. More miles per vehicle before it needs replacing. What more could you ask for. Get the full, money saving story. Contact your regional Calor Gas office now.
Scottish Region Friarton, Perth PH2 8DQ Tel: Perth (0738 ) 25222. Telex : 76129
Northern Region , 171 Elland Road, Leeds LS 11 8BU Tel: Leeds (0532 ) 707193 Telex 55479
North Western Region. k d R d Ellesmere Port, Wirral , Doc yar 00 , Cheshire L65 4EG Tel: (05 1) 355 3700 Telex: 629332
Eastern Region. 63 Thorpe Road, Norwich, Norfolk NRl l UF Tel: Norwich (0603) 27207 Telex : 971 51
South Western Region. Millbrook Trading Estate, M illbrook , Southampton S09 1WE Tel: Southampton (0703) 777244 Tele x: 477442
South Eastern Region. Point Pleasant, Wandsworth, London SW18 lNN Tel (01) 870 4231 Telex : 9286 13
During the past 2 years a different type of drive belt has appeared on forecourt petrol dispensers. The name IS Tab-Link, and its unique polyester/polyurethane construction enables this belt to last a minimum of six times longer than conventional V-belts It's easier to service, as one enables the service engineer to make up any length of belt to SUit all pump assemblies thereby greatly , reducing the stock carried
When it comes to the manufacture of pump equipment a design is possible uSing Tab-Link as the tensioning and sliding systems used with conventional drive belts aren't needed , Tab-Link is in successful usein petrol I dispensers throughout Britain , Including those ' serviced by Pump Maintenance Limited, and bUilt by Avery-HardoIlLtd., TokheimLtd. and Ferrantl Ltd
VOLUME 21 Number 2
APRIL, 1983 £2.50
(Free to Members)
Published by the Association for Petroleum and Explosives Administration
Opinions expressed in this Joumal are not necessarily the views of the Association
TALKING POINT
19 20 22 23 ELECTRICAL APPARATUS IN EXPLOSIVE ATMOSPHERES 24 PROSECUTIONS 29
NOTES AND NEWS CHAIRMAN'S ADDRESS SAFETY TRAINING
LONDON NEWS 31 BRANCH MEETING 32 ROAD TANKER LOADING SYSTEMS 33
The Council of the Association are working on the introduction of an updated code of practice for petrol filling stations which is intended to replace the Associations present code and the outdated Home Office code.
A draft is being considered and this reflects modern thinking and standards and it is hoped that a decision will be made soon on the date and method of its publication.
If members of the Association wish to make any comment on the existing code and its shortcomings they may contact the Hon. Secretary who will pass these comments to the Council for consideration.
Honorary Secretary M r. E. Brown, Cambridgeshire County Council,
Honorary Editor Mr..J. A. J. Thompson,
On the IstJanuary 1983 the above regulations came into force, and in consequence of Regulation 7 (1) the Health and Safety Executive becomes the enforcing authority for any sites which are subject to notification. The list of hazardous substances which make a site subject to notification are listed in Schedule 1, and it includes liquids having a flash point ofless than 21 "C when kept in a quantity exceeding 10,000 tonnes. This definition obviously includes petroleum spirit and petroleum mixtures.
Accordingly, licensing authorities have no enforcement jurisdiction, but it appears that they may continue to issue licences and collect fees until 1st February 1985, since the power to issue licences is not gi ven to the Heal th and Safety Executive until that date Regulation 7 (2).
In the transitional period, the Health and Safety Executive will be enforcing different licence conditions imposed by various Local Authorities on sites which the Local Authorities have no powers of inspection.
In addition to the relatively simple situation of a large quantity of petroleum being a notifiable substance there will also be situations where a smaller quantity of petroleum, or even any quantity of Carbide of Calcium, or liquid Methane, being kept on the same site as some notifiable substance. For example, two tons of hydrogen kept on the same premises as any licensed store would bring the enforcement requirements on the site under the control of the Health and Safety Executive as from the 1stJanuary 1983. Whereas the Health and Safety Executive may not grant the licence until the I st February 1985.
The fees payable to local authorities for the licensing of stores and registration of premises used for the keeping of explosives are to be increased from 1 April 1983.
The Explosives (Licensing of Stores and Registration of Premises) Fees Regulations 1983, drawn up by the Heal th and Safety Commission (HSC) following consul tation with the CBI, TUC, local authorities and other relevant organisations, amended the appropriate sections of the Explosives Act 1875, as follows:
maximum fees payable for the issue or renewal of a store licence (Sections 15 and 18) to be increased from £17.50 to £30;
payable for the registration, or of of premises used for the keeping of explOSives (SectIOn :ll) to be increased from .£:i to .C5.
The Commission, which says the increases are designed to help cover t.he full economic costs of carrying out the licensing and registration services, has estimated that the additional costs to be borne by industry will comprise an extra £:l for each of about :21,000 registered premises, and an extra
£ 12.50 for each of about 1,400 licensed stores. The increase in revenue to local authorities, therefore will be approximately £60,000.
The Explosives (Licensing of Stores and Registration of Premises) Fees Regulations 1983 were laid before Parliament on 4 March by MrJohn Selwyn Gummer, Parliamentary Under Secretary of State for Employment.
NEW EXEMPTION CERTIFICATE ISSUED UNDER THE DANGEROUS SUBSTANCES (CONVEYANCE BY ROAD IN ROAD TANKERS AND TANK CONTAINERS) REGULATIONS 1981 Exemption Certificate No.l of 1983 has been issued by the Health and Safety Executive (HSE) under the Dangerous Substances (Conveyance by Road in Road Tankers and Tank Containers) Regulations 1981.
The Regulations, which with the exception of Regulation 7, are now fully in force, control the of dangerous su bstances in of any capac.I ty and m tank containers with a capacity m excess of 3 cubiC metres.
Paragraph7 of Schedule 3 of the Regulations allows an operator to use the words 'consult local depot'.in the lower space of a hazard warning pane.1 as an to a phone number, provided certam conditions are compiled with.
When the Regulations were drafted, it a reed with industry that the words contact local depot g t ble alternative to the telephone number, were an accep a , I I Id' . d afting error the words consu t oca epot butowmgtoa r , d'n the Statutory Instrument. were contame I hrase 'contact local depot' is already widel y used Smce the: panels throughout industry as an alteron ?azar number, in many cases going back to native to a p I 'ere first used under the Chemical Inthe days when scheme, Exemption Certidustries AssoCla 10 d d h 1981 . f 1083 allows its continue use un er t e , flcate No. 1 0 Regulations.
. h tificate can be obtamed from: Copies of t e cer
Health and Safety Executive HSDA3
ESSING ELECTRIC SURFACE HEATING ASS ., h St dards Institution has published the first The Bnhs an rf h . ·h· lb· f BS ('3 r.: 1 Electric su ace eating VI' IC 1, ) t Parts 0 ) ,) '\I wo 'd" mmon method of assessing ESH systems, WI Pro VI mg a co th t f· h working in chemical engmeenng, e ranbene It t ose d 'h h t f . d t and anyone concerne Wit t e s orage 0 sport m us ry ., temperature senSitive matenals.
P , 1 S ecification for electric surface heatin,g, ?ealt the applications for and advantages of 1<.SH. vices.out metss fOl' construction and testing applit'd to metal ReqUlremen , f ecified both in non-hazardous areas and 111 SUl aces ale sp, .' , I' h h 'd )llS areas (other than 111 all ne and 1111 11l ng app I t ose azal l )
, 'xplosive processing and manufacture class! catIOns, Ol e " -, -C d f ti f fied as Zone 1 or Zone '2 1\1 BS :),1-L1: ° eo prac ce o.r the selection, installation and maintenance. of electncal apparatus for use in potentially.explosIve atm.ospheres (other than mining applications or explOSIve processing and manufacture).
Specifications for the construction of heating cables and tapes, heating cable units and tape units surface are given separately, together with requIrements SUItable terminations. Test methods described mclude temperature, mechanical strength, tests for factors such as conformity and rehablhty. Markmg requirements are given. A special section additional requirements for ESH devices for use areas and an appendix gives guidance on certIfIcatIOn.
As its title suggests, Part '2 Guide to the design of surface heating systems serves as a gUIde to the design of a safe ESH device. Energy reqUIrements, temperature consideration and the selection ESH systems, well as thermal insulation and control eqUIpment are conSIdered.
Minimum safety requirements for different types of ESH device and control equipment are given with help. of tables. Specifications are provided for thermal msulatIOn and wiring systems, while a separate section serves a guide to the design of ESH systems generally. Append.lces, largely in the form of tables, cover heat loss calculation of spiral pitch, an example of how the deslg.ner should work to manufacturer's specification, mathematIcal formulae and meteorological data.
Part 3 of BS 6351 Code of practice for installation, testing and maintenance of electric surface heating systems is in preparation.
The British Standards Institution has published a revision of BS 5045 Transportable gas containers Part 1 Specification for seamless steel gas containers above 0.5 litre water capacity, one of a series of standards relating to the conveyance by road of permanent, liquefiable and dissolved gases under pressure in various types or sizes of containers.
Part I specifies the materials, deSign, construction and testing of seamless steel containers of water capacity greater than O.S litres. The main changes from the earlier edition are the incl usion of requirements for the carriage of dissolved acetylene and for containers fitted to trailers in hydrogen service, in addition to a general updating of the material requirements. The reVISIOn incorporates appendices which provide examples of design calculations, a description of methods to be used for pressure testing and ul trasonic examination, and model forms of design and acceptance certification.
(>ther Parts of the standard published previousl y are Part '2 Specification for steel containers up to 130 litres water capacity with welded seams, and Part 6 Specification for seamless containers of up to and including 0.5 litre water capacity.
of BS .j(j4.) : Part I may be obtained from the BSI Sales Department, 101 Pentonville Road, London N I 9ND. Price (lkO() CO.OO to BSI subSCribing members).
/{('centl y there was a small explosion at an Ayrshire quarry. All electric detonator blew up without warning. No damage was d()Ile'. and IlO one was injured. S() lar, n() explanation for tlw cause of the blast has been f()lJnd.
BIJI ()/](' i1W()I'r is that the det()nator may have been trig ).!,1'H'd /)\ illl dlegal citizen's band radio unit.
As a result, quarries throughout Scotland have po.sted warning signs banning all c.B. radios from blastmg SItes.
The warning was issued by the explosives division of I.C.1. Ardeer.
I.C.1. manufacture nearly all detonators used in Scotland. Their research has found that C.B. units which conform to legal requirements pose no danger to detonators.
But a C.B. unit that is illegally modified to transmit more powerfully, may be a threat.
The stronger radio signal can trigger detonators.
Retail outlets of LPG (liquefied petroleum gas) should operate under a strict compulsory code of practice says Association of County Councils (ACC) to give the publIC similar safeguards already existing with petrol filling stations.
There are strict controls over petrol filling stations, but no such controls exist for LPG despite its increasing use as a motor fuel and the risk that it can be more dangerous than petrol.
The Association's Consumer Services Commi ttee is now to ask the Health and Safety Executive for the introduction of regulations which would make compliance wi th the code of practice mandatory for all retailers of LPG for use as motor fuel. Warwickshire County Council had expressed concern to the ACC about the absence of a retail licensing system.
Self-service LPG dispensers can be particular hazards as incorrect operation by the motorist can cause the tank to be overfilled, with the risk of excessive pressure with temperature rises. Tank gauges have been found to be unreliable and there have been several dangerous escapes of LPG.
If petroleum spirit is spilled, it remains as a pool and only the upper surface has the flammable vapour-air mixture. The LPG vaporises immediately into a mixture that easily find a Source of ignition, with the risk of an hornfIc accident and extensive damage.
In the long term, the committee felt that LPG should be specifically controlled as a substance rather than by each method of use, such as by storage, heating or motor fuel.
Chairman of the ACC's Consumer Services Commi ttee Geoffrey Waterer a member of Essex County Council, '. the saId "We believe there should be stnct control over retail sale of LPG as motor fuel, because it is so important to public safety with the inherent dangers )11volved in handling the product."
With the difficulties which b eset the Association on lo cal government re-organisation well b ehind us I beli eve that this yea r has seen a further enhancement of our aIms and e n deavours. In particular I feel that tt was ftttmg that the members decided to invite into full m em bership our co llea gues from industry and commerce: Thegreatest strength o f our organisation is th e forum for dU'ect mt e rc hange of te ch nical and legal knowledge betw ee n enfo rceme nt offi ce rs and the petro leum industry which is created at our meetings nationall y and lo call y It h as been very gratify in g to note that increasing role which industr y members ha ve pla ye d duting this year at the nati onal seminar and in branc h activities.
I am proud to hav e taken the leading role in the Assoc ialiun as yo ur C hairman during the past yea r and h ave enjoyed the experience imm ensel y I trust that I h ave ful filled III y in · tention of setting the Association on a firm point e r for thi s Silver Jubile e yea r and th e years ahead
R. C SmithThe requirements of legislation, both specific as in the new Dangerous Substances (Conveyance by Road in Road Tankers & Tank Containers) Regulations and more generall y as in the Health & Safety at Work the need to introduce comprehensive inductIOn trammg programmes for all new recrui ts, for repeat trai.ning.( ei ther "onthe-job" or in a classroom or equivalent situatIOn). to take place at regular intervals and for attention to be paid to the training needs of existing employees (including managers etc.). Details of all such training given and received should be well documented.
Those who handle petroleum spirit should especially have achieved a reasonable level of competency. It should be remembered that they hold a duty not only to take steps for their own safety, but that they have a much wider duty towards the community as a whole. But it is not to indicate that in merely providing training, this, by ImplIcation, establishes competence in an individual to undertake his duties. The recognition of the competence of individual must remain with the appropriate manager. Howev:er, training of the right kind can provide the knowledge, skills and understanding required and can do much to influenc.e attitudes in the right direction. Professional competence IS a mixture of training and experience.
All employees should be trained so that they will be alert to the specific risks found in their work, as well as the more general ones associated with any modem industrial undertaking. They should be thoroughly trained in all of their duties, not only by theoretical training, but also With a period of practical work under supervision. In both of these, it is important that employees should be given an understanding of the reasons behind the various procedures adopted. It is essential that all new employees a.re. so trained, but the necessity for refresher training of eXlstmg employees should not be neglected.
It is especially necessary to alert those who handle petroleum spirit to the hazards inherent in their everyday work. El t··t df ·ngobiects ec nCI y, gas, fire, high pressures an ast-moVI J are familiar of aspects of day-to-day life, but they should be treated with respect. Familiarity can lead to often with fatal consequences, particularly when handling petroleum spirit. The aim of training should be to promote understanding as well as awareness of the hazards. It should designed to give, under controlled conditions, some idea of the n.ature of the hazards that may be encountered, how they anse and how they may be controlled.
When considering the theoretical aspects of training, it o.;ho uld be remembered that those who handle petroleum o.;pirit often on critical operations without .,1IJ'l'rVlslon. I herefore, a higher level of understandmg r /1;J 11 rhat merely required for routine operations should be lled;tf In any training programme for such employees ,tIll I. ,/I, ,v\ I ng specific points should be covered in depth:
The characteristics of the material and the hazards to which it can give rise, including flammability, toxicity (both ofliquid and of vapours) and the liability to cause skin irri tation or eye damage. How these hazards can be avoided or minimised.
The law, in so far as it relates to the trainees duties and responsibilities, statutory and otherregulations relating to the storage and handling of petroleum spirit.
a) The procedures to prevent fire, and the action to be taken in the event of fire including the design, operation and limitations of extinquishers and hoW to summon the fire brigade.
b) The procedures to avoid the risk of spillage and the methods of containment, preventing ignition and cleaning up of any spillage that does occur.
c) The procedure to prevent the hazardous contamination of other materials by petroleum spirit and the necessary steps to be taken in the event of such a contamination.
The training of people who handle petroleum spirit has been going on in varying degrees for a long time. Guidance on the subjects to be covered have appeared in earlier publications of the (then) Petroleum Industry Training Board and the Road Transport Industry Training Board. However, so far, no national standard for training has existed. If such a standard could be introduced, it would be a valuable contribution to safety. Employers are urged to enthat their employees receive the "necessary" trainmg, but With no definitive advice. Petroleum Officers have a role to play in this. I have often considered that enforcement authorities in their quite correct zeal to ensure that the "hardware" (design, construction, location of equipment etc.) involved in handling petroleum spirit is adequate and safe, have tended to overlook the "software" (the people) involved. Perhaps some greater concern as to these people's competency (including the training they have received) might effect an improvement.
(G.A. Edney was previously Project Manager, Fire & Safety with the Petroleum Industry Training Board. He is now a leading fire, safety and training consultant to the oil industry).
For information of his courses Mr. Edney may be reache.d on OH444 7!J!):·t
This paper was presented at the Third International Conference on Electrical Safety in Hazardous Environments at The Institute of Electrical Engineers in London on 1st December 1982.
0.800n Shell Internationale Petroleum Maastschappij, The Hague, Netherlands.
The selection of electrical apparatus for industrial applications should primaril y aim at a long-time reliable operation and good performance in an, often hostile, industrial environment. When the electrical apparatus is to be used in an explosive gas atmosphere, proper attention shall also be paid to the prevention of an explosion created by the electrical apparatus as a consequence of sparks or hot surfaces. The selection shall then aim at reducing to an acceptable low value the probability that the electrical apparatus could cause an explosion.
For causing an explosion it is necessary that the explosive gas and a source of ignition exist simultaneously. When at a certain location the likelihood of having an explosive gas is high, the electrical apparatus shall be so constructed that the likelihood of creating a source of ignition is small. On the other hand, a somewhat higher probability of a source of ignition can be accepted for places where the likelihood of having an explosive gas is only small. A careful matching of the electrical apparatus to the actual hazard condition is therefore necessary, on one side to ensure an adequate level of safet y and on the other side to avoid unnecessary costs for the apparatus, complications in system design etc.
paper provides guidelines for assessing the hazard condition and a survey of the special executions of electrical apparatus intended for use in explosive gas atmosphere. on this information, a rational procedure for the selectIOn of electrical apparatus with an adequate level of protection is developed.
The gas atmosphere surrounding the apparatus are usuall y classified as follows:
area: An area in which explosive gas/air mixtures not expected to be present in quantities such as to reqUire special precautions for the construction and use of electrical apparatus.
Hazardous area' A . h' I I' /.. . n area m w IC 1 exp oSlve gas air mixtures are or may b ." h ' . e expected to be, present m quantities sucd as to require special precautions for the construction an use of electJical ap t para us.
Z A la:ea is divided into zones as follows: ,one : 111 w 11Ch an e I' /.. xp OSlve gas all' mixture IS contInuousl y present or present for long periods.
Zone I: in which an explosive gas/air mixture is likely to OCcur in normal operation.
,-.. ,-
Zone: $ in which an explosive gas/air mixture is not likely to occur and if it occurs it will only exist for a short time.
The extent of each hazardous area should be determined by properly qualified specialists and be indicated on an Area Classification Drawing.
Apart from the classific:. on of the hazardous areas and their extent, the area classification drawing should also indicate the temperature classes and the grouping of the gases in relation to the explosion-protected apparatus.
In a well-designed, well maintained, open air installation the hazardous area will be predominantly Zone 2, with isolated places being Zone 1 and very rarely a Zone O.
The internal hazards in process vessels, associated piping etc. do not form part of the above area classification procedure for assessing the hazards, if only because there is normally no air at atmospheric pressure. When, however, electrical apparatus is used inside such equipment, the hazards can be assessed by comparing them with the hazards as defined for area-classification. For instance, in a vessel processing hydrocarbons under normal operation, but where air may be present during abnormal situations such as plantcommissioning or shutdown and then only for a short time, the hazards are comparable to Zone 2. When flammable substance is stored in an open vessel and the vapour space is in open communication with the surrounding atmosphere, the hazards are comparable to Zone O.
Sometimes a flammable substance is of necessity introduced into the enclosure of an electrical apparatus, in particular in instruments used for measurement and control of process variables. on the integrity of the const · the devices contammg the flammable substance truc IOn, t ·t te a source of release. The seven ty of thiS mterI nal hazard depends basicallr?n whether an mternal re ease d r nOllnal conditIOns or only under abnorn1al occurs un e condi tions.
It should be realised that the consequences of a release of flammable substance in an enclosure may be more than a similar release in the the matenal released internally usually remalllS .wlthm the enc.losure. A leak which might go undetected m the open,. will slowly the concentration inside an enclosure until the atmosraise l'h' . . t t' h becomes flammable. IS lllcrease m concen ra IOn slowed onl y slight! y by breathing and diffusion.
On the other hand it should be realised that in the usualh small-size enclosures in which the internal release may octhe g'as concentration will quickly pass the higher ex< • plosive limi t when the release contmues.
Although specific rules cannot be written .which "viii apph al ways to all types of apparatus, the tollowlIlg ma y serve for general guidance:
Electrical apparatus may be consider:-d to have no abnormal release when even under any foreseeable abnolll1al conditions there is no possibility that an internal release ut flammable substances could occur. A typical example is a bourdon tube with such mechanicalligidity that overrang ing to any foreseeable oyerpressure \\ill not cause a failure of the tube (figure I).
Electrical apparatus should be considered to have an ab· normal release when under release nt tlammable subs tancecollld OCCLll". A typical example is a thill ,\alled metal
diaphragm or bellows, which could develop a mechanical failure due to repeated flexing and/or incidental overranging (figure 2).
In order to have no nonnal release inside an enclosure there must be a minimal risk that flammable substance will escape from its containment system during the time the apparatus is in service within the range of service conditions to which it is likely to be subjected.
Apparatus which cannot meet the requirements for "no normal release" should be considered to have a nonnal release. Seals, rotating or sliding seals, flanged joints, flexible non-metallic tubing should be assumed to leak minutely after a period of service.
Where dilution with air is applied, it is also necessary to differentiate between restricted releases and unrestricted releases. In this context, a restricted release is one in which any release of flammable material is limited to a value within the diluent capacity of the protective gas system. Where necessary, this may be achieved by placing restrictions in the pipes supplying flammable substance to the apparatus.
An unrestricted release is one in which any release is not restricted to a value within the diluent capacity of the protective gas system.
In general, the internal hazards caused by abnormal releases are comparable to those in a Zone 2 hazardous area, whereas normal releases will create internal hazards which are comparable to Zone 0 hazardous areas, but exceptions to this rule can occur, e.g. where pressurisation with inert gas or dilution with air is applied.
After assessing the external hazards and the internal hazards in the process eqUipment and the electrical apparatus, the most onerous of these conditions shall be taken as a basis for selecting the electrical apparatus.
When, for instance, apparatus in which the internal hazards are comparable to Zone 2 is installed in a non-hazardous area or in Zone 2, the internal hazards determine the actual ?azard condition, but when the same apparatus is installed III Zone 1 or Zone 0 the external hazards determine the actual hazard condition.
Where the external hazard is classified as a Zone 2 hazararea or the internal hazards are comparable to Zone 2, It often be possible to use apparatus of good industrial quality and primarily intended for use in non-hazardous provided that in normal operation it does not create I?ruhon-capable arcs or sparks and does not produce ignitiOn-capable hot surfaces.
This concept does take into account that under abnormal the apparatus may become ignition-capable, but nsk of the Simultaneous presence of such a source ofigand an explOSive atmosphere is considered to be negligible for Zone 2 hazardous areas.
The SUitability of industrial apparatus for use in Zone 2 shouldbe assessed by a competent person. This assessment IS relatively easy because only the normal operation of the apparatus needs consideration. EspeCially in the field of light ( urrent technology, such as process-instrumentation, iI wdJ befuundthat most, if not all, industrial apparatus can "f' IlSf'{.J furthwlth, because heat-development is usually no
problem and most circuits are fully closed. Where sparking occurs under normal operation, such as switches for alarmannunciation, the maximum safe circuit parameters can be found in the Widely published ignition curves for intrinsic safety, but without the application of safety factors.
Where the use of industrial non-sparking apparatus is not possible, special methods must be applied for ensuring that the electrical apparatus will not cause an explosion, these methods are known as "types of protection".
The recognised types of protection are norm all y indicated by a letter-symbol, a survey of these symbols and a short explanation of the intentions of the particular type of protection is given below, see also Figure 3.
d: Flameproof enclosure. A type of protection in which those parts of the electrical apparatus which could cause an explosion are located in an enclosure which will whi thstand an internal explosion of an explosive mixture without suffering damage or propagating the internal flammation, through any joints or structural openings in the enclosure, to an external explosive atmosphere.
e: Increased safety. A type of protection giving an increased security against the possibility of excessive temperature and of the occurrence of arcs and sparks.
h: Hennetic sealing. Apparatus designed to contain potential means of ignition in a gas-tight shell protected against mechanical damage.
i: Intrinsic safety. A type of protection in which all circuits are designed such that any spark or thermal effect, produced either when it confirms electrically and mechanically with its design speCifications, or in specified fault conditions, is incapable of causing ignition of a given explosive mixture. There are two categories of intrinsic safety:
Category ia, in which the apparatus is incapable of causing ignition in normal operation, or with a single fault, or with any combination of two faults applied, with a speCified safety factor for current and/or voltage.
Category ib, in which the apparatus is incapable of causing ignition in normal operation, or with any single fault applied, with a specified safety factor for current and/or voltage.
m: Encapsulation. A type of protection in which potential sources of ignition are embedded in a mass of fire-resistant solid insulation material. This material should be proof against fracture under internal fault conditions.
n: Non-incendive apparatus. Apparatus which in normal operation produces neither ignition-capable arcs or sparks nor ignition-capable hot surfaces is considered to be oonincendive.
0: Oil immersion. A type of protection in which the electrical apparatus or parts of the electrical apparatus are immersed in oil in such a way that an explOSive atmosphere which may be above the oil or outside the enclosure cannot be ignited.
p: Pressurisation. This type of protection has three categories:
Pressurisation with air applies where the entry of an explosive atmosphere into an electrical apparatus is prevented by maintaining the pressure of the air within the enclosure above that of the external atmosphere.
Pressurisation with inert gas applies where the entry of the external atmosphere into an electrical apparaus is prevented by maintaining the pressure of an inert gas within the enclosure above that of the external atmosphere.
Continuous dilution (artificial ventilation) is the application of a flow of protective gas (usually air) through an enclosure in sufficient quantity to disperse and dilute any possible gasor vapour resulting from an internal release of a flammable substance so that an explosion is prevented. In a hazardous area an overpressure should be maintained within the enclosure to prevent the entry of the external atmosphere.
To guard against a hazardous si tuation arising if the suppl y of protective gas within the enclosure is not maintained, a visible and/or audible alarm shall be made. Immediately following an alarm condition, corrective action shall be taken to restore the supply of protective gas or, when necessary, to manually switch off the electricity supply to the apparatus.
Where this cannot be realised, automatic switching-off the electricity supply may be necessary.
g: Powder filling. A type of protection achieved by filling the enclosure with a material in a finel y granulated state so that in the intended conditions of service any arc occurring within the enclosure of an electrical apparatus will not ignite any external atmosphere. A typical filling material is granulated quartz.
r: Restricted breathing. A type of protection where sources of ignition are contained within an enclosure tight enough to prevent for a limited time the penetration of a sufficient quantity of the external atmosphere to produce an internal explosive mixture and where external components are incapable of causing an explosion.
s: protection. A designition for those types of protection that cannot be classified as belonging wholl y to any one of the above types. It may be that a combination of several types of protection is incorporated within one piece of apparatus. For apparatus with this type of protection, the related documentation shall indicate for which hazards the specific version is adequate.
types protection providing an adequate level of safety In a particular hazard condition are indicated in Tables 1 and 2. Among the types of protection indicated as being adequate, a large number is not really necessary or is too for the particular hazard. A further analysis of all app.hcable details is therefore required to arrive at an selection of a type of protection required for the partIcular hazard.
It should further be noted that there is not yet a common on this subject, in particular on the need for automatIc switch ff f' I f -0 0 pressunsed apparatus. n case 0 uncertal11ty the m . . h h b C I Die conservative approac as een.olowed and some I . d . h f re axatlOns may therefore be expecte 111 t e uture.
eleven types of protection described above cover the baSIC approach for h" f ac levl11g sa ety, but do not speCify constructIOnal requ' t f hI' nemen s or tee ectncal apparatus, these are the subject of construction standards. There is a
large number of such standards, published by national standards organisations, the European Committee for Electrotechnical Standardisation (CENELEC) or the International Electrotechnical Commission (IEC). A survey of the standard publications currently in use is given in Table 3.
The national standards often show large differences in requirements for the same type of protection. A considerable improvement in harmonisation has been achieved by the publication of the so-called European Standards (EN50.014/50020) which have been published as a national standard, or accepted as such, by all countries organised in CENELEC. Moreover it has been formally stipulated that member-countries of the European Economic Community cannot prohibit the sale or free movement or use of electrical apparatus when it complies with the requirements of the above european standards and as proof thereof has been certified by a recognised testing institute. This agreement is clearly an improvement over the barriers to trade existing formerly and it is to be expected that in the future new designs for electrical apparatus will be based almost exclusively on these european standards, but the use of electrical apparatus in confoimity to other standards remains possible.
Several countires have testing institutes, such as BASEEFA in the United Kingdom and PTB in Germany, as independent organisations for assessing whether the electrical apparatus complies with the requirements of a specific construction standard and for subjecting the apparatus to certain tests when so prescribed in that standard. The testing institute issues a "Certificate of Conformity" when the aparatus complies with the requirements of the standard, or "Inspection Certificate" when it does not compl y wi th all details in the standard, but provides a degree of safety at least equivalent to that of the standard.
The above applies primarily to electrical apparatus intended for use in Zone 1 or Zone 0 hazardous areas. For . t ded Cor use in Zone 2 hazardous areas, such as WI th tUS111 en .' t e of protection n or r, it is not usuall y re9U1red to engage yp t' I'nstitute in such cases the manufacturer can pro- a tes 1l1g , vide a declaration of conformity.
Wh these certificates or declarations exist, the user collect, study and file them. Their value should, h not b e over-estimated, if onl y because do not owever, d h' I cover other aspects on which safety depen s, suc as 111sta lation and maintenance procedures.
It is therefore not uncommon that users who well aware fth xplosion hazards in their plant use electncal apparao ee f" I tus made by reliable and competent Wit lOut a formal certificate. This can happen 111 partIcular for new . s (fol' w'hich the certification procedure has not yet verSIOn· . been finalised) or for special apparatus of \vhich the small uantities required make it not reasonably practicable to them to the usually time-consuming and expensive certification procedures.
Based on the general consideration on hazard conditions and types of protection as described aboye, a rational selec tion procedure can be summalised as follows:
Step 1: Study the area classifiration drawing and locale the electrical apparatus as far as possible in a non hazardous area, e.g. a switch house or control room
The Hazards Type of Protection
Internal Release Area Symbol (Note I)
Normal Abnormal Classification d e h i i m n 0 p q r s a b
Zone :2 A A A A A A A A A A A
None None Zone I A A A A A A A A A See Zone 0 A A table
Zone :2 :2 A A A A A A :2 A
None Yes Zone I :2 A A A A A A Zone 0 A A
Yes (Note :2) Zone :2, I or 0 A A
Legend: A = adequate -= not adequate :2 = adequate if the internal components or circuits are not ignition-capable in normal operation, or have type of protection e, h, ia, ib, m or n.
!\iotes: I) Types of protection h and m are only adequate if the internal release does not occur inside components with this type of protection. :2) In this case the release is not of importance because other hazards take priority.
The Hazards Pressurisation Pressurisation Pressuirsation and with with Dilution
Internal Release Area Air Inert Gas with Classification Air
Normal Abnormal Alarm Switch off Alarm Switch off Alarm Switch off Zone :2 None None Zone I Zone 0
Restricted Zone :2 None Zone I Zone :2 Unrestricted Zone I
Restricted
Restricted Zone:2 or I Unrestricted Zone L or I l 'nrestricted Note L Zone:2 or I Note L Nott, L Zone 0
Fur legend alld Notes, see Table I
Step 2: The majority of the remaining apparatus will probably be located in a Zone '2 hazardous area. In this case attention should first of all be paid to the possibility of using Ilormal Industrial apparatus, provided that it is not ignition-capable in normal operations.
Step 3: Where step '2 does not apply, an adequate type of protP( IIOIl slwllld be selected from Tables I and '1. Among the variOllS p()ssibilities given in these tables, preference should 1)(' gi vpn to those cases which are just adequate for tl](' partl( IIlar hazard. hut not adequatE' for a more serious h,IZ;' rr/
A A A A A A :2 A :2 A :2 A :2 :2 A A A A :2 :2 :2 A :2 A :2 :2 A A :2 :2 :2 :2 :2 A :2 :2 A A L A A A :2 :2 A A
Step 4: Establish the appropriate temperature class for the apparatus and the appropriate gas group when types of protection "flameproof enclosure" or "intIinsic safety" has been selected.
Step 5: Determine the commercial availability of electrical apparatus with selected type of protection, proper temperature class and (where necessary) proper gas group. If unsUCcessful. select apparatus for a more onerous hazard.
Step 6: Where several possibilities remain, compare equipment costs, operating costs etc., and make a final selectIOn.
Type (BRD)
United Kingdom United of International Europe Netherlands I) 3) France States Protection IEC CENE- 1) :2) 1) of LEC DIN-EN VDE New Old America 0170/0171 1)
General EN NEN-EN
NF BS 5501 Requirements 79-0 50014 50014 SOOl4 Teil I C :23.514 part]
BS :2:2ll; d EN NEN-EN NF BS 550] BS UL-674B 7!J-I SOOIH SOOIH SOOIH Teil 5 C :23.5IH part .5 part 2 UL-(ilIH e EN NEN-EN
NF BS 5501 BS 46H3 79-7 50019 50019 50019 Teil 6 C 23.51l1 part (j part 4 h NEN 4) :H:25 i EN NEN-EN
NF BS 5501 BS 1259; UL-lII3 7!J-!1 500:20 500:20 500:20 Teil 7 C 23.:250 part 7 BASEEFA NFPA 493 SFA 301:2 (79-3) m 4) 5)
BS 46H3 n NEN 5) 3125 part ;) 0 EN NEN-EN
NF BS 5501 BASEEFA 7lHi 50015 SOO!5 50015 Teil :2 C 23.515 part :2 SFA 3013 P En NEN-EN
NF BS 5501 NFPA 4lHi 7!J-:2 SOOI(i 50016 5001(i Teil 3 C :23.S!(j part 3 q En NEN-EN
NF BS SSOI 7l1-5 50017 SOOl7 50017 Teil4 C :23.517 part 4 r 5) S 4)
Notes: I) Th d d ese national standards are identical to the European stan ar s. , d d 2) 1'1 f t f n not yet covered 111 the European stan ar s. le new standard NEN-312S (llJHO) covers only the two types 0 pro ec JO • 'cl) I G . I DIN t dard and as a \J DE regulatIOn. , n ennany the publications carry two numbers: as a natlOna s an 4) Under consideration. 5) In advanced course of preparation.
Figure 7' El t' I ec nca apparatus with tw internal release.
Figure 2: f;/ectrical apparatus u.'ith possible ahlZormlll reimsI',
Note: = Explosive atmosphere
Figure 3: Recognized types ofprotection.
Nottinghamshire CC Trading Standards took the following prosecutions against the National Coal Board at Worksop Magistrates Court on :2Hth March. The N.C.B. pleaded guilty on all charges and were fined a total of £2,650.00 plus ,[(is costs.
I. On the 7th September 198:2 at the Shireoaks Colliery, did keep explosive in an unauthonsed place contrary to Section S and Section 30 of the Explosives Acts I and 19:2:1 as amended by the Acts 1 and 19:23 etc (Repeals and ModifICatIOns) Regulations 1974 and the Explosives Act I and 1<):2 'j (R d'f' . ) , "etc epeals and Mo I Icatwns Amendment Regulations 1974.
:2. (N)n 7 th Septem bel' I at the Shireoaks Colliery, ottlI1gha msh' d'd b I . . Ire, I reach the general rules re atmg to premises re . ,t d f . ' d ' gls ere or the keeplI1g of mlxe explosives prescribed by Order in Council Number Hi as amended by Order in Council Number HiB in that the quantity of I' , '·b. exp OSlve was II1 excess of that pres(n ed contrary to Section :n and Section 39 of the Exd d ( b e) , , Lv as amen e etc as a ov .
L ()n 7th September 1<)0<). t th Sh' k C 11' N t- ' h h ' OL a e Ireoa s 0 lery, 0 LJ ng ams re did b. ' reach the general rules relatIDg to pH·ml.ses registered for the keeping of mixed explosives f1res( 11 bed by ()rder 1'1 C' '1 NI" h t the 1 (JuncI urn )er I h In t a' I I'glsferednremiseV\'as ·t I d 's ' r no c ose so as to prevent t 1/1'1 er" ( 11 III I al y to Section :2:2 and Section of the Ex plllSI \ ,-, \(;, I and I ():2:1 as amended(as above).
4. On 7th September 1982 at the Shireoaks Colliery, Nottinghamshire, did breach the general rules relating to premises registered for the keeping of mixed explosi ves in that the registered premise was not exclusively appropriated to keeping explosive contrary to Section 22 and Section 39 of the Explosives Acts 1875 and 19:23 as amended etc (as above).
5. On 13th September 1982 at Steetley Colliery, Nottinghamshire, did keep explosive in an unauthorised place contrary to Section 5 and Section 39 of the Explosive Acts 1875 and I!J23 as amended by the Explosives Acts 1875 and 19:23 etc (as above).
The offences came to light during routine inspection visits with police crime prevention officers. The visit to Shireoaks was on the Tuesday after the pit had closed for a weeks holiday the previous Friday.
There are three "South Yorkshire" area pits in Nottinghamshire. Shireoaks and Steetley are two, the third, MantoO, was cautioned in September 1981 for overstocking aod leaving the cupboards unlocked!
During the interview at Area Headquarters, Senior Safety staff expressed surprise that Count y Council Officers could enforce Explosives Legislation.
The offences:I. "unauthorised storage".
" al total
This relates to nine pouches contalI1mg a nom1l1 of 2(iA pounds of explosive on the floor by the maID en
trance to the distribution store and a further eight pouches containing 39.24 pounds on a bench behind the counter. These had apparently been found underground after the men had finished for the holiday. There were no instructions for records of issue and return of pouches to be checked, or for reporting pouches missing.
Fine £750.
2. "excess quantity".
One of the three cup boards contained a nominal total of 113.3 pounds. Maximum quantity for premises registered Mode A is 60 pounds.
Fine £ 1,000.
3. "not closed so as to prevent access thereto".
The cabinet was unlocked.
Fine £250.
4. "not exclusively appropriated to keeping explosive".
This was the unlocked cabinet of 3. above which, as well as a 25 kg box of Penobel, contained tea, a mug and a bottle of non-brewed condiment (very similar to vinegar).
Fine £400.
5. "unauthorised storage".
Eighteen pouches containing a total of 89.29 pounds of Penobel had been made up and stacked by the open door of the premises ready for issue. The cupboards had then been refilled.
Fine £250.
Following an explosion at a service station, it discovered that the cause was attributed to a failure by fItters to effectively c3;P a stand-pipe following installation No cap was available for sealing the stand-pipe from .whIch a s.ubmersible pumping unit had been removed. Dunng a defrom a petrol tanker, vapour vented out of the standthrough electrical ducting which had not been sealed dunng the alterations, into a kiosk housing the petrol console. An explosion occurred and blew out the side of the bUilding, causing an injury to the petrol attendant. The flow of petrol to the underground tank was immediatel Yceased, the hose-pipe disconnected and the tanker driven away. It was indeed fortunate that no more damage or injury resulted.
charges were also suggested to the procurator Fiscal agamst the licensee and a major oil company who were the o.wners, the latter, following an appeal to the Court of Sesagainst the charge, no proceedings emanated against eIther.
At Edinburgh Sheriff Court on December 198:2 contraof Health & Safety at Work etc. Act 1974 Ss. 4(:2) & 3.3( 1) Pump Maintenance Ltd. were fined .£400.
Senior Fire officers wasting valuable time chasing licence reminders were supported in Magistrates Courts in the West Yorkshire area where the following six prosecutions were taken for storing petroleum without a licence.
1. For keeping 23 gallons of petroleum spirit in unmarked containers, without proper storage facilities and without a licence:
20th October 1982
MrD Lee Oakleigh Road Bradford
Fined £100 and £27 costs at Bradford Magistrates Court.
2. For failing to renew petroleum licences for 1982: a 29 September 1982 MrB Cowan Briggella Garage Bradford b 20 October 1982 Mr J A Clayton Reva Syke Road Bradford c 14 November 1982 Spencer Motor Services (Todmorden) Ltd d 10 November 1982 Mr R Fleming Mr H Fleming Bog Green Lane Huddersfield e 30 November 1982 Mr B Tonge Mr P A Malins Bradford Road Batley
Fined £32 and £57 costs at Bradford Magistrates Court.
Fined £25 and £27 costs at Bradford Magistrates Court.
Fined £100 and £30 costs at Todmorden Magistrates Court.
Fined £ 100 each and £28.50 each costs at Huddersfield Magistrates Court.
Fined £15 each and £28.50 each costs at Batley Magistrates Court.
When petrol station manager Ronald Auty an elec. I Its he closed for the night, he could httle have tnca p ug ou a Id I realised the devastating effect It wou lave.
For it sparked a big explosion which blew out front window of the filling station kiosk and caused the ceIhng to collapse
The blast happened on :2 la,st. year and on T d M Au ty of 13 Shire Green, FaIrstead Estate ues ay r, ' Lynn, found himself before Lynn maglstrates for offences relating to the incident.
He admitted failing to keep a constant watch while petrol from a tanker was delivered to storage tanks at the Marga retta filling station on the A 17 at Clenchwarton.
And he also admitted failing to ensure that no petrol overflowed from the storage tanks, or escaped at the filling point of the tanks.
He was fined £30 on each of these contraventions of petrol delivery regulations and was ordered to pay £30 towards prosecution costs.
Mr lan Crookall, prosecuting on behalf of the county's chief fire officer, said Lynn firemen found there had been a severe explosion in the office building at the filling station.
The front window had been blown out in the blast and the plasterboard ceiling had collapsed. It was clear that this happened when Mr Auty was closing up and had removed an electrical plug from a socket, he said.
Further investigations revealed that there had been a delivery of petrol at about 5 pm that day and the storage tanks had been overfilled.
Some of the excess had gone through breather pipes beside the kiosk and petrol had got onto the roof and had percolated between the roof and the plasterboard ceiling.
An expensive way to check a faulty
Whilst a car's engine was being run in a mews garage to check for possible leaks from the exhaust system, a leaking plastic fuel line came into contact with the exhaust pipe. Petrol was igni ted and in the ensuing fire the car was destroyed and the walls and ceiling of the garage were damaged. The Brigade was called and extinguished the fire.
The purchase of petroleum spirit can lead to many shocks which are not only confined to the price charged. Some 3 weeks before Christmas a motor cyclist served himself wi th petrol at a self-service site. Once he had filled his motorcycle he went to pay for the petrol. Whilst in the kiosk he and the cashier were somewhat surprised to see the bike catch fire. The cashier promptl y tackled the fire. It seems that the motorcylist had slightly overfilled his bike and the vapour crept downwards off the tank and was igni ted by the heat of the engine.
A car was in collision with a road tanker and 500 litres of petrol leaked onto the forecourt. The Brigade washed down the surplus petrol and blanketed the forecourt with foam. The Company failed to notify Petroleum Section and a cautionary letter has been sent.
A London Borough finall y decided to report a smell of petrol after some S months. The smell was more apparent at week-ends and was prevalent at two houses which were a little way from an installation. The houses nearest the installation reported no smell. Pressure testing was carried out on all storage tanks and suction lines, and the site drainage and interceptor were cleaned. The pump bases were also recuncreted. Two faul t y suction lines were discovered and were replaced, thus making the installation satisfactory. As a tailpiece to this story, rumours abound in the area that a IJlowrcyclisl may have been partially responSible for the (,I rol snwlls as he allowed petrol to enter the drains. It f), lIS or so il is rumoured, that the local residents have /./" ., , It' him aware' of t1w pmblems he may have caused. iI
A spark as Mr Auty removed the plug had ignited the petrol vapour, Mr Crookall explained.
The defendant had not kept a watch, as he was required to do under the regulations, while the tanks were being filled. He had been serving customers at the garage the prosecu tor pointed out.
Mr Auty, a married man with four children, told the court that he had lost his job after the incident as the firm had closed the garage and gone into liquidation.
He said he had been in charge of the filling station for about two years but had not been aware of the petrol delivery regulations.
Magistrates chairman, Mr R. J. Russell, said the fines imposed might appear to be low, but the bench had taken into account the fact that Mr Auty had lost his job and the particular circumstances of the incident.
A lady driver in an automatic car drove on to the forecourt of a filling station intending to buy petrol. Unfortunately she hit the kerb of a pump island, panicked and mistook the car's accelerator for the brake pedal. This caused the car to shoot forward and hit the adjacent pump island. Two pumps were completely demolished and thrown across the forecourt. Thankfully, no igni tion took place and the car finished across the two fractured suction lines. No doubt the lady had a little explaining to do to her spouse and, perhaps, the insurance company.
The occupier of premises next to a filling station had been warned by the licensee about the dangers of lighting bonfires. The warnings were ignored by the Occupier and consequentl y a bonfire got out of control and spread to his garden shed, a neighbour'S garden shed and to the fence on the site boundary. The facade of the sales building on the site was next to suffer and began mel ting. The fire then spread to the above ground kerosene tanks.
Thankfully, the Brigade arri:ed the situation got any worse, although the bonfIre enthUSiast received burns to his arms, It is interesting to note that it is proposed to provide an LPG tank on another boundary wall of the site, but, hopefully, by this time the enthusiast, like Guy Fawkes in 1605, should have learnt the perils of playing with fire!
A motor vehicle repairer, replacing fractured fuel pipe, escaped with superficial burns to his right hand and forearm following an explosion and fire under the vehicle on which he was working. It seems that he replaced the broken fuel line with a length of plastic pipe, securing the ends withjubilee clips, but the end connected to the vehicle's fuel tank continued to leak. When he crawled under the vehicle to tighten the connection, petroleum spirit leaked onto an unshielded lead lamp bulb which exploded and ignited the petrol. The occupier (the injured party) has been severely cautioned under the Petroleum Spirit (Motor V ehides ete.)
A fire occurred at a petrol filling station and vehicle repair
work shop. At the time of the fire, which evidently was caused by vapour emi tting from the ventilation pipes of an underground storage tank coming into contact with a halogen lamp, a road tanker was commencing delivery. 20 foot flames were noted but the driver closed the tanker's valves an? thus prevented an extremely serious incident. The Bngade extinguished the fire. The floodlights (there are two) were installed for possible late deliveries by road tankers but more generall y for night security. They had been left on during the day as visibility was poor owing to fog. The fo.g caused the vapour to remain in the yard. The floodlights WIll be removed to a position away from the vents and in the meantime will be switched off during deliveries.
A customer pulled up to a pump to serve himself with petrol. Because the stock in the tanks feeding that particular pump was a bit low, he was asked over the PA system to use another pump. This he did, but, unfortunatel y when driving offhe forgot that the hose nozzle was still in his car tank. The result was that the pump was dragged off its fixings. No other major damage was incurred and the petroleum spirit spillage was confined to the draining out from the pump, which was hosed down by staff.
The G.L.e. obtained a successful prosecution against a careless employee of a licensee. During a delivery of petroleum spirit from a road tanker into a storage tank, approximatel y 2 gallons of spirit spilled from the ventilating pipe of the tank. The spillage occurred because the tank had been overfilled. The Magistrates agreed that offences had been committed contrary to paragraphs 6(a) and 8 of No. 16 of the Petroleum Spirit (Conveyance by Road) Regulations 1D57. The defendant was fined £50 on each information with .£25 costs.
Following the introduction of the Dangerous Substances (Conveyance by Road in Road Tankers and Tank Containers) Regulations, the Petroleum Inspectors may have thought that tank wagon incidents, now the responsibility of the Police, would be a thing of the past. However, the London Fire Brigade, sensibly still seek the advice of the experts when faced with an incident particularly when a police presence is not quickly forthcoming as the following tale relates.
A petrol tanker on approaching a filling station to off load, burst a tyre as the cab of the vehicle was on the crossover turning left into the filling station. The tanker driver immediately stopped the vehicle and found that the tanker section, by virtue of the deflated tyre and the camber of the r?ad, was listing. Having taken a wide sweep to enterthefilhng station, in its stationary position the tanker was diagonally across the road, completely blocking one side of the carriageway.
The driver immediately requested assistance from the Police, asking them to call the Brigade at the same time. A Brigade appliance turned up within 5 minutes and also s.ummoned the assistance of a Petroleum Inspector. The Pohce took rather longer to anive.
bulk of the spirit was off-loaded using extended hoses WIth the tanker in the position where it had stopped. This completed, the tanker was driven onto the forecourt where the wheel was replaced. No spirit was spilled and the incident was concluded without injury or seriolls damage.
Minutes of the Yorkshire and Humberside Branch of the Association for Petroleum and Explosives Administration held on the 23rd September 1982 at the Red Hart, Blyth, Nottinghamshire.
The Chairman Mr. R.J. Smith extended a warm welcome to the 36 members and visitors present. With a special welcome being extended to Mr. e.G. Davies and Mr. 0 Tindale of the LPG Department of Shell UK Oil and also to Or. P.G. Kirk and Mr. Sj. Bates of the Heal th and Safety Executive.
The minutes of the Annual General Meeting held on the 22nd April 1982 were read and approved as a true record.
Proposed B. Marsh
Seconded R.D.T. Charlesworth
There were no matters arising.
Apologies were received from 4 members.
The treasurer reported that the balance in the Current Accounts stood at £45.85p.
Report of the Council Meeting held on the 13th September 1982
The secretary reported that there was no proposal to increase the member subscriptions to the national association, but discretion had been given to the editor of The Bulletin regarding advertising costs.
The programme and ancillary details regarding the forthcoming seminar were discussed. The topics for the seminar were basically LPG and concrete paving.
It was proposed at the meeting that a working party be set up to look into the current positio.n regaI:ding LPG storage associated with petroleum and III partIcular as to what licence conditions should be recommended.
A short talk was given by Dr. P.G. Kirk regarding the storage of LPG on petroleum licenced premises. The talk was most infonnative and very topical, resulting in a considerable amount of discussion.
This was left in the hands of the Secretary.
The business meeting concl uded at I :2:-1-0 pm
The afternoon session commenced at 1:-Li pm \\hen Cl talk illustrated with a film \\as giwn Mr l'.C. Davies and Mr D. Tindale of Shell UK ()il un the use uf l.Pl; as an aut01l111 tive fuel. Mr. Bre\·eton g-ave UIl behalf of the Il1t'1l11wrs a vote of thanks.
Da vis Fill Safe Unit being po sitioned on the ri m of a ha tch.
T h e Dav is Fill Sa fe uni t p r ev e n ts spill age when loadin g roa d ta nk er s. It is prin c ipall y d esig n ed for use on p e trol eu m t e rmi na ls but has ap p licat io ns in a n y indu str y wh er e d a n g e ro u s vo lat il e liquid s a r e b ein g carried b y road
T h e Fill Safe unit is in sta ll e d on th e te rm inal gantry a nd m o u nt e d o n th e loadin g a nn s whi c h it controls . T h e uni t is IIl s ta lle d so th at it ca n o nl y b e po siti o n ed o n the rim o f th e hatc h of th e co mp a rtm e nt to be fill ed w h e n th e arm is in th e ' a rm d ow n' pos iti o n.
T h e Fill Safe unit is d e sig n e d to fit ove r the rim of th e ta nk h a tc h a nd it co nt a in s a mi cro switc h whi c h is a cti vat ed o nl y wh e n th e bO d y of th e uni t is co rr ec tl y p osi ti o ned o n the rim a nd sec ur e ly h e ld in po siti o n by sp rin g o pera t e d ho lding cl a mp s U n til th e sw itc h ha s b ee n opera t e d it is imposs ibl e fo r the lo a di ng pump to o p e rate .
Fro m t h e ma in bo d y o f th e uni t, a shor t t ub e p ro trud e s in to t h e tank e r co mp a rtm e n t. W it hin t he t ub e is co nt a in ed a fl oa t sw itc h whi c h is o nl y a c ti va t e d w h e n t h e p rod uc t W I t h ll1 th e ta n k excee d s th e a ll o we d level.
T h e Da vis Fi ll Safe u ni t is co nn ec t e d to e ith er a n in trin s icall y Sa fe R e la y u ni t m o u n te d in t h e safe a r ea, o r a F/ame pru ofl l ntrin isc a ll y S afe R e la y un it m o un te d on t h e ga n (r v \IV h en t h e flo a t sw ilc h is ac t iva t e d a r e la y op e rat es lA /111 h c <Ill tro ls t h e pump , t h e p ump is stop p ed an d a so le Il(Jld () p eraled va lve ca n be close d so ha lti ng pro du c t fl ow.
Ve hicl e Ea rthin g E qUipm e nt is de sig n ed to e n sure t h a t, whe n fu el ta nk e rs a re loadin g , o r unl o adin g, th e v e hicl e h as bee n effecti ve ly eart h ed to p reve nt th e ri sk of exp los io n resui tin g from th e pri o r build up of static el ec tri c i t y Th e syst em IIlCOrporate s int erl oc ks into t h e pump m o to r c i rc ui t s to ensure that fuel ca nn o t b e load e d o r unload e d, pri o r to th e ve,hlcl e bein g prop erl y ea rth ed. The system c on sist s o f a Ij/' (I 2.5 mm) brass pin m o unt ed o n the vehicle and a ng le d to ensure th a t, in th e event o f a ta nk e r being driv e n away b e fo r e dI sconn ec tion, the soc k e t pull s off w ithout d a m aging itself or the sys te m
A h eavy dut y soc ke t, whi c h is d es igne d to fit o n to t h e pi n, is co nn ect ed by m ea n s of a h eli co il ca ble to Intri nsicall y Sa fe R elays, whi ch a re co nn ecte d into th e pump co nt ro l c irc uit. When the syst em is co rrec tly earthed, th e r e lays will cl ose a nd allow the pum p to o p era t e
co mplet e n ew ra nge of LS r elay transfo rm er unit s Co IU pn ses power suppl y units, re lay units and co mb in e d p ower supp ly r ela y units, a ll d es ig ned to m e et th e r e quire m e nts of BS55 0l Pa r t 7 (Ce n elec st a nd a rd E N 500 20) w ith ve r sio ns ava Ilable fo r G roup II A , I1 Ba nd II C appli catio n s.
T he d es ig n co nce pt has bee n to pro vid e a m o dul a r ra nge of equipm ent, tha t ca n be inte rco nn ec ted to e nabl e con tro l an d m onit o rin g sys tem s for use in many diffe re nt appli ca ti o ns
Un its a re ava il a bl e in two sizes of e ncl os u re b ot h d e sig n ed to m eet IEC r egu la ti on IP (-is with ve rsio ns ava il a bl e wit h in trins ica ll y safe o u tputs h a v ing a fac to r o f safe t y of 1 S an d 3, t he latte r ve rsion ena bli ng th e use of sp aI' ki ng co n tac t s ill Zo ne 0 areas to ini ti a te t h e re la ys.
The flameproof Monitoring System has the capacity to monitor up to six intrinsically safe transducer circuits. The transducers are monitored by electronic circuits. When a transducer changes state the electronic circuit causes its associated relay to energise, or de-energise, depending on the way the circuit is set up.
Two types of electronic circuit are available, depending on the type of transducer being monitored. A fail safe circuit, comprising a thristor circui t, when transducer contacts connected to the fail safe circuit open, orin the event of an open or short circuit fault in the transducer cables, the associated relay will de-energise. The other type of electronic circuit being a function circuit, which can be connected to perform a wide variety of different functions such as Temperature Detector and Time Delay.
The LS. Monitoring System is certified to BS 5501 Part 7 (Cenelec standard EN 50 020) designed for wall mounting in the safe area.
is a six-channel transducer monitoring system and verSIons are available certified intrinsically safe for either Group 11A or Group lIB applications.
Each of the six channels can be fi tted with ei ther fail safe or function circuits to monitor either digital or analogue A 1S V a.c. intrinsicalI y-safe supply is also provided, for connection to any appropriately-certified apparatus.
The LM.S. is adaptable to suit many applications, including and loading arm monitoring and control, Marine Loadlllg arm control, Refrigeration plant monitoring and control, Road tanker earthing and overfill protection systems and Conveyor control.
The Intrinsically Safe Digital Multimeterprovides installation and maintenance engineers with a conventional electronic multimeter which can be used with safety in explosive atmospheres in mines and petrochemical plants, in measuring LS. circuits.
The new instrument is battery powered and portable, weighing only 2 kg, when complete with every-ready leather case, batteries and test leads. Resolution is I millivolt or 1 microamp on the most sensitive d.c. ranges and there are also a.c. and resistance ranges plus a "diode check" feature, there is automatic indication of "over-range" inputs.
The Davis multimeter is certified to the latest British and Cenelec Standards for Group 11 B applications. The external test circuit is certified EEx ia and may therefore be connected to LS. circuits in Zone 0 areas.
The availability of this instrument is expected to have far reaching effects on the development and application of complex electronic systems in hazardous environments. Conventional installation and maintenance procedures will now be possible in areas where previously they would have been prohibited.
Also available from Davis Derby is a brochure entitled "Standards Applied to Electrical Equipment in Hazardous Atmospheres". This booklet explains the protection concepts applied to electrical equipment used in hazardous atmospheres.
For a copy of this booklet or for more information Contact:John Davis & Son (Derby) Ltd Alfreton Road Derby DE2 4AB Telephone: 0332 41671
A device to attach to the rim of a road tanker hatch during filling operations. The device is permanently attached to the loading arm.
A range of intrinsically safe relays and power supply units.
An intrinsically safe six channel transducer monitoring system. Each each input is fail-safe and electronic timers, temperature detectors and warning flashers may be fitted if required.
A flameproof version of the IMS 1.
Prevention of Cargo overspill. The device may be used in Zone 0 areas.
This range of products are suitable for loading arm position monitoring pump con trol and in terlock systems. They may also be used in conjunction with the Fill-Safe device to provide overspill protection for road tankers coupled with earthing protection to ensure elimination of static electricity.
A hand held portable test Circuil testing in hazardous 1 I 8 inSlnlll1f'1l1 for 1l1('aSllrpment areas. of voltagp ('lIITf'nl resislam'p & diod(> tesling.
Davis of Derby, manufacturers of electrical safety equip m e nt for harzardous atmosph e r es, announce a new range of high-output ai r dliven lamps.
The most effective way of illuminating a working area is the obvi o us one, electric light, but if explosiv e or flammable gases are in th e area, then the presence of electricity could b e ha zardous b eca us e a ny sparking which might tak e place could cause a n explosion or fire
In th e Solaris lamps, danger is prevented by using co m pres sed air to drive a turbine co upled to a perm a nent mag net alternator which s uppli es a merc ury vapour bulb Th e unit is d es igned so that all of the elec trical circuitry is contained within an enclosure which is filled with the exhaust air from the turbin e, electricity being mad e av ail able only when this condition is achieved. Any explosive or flammable gases within the area of th e lamp are thus preve nted from reac hing th e electrical circuits. Beca use th e lamp is fed from an air line and no t via elec trical ca bl es, the source of pow er is not hazardou s.
The n ew Sol ar is lamp s, with bulbs rat ed a t 125W, ha ve a very high li g ht output (58 00 lum e ns) Two versions are available giving a c hoic e of bulb fl ood light , or spot lig ht.
The lamps are design ed to meet BS .1.10 I : Part 3, EEx P (CENELEC standard EN SO 0 16) a nd are certi fi e d b y BASEEFA (BJitish Approvals Serv ice for E lect ri cal Equip m e nt in Atmosp h eres) fo r lI se in hazardous at m osph e res The certificate numb e r is Ex H2 1209X.
The eMS 2000 gauging system is not a 'mechanical dipstick' it is an effective stock control and management system.
eMS gauges are based on a dvanc e d technology pion ee red by Smiths Industries. for accurately measuring fu e l in some of the world s most a dvan ced aircraft. It is this t ec hnology that th e e MS 2000 brings to today 's fore c ourts.
The unique eMS increm e ntal fill method o f calibra tion . involving the use of specially develop e d equipment and sophisticated co mputer programm es ensures that the eMS 2000 system is so accurate that it can monitor the perform a nce of pumps and. for th e first time provide effective fore c ourt man agement checking on what is delive red into the t a nk s and what goes out of th e m.
That's why it's in daily use with m ajor oil companies distributors and ind e p e ndent retail e rs throughout the UK.
The eMS 2000 puts man age ment in c ontrol of its liquid assets
Please address any communication to the undersigned.
Honorary Secretary Eric Brown
Cambridgeshire County Council Hinchingbroke Cottage Brampton Road, Huntingdon Cambs. 0480 57344
I wish to apply for Membership of the above Association and I enclose the sum of £10.00 being the Annual subscription.
Name: Address: ........................................................................................................................................................
Authority or Company: The completed form should be returned to the secretary with the fee.
SubSCriptions: Membership £10 per annum.
Membership is open to those persons who are authorised Officers within the meaning of the Petroleum or Explosives Acts, or is open to any body, company or person being otherwise concerned with the handling, storage or transport of substances covered by this legislation.
Technical progress within the industry promoted by Oil companies and large industrial groups durin Year' h . L I A h th Ad ". g lecent s as Increased difficulties encountered by oca ut ontles III e mllllstratlOn of Petroleum ExplOSives Act. and
The ASSOCiation was formed in 19SH and its objects are to further:-
I) The advancement of scientific, technical and legal knowledge in this field.
:2) To supply and interchange information.
i) T () try and promote uniformity in administration.
i) To promote the formation of branches.
-;) co-operate with other bodies having similar objects, or who are otherwise connected with Petroleum or f legislation.
Eltra Gas offer a complete service for industrial and domestic fuel supplies of Liquified Petroleum Gas
Using the latest computer technology, Tank Master measures fuel oil, chemicals, milk, drinks in fact any liquid in any shape of tank at the touch of a button with the added option of Specific Gravity Compensation.
• No electrics in tank area
• Any number of tanks may be measured on one unit
• High level, low level, fail safe, and air fail alarms built into system
• Alarms can be set to warn if S.G. of product goes outside pre-programmed limits
• Alarm status of all tanks displayed on demand
• Delivery capacity of each tank can be displayed on demand
• Additional product loss alarm available to activate if contents of tanks drop more than a pre set percentage
• Facility to back calibrate the gauge against petrol pump totalisors for extreme accuracy
• Integral ticket printer
• Video monitor can either show details of a single tank or groups of tanks on system
• Printer will give details of one tank or full shift totals if required
• Simple operator controls
• End of shift totals on printer will show quantity gone from tanks since last shift
• Time and' date facility built into system
• Full facilities for Remote Data collection or for interface with modern petroleum self service units
• Accurate volume measurement of any liquid product in any shape or size of tank