Journal of the Association for Petroleum and Explosives Administration
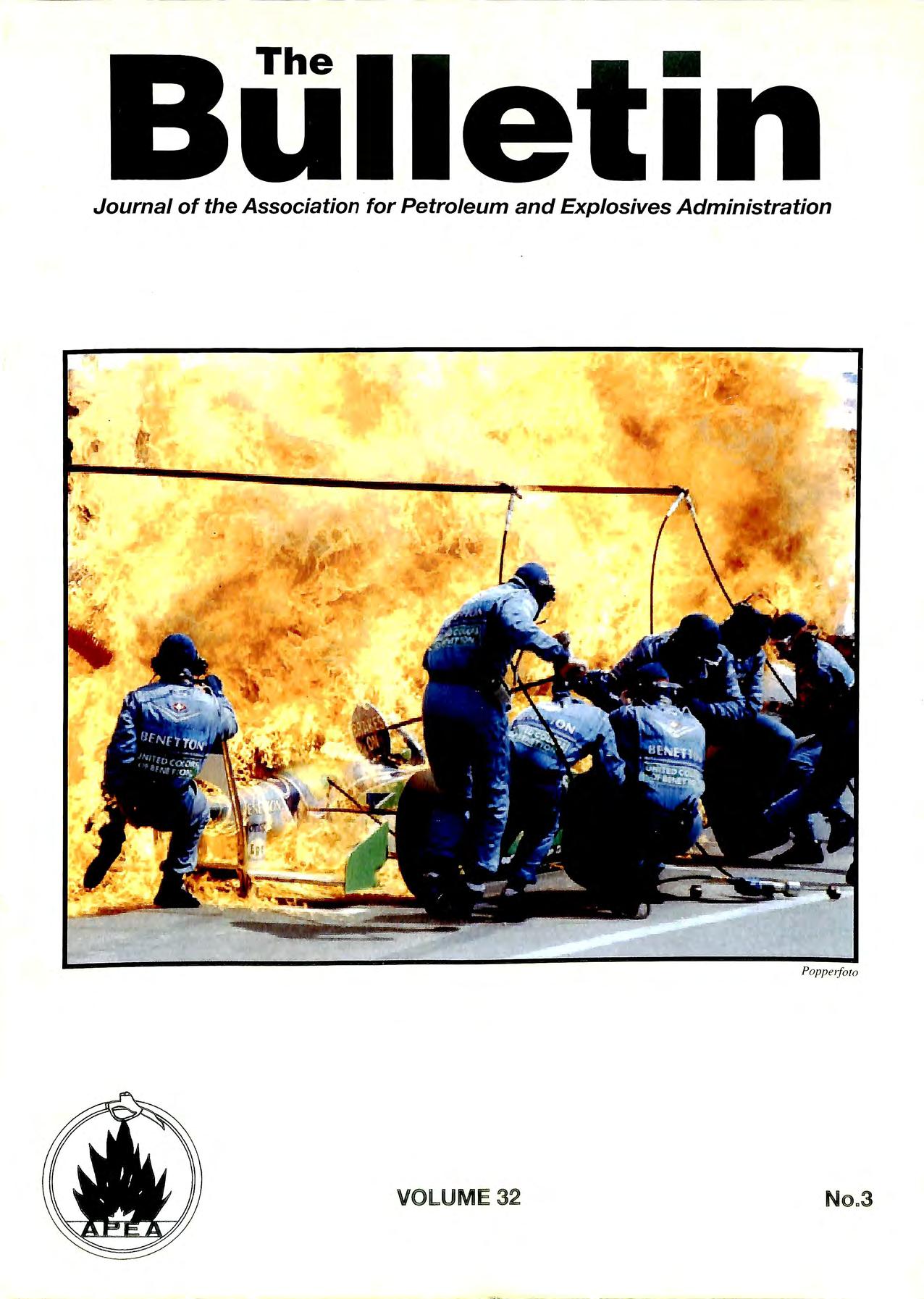
If you're rebuilding your station, you're probably in a rush for th e pip e to be in the ground and tested so you can get on with your real busin ess of selling fuel.
But don't forget to take a close look at your choice of piping materials.
Here are three things to think about when you choose between 'hard' piping like Dualo y®3000/L and the 'soft' system that' s just come on the market.
For starters, there 's fluid h ammer. Topping off can cause pressure spikes of 20 atm or more. Soft systems use thermopl as tic hoses in the primary with safety factors of 3: 1 or less. That's not a lot of margin for failure. With Dualoy 3000/L rigid-wall fiberglass pipe from Ameron you get a sa fety factor of over 10:1 Second, there's UL-listing. Soft sys tem containment doe sn 't have it. Wouldn't yo u wa nt the assurance of a
Inc. @ third party like UL that the containment can prevent soil contamination in case of a leak? You have that assurance with Dualoy 3000/L.
:/ )
,_
Ameron fiberglass pipe : the proven way to move fuels fiberglass Pipe Division
1A Christchurch Road Ashford, Kent TN23 iXB
Fax: 0233 613 884 ' l ' j
forecourt safer.
has a network ofdistributors throughout Eur_ope . Each has been selected for its high standard ofexpertise and knowledge ofthe industry.
PETROL FILLING STATIONS:
For over 30 years PERMEX has led the field in fluids handling for the transport industry Now PERMEX moves even further ahead with the introduction of:
Fuelfax the revolutionary touch-screen fuel monitoring system with read-write keys .. . ... and "Oil Watch" the automatic oil dispensing system that will boost profits in the workshop.
These new systems are designed for easy operation while providing management with data that's vital to efficiency, economy and profit!
Fuelfax, "Oil Watch" and a comprehensive range of lubrication Equipment set the standards for fluids handling for transport Get the PERMEX facts TODAY!
This is wha t 0.1 % fu el loss represents to a typical forecourt op erator Most sites are los in g many more times this amo unt each year!
Pe t roVen d 's SiteSentinel forecourt monitoring sys tem g uards against wetstock loss, leaks, theft , short deliveries to mention just a fe w!
It tells yo u through accurate printouts and easy to understand graphical a n a lysis, not only how much fuel you are losing on a day by day basis but indicates where in the system the loss is.
ISSN 0263 4597
are a number of papers on the subject of tank testmg m this issue, and it is clear that some uncertainty exists in the eyes of the customer, the local authority, and the competition over which tests are acceptable and who is con:petent to carry out evaluations on precision tank testing equipment.
The UK benefited from the work carried out in the US, the first system imported from the US some 6 years ago had ?-1ready received evaluations from US test houses. At first expressed concern that there would not be enough but as time has progressed this has altered. Inevitably there is now a lot of choice, with numerous systems and running them, most with US test evaluations and providing lots of competition. In addition there are some home grown systems from the UK and I am certainly aware of three, but where do they go for their evaluation?
It is. not fair that they should have to go to the US for evaluation, but where else can they go? There are a number of Universities and Test Houses who could perhaps carry
Opinions expressed in this Journal are not necessarily the views of the Association
out the work but none at present appear to have all the facilities that the US test houses have.
Home grown systems should be given the to prove themselves and it is hoped that through this _wm . a recognised test house in the UK emerges that will confidence to us all, encouragement to the not least a feeling of fair play from those already 111 t e business.
FRONT COVER
·d nt at the The front cover photo shows the refuellmg acct e 31 J I The Benetton German grand pnx m Hockenhe1m on u Y· fi the crew tnes to Ford and dnver Jos Verstappen 1s on ire as . · · · to dnver escape once the fuel ignites, fortunately the mJunes h d and crew were not serious. The new refuelling system da recently been introduced into formula one racing and ha a full risk assessment carried out.
As the Bulletin is prepared for publication, the UK Government has, following their de-recrulation initiative announced its intentions to review the whole of Petroleum (Consolidation) Act 1928, and all the regulations made under that Act. The proposals were announced in two documents, one governing fire safety, and another reviewincr all Health and Safety legislation have been published and comments are being sought on the proposals from both industry and local government.
All Health and Safety legislation issued prior to 1974 is to be reviewed and repealed. Their intentions are to introduce a new set of Flammable Liquids regulations which will cover petrol filling stations, it is likely that petroleum licensing will only remain where the public has access for public filling stations, it would appear that licensing will not be necessary at commercial installations keeping petrol, or farms etc. In addition the petroleum mixture stores would no longer be part of the responsibility of the petroleum licensing authorities. The new regulations would be unlikely to include car park licensing. The proposals are a radical change in the way flammable liquids have traditionally been controlled.
The APEA will be commenting on these documents in due course and be making the point that public safety at the filling station is not compromised by these proposals.
Total Oil has announced that it is to add perfume to its products in the future following a trial in France of fruit flavoured petrol which has apparently gone down well with the customers. One can imagine the advantages to the petroleum officer who on smelling a banana smell announces it must be Total unleaded!!
The Eastern branch of the APEA is holding a meeting on J3 September in Needham Market and the subject of the day will be HS(G)41 Absence and Implication. The event has been organised by branch secretary Barbara Jacketts and a number of speakers will giving presentations on the up to date thinking on the rev1s10n of HSG4 I, and the reasons for change with the Chairman of the Industry group laying out the programme for the future guidance which is to come from the group chaired by the APEA.
All members of the Association are welcome, should you wish to attend please contact Barbara Jacketts on for details.
A number of Oil companies are checking the leak detection fluid in the double skin steel tanks they have been installing for the past 4 years. It w_ould that differing standards of the liquid and the ratio of hqutd to water have been used and some of them are now proving ineffective. One major oil company has arranged to have all its tanks checked and the majority of the fluids will be replaced using the correct fluid. The ratio of 3: I is used by most companies but some have been using 9: I.
A_ eur?pean standard is in preparation covering the spec1ficat1on of the fluids to be used the ratio and also tests to be carried out which will ensure' that the fluids are still performing some 30 years after installation. It would seem that some of those used in the early days in the UK have not lasted 3 years!
The above case was heard at Launceston Magistrates Court on the 27th June, 1994, where a Director of the Company guilty to failing to comply with the contents of an improvement Notice issued on the I 7th January, 1994, which contained a directive to render four disused petroleum spirit tanks permanently safe.
The Magistrates awarded a fine of £1000 together with costs of £450 in favour of Cornwall County Fire Brigade.
As a train, comprising 20 tank cars each loaded with 75,000 litres of petrol, was passing through the ZurichAffolten station in Switzerland at about 0800 hours on the morning of March 8, 1994, the driver noticed a slackening of the brake pressure. Although he immediately activated the emergency brake, it was too late. Five of the tank wagons in the middle of the train jumped the tracks, rolled over and began leaking petrol. The fuel was ignited almost immediately and a massive blaze ensued.
The Zurich suburb of Affolten is heavily populated and it was necessary for the emergency services to aiTange for the evacuation of eight buildings, including a school and 120 residents from a nearby block of flats, without any delay. The intact wagons remaining on the rails were detached from the front and rear of the train and shunted to a safe place. Hoses were used to play water on the intact wagons while they were being detached.
A significant amount of the spilt and burning petrol leaked into the sewers and damaged nearby buildings while other structures and vehicles in the vicinity were scorched by the blazing tank cars. Although a heavy pall of smoke covered the area, miraculously, the extent of personal injury was limited to three people who were shaken by the blast effects of the tank cai·s as they initially caught fire. The I 00 fire-fighters were unable to extinguish the blaze until late afternoon and not before a further explosion took place. a development which delayed the return of the evacuees. Throughout the day police helicopters overflew the area. and officers used loudspeakers to warn people in the smTounding areas not to smoke and to explain why the electricity supply had been cut off.
A total of I .SOO.OOO litres of petrol were involved in this latest incident.
Two significant retail petrol innovations will be unveiled at the APEA Conference, which takes place on Tuesday, 27 September, 1994, at the Birmingham Metropole Hotel, National Exhibition Centre, Birmingham.
In a keynote address to delegates, Alain Dujean of Elf Oil UK will discuss the development of the portable service station. Already in use in Italy and France, the concept is poised for introduction to the UK. Such self-contained "pick up/put down" stations have many applications, including provision of refuelling facilities at one-off events and when a forecourt is closed for alterations.
A second glimpse into the near future will come from Cees Zaalberg of Netherlands-based SABER Europe, who will detail benefits for retailers and consumers in using an advanced electronic petrol pump nozzle. The nozzle, currently in use in the USA and some European markets, is ergonomically-designed, lightweight and offers vapour recovery facilities.
The 1994 APEA International Conference has the theme: "W together to protect the European Environment", and a senes of presentations will be featured which focus on key environmental issues, such as vapour recovery and underground technology.
of the APEA programme are scheduled to mclude:
• A Spanish view of European service station construction practices and regulations from Serge Olid of Texaco Petrolifera SA.
• With St I y d ii age. apour recovery regulations schedule Eor m September, Phil Lambert of Mobil _Oil urope w11! deliver a timely look at the practical of making new-site and retrofit vapour a ancmg systems work efficiently.
• Dyson, of UK-based Alan Dyson Ltd., will effective ways of installing tanks on g station forecourts and ensuring product temperature stability.
• A process th t . into an · . a converts an existing single-skm tank will be d preferable double-skin unit in a by Robotham of Prime Safe UK, a ion entitled: "New Tanks for Old".
The APEA inte · Conferenc · rnationa\ petrol . e is one of the major events in the attract around industry calendar and is expected to gates from around the world.
The Conference d
APEA members and cost is £48.50 (inc. VAT) for me. VAT) for non-members.
Staged alongside the C . .
The two day exh"b· . onfeience is the APEA Exhibition. Hotel on at the Birmingham Metropole from more th·m 8(), , and will feature displays ' companies.
Conference delegate b k" Dave Buckinll (t 1 h 00 mgs can be made by contacting .> '. e _e_p 0472 341344 ). Information on the Al I .A Lxh1h1t1on is avallable from Chris Knight (telephone l)l)!J,?4"14941
The publication of HS(G)41 "Petrol Filling Stations: Construction and Operation" in 1990 was aimed at encouraging consistency of standards, as applied by Petroleum Licensing Authorities (PIA), says a draft proposal under discussion by the HSE. It adds that there is evidence this aim has not been met, and that further guidance is required.
New recommendations propose that a risk-based framework of guidance be adopted, recognising one of the recommendations made by the Governmental Deregulation Task Force.
Based on this approach the draft proposals being put forward aim to provide the following:
1. Goal-based guidance setting out basic essentials, describing principles of risk assessment and control applicable to all sites.
2. HSE Petroleum Licensing Liaison Group. To facilitate consistency in enforcement by PLA's.
3. Technical guidance on the design and construction of new and redeveloped retail sites.
In order to provide the above guidance the HSE is proposing the setting up of three bodies:
1. An HSE Petroleum Working Party
2. An HSE Petroleum Licensing Enforcement Liaison Group
3.
The Deregulation Task Forces, in addition to the risk assessment approach to the application of standards, recommended a more consistent approach to this application, an improved appeals procedure and establishment of a body to recommend standards on design and construction of petrol stations. While the proposals do not set out an improved appeals procedure, they do recognise the other DTI recommendations.
The specific aims of the three groups are described below:
I. HSE petroleum Working Party.
To advise HSE on the basic measures relevant to safe storage and keeping of petroleum as. a fuel motor vehicles in line with the general reqwrements 0 HSW A and relevant statutory provisions.
2. HSE Petroleum Licensing Liaison Group.
To facilitate consistency 111 en101
c ·cement by PLA, s.
3. Industry Co-ordinating Body.
, d . d try on available
To provide advice to PLA s an 111 us w and t ol hazards at ne technical options to con r . .' r ht of the redeveloped petrol filling stat1donsh !'¥reasonably principles of risk assessment an w a is practicable".
d d ·tage have already
Discussions which are at a vance s , .· , , ddition a stee1 mg taken place with interested parties, 111 a . t·101n · sent·1t1ves group is being formed, with semor repre. ' H PLA's and industry bodies to ensure the e implementation of.these It is understood that t e re-draft of HS(G)4 I, completed some will not be sent out for public 111 its p1esent fo · but may form the basis of the new gwdance.
It is with much regret that we report the death in service of Brian Marsh Thompson who was a principal officer with West Sussex County Council. He was 55 years old.
Brian who was born in Cheltenham, began his local aovernment career in the Surveyors Department of Gloucestershire County Council. After 2 years national service as the regimental surveyor with the First Royal Horse Artillery in Germany he returned to Cheltenham but decided that his future lay with the Trading Standards Department. Whilst training as an inspector of weights and measures , Brian was responsible for the administration in the Cheltenham office and he is still fondly remembered by his former colleagues who remain with the County Council, for his administrative ability and his wicked sense of humour.
Upon qualification Brian moved to West Sussex in 1973 as a Trading Standards Officer. He was quickly promoted to Divisional Trading Standards Officer and later became a Principal Trading Standards Officer with countrywide responsibility for petroleum, fertilisers and feeding stuffs, and health and safety, a post he continued to hold until his death. His particular professional interest was in petroleum where he was recognised as something of a national figure and expert He was a long standing member of the APEA and had contributed a number of valuable articles to "The Bulletin". He was also an adviser to both the Institute of Trading Standards Administration and the Local Authorities Co-Ordinating Body on Food and Trading Standards on petroleum matters. played _a part the revision of the "National petroleum hcensmg cond1t1ons His state of the art knowledge in petroleum was widely recognised and respected by all the major oil companies.
Outside work Brian was a devoted family man , a keen photographer, gardener and supporter of the Bognor Regis branch of the Royal British Legion
His funeral at Chichester was attended by very many fiiends and colleagues and representatives of the Royal British Legion, reflecting the popularity of this quiet and dedicated man.
We exte nd our sympathies to M aureen, hi s wife of 31 n•·s hi s son Mar·k and daughter Lind a yecu ,
I · with deep sadness that we announce the untimely t. is t the acre of 61, of Wyndham Carey , Managing Pas smg, a ' 0 · '. . f GCS Garaae Consultancy Services Ltd. of South Directo1 o 0 Wales.
dh be aan hi s cru·eer in the oil and petrol e um Wyn am o · th 1960s workma for Valvolen e as A1ea mdu stry 1l1 e 0 d Tex aco (Reaent ) as Regi o nal Manager Manager an ' 0
In 1968 he moved to VIP Petroleum as the Sales Manager for indu strial outlets and di stribution throu ghout Wale s
In 1973, together with Barrie Gardner, he formed GCS Gar age Consultancy Services Ltd. providing a comprehensive service of specialist forecourt work to the petroleum industry.
He felt great personal satisfaction in 1993 , celebrating 20 years in business, culminating in becoming registered as a BS5750 quality assured company with the British Standards Institution.
His enthusiasm, commitment and personality will be greatly missed by his many friends and colleagues.
A funeral service was held in Merthyr Tydfil on Tuesday 12th July at which a lar ge number of Wyndham ' s friends from the local male voice choir sang ' Gwahoddiad' (Invitation from God). Thanks ar e expressed to those who travelled great distances to pay their respects.
Deepest sympathy is extended to his partner Sue, and his family.
Regional terminal
He diversified in 1971 becomin g Acquisition Direc to r for Brushdean Properti es , re sponsibl e for th e of. petrol fillina station s for re-dev elopme nt and hai smg with 011 b companies for the ir sub sequ e nt sa le.
This Code of Practice has been prepared by the United Kingdom Petroleum Industry Association in consultation with LACOTS (local authorities coordinating body on food and trading standards), and published by the Institute of Petroleum to provide a safe and practical operating framework under which Driver Controlled Deliveries can be carried out and guidance to persons concerned with Driver Controlled Delivery operations.
Driver Controlled Deliveries are permitted under "The Road Traffic (Carriage of Dangerous Substances in Road Tankers and Tank Containers) Regulations 1993". (Schedule 4). The changes to the Legislation allowing DCD's followed extensive trials by the Oil Industry under the direction of the Health and Safety Executive and a number of Petroleum Licensing Authorities. All those concerned with the trials fully supported the introduction of DCD's as a safe and practical means of delivering motor spirit to Licensed sites, and their experience has been used to develop this Code of Practice.
Licences for Driver Controlled Deliveries, granted under the above legislation, are issued to a Person or Company (Licensee) and not to the site if the Licensee changes, a new application must be made to the Licensing Authority to continue with DCD operations. Fees specified in The Road Traffic Regulations 1992 Schedule 4 Part III are payable with each application.
ISBN-0-85293-141-7 £16.00 (Overseas £18) 25% discount is given to IP Members.
identify the source of the problem and address the question of the land contamination. The Posisump installation may be temporary or in situations where the source of the problem cannot be confirmed, the system will provide a permanent solution. The system has currently been successfully used to overcome the ingress of petroleum vapours to forecourt kiosks and adjacent property where levels in excess of the explosive limit had threatened evacuation.
Technology originally developed in the fight against Methane and other Landfill gases has now been successfully api;>lied to the growing problem of petroleum vapours and their impact on forecourt buildings and adjacent property. Positive pressure technology is applied to the problem by two separate systems, the Posisump and the ERIC. Both systems have recently been assessed in the field by the London Fire Brigade.
The. Posisump achieves its effect by diluting and the vapour accumulated below the property and mtroducmg a zone of positive pressure which creates a . air blanket, so preventing any further from .nsmg up and putting the property at risk. The Pos1sump is unobtrusive and fits neatly on the exte'..1or of the. property within its own weatherproof T?e umt. can be installed within eight hours and is 1mmed1ately upon activation. The zone of of the positive pressure is demonstrated at the pomt of mstallation by tracer gas tests which confirm the extent of the clean air blanket and allows the balance of the system to be affected. The system installation is site specific and has proved effective for all types of floor construction. In its. application to commercial prope11y there is no size limit for the system. Where property has become affected by petroleum vapours rising up from the ground below. the install al ion of a Posisump has immediately removed the risk hoth to the structure and to the occupants. giving all parties c1 mcerned a valuable breathing space within which to
The ERIC system operates by applying positive pressure within the property from a self contained unit located within the loft space. Petroleum vapour accumulated below the property can be drawn in by the natural negative pressure gradient caused by the occupation of the property. The ERIC system acts by reversing this pressure gradient and prevents the vapour from being drawn in. As the ERIC system operates by regulating the internal atmosphere it bestows many secondary benefits on the property by providing a clean and fresh environment. The ERIC system is most effective when the levels of contamination are low and may be used in conjunction with the Posisump to provide a complete clean air system. Both patented systems are now actively being specified throughout the UK and will soon be available under licence outside the country. All enquiries to be directed to Prestige Aire Technology. Tel. 0233 740844.
Hytek, the leading supplier of specialist products to the fuel handling industry, continues to defy the effects of the recession by announcing that sales last year were up by an impressive 24% on the previous year's trading. Staff numbers also increased by one third.
Hytek have long since realised that to be successful via a network of distributors requires product quality, availability and service levels to be hand-in-hand.
Product quality is very high as anyone would expect from a company accredited with the BS5750 quality standard. In order to maintain consistency in meeting availability an.d service level requirements, Hytek have Elsenham premises resulting in a 501* mcrease Ill
floorspace. This in tum means that the number of stock items been increased so that the minimum value of stock at any exceeds £350,000. Every component, stocked is entered mto the company's computerised stock and administration system which, via network linking all the company's. P.C.s, allows interrogation by any member of staff handlmg a telephone enquiry. All items ordered leave the Hytek premises on the day of ordering.
Hytek also identified the need for improving communications with distributors to ensure that their product knowledge was never found lacking. To satisfy this need c?nstructed_ a dedicated training facility within the new bmldmg extension. The new training facility, which boasts eve_ry modem audio-visual training aid, was completed m I993. It is already being put to regular use for mtroducmg new products, updating product developments and for staging open discussion forums with distributors on ways to further improve service levels.
A programme of new product development ensures that Hytek range is continually being reviewed and updated m order to take advantage of the changing needs of the marketplace.
Dear Sir,
Water the United Kingdoms most precious resource is under serious from every imaginable source threatens its supply daily_. Narrowing and defining the of pollutants :eqmres study, meetings by professional boards or commissions, and expensive research into new technology offer solutions. At a time when the cons_e9uences of are not budget sensitive, government 1s deregulatmg and businesses are trimming resources. Determining who is liable for failure to respond to water pollution is as hard to define as paying the bill.
Years of environmental damage to water resources is hard to swallow. Other countries, principally the united states, have enacted statutory laws regulating environmental issues. Such laws specifically identify storage facilities as possible sources of petroleum, or benzene, pollution to ground water supplies. On a broad _scope the UK has defined and adopted statutory regulat10ns restricting certain petroleum products from being introduced into ground water or water aquifers.
Under the water resources act of I991, the main pollution offence under section 85 and 86 is "to cause or knowingly permit: any poisonous, or polluting matter enter controlled waters". Penalties attached to the law mclude, upon conviction, a fine up to £20,000 and/or imprisonment for up to three months.
The national rivers authority provided information on two important issues relating to the water resources act. First. groundwater is definitely considered "controlled waters" under the act. Second. products containing benzene, like gasoline, are specifically included under section 85 and 86 of the act. Several years of study by independent boards and commissions led to recommendations on strictly defined UK laws.
HS(G)41 is an example of continuing efforts to regulate the release of benzene into the environment. HSG-41 a of de:egulation, yet, still remains a strong omde. The Nat10nal Rivers Authority may be the guardian of_ water resources, but, HSG41, while only a gmdelme, places British Petroleum officers at the forefront of policing an identifiable source of benzene pollution underground storage tanks.
Petroleum officers are responsible for safety on petroleum foreco_urts. That responsibility includes storage tanks and ancillary piping that may contain hazardous matenals. Rivers authority has a . . to gmde its actions. The burden of responsibility 1s i_nuch greater for the petroleum officer. Insurance for simply refuse to provide or _renew a pohcy until satisfied that a property is environmentally safe. Neither a tank owner nor a petroleum officer have the same recourse. The tank owner, however, can close or replace a tank. Petroleum officers can limit their liability by making correct decisions on what tanks to test who is qualified to do the testing and what equipment will pass the scrutiny of a legal challenge.
In the UK it is generally accepted that tanks over 20 years old must be inspected for structural integrity prior to renewal of a license to operate. Lines are tested every five years. A license to continue operating a tank is approved by petroleum officers. They also approve equipment and technology used to inspect tanks. Criteria for accepting a technology generally follows U.S. EPA guidelines. By accumulating and reporting research data for ten years prior to implementing statutory laws, including certification test protocols, the EPA is accepted as a standard world wide.
Companies offering services to test the integrity of underground storage facilities provide independent equipment and technology certifications for precision measurements. This "third party certification" by nationally recognised research petroleum a unique opportunity to hm1t his habihty. The precision equipment certification process uses standar? ?PA protocols to independently measure accepted cntena agamst equipment manufacturer's specifications. Claims by manufacturers are measured against such criteria as the ability to accurately measure the effect of product temperature (coefficient of expansion) and includes extraneous measurements such as product levels, size of tanks, differential volumes, leak masking due to outside tank pressures and standard deviations of test results. By not following a universally accepted ce11ification process the petroleum officer puts himself in a position of being the ce11ifying authority for precision test equipment and technology. The liability attached to these decisions is obvious.
Who will be held responsible when drinking water, a commodity typically taken for granted. is contaminated? Petroleum officers will be at the top of the list when the question is raised. I believe the men and women in the petroleum officer cadre should be commended for the excellent manner they are executing their responsibilities. It is in everyone's interest to support their activities to professionalize the industry by demanding the highest levels of professional standards and integrity by those companies working in the forecmnt environmental sector.
Nick Lane EurotestI read with great delight the article by Harry Reid (Bulletin Number 2 May 1994) and agreed heartily with some_ of what he had to say. I would reiterate his sentiments over mcon sistencies within the Regulating Authorities of the UK and I believe that some have had the good sense to join togeth e r as an association and speak with one voice to an indu stry looking for the com mon playing field with fixed goa l po s ts . I would s uaaest howe ve r that their first choice of bb standa rd s, how ever well meaning was like choosing to play on a s lope that did nothing to help those trying to play the ga me.
My delight , a s I referred to earlier was in the rea dina of a number of fact s quoted within article. Now an opport unity to answe r the many c ritici s ms lev e lled at my compa ny mad e through ig noran ce of my product and service a nd more imp o rt a ntly th e ig noran ce of their own sy stem s a nd pro to co ls
1 wo uld lik e to s tart w ith th e fact that there is no s uc h thin g as be in g EPA acc re dit e d , a c onc e pt ofte n bante re d about. E P A d o not test , ce rtify o r approv e any s pec ifi c co mm e rc ia l brand of lea k de tect ion sys te ms In s tead the EPA d esc rib es how e quipm e nt s ho uld be tested to prove that 1l m ee ts th e ir s tanda rd
C (J nclu c ting thi s tes tin g is left to e quipm e nt manu fact ure rs 1n c on jun c tion w ith third party tes tin g o rga ni sa tion s T he manufactu re r th e n prov id es a co py of a re po rt s how in g th e tc -; t m e th od m ee 1s EPA ·s pe r fo rman ce c r it e ri a
EPA test method may be evaluated by the manufacturer or a third party independent group, the latter being the accepted normal course of action. EPA accept a third party as being consulting firms, test laboratories, non-profit research organisation s or educational institutions with no organisational conflict of interest. In general the EPA believes that evaluations are more likely to be fair and objective, the greater the independence of the evaluating body. No third patty test house in the USA or the rest of the world has accreditation to or by the EPA.
There are a number of Authorities who for one rea son or another have not understood fully the guidance given from the HSE with regards to tank testing, only taking a general intere st in it or accepting it to the last full s top and comer without understa nding its intentions. A s a consequence to the se ac tion s we have taken the is sue to the Department of Employment who preside over the HSE and they have asked the HSE to send out further advice to Licen s ing Authoritie s on thi s iss ue apart from the wide reachin g refo rm s already propo sed by deregulation , that being another debate. We have been prornise d thi s clarification from HSE to be published by mid Auau st at the late st. We mu st hop e it b co ntain s the good common sen se that so many Authont1e s are see king. HSE we re hopin g that thi s alre ady ex is ted , but appare ntly not.
Harry we nt o n to say that the EPA accre ditation safety , acc uracy a nd re li abi li ty J wo uld take iss ue w it h thi s fac t a nd sta te that th e eva lu atio n re port wo uld c le arl y
indicate that no safety factors were implied or accepted during the tests. I would ask, therefore , where the HSE evaluation was carried out?, by whom? and was it acceptable?
Reliability The evaluation again makes no attempt to check, certificate or assess a products reliability. The protocol clearly allows time for manufacturers to interchange equipment that fails, without detriment to their test. I would also point out that many pieces of equipment are assessed prior to meeting U.K. BASEEFA certification and any changes made are not then resubmitted for assessment only certification by the manufacturer as still complying I also believe that many inhouse modification are made to equipment without any reassessment or even returned to the manufacturer on a regular basis for calibration or servicing Why is this acceptable?
Harry then makes his final attack on a low pressure testing system , without I assume, first reading his own protocols. I quote "When the ground water is above the bottom of the tank , the operator has one of three options
l. "Defer test"
2. "Test as per normal routine and run a supplementary routine ' WTCOMP ' to properly evaluate the tank status"
(YOU MUST KNOW THE WATER LEVEL TO COMPLETE THIS PROGRAMME)
3. "Pressurise the ullage space with Nitrogen" (BAD PRACTICE says Harry).
I would suggest that with the number observation wells available on U.K. filling stations being in the minority of situations , the obvious course of action would be to assume the worst and therefore only option 3 is available I know this not to be general practice and assume that by divine providence the w_ater is and a test conducted. The Nat10nal Rivers Authonty will be fascin a ted to learn of this calculated formula and I am sure will very soon ask the question. .. ..
Harry then goes on to the credibility of low pressure systems and their accuracy. I assume he has qualifications to match those of our Evaluation from Leeds University. If so it certainly would have been cheaper to ask him to evaluate the system. I think it was unfair to criticise a system he had no in-depth knowledge of and he would not want me to say that I do not believe you can measure level changes as he claims, based on the knowledge of working with Veeder Root pump-up gauges as a datum point.
The PSL tank testing method does as you would expect, conf01i:1 to A. standards as assessed and validated by an Educat10nal mstrtute (University of Leeds) as detailed acceptable earlier. It has been submitted to Health and Safety for evaluation and passed with its electronic components approved prior to all assessments. To ask anything more is outside the scope of HSE intentions or requirements outlined in HS(G)41.
I end this reply to Harry with clarification of the title:
When is a tank test, not a tank test? When those testing do not fully understand or comply with protocols, criteria and obligations set out by themselves.
This reply is provoked and not designed to be derogatory to any one system. All systems operating within the U.K. at present have their faults and problems. Tank testing companies fighting among themselves will prove to be futile and non-productive with the industry and the environment losing out. I have in my past been very involved with conservationalist issues and on large scale environmental projects for Metropolitan The green iss_ue_ is not driven by greed but a true de sire for a cleaner Bntam. The way forward must be , to ac cept that can adequately detect leaks in tanks and pipework. Bemg better rnorntored by results rather than some evaluation papers , this has always been the EPA ideal.
Promptin g the regulating authorit.ie s _ into action should _be a high priority instead of everybody arguments that detract from the. iss ue and stop te stmg altogether with leaking tanks bemg undetected and the environment suffering the consequences.
When it is realised that more people enter petroleum filling stations than any other establishment having highly flammable materials, it is surprising that only recently have steps been taken to introduce European safety and performance standards for much of the ancillary equipment used on such sites. In other industries strict rules are applied to ensure that standards of performance and safe operating practices are maintained. It has always been necessary for electrical apparatus to be formally certified for use in zoned areas and now mechanical equipment must also be examined. To date however, no independent functional tests are required on much of the equipment in use on petroleum forecourts and safe operating practices are not always clear. The result is that the burden of responsibility falls on licensing authorities. Is this reasonable and is there not now a need for independent testing and assessment by an independent body in the UK?
For suppliers of equipment and forecourt operators the absence .of standards could be considered a bonus, because potentially this permits them complete freedom. This is a short sighted philosophy however, because in the absence of generally recognised performance standards, reputable suppliers will always be at risk of unfair competition from those wishing to take commercial advantage of the situation.
Equally, as the Machinery Directive assumes wider impact, strict observance of essential safety requirements will become more important. If it were necessary to prove that equipment is both safe and operates to an acceptable level of performance, both suppliers and users alike would benefit, because only fully acceptable equipment would reach the market place. Whilst for suppliers this might incur cost, it would at the same time safeguard their 111terests, because users would have a more discriminating basis on which to choose. Users, on the other hand, would be less at risk of receiving unsatisfactory equipment.
Much of the real responsibility for overseeing petroleum to the licensing authorities. As suppliers cont111ue 111troduce more sophisticated equipment, judging the effectiveness of such equipment is increasingly difficult. The_ knowledge needed to properly evaluate such is considerable, particularly when software is and is probably outside the competence of most Ultimately, licensing authorities must therefore from their own experience, which may be inadequate, or simply reject the new equipment which could slow progress. How much better it would be therefore, if they could_ refer s_uch issues to an independent body that is expe_nenced 111 the wide ranging technical disciplines required to test and assess such equipment.
Some of the techniques now being adopted to protect eleclrical equipment for use in flammable atmosphere bring with them a new generation of installation requirements.
( lse. for example. of equipment protected by Increased Sali:ty techniques places far more emphasis on ensuring that r·ircuits are properly rated. This was of less concern when
using Flameproof equipment alone. It is also not generally recognised that when equipment is certified Intrinsically Safe, this often requires modifications to electrical circuits, which can influence functional integrity. Even time honoured devices, such as flame arresters, actually require closer scrutiny than has been realised in the past. The ability of a deflagration flame arrester to stop a flame is almost entirely dependent on the system of pipework into which it is placed and this needs to be properly examined. Earthing strategies, particularly when intrinsically safe circuits are involved, need to be appropriate and the influence of fault currents due to installations local to a petroleum forecourt, must be understood and neutralised.
There are therefore many reasons why an independent body is needed to examine all these issues. While the standards are being created their involvement is perhaps even more important, because in setting new rules, well established practices and test procedures should be understood before developing new ones, otherwise the quality of new standards could fall into disrepute.
At present much functional test work is carried out by organisations in the UK, where much of the latest equipment is now being produced. It is acknowledged however, that many of their test methods have not been wholly adequate, which leads to the conclusion that in setting new standards we must not fall into the same trap.
The credibility of any body that chooses to offer a test and assessment service must also be considered. Such a body would need to be very experienced in explosion safety, have wide ranging technical expertise, extensive test facilities and access to the very latest research on this subject. This body would also need to be governed in such a way that the validity of any test and assessment work is kept under strict scrutiny. This is very important because social and commercial pressures must not be allowed to influence the conclusions they may reach. Responsibility for overseeing such bodies normally falls to organisations as NAMAS and NACCB, who accredit test and certificat10n authorities in the UK. These bodies examine in detail test methods, equipment, management and quality assuran_ce systems and ensure that such bodies are kept under stnct control by regular surveillance visits.
Suppliers should also have approved quality ?t least 111 accordance with BS 5750 Part 2 or !So 9002. This is important because it is the only mechanism that imposes _a control on the manufacturer to faithfully reproduce his products. The only other approach is for a third party to inspect equipment to ensure that it is being faithfully reproduced. The latter approach has been adopted in the UK by companies from abroad who have no quality system of their own. Frequently such companies have European certification of electrical apparatus for use m explosive atmospheres, where unlike the situation in the U!<· the certification authorities have not imposed strict qualtty controls. More informed users who need to be sure that the products they are buying are of consistent quality will often
however, insist on quality control. Independent inspection by a third party resolves this problem for companies who might otherwise be in difficulty.
The cost of setting up as an authority to satisfy all of the above requirements would be prohibitive for most organisations wishing to act in the role of an independent test and assessment body. ERA Technology, are however already well down this road in every respect. For many years they have offered an independent technical service to all parts of industry and have all the major electrical and mechanical engineering skills and test facilities assembled on one site. They have a number of NAMAS test laboratories and in particular a whole department concerned with explosion safety and all types of explosion protection. A great many of today's product and explosion safety standards were based on research conducted at ERA and new frontiers are always being explored. Specialist areas of
expertise include the performance assessment and calibration of level measuring instruments, assessment of precision leak detection systems to the US EPA code, specification of safe operating practices, earthing surveys, hazardous area assessment, testing of polymetric materials for handling petroleum products, evaluation of flame arresters and inspection of many peripheral components. ERA Technology are also in the process of acquiring notified body status under the Machinery Directive as the final step in offering a complete service. Members of ERA also sit on a large number of CEN and CENELEC working groups and bring with them a wealth of experience.
There is therefore no longer a need to continue as we have in the past. By taking moderate steps, proper tests and detailed assessments can be conducted in the UK. All that remains is for the industry as a whole to recognise the need and begin to make use of the facility.
We realise now, if we did not before, that testing tanks as we did in the past will not find the size of leak which the HSE draft document HS(G)41 recommends and which modem technologies can achieve. It would be surprising indeed if only in this industry did technology not advance significantly over the years. We have come to realise that a leak threshold as small as 0.38 litres per hour, depending on the size and contents of the tank, and such a change of temperature would be unusually small, as anyone involved in volumetric precision tank testing can readily prove. We can therefore rule out old fashioned pressure testing as a viable means of testing tanks to the new leak detection standards unless temperature layer profiling is done simultaneously.
With these as limitations, it was natural for new technologies to emerge but, since they were unknown, it was right to establish safety and performance criteria for them. It would not however be right to set such criteria for new tests and not also to apply them to existing tests. Licensing authorities should not be expected to have the knowledge or resources to judge the performance or safety of equipment . use in their area and they would be taking an 01 ssary and potentially onerous responsibility for so unnece. d It is right then that they look to the proper observance omg. d f . 1 ble standards or co es o practice. ofavat a ·
f fety standards are concerned. Europeans have
As ai as sa · h. CENELEC . d C ntral European Norm. 111 t 1s case a ag1ee a e . )14 "'O Th.· f·· ·1 1· d d " 1 ·tr1·cal s·1fety EN 50( -L 1s c1m1 y o st·m ar 1or e ec · • · ' d d ·ncltides the intrinsic safety standard required ot stan ar s 1 · · Th' electronic equipment m zones. is standard has been translated mto a of languages and has been adopted by a!l EEC In corresponding standard 1s VDE 0171 Pm t 7-.5.78 ce1 t1hed Y PTB. in the UK the corresponding standard 1s BS5501 Part 7 certified by EECS or by SCS etc. CESL DEMKO and INIEX are other certifying bodies often encountered on electrical equipment used in hazardous areas.
In the UK, test houses such as BASEEFA, ERA or ST & C evaluate equipment conformity to the standards on behalf of certifying bodies. In all cases, confirmation that the equipment is of an intrinsically safe design is that it will be marked as follows "EEx ia IIA T5" (or similar) for equipment used with petroleum in Zone 0, for example. It will also carry the mark of the certifying body a unique certificate number. These marks mean that the design of the equipment which was submitted for approval met. all requirements of the European standard. It this nomenclature which needs to be present on all eqmpment permanently or temporarily installed in h_azardous zone. Not only is this design standard always 1dent1cal and agreed across Europe, but failure to accept a member country's version of it, is contrary to European law.
What "EEx ia IIA T5" does not guarantee is that the paiticuJai· piece of has been built to the certified design or, that if it has, has not subseque?tly been modified. This ai·ea of comphance to the standard 1s a w01Ty to many. In some cases, a assurance may be approved, as with an EECS MET certification. In both cases random penod1c 111spect1on of the manufacturers premises and systems is involved. Even more reassurance can be gained if products built to the standard have been 100% inspected to the standard and there is a fixed population of such products. Neither. though, is a guarantee that the equipment has not been modified subsequently or that its performance has not been impaired. There is not yet a comprehensive or accepted solution to this compliance problem.
There are no known European accepted performance standards for leak detection and until there are. and there arc moved afoot. the recommendation is that we in Europe accept the tried and trusted American Environmental Protection Agency (EPAl protocol for the testing of tank tests. There are a number nf NAMAS approved agencies which have the potential to certify. either to EPA protocol or to a European one when it
As with intrinsic safety, there is the standard and there are recristered test houses which have the proven facilities for out the suite of tests specified in the EPA protocol. As yet there are no such registered test houses in the UK and none known to the author with the facilities to carry out such tests. It could be argued to be imprudent for a licensing authority to accept proof of leak detection capability other than from an authorised test house such as Midwest Research, Vista or KW A if they do they could be taking more responsibility than they need should such a system subsequently be proven not to work.
Certification to the EPA protocol is intended to provide assurance that the design of the equipment submitted for test was able to detect a leak rate of 0.38 litres per hour with a better than 95% probability of detection at that level. The test results report the settling time used, the temperature change to which the product was subjected to and the time period over which data were recorded. This same document can be used to check that the test company is testing to the conditions under which it was able to meet the standard. Again, it does not guarantee that the test equipment is as submitted for test, nor that the procedures used are being adhered to.
One issue is that test equipment which had to be modified to gain European intrinsic safety standards has usually not been resubmitted for EPA testing to confirm that the modified equipment still performs to the EPA leak detection protocol.
The equipment must be manufactured in accordance with the intrinsic safety design, in accordance with the design standard of the equipment which was used to gain EPA approval, and to a recognised quality assurance standard such as ISO 9000 or MET or other equivalent. The quality standards should include a programme of random inspection of the assembly process and of the quality assurance procedures.
There are four distinct areas to tank system testing: testing of the wetted volume; testing of the ullage space and vents; testing of the product lines; and testing of the offset fills. The leak scenarios which this suite of tests should be able to detect should include:
a a leak of product outwards into dry soil.
b a leak of product outwards into soil already saturated with product.
c a leak of product outwards into water.
d a leak of water inwards into the ullage space.
e a leak of water inwards into product.
r a leak of product inwards into product from soil and/or concrete already saturated with product.
g a leak involving no change of level due to counteracting effects of temperature.
h a leak from one compartment into another. a leak in a single offset fill line.
J a leak from a suction or pressure line.
k a leak in a vent line.
Few tests can detect all of these but a combination of volumetric testing and acoustic ullage perhaps uniquely, does appear to cover them all. If all these events require to be detected, then those prompting or commissioning the test need to confirm that the selected test has that capability.
The protocol adopted by the testing company should be lodged with the licensing authority and cover safety procedures and test procedures. The test procedures need to reflect the protocol which was necessary to achieve the EPA certification. Regrettably, this is not always the case. Companies may claim, for example, to test in less time than their EPA test results required.
In addition, staff need to be individually trained and certificated on the equipment, rather than the company.
The third element of performance standard for the tank test personnel are the quality assurance standards and procedures of the testing company itself. Increasingly, the requirement will be for the tank testing company, as well as the manufacturer, to have IS09000 quality assurance registration or an equivalent standard.
A fourth element of personnel performance is that it should be ideally impossible for there to be an incorrect result due to inadequacy on the part of the tester or his company.
If we are to declare an expensive asset such as an storage tank tight or leaking and we risk creatmg hazardous conditions when we test, we need to be of safety and performance standards. For tank this means that the equipment must be to an mtnns1cally safe design, have been built to that standard and not have been modified from that standard. The equipment needs to meet an accepted leak detection standard and at present, the only accepted standard is EPA. The test protocol needs to match that required to meet EPA standards, and to the needs. of safety on site. Finally, staff need to be mdividually work to recognised quality assurance and 1f at all possible the responsibility for an mdividual tester on site to call the tank tight or leaking should be removed.
In absence of such practice the lowest standard of capab1hty and performance will become the norm.
An overfill prevention device is the last line of defence against a spillage. By its very nature it is only ever used when all other systems and procedures have failed. Where hazardous product is being delivered into a tank it is vital that this final line system is designed to ensure that an overfill cannot occur.
The main advantage with Mechanical Float Valves is that they are in themselves an individual unit entity. In other words one Mechanical Float Valve will provide a certain degree of overfill prevention for one tank. As such if the requirement is to protect one or two underground tanks on only a few petroleum retail sites the Mechanical Float Valve probably offers the best overall option.
There are however, a number of important limitations on the effectiveness of Mechanical Float Valves and in certain applications they can contribute to serious safety related problems.
Mechanical Float Valves, like all floats, are prone to stick or fail. In an .overfill prevention application, where the device should, m theory, never be brought into action the o.f a .Mechani.cal Float Valve eventually sei,zing up and st1ck111g 1s a certamty. The only question is when this will happen. It is therefore vital with Mechanical Float Valves that a regular maintenance and monitorinoprogramme is throughout the life of the sit; However even then 1t should be appreciated that if an overfill occurs between maintenance checks there is a significant c?ance that the Mechanical. Float Valve has seized. This 1s borne out by concerning fact that even 'th the small number of sites cmTently fitted with Float Valves. and the relatively small incidents of tank overfilling anyway. there have been a nber of dangerous ove1f11ls where the Mechamcal Float nm II v I e has failed. In essence 1t 1s rea y maccurate to call a in any application. an overfill They cannot be failsafe and are simply another !me of defence or factor of safety.
Mechanical Float Valves also have an impact on delivery efficiency and safety.
Because Mechanical Float Valves must be mounted directly into the fill line there is a certain degree of restriction to flow. This equates to an approximate 15% increase in the time taken to deliver product into each tank. Although this may seem insignificant it flies directly in the
face of determined industry moves to extend and streamline delivery efficiency. Indeed over the life of a site many thousands of deliveries will be made and a 15% decrease in delivery efficiency subsequently becomes an extremely relevant factor.
Probably the most concerning effect of Mechanical Float Valves is their impact on safety, particularly with regard to pressurisation of the petroleum retail site vapour recovery system.
Many Mechanical Float Valves cause a restriction to flow because a deflector plate must protect the flapper valve from closing due to product flow. Unfortunately if installation is poor or unusual turbulence is created, the flapper valve will close even when the float has not been triggered by overfilling product. This is an habitually reported problem with some types of Mechanical Float Valve and will obviously once again have an effect on delivery efficiency.
The problem may be compounded as the only indication that a Mechanical Float Valve has triggered is a small kick in the delivery hose. If the driver does not see this kick, there will be a delay of several minutes before he realises what has happened. Subsequent to this there is no fast way of emptying the hose of product and he must wait until either cars filling from that tank lower the level below the float or a small bleed hole in the Mechanical Float Valve empties the hose. Both options are likely to take half an hour upwards.
Most UK sites are designed such that the fill tube assembly extends to the very base of the tank. This ensures that the end of the fill tube is always submerged in product thus reducing splash and turbulence during delivery. It also complys with regulations that pressure built up in the tank should not be transfell'ed to the fill pipe.
The Mechanical Float Valve when installed will always have an affect on vapour tightness. In other words pressurised vapour in the tank can freely enter the fill pipe assembly. The degree of vapour leaks varies between types of Mechanical Float Valves but typically occurs around the hinge pin holes. pin connections for the external float. flapper valve mechanism and the connections to the top and bottom fill tubes. So bad are the leaks that in pump vacuum tests on the fill pipe the uplift achieved with even the most favourable Mechanical Float Valve was under half that achieved without Mechanical Float Valves fitted. In most cases the uplift was one quarter that achie\·ed withuut the Mechanical Float Valve. In the worst case no uplift was
Where tanks are manifolded together this means that the entire vapour recovery system and the fill pipe is pressurised. Consequently when a driver a fil_l pipe cap the pressurised vapour escapes at this pomt. Obviously the amount of vapour escape varies on the pressure build up but it has been high enough to blow the cap across the forecourt, in one incident only narrowly missing the drivers head. More normally a stream of vapour is allowed to flood the drivers working area and conceivably could traverse the forecourt to where the cars are filling.
Although, relatively cheap as units, Mechanical Float Valves are not easy to retrofit. Considerable work is nearly always required on the tank. This is time consuming and expensive but also causes considerable disruption to the petroleum retail sites normal operating business. It is the extremely high cost of retrofitting Mechanical Float Valves that multiply the actual equipment purchase costs by as much as 500%.
It must also be remembered that because Mechanical Float Valves are not failsafe they must be regularly maintained. their reliability is directly related to the quality and frequency of maintenance they receive. This is an ongoing requirement which can only become more time consuming and costly as Mechanical Float Valves age. Ultimately, as already stated, such a device will stop working and this is either picked up during maintenance checks or when an overfill occurs.
it is worth noting that in the early days of overfill preventJon on tanker loading at terminals a major UK oil company used a float system. After implementing this system o? most of their fleet they shortly afterwards scrapped 1t because it could not afford the level of overfill prevention that was expected of it. The float system was replaced with the internationally recognised failsafe SCULLY electronic system which is, in principle, identical to that proposed for retail site overfill prevention by SCULLY.
Scully RSVP INTELLICHECK comprises of a small and lightweight controller which is mounted permanently on the delivery tanker. The RSVP controller is linked via an air s':"itch to the foot valve pneumatics such that in a non permissive" or "overfill" state the air pressure holding the footvalves open is released.
The RSVP system utilises an optic sensor mounted in the each underground tank. The sensing tip can be to any level in the tank but is usually set to 97% 0 _f maximum capacity. These probes are wired in series to a socket which would typically be mounted at the fill point. It could, however, be positioned at any suitable access point for the vehicle.
When the driver arrives at the site he simply makes a connection to the site socket with a plug and helicoil cable that is carried by the vehicle and is permanently wired to the RSVP controller. This links the vehicle controller to the site prohes and completes the system. Provided the probes are dry and all components are working the RSVP controller will indicate a permissive green light and the driver can · harge and open his footvalves. If the probes are wet or the · ..,1crn 1s not working properly or the driver forgets to make
the plug/socket connection the controller will not give a permissive signal and he cannot charge and open his footvalves.
If one of the probes is wet or is not working properly the RSVP will indicate this on a diagnostic display.
In the event of an overfill on one of the underground tanks during delivery the controller will, via the air solenoid switch, release the footvalves and stop all discharge. Once again the diagnostic will indicate the tank that has been overfilled.
It should be noted that for the basic system as described above (which is exactly as used by ESSO in Belgium) the only equipment required on site are the probes and wiring the socket. The very low power requirement of the system is drawn from the vehicle battery and no site power is needed. All output from the RSVP INTELLICHECK controller is intrinsically safe (IS) as BASEEFA/CENELEC certified.
There are a number of specific benefits offered by the RSVP INTELLICHECK:
As indicated above the RSVP INTELLICHECK incorporates the SCULLY patented DYNACHECK. DYNACHECK is a continuous (30 times per second) and automatic self test on every single component in the system. This includes the controller, probes, cable and all connections. IF ANY SINGLE COMPONENT IS NOT WORKING CORRECTLY THE SYSTEM WILL FAILSAFE. In other words the very act of ,th_e system means that it must be working correctly. If 1t 1_sn t_It will not only display a diagnosis of the problem but it will also prevent a delivery taking place until that problem been rectified. This reassurance is not present with mechanical float valves and indeed most electronic systems.
Related to the above, the RSVP equipment, unlike the mechanical float valve, does not need any regular maintenance programme. Because it is failsafe any problem will be picked up when the driver cannot discharge into the tank with the problem. The diagnostics of the system are also such that it is normally possible to determine the exact nature of the problem thus allowing quick and reinstatement of the system. It is also worth emphas1smg that not only is the system failsafe but both the controller and probes are extremely reliable and proven. Scully provides a two year warranty on all parts.
The RSVP INTELLICHECK utilises the road tankers existing pneumatic footvalves. As such there is no need for additional valves which are both expensive and ca,n restrict flow. The RSVP probes are not fitted in the fill line and the system has no effect whatsoever on delivery rates.
The use of the footvalves also ensures that when cutoff occurs it does so at the tanker and not, as with mechanical float valves, at the underground tank. When an overfill occurs, therefore, the fill pipe and hose drains freely into the spare tank ullage allowing the driver to remove the hose as he would normally do after finishing delivery. Obviously the RSVP overcomes one of the main problems of the mechanical float valves that when activated they give little indication that they have closed and leave the hose full of product, thereby effectively stranding the driver and tanker.
The RSVP INTELLICHECK is highly flexible allowing,_ among other things, various interlocks. The most these is probably the vapour hose interlock whJC_h. if included, ensures that delivery cannot take place until the
vapour hose has been connected. The RSVP INTELLICHECK also has the capability to monitor retained product in the tankers compartments and is designed to allow modular build up in the future, ie the introduction of Cross Over Prevention (COPS) or the feeding into an On Truck Computer (OTC) Protocol can be changed as required.
The RSVP system can be fitted to the road tanker in approximately one day. The probes, socket and associated wiring can normally be fitted to the retail site in half a day to a day. There is no adverse disruption caused during the fitting of the RSVP to the retail site.
The control part of the RSVP, being on the tanker itself, allows it to utilise components, such as the footvalves, that are already available. The ratio of tankers to retail sites (normally approximately one tanker to ten retail sites) also means that there is a ten fold decrease in the number of controllers required over a site based system.
Because the retail site equipment is minimal (probes for each tank, cabling and socket) and is so easy to install (no site power required) the installed cost of retrofitting a site is normally actually lower than for a site fitted with mechanical float valves. The commercial savings obviously increase with the number of sites fitted with overfill prevention.
In summary the RSVP INTELLICHECK offers failsafe overfill prevention for retail sites at lower installed cost than for mechanical float valves and with ongoing savings in cost of ownership (no maintenance check programmes). Following an overfill the RSVP INTELLICHECK quickly and safely allows the driver to recover from the incident and continue delivering to other tanks.
But
Our specialist support teams are now backed up by a brand new control system and communications' network All focused on satisfying you , our customers, from your initial enquiry right through to after care Anywhere. Everytime
..
A WEFCO underground storage tank delivers petrol to the nozzle , where it's needed, not into the ground. That's because at WEFCO we're leading the field in environmentally friendly fuel storage with our double skinned tanks , giving maximum protection against leakage
WEFCO were the first petroleum tank manufacturer to be accredited to BS 5750 Part 1 ISO 9001 1987 , so setting the standards for other manufacturers to follow.
Underground storage is just one aspect of the WEFCO range of services and products , which also · lude GAP access chambers and cathodic inc f ff " · rt protection , all designed e 1c1ency, pe ormance and environmental protection.