
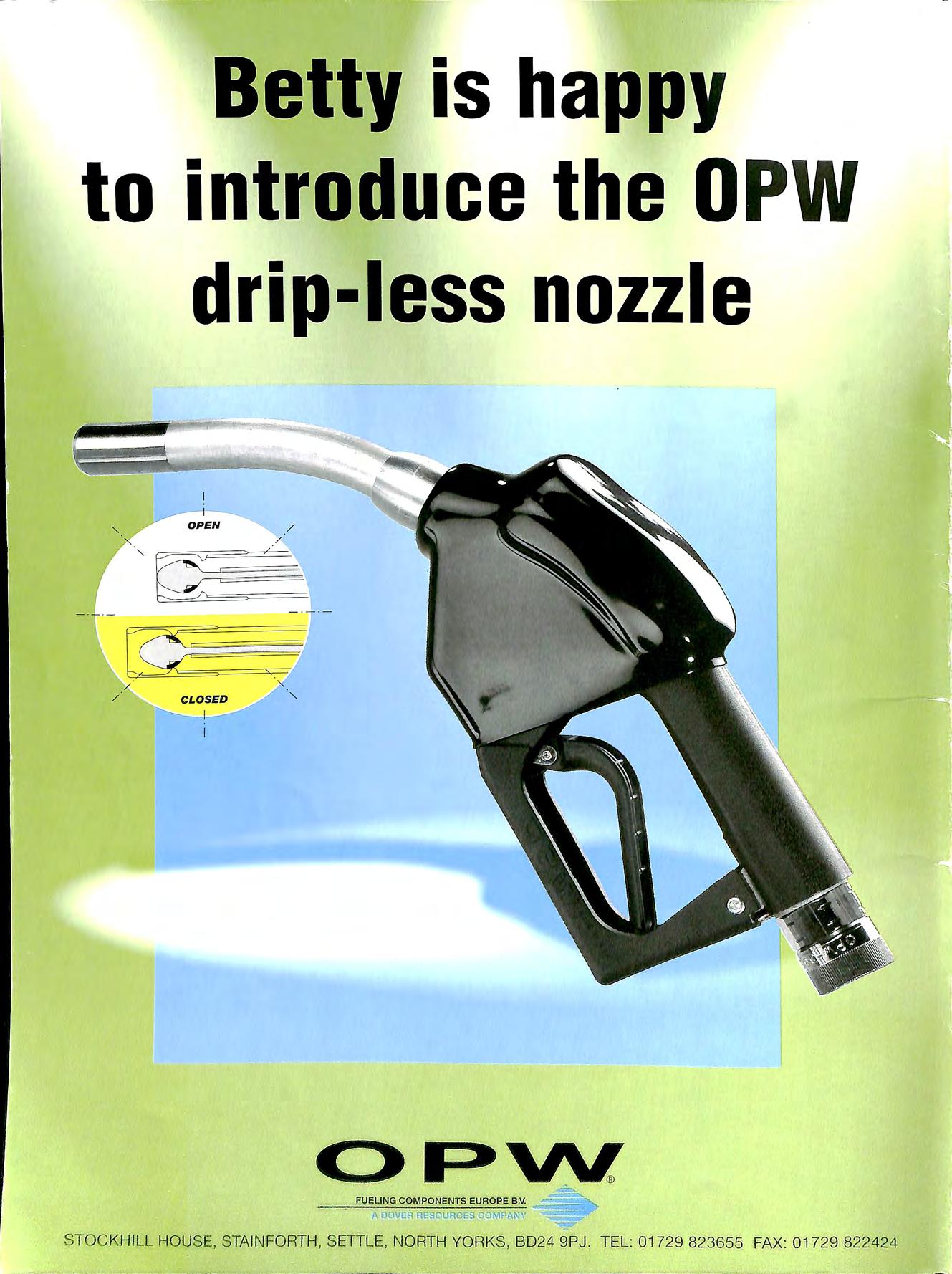

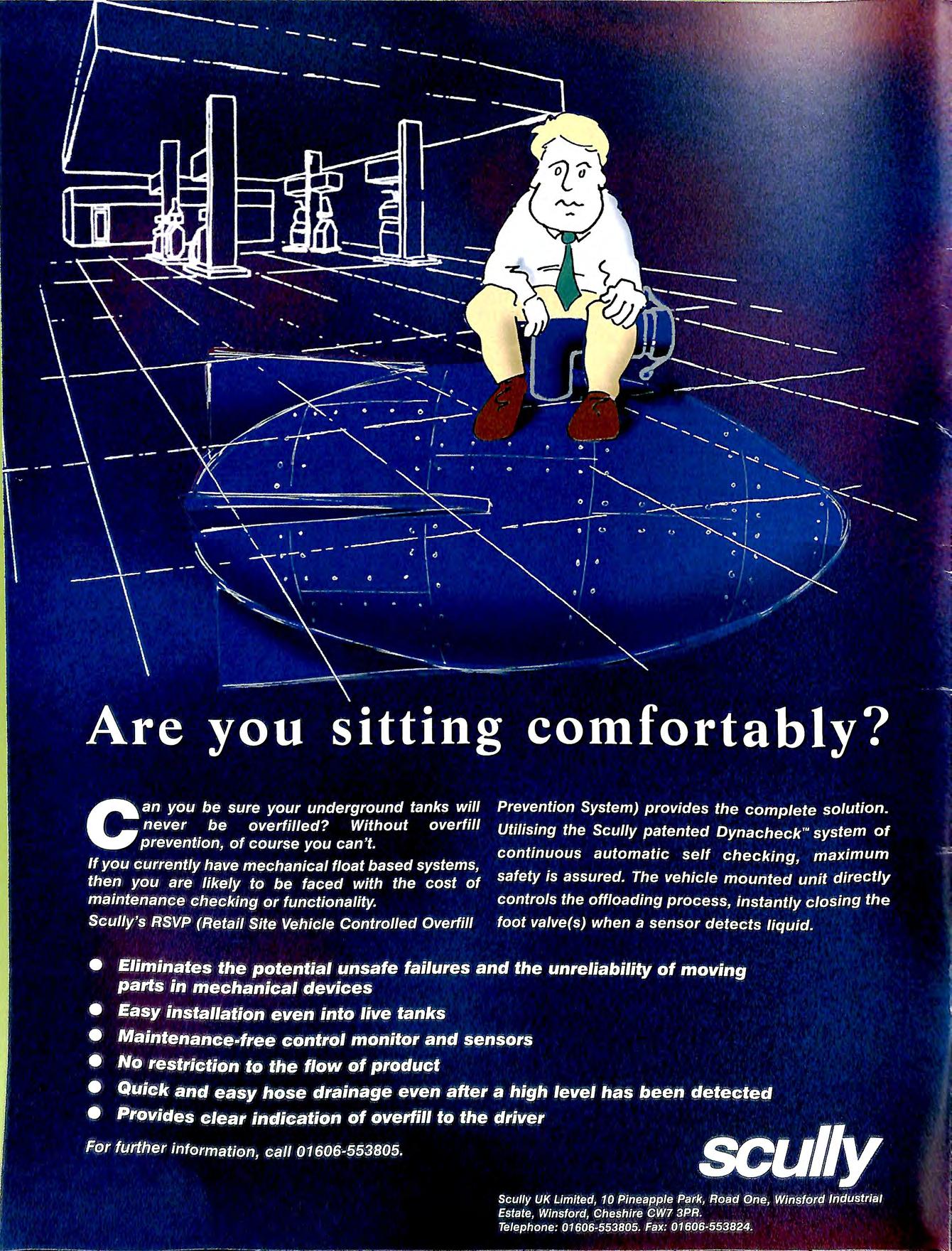
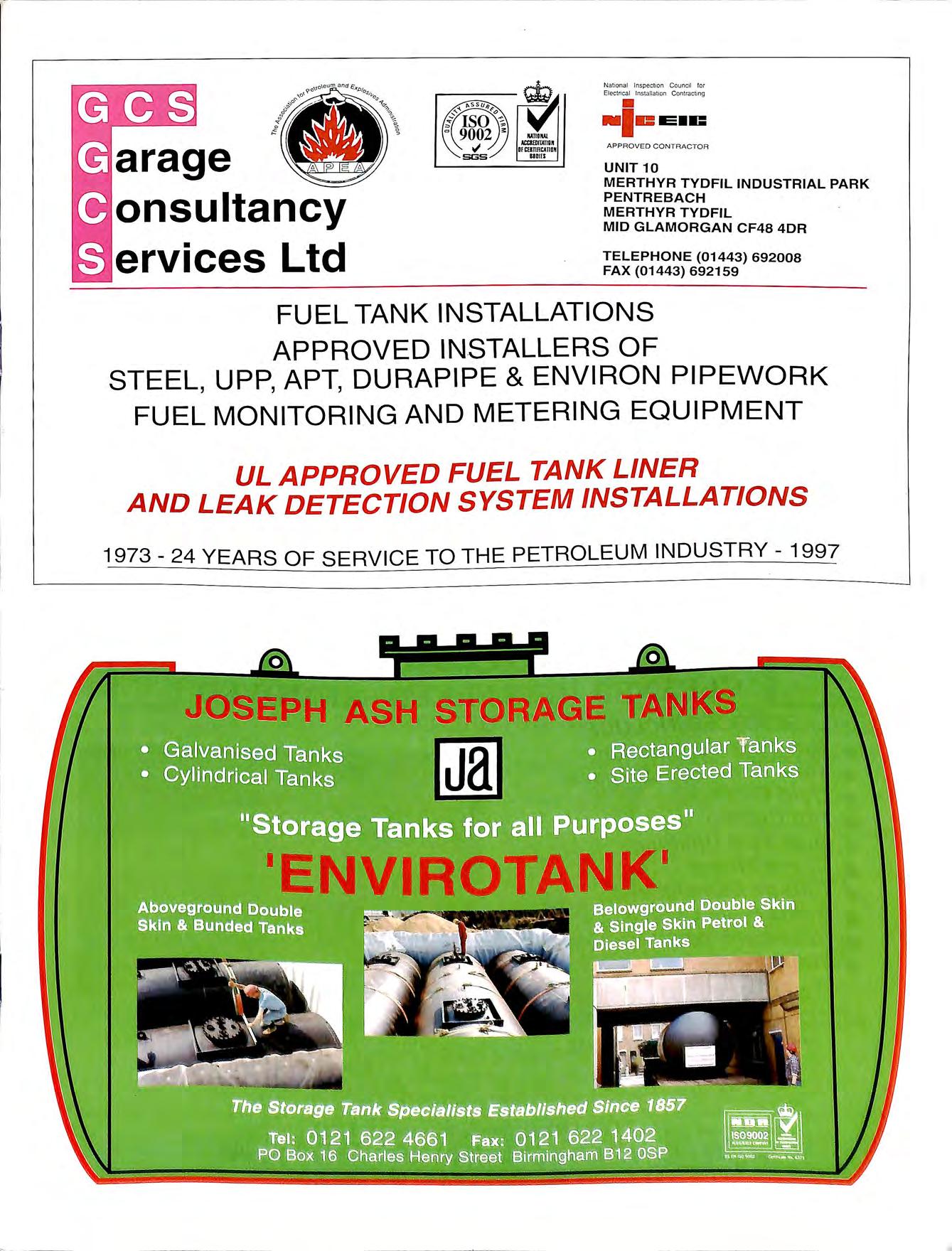
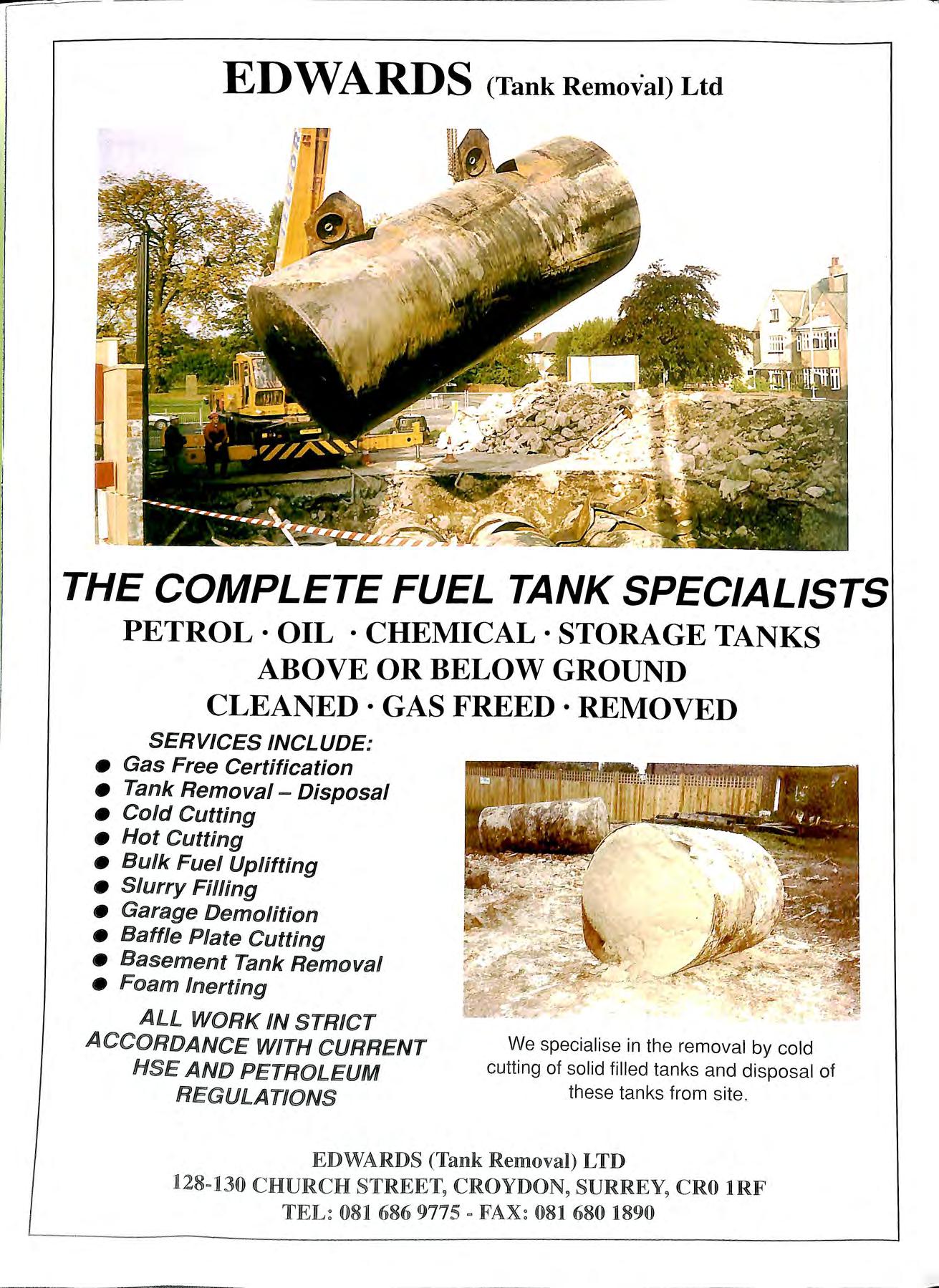
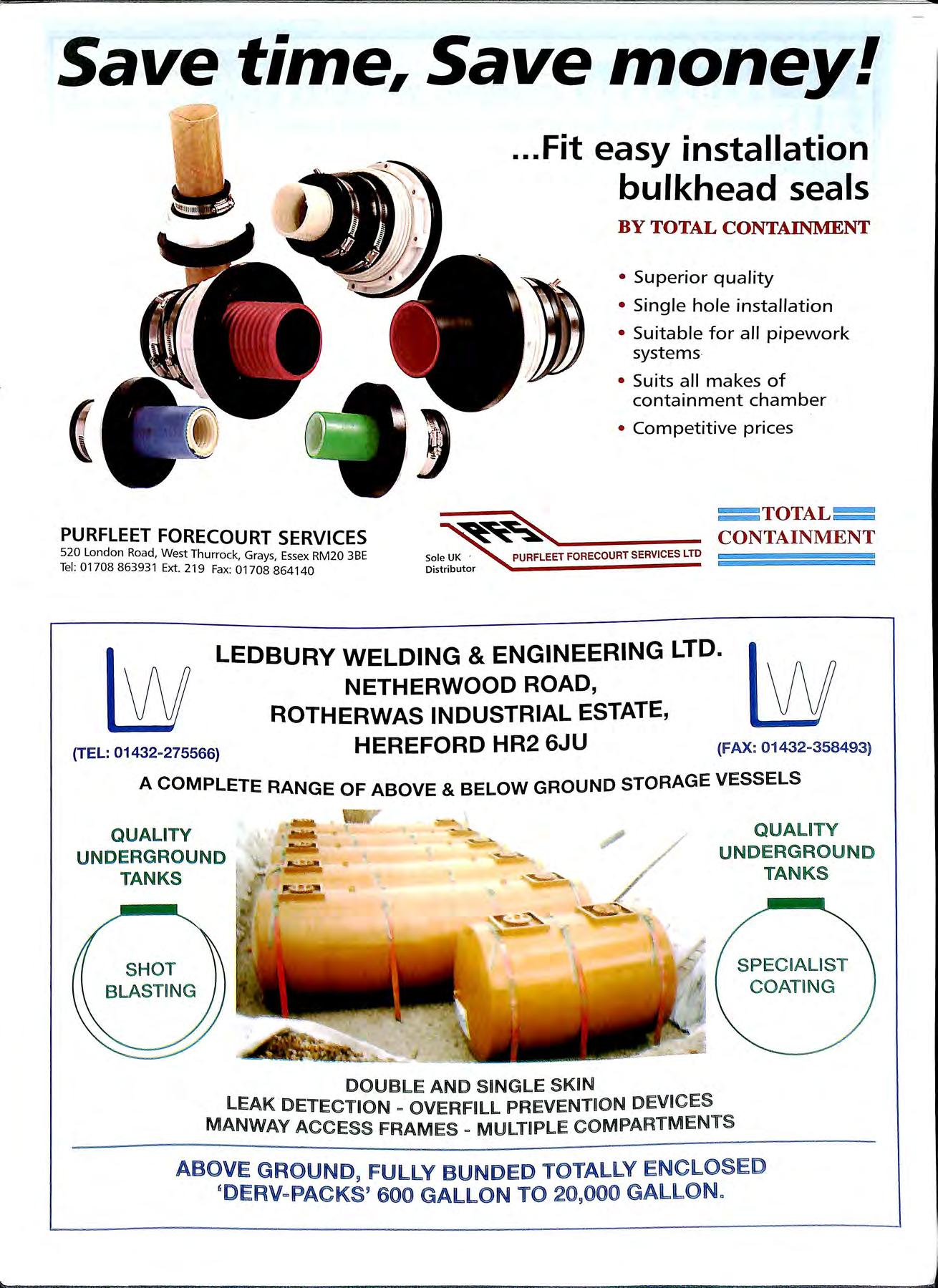
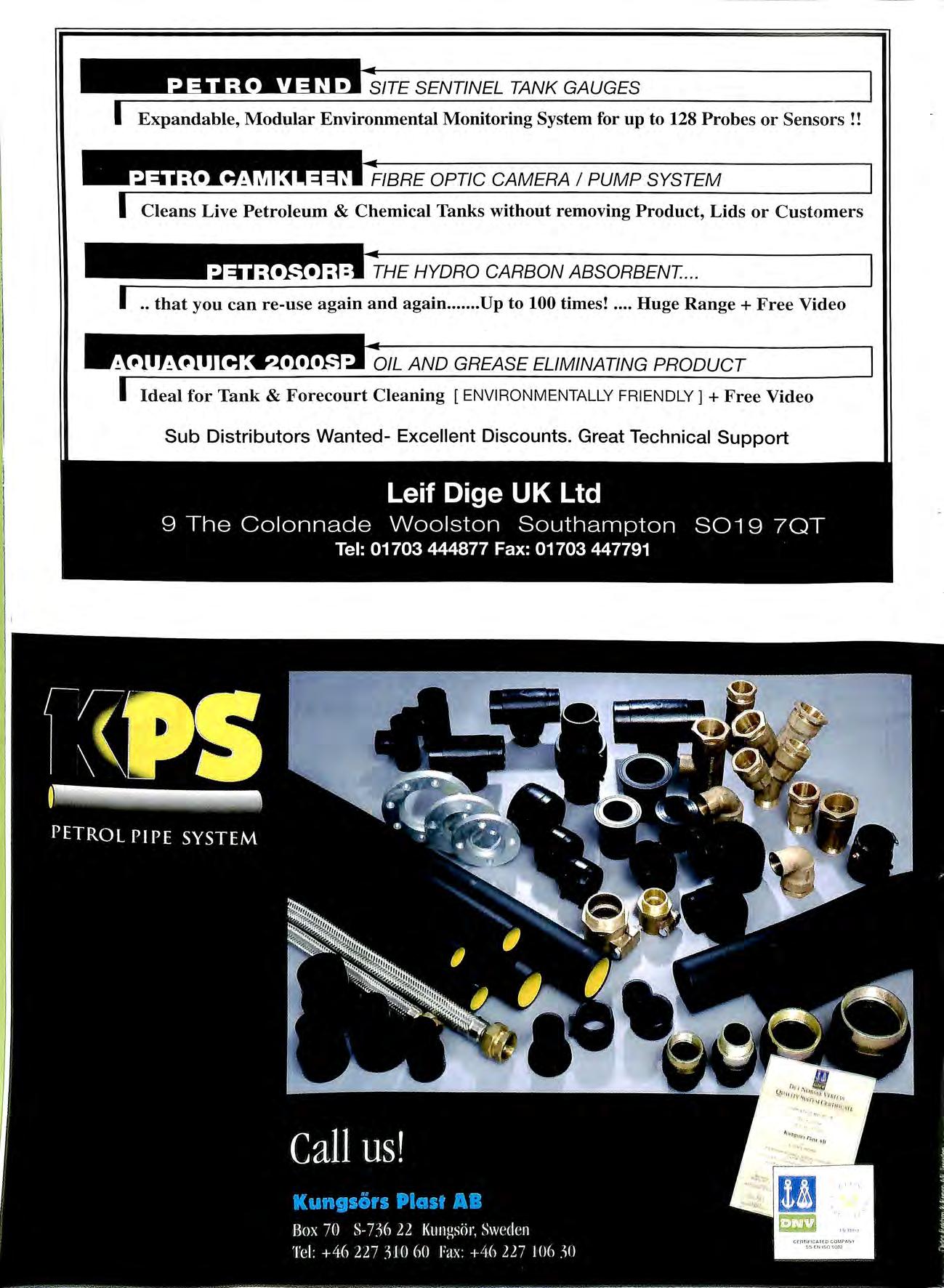
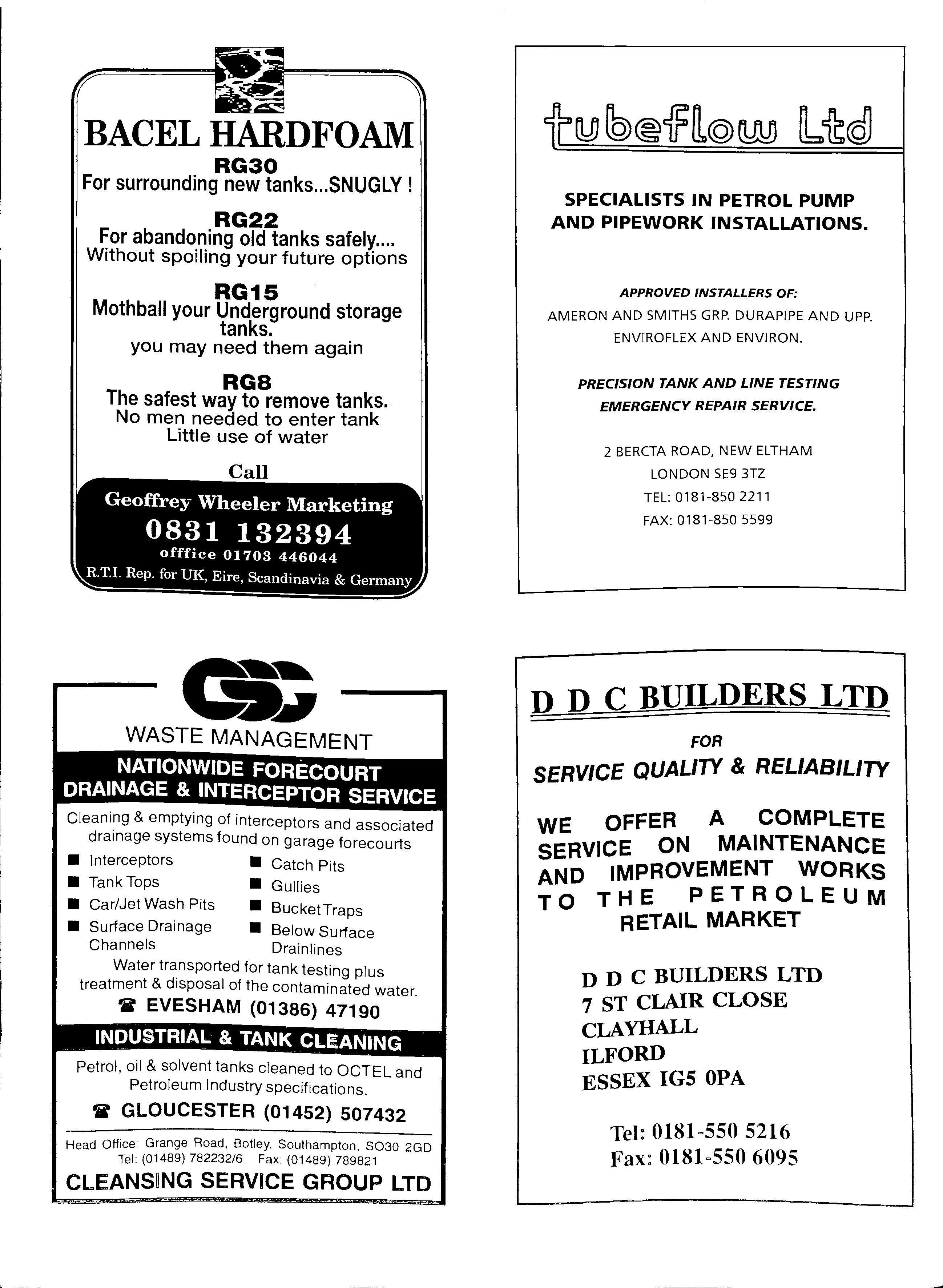
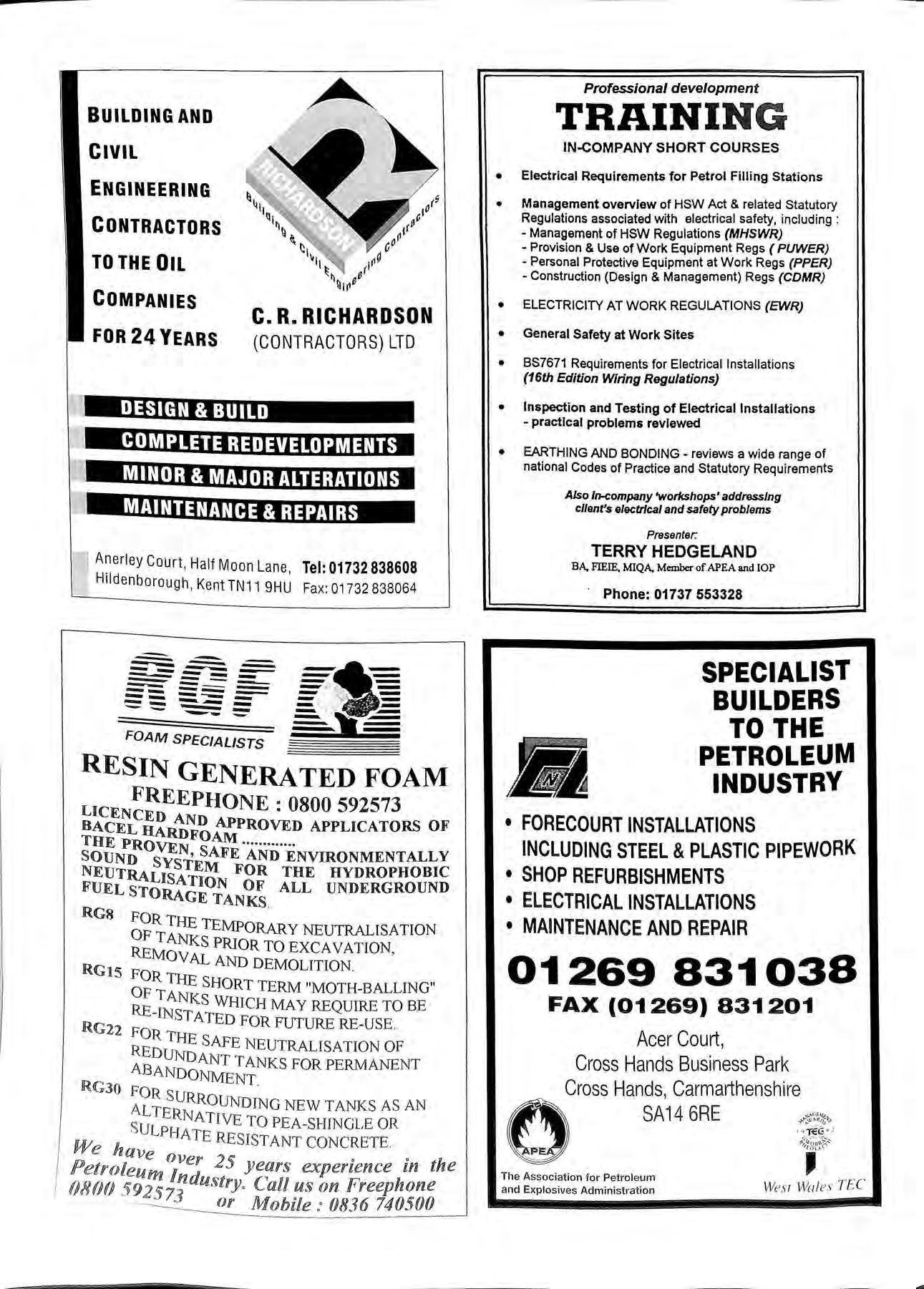
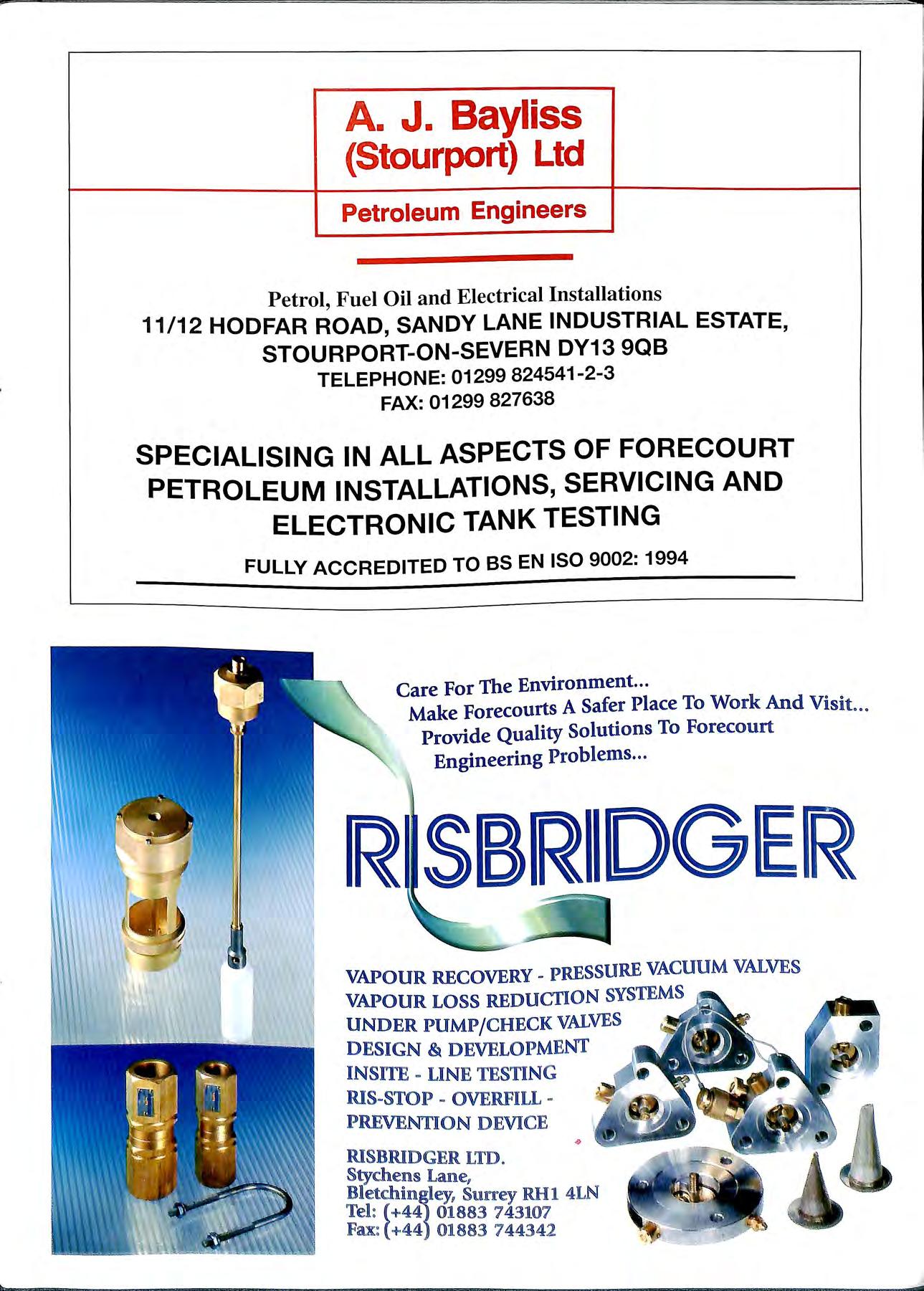

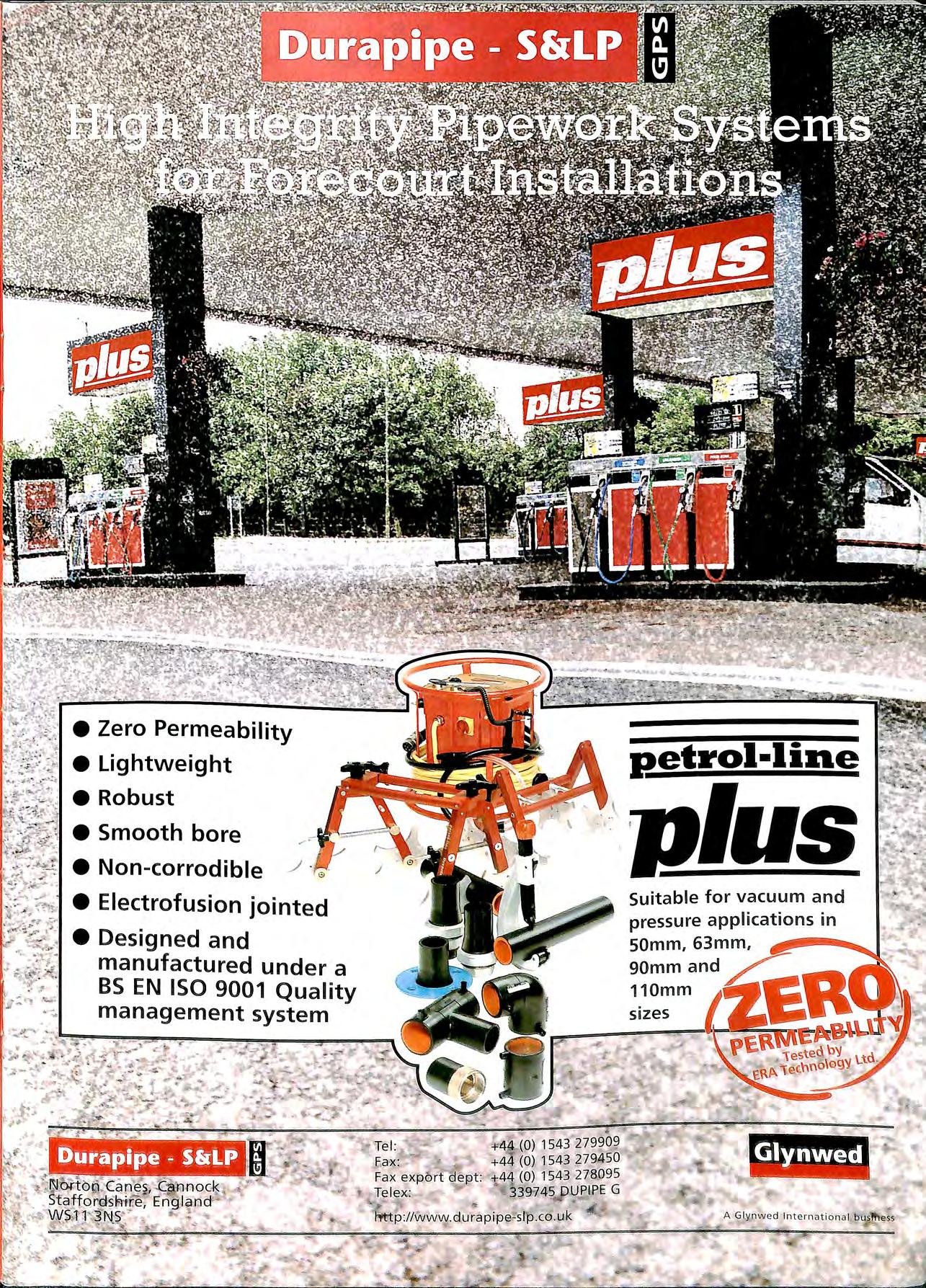
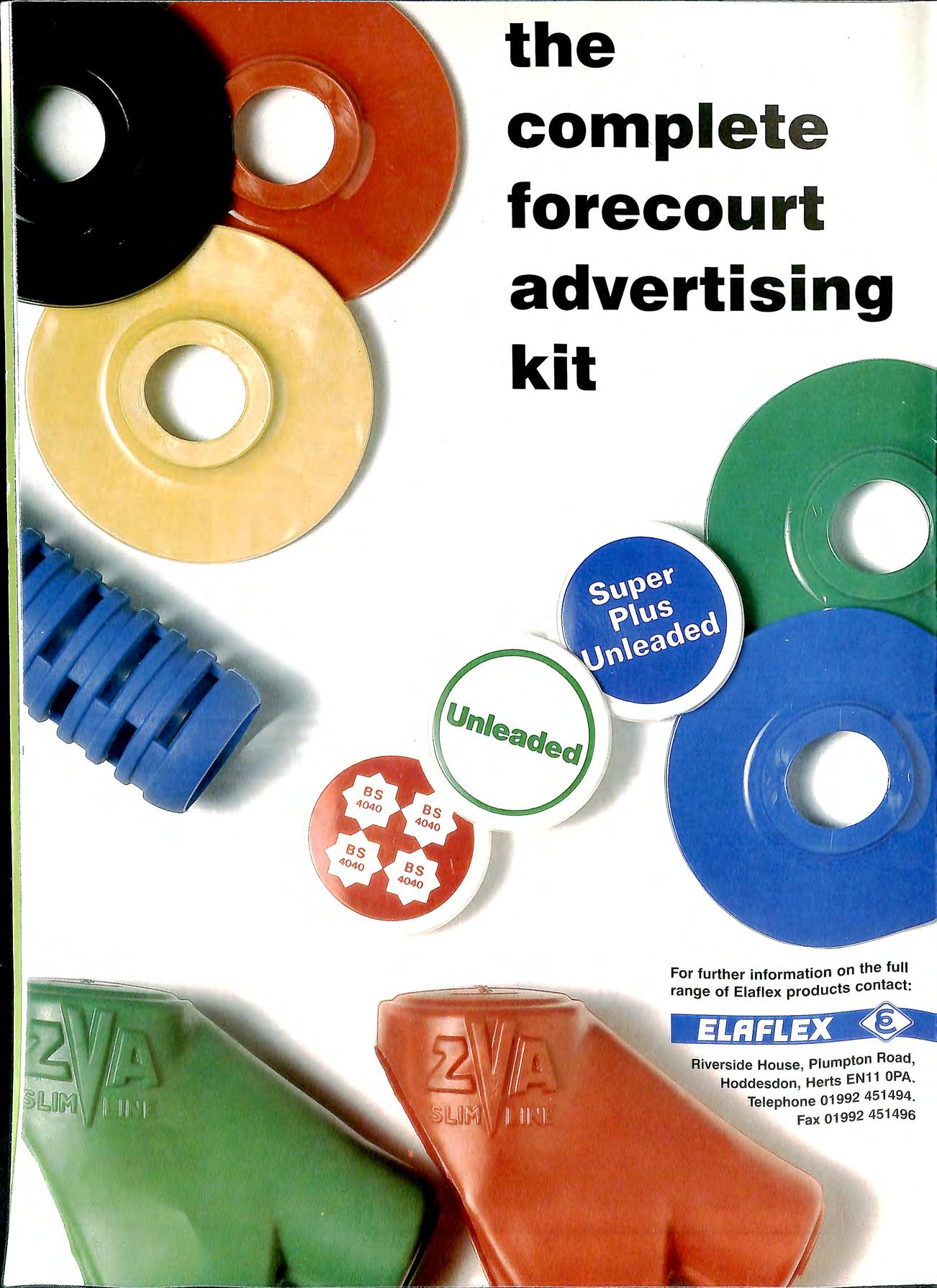

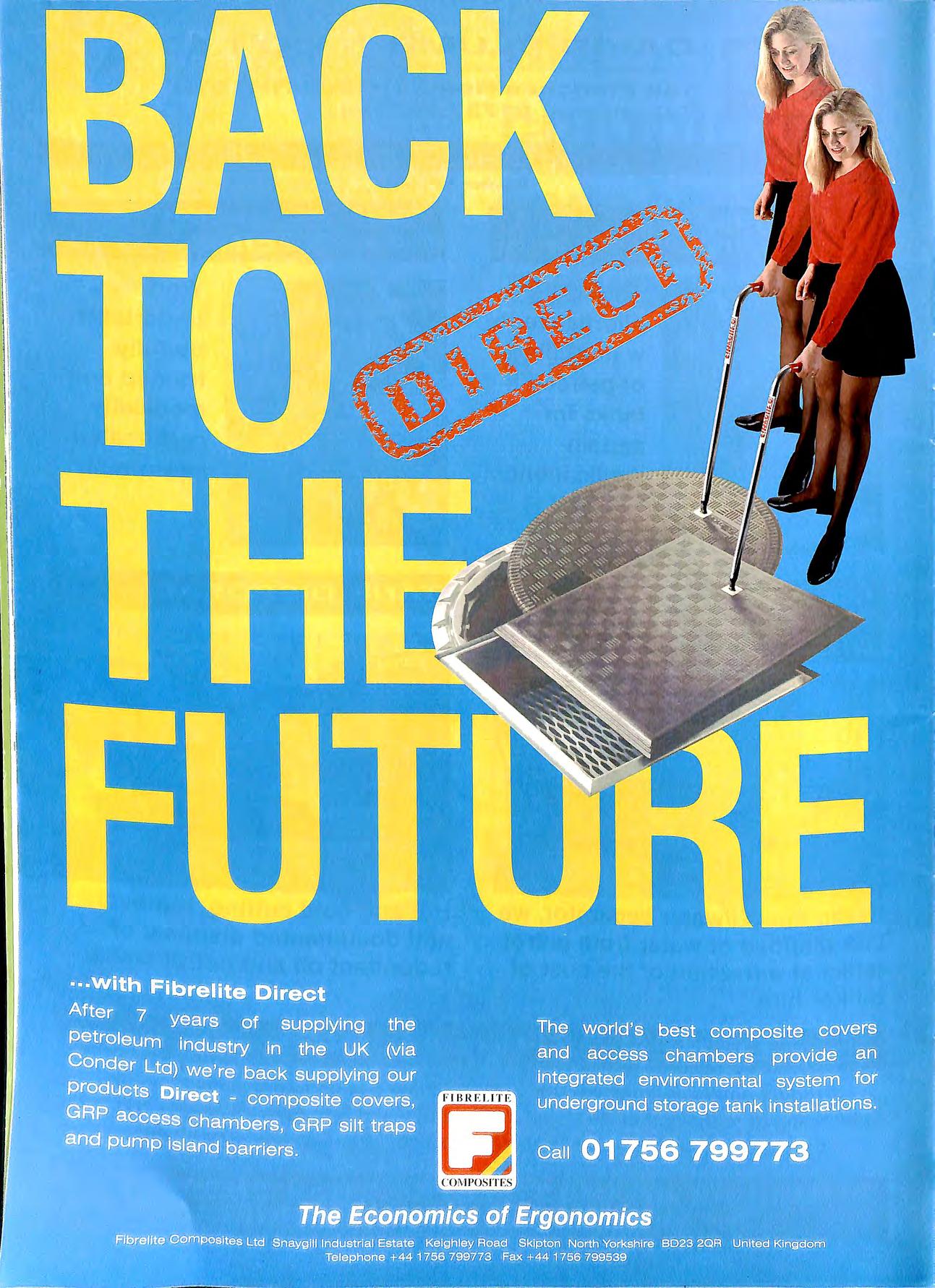
Often the area around a diesel dispenser is contaminated by diesel which has fallen onto the forecourt for one reason or the other. One of the main reasons is that motorists do not wait that extra second for the nozzle to drain before removing the spout from the car filler pipe.
The ZVA Slimline nozzle is now available with the New Drip Stop spout ER242. 1TMV. The patented magnetic closure inside the spout works after refuelling has finished . The Drip Stop operates in two ways. Firstly it closes to prevent diesel dripping when the spout is removed from filler pipe too quickly and secondly, it retains the remains left in the spout so that the next customer doesn't spill this diesel onto the forecourt when removing the nozzle from the dispenser
The Drip Stop functions. on the principle of a floating magn rather than a strong spring When the nozzle is not in use tH floating magnet holds the "valve" closed. Since the magnetic force is very small when compared with a spring the pressure loss is minimised in such a way that the pressure drop even at flow rates up to 501pmin is negligible. Also the innovative patented design allows for quick opening and slightly delayed closing , this prevents the ZVA Slimline from being placed in the dispenser holster with a full spout.
The well known ability of the ZVA Slimline "to the penny dispensing" is as sensitive as ever and is in no way compromised by this new designed spout. The new spout is also supplied as standard with Drip Catcher f itted.
How to order: Please contact our Sales Offi c e for further details .
This is the "silly season".
The front cover shows some of the bizarre things that can happen to petrol stations, which may not be picked up in a "risk assessment"!
The photograph shows a hot air balloon that landed on a petrol station in Bristol, the pilot who was taking 12 feepaying passengers on a flight in the area was running out of daylight and places to land and chose to crash land on the service station. He had apparently not considered the risk the propane burners could cause to the petrol station and a rather surprised occupier helped him and his passengers, who were unhurt, scramble from the balloon.
The Annual Conference and Exhibition will this year be held on the 10 and 11 November at the Metropole at Birmingham NEC.
The Conference will include presentations on new innovations in the future of petrol retailing and the programme will be sent out to members soon.
In addition to the Conference, free workshop sessions on vapour recovery at the service station will also be held on the first day.
For further information and a booking form contact Barbara Jacketts on 01473 828539.
Just as the Bulletin goes to press further reports of petrol leaks in Wales affecting members of the public reached the radio and TV news, making this the third major problem in 6 months.
In Conway a disused petrol station was brought back into use and petrol was found to have leaked from a storage tank on the site to affect houses and roads for a 200-metre distance from the service station. The main road to the holiday destinations of North Wales was closed due to the leak and diversions had to be put into place. Remedial action is taking place to recover over 9000 litres which is thought to have leaked from the tank.
The site owner is alleged to have opened the site without reference to the enforcing authority and to have operated it without a licence.
A supplier of a popular P& V valve, which has reported to fail on a number of occasions, has just issued a safety tice to the purchasers of the valve. It would appear from no . h d reliminary investigations that the valve seatmg as reacte f 0 the petrol vapour and has swelled up causing _the valve to jam solid. This is affecting the of the vapour balancing system and safety of the site.
Investigations into a number of other makes of P& V valves has revealed that many are not performing within the ranges recommended and in some springs corroded within a few months of fitting. The APEA is to have ·t. l)t1 the oerformance of these valves 111 the next repm s t . edition of the Bulletm.
At a site in London two mechanical OPD's failed to operate on two separate occasions to stop the overfilling of a storage tank when the operator made an error during delivery.
The valves were eventually replaced and although they have been returned to the manufacturer for checking so far · no explanation has been received about the cause of the failure.
The inability of operators to be able to check that OPD's installed inside the tank are operating correctly, could cause Oil Companies to move away from these to more reliable systems.
A fire occurred at an Asda hypermarket site in Bristol involving a lighting unit fitted in the canopy. The apparent cause was that the Mercury bulb fractured, allowing the igniter unit to drop onto the acrylic diffuser. The Igniter continued to flash, causing the acrylic diffuser to catch fire, which produced burning droplets of molten plastic to fall onto the forecourt around the pumps. Other bulbs were found to be defective on checking the remaining units.
A woman console operator collapsed after being overcome by petrol fumes at a Sainsbury's hypermarket in Suffolk. The operator who was taken top hospital was overcome by petrol fumes after they had entered the kiosk building via a sand filled electrical duct. Officers investigating the source of the fumes discovered that the installation was not leaking, but the petrol had been placed in the sub soil following a customer who had filled a diesel vehicle with petrol. The customer drove to the rear of the kiosk and drained the petrol/diesel mixture from his car and the resultant spill of around 40 litres soaked into the electrical duct and resulted in site closure until the cause had been established.
I00% explosive readings were taken in the ducts. hut was learnt from the incident. Sand filled ducts will not stop petrol vapour entering the building, the sand was removed from the elect1ical ducts and each pipe was correctly sealed with closed cell foam.
In California Mobil has been orc.kred to pay the Citv of $140.000 to rnver the cost of replacing ,part ot the City s water supply. Fuel leaking from a Mobil station allegedly contaminated the drinking 'Nater. Mobil
'j ! j ' i i.
has also been ordered to pay $20,000 per month until the contamination has been cleared up. It was alleged that the company knew about the losses from a franchisee-operated service station but did nothing to stop it. Mobil claimed that the gasoline in the groundwater had no connection with the MTBE contamination found in the City water supply.
At an Industry/Regulators meeting recently a debate commenced on th · h e ments of tank burial and the media that s ould be plac d d . . e aroun the tank. In lme with most current codes the regulat f ors were avounng pea shinale surround to ensure easier I o . remova of the tank. One oil company engmeer still stated his preference for the now outdated concrete surrou d b h b . n , ut w en asked how he would like to be uned when th f e 1me eventually came his preference for concrete disappeared!
A woman custo 11· L d mer ea mg at a filling station in south on on was sudden! · was d" h Y sprayed with petrol as some 60 litres isc arged from ,, b toward th k" a saie reak coupling. The woman ran s e 1osk and th called th F e operator cut off the pump supply, cove d .e Ire Brigade and Ambulance. The woman was re m petrol incl d" h f to h · 1 u mg er ace and eyes and was taken ospita where she received treatment.
The site had be the en redeveloped 9 months previously and pumps toaether w·th th from th 0 1 e couplings were new. Evidence e site operator w th h coup!· as at t ere was no pressure on the mg and the fail f" down t . ure at Irst mspection would seem a quaht7 problem, however the Oil company are ests earned out d break coup!" · an as a precaution all the swivel mgs were replaced.
The Elaflex cou 1· recently followin P mg had been redesigned the public had of failures where members of safety not· . n m.1ured. It was also the subject of a ice issued b th HS replacing un·t ·f· _Y e E, with the company 1 s o the failed 1· T · passed strin B coup mgs. he new design had · gent aseefa tests.
contractors up to ask them to deal with it and remove the sand. At some sites the solution was quite easy and a hose to the bottom of the tank was enough, however in one site in south east London the problem appear more severe with a larger amount of sand in the tank affecting the pump.
The petroleum inspector was contacted over the phone by an installation contractor with long experience in the field. He explained the problem and asked if they could remove the tank lid from the "live" tank (i.e. with petrol still inside) to put a hose down from a gully sucker and remove the offending sand and petrol.
This was refused and explained that the tank had to be made safe before such an operation could go ahead and also a method statement on the method agreed with the PLA before work commenced.
This advice was ignored, and within a few hours the Brigade were called to the service station to effect the rescue of a man collapsed inside a petrol tank.
The scenario pieced together after the event was as follows; the installation contractors subcontracted this part of the operation out to a company with a large gully cleaning tanker, the two contractors decided to remove the lid despite advice to the contrary. They also decided to go to the local hire shop and hire a compressor and face mask in order to enter the tank which contained about 300mm of super unleaded petrol across the bottom of the tank. No ladder or tackle and equipment or other protective clothing was used. The Contractor entered the tank complete with mask and used the suction pipe to start to remove the sand and petrol into the tanker. The compressor supply air to the operative in the tank suddenly stopped. The noise from the gully sucker drowned out this fact from the other contractor who was doing other work on the site. When he did notice the operative in the tank, he observed he had removed the mask and collapsed unconscious in the petrol. He immediately started the compressor again and entered the tank (again without assistance) placed the mask on his face and climbed back out and called the fire brigade.
The Brigade arrived and rescued the unconscious operative, this rescue was particularly difficult due to the entrance with Breathing Apparatus. When the operative was brought to the surface he suffered a fit and was taken to hospital by ambulance where he remained for 7 days. He suffered severe reaction to his face and torso and his respiratory system from being immersed in the petrol and breathing in the fumes for a prolonged period and was extremely fortunate to be alive.
The followin · ,. perhaps in . lg Incident occurred 111 London in 1996 and · 01 e l ian a th · . of thi!-. ind . ny mg pomts to the fact that sections ustry needs lo h . . . ensure lh·it k · impiove t e1r commumcat1on to < wor proced d ures an contractors are competent.
The major oil ·. company concerned had received a nurnhcr of reports th· · <1t s,md had madvertently heen delivered w11h 11etrol l . . . . 0 some service stations 111 the south t·;i-,1 111 hiohnd fhe ·r . · ,.. ' 01 company engmeers phoned
The HSE decided they had no jurisdiction in this case and the Local Borough responsible for this took no further action.
The Oil Company stated that the contractor who carried out the work signed a form some months before stating that they knew about all the company H&SW policy and would comply with it.
The contractors are still being used'
AT 14.00HRS - 15.30HRS
The Association is again pleased to announce that a free workshop on Vapour Recovery Systems at Petrol Filling Stations has been arranged for Monday, lOth November commencing at 14.00hrs.
The presentations will be by Mr. Peter Edgington (Consultant) and Mr. David Kerr (Engineering Manager Wayne Dresser). Subjects to be discussed are:- Design and Operation of Vapour Recovery Systems and Vapour Recovery at the Petrol Dispenser.
The session allows delegates attending to discuss and witness a live demonstration and will be of particular interest to regulators, engineers and site owners.
This free session is limited to 50 persons and is on a first-come first-served basis.
To reserve your place or places you should contact the APEA, PO Box 2, Hadleigh, Suffolk IP7 5SF. Tel: 01473 828539 or Fax: 01473 828538 by lst November 1997.
The Association is a non-commercial, non-profit making body which was formed at the beginning of 1991 and is a collection of UK established Forecourt System Support Companies.
These companies came together to achieve the following objectives:
• To provide a competent and support to the retail and commercial petroleum mdustry throughout the UK.
t dy common problems relating to Health and • To s u . .,... .d "f ., t Legislation and Environmental issues. io 1 ent1 y Sa1e y, · and agree solutions.
tabl ish and promote crood working practices and
• To es !" n1sed standards w1th111 the forecomt service and recog · installation industry.
• To liaise and cooperate with other organisations relevant to the industry as appropriate.
A Voice in the . , . . he Association 1s recogmsed by a numbe1 _ot . '. 'd als and oroanisations as able to present a case tor tndl VI U · c · standards of sate workmg. These 1m: Jude. common . d . · for Petroleum and Explosives A m1111sttat10n. Associatton . · · · CPL 706 Technical Committee: Health and Safety BSl Institute of Petroleum: LACOTS: Lncal Execuuve. · , · · · Oil Compa111es and Petroleum Ret<1tlt1s. Authonttes.
Petroleum Retailers Association; UKPIA
Membership applications will be considered from any company providing a related service in the retail and commercial petroleum industry.
For further details of membership please contact the Secretary on 01737 352766 to complete and forward an application form.
Milton Keynes Council has appointed an experienced former firefighter as its new Petroleum Officer.
Brian Baker has a wealth of experience, having served in both the Isle of Wight and Buckinghamshire Fire and Rescue Services, as well as a short spell with the Home Office. For the past five years he has been responsible for the successful privatisation of British Rail's Fire Safety Organisation.
Under recent local government re-organisation, Milton Keynes Council assumes full responsibility for petrol licensing on August lst. This entails full regulatory control on petrol filling stations and other that keep or store petroleum spirit. This was undertaken by Buckinghamshire Fire and Rescue Service.
Mr Baker said: "I look forward to the challenge ahead and followino in the very high standards and traditions set 0 by the Fire and Rescue Service over many years.
Graham Allsop, Milton Keynes Council's Chief Building Control Officer, added: "As regulations adapt to a changing environment with solutions becoming more complex, and continued technical development of the petroleum industry continues, it is essential that we keep pace and offer a professional and quality service to the people of Milton Keynes, as well as licensees who keep or serve petrol."
Technical enquiries may be referred direct to Brian Baker on O1908 252332. All administrative matters are dealt with by the Licensing Officer, on 01908 252363.
A waste management licence has been granted bv the Environment Agency to Norchem Environn1L'ntal Stanier Road. Shire Business Park. Warndon. to operate a special waste transfer station and oil reclamation facility.
The site is to be used to collect and bull-. up wastes into economically-viable loads for ultimate renwery or disposal. and to recycle wast\.' oil. consents have
already been granted by the County Council for these activities.
The purpose of the waste management licensing process is to ensure that waste management facilities do not cause pollution of the environment, harm to human health, or serious detriment to the amenities of the locality.
In accordance with statutory guidance, Norchem has submitted a working plan to the Agency. The plan consists of a written statement accompanied by drawings, specifications and procedures detailing the design of the site and how the site is to be managed and operated on a day-to-day basis. It also provides details of the provisions to deal with environmental monitoring.
An Agency spokesman said: "The working plan has been the subject of extensive discussions and negotiations with the Agency, and we are now satisfied that the necessary procedures are in place."
The working plan is approved and controlled by the waste management licence. Conditions in the waste management licence set performance standards to which the site must be operated.
The Agency will ensure that the conditions of the licence are complied with and that the objectives of licensing are achieved. This will be done by regularly inspecting the size and reviewing the licence from time to time to ensure that the conditions remain appropriate and effective.
The Agency operates a freephone emergency hotline number 0800 807060 which operates 24 hours, 365 days a year.
HECTRONIC the Swiss tank Gauge manufacturer has been granted a BASEEFA certificate for its OPTLEVEL system.
, The system is based around easy to install and mamtam probes, linked to a HECTOR dedicated box or to HECPLUS PC software. Links to other equipment is achieved through the use of an lFSF LON Interface.
For more i + · n1ormat1on contact Hectronic on 0041 5644 200 31.
The 47th annual convention of the Petroleum Equipment Institute IPEIJ will he held September 30-0ctobcr 2. 1997. at. the Minneapolis Convention Center. Minneapolis, Minnesota. PEI is the international trade association for d1-,trihutors. manufacturers and installers of equipment used
in petroleum marketing. Users of the equipment include service stations and convenience stores, terminals, bulk plants and airport refueling operations. Attendance is expected to exceed 4,500 delegates.
A major feature of the convention is the world's largest exposition of equipment used in petroleum marketing operations. The 693-booth trade show will open Tuesday, September 30, at 1.00 p.m. and will run through Thursday, October 2, at 1.30 p.m. The show will feature underground and aboveground storage tanks, dispensing equipment, leak detection equipment, meters, canopies, electronic controls and related equipment.
An industry luncheon will be held Tuesday, September 30, with Dr. Lowell Catlett, a professor at New Mexico State University, making a presentation on "Future Tech." The inspirational breakfast on Tuesday morning features Mr. W. Mitchell who will discuss his life's challenges after a motorcycle crash left him burned over 65 per cent of his body and an airplane crash left him unable to walk.
Nine education sessions will be presented during the convention. On Monday, two pre-Convex education sessions will be held. Brian T. Whitlock, an attorney and CPA, will speak on business succession; Rick Barrera will speak on the challenges of technology in the 21 st Century. Tuesday's sessions will focus on "Dealing With Difficult People," presented by Ben Bissell and "Customer Service The Competitive Edge" presented by Rick Barrera. Wednesday, Steve Epner will discuss "Vendor Managed Inventory" and Don Hutson will talk about "Hard-Hitting Sales Techniques." Steve Hartmann, of the Chicago law firm of Freeborn & Peters, will present a session both Tuesday and Wednesday on 'Ten Contract Clauses You Cannot Afford to Do Without." This session is geared toward distributors/contractors who will be using PEl's new standard form terms and conditions for agreements with customers. The speaker for Wednesday's general session will be Thomas J. Winninger, speaking on "Price Wars: How to Win the Battle for Your Customers." Bill R. White, 1997 PEI president, will open the session and preside over a short membership meeting immediately following the general session. A slate of new officers and board of directors will be inducted at the membership meeting. White is president of White's Pump Service & Supply Inc. in Lubbock, Texas.
Entertainment for the Wednesday dinner show will feature Michael Davis, comic juggler, and Ron Hawking, singer/impressionist.
The Petroleum Equipment Institute (PEI) has released PEI RP300-97 "Recommended Practices for Installation and Testing of Vapor Recovery Systems at Vehicle Fueling Sites." The 21-page manual is now available to companies interested in the preferred practices for the installation and testing of Stage I and Stage II vapor recovery systems. PEI
RP300-97, the only recommended practice available that details the correct installation procedures for installation and testing of Stage I and II vapor recovery systems, is a revision of the first document published by PEI in 1993.
The new edition reflects the recent revisions made by the California Air Resources Board (CARE), the leading agency in the nation regulating air quality. The bulk of the changes describe the steps and actual test procedures for static pressure decay, and blockage and dynamic backpressure tests outlined in Chapters 6, 7 and 8. Another significant change is the addition of a new test procedure regarding an air to liquid (AIL) volume ratio test in Chapter 9. Other changes in the document provide clarifications of portions of the original text, updated diagrams and new and expanded appendices to correlate with the information provided in the document. PEI RP300-97 is the consensus of the PEI Vapor Recovery Installation Committee, who solicited comments and suggested changes from PEI members, environmental officials, petroleum marketing associations, oil company engineers, and other parties interested in the topic .
The price of single copies of RP300-97 is $25.00 Standard postage and handling are included. For those ordering in quantities of eleven or more, discounts will apply. Call PEI at 918-494-9696 for discount rates. Payment must accompany all orders. Send payment to PEI, Publications Department, P.O. Box 2380, Tulsa, OK 741012380. PEI also accepts VISA and MASTERCARD. Orders paid for by credit card can be faxed to 918-491-9895.
Maximum fees payable to keep petroleum spirit
Item
Licence to keep petroleum spirit of a quantity: Not exceeding 2,500 litres
Exceeding 2,500 but not exceeding 50,000 litres Exceeding 50,000 litres
Transfer of licence
Previous Fee £28.55 per annum £42.15 per annum £83.00 per annum £7.00
New Fee £29.60 per annum £43.75 per annum £86.05 per annum £7.05
A major Oil Company had reported a safety problem tly dul·ina a delivery of petrol to a site fitted with a recen o vapour balancing system.
The incident occurred when a P&V valve stuck in the 1 d position , the pressure in the vapour recovery system c osed pi·oduct out of a below ground fill pipe from another force k W hich was almost full. tan
The company reproduced the incident during a t Oi led delivery in sirnilar circumstances . con r
There have been many reports in the industry of similar ·dents and of failure of P&V valves. There is evidence JI1CI that many do not conform to _the stated press ure or vacu um settings and the poor quality 1s contnbutmg to safety problems.
The industry needs to ensure that system s are prope rly . d c1nd qualit y equipment is in stalled to prev e nt de s1gne < d e t be ino di splaced. pro u 0
What happens on sites now?
With any movement or agitation of petrol; vapour is generated 'vapour growth'. This happens during a normal unloading of a road tanker to an underground storage tank every delivery and can be as much as 40% more than the volume delivered. This, of course depends on various factors length of pipe run, size , vapour pressure, temperature etc. but is always more than the volume delivered.
One of the causes or this 'vapour growth' is the air, trapped in the hose and pipework, between the tanker valve and the level of fuel in the underground tank. This air is purged through the bottom of the drop pipe which bubbles through the product causing turbulence of the petrol producing vapour growth.
The situation is made worse by the fact that in the normal configuration the vent is almost directly above this area and naturally the draw effect of the vent, or vapour recovery system, attracts this saturated vapour which is then either taken away by the road tanker or out to atmosphere .
The waves in the caused by the bubbles continue to create vapour after the tanker has gone and also disturb the stratified vapours in the tank.
The se waves also confuse the gauging system. At the moment the readout button is pressed the signal from the indicator may be sent from the trough or crest of the wave therefore not giving the true ' mean ' reading.
The nature of the turbulence when this volume of air is purged though the drop pipe is pos sibly a cau se for pipework, valves and joints, to eventually show problems e.g s pontaneou s operation of ovetfill valves, le a king joints, etc what else causes the se problem s?
For those of you who are familiar with s ubmerged pumping (P re ss ure) sys tem s there is a problem which sometimes o cc urs when the s urge of air around the drop pipe ca use s the se nsors on the s ub pump to close down the motor. In th e past the drop pipe ha s been mounted in a different position to th e pump normally the other end of th e tank. This add s co ns iderable extra ex pen se with manhol e c ha mb e rs etc
Now and aga in , particularly when delivering a sma ll load to an a lm ost full und ergro und tank there is not e no ug h he ad press ure in the tank e r to overco me the a ir trapped in th e p ipes a n a ir lo c k W hat doe s the driv e r do ? he may he te mpt e d to ' c ra c k · th e hos e conn ec tion at the ta nk er encl lo pe rmit th e trapp ed air lo bleed away a hazardou s o pe ra ti o n w h ic h is not pe rmitt ed by most o il compan ies. O r do e s he ' boun ce· th e air lo c k by ope nin g a nd c los in g the dc l1 ve ry va lvc '1 ag ain not to he rec omm e nd e d
One system which can provide a solution includes a perforated pipe complete with flame gauze, high flow pressure vacuum vent, scale filter and fixing kit.
The system addresses the cause of some vapour generation 'Prevention rather than Cure'.
The compressed air trapped in the system will take the 'path of least resistance' i.e. through the perforations and di ss ipate calmly into the Vent/ullage space. The instant there is liquid flow over the pe1forations the pressure changes to vacuum and this causes the closing of the check valve This check valve also serves to prevent any press urised vapour passing directly into the fill pipe and exposing the delivery driver to exposure.
In one of two ways. The easier way is to remov e the drop pipe drill 5 hole s fit the perforated pipe unit and replace the pipe. The other option, where the drop pipe is not removabl e, is to drill th e 5 ho le s in th e ta nk ris e r (after removing off site ) sc rew in the unit and th e n run pipin g to the ullag e (spa re port) or vent sys tem.
If the va lve should shut th e upper portion of the pipe w ill fill w ith liquid ln the pe rforated pipe is a ball w hi c h will fl oat o n the produ ct: until it re ac hes it s sea ling point and
th e n shu t off, thereby preventi ng the product pass in g throug h The unit is desi o ned to be h ioher in th e tank th a n b b co n ve ntio na l ove1fi ll va lves a nd wi ll therefore not inte r fere wit h the opera ti o n of th es e va lves
• B y re duci ng th e amo unt of va po ur, it w ill c o ntribute toward s the profitab ili ty of th e s ite. A n examp le of how mu c h is s how n in the ty p ic a l re port tha t ca n be prod uced for each s ite under c on s ide ration . Ea rl y tr ial re su lts indic a te a minim um of 0 .2 % improve m en t in lo sses .
• It wi ll speed up d e li ve ry. T he fu e l no lo nge r has to p ress uri se th e ai r and a liq ui d to li q ui d co n tact is a lmo st imm e d iate , th e refore improvin g flow .
• It wi ll e li m ina te a irl oc ks whi c h ca use de lays a nd poss ibl e ha zard s
• It wi ll re d uce th e s tres ses o n the inte rna l pipe wo rk
• lt w ill a ll ow fi ll pip es t b 1 d . b o e 1tte 1n the s am e c h a m e r as a s ub-pump and re du c e the ri s k of s hut off.
• It w ill m ak e ga uges se tt le qui c ke r.
• It w ill d is turb less sedim e nt in th e ta nk to b loc k fi lte rs.
• It will red uc e fo amin g thi s w ill a ll ow mo re of th e tank space to be uti lised before the foam (not the prod uc t) operates the ove1fi ll valve.
• It wi ll make any vapour recovery system m ore e ffi c ient. T here is less vapour ge nerate d re d uc ing the po ss ibi li ty of over pre ss ure vapo ur in the system e sc a ping to at mosphere afte r the tanke r has go ne
Perhap s th e sys te m may a llow an e xtra hose to be used for de live ry to a site that has a low ' H o se Certifi c ate' _ (a measure where eac h vapo ur reco very s ite h as to be ce r tifi e d as a 1, 2, or 3 hoses de liv e rin g s imulta neo us ly, de pe ndin o o n the efficien cy of the syste m ). 0
Eac h system is suppl ied with a de ad w e ig ht pres s ure vac uum ve nt to e nsure lo ng te rm re liabi lit y an d fo r f utu re integ r it y tes ts. A lso in c lud e d is a sca le fi lte r to protec t th e PVV sea ling fac e fro m pipe de bri s.
T hi s ' Va po ur Redu c tio n S yste m ' sho u ld no t be c o nfu se d w ith e ithe r th e ' diffu s io n · me thod of c a lm ing w he re a ll o f th e trapp ed of air is bubb led th o ug h s m a lle r ho les m the vapo ur re te ntio n· syste ms w hi c h co mpres ses as mu c h va po ur as possib le w it h in th e limit s se t fo r a ll o the r press ure vac uum ve nt s.
N B. lt sho uld a lso be m ade c le ar th a t thi s w ill no t ne ga te the need fo r Stage I B (Vap o ur Ba la nc in g ) u n s ites that need to co mp ly.
In 1996 German officials asked me if we had experienced any problems in the UK from fires occurring while refuelling on petrol stations, apart from the isolated incident which was normally explained, I was unable to report any widespread problem. The Germans had though experienced something quite different, and during the period mid 1992 to 1995, officials had notified them of 36 fires during refuelling operations. Investigation into the cause of these incidents revealed that in the majority of the cases static electricity was the source of ignition, and I read their report with interest.
In the first 6 months of 1997 a small number of fires have occurred at petrol filling station in the UK while vehicles have been refuelling. Although these occurrences may have seemed to be isolated incidents, when taken in context with other incidents across Europe we seem to have ?ad a "mini epidemic" which appears to have caught the industry by surprise.
A refuelling fire at one site in the UK resulted in the car being completely burnt out; two others in Ireland resulted in an attendant dramatically being engulfed in flames. This would seem nothing to the repo1ts I have seen that up to 100 such fires had been reported in France involving at least 5 cars completely burnt out during March of this year. Some of these incidents occurred at the same sites, when an exceptionally dry spell was experienced, (ideal static generating conditions) there were no incidents reported in April during the rainy month.
In Germany research into these incidents came to the conclusion that static electricity was the cause of 31 of their 36 fires.
The research highlighted a number of findings.
• Today many car-refuelling inlets are constructed using non-conductive )· · Th' · P <1st1cs. 1s prevents the earthrng of the vehicle via th · d . . e 111serte filling nozzles and the electrically co d . · n uct1ve pump hose unless other measures are taken.
• Increasingly car tyres are made of a non-conductive mater··1r··1·., · ia SI ICdJ to 111crease tyre wear.
• This is often made worse by a non-conductive paved l<>recourl .surface.
• Since the fuel is electrostatically charged while running lhrnugh pipes and hoses. the entire vehicle can receive a d1;111u· ol several thousand volts during refuelling.
• In addition it is possible that a highly insulated vehicle has already received a charge from the application of the brakes, before the actual refuelling process begins.
• When parts of the body are approached by a conductive body such as the filling nozzle or the person who is refuelling the vehicle, spark discharges will occur which are capable of igniting the explosive mixture formed by the displaced fuel vapours.
• Even if the car body is earthed, electrically insulated conductors may present an ignition hazard when they are charged by electrostatic induction or contact and when their electrical capacity is sufficient to produce an incendiary spark. A metal ring fastener for the filler cap, fitted to the insulated tank inlet pipe is such an electrically insulated conductor, unless a discharge path to the car body is provided.
• During refuelling, the interior surface of the nonconductive inlet tube can be charged by flowing fuel to such an extent that brush discharges may occur at the metal filling nozzle. Model experiments indicated that these discharges could be incendiary for fuel air mixtures. However it has been proved that ignition hazards do not exist since the petrol air mixture in the tank inlet tube cannot be ignited by brush discharges even in the case of stage 2 vapour recovery systems.
• When persons leave their vehicle seats, they can become electrostatically charged and remain charged for some time. Electrical discharge by individuals in proximity to escaping fuel vapour can create a hazard.
The following measures can be taken by the Oil Industry:
The conductivity of the fuel is an important factor and I understand can differ considerably per load, although many of the accidents have occurred using super unleaded I am informed this is likely to be more conductive than the other fuels.
The paved surface of the refuelling areas should be capable of discharging any static huild up to earth, therefore it is essential that paved slllfaces at filling stations are conductive.
Experiments showed that paved surfaces with a resistance of 10 11!1 allows 2000 volts to exist for SL'veral minutes.
Experience and measurement has demonstrated that concrete surfaces are adequately conductive.
Asphalt surfaces are however not likely to be conductive
Block paving on a sand bed will differ according to the state of the sand (wet or dry) and any sealant placed on the surface, but the resistance can be measured.
• The leakage resistance of the paved surfaces by the dispensers should not exceed 10-sD.
The Dispenser and hose should be constructed to the appropriate standards and the case of the hose the electrical resistance should be between 10-30/m to 10-sD/m
These should be checked regularly.
Do not introduce extraneous items on the nozzle that are not proven to be conductive, i.e. nozzle adverts, splashguards.
Perhaps the vehicle manufacturer can make the most influential safeguards.
• Suffic iently conductive connection of the fillino nozzle b support in the tank inlet to the car body.
• Provide bonding of all conductive parts in the area of the tank inlet tube to the car body
• Supply conductive tyres to cars.
• Avoidance of charging persons by having anti-static car seats.
As a result of the tests in Germany the General Motors Opel Kadett also sold as the Vauxhall Astra model was found to have no bonding of the metal parts inside the plastic fuel filler area. This was subject to a safety recall in Germany and the appropriate bonding was provided. It is interesting to note however the majority of the cars involved in fires in France were the Opel Kadett or the older Peugeot 205 models, and in the UK the burnt out car was a Vauxhall Astra.
To put this problem into perspective we should remember that millions of refuelling transactions that take place each day safely in Europe. These accidents are very small percentages that appear to have increased due to the favourable dry climatic conditions and a se1ies of other factors. Luckily so far the injuries have been slight but we should heed the conclusions of the research and work towards safer refuelling .
I recently had a letter published in Environmental Health News (Vol 12, No 22) in which I sought expressions of interest in my suggestion for a network of EHOs involved in petroleum licensing. Unfortunately, my original letter, in the interests of brevity at the time, did not contain my full thoughts on the matter which may have led to the subsequent letters from both Andy Berry on behalf of the APEA and Alison Edwards of LACOTS in EH News, Volume 12, No 24. I fully agree with both of these letters and appreciate the work done by both of these organisations. I am, in fact, a member of the APEA and I am very grateful to a number of local APEA members who have given me much advice and assistance.
EHOs are inevitably going to become more involved with petroleum and petroleum products in the next few years; the implementation by Local Authorities of stage l bv vapour recovery will be starting this Autumn, petroleum is a common land contaminant and, although there is not yet any firm guidance or timescale, it will be an issue in relation to Part II of the Environment Act 1995. Also, the current proposals for altering the petroleum licensing regime will make EHOs responsible for the Health and Safety aspects of petroleum storage in premises such as distribution depots, tool hire centres, and DIY stores. Furthermore, the whole issue could be confused by the introduction of alternative fuels such as CNG and alcohol derivatives.
My concerns are firstly that there is a potential conflict between the safety side of petroleum licensing and the environmental issues of land contamination and atmospheric hydrocarbon discharges mentioned above. Secondly, with the potential deregulation of petroleum storage, this will introduce a new area of enforcement to many EHOs who will have no previous experience of the product. Here, there is a potential for lack of knowledge to much of the good work that has been done by hcensmg authorities in the past. Certainly, there will be a for information etc to be made more widely available withm my profession. Thirdly, as far as I am aware, the CIEH not, as a body, been involved in the past in c_onsultat1ons about petroleum matters. Although new to the the greater involvement of EHOs in dealing with a vanety of petroleum issues will give the CIEH a need to be able comment on the subject. In this regard, the proposal by Alison Edwards of LACOTS to invite the CIEH and REHIS to nominate representatives to the Petroleum Working Group is most welcome.
At the present moment in time. those EHOs like myself who have p · ·L·1· · t" espons1u1 1t1es or both the licensing and environmental aspects of petroleum are perhaps uniquely placed to act as an interface between the two fields during the impending changes that I mention above. Here we have lhi· potential. perhaps hy· being more able than other 'lr·,crplr 11 "" tlia! d<• IH1I lrnvt• •)llf c'f1V/i"ll!li1it'11IHI h;wk!!i"lilrild '" '-'''' holh sides ol aJJ i-."ut: aud Lllw. Lo achieve a helter '' '· 11'1 ''' -.1.111danl lii;in 1·iflwr <'f)1ild ir1 isol;11ion Wl· ;m· ;dso
a potential resource to advise our officers and representatives within the CIEH and to disseminate information to those of our colleagues for whom petroleum will be a new subject.
For these reasons I thought that it would be a good idea to make contact with other EHOs involved in petroleum licensing and for us to be aware of one another in the form of a list of names. Also that the CIEH should be aware of those of us in this situation to act as an infonnation resource around the subject. It is certainly not my intention to start any form of new organisation; rather I would hope that we could act as a useful contributor within our field to the considerations and work of organisations such as LACOTS and the APEA.
In hope that the above comments have clarified my intentions and I would apologise for not making these clearer at the outset. Finally I would like to thank all those people who have taken an interest in my original letter.
It occurred to me recently that some agencies enforcing petroleum and explosives legislation may not be aware of the availability of centrally stored details on historic prosecutions carried out by the Trading Standards Service.
To assist local enforcement officers with the collation of current information on actual or prospective defendants, it has been the practice for many years to use the good facilities of the Office of Fair Trading. Prior to legal proceeding being instituted and also at the conclusion of any proceedings, officers make written contact on standardised documentation.
On first contact the Office of Fair Trading provide by return all details covering previous convictions as reported by enforcement agencies throughout the country. These are not certified extracts from court records but are sufficient to approach a defendant for acceptance/agreement prior to any court hearing. This saves considerable time when dealing with national companies with extensive histories. Following prosecution a 'return of legal proceedings' form is completed by the enforcement agency concerned and lodged with the registry for dissemination as described above. To retain the fullest and clearest details of prosecution results around the country I would hope that the lodging of all such material be continued by existing agencies and taken up by new agencies.
Further information is obtainable directly from: Central Register of Convictions, Consumer Credit Licensing Bureau. Office of Fair Trading, Craven House. 40 Uxbridge Road. Ealing, I .ondon W1 2BS
Yours sincerely I·· Oliver Ki11gsto11
The first case involved the allegation of keeping explosives (fireworks) in an unauthorised place contrary to Section 5 of the Explosives Act 1875.
As a result of information received the police visited a dwelling house in the suburbs of Wakefield on 25 October 1996. On entering the property their attention was drawn to a collection of merchandise in the kitchen including 40 x selection boxes of fireworks. The fireworks and other assorted articles were seized by the police along with a "Fireworks For Sale Here" notice that was prominently displayed in the kitchen window facing the footpath and adjacent school playing fields.
The occupant was arrested and interviewed at the local police station in respect of selling fireworks from unregistered premises and other matters. The fireworks allegation was refuted by the interviewee who claimed he had bought them for his family and friends.
It was only when the police were deciding on the appropriate charge that they realised it was the West Yorkshire Fire Service who enforced the Registration and Licensing provisions of the Explosives Act.
Following discussions between the police and the Brigade Explosives Officer (EO) it was agreed there was a prima facie case to answer and that the fire service would continue the investigation with a view to prosecuting the offender.
The seized fireworks, interview tapes, transcripts and police statements were handed to the Brigade (EO).
Further enquiries made by the EO revealed that the person being investigated had received a delivery of some 98 selection boxes of fireworks from a legitimate dealer. on or about 17 October 1996.
With no record of the premises having been Registered with the Fire Service, a charge of ''Keeping fireworks for the purpose of sale at a place not authorised for the keeping of explosives contrary to Section 5 of the Explosives Act 1875" was made against the occupier of 2 Milton Road. Lupset.
The defendant pleaded guilty before the Wakefield Magistrates on 2 May I997 and was fined £200 with £ IOO custs heing awarded '"the Fin' Authu1·ity.
A Deprivation Order applied for by the Fire Authority under Section 43 of the Criminal Courts Act 1973 was also granted by the Magistrates depriving the defendant of £321 worth of seized fireworks.
The second case resulted from a complaint made to the Fire Service by the driver of a car which caught fire on a forecourt of the Save Service Station at Castleford on 16 October 1996.
The complainant and one of his passengers made statements saying that when the engine compartment of the car suddenly burst into flames as it was about to be refuelled, the sole attendant on duty failed to offer any assistance whatsoever in dealing with the incident.
When they asked for a fire extinguisher (none were visible at the time) the attendant offered them a bucket of sand which proved ineffective when the sand was thr?wn into the encrine compartment. The attendant, who remamed at the directed the complainants to a water tap the side of the sales building when they repeated their request for a fire extinguisher.
Of their volition and without any assistance from the attendant, the driver and his two passengers the burning car to the edge of the forecourt the quickly developing fire would not endanger the dispensers or property.
After moving the Metro car, the driver and one of the passengers returned to the sales to that the attendant had telephoned for the Fll"e Bngade. To the driver's annoyance. the attendant hadn't even summoned the Fire Brigade. The driver in his statement claimed that it was only at this point in time when he shouted instructions to the attendant that he witnessed the 999 call being made 1
The complaint. investigated by a Petroleum Officer (PO). centred on the site operators competency and the devolved method or site operation. The attendant on duty at the time of the incident was one of the two joint operators of the site who had taken over the tenancy on 20 Septl'mlwr 1tl'lh. sn1m· 21' brr11n' tlw im idn11
Interviews under caution were conducted with the joint operators and the area manager re_s?onsible for induction and on-going training. In add1t1on the PO used his powers under Section 20(2)(j) of the and Safe_ty_ at Work etc Act 19742 to require the production of trammg policies and programmes from the licensee, Save Service Stations Ltd
The investigation culminated in Save Service Stations Ltd being charged with "failing to ensure that the premises were properly supervised at all times when in operation couttary to Part V(25a) of the Licensing Conditions (Section 1(3) of the Petroleum Consolidation Act 1928).
At a recent APEA Training Course the following statement was made:-
'Fireman's switches on a considerable number of petrol stations (usually privately owned) operate in a manner that when the fireman's switch is turned off, this cuts the supply the the hazardous area equipment, but on switching the fireman's switch on again, it immediately re-energises the relevant circuits'.
The usual and accepted manner of operation is that once the fireman's or emergency push button switch has been operated to isolate the supply to the hazardous area, it can only be re-energised when the area is declared safe, by operating a reset button within the console/shop area This operation being carried out by a competent person, duty holder, etc.
HS(G )4 I although not retrospective is the current and only official s peciali sed guidance document. It states the above s tandard s on page 46 para 21 O, ' Emergency switching'.
The Health and Safety at Work Act, Electricity at Work R eg ulation s 1989 , are th e law of the land. These state:-
Means of cutting off the supply and for isolation
(I) S ubj ect to parag raph (3). ( P e rson s on whom duties are imp ose d etc.)
Where necessa ry to preve nt danger s uit a ble m ea ns shal I be ava il ab le :
(a) c ut tin g off th e s upply of electrical energy to any elec trical eq uipm en t a nd
(b) th e iso lation of a ny e lec tri ca l equipment.
12 J In para ( I ) iso lation, me ans the disconnection a nd se paration of e lectr ic al equipment from every so urce of e lec tr ica l e ne rgy i111 suc h a way that this disnnmection and sepaI"ation is secure. (eveI"y : 111 er 111 1!he11eu1 rol umdu!'/or lo he include d)
WestFurthermore Regulation 13 states:Precautions for work on equipment made dead.
Adequate precautions shall be taken to prevent electrical equipment, which has been made dead in order to prevent danger while work is carried out on or near that equipment, from becoming electrically charged dunng that work if danger may thereby arise.
The design for emergency switches, fireman ' s switch_es, applied to the hazardous area, are such that their operation is in a series electrical configuration. This means that the emergency switch when operated will ' drop out ' (a latching circuit) , an electrical solenoid operated contactor, cuttmg off all power to the relevant area and thu s isolating all conductors. To re-e stabli s h power, following the re set:t mg of the fireman's s witch( s) or emergency button to the 'on ' position , a specially marked , internally located manual button ha s to be depre ssed to re -e nergise and ' latch in ' the co ntactor thu s re-energising the ha zardous area equipment.
Please not e: Thi s doe s not see m to apply to ' high voltage sig nag e isol ating fireman 's sw itc he s'.
The interpretation , res pon s ibility a nd e nforce me nt is the duty of the Trading Stan dar ds/P etro le um Offi ce r. Co mp ete nt e lect ri ca l tes tin g s ho uld revea l any d efec ts.
The defendant pleaded guilty at the Pontefract Magistrates Court on 12 May 1997 when the Magistra_tes imposed a fine of £2,500 with £1,056.51 costs bemg awarded to the Fire Authority. 1 w·lh 11 ggg calls to Fire Service Control being automatically tape recorded: the li stened to foaur emergency calls made. Only one call was received from the filling station thereby supporting the complainant's statemenL The advantages and mclhod of using Section 20 (2)(j) powers is also referred to in an article published the May 1994 edition of the Bulletin. Roger Marris Yorkshire Fire and Civil Defence AuthontyIn many countries around the world submersible pumps have become the primary means of pumping motor fuels at retail service stations. This is the case in the United States, Canada, Mexico, Central and South America and many parts of Africa and Asia. Many countries in Europe are now changing to this system and seeing the benefits.
Submerged Turbine Pumps are installed directly in the underground storage tank. The pump intake is set a few inches off the tank bottom. The pump itself is a centrifugal type which pressmizes the fuel inside the pump motor, which then pushes the fuel under pressure through the piping system of the station to the dispenser. By contrast, as most readers are aware, suction pumps are located inside the dispenser cabinet. They are generally rotary vane pumps and operate on the principal of reducing atmospheric pressure at the pump inlet, allowing atmospheric pressure, acting on the surface of the fuel in the underground tank, to push the product from the tank into the dispenser pump, where it is pressurized and pushed through the meter.
The reasons for changing from suction technology to submersible technology are based on three situations:
1.
2.
3.
Petroleum fuel can vapourise when pulled from the underground storage tank with use of a suction pump. When the fuel converts from liquid to vapour, the suction pump severely slows down or stops pumping completely. Yapourizing occurs when the suction required to lift the fuel up to the suction pump exceeds the vapour pressure of the fuel being pumped. This situation is affected by various factors. The fuel type and octane rating will have an impact on this situation. Unleaded fuels , particularly premium grade fuels have higher vapour pressures than leaded fuels. Put simply unleaded fuels vapourize easier than leaded fuels. The higher the fuel octane rating the higher th e vapour pressure and therefore the easier it is to vapouri ze. Temperature is another factor that will influence cavitation. The higher the temperature the more likely fuel is to vapourize. This explains why cav itation is mo st preval e nt during the hot s ummer months and why some serv ice station s have had problems pumping during the rece nt hot summers , ex pe ri e nced in ma ny European co untri es The us e of s ubm e rs ibl e pump s complete ly e liminates th e probl e ms of cav itation
Cavitation or "vapour lock"
Worldwide trends in station design
Availability of secondary containment and leak detection technologies
Another factor to consider is the service station elevation above sea levels, the higher the elevation the easier the fuel vaporizes.
The worldwide trend in station design is that the total number of service stations is decreasing each year. The total number of automobiles is increasing and the total number of litres of fuel consumed each year is increasing. This means there are fewer services stations pumping more fuel. In order for this to be possible the trend has been to build larger more efficient service stations and these favour the use of submersible pumps. Submersible pumps do not have the physical limitations that are associated with suction pumps. Flexibility in station layout is dramatically improved when using pressure systems. Length of lines, tank diameter and bury depth, placement of dispensers and tanks and overall design are not significant factors when submersibles are used.
It is also important to recognise that the removal of pumping units, motors and drive systems and air separation equipment from each dispenser, provides potential to reduce the size of dispensers when using submersibles. It can increase design flexibility and reduce overall cost of ownership of the total site.
When submersible pumps were first introduced thirtyf1_ve years ago there was concern about pressurizing the fuel at the service station. Since then there has been much innovation in secondary containment and leak detection. Due to the availability of these technologies, if a leak was to occur it would be contained in the interstitial space of the double wall pipes or double wall tank and would be detected by either mechanical or electronic leak sensors. The. P?pularity of this technology is such that it is begm111n° to be u · d · · · "' se m service stations that use suction pumps as well.
The first significant advancement in submersible pump technology has recently been introduced by FE Petro The 0 ST) I t 11' s · . . ·. n e 1gent ubmers1ble Turbme and the (VL) Yai l<tble Length submersible turbine.
The UST) Intelligent Submersible Turbine is a vanable speed . b 'bi · su mers1 e pump that is capable of ma111ta1nmg a con ·t· t 1·1 . s an ow rate from each nozzle, up to a total of eight n 1 ozz es operatmg simultaneously. With a st.mdard lixed . d b , spee su mers1ble pump, the flow rates ieduce as e· h dd' , · ac a 1t1onal nozzle is opened. When the service station · · . t · · k b · · is a 11 s pea usmess hours customers need to he a?Ie to move through the site as fast as possible. This ts precisely wh h · ·. en t e service station requires its bet flow and is what the IST delivers. The is the pe1 feet suhmers1ble for busy stations.
The (VFC) Variable Frequency Controller which controls the IST, monitors the pumping demand at the station and responds by increasing or decreasing the RPM of the pump motor. This maintains a constant flow for up to eight nozzles at a predetermined flow rate set at installation. The faster one can move customers through the service station the more customers they can service on a daily basis. The IST allows service stations to simply sell more fuel per hour than they could with a standard submersible pump. The VFC also has built in 'intelligence' that includes Dry Running Protection. If the tank runs dry the VFC will turn the pump off immediately, resulting in less bearing wear in the pump motor.
This intelligence also gives protection against low voltage, open and short circuit, in fact up to seven different conditions.
The (VL) Variable Length Submersible permits one model of pump to be stocked to cover over 94% of installations. The length of any submersible pump is dependent on the specifications at each service station installation. This includes the diameter of the tank, the style of tank, the bury depth of the tank, and what kind of containment technology is used. Many times when nonvariable length STP's arrive at the job site they must be altered in length to fit correctly, when this occurs there is a delay in the installation, a cost to cut and re-thread the piping, a cost to re-assemble the STP, and the STP must be returned to the approved assembly plant and be re-tested to factory specifications. The (VL) Variable Length turbine is shipped fully assembled from the factory. When it arrives at the installation site the length can be adjusted to fit each specific installation. The length can be adjusted to fit the exact tank diameter, bury depth and containment sump for a perfect fit.
The (VL) Variable Length submersible greatly simplifies installation requirements.
The scene is set for further developments in the field of Submersible Pump technology, and while submersible vs. suction remains a consideration for companies today, increasingly the move is towards Submerged Turbine Pump installations.
LEAK DETECTION SYSTEMS FOR DOUBLE SKIN TANKS.
LEAK DETECTION SYSTEMS FOR DOUBLE CONTAINMENT PIPES AND DISPENSER SUMPS.
TYPE 2000 INTELLIGENT TANK CONTENTS GAUGING SYSTEM.
INTERCEPTOR LEVEL ALARMS.
*BS 5750 Part 1 quality assurance.
*All systems meet relevant safety standards (EEx ia /JC for zone 0 & EEx ib /IC for Zones 1 or 2).
*Systems approved by LFCDA.
TALK TO THE EXPERTS on: 0342-323641 Fax: 0342-315513
Northern Sales: Tel & Fax: 0706-3706g 5
I
In the current economic climate only the strongest will survive.
Some businesses that are trading successfully today may not be around tomorrow. That's so often the case nowadays with technology, or indeed, manufacturers
Not with Veeder-Root.
Our tank gauging and environmental s ystems are entirely future proof.
The reason? By designing a unique modular system, we can upgrade your equipment quickly and easily whenever you choose to enhance your syst em.
Which i s ju st as well. Because our
on-going investment in the future means we are continually developing new ways in which our tank gauges and leak detection systems can be used to help you run your business
It's no real surprise that more than 250,000 underground tanks around the world already have our systems in place.
But it's not only our technology which is future proof, so is Veeder-Root. We have the resources to support you and your investment, both now, and into the future.
Veeder-Root. The secure way to gear up for your future
An addition to our extensive list of products, is the facility to manufacture a wide range of engraved signs for many Industries. With our computer controlled machines, including CAD facilities you can now order your signs with the rest of your material.
Polyethylene: Tank Chambers and Dispenser Sumps. G.R.P.: Tank Chambers with Corbel Tops, Dispenser Sumps with Pump Stands. Interceptors, Separators and Silt Traps. ACCESS COVERS
G.R.P. Lightweight or Heavy Duty Steel Covers and Frames.