THE BULLETIN
Journal of the Association for Petroleum and Explosives Administration
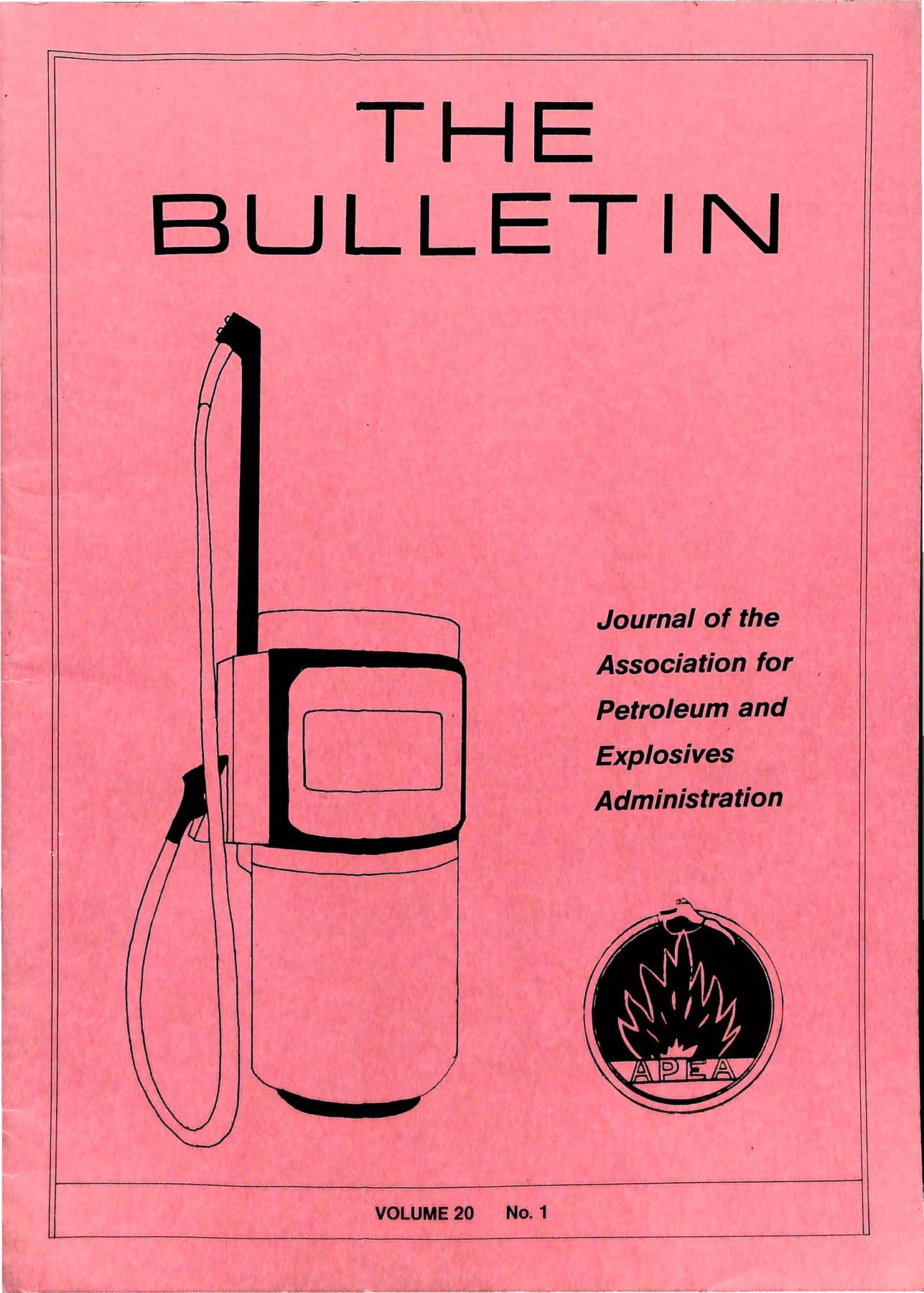
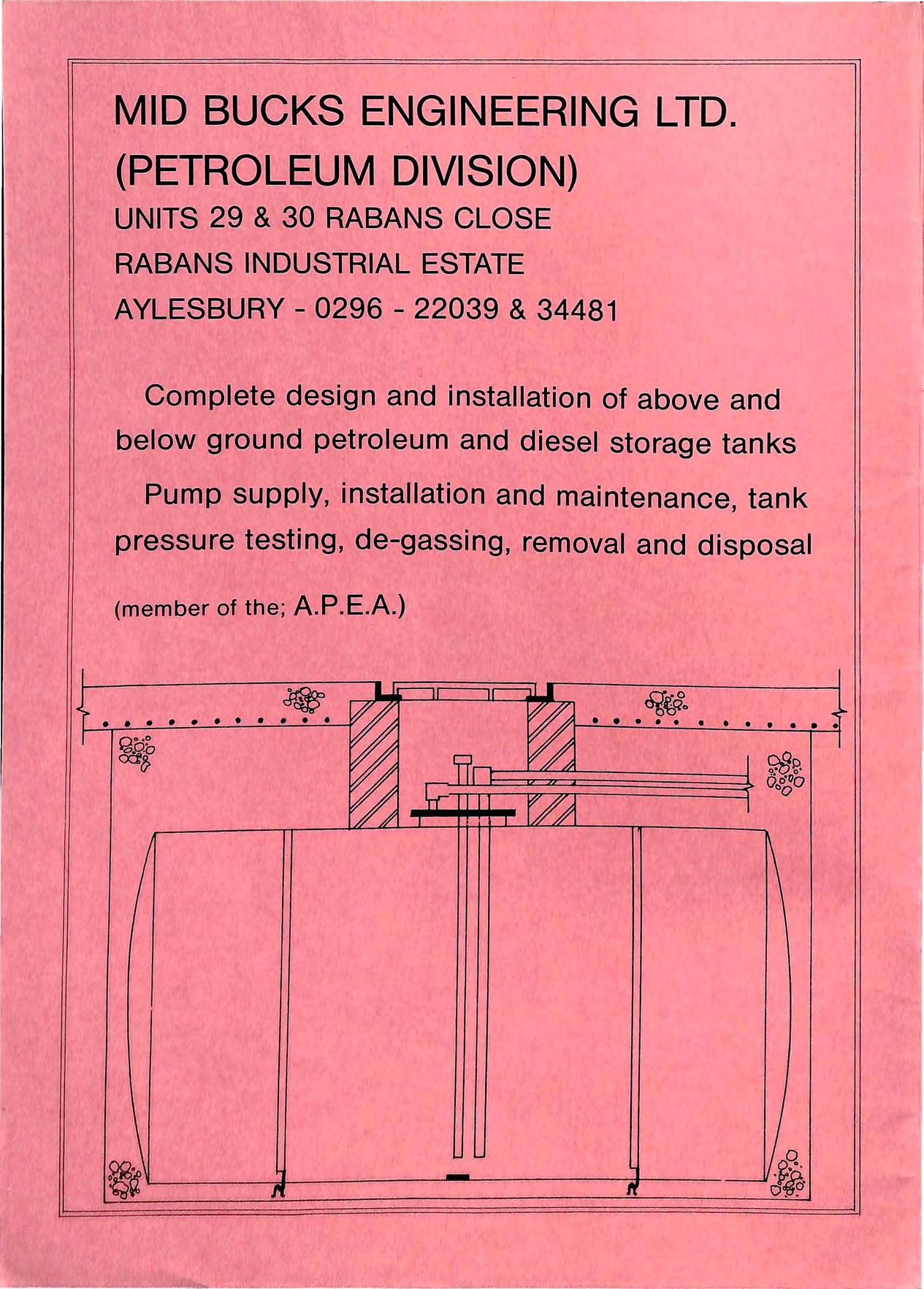
"THE INDEPENDENT FUEL"
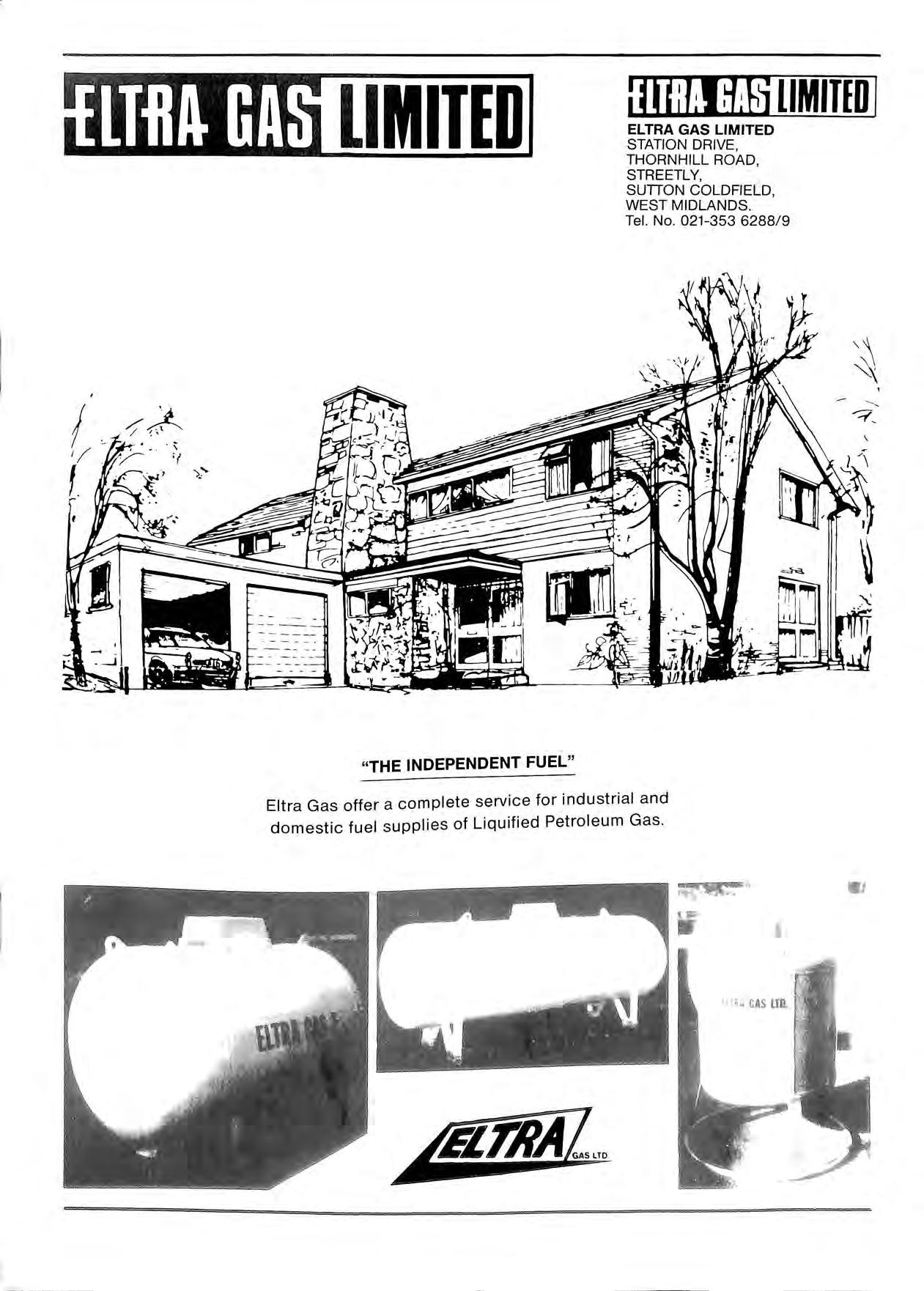
Opinions
oumal
The Bulletin is twenty years old this year, the first issue was published in 1962 some 4 years after the Association was first formed. I have asked two contributors of that first issue to write in the 20th volume. Bill Dale and Bob Holdaway contributed a lot over the years to make the Bulletin and Association prosper and I am grateful to them for "following up" twenty years on.
The HSE are in the process of looking into revising the old Home Office code on Petrol Filling Stations. In looking at this it is hoped that they might consult practising petroleum officers or perhaps the council of this Association who are aware of the practical problems of this outdated code.
There is a new branch secretary for the Midlands Branch, he is Mr. A. Levett, Trading Standards Department. 160 Old Budbrooke Road, Warwick. Tel. (0926) 49615l.
In the last Bulletin I gave Yorkshire Secretary Mr. R. Kitching the wrong address, he is at Trading Standards Department, King Edward Street, Grimsby, South Humberside.
The Bulletin is only as interesting and informative as members can make it. I hope that during 1982 that many more members put pen to paper, and keep us informed of interesting installations, equipment, accidents and fires. In addition I would ask all Branch Secretarys to send minutes of the Branch Meetings for publication in the Bulletin.
We ?ave a number of Associate members with products or services to offer, we are willing to publish these if felt they are of interest to members.
The new Conveyance Regulations described in the last Bulletin. came into force on January 1st 1982. The new Regu.latlOns do not make it necessary to have petrol tanker manhds locked as was the case under the 1957 Regulations. It has brought to my attention that a number of oil are dismayed at this, as it is felt that although their own rules require manlids to be locked before leavmg the depot, they have always preferred this to be backed by legal enforcement.
The 1982 IFSSEC exhibition is being held at Olympia in London from 19 to 23 April 1982.
Apart from the papers and conference facilities visitors can see the large number of exhibitors who are showing up to date safety and fire fighting equipment.
is free and members can obtain tickets by wntmg to V Ictors Green Publications Ltd., 106 Hampstead Road, NWI 2LS or by telephoning 01-388 7661.
Guida.nce on the Dangerous Substances (Conveyance by Road In Road Tankers and Tank Containers) Regulations 1981 is published by the Health and Safety Executive.
The regulations which were laid before Parliament on August 11, come into force with certain exceptions on January 1, 1982.
Although not an authoritative interpretation of the law, the notes in the guidance are designed to assist those who have responsibilities under the regulations, which control the conveyance by road of dangerous substances in road tankers of any capacity and tank containers with a capacity of more than three cubic metres. For the detailed provisions of the regulations reference should be made to their full text reproduced in an appendix to the guidance.
Amongst other aspects, the regulations: incorporate the current road tanker labelling regulations and extend to tank containers with a capacity of more than three cubic metres the use of the familiar orange, black and white hazard warning panels which provide the emergency services with vital information in the event of an accident;
require the operator to provide information in writing about the load being carried to the driver of a vehicle, which would also be of value to the emergency services who may have to deal with an incident; require the use only of vehicles or tank containers which are properly designed and constructed; impose requirements for the periodic testing and examination of tanks and tank containers; require the training of drivers in safe procedures, and supervision of vehicles in certain circumstances; incorporate the current requirements, slightly amended, governing the construction of road tankers used for the conveyance of petroleum spiri t and carbon disulphide, and also for the unloading of petroleum spirit at filling stations and certain other places licensed for the keeping of petroleum spirit.
The regulations are the first of three sets generally designed to extend and update existing legislation for the conveyance of dangerous substances by road, .with the exception of radioactive substances and explOSives. The others will cover the packaging and labelling of dangerous substances both for supply and transport purposes, proposals for which were published by Health and Safety Commission (HSC) in a Consultative Document on December 8, and their conveyance as packaged goods.
Under the regulations 'dangerous substances' are either those named in an Approved List, published separately by the HSE or those whose characteristic properties mean they fall into one or more of the 13 classificatio?s in a Schedule to the regulations such as toxiC gas, 'flammable solid' or 'corrosive substance', and for which appropriate hazard warning signs are assigned.
The Approved List, to be updated and extended from time to time, details those substances so far identified as likely to be conveyed in road tankers and tank containers, together with substances identification numbers, emergency action codes and hazard warning signs.
An Approved Code of Practice on the classification of dangerous substances was published by the HSC on December 11 giving advice to industry on how to classify a substance not on the Approved List.
There are a number of dangerous substances, not on the Approved List, for which emergency action codes have been assigned. The HSE reminds operators that from January I, 1982, they are required to stop using this infOlmation on hazard panels until such time as the substances appear in the Approved List. Paragraph 23 of the guidance gives information to operators on seeking additions to the Approved List.
Contents Measuring Systems, who manufacture and market the CMS 2000 tank contents measuring system, are mounting a "Programme of Explanation" aimed specifically at petroleum and fire officers and other personnel concerned with the supervision and regulation of petroleum retailing.
Presentations have already been given in Manchester, Bath, Bradford, Leeds and Newcastle upon Tyne, wi th more planned for the coming months.
The presentation, which lasts approximately one hour, is given by a technically experienced CMS executive, who explains the functions, operating principles and benefits of the system, using a working model. After the demonstration session, participants are encouraged to ask questions concerning the relevance of the system to the work of the regulatory authorities and the service station, and to discuss potential developments of the technology.
CMS are very pleased with early reaction to the programme and plan to extend its scope to include training centres and other interested parties.
Product Manager, Tim Giles, comments: "With an increasing number of garages wishing to install the CMS system, we believe it is important to create the widest possible awareness amongst regulatory authorities from whom approval must be obtained".
For further information please contact:Nick Johnstone Campaign Publicity 43 Cromwell Road London SW7 2EG Tel. Sl-l1 4971
Cleaning Service Group have introduced a unique service designed to assist in the maintenance of garage and forecourt drainage systems. They have equipped vacuum tankers with specially adapted pumps and pressure hoses, they are able to check by means of explosimeters the dangers caused by disturbed fumes and vapours. This service has already secured contracts with National petrol station forecourt chains and although based mainly in the south provide a service as far north as Aberdeen.
A drainage report is issued after the visit reporting on any faults in the system and reporting on work carried out. A certificate is left which is available for visiting Petroleum Officers. Jn addition all customers have access to a 24 hr Hotline service which provides in times of emergency a guaranteed visit.
A short (i minute film can be provided showing this service to interested parties, or for more information contact Mr. P. Johnson, Cleaning Service Group, Pinchington Lane, Greenham, Newbury, Berkshire. Tel. Newbury 4.i:i.'J7.
At TrUfO Magistrates Court on the 12th October, 19H1, a tin mining company pleaded guilty to keeping explosives (JliI mel y plec:tric detonaturs) in a purtable office bUildi;:9" in contravention of Section .'i of the Explosives Act, 1l-l;:J as amended by the Health and Safety at Work, etc., Act, 1974.
Th!' company was fined .L2(JO with .£2.'> costs.
A third edition of a comprehensive catalogue of Health and Safety Commission and Executive publications is published. A completely revised format makes it easier for the reader to find his way through the catalogue and there is also more information on how to obtain the various publications.
The guide, containing more than 2,000 entries, is alphabetically indexed and cross-referenced. Items listed include: annual reports going back to 1969 and other reports, advisory literature, regulations, forms (including material that has to be displayed in factories) and certificates of approval. The new edition also includes publications from HM Mines and Quarries Inspectorate, the Explosives Inspectorate and the British Approvals Service for Electrical Equipment in Flammable Atmospheres.
To ensure receipt of future issues when they are revised annually it is advisable to place a standing order with HMSO. Further details of this service can be obtained by writing to the Government Bookshop, P.O. Box .169, London SEl 9NH.
In the final quarter of 1980, 63,894 accidents at work were reported to the Health and Safety Executive and other enforcement authorities, bringing the total for the year to 272,822 compared with 318,873 in 1979. Among these were 565 fatal accidents, compared with 615 in 1979.
These figures show a further reduction in accidents during 1980. They include 21,000 accidents involving 'new entrants' the 7 to 8 million employees who were brought wi thin the scope of safety legislation for the first time by the Health and Safety at Work Act, much the same number as in 1979.
For comparison over the years, it is preferable to exclude the new entrants. On a comparable basis the total number of accidents reported fell from an average of 327,100 in 1976-78 to 299,600 in 1979 and 254,000 in 1980. Over the same period fatal accidents fell from .136 to 492 and 43.1. The falls in reported and fatal accidents between 197o-7l-l and 1980 amounted to 22 and 19 per cent respectively, and may be compared with reductions in industrial production (excluding North Sea oil and gas) of 0 per cent and in employment in industry of 5 per cent.
The fall in all fatal accidents between 1979 and 19l-l0 was most marked m metal manufacture (from 3.1 in 1979 to 21), transport and (from 08 to SO) and agriculture (from ?1 to (3). The fall in metal manufacture was mainly m steel where output was :17 per cent down on 1979, partl.y the trade dispute earl y in 1980. Although some mdustnes dId show small increases they were more than offset by falls in other industries. '
Th: fall in all reported was very Widely spread, affectmg all the major mdustry groups within manufacturing and most other industries. However, there was an increase in the number of accidents in agriculture.
In 19l-l0, IS,l-lo:i enforcement notices were issued compared with 17,Wl in 1979. The decline was mainly in notices issued by HSE authorities as local authorities issued a similar number to 1979. In addition 3S Crown Notices (in respect of Crown premises not subject to statutory notice) were issued in 19l-l0 compared with 29 in 1979.
More prosecutions were completed during 1980 than in 1979 1,668 (including 228 by local authorities) compared with 1,632 (264 by local authorities).
The figures quoted are based on the records of the Inspectorates of Factories, Explosives, Mines and Quarries, Agriculture, Railways, Nuclear Installations and Alkali and Clean Air, of the Petroleum Engineering Division of the Department of Energy and of local authorities.
Proposals to revise the fees charged by local authorities for licensing and registering premises where explosives are kept are published in a consultative document by the Health and Safety Commission.
It is proposed that the fees for an explosives store licence should rise from the current £17.50 to £30 and for the registration of premises, from £3 to £5.
The fees are intended to cover the full economic costs incurred by local authorities in issuing licences and registering premises. Costs were last fixed in 1978 for licences and in 1977 for registration, and the proposed increases take account of the amount by which costs to the local authorities have risen since that date.
The Approved List, published by the HSE in early August this year, details substances so far identified as those likely to be conveyed in road tankers and tank containers, together with substance identification numbers, emergency action codes and hazard warning signs which have been approved by the HSC.
A notice warning of the explosion risk if the proper are not observed when using oil storage tanks fitted with immersed heaters is published by the Health and Safety Executive.
For some applications, such as factory heating, oil has to be kept at a temperature of about 40 degrees centigrade, so it can flow freely to the burners. When this is done by Immersed heaters the level of oil in the tank should not fall so low that heating elements or thermostat are uncovered and extra precautions should be taken when welding is required.
The notice, which is intended for display wherever this type of tank is used, says the following precautions should be observed:
the oil level indicator should be maintained in good working order;
the oil temperature should not be allowed to rise above SO"C at any time;
the oil level should not be allowed to fall so low as to uncover the heating elements, or the oil thermostat.
The notice stresses that when the tank has to be drained care should be taken to ensure that the power supply to the elements is switched off.
Practical guidance on methods of meeting the classification requirements of the Dangerous Substances (Conveyance by Road in Road Tankers and Tank Containers) Regulations UJHl is published in an Approved Code of Practice by the Health and Safety Commission (HSC). The Approved Code comes into operation onJanuary 1, 1982 at the same time as the major part of the new regulations.
The Approved Code has been prepared on the basis of jOint discussion between the Health and Safety Executive (HSE) and representatives of the CBI, TUC, local authorities, Government departments and independent experts. It has been approved by the HSC under Section I h( I) of the Heal th and Safety at Work Act wi th the consent of the Secretary of State for Transport.
The main aim of the Code is to lay down criteria to be by operators of road tankers or tank containers for determining whether a substance not on the Approved List possesses any of the characteristic properties set out in tabular form in a Schedule tu the regulations, and therefore IS a dangerous substance.
The new Approved Code of Practice, says the HSC, not only explains how, in the main, substances in the Approved List have been classified according to their characteristic properties, but gives practical guidance on how substances, solutions, mixtures or preparations not appearing in the Approved List should be classified to comply with the regulations. The detailed criteria for classification are based on the recommendations of the UN Commi ttee of Experts on the Transport of Dangerous Goods.
As a result of being able to classify a dangerous substance, an operator will also be able to determine which hazard warning sign (the now familiar 'diamond') he should use for the purposes of labelling his road tanker or tank container, and so provide information to the emergency services in the event of an accident.
Guidance notes giving general advice on the regulations will also be published before the end of the year.
There have been reports, in newspapers and periodicals, that the HSE has suspended all Petroleum Licence Appeals. A number of members have sent this information to me and I read it with interest. In fact the reports are quite wrong al though there has been concern at the HSE over the attitude of some local authorities recently.
A spokesman from the HSE pointed out that legally they had no powers to suspend petroleum licence appeals and in fact appeals were still being dealt with.
The problem however within this field has been the differing ways of approaching the licensing of sub standard premises. In 1974 with the upper tier authOrity taking over licensing from the 1400 local authorities it seemed that at last some uniformity would prevail, but most of those authorities found premises which did not comply with th Home Office code on petrol filling stations. Here the differing methods of administrating the Petroleum Act: between authorities has been brought to a head.
Some Authorities took the view that the licence for th premises had been issued well before any code had issued and also had been accepted by their predecessor. These were then dealt with by either refusing to transfer a or to any improvement on the premises Without the unsatisfactory element being resolved. Those premises considered truly dangerous would have the backing of the HSE on appeal.
Other Authorities have given a "limited life" to the offending premises in the hope that improvements durin the time be carried out which would do away these unsatisfactory elements. For most, the time is up in 1982 and therefore a large batch of appeals was considered likely. It was clear from the stand taken by the HSE that the majority of these appeals would succeed. This could prove a problem to the HSE as the licensing authority could insist that the HSE take over these premises.
This however would appear to have been averted as talks between the HSE and Local Authority representatives have gone on and a committee has been set up to look into the question of appeals and some guidelines are being drawn up which will give a clearer indication of when the HSE will back the local Authority in refusing a licence.
In addition the HSE is also looking into the Home Office Code which is to be updated. It is not expected that the new
code will be out for about a year but this again may help in those grey areas. I hope that during the exammatIOn mto Code that the HSE examine Petroleum Stores and the differing standards, and also the items like lining petrol tanks with GRP etc.
The HSE will be invited to comment by the Association on these guidelines, and the columns of this Journal will be made available for their use.
An incident which occured in North London on 23 November involving some propane cylinders, an asphalt pot and a petrol filling station resulted in road closures and chaos in the immediate area.
A Commer open truck used by roofing contractors containing an asphalt boiler using propane cylinders to fuel the boiler, the equipment was alight while on the road and the occupants decided to stop for a cup of tea in a Cafe in Seven Sisters Road. The lorry with its boiler and three 47.2 kg cylinders and one S kg cylinder was noticed to be on fire, the driver knowing of the cylinder involvement evacuted the Cafe and Betting Shop nearby, he ran over to the Station opposite to call the brigade. The fire on the vehicle was well alight in a short time and the asphalt and LPG cylinders were involved.
One of the 47.2 kg cylinders exploded and windows for up to ISO ft away were blown out the remaining three cylinders were thrown off the vehicle one was deposited some WO ft away in th f '. '. e orecourt of a petrol fdlmg statIOn OppOSite.
The forecourt staff had already isolated the pumps, a customer on a moped had called in at the station parked his bike b!, the pump to watch the fire at what he thought was a safe distance. Th.e next instance after the explosion found
.a la:ge hurtling across the forecourt just ITIlssmg him, moped and the pump and involving the petrol statIOn a fire. The cylinder had a damaged top from the Impact from which LPG was flaming from.
The petrol pump, an A very Hardholl Mk IV was burnt out, with heat so fierce that much of the metal had melted, a nearby pump was damaged by heat, the canopy and canopy staunchlOn was damaged for considerable distance, and the
concrete forecourt will have to be replaced due to severe spaIling of the concrete. In addition to the damage done at the filling station, the Commer lorry was a total wri te off, all four shops by the lorry were damaged and windows blown out. Showroom windows opposite were blown out, the cylinder which exploded was blown flat and part of the regulator assembly was found 100 yards away where it had come through the roof of a workshop and embedded itself into a bench. A pick from the lorry was found embedded in the fence of the filling station opposite.
The most miraculous thing was the fact the no one was seriously hurt, the moped I;der had singed eye brows and was taken to hospital suffering from shock but was released.
The cause of the start of the fire was not known, the cylinders supplied by Air Products Ltd. all had pressure relief valves fitted to them, and in normal circumstances would not have exploded when in a fire situation. In this case the rapid build up of heat involving the cylinder and the asphalt would have caused the pressure relief valve to work but the pressure build up in the cylinder was too great for the valve to cope, therefore a mini BLEVE (Boiling Liquid Evaporating Vapour Explosion) occurred.
The Health and Safety Executive who followed up the incident with an investigation explained that similar fires involving LPG cylinders had been investigated, thpy have been common on building sites and in research at cylinders have been seen to explode even though prt'ssure relief valves are fitted. The time in this rasp between the fire being seen and the explosion was about :i minutes.
I understand that the code of practice is against tlw common practice of burners being alight while on the road or unattended.
At about 1915 hours on Thursday, 20 November 1980, abo.ut five tonnes of propane began to leak through the dram valve of a ten tonne storage tank in the factory yard of Whitefriars Glass Ltd Tudor Road Wealdstone Middlesex. ' , , five tonnes of propane was all that was left in the tank was being disposed of with other plant and qUipment after the closure of the factory had been announced.
The works engineer and a fitter had removed three of the four bolts securing the adaptor to the body of the drain valve. The valve was in good order and it was not :ecognised that the removal of these bolts would affect the mtegrity of its working parts.
The resulting leak of propane was discovered at about hours and the fire brigade arrived ten minutes later been called by a passer-by. The leak continued over penod of several hours and a gusting south-westerly wind elped to disperse the gas cloud' around 2000 local reSidents a d 100 '. ' n some students from the adjacent college were temporar'l d A I Yevacuate as a precautIOnary measure. number of people including firemen suffered from nausea and eight-year-old boy was detained in hospital overnight, but he was discharge next morning with no ill effects.
The report concludes with recommendations designed to prevent a repetition of the circumstances.
The factory was occupied by Whitefriars Glass Limited, for the of decorative glassware, and glass tube used III the manufacture of thermometers and other laboratory glassware.
. The factory, which had been on this site since 1923, was in a built up area, with a college separating it from ouslng one side. Private housing bounded the other two whIlst the main electrified railway line from Euston ay Immediately beyond Tudor Road. Virtually all the development had grown up since the estaiIshment ,of the factory. A general layout of the area is shown III Fig. I.
During its busiest years some 2()O people were employed 111 the fact H h h d b ory. owever, over more recent years, t ere a heen a gradual reduction in the numbers employed and on t e 12 S r. ' eptember I!IHO when It was announced that the a,ctory was to close, there was a total workforce of llfi. On t w 20 Nove b ,-() . d . S' m er on y:) remame on site. Ixteen (·mIJ!oyees we' d' I f'" h' .' Ie engage m g ass mls mg processes I ncllJdll1g' th h' , A h e was mg and packmg of glassware. t t e t II1]P ()f the incident the only employee in the factory was t 11Ightwatchman,
fG, ,:fi-AJ Whitefriars factory "";»,!rn" CollE'ge builriings
Fig. 1. General plan of area
Propane had been used as a fuel in this factory since the early 1960s when a five tonne horizontal storage tank was in use. However, by 1964 the company were using more propane and by April of that year the five tonne tank was replaced by a 10 tonne capacity vertical cylindrical storage tank in the middle of the factory yard, as is shown in Fig. 2 was mainly used to fire furnaces, process eqUipment and one or two small umt heaters in the factory A maximum of approximately five tonnes of propane was used weekly but in recent years its use had gradually diminished to about one tonne per week. Throughout the period the propane was supplied by the Esso Petroleum Company Limited.
The 10 tonne propane storage tank was manufactured by Old Park Engineering, Dudley in March 1964. It was approXimately 2·1 m diameter and 7·4 m high, and had a water capaci ty of approxi matel y 20,000 litres. The tank was supported by four fabricated steel legs approximately high which were bolted onto a concrete base within a compound approximately 7 m by H,!) m surrounded, except at the gateway opening, by a breeze block wall some :2S0 mm high. The wall was surmounted by concrete posts and chain link fenCing. There was one gate in the compound
fence. The ground between the edge of the concrete base and the compound fence was infilled with gravel.
The tank was fitted with a pressure relief valve, pressure gauge, drain and contents gauge. Take off was in the vapour phase from the top of the tank.
All buildings were at least 15 metres from the tank except the Tube Tower and a covered parking area, 11 metres and 10 metres away respectively.
The site was well ventilated and though almost completely surrounded by buildings the factory yard was large enough to allow an adequate standard of natural ventilation for a tank of this size. There were two surface water drains in the yard one 6 metres and the other 11 metres from the tank.
No electrical equipment was in the vicinity of the tank.
It was stated by the occupier that the tank was examined ten years previously but no records of such examination were kept.
The drain valve was a Class 150 flanged end firesafe ball valve manufactured by Weir-Pacific Valves Ltd of Glasgow. It was 50 mm nominal bore and made of steel. The manufacturers of the valve ceased trading in 19HO, but as far as could be ascertained the valve fitted to the tank at the time of the incident was the original valve fitted by Old Park Engineedng when the tank was manufactured.
The valve consisted of two main sections connected by four bolts through mating flanges as shown in Fig. :i. The upper section or body which was bolted to the underside of the tank, contained the stainless steel ball, its poly tetra-
fluoroethylene (PTFE) seat rings and operating mechanism. The lower section or adaptor had a spigot which extended into the upper section and held the seat rings in place against the ball. Rotation of the ball by moving the operating handle to the open position, allowed the bore in the ball to line up with the bore in the body of the valve, thus permitting propane to flow. There was a 2S5mm space between the underside of the tank and the concrete base. The valve consisting of the body and adaptor was 168mm long, thus leaving a gap of 87 mm between the bottom flange of the adaptor and the concrete base. The integrity of the ball valve was completely dependent on the body and adaptor being maintained together by the bolts and mating flanges.
Following the announcement of the closure of the factory the glassmaking furnaces were shut down and arrangements were put in hand for the disposal of plant and equipment, including the propane tank and approximately five tonnes of propane still remaining.
On Monday 10 November a site meeting was held between the technical manager, the works engineer and a representative of Esso, to discuss what arrangements were required for emptying the tank. The advice given to the Whitefriars representatives was that a length of pipe be connected to the drain valve, and that a second valve be fi tted on the open end of the pipe; an el bow piece would be required to join the pipe to the drain valve. During their general discussion mention was made of the limitation of space between the bottom flange of the adaptor and the concrete base, but it was agreed that it would probably be possible to fit an elbow in the clearance available.
The Esso representative advised that the drain valve should not be tampered with and the two Whitefriars representatives acknowledged this advice. What tlll'V did not understand, and what was not made clear to was
Factory boundary Propane tank Tube towerCow,,", po,k;o,
that the adaptor should be treated as an integral part of the valve. Both the Whitefriars representatives thought the adaptor was merely a distance piece or spacer and that the operative parts were entirely contained within the valve body.
No written confirmatory advice was given following this site meeting.
On the afternoon of Thursday 20 November the works engineer assisted by a fitter went into the compound to undertake preliminary work prior to fitting the elbow piece. Three of the four bol ts connecting the two mating flanges of the body and the adaptor were removed and the fourth loosened. By the time this work had been done it was considered too dark to continue, and the two men left the not realising that what they had done amounted to partially dismantling the ball valve. Some time later the technical manager, who had been away from the factory th.at afternoon, returned and went inside the compound, wIth the works engineer, to see what progress had been Having examined the position, he too went away with the work done. At this stage there was no mdlcation whatsoever of any leakage from the valve.
At 19.00 hours the two men employed as security nightwatchmen changed shift, and did not notice any sign of a gas .leak. However, at about 19.15 hours the nightwatchman a smell of gas whilst he was in one of the factory His immediate reaction was to look for a possible leak.m the building, but he soon heard a loud hissing noise commg from the yard, and on investigation saw a white cloud approXimately 1·2 metres deep around the base of the propane tank, mainly within the compound. He promptly telephoned the works engineer to report the leak and adVIsed hIm to call the fire brigade. However, the fire brigade had already been alerted by a 999 call at 19.20 hours by a passerby who had seen the vapour cloud and believed it to be smoke.
The fire brigade arrived at 19.25 hours and immediately began to play water on the tank. At 19.31 hours having the potential danger from the leak, they contacted the polIce who arrived at the factorv at 19.46 hours. The police closed Tudor Road to through traffic and later on other roads in the neighbourhood were sealed off.
At approximatel y 19.30 hours the works engineer arri ved on the scene and advised officers of the fire brigade of POSSI ble sources of igni tion inside the factory and in partIcular of the need to shut down the boilers which were located in the basement boilerhouse some 26 metres from the tank as shown in Fig. 2. The works engineer together WI th a fire officer first shut down the boilers and then toured the factory buildings to identify and eliminate other possible sources of ignition.
A gusting south westerly wind was blowing and it was deCIded to evacuate the adjacent college building, and this took place at approximately 20.15 hours. The students were all advised to leave on foot because it was thought there was a risk of ignition if car engines were started in the college car park. A total of about 100 students and staff were evac uated.
At about 2().4.1 hours on the advice of the fire brigade, the police warned residents living in roads nearby to close all d()()rs and windows and to extinguish any naked flames. rn thp meantime, the fire brigade had summoned help from thp Greater London Council's Scientific Department and t Ill' 1,( Jl1d( H] Fi re Brigade's Petroleum Department.
It was also thought desirable to summon help from the safety adviser of the marketing department of Esso. Representatives from these departments arrived on the scene between 21.30 and 23.1 0 hours. The petroleum officer toured the area bounded by Athelstone Road, Whitefriars A venue and Graham Road, and took several air samples using an explosimeter. Although the smell of propane was strongest to the rear of the houses in Whitefriars Avenue, some 200 metres from the storage tank, no readings were obtained on the explosimeter.
At approximately 22.15 hours the police began touring the neighbouring roads to warn residents to be prepared to evacuate their homes. At 22.30 hours the police became aware that a number of people living in Whitefriars Avenue were complaining of nausea. Shortly afterwards it was decided that persons living within the area bounded by Athelstone Road, Whitefriars Avenue and Graham Road and Tudor Road should be evacuated.
The local authority (London Borough of Harrow) were now alerted of the position by the police and of the need for emergency assistance. Contact was made with staff at the Harrow leisure centre to make arrangements for accommodating the people evacuated from their homes. The police contacted London Transport at their local bus garage to seek assistance in moving the evacuees from their homes to the leisure centre.
The evacuation proceeded efficiently and by midnight had virtually been completed. Approximately 2000 people had been evacuated and it became apparent that persons living outside the defined evacuation area had joined the exodus at their own volition.
Police remained in the area overnight to ensure the safety and security of the evacuated houses.
Two of HM Chemical Inspectors of Factories arrived on site by about 23.30 hours having been alerted by the television news.
Although the liquid contents of the tank had ceased by approximately hour.s it was thought pOSSIble that there was an explOSIve gas/aIr mixture inside the tank. It was therefore decided to remove the adaptor of the drain valve and to reseal the outlet with a blank flange. This was successfully completed by about 02.:-:10 hours the following day.
During the incident several meetings were held on site to evaluate the situation and agree upon the best course of action. The final meeting took place at 0.300 hours when it was agreed that:
the immediate risk of explosion in the vicinity of the tank had passed;
residual risk of explosion in isolated pockets of gas in confined such as garden sheds, garages, etc, would pOSSIbly perSIst, and the return of residents to their homes should therefore be delayed until the morning.
written advice should be given to the residents on the necessary precautions to b.e observed when returning to their homes. ThIS was achieved by preparing a suitable notice on si te and it was distributed throughout the area later by the police.
People evacuated were allowed to return to their homes at O().OO hours the following day.
Commercial propane contains a non-toxic odorising agent with a nauseous smell to give warning of the presence of gas. A number of people living in the area complained of nausea but the only casulties reported were three firemen (all suffering from nausea) and one eight year old boy who was also affected by the smell. He was detained in hospital overnight but discharged the next morning with no ill effects.
The only major problem remaining after the incident was to de-gas the tank which possibly contained an explosive gas/air mixture. Careful consideration was given by HSE inspectors to a number of alternative ways in which the tank could be made safe. It was finally decided to fill the tank with water and to discharge the gas to atmosphere approximately IS metres above ground level through a pipe. This was completed on 25 November.
When investigation into the circumstances of the incident began enquiries were centred on the drain valve. After the valve body had been removed from the tank it became clear that the integrity of the valve was dependent on the two sections of the valve being retained together. The effect of loosening or removing the bolts connecting the two sections together was to allow the adaptor and hence the spigot to move, thus reducing the sealing pressure between the PTFE seat rings and the ball. This would allow propane to leak around the ball even though it was in the closed position. Detailed examination of the valve revealed no defects whatsoever. This confirmed the fact that the valve was functioning normally prior to the incident.
The probable reason for the leak being delayed was that propane had been taken from the top of the tank as gas. Thuse for at least ten years the light fraction had been distilled off allowing the non-volatile residues to remain in the base of the tank.
Owing to the viscosity of these residues a considerable time elapsed before the gas pressure eventually forced the liquid around the loosened ball.
Although the main production processes at the factory had ceased on 12 September 19HO, the premises were subject to the Factories Act 191iI. On the day of the incident lIi people were still employed in finishing processes, including the washing and packing of glassware. Because the escaping vapour did not ignite and no-one was seriously injured, the incident was not reportable to the HSE under the Factories Act, Sections HO or HI. Had the incident occurred on or after 1st January 19H1 it would have been reportable to the HSE as a dangerous occurrence under the Notification of Accidents and Dangerous Occurrences Regulations 19HO.
The storage and use of propane at the factory was subject to the Highly Flammable Liquids and Liquefied Petroleum Gases Regulations 1972 made under the Factories Act I. Regulation 7 relates mainly to the storage of LPG which includes propane. The propane tank at Whitefriars was a suitable fixed storage tank in the open air. The tank was not
clearly 'Highly Flammable LPG' as required by RegulatIOn 7( 4). However, the absence of such marking had no bearing on the circumstances of the propane escape. 'No Smoking' notices were displayed around the tank enclosure.
The Health and Safety at Work etc Act 1974 also applied. Section 2( 1) requiries every employer to ensure, so far as is reasonably practicable, the health, safety and welfare at work of all his employees. Section 3( 1) is also relevant. This requiries every employer to conduct his undertaking in such a way as to ensure, so far as is reasonably practicable, that persons not in his employment who may be affected thereby are not thereby exposed to risks to their health and safety.
The incident created a potential hazard to safety and those who could have been affected were people living near the works, those attending the college and members of the emergency services who attended to deal with the escape.
In this case, precautions necessary for the protection of others were no different from thos required for the protection of the firm's own employees.
These two sections of the Heal th and Safety at Work etc Act 1974 are wider in their general effect on the storage and use of LPG than those contained in the Highly Flammable Liquids and Liquefied Petroleum Gases Regulations 1972. Compliance with these general obligations can be achieved by following the guidance available in several publications including the HSE's Guidance Notes for the Storage of Liquefied Petroleum Gas at Fixed Installatons."
These guidance notes were originally produced as a code of practice by the Home Office in 1971, seven years after the installation of the tank at Whitefriars. The foreword of the code of practice stated that it was not intended that the recommendations of the code should be applied rigidly to existing premises, where it was not practicable to comply with them. It was suggested that only such alterations as were considered reasonable or necessary for the safety of the publiC should be made.
The most relevant of these recommendations in relation to this incident was that drain valves on 'large tanks' should have an extension pipe fitted with a second shut off valve. The recommendation for a second shut off valve was a consequence of the Feyzin disaster which occurred in France in 1966. A second shut off valve is required to allow the drainage system to be shut off in the event of any malfunction of the main drain valve. The code does not define 'larger tanks' but there is little doubt that the presence of a second valve would have prevented this incident. Unfortunately it was as a result of the attempt to fit such a valve that the escape occurred and it has to be recognised that a similar incident might have occurred if the I'i tting of a second valve had been attempted earlier.
A minimum separation of \:'i metres is recommended between any tank of between 9,(lOO and 13:1,000 Iit res water capacity aI{d a building, boundarv. pmpert\ line (lJ' fixed source of ignition. This installation cumplied \\ith this recommenclat ion wi th t he except iuns of the cli stal1l't's tu the covered parki ng-s area and the t ubt' t()Wl'L Sl'l' Fig. 1..
The propane escape was clearly due to the action of undoing the securing bolts of the mating flanges of the drain valve whilst the tank was part filled with liquid propane. Investigation of the incident established that the leakage of propane resulted from a genuine misunderstanding of the function of the adaptor, and a failure to appreciate the significance of the advice given by the Esso representative. There was no evidence of any defect in the valve.
The incident might have been avoided if an extension pipe and second shut off valve had been fitted earlier. Given the special circumstances, i.e. the need to drain about five tonnes of propane from the tank following the factory closure, the fitting of an extension pipe in the limited clearance available presented a difficulty and the attempt to increase the clearance by removing the adaptor was quite understandable.
It is doubtful whether the need for a second shut off valve on a tank of this size had been clearly established at any time prior to the incident it was certainly not clear when the tank was first installed. Whitefriars' management recognised that, like many other users of propane, they possessed only a limited knowledge of the technology, and it was for this reason that they sought and received advice from their suppliers on how to empty the tank when the factory closed.
Some users of LPG who have Weir Pacific, or similar, fire safe ball valves fitted in the drain lines of bulk LPG storage tanks may be unaware of the detailed construction of the valve and the hazards associated with an attempt to dismantle it by removing the adaptor. Publicity should be given to the resultant hazard to the integrity of the installation arising from the tampering with fittings and attachments.
HSE proposes to co-operate with suppliers of LPG for bulk storage in making users aware of the hazard.
2 Guidance on the storage of LPG at fixed installations should include reference to the need for repairs or to fixed storage tanks and their fittings to be carned out by or under the supervision of a competent person.
Note
HSE already has a revision of the guidance note in hand and will incorporate this recommendation.
3 The need a second.drain valve on fixed storage tanks should be cons.Idered for mclusion in any future legislation, codes of practIce or guidance literature.
A review of existing LPG legislation is included in the HS,?/HSE programme and this recommendation WIll be conSIdered.
There is no great mystery about the title ofthis piece. It is simply that the first Bulletin appeared twenty years ago and the Editor has noticed that I had a paper in that first edition. He therefore thought that it might be a good idea if I did a follow up; it is surprising the lengths to which some people will go to get copy! For my part I am left wondering whether the impact of my earlier paper was such that only after years is a repeat necessary or whether it was so poor that it is only after years that the Editor dares risk me again.
The original paper was written at the start of the swinging prosperuus sixties at a time when new marketing Ideas abounded. Use of latched nozzles was being urged so as to create a 'Fill 'em up' customer reaction. Local authurities were reluctantly being pressed to accept attended self service on petrol filling stations to speed sales. Unattended self service were dirty words and it was seven years before the cachet of respectabi li ty on I his system was to be enshrined in a new Home Office
Model Code. There was a world surplus of Iow boiling to my horror I was once even approached wi th a suggestIon these petroleum spirits could safely be used to fuel domestic central heating installations.
The motto on the forecourt was 'speed and efficiency'. Forecourts needed to. be larger to simplify vehicle movements and more dIspensers had to be provided so as not to delay the customer. The need for more dispensing points capable of dispensing a number of grades led logically to the development of blending pumps. With blending pumps the use of remote pumping from large tanks became a possibility and thoughts turned to the development of a number of remote pumping systems including the use of submerged pumps.
Large tanks demanded the provision of larger road tankers and it can have been no surprise when the Petroleum Spirit (Conveyance by Road) (Amendment) Regulations, 19fifi emerged to permit this. It is interesting
to recall that there was a gentleman's agreement with industry before the making of these Regulations that the new breed of road tanker would incorporate certain additional safeguards such as combings to protect top fittings in the event of the tanker overturning and shear sections or foot valves to ensure the integrity of each valve in the event of the tank shifting in an accident; the major oil companies also agreed at that time not to convey heating oil on tank wagons carrying petrol. These provisions still have to find their way into statutory instruments but the agreements are nevertheless observed.
Large tanks under the forecourt meant in turn larger tanks at distributing depots. The increased size of depot storage tanks opened the way to the wider use of the floating roof tanks which are now a familiar feature in this country. In the process high level alarms and automatic cut outs to prevent overfilling and anti-head valves to prevent outflow were introduced.
The familiar petroleum spirit measuring pump on the filling station forecourt still kept its old familiar coffin shape, however. There was a minor flirtation with the Tshaped pump with its slim waist and big head but all to no avail. The blender with its many extra parts caused the slim waist to swell and heigh-ho we were back with a coffin but this time for a fat dwarf. The shrinking of the pump for a while gave problems with the ejection of fuel from air separator vents but this was a problem which was quickly resolved by means of a float valve in the vent pipe of the drain line eliminator.
Fundamentally it was not possible to alter the basic shape of a petrol pump until the mechanical computer and register could be removed. The early self-service systems were in fact contrived merely by adding electrical counting and control systems to the old standard pumps. Thus we had the situation where the pumping unit developed power not only to move liquid but also to drive a meter which in turn became a hydraulic motor driving electrical pulse generators and mechanical gears. It speaks much for the meter design that the meters were able nevertheless to retain their high degree of accuracy.
All this was to change with the introduction of electronics onto th e orecourt. The bulky mechamcal computer and regl' ,t d' d d s er lsappeare an the pump shape changed to the mod h' hi' k ern 19 lOse confIguratIOn whIch we now today. It can lb' , b sa eye stated that after the mdustry s very rief flirtation 'th fl 'd' WI UI ICS the silicon chip is here to stay.
In some respects th ·1 f I d b e pat 1 or the electromc pump was c eare y the format' f h f El' Ion 0 t e British Approval Service or ectncal Equipm t' Fl (BASEEFA) I h . .en Il1 ammable Atmosphere . n t e Sixties 'saf' I I still designed 'th h " e e ectnca equipment was that it might bWld t e thought at the back of one's mind , t' e I am aged by a rock fall such as one mig'ht expec Il1 a coa mine' th', b h' h h db d ' IS ecause safety philosophies w IC a een eveloped for minin h db the petroleum indu t . I I g a een extended to sry. nt10sedayswet Ik d f'd ' 'intermediate' and' f' . a e 0 anger, sa ety zones' our h I zones and the equi ' approac to [1eSe pment we allowed in tl h II parochial. Now we have i ' 1em was w 0 y Zones () 1 and nlt l ernatlOnal standard. s, we talk of , as we as safety are'l th f concepts to prot t, ' s, e range 0 , ec eqlllpment in these zones is conslderabl y extended and c ·t'f .' . being internationalized. el I IcatlOn of equipment is
the sixties, oil was still a cheap commodity with its pllce tendlI1g to decllI1e each year in real terms. Steel on the
other hand was rising significantly in price. What more natural therefore that industry should be starting to think at that time in terms of using G RP as a substitute for steel in the construction of tanks; the resin used in GRP was after all a material derived from oil. Not only might it be cheaper in the long run but is was keeping it in the family. One wonders to what extent the present apparent lack of interest in G RP tanks can be ascribed to the escalating cost of oil.
Throughout the years various gimmicky gadgets were attached to petrol pumps in order to promote sales in a market which was expanding by some 7% per year. Many of these gadgets and may I instance automatic Green Shield Stamp and 'Lucky Coin' dispensers are forgotten and perhaps better so although at the time the use of such techniques as fibre optics for the purpose was fascinating indeed. In retrospect it seems to have been a period of constant change with the concomitant problems of ensuring not only that safety standards were maintained but that they were uniformly applied.
One of the main purposes in forming the Association and publishing The Bulletin' was to achieve consistency of enforcement among some 1400 local authorities. How industry was cheered when local government reform reduced this number to less than seventy! With governmental responsibility being transferred from the Home Office to the Health and Safety Executive (HSE) this trend is now being reversed. Although the oil industry lobby will probably be strong enough to resist this move so far as petrol filling stations are concerned it does appear that the HSE is firmly set on the path offragmenting control over flammable liquids and LPG.
One can only be appalled at the shocking waste of the limited available expertise in the field that this will involve. From 1January 198'2, the police will be trying to learn the things about enforcement of conveyance regulations which officers of the current enforcement authori ty are engaged in forgetting. But maybe this is how the brave new world is to operate in the future.
One should never ask an old man to look into the future because he can see onl y the past. Nevertheless there are a few things that are apparent. In the short term the future of the motor car is assured and there is no ready substitute for petrol. The new electronic pumps and electronic tank gauges will simplify forecourt control and monitorin,g, Stock, reconciliation, recording, ordering and control wdl be done by centralised computers.
There is, however, the troublesome commodity which has no place on the forecourt and that is money. With the present price of petrol money is both. bulky and dangerous. We can rest assured that every effort wdl be made to replace cash, if not by our flexible friend, then by bank validation cards which will automatIcally check accounts and then transfer figures appropriately from one account to another. Equipment to do this is available is already operating in some Scandinavian CLluntnes. FullI IIment Il1 this country requires only the polItical wdl and available finance.
One also wonders how long it will be before ecohlgists demand the virtual elimination of vapour from filling station forecourts. Once again the equipment is available and is already in use in California where els(:,1
In looking back over twentv vears the mind exceeds its alloled span and travels back to sd1Lloldays and tll thost' meaningless words of ()vicl which Stl suddenh han' substance. Eheu, eheu, fugaces,
It was at the Annual General Meeting of the West Midlands Petroleum Acts Administration group held at Solihull in 1962, that the proposal "that a good means of keeping members informed would be through the medium of a bulletin issued at intervals" was agreed by the meeting. Not suprisingly the proposer rapidly found himself in the Editorial chair with little more than enthusiasm, promised support from various sources and a typical reminder from the treasurer that there was very little cash available, to sustain him. So commenced what for me was probably the most rewarding experience of my professional life.
A few words on the birth of the group may not be remiss. It was formed in the West Midlands in 1958 by some thirty stalwarts. Its unique character was epitomised by the fact that petroleum administration was practised by some four or five diSCiplines within local government service and that membership was confirmed to Local Authorities who nominated an accredited representative. Two names stand out in that era Len Cave of Dudley, the first secretary / treasurer who held the office until 1970 and whose painstaking thoroughness, administrative ability and gUidance built the foundation that stood the test of time. The other Geoff Dean of Solihull, a flamboyant character whose gifts as Chairman for two years were surpassed when as liaison officer in the early days, his contacts in the industrial world and other corridors of power brought benefit to members and industry alike. Coupled with the practical support he gave the writer in the preparation of early Bulletins, visits to the continent of Europe in pursuit of learning brings back memories evergreen.
For three years every quarte.r the Bulletin was typed, stencilled, stapled and distributed by a small band of enthusiasts whose efforts cannot be measured. With its publication the Bulletin immediately acheived a success beyond its sponsors widest dreams. Membership increased rapidly far beyond the boundaries of the West Midlands. Becoming National in 1963 with the title The Association of Petroleum Acts Adminstration (The explosives bit was added in 1973). Membership now embraced not only local authorities whose accredited members were in the main chief officers, but petroleum officers in their own right and associate members comprising the major oil companies, manufacturers of petroleum equipment, electrical contractors, county fire brigades and others having an interest in petroleum administration.
The support and interest in the Assoication given by associate members cannot be overestimated. Obviously the main objective of the Association the attainment of uniformity in the administration of the petroleum act was one of paramount importance to the industrialists among them; but they more than repaid any valued membership brought them by the help and advice given on many technical pronouncements made by the Association together with the willing provisions of lectures and speakers at branch meetings and residential schools which became sllch an important feature of the Associations f rCllning programme. Coupled with opportunities
presented to members to visit refineries, installation and research centres and so on, both m the United Kingdom and on the Continent it. can be seen that a close and happy relationship was established.
A National body brought a rapidly rising membership. As indicated above branches were being formed and the residential training school at Attingham Park. near Shrewsbury was always oversubscribed. The Bulletm was comfortably running at quarterly intervals with no lack of copy (Lucky Editor) It was the shop window of the Association with copies going to subscribers all over the UK and the continent in addition to members. Apart, therefore, from the growing impractibility of typing, stencilling and so on a better produced printed journal. was a must and this was acheived early in 1965. When WIth a circulation of over 300 negotiations were entered into with Walkers of Shrewsbury. Gradually both printer who had never tackled this type of work before and the editor who was in similar position began to produce a journal which was a credit to the Association and local government in general.
Len Cave who had retired from his official duties some years earlier decided in 1968 to relinquish the Secretary/ Treasurership. Tribute was duly paid to his services. His was the guiding factor, the dream come reality, the corner stone of the whol enterprise. He was honoured by being elected the first and to date only Vice President of the Association. Len was succeeded as Secretary by John Frid of Cambridge and Cliff Peacock a retired memberformerly of Hemsworth RDC took over as Treasurer. At the time of their appointments there were rumours and rumblings regarding re-organisation and it was realised that the Association membership could be badly affected. It was during this uncertain period the Association reached its peak. A membership of over 700, a print of 900 Bulletins quarterly, publication of codes of practice, reSidential schools held at Lancaster, York and Surrey Universities, acceptance by Local organisations and a strong relationship with the ExplOSIves Branch of the Home Office. 1971 saw a change in Editorship with Bert Thacker of Teeside a past chairman taking over.
Disaster in the shape of Local Government reorganisation occurred overnight in 1974 when the enforcement of petroleum legislation was vested in the top tier authorities, the County Councils. This resulted in a drastic drop in membership and the subsequent loss of subscriptions effected not only the activities of the Association but curtailed the frequency of issues of the Bulletin. For two years the future of the Association was in jeopardy, that it survived was due to two factors. First of all the considerable Sllpport of the unaffected so far as reorganisation was concerned, associate members who were quicker to recognise the value of the Association than were a number of the new County Councils, who on taking over a function new to them with a limited number of experienced petroleum officers, should one would have thought been more thankful to have established and
professional body available to them. Secondly to the sustained and dedicated hard work of the few who li terall y battled against the odds for the long term benefi t of their colleagues, present and future. Two names stand out. John Frid an indefatigable fighter who during his period as a secretary experienced the "heady" heights of the seventies to the difficult years when by necessity a firm policy of retrenchment was adopted. Cliff Peacock kept a tight hand on the almost empty purse during this period and it was his skill and careful stewardship that prevented the demise of the Association due to lack of funds. Both officers handed over their duties to a younger generation two years ago and our grateful thanks go to them for their selfless efforts.
During this traumatic period my own sympathy went very much to the editor of the time, initially Stuart Crewe an old colleague at Shrewsbury later Bedfordshire and the present Editor Jamie Thompson of the Greater London Council. My own task in the formati ve years was by far the easier. A continually expanding membership, a regular training programme numerous branch meetings, no financial curbs all meant plenty of material or copy and a routine was readily established. To keep the Bulletin going in adverse conditions needed a strong will and a belief in the future, and I am convinced if the Bulletin had ceased production, then in the absence of schools and other regular meetings, the link in the chain could have broken and the interest of the Association been affected.
Happily there are signs that the tide has turned, the Bulletin appears regularly again, membership is increasing slowly but surely, branches are being re-formed and successful one day seminars have taken place. The future of the Association appears assured providing all members give their full support. This year sees the 20th anniversary of the first issue of the Bulletin, next year the 25th
Anniversary of the founding of the Association. It is my fervent hope that many who read these reflections will still be members when the Association reaches its half century as it surely will!
Two further names remain in my memory to whom the Association owes much. They were both elected Honorary Members many years ago and to that degree their services were recogonised. One is Bill Dale of the Greater London Council, he presented a paper to the group at the aforementioned meeting at Solihull in 1962 published in the first issue of the Bulletin. Since that time has presented many papers at meetings in all parts ofthe country, given lectures at almost every school that has been held and under the cover of "Otto" produced a regular quarterly contribution to the Bulletin for five years that provoked as well as entertained and instructed. He encouraged, may be even coerced into officer membership nearly all his colleagues in the Petroleum branch of the powerful G.L.C. He is the only person as far as the writer is aware to have actively retained his connection with the Association over the twenty year period under review. The second is Jim Jeacock HM Inspector of explosives another who was always willing to present papers, lecture at schools, offiCially and sometimes unofficially offer advice or information either individually or collectively. He above all is the authority that brought together the close relationship between the Association and the Home Office which greatly helped to establish the Association in the early days.
Finally the pleasure and privilage of being the first editor of the Bulletin was very much mine. Many friends and contacts were made and much learnt. The Association and the Bulletin are in good hands, may its officers and members find satisfaction and share in rich friendships as we did in the years now past.
Modern tendency inclines to the production of uniform standards throughout the Common Market and to some extent an acceptance of U.S.A. Standards. Whether one agrees with, or welcomes the new standards is no longer relevant, they are here and, at least, they assist Manufacturers to produce a commodity acceptable over a large international area. For example, the IEC standards for Electrical Equipment in Hazardous Areas may not please everyone, but has facilitated international trade in machines and equipment used in hazardous 'Zones'.
It is therefore remarkable that nothing has been done to remove the obstacle in this Country to the uniform treatment of Highly Flammable Liquids. I refer of course to the Petroleum Regulations.
Standards for the storage and use of Highly Flammable Liquids have been applied by the HSE and copious guidance notes published. If however, the HFL happens to be Petroleum Spirit or Mixture an entirely different ball game results.
The standards are set by the Fire Authority and each of the 63 authorities has its own rules and regulations, usually differing from those applied by the HSE.
There is no fundamental difference in risk Petroleum based and other HFL's but the legal situatIOn IS different and the standards are different. It is true a large proportion of the Petroleum Spirit is kept at Stations used by the Public and that Safety s. at h . es should be higher than in Factones. In which suc premls . . I case it is logical to treat that type of premises y 01 all HFL storage (including LPG) and not impose different standards only for one type of HFL.
LPG . a Petroleum based HFL but is not subject to the Act because it cannot be tested for.Fla.sh Point in the approved manner. On the other hand Natural Gas (Methane), was brought under the Act Special Order. Storage of LPG at mal1\·. locations many of which are not 'Factones. Storage u1 Liquid Methane is restricted to a fe."" sites occupied by t1w Gas Council at which I expect the Local Petroleum Inspector has a minimal influence. If it had been tht' other way round and LPG brought under the Petroleul11 Act. there might have been some sense in it. The l.ocal
Authority Petroleum Inspector would be better employed -regulating storage of all HFL's, including LPG, at premises used by the Public instead of wasting their time duplicating the HSE Inspector's work at Factories, and then confusing the situation by making different requirements.
If one compares the Petroleum Code (i.e. The APEA Code), with the HSE Guidance notes, the differences are substantial, and to make confusion worse confounded there is no guarantee that the Local AuthOrity adhere to the APEA Code.
For example:- The HSE in the Guidance note CS/2 state that storage in above ground tanks is preferable (para.2). The APEA Code says "Save in exceptional circumstances every Petroleum Spirit storage tank shall be below ground". The HSE state that storage in containers is preferred in the open air, or in a 112 hr. F.R. store if within 4 metres of buildings or site boundary. The Petroleum Code requires a 9" brick store with 2" concrete roof and 1 hr door for all Petroleum in excess of 50 gallons without any regard to the position of the store. (The GLC Code for stores is more flexible and realistic, and is better than both the above).
Electrical standards also differ. The HSE classify a store as 'Zone 2' up to a height of 3 metres, but according to the Petroleum Code, a store is 'Zone l' and the outside of the store is 'Zone 2'.
There is the right of appeal against any condition of a Petroleum Licence and such appeals are now adjudicated by Senior Chemical Inspectors of the HSE who presumably accept the HSE standards. It would be interesting to appeal against all requirements made under the Petroleum Act which exceed the HSE standards!
As far as Industry is concerned, and in particular the suppliers of equipment for the safe containment of HFL's, the present situation is most unsatisfactory. Contacting all Fire Authorities to try to obtain some common standard is of no value. Most of them did not bother to reply, and of those who did many merely stated that the work had been delegated. In short, no help at all. A standard store for Petroleum is impossible to design, one Authority requires gauzed vents at high and low level in metal bins.
Surely it is time that this confusion was ended and the storage and use of all HFL's brought within one set of regulations and covered by one Safety Standard.
This paper first appeared in Hazardous Cargo Bulletin
Comm. ander H G Stinton of the Hampshire Fire Brigade summ.arzses current knowledge on liquid gas explosions and eJfectlVe response
body of the tank caused by a road accident cannot be ruled out. A rupture would result in the contents out and forming a gas cloud, possibly by from an external source. In a fire condition external heatmg to the outside of a tank would cause a pressure build-up and allow the material to reach its critical temperature, expand rapidly and cause an explosion.
InJuly 197H, 200 lives were lost and a further 100 people injured when a road tanker carrying 23 tonnes of lIqUid propylene exploded while passing a camp site in San Carlos de la Rapita, Spain. This explosion was thought to be a boiling liquid expanding vapour explosion (BLEVE). this tragedy, BLEVEs have been more widely discussed and with greater concern.
At the end of a six-month inquiry into the Spanish disaster the judge concluded that the supposed cause was a pressure build-up above the liquid gas. Several factors contributed to the explosion but the fact that there was no pressure relief valve fitted, the tanker was overloaded and there was a high ambient temperature which constituted a dangerous situation.
This disaster represents the world's most serious accident involving the transport of hazardous material by road and consequently many questions have been asked in the UK as to the possibility of such an explosion occuring here. Even though special circumstances surrounded the Spanish tanker explosion, the possibility of a rupture to the main
The hazards associated with the release to atmosphere of a boiling flammable liqUid show .themselves dispropor_ tionately when large quantities are They can give rise to two phenomena: (a) the unconfirmed vapour cloud explosion and (b) the boiling liquid expanding vapour explosion.
Consider the vapour cloud first. If a large quantity of flammable gas is released to atmosphere, three things can happen:
(i) It can disperse without igniting.
(ii) It can ignite and bum as a deflagration. Such deflagrations or fireballs can cause a lot of damage by radiation starting secondary fires at some distance.
(iii) It can ignite and explode, causing high overpressures and very heavy damage. This occurred to some extent in the Spanish case.
The last of these is by far the most damaging, combining the effects of a blast with those of fire. Because the deflagration can, on occasion, produce modest overpressures, the explosion needs to be differentiated in name. A descriptive term is 'unconfined vapour cloud explosion' UVCE for short.
There are still differences of opinion about the precise of the UVCE and the manner of its production. to say that it is generally agreed that a minimum quantity of fuel/air mixture is necessary for it to occur. For saturated hydrocarbons it seems that an emission of at least 10. tonnes necessary, although probably only a fraction of thIs contn butes to the percussive effect. (More reactive molecules such as ethylene have caused UVCEs with much smaller quanti ties.)
The chances of forming a cloud of more than 10 tonnes of hydrocardon with a large part of it mixed wi th air wi thin flammability limits are not great. The amount stored In system must be adequate to start with. The emISSIOn .must fast enough for atmospheric conditions not d.Isperse. It, and it must be turbulent enough to entraIn aIr, or mIX subsequentl y wi th the atmosphere rather than form a vapour cloud. A liquid held under pressure abov.e its boiling has the best chance of meeting these reqUlreme.nts: Expenence bears this out. Over half of the forty-odd InCidents involved material of this sort, and ab.o u t half.a f these mvolved liquefied petroleum gas (LPG) In ItS forms. This ratio is not very impressive in itself, but It IS that nearly all the non-LPG incidents wer: confmed to the chemical industry, i.e. concentrated m areas where the expertise and facilities exist foi' dealing with them. Against this, LPG is distributed univerally, including urban areas full of untrained people.
In or.d:r for a BLEVE to take place, the following four condItIOns must prevail:
1. Theres must be a substance in liquid form. Most destructive BLEVEs have involved flammable liquids and liquefied flammable gases. The large amount of published material on BLEVEs unintentionally conveys the idea that they only occur if flammable fluids are involved. This is not true. BLEVEs can occur with any liquid, even water. The only difference is that with non-flammable liquids there is no fireball. However, there will still be damaging effects including the propagation of cracks in the structure of the container together with possible subsequent failure and propulsion of the container, or pieces of the container.
2. The liquid must be in a confined container, such as a road tanker, storage tank or small drums. Even if the container had spring-loaded relief valves, there could still be a BLEVE. BLEVEs will not occur if the liquid is in an open container such as a vat or dip tank.
Useful data are collected by the Office of Pi peline Safety Operations (OPSO) in the USA on the incidents involving LPG pipelines. Over an 11 year period from 1968 to 1978 they recorded 296 spillages, nine percent of which involved more than 1000 rn. of liquid. Of these, 81 (27 per cent) took fire, but only 25 (eight per cent) were classed as explosions, i.e. less than one in three. No record was made of the overpressures experienced and it is likely that only a proportion of these would be classified as UVCEs. More detailed manipulation of these and other records suggests that of those LPG vapour clouds which are ignited and which are large enough to sustain UVCEs, less than one in ten does so.
As we have no experience in the UK of the effects of BLEVEs, it is necessary to look to America, where there have been a number of such incidents. The term 'Boiling Liquid Expanding Vapour Explosion' was adopted some twenty years ago by an American, Willbur Walls. Between 1950 and 1970 18 BLEVEs involving LPG, each with a capacity in excess of 2,:-lOO litres, were reported in America.
Those 18 fires resulted in the deaths of two firefighters and 20 civilians and serious injuries to a total of 318 firefighters and civilians. In the five years from 1970 there was a sharp increase in the number of fatalities and injuries resulting from BLEVEs. During that time 12 incidents were reported. These claimed the lives of firefighters and six civilians and seriously injured over :-lOO people. Combining the US incidents between 1970-197,) with the Spanish disaster, it is evident that the risk of BLEVE incidents is increasing and must be taken very seriously. Any lessons which can be learned from these incidents must be seriousl y considered and applied. Tankers carrying highly flammable materials use roads through highly populated areas thus produci ng hazards which ought to be selfevident.
3. The confined liquid must be at a temperature above its normal boiling point at atmospheric pressure at the time the container fails. Due to the fact that the closed container allows the pressure inside to build up above the atmospheric pressure, the fluid in the container is able to remain in the liquid state, even though its temperature is its normal boiling point. This increase in pressure raIses the boiling point of the confined liquid above its normal boiling point. An example of this is a steam boiler, where water is kept at a temperature above its normal boiling point, and is called superheated water. A source of heat is not always needed to bring the liquid above its normal boiling point. Some !Jq.Ulds such as propane have very low normal boiling (-43"C) and are already above their normal boiling pomt (therefore, superheated) when stored at ambient temperatures.
4.With the above three conditions present, there then must be a faI.lure of the container. This can result from many causes, mcluding:
(a) flame impingement, which weakens the container; (b) inherent structural weaknes of the tank;
(c) failure of lack of, or improperly designed relief valves which allow the pressure within the tank to increase to the point of failure; and
(d) impact from a mechanical cause such as a road accident or rail car derailment which would allow flammable liquid to flow out, form a gas cloud which, when ignited, would create a fireball and cause an explosion of the tank container.
In most BLEVEs caused by exposure to fire, the container failure originates in the metal area of the vapour space. Failure of the container is characterised by the metal stretching and thinning out, and the appea;'ance of a longitudinal tear which gets progressiyelv larger until a cntIcal length is reached. At this point, the material becomes brittle in nature and propagates at sonic velocity through the metal in both longitudinal and directions. As a result, the container often comes apart in two or more pieces.
The reason that the container llsualh fails in the metal around the vapour space is because it difficult to heat the container metal significantl\' \vht',:e it is in contact wi th Iiquid, The liquid conducts t he heat a\\a\ from the metal and acts as a heat absurber.
The results ofBLEVEs·are awesome, especially where large tanks of flammable liquids and liquefied flammable gases are concerned. When such a tank is involved in a BLEVE large sections of it can 'rocket' great distances with devastating velocity. Tanks may pivot and move in a direction different from their original alignment and large and small fragments of the tank can be hurled some 300 to 600 metres in every direction.
When flammable liquids are involved there is usually a fireball, which is a massive simultaneous release and ignition of vapour from the failing tank. This fireball could area of several hundred metres from the point of m all directions. As the fireball rises, it also gives off a fringe of radiated heat sufficient to ignite most combustibles and cause severe burns. is also a blast wave effect from exploding tanks. ThiS can vary widely and although it is probably not the greatest threat, it can be serious enough to cause injuries.
. A cloud of hydrocarbon vapour mixed with air but too rich to explode will start to burn around its outer envelope will 'lift off to form a fireball. Such fireballs are angerous in the extreme. When formed of hydrocarbons they are luminous, they radiate heat which can cause fatal burns to bystanders and which can ignite other carbonacious material in close proximity. This fireball rises to form a mushroom cloud. The stalk of the fireball consists of a violent upward convection Current which can suck up debris, igni te, then scatter burning brands over a wide area. size of the cloud and the rate of burn-up are difficult to Imagine. Perhaps it might help to say that the cloud would have a volume equal to about 3.5 tonnes per second, compared with 0.1 tonnes per second which is the rate of burn-up in the boiler of a 1000 megawatt power station.
In only relatively few cases have explosives experts been able to estimate with any degree of accuracy the TNT equivalent of the blast of a hydrocarbon vapour cloud. Estimations are difficult as vapour cloud explosions are not equivalent to TNT. They depart markedly from being pomt sources that TNT usually is. A vapour cloud has a volume about IO,Onn times as great as the volume of an equivalent mass of TNT. Furthermore, the explosions of vapour clouds are 'softcentred'; they do not have the shattering effect of TNT. As a consequence, they do not form craters. For example, in the Spanish tanker disaster, although the violent explosion occurred on the narrow roadway outside the campsite, the road surface was completely untouched. In fact the road was re-opened to traffic shortly following the disaster with no apparent damage to the road surface whatsoever.
area is essential and all naked lights should be extinguished, particularly those downwind. In populated areas it could be assumed that an early call to the fire brigade would be made and the exact timing of flame impingement on the tank would be known. Extreme caution should be exercised on gas release situations because of the ignition potential.
The following are guidance points:
(a) The application of water must be at the point of flame contact. The tank's vapour spaces (the area above liquid level) are the most critical and is the high priority area for cooling. (It is, however, not always possible to identify the exact level of the liquid).
(b) For effective cooling, 2000 litres per each point of flame contact is the minimum amount of water that should be used. (Priority should be given to the uppermost portions of the tank.)
(c) A large and sustained supply of water is required for both cooling and personnel protection. There must be an available water supply to sustain an attack for periods of several hours or longer.
(d) Ensuring accurate direction of water streams is of major importance. This is often impossible in a transportation incident, due to the wreckage and lack of Visibility.
(e) It should be carefully noted that any personnel positioning ground monitors or using hand lines would be exposed to extreme danger. Therefore, if a decision is made to the fire, only personnel essential for the operatIOn should be put to the task.
(f) Personnel must be clear instructions on the tactics to be employed. The entire operation must be highl coordinated. y
(g) Entry, to attempt to extinguish fire by shuttingval . h Id b vesor pluggmgholes,s ou only eattemptedafterestabli h· effective cooling streams on the tank shell at the p . s mntsmg of flame contact. ThiS IS a dangerous operation and h . d h b s ould only be came out w en a solutelyessential.
(h) The approach to a tank should be made f d d d h rom its win war si e w enever possible.
(i) Pre-fire for this type of an incident sh arrange for maximum support. Safe area ould bl · h d s must be esta IS e to ensure protection, proper contr deployment. 01 and
The absence of any predictable time ele b ·bl I· ment efore a POSSI e exp os IOn makes decision-making c . . f oncemmg the 0 thhe area more difficult. The follOwing consl eratlOns s ould be taken into account:
(a) The. zone should be approximatel 1 ()O{) metres m all directIOns. y
(b) Getting persons out of the zone of immed·· t d k ·d la e anger may ta e consl erable time and manpower e . II highly populared areas. This phase of operat; specla y m b · ·bl d Ions may even e Impossl e un er certain circumstanc es.
The method of dealing with a potential liquid gas explosion would have to be varied depending on where the incident occurred. In populated areas an instant and massive cooling attack would need to be launched very quickly indeed, employing all the available water supplies and using ground monitors or fixed branches in order that personnel ("ould be withdrawn as soon as possible. Evacuation of the
(c) Control of bystanders and spectators is dl·ff· It d f· f· h . ICU ,an Ire Ig tmg personnel may be insufficI·e t . b . n m num ers to cope With both crowd control and firefighting.
(d) public, unaware of the potential extent of a BLEVE and Its effects, may be unwilling to evacuate.
(e) should be made in advance for the use of the polIce to. public evacuation. Plans should provide for automatic Implementation immediately after the need for evacuation has been determined.
Inevitably, BLEVEs and UVCEs will continue to occur and as a result lives will be lost, injuries will be suffered and property will be damaged. However, an understanding of the mechanics of a BLEVE will assist the fire officer in reducing the grim statisics listed earlier in this article, and it will surely help him in making the crucial decisions which are necessary when faced with situations that can lead to a BLEVE or UVCE.
would suggest, with flame fronts travelling at shock-wave velocities when conditions for detonation do not appear to exist.
There is little reliable data on UVCE's. It is estimated that about 12 occur annually, mostly in circumstances that preclude detailed investigation. However, industry sponsored research at London's Imperial College of Technology may have solved one mystery: why vapour cloud explosions can be much more violent than theory
In a paper published in Nature Dr. S. R. Moore and F.J. Weinberg describe the results of experiments that suggest that minute particles in suspension ahead of the flame front and subject to intense radiation can form multiple ignition points. This increases total flame area and decreases the distance each flame front cycle has to cover to complete bum-out, accelerating the total flame advance. The particles themselves do not have to be of flammable material, and the types of particles most likely to be raised by blast or convection are also those most conductive to radiation ignition.
If the theory is correct, it will have important practical implications for UVCE prevention, and underwrites the current practice of wetting surfaces adjacent to a vapour cloud and forming a water-spray 'fog'. Besides damping down dangerous dust, the water mist could absorb some radiation should an UVCE occur.
The seminar was held at Dunstable on October 20th in the Vernon Room of Queensway Hall. All members of the Association were sent details together with other persons and organisations thought interested. The response was excellent with a capacity of 130 this was soon filled up and some late applicants had to be turned down.
The morning session was opened by Jim Cook our Chairman who welcomed the delegates explained the aims of the Association and introduced the first speaker Peter Norfolk of Normond Instruments. Mr. Norfolk gave a detailed insight into the working of his gauges and how they had used the micro chip to transfer information an electric read out and ticket printer, with water detectmg device a newer addition. The high cost of petrol in addition to the safety factor is influencing users to fit this accurate type of stock control package to sites.
Next Mr. Alien of Pump Maintenance and Mr. Pardoe of Fibresec spoke on and displayed the GRP manhole. The unit is designed to produce a water and spirit tight manhole for petrol tanks. We heard the many virtues of the manhole and the problems encountered while fitting the prototypes. With this experience and some 200 manholes in use, it is felt that this is an idea the Oil companies will use in the future.
Mr. Dave Rees of Bennet Beck together with all his equipment then gave a brief history of his and how they became the leader in the micro processor held 111 petrol retailing. Their experience has stood them in good stead as they are ready to adapt their equipment to take new credit card readOllts being experimented with at the moment.
The mornirig session ended with delegates examining the equipment on display and with Local Authority
members and the remainder coming from Industry a lot of discussion continued over lunch.
Mr. Jackson of the GLC started the afternoon session with his views on the problems of forecourt development from the petroleum officers view. Many areas were covered, from considering GRP suction lines, tank linings, credit card pre payment authorisers. Mr.Jackson ended his period with a lively question time dealing with tank testing, differing standards oflocal Authorities and looking into his crystal ball at future legislation.
Mr. Lugg of BP Oil then explained most ably the reasons why an Oil Company might develop the site, and what influenced their design and how they planned the maximum use of the site. An explanation into how much the Chancellor takes from every gallon of petrol was necessary to remind us that the Oil companies too have to watch their pennies and be profitable. The question session at the end on why filling stations sell other products as well as petrol was answered by the fact that this is likely to increase as the low profit on petrol for the retailer makes it necessary for him to sell other products to his captive customer.
All speakers were "veil versed in their subject and gave an excellent account of themselves. The Associatiun is grateful to the speakers who collectively made the seminar a success. ()ne of the aims of the Association is to promote discussion between the Petroleum Officer andlndustrv. It was clear from this seminar that there is an increasing lH'pd for this. By discussing mutual interests and lwing ,I\vare llf each others problems the Petruleul11 Officer and lndllstr\ can reach an understanding impurtant in their wLlrk together.