1958 -1983 '
1IIIIIIIII
Journal of the Association for Pe ·tro/eum and Explosives Administration
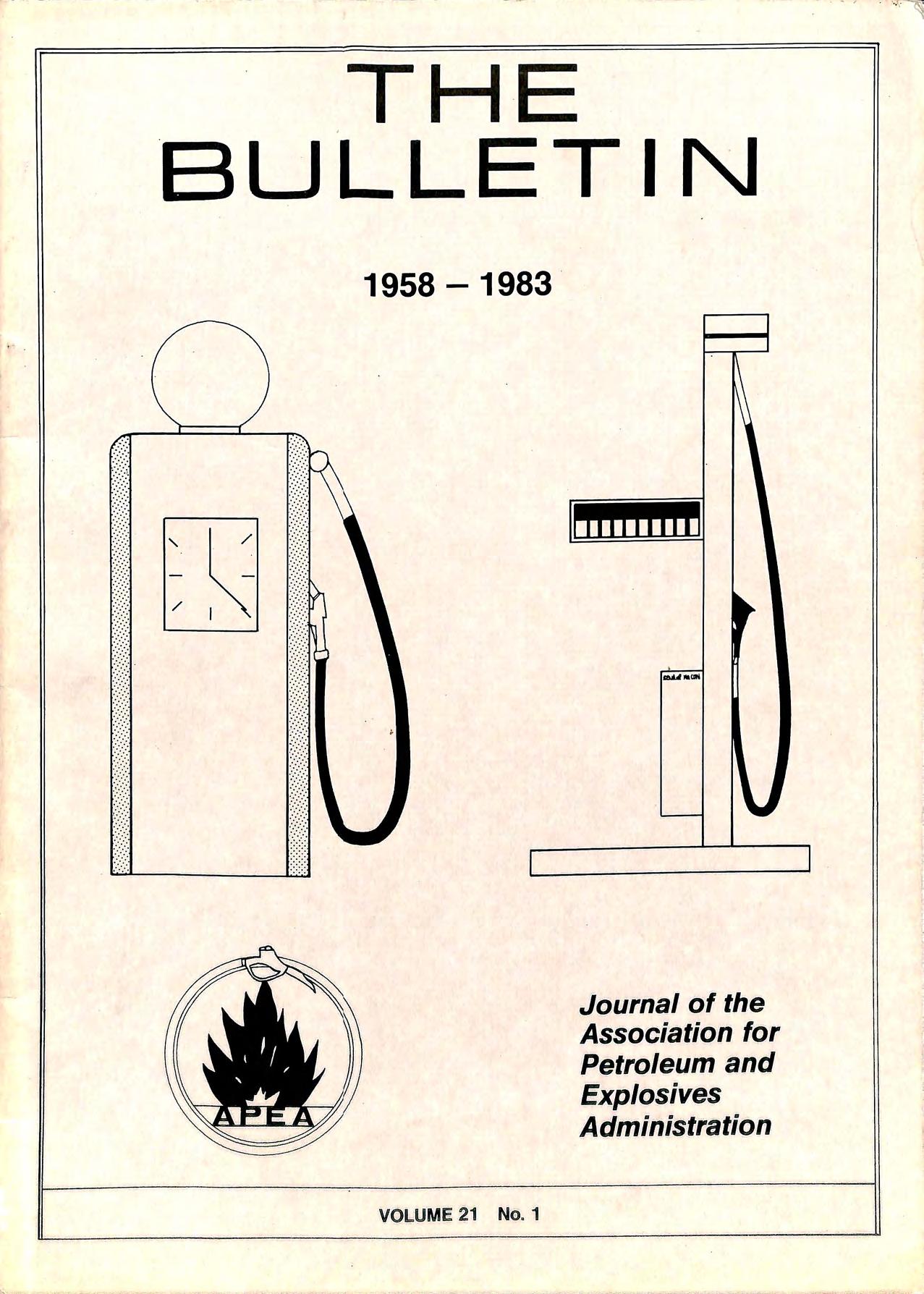
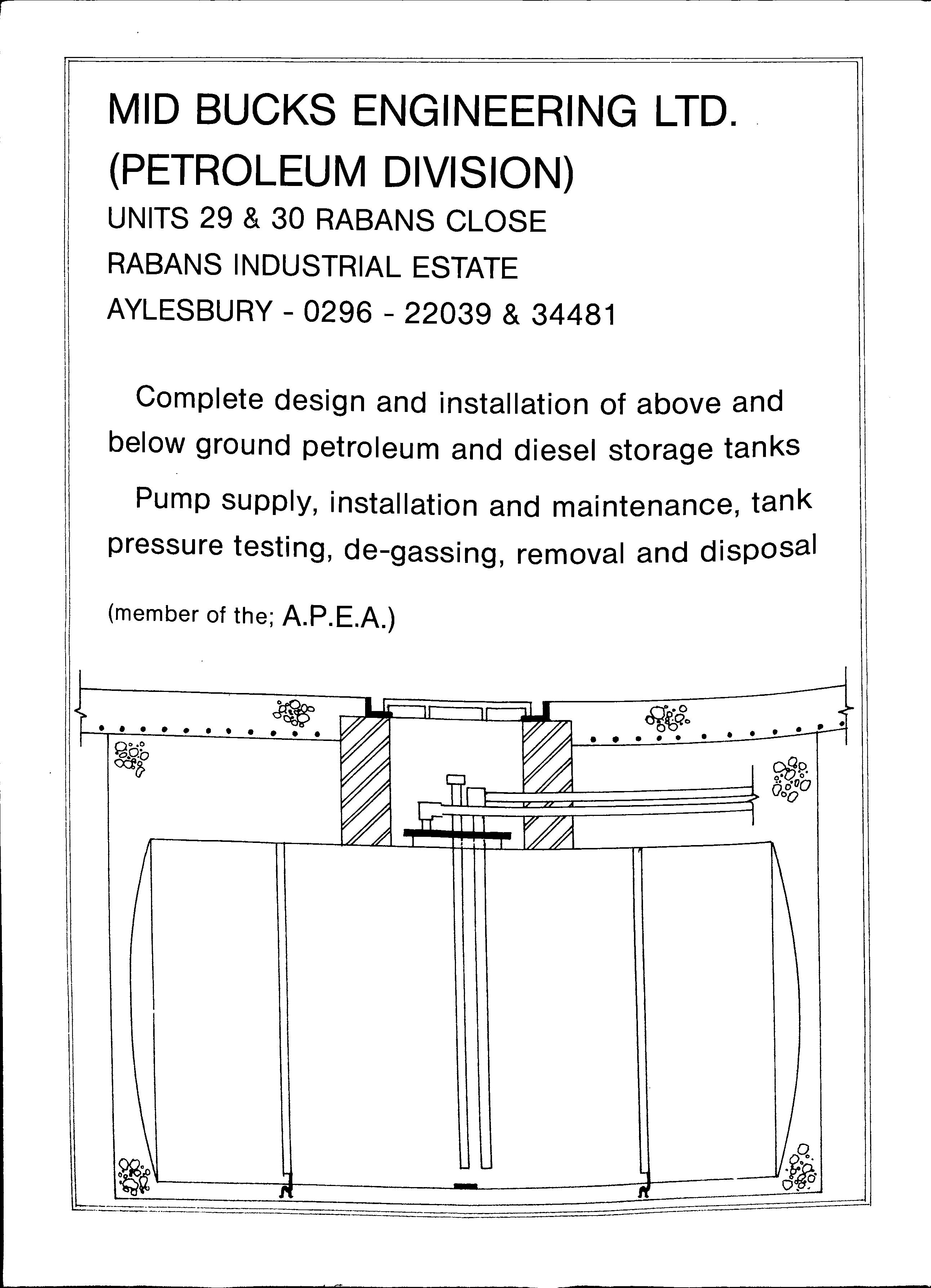
"THE INDEPENDENT FUEL"
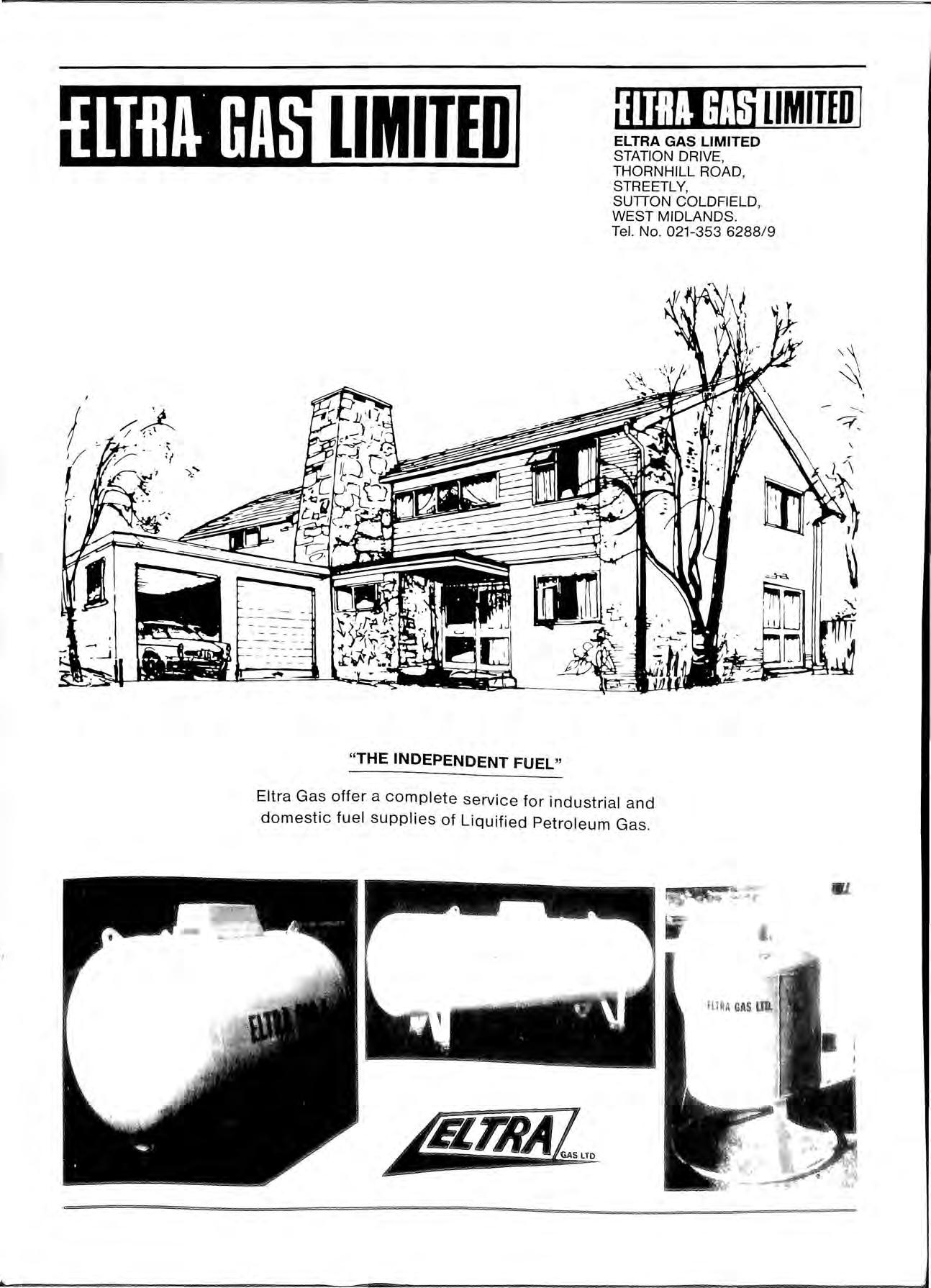
ELTRA
Using the latest computer technology, Tank Master measures fuel oil, chemicals,milk, drinks in fact any liquid in any shape of tank at the touch of a button with the added option of Specific Gravity Compensation.
• No electrics in tank area
• Any number of tanks may be measured on one unit
• High level, low level, fail safe, and air fail alarms built into system
• Alarms can be set to warn if S.G. of product goes outside pre programmed limits
• Alarm status of all tanks displayed on demand
• Delivery capacity of each tank can be displayed on demand
• Additional product loss alarm available to activate if contents of tanks drop more than a prc set percentage
• Facility to back calibrate the gauge against petrol pump totalisors for extreme accuracy
• Integral ticket printer
• Video monitor can either show details of a single tank or groups of tanks on system
• Printer will give details of one tank or full shift totals if required
• Simple operator controls
• End of shift totals on printer will show quantity gone from tanks since last shift
• Time and- date facility built into system
• Full facilities for Remote Data collection or for interface with modern petroleum self service units
• Accurate volume measurement of any liquid product in any shape or size of tank
During the past 2 years a different type of drive belt has appeared on forecourt petrol dispensers. The name is Tab-Link, and its unique polyester/polyurethane construction enables this belt to last a minimum of six times longer than conventional V-belts.
It's easier to service, as one reel enables the service engineer to make up any length of belt to suit all pump assemblies, thereby greatly reducing the stock carried
When it comes to the manufacture of pump equipment a simpler design is possible using' Tab Link, as the tensioning and sliding adjustment systems used with conventional drive belts aren't needed Tab-Link is in successful use in petroi ' diSpensers Britain, including those serviCed by Pump Mamtenance Limited, and built · by Avery-HardoIlLtd., TokheimLtd. and Ferranti Ltd.
Honorary Secretary
Mr. E. Brown, Cambridgeshire County COUl1cil,
The Council of the Association wishes readers and members a Happy New Year in what is an important year for it as it celebrates its Silver Jubilee. I wonder if those petroleum officers of the West Midlands in April 1958 realised that it would grow nationwide and satisfy a need 25 years on.
During the formative years excellent relations were forged between the Home Office and the Association and our views were sort on proposed changes. While the same relationship has not materialised with the H.S.E. perhaps the recent signs of their participation at our seminar and contribution to discussion in this journal augers well for the future.
Honorary Editor
M r. J. A. J. Thompson,
Stronger legislation and more enforcement powers for local authorities on the storage of hazardous materials were called for by Mr. J. C. Cook, principal petroleum officer with Surrey County Council, at a meeting on board H.M. S. Belfast organised by Marley Buildings.
Mr. Cook, who was The Associations Chairman last year expressed concern that current Health and Safety Executive legislation was self-regulatory.
"You cannot trust people to regulate their own safety", Mr. Cook contended, and he showed several illustrations of small firms who had not stored flammable liquids in safe containers or areas. He particularly condemned the "hundreds of cowboy spray firms."
Marley Buildings, who manufacture the "Flames tor" are launching a two-pronged campaign to persuade employers to tighten-up their safety procedures and to put pressure on the Government to publicise requirements and simplify existing legislation.
At the request of members we are sending out in the Bulletin a membership application form which members may use to hand to colleagues or associates to encourage growth of The Association. Members wishing for additional forms may contact the Hon. Secretary.
An addition to the list of approved substance identification numbers, emergency action codes and classifications for dangerous substances conveyed in road tankers and tank containers ('The Approved List') is published by the Health and Safety Commission. The substance is the organic peroxide di-{:l-ethyl hexyl} peroxydicarbonate.
A Notice of Approval has been issued by HSC under Regulation 4(2} of the Dangerous Substances (Conveyed by Road in Road Tankers and Tank Containers) Regulations 1981 following consultation with the CBI, TUC, local authority associations and other relevant organisations. Two conditions are attached to the notice relating to the maximum permissible concentration of solution to be conveyed and the maximum temperature during conveyance.
Since any revision of The Approved List cannot become mandatory until six months after approval by the HSC and Section 9(a} of the 1981 Regulations prohibits the convey· ance of an organic peroxide unless it is listed in The Approved List, the Notice of Approval cannot take effect until 5 April 1!J83.
In the interim, the Health and Safety Executive (HSE) has issued simultaneously Exemption Certificate No. 4 of 1982, also under the Dangerous Substances (Conveyance by Road in Road Tankers and Tank Continers) tions, allowing organic peroxide to be conveyed 111 road tankers and tank containers until the Notice of Approval comes into force next year.
Copies of both the Exemption Certificate and, the N of Approval can be obtained from: Health and ("utive, HSD A3, L.S Chapel Street, London N'A I ,lD I
Three important regulations on aspects of safety in the conveyance by road of dangerous substances in road tankers and tank containers came into force on 1January 1983.
They are Regulations 8, 10 and 21 of the Dangerous Substances (Conveyance by Road in Road Tankers and Tank Containers) Regulations 1981 covering the provision of information about the load to be conveyed and driver instructions and training.
The 1981 Regulations, which for the most part came into force on 1January 1982, extended and updated legislation on the conveyance by road of a wide range of substances in road tankers of all sizes and tank con tamers with a capacity of more than three cubic metres.
Regulations 8 deals with the information which an operator must obtain from the consignor he conveys a dangerous substance. This must enable the operator to comply with the reqUirements of the Regulations and be aware of the risks created by the substance to the health or safety of any person.
Regulation 10 requires an operator to gi.ve driver information in writing concerning the Identity .of the substance and the nature of the dangers to the . . d th mergency actIOn he substance may give nse an e e .' should take. The most common way of thiS 111. h C f 'Tremcards which are formation is 111 t e form 0 ., published by Conseil European des FederatlOnfs de I dustrie Chimique (CEFIC) and are available rom t e Chemical Industries Association Ltd.
Regulations 21 deals with the an? trainin.g .' to thelrdnvers. ThiS which operators must ensure IS given f the is to enable the drivers to understand the nadture 0 b · conveye may give dangers to which the substance e1l1g k d h' . h should ta e, an IS rise and the emergency actIOn e duties under these Regulations.
I t provisions of the Guidance on these and other re evan h d S fety Exenew controls was published by the Healt an ha d S f dd " the Healt an a e- cutiveinDecember 1981.Ina ItlOn, Itative h d' J this year a consu ty Commission publis e 111 une d f 'actice on document containing a draft approved clo .e 0 gives h I · . f the Reg'u atlOns. t e operationa proVISIOns 0 th thl' ngs on .d amongst 0 er , more detailed practical gUl ance, . f the code is exRegulations 8, 10 and 21. The final verSIOn 0 pected to be published in the spnng.
"11 be aware of the new In ternational transport operatOl s W I h E 1 AgTeelnent (on- driver training provisions oft e uropeal db' . . . I '. f' dang'erous g'Oo s \ cermng the 1I1ternatlOna carnage 0 D t of Transport on road (ADR) publicised by the epartmen 11 November U182. These also come into force 1January 198:1, and the issue of a driver's training certifIcate un-, der this Agreement will satisfy, in part, the reqUirements 01 Regulation 21.
W 'th h ., I' -. 11 the 1Jrt>visions of I t e exceptIOn of Regu atlOn I, a r . the Dangerous Substances (Conveyance bv Road 1\1 Road Tankers and Tank Containers) Regulations I !181 \\ill be \11 force from 1 January 198:1. Regulations 7. which outlmes the requirements the examination and testing ot tht' tanks and fittings of road tankers and tank containers. \\ill come into force on I.Januarv I
Some 10,000 companies will receive a letter from the Health and Safety Executive impressing on them the urgent need to check that chemical substances they manufacture or import are included in a core inventory of such substances. HSE warns that failure to do so could have serious commercial consequences.
This move follows increasing concern wi thin HSE and representative bodies of industry, that many smaller manufacturers and importers, includin?; some who do not normally consider themselves to be in the chemical field, may be unaware that many of their product contain substances which ought to be on the inventory or that failure to take action now could lead to heavy costs being incurred in testing substances.
The basic inventory (ECOIN) is a core list of chemical substances known to be on the European market between I January 1!J71 and 18 September 1!J81. It is the first stage in the preparation by the European Commission of EINECS The European Inventory of Existing Chemical Substances. When EINECS is finally drawn up and published any substance not listed will be deemed 'new' and may therefore be subject to the extensive testing and notification requirements of a European Communities Directive.
Firms have until 31 December, 1!J82 to check the core inventory and report to HSE any substance not included which should be listed. It is in their own interest to do this. The notification requirements of the Directive are unlikely to cost below £SO,OOO in testing fees for each substance and in some cases could cost much more.
A 'hot line' telephone service has been set up to provide urgent advice to any manufacturer or importer. The telephone number is 01-723 2108. A leaflet introducing EINECS is available from all Area Offices of the Health and Safety Executiveor by writing to: Health & Safety Executive, Room 11.8,25 Chapel Street, London NWl SDT.
Regulations to implement the EC Directive will shortly be laid before Parliament.
P . Is Cor a future policy on certification and approroposa I' bl' h db vals are contained in a consultative document pu IS e y the Health and Safety Commission as a further step towards the implementation of the I!JHl Rayner Study on Certification and Approval in the Health and Safety Executive.
The document proposes that a review of the numerouS mandatory certification and approval schemes presently contained in a mass of health and safety legislation should be carried out with a view to their revocation or simplification, and suggests the criteria on which the need for such schemes should in future be judged.
Approval and certification sc.hemes, the document require that particular types of plant, artIcles and, III a few
cases substances, are not used at work without the approval of HSE. Many of these schemes, it says, have evolved for historic reasons and are now moribund. Justification for them is greater when technology is new and developing and safety problems have not been identified and evaluated. When a stable technology has permitted the formulation of standards of safety and reliability their justification is much less, it says.
The document does not di!>cuss individual schemes but lists in an annexe some 40 products which are the subject of formal approvals. Existing schemes, it says, should only be revoked or simplified where there would be no loss to safety and after full public consultation in each case.
Among factors which the document suggests should be taken into account in determining a future policy are the extent to which the control of the hazard requires technical expertise unique to HSE and the feasability of codifying safety factors in each field. Attention is drawn to the longstanding policy of using and recognising external bodies for certification, where this is practical without loss of safety control.
Because it is concerned with the possibility of using external certification and standards, this Consultative Document complements "Reference to Standards in Safety at Work", which the Commission published on 24th August.
Following a spot check on a petrol tank-trailer in Edinburgh on 30th October 1!J81. A compartment which contained petroleum spirit was found to be insecurely fastened. When questioned by an authorised officer, the driver of the tank-trailer, a David Marshall Boyd of Winchburgh, West Lothian produced a brass key which he used to open the lid of the compartment which he had closed in the officer's presence. As you are aware, a driver was expressly forbidden to carry such a key.
At Edinburgh Sheriff Court on 5 October 1!J82 an additional trial did not proceed due to Boyd pleading guilty. He was fined £100 for having an unlocked filling compartment and £50 for being in possession of the key.
Would anyone who regarding a 5 litre ca acity plastiC petrol can dIstnbuted by a company known p MOTUS DESIGNS LTD., BOBY INDUSTRIAL ATE, BURY ST. EDMUNDS, SUFFOLK, please contact Rod Jones at Trading Standards Department, 4B, St. Mary's Square, Bury St. Edmunds, Suffolk IP:-l3 Telephone 0284 03141 Ext: 404.
The petroleum licensed premises are situated in a rural village in Perthshire and consist of two petrol pumps and three underground storage tanks. The vent-pipes are supported against the corrugated wall of the service building and extend some feet above the eaves where the corrugated sloping roof meets the wall.
The premises have been licensed for the storage of petroleum since the early 1930s and were re-developed in 1960 when new tanks were installed.
The service building had previously been used as a garage workshop with a large front door usually kept open and there was partial wood lining on the interior walls. The present owner had converted the premises last year into a shop area which involved closing the front of the building except for an access doorway and lining the interior walls with plasterboard. He had built an internal partition to create a small back shop area access to which was via a curtain made of simulated straw/raffia material. There was a slight step down of some 11//' 2" into this area in which was an electric cooker and fluorescent lights although none were operating at the time of the incident.
The department had not been notified of the alterations but it is unlikely that the petroleum officer would have objected as tanks and pumps are the required distance away from the building and the alterations were all internal.
The proprietor's wife had just deposited some messages in the back shop and was re-entering the front shop through the straw curtain when there was an explosion. Her tights were burned off and her hair extensively singed at the back but no physical injury or burns to either her legs or any other part o.f her body. There were signs of scorching on the straw curtaIn. A section of plasterboard was blown out at the foot of the wall in the rear shop on the opposite wall to the cooker but adjacent to where the vent pipes were externally attached. Slight structural damage also occurred when the shelving behind the counter in the front was blown into the middle of the shop and the corrugated wall buckled outwards. Flames were restricted to the vent-pipe outlets and were extinguished by a customer using an extinguisher handed to him by the tanker driver who immediately was turning off supplies to the tanks.
The incident occurred when the petrol tanker was refuelling the tanks. Petrol fumes on being discharged from the vent-pipes apparently entered the building at the eaves which were not sealed. The fumes had been deflected into the building by wooden guttering and lodged in the cavity between the external wall and the plasterboard framing. The wooden guttering had been in position for a number of years and was possibly intended to deflect water from continually dropping down to the base of the vent-pipes.
The weather that day was very still with mist low down over the surrounding hills.
The cause the explosion would appear to have been the discharge of static electrici ty caused by the rubbing of the lady's tights against her nylon underskirt as she stepped through the straw curtain.
No further delivery of petrol is to take place until the vent·pipes have been re-sited.
Liquefied Petroleum Gas is, as its name implies, a gas produced from petroleum products, it is also a by-product from some of the natural gas fields in the North Sea. Increasing amounts of this fuel are becoming available in the U.K. and one use for it is as an alternative to petrol in motor vehicles.
LPG consists mainly of two substances, propane, with the chemical formula C 2 H K and butane, with the chemical formula C,H ,O , and it is the former which is used in the U.K. as a motor fuel. Propane is a gas at normal temperatures and pressures, but it can be liquefied at normal temperatures by pressure. This is different from natural gas which needs to be cooled before it can be liquefied. At a pressure of 125psi (8.6 bars) and a temperature of 16°C it liquefies and occu pies about '/L"o of its volume as a gas. When the pressure is released it vaporizes, giving a fuel that can be used instead of petrol in an internal combustion engine . It is this ability to liquefy and occupy a small volume that makes it portable and suitable for motor vehicles
LPG as a motor fuel is not a new concept. It has been used both in the u.K. and abroad for many years, particularly in Holland and Italy where it provides a substantial part of the fuel for motor vehicles. In the u.K. until recently it only accounted for about 0.3 % of the market, mainly with fleet operators or firms in the LPG business, so that it was not widely available to the average motorist, but this is changing. Many firms are entering the market, both in providing bulk LPG tanks and dispensers and in converting cars to use LPG.
The additional hazards from LPG, over and above those o f petrol, arise because:
a) the material is stored and handled pressure in a sealed container.
b) any leak would quickly and completely vapOlize and not remain as a pool of liquid.
The standard for siting of the bulk LPG tank is given in the HSE Guidance Note CS.'> "the storage of LPG at fixed installations" and in the LPGITA Code of Practice No. 1 " installation and maintenace of bulk LPG storage at con s umers premise s" The main advice for use as a motor fuel is given in LPGITA Code of Practice No.ll "recommendations for the safe handling of LPG used as an internal combustion engine fuel for motor vehicles " but this does not COve r all situations and some of the advise is being revised. T he ln sti tu te o f Pe trol e um has a Working Party drawing up a Code o f Practice that will take into account the dispensing o f LPG at petrol filling stations and both the LPGITA and the HSE ha ve representatives on that Working Party , but it se ems probable that it will be some tlIll e b efore it is pub li she d T he Health and S afet y Executive are publishing m e moranda to Frs and LA ' s on LPG as a motor fuel and hope th,is will provide guidance until the Institu te o f Petro le um C od e o f Practi ce has b een published.
Th e re a re anum ber of fa c tors that need to be taken into con sid e ration including t he following:
1. Is the bulk LPG tank in a safe position?
It is fair to say that a simple bulk static vessel of LPG is unlikely to leak; escapes of material are more likely to occur at valves, pumps etc and where it is handled.
The tank should, therefore, a) meet the standard as in the Guidance Note CS.'>. b) be protected against possible vehicle damage. c) be separated from the dispenser or other activities.
The current LPGITA Code of Practice asks for ::3 metres separation between the bulk tank and the fuel tank of the vehicle being filled. A more realistic approach would be to have the bulk tank at least 3 metres from the dispenser and the fuel tank of the vehicle being filled.
2. Should the LPG dispenser be separate from petrol dispensers?
The LPGITA Code of Practice No 11 asks for at least (i meters separation between LPG and petrol dispensers difficult to justify. For several years there have been a few licensed petroleum installations with the LPG and petrol dispensers close together and this is common practice in serveral European countries. As far as I know this has not caused any major accidents. Dispensers, either for LPG or petrol, do not contain massive amounts of material and there seems to be no greater risk from adjacent LPG/petrol dispensers than from several petrol dispensers close together.
3. Is the connection from dispenser to vehicle adequate?
Petrol is dispensed and flows into the tank from the nozzle by gravity, displacing air or petrol vapour from the fuel tank. LPG is forced into a closed system under pressure, compressing and liquefying the gas in the vapour space. In the event of aleak it will spurt out as aliquid, vaporizing immediately and if igni ted could cause a very dangerous fire. Even if unignited it can give a "cold" burn if it falls onto a bare arm or hand. Most modem fittings seem to be to a good standard, but they will need careful handling and regular maintenance.
The flexible hoses have to withstand a much higher pressure than petrol and past history of LPG suggest that these will be a likely source ofleaks. They should be designed to a d d -d well maintamed and lI1stalled so that they goo stan aI , cannot be run over by vehicles
4. Should break away couplings be fitted?
There have been instances of vehicles driVing away when t d nd fo r self-service I would deflI1ltely ask for connec ea.
h b 'nstalled but there IS also a good case for them at t em to e I all LPG dispensers.
r:: Sh Id pipework be above or below ground? .). DU
In the past both the HSE and the LPG ITA have preferred above ground pipework , but that IS be ca use most LPG lIlS tallations we re at indu stnal premises not on garage for e
courts. There have been a number of leaks from underground pipes, one caused an explosion in the cellar of a pub, the landlord was quite indignant, he did not even have gas, another (from a motor fuel dispensing facility) filled drains and telephone cable ducts with a flammable mixture for several days, but fortunately it was not ignited.
The advantage of underground pipes at garage forecourts is 0 bvious and I would suggest that if they are installed they should have some form of secondary protection, eg the pipe
can be in a concrete lined trench back filled with sand or the pipe within a pipe concept used, ie a inner pipe containing the LPG and an outer concentric pipe with a space in between monitored for pressure or for LPG.
LPG is a convenient fuel for motor vehicles and its use is undoubtedly increasing. It should not automatically be regarded as too dangerous to be on the same site as petrol but it does justify good installations, good maintenance and care in its handling and use.
Why should the use of liquid petrol e um gas for propel ling petrol engined motor vehicles increase now in the United Kingdom when the d eve lopm e nt for th e last five years has been comparatively slow ?
Should self service LPG stations be allowed and, if so, what safe ty standards should b e set when confronted with a potential inst a llati o n ?
Where can the Petroleum O ffi ce r go for bac kground in fo rm ation, advice and inform at io n o n la t est
Is there suit ab le foreco urt equipm e n t a nd technolog y avail a bl e to m ake se lf se rv ice LPG in sta ll at io ns a realit y now ?
The above qu estions are a ll o nes w hi c h n ee d to b e answered an d I will try in t h e following a rticl e to g ive sO lll e answers to th e m.
To set the scene, liquid petrol e um gas is d e rived from three so urces . It is the product of refining crud e o il. Lt is found a lso as a co nsti t uen t p a rt of n at ura l gas a nd it is fo und in assoc ia ti o n with nude o il on e x tract io n. Up tu nea rl y a ll th e LPG u sed in t hi s co untr y h as cullle fr um th e refin in g process , but p rog res si ve ly , w ith th e d eve lu pm e nt of th e Nort h Sea fi e ld s, m o re and m o re propan e is bE' in g brought as h ore o n th e Eas t Co ast of E n g la nd a n d Scut la n d Accurding to ex p e rt s, by t h E' m ajo r it \ of LPC w ill Iw ulming direc t from th e No r t h Sea
The two most common types of LPG are propane and butane. Butane is the type found in cylinders for camping and in mobile domestic heaters, and often found in blue cylinders. Butane has a higher calorific value and a lower pressure than propane, ideal for indoor application. The problem with butane is that it stops vapourising at about the freezing point of water and, therefore, you cannot extract vapour from the liquid when it is below 0° centigrade. This is why propane is the main product in this country for industrial, commercial and autogas usage and any applications which require larger cylinders. World wide LPG production is expected to treble by 1985, according to Oil and Gas Journal of 1 November, 1982, so product availability should not be a problem, particularly for propane as in the non-refining exraction about 60% ofLPG is propane. Butane may well be scarce as it is used in the refineries for increasing the octane number of motor spirit, to cut down lead pollution.
LPG is an expensive product to store as it either has to be kept under pressure or refrigerated and, therefore, it is logical that we should find applications where it can be used throughout the year and not just for heating use in the winter. product has a high octane value, is extremely clean IS It is therefore hardly surprising that many ountnes In the world are now looking at LPG as a viable to petrol. For instance, 10% of all passenger mIles in Holland and Italy are completed on LPG and 95% of :axis in Japan run on it. In the United Kingdom, for vanous reasons, we have been rather slow to recognise this market but now the situation, many believe, is changing.
The duty on LPG is half that on petrol and on enquiry some years ago it was stated by the then Chancellor of the Exchequer that this had been calculated on calorific value and, therefore, was on a logical basis. It is a matter of personal opinion whether the politicians want to alter the duty vis-a-vis petrol but many people feel as long as autogas IS mainly used by fleet and commercial customers and is not particularly attractive to the private motorist, the Government are likely to be satisfied with the Petroleum Tax that they will be gaining from the product not beIng wasted in the North Sea.
. The major oil companies are now showing serious Interest in developing the autogas market and have been waiting for Health and Safety authority to confirm the requirements for self-service LPG.
This is nearly complete and will encourage the major oil companies to put retail LPG self-service sites on to their stations which, in turn, will help to generate more LPG conversion interest from fleet users.
There are also rumours of a much advanced and simplified car conversion system which should be on the market shortly. Therefore, with product availability, with the right price differential, and With major oil companies getting involved, these are the reasons that many believe LPG will start to catch up with its usage in other European countries.
Cost-conscious fleet owners are converting their vehicles to run on either LPG or petrol at the flick of a switch on the and are claiming a 30'1" saving in their transport costs. Public utilities have also seen the advantages with poll ution control as an extra bonus as well as irradicating "stock loss"! '
What does the fleet motorist need to operate with LPG (4Iectively'?
Apart, obViously, from the conversion kit to his vehicle, whHh he should have installed by competent installers, he l)f ((lIlrSe n"fJllires a fast and efficient way of refuelling. He ("dd ha\,(' ,I lank and installation ill his()wn transport yard
but, obviously, this is not much help to him when his vehicles are away from base. Fleet customers are the biggest users of self-service petrol stations and, therefore, they will be expecting LPG to be dispensed by self-service along with petrol and derv.
Can self-service LPG be made as safe or safer than petrol which is already accepted?
With any new form of energy a very critical hazard assessment is carried out to see if a high enough standard of primary and secondary features can be incorporated to make the product application acceptable. Bell Gas Products Ltd. of Grimsby have just installed Britain's first electronic self-service major petrol company operated LPG stations for Total on the Al at Colsterworth, between Grantham and Stamford. These stations have many unique features which have been welcomed by the Health and Safety Authority and licensed by the appropriate Petroleum Authorities.
Let us look at these in detail.
In a modern electronic self-service forecourt installation there are usually five elements that make up the package.
The first is the pressure product storage tank; the second is the pumping, vapour separation and metering equipment; the third is the piping from the pumping equipment to the dispenser position; the fourth is the dispenser itself, and the fifth is the double reading console in the office.
Let us start with the storage tank. This is usually above ground but can be placed underground, should this be required. The tank should be placed so that the safety distances from boundaries, bUildings and fixed points of ignition are exceeded. It should be placed on a firm surface, well clear of combustible materials. It is usuall y therefore put on a concrete base with the valves protected from tampering by a fence. In the Al installation the tanker fill point is at one end of the tank at waist level, and the pumping gear is at the opposite end so that the tanker driver does not have to scramble over any pipework when filling. As LPG has double the expansion rate of petrol, LPG tanks are only filled up to an ullage valve level which allows enough expansion for all possible temperature conditions prevailing on the site.
It should be noted when there is a restricted space at the station and it is impossible to achieve the required safety distances that a radiation wall may be erected on one side of the tank, subject to the agreement of the Petroleum Officer and the local Planning Authority.
The second eler.nent is pumping, vapour separation and metering eqUipment .whlch Will get the product safety and accurately pumped mto the customer's vehicle tank. The conventional system is to have the pump and motor near to the tank and the vapour separator and meter in the bottom part of the dispenser. has many disadvantages and few, if any, advantages as It means you have to have both liquid supply and v.apour pipes all the way from the tank to the dispensmg pomt, as the vapour separator and meter are in the bottom of the dispenser. This system has a tendency not to operate effiCiently in some temperature ranges and also, s.hould a break through the safety barriers and demohsh the dispenser, an unnecessary amount of product is put at risk. The Total sites are fitted with the latest Brabantgas single pipe system which operates in a completely different way; the pump and motor, the positive displacement meter and the vapour separator are all contained one unit placed just outside the direct shadU\\ uf the tank. r hiS allows consider-
able reduction in the amount of pipework required, and the liquid supply pipe in particular should be as short and direct as possible, to cut down the possibility of cavitation.
The whole modular "pump measuring unit", as it is called, is placed at the opposite end of the tank to that used by the driver for filling. When, and only when, the vapour has been extracted from the liquid is product measured and the pulsed signal of measurement is sent to the dispenser position and to the office console, and the system requires only a single pipe to convey the liquid to the vehile.
This is come upon the third element, the liquid supply To LPG onto a self-service petrol fore.court It IS deSIrable to have the dispenser placed so that vehIcles can pull up on either side, and this means that the pipe has to go underground. As LPG is heavier than air it finds the lowest point and therefore it is vital this underground liquid pipe should have excellent primary safety, should be constructed from top quality materials to stop any leak occuring, and should be protected so that the contaminants in the ground do not erode the pipe; and preferably have a secondary safety feature that should a leak occur the leak can be contained in a safe area.
The Total Al installation has a piping system of the most advanced type in the world. This consists of a double concentric pipe system where a vacuum is maintained between the two if propane escapes from the inside or if the outer plpmg IS damaged, the vacuum disappears. This closes the supply valve instantaneously and automatically.
The of this system into the United Kingdom by Bell IS Just a sign of the safety considerations which are taken mt.o ac.count in the design stage to help maintain the extra.ordmanl y high safety record of LPG generall y and autogas m particular.
The fourth eleme t' th d' . . n IS e Ispensmg Ulllt. The Brabantgas dIspenser IS very h' 1" 11 bl d . muc slmp Ifled for apart from a sma pIpe feeding the pressure gauge no part of the gas
am IS above the island level, apart from, of course, the ose and nozzle. Under the dispenser there are 3 gas safety valves. There is a standard hand valve which is normally left open' there' .' IS an excess flow valve for emergencies, but, as an integral part of the Brabantgas system IS ItS electro-magnetic cut-off valve which is fail safe in that it is closed except when the dispenser button is pushed to dIspense gas into a vehicle. On the Brabant dispenser gas will only be dispensed whilst your finger is on the stop/start button. Immediately your finger is removed the electro-magnetic valve at the bottom of the dispenser closes a.utomatically and the flow of gas stops. People have complal.ned that they do not want to keep their finger the whole time on the button while dispensing gas, but with flow rates of :-30-50 litres per minute the time required for doing this is not excessive and it does ensure that the attend.ant or customer is always in control of the filling operation. He cannot stroll off and do another job in the middle of the fill. With this system, in the event of a hose leaking the pumping would be stopped immediately, thereby minimising the risk.
A particular safety feature of LPG is that it is delivered in closed circuit system, the hose nozzle is attached to the vehicle by screwing it on and the gas valve will not open unless this is correctly connected to the vehicle.
The dispenser comes complete with its own steel framed island "vith crash barriers, good illumination and "vith the appropriate safet v signs. The dispenser itself is made out lIf
heavy duty steel and it is installed in such a way that should the dIspenser be knocked over by a vehicle, the break point is above the level of the gas train. As there is no meter or vapour separator in the dispenser hosing, from a gas safety point of view the incident is of minor importance. The Brabantgas self-service dispenser is fitted with a low level hos.e retractor. This is to stop the hose being run over by a vehIcle, and also to keep the hose at the right level for th.e break which is incorporated to act efficiently wIthout damagmg the dispenser, which has been known to happen with some of the high line hose systems.
The break coupling mentioned previously is built into the hose, is self-sealing on both parts and is re-joinable by the forecourt staff. This safety feature is buil t in to cater for the absent-mined motorist who drives off while still connected to the hose.
As the dispenser is electronic, it is a simple matter to carry out a change of price.
The fifth element in this self-service LPG safety system is the console in the office, this not only gives a double reading oflitres taken by the customer and the price to be paid, but completely controls the filling operation. When a customer removes the nozzle from the dispenser the reset buzzer and light are activated. The operator pushes the reset button and zeroes the read-out on the console and on the dispenser, and allows the customer to start the pumping procedure by way of the stop/start button. Should the operator want to stop the delivery for any reason, they can use an override switch on the console and can give instructions to the customer over the tannoy system which is installed on the site.
All in all, this is a station of the future and wi th an installation of this type the fears of some Petroleum Officer5 about self-service LPG should be much reduced.
With so many technological advances over the last few years most of the Guide Notes and Code of Practice are outof-date, making it extremely difficult for a Petroleum Officer, and other interested parties, to get current information. Fortunately, this situation is now being remedied as the Liquefied Petroleum Gas Industry Technical Association (LPGITA) and the Institute of Petroleum are at present up-dating their Codes and we understand that the Health and Safety Executive are preparing and issuing up-to-date guidance notes.
If I can make a plea from the industry t.h.e .Petroleum Officers, it is this. Your jobs and responslbliltIes cover a wide spectrum and nobody can be an expert on everything, keeping up with fast-moving technological advances in every specialist activity, particularly if they have not come across them before in their area. The specialists in the industry are only too willing to give any advice to Petroleum Officers that may be required as it is in the interests of all those involved in the responsible development of the LPC automotive market to ensure that the current safety record is maintained. '
BelIamy is the Managing Director of Ht'll Cas I roducts Ltd., bulk LP(; distributors from the Humber side area. Mr. Hellamv is a council nH'mbt'l" ut" the and his are the lTK cllnn'ssionaires tor the Brabantgas Electronics LPC dispt'nsing system.
Bell Gas Products Lld are at East Marsh Strt't't, l;rt'<I1 Crimsb" South Humberside (0.172) .'H I H I
The subject of "Vapour Recovery", the collecting of volatile vapours during the transfer of gasoline or bon product, is one which is being given an .mcreasmg amount of thought by major oil companies, both m the U.K. and continental Europe.
The practice of controlling or recovering vapours has been common in the USA for many years, where oil marketing companies have had to decide either to bum them off or recapture them. In both cases equipment to the vapours is necessary. There are various options aval.lable when making a decision between combustion techmques and processing systems. Most of the processing systems have been developed in the U.S.A. (one in Italy), and examples, currently on trial, exist in oil company loading terminals throughout Europe, and two are planned for the U.K. during 19W2I83.
Opinions on the economic advantages of recapturing vapours vary widely and depend on the cost of the product and the cost of the equipment needed to collect and to process the vapours.
I · h .. I d 'be the method cur- t IS t e purpose of thiS artlc e to escn rently used by most existing installations, wh.ere top-loading of the road tank vehicle is standard practIce, to collect those vapours coming out of the road-tanker.
In any typical top-loading procedure, at product is dispensed through either 3", 4" or loadmg arms into vehicle compartments at rates varymg from. 1000 IImin to ()()OO IImin. To prevent potential gen.eratlOn of static electricity, associated with splash loadmg, droptubes are designed to touch the bottom of the vehicle compartment.
During this (splash) loading, a vapour/air mixture is displaced by product through the hatch into atm?sphere, at the rate of (about) one litre of vapour per one lItre of product.
When vapours are collected and the loading takes place in a tight system, it is generally accepted that 95% or more of the available vapour can be captured during the loading sequence. By collecting the vapours to this extent, two distinct advantages are achieved:
I) If vapours can be processed and be put back into the storage tanks in the form of liquid product again, a possible pay-back advantage can be gained.
L)This would also mean a positive contribution to the impOI'tance energy conservation effort.
The ()PW Division of the Dover Corporation, through its European office Dover International B.Y. manufactures a 4" Vli4-FV loading arm, which has successfully the, task of collecting vapours for more than 10 years III the U.S.A. Trial arms are currently installed at numerous Road loading terminals throughout Europe, including '2 in the lJ.K.
The V 'li4-FV loader consists, in essence of a 4-" product ann, and a :i" vapour return arm, in tandem or"Piggy-back" lI1('orporated in one unit. The loading outlet and vapour wf Ilrn line both operate through the vapour-head or"Plug" S('I' rllllsl.) which seals thf' tanker hatch by means of a Buna 1,lilSIOIIJl'r noating collar or shroud_
The entire loader is air-operated, and controlled by a single air control valve. Opening and closing of the loading valve is automatic, and can be overridden in case of emergency. Raising and lowering of the arm is by air cylinder.
The operation cycle is as follows:-
The operator actuates the arm down switch and the loading arm will start to travel downwards. All the operator has to do is toguide the vapour cone into the manhole. Once the vapour cone has made a tight connection in the manhole, a pneumatic signal will open the main valve.
During loading, the generated vapours are displaced by the inflowing product at the rate of one litre of vapour per one litre of product. Since the system is absolutely tight the saturated vapour is well above the igni tion zone. This eliminates the ignition hazard normally associated with splash loading through open tank hatches.
A vapour check valve in the vapour return line will prevent vapours from flOWing out of the vapour collection system when the loading arm is lifted off the manhole, or is otherwise not in use.
As the operator truck driver can not see the liquid level in the tank, an automatic level shut-off system is provided. This is a pneumtaic sensor located in the vapour cone. When the liquid level reaches this sensor and floods the vacuum sensing port (like the automatic nozzle on a service station) the main valve will close. The system is just as reliable as the automatic service station nozzle now in common use, on every service station in the U.K.
In normal operation the liquid level sensor will not be submerged since the pre-set meters at the loading rack will shut off when the selected quantity is reached. It is only in case of error that the sensor will shut off the loading valve e.g. when the operator has selected a larger quantity than the tanker compartment can hold or when there is a quantity of petrol left over in the truck. The pneumatic sensor in the vapour cone does not only shut off the valve in case of high level signal. If the pressure in the tank builds up to '2 psi (140gr/cm2), the sensor will also shut the valve and stop the loading procedure. This could happen when the vapour return line was blocked or if there was liquid present in the vapour line.
The whole pneumatic system is self contained. New technology had to be developed to control all operations of the OPW V -04-F pneumatically in order to avoid installation of electricity in hazardous areas. FollOWing safeties are built into the system; the main valve will shut off:
a. when liquid reaches level sensor b. when vapour cone is not properly located in the manhole.
c. when vapour pressure in return system exceeds 140 gr/cm" d. when loading arm is in e. when loading arm is in stop position
The outlet of the loading arm, the vapour shroud, contains both the tube for the outflowing product as well as the return line for the vapours. A droptube to reach the bottom of the tanker is not necessary, as the whole loading operation takes place in a fully saturated vapour atmosphere. A short droptube, detachable, is available to reduce turbulencf' in the tanker in order to achif've a more accuratf' shut off.
The pr?blems of handling flammable materials in industry dIverse and require many different solutions if safe workmg are to be achieved. Electrical hazardous area claSSIficatIOn, as it is usually understood, deals with a part of the problem. Health and Safety at Work m the UK requires the employer to consider safety m a wider context. As part of the approach by the employer to meeting this legal requirement, the danger of atmospheres being ignited must be evaluated ean . . d h ' '. ng m mm t e consequences of such an event. Plants, IS sug?ested, may be divided into "dangerous", "safe" and potentially dangerous" regions. The division of plants into such is seen, primarily, as a Chemical Engineering functIOn. The paper suggests definitions for such regions which would be fundamental to overall plant safety and apply to all sources of ignition. Present practices of hazardous are classification would fit readily into the proframework. The concept would allow wider latitude m equipment selection, recognise the influence of physical, chemical and economic factors and would not lose sight of the realistic safety issues.
Industry is diverse in the United Kingdom varying from of the largest industrial complexes in the world with sophisticated technology to the one man operation. [he handling of hazardous materials is also diverse. Complex petrochemical plants contain large inventories of flammable liquids posing potentially substantial hazards and yet it is encouraging that so few accidents with hazardous materials occur in these premises. It is, perhaps, in the industries where these materials are processed or handled, inCidentally to some other activity, that the accident record is less satisfactory. Batch paint making, coating, spraying and small container filling, not to mention the handling of petrol by mechanics in garages, regularl y claim their victims. Large firms often operate on a seven day week, hour shift basis and much of the equipment is designed and installed "in-house" by qualified and well supervised staff. Small firms are more likely to start up and shut down plant on a daily basis, to buy equipment "off the sheJr', and may not have available to them the expertise necessary to analyse the problems inherent in the classification of hazardous areas of the purposes of installing electrical equipment. How are these firms to be advised to ensure that they meet the requirements of the Health and Safety legislation? Incidents, such as the Flixborough disaster, are cause for concern, but of equal and continuing concern are the accidents typified, for example, by that of the woman who worked in a factory that made tobacco pipes. Her job was to clean pipe bOWls and stems before they were lacquered. She sat at a picked up the bowls, dipped them into a small jar (,f alcohol, shook off the excess and placed them back on the hell. ()ne day the jar of alcohol tipped over her skirt. She walh·d over to an electric fire and was burnt to death in the pnslIing fire
This paper was presented at the Third International Conference on Electrical Safety in Hazardous Environments at The Institute of Electrical Engineers in London on 1st December 1982. The difficulty of the Authority charged with enforcing safety legislation lies in the fact that large employers, with considerable inventories of flammable materials, seldom contribute to the day-to-day statistics of death and injury to people from this hazard. Rather it is the small user that has the fatal accident. Hazardous Area Classification, as it is presently understood, has little impact in the small userpremises where, perhaps, precautions are most needed.
Another. aspect of the can be seen in the report by the Tnbunal of mto the disaster at Whiddy Island. The report descnbes how large sections of the Offshore Platform Area were reclassified in 1976 as Division 0 by the owners. It seems the high requirements of this classification were not practicable on the Platform. As a consequence, the standards of electrical equipment installed appear to have fallen away. This was identified b th Tribunal as a shortcoming. y e
It is appropriate, therefore in our view that fro t' .' ' "m Imeto tome, the Issues mvolved should be reviewed and 'd . gUI ance given on the problems and difficulties of hazardo I 'f" fr us area c aSSI IcatIOn as It a Iects safety at work.
Legislation in the United Kingdom designed t h h I h r d ' 0 secure t e ea t ,saIety an welfare of persons at work d' h H I h d S r ' IS con- tame m t e ea t an aIety at Work etc Act 197 Under the Act the Health and Safety CommissI' . 4. . on IS ap- pomted by the Secretary of State for Employment" such things and make such arrangements as it consI'd to do . h ers ap- propnate for t e general purposes of securing the heal t safety and welfare of persons at work" as expressed i p h, of the Act. In turn, the Commission appoints the 1 Safety Executive to enforce the Act, to recommend R nd tions to the Secretary of State, and to draft C Practice. Codes of Practice, if approved by the Corn 0 of b d . ., I d' mISSIon are able to ekusfe mgs. Act from the wor 0 t e 0 ens ommlttee on Safet Health at Work (l9T2) which CritiCised thY . . d e t en multiplicity of prlovIsIOlns adnbrecommended that they should be progressIve y rep ace. y a system afRe ulations and Approved Codes PractIce operating in bination. The Robens saw health and safety as essentially self-regulatmg, based on a consultative pr . ocess between labour and management WIth other inte d rested Parties such as the Health an Safety Executive T h' , ' 0 t I end the Health and Safety at Work Act lays down b d s , d d roa req uirements for employers an oes not contain. " , Id' speCifiC legal requdlfe,ments re ate d to , pasrtrc,ular processes, The PrinCipal utIes are con tame In ectlOn '2 and' t ' f ' I requires employers to ensure, so ar as IS reasonably practicabl health, safety and welfare at work of all their em I e, the " d h' I P oyees
The SectIOn expan s t IS duty specifically by Ing' that the employer must, so far as IS reasonabl,; , '", I practicable, proVIde and mamtam hIS plant and Syslems of work, so
as to be safe and without risk to health. The phrase "so far as reasonably practicable" is most important and, in the context of earlier legislation, the standard of reasonable practicability has been defined in some detail by decisions of judges in court. To paraphrase those judgements, the standard of reasonable practicability requires the employer to consider the risks and the consequences on one hand, and the cost in time, trouble and money in dealing with that risk on the other, and, ifit is shown there is a gross disproportion between them, ie, the risk is insignificant in relation to the sacrifice, the employer discharges the onus upon him. This computation, it should be noted, needs to be made before the event. The courts have, historically, set a high standard for this duty.
Within the United Kingdom the Health and Safety Executive are concerned with enforcing requirements so that the duty of care for people at work under the Act is met. What then is an appropriate standard of safety? The question is quite properly put to enable Inspectors, people in industry, the general public and other interested parties to operate within the Act. There are, as yet, no "Approved Codes of Practice" for hazardous area classification in the sense envisaged by the 1974 Act. Undoubtedly, each group of persons, even individuals within groups, may have differing views on what standard is appropriate in a particular situation, but the standard usually sought is a definition of that which seems appropriate to the HSE as the enforcing authority, with the courts, ultimately, being arbiter.
The transition from the older and more specific legislation to the HSW Act is, necessarily, a slow process and in the of earlier law there are requirements which are still applicable. In particular, the Electricity (Factories Act) SpeCIal Regulations 1908 and 1944 are statutory to certain premises, principally factones, defmed m the Factories Act 1961. Regulation 1 places a general duty on an occupier to ensure "all apparatus and conductors shall be sufficient in size and power for the work they are called upon to do, and so constructed, installed, worked and maintained as to prevent danger so far as IS reason.ably practicable". In a sense, this Regulation begs the questIOn posed earlier as to "what standard?" for it again reasonable practicability. However, RegulatIOn '27 reqUIres that "all conductors and apparatus exposed flammable surroundings or explosive atmosphere shall be so constructed or protected and such special precautions shall be. as may be necessary adequately to prevent danger m vIew of such exposure or use". In its published view* the Health and Safety Executive states that "to ensure a satisfactory standard of safety apparatus in conformity with British Standards should be used."
Again, specific legal requirements for Factories Act premises may be in, for example, the Highly Flammable Liquids and LIquefIed Petroleum Gases Regulations 197'2, where Regulation!) deals with sources of ignition and states "no means likely to ignite vapour from any highly flammable liquid shall be present where a dangerous concentration of vapours from highly flammable liqUids may reasonably be expected to be present". "Highly flammable liquid" and "a dangerous concentration of vapours" are defined terms in the Highly Flammable Liquids Regulations, the former is based on flash point and the latter defined as a concentration greater than the lower flammable limit of the vapour. The requirement, under Regulation !l is similar to Regultion '27 of the Electricity Regulations save the duty appears to be less than absolute in the sense that there has to be a reasonable expectation of a flammable concentration, At first sight, this may seem a relaxation in the stan
dard, but Regulation 9 does not stand alone and should be considered with other parts of the HFL Regulations that deal with standards for storage, precautions against spills and leaks, the prevention of escape of vapours, and the dispersal of dangerous concentrations of vapour.
These, then, are the basic legal control measures intended to reduce to a minimum the uncontrolled release of highly flammable liquid or vapour and its subsequent ignition.
In addition to the legal requirements, much practical information on safe practices in handling flammable materials is available in British Standards and published Guides. Guidance is published by many organisations by firms for their own use, by industrial associations and by Governmental bodies. Examples of such guidance are as follows:-
1. Electrical Installations in Flammable Atmospheres (RoSPA/ICI Ltd, Publication No. IS91, 1972).
2. Guide for the Storage and Use of Highly Flammable Liquids (Chemical Industries Association November, 1977).
3. BS5345: 1976: Code of Practice for the Sections, Installation and Maintenance of Electrical Apparatus for Use in Potentially Explosive Atmospheres (British Standards Institute: 1976).
* Memoradnum on the Electricity Regulations. Health and Safety Executive. HMSO London 7978.
4. Marketing Safety Code Model Code of :ractice Part 2 (Institute of Petroleum February, Ll/8),
5. The Storage of Highly Flammable Liquids Note Chemical Safety '2 (Health and Safety ExecutIve 1977).
<i,Petroleum (Consolidation) Act 1928 Model Code etc (Part 1) (Home Office HMSO 1971), r Much of this guidance deals with t.he h dl ' d storing of flammable matenals and only mClan mg an I ,'f' . dentally with the detail of hazardous area c. assl IcatIOn, Many of the Codes have achieved a substantIal deg:ee of t b bo th industry and the Health and Safety accep ance y 'f' , ,E t · b t where hazardous area classl IcatlOn IS 111xecu Ive, u I volved, the detail remains complicated and controversla . , fal observer would find the contents At present, an Impar Id' f h ' d' 'd I Code of Practice to be coherent an ,111 o eac m IVI ua r most cases a arently straightforward to apply, r, h ,pp t' made to compare different Codes, or owevler, an atttehmp to a particular plant or process, the to app y more an 0 W'd 'f anomalies and discrepancies soon appear, I, e "ana IOns 'f h' le hazards as vents, or drams, and e\ en eXist or suc slmp' ", I ' ' for these a straightforward companson IS Virtual y I,mpos'bl A' le example taken from some of the gUIdance SI e, Sl1np , -d that is available may serve to emphasise the pOint. Cons) a fixed roof storage tank handling highly flammable hquid:-
Guidance Note CS 2 (HSE):
Division '2 vertically from ground level up to '2m abllH' the tank connections: horizontally 8m from tank l'onnel' tions or shell.
"Electrical" Code of Safe Practice (IP):
Division 1 3m above the tank shell extending horizon tally ISm or to bund wall vvhil'hever is greater. Bt'Yond :im from the tank shell horizontally the division nw\ Lw H' duced in height to 4' 'm abo\'e gl:ound len'l, III tu tht' Iwight of the bund wall whicheyer is the greater.
Zone I 3m above tank vents and 3m from the tank shell, extending to bund wall and height ofbund at ground level: Zone 2 horizontally Srn above ground level extending a minimum of 2.Sm to Srn beyond bund wall, depending on tank size, providing the distance from the tank shell is not less than 6m to ISm depending upon tank size.
On the other hand, the scale of the range of industrial undertakings perhaps is such that no single practical code can be expected to cover them all. It is cl earl y desirable that recommendations relevant to definable industries or types of installation should be available, but it is equally important that they should be seen to be derived from a common basis and thus compatible with each other to give levels of protection that are equivalent, or levels that differ with the justification based on the scale of hazards presented.
BS5345 is intended to be a Code of Practice to cover the installation of electrical apparatus and Part 2, yet to be published will deal with the classification of areas. The gestation period of Part 2 has been long and the drafts that have been seen are couched in terms of broad generalities, giving an approach to hazardous area classification, within its terms of reference, that is excellent. Regrettably, the text will offer little practical help to the smaller firm and the formulae presented in Appendix "A" of the Standard are well beyond the ken of the average small user of flammable liquids and gases. It is to be expected that the Simpler Codes will probably remain in use for many years, even at the larger installations, and perhaps indefinitely at other places where substantial fire and explosion hazards exist.
Com.pliance with the HSW Act implies a requirement of safety III the design, installation, operation and maintenof plant. In exercising its role as the relevant enforcing authonty, the Health and Safety Executive must and does look at the safety of any particular process or proposal as a whole. The input from relevant disciplines must be seen to be co-ordinated with the appropriate emphasis and to have drawn correctly from relevant guidance. The decisions taken at all stages must reflect appropriately the nature and SIze of the hazard (ie, the consequences of failure) and the risk (ie, the probability of occurrence of this failure).
The fire and explosion hazards associated with flammable materials can be minimised and controlled by the pnnCIples of safe location, containment, safe handling of spillage or leakage, ventilation and the control of sources of ignition, or, in more general terms, the avoidance of the simultaneous co-existence of fuel. oxygen, and a source of igni tion. In the context of sources of ignition, the control of electrical sources is only one aspect and, logically, the relevant decisions should be applied to all sources. Thus, the imposition of expensive electrical protection at a plant where, for unavoidable processing reasons, large sources of Ignition are continuously present, may be anomalous, and other means can be adopted to give an equivalent degree of safety. Equally, the regular uncontrolled introduction of mobIle Sources of ignition into an area within which the electncal equipment is protected is also an anomaly which, regrettably, is frequently found by Inspectors.
An example of this recently occurred when a solvent recovery plant in the North West caught fire and the resulting destroyed the building and resulted in a fatality I he stills fi)r the room were installed in a plant "fully flame· proofed" ilnd indeed the room was referred to as the "flamepn)(,j J"()(Jrn" within the common parlance of the factory. W hell 111(' ("()oli ng water on tlw condenser failed, flammable VdP'"J1 ('sc<qil'd into that J"(J'Jrn. It was ,I regular practice in
the factory to use an unprotected forklift truck in the room and, although it is thought a nearby boiler, in the particular incident, caused the ignition, the forklift truck was regarded as a particularly "hot" second favourite.
There is, associated with any plant or process, a continuous spectrum of fire hazard arising from any particular source of flammable vapour and ranging from an area of high hazard in its immediate vicinity, through areas of reducing hazard, to a safe area at a particular distance. There is, similarly, a spectrum of protective measures in the context of the control of sources of igni tion, including the range of methods for the protection of electrical equipment. The problem of Hazardous Area Classification, as currently revolves round the relationship chosen for the matchmg of these spectra and the degree to which factors, such as the probability of ignition, are taken into account.
To allow safe of a wide ra?ge of electrical apparatus, plants are claSSIfied for economIC and technical reasons into three zones pi us an implied 'safe' zone. We propose that for non-electrical ignition hazards and as a starting point for the classification of plants for electrical purposes, chemical engineers should consider dividing plants into three regions namely dangerous, safe and potentially dangerous.
It is generally accepted, we suggest, that those parts of a plant, or process, which will, during normal operation, contain a flammable gas or vapour are easily defined by physical plant limitations, such as the vessel and pipe walls. Equally, those areas of a plant which may, during normal operation, discharge a flammable gas or vapour and give rise to a flammable mixture are readily defined, given that some estimation or calculation is required to define the limits of the flammable mixture with accuracy. Such items as vents, drains, etc, are included in this category. The area round these parts of a plant is readily recognised as dangerous and deserves, a priori, a high standard of protection against sources of ignition. Thus, in the context of an overall strategy for safety, we may define a "Dangerous Region" as a volume or space within which f1ammable gases or vapours are present continuously, or within which a combustible mixture may occur as a feature of normal operation, and from which sources of ignition should be excluded.
It is also generally accepted, if only by implication, that it is possible to define, by calculation or othenvise, those parts of a plant or process whIch are so far from sources of hazard that the need to take any precaution against sources of ignition may be discounted. Thus, in the context of an overall strategy of safety, we may define a "safe Region" as a volume or space within which the presence of a combustible mixture is so unlikely that the probability may be Ignored and precautions are not necessary to control sources of ignition.
Turning to the remainder, the region falling between "Dangerous" and "Safe" regions, we thiS be called the "Potentially DangerouS RegIOn and denve ItS definition from the others as a volume or space within which a combustible mixture is only present as Cl feature of abnormal operation, and within which sources of ignition should be controlled to take account of such abnonnalities in an appropriate manner. It is, as its name implies, a region which is normally safe and free from flam· mable mixtures, but, where, because of the nature of the process, and the many other factors taken into account, it is accepted that a flammable mixture may occur. In such a re gion, an appropriate degree of control over sources uf igni li()n is considered to be necessary as a ,·oI1sPljuence.
The regions are defined in such a way that their delineation is, primarily, a Chemical Engineering responsibility as part of an overall safety strategy. The first objective of the safety strategy would be to identify potential sources of hazard and to minimise the escape of flammable vapour from such sources by either eliminating the source, or by reducing the rate of release of vapour. The second objective would be to ensure the selection of practices to control all sources of ignition within each region by the proper application of the relevant engineering discipline depending upon the type of ignition source. Broadly, it would be an Electrical Engineering responsibility to select appropriate electrical equipment, whilst it might be a Mechanical Engineering responsibility to designate control over other sources of ignition.
It might be envisaged, for example, that the Dangerous Region would contain electrical equipment as currently specified for use in Zones 0 and 1, the region being sub-divided for the purpose on the basis of the Electrical Engineering considerations of equipment performance and the Chemical Engineering considerations of the nature of the hazard. The potentially Dangerous Region might contain electrical equipment as currently specified for use in Zone :2, or it may be that other considerations apply.
The terms "normal" and "abnormal" are not quantified since they are seen, in the context of the regions as defined above as variables whose significance would depend upon the circumstances. The decisions made in respect of each region need to take into account the probability of the occurrence of a flammable mixture as well as the probability and consequences of its ignition in the context of practicability. Decisions may be particularly diffIcult 111 the Potentially Dangerous Region, but it is suggested due prude.nce should always be exercised, so far as is practlca.ble, particularly with respect to situatl?ns where very senous consequences would arise if the igmtIon 0: an escape occurred. For example, it may well be appropnate at plants of high hazard but low risk to install equipment in the Potentially Danagerous Region to the standard of Zone I.
The approach of the British Gas Corporation to Hazardous Area Classification on the methane terminal at Canvey Island is of interest in this context. The terminal was inspected by Health and Safety Executive in detail in 19R 1, and with the permission of the British Gas Corporation, the following details can be made available:-
When the site was first developed for the storage of liquefied natural gas in 1D(iO, the then current philosophy was followed and. large areas were designated where only flameproof electncal equipment was allowed. In 1!l7S, the produced internal guidance on the application 01 Hazardous Area Classification and the Site Vias on this basi.s new Zones 1 and:2 were slightly dIfferent from the ongll1alflameproof areas and, over the years, this resulted in variations in the standards of maintenance in the installation of new equipment, and in the control of access by vehicles to the hazardous area.
In 19R 1, the Corporation reviewed the application of the original 1m!) guidelines to the site and realising that difficulties had arisen in interpreting the distinction between Zone 1 and:2 decided to combine the Zones 1 and :2 on the terminal as a single "region" wi thin which Zone I standards would apply to the control of both electrical and other sources of ignition. By installing new electrical and other equipment, where appropriate, a higher degree of protection than had been the case in I UH I was achieved. The Cor
poration decided that the advantages of this approach outweighed the drawbacks in the circumstances of the particular case. The disadvantage of "blanket zoning" of this type cannot be denied. Maintenance of flameproof equipment is invariably costly and the implication of the blanket Zone 1 approach on the overall control of other potential sources of igni tion, if properl y applied to a similar degree, can be very restrictive. Nevertheless, we believe the approach used by the Corporation has many advantages and their experience with it in the next few years can be expected to yield much useful information.
In the 1981 review the Corporation identified about :20 major anomalies. The problems were resolved by taking such steps as moving a road, removing walls from compressor houses, the wider use of gas detectors, and the use of calculation methods to define the position more precisely. In addi tion strictly applied systems of work were extended to control access by vehicles.
The framework of regions in the approach we are descri bing contains flexibility for professional decisions to be reached within it by each and every discipline involved, taking all the relevant factors into account. The valuable data and guidance existing within many current Codes can be readily used, as can calculated val ues, in appropriate circumstances. The widest use can be made of advances in equipment design, as they occur, by the relevant High standards can be adopted for those plants whIch justify them on the basis of risk analysis, while the hazards posed by many smaller users can be rea.dIl.Y accommodated within the same framework With realIstiC results,
The concept of regions as described is, it is no more than a formal expression of current best practIce, as used in many premises in an mann.er.. If applied, it laces the selection of electrical eqUipment 111 Its context as albeit an essential part, of an strategy in many disciplines should glvlllg
'I' f d to operate WI thll1 a defllled frame\,> ork dnd Cl p 1I1e ree om " with the application of profeSSIOnal Judgement.
At the 1m!) Institution of Electrical Engineers Conferh ' b' t concern was expressed about the legal ence on t IS su , , , f C des and Standards and the attitude of the posItIon 0 0 Th ,I ' H I I d S f t Executive to\\'ards them, e e\ 0 utlOn ea t 1 an a e y _ _ . f II f" f g'uidance since UJ/;l has done lIttle to Imo a Olms 0 " l-lSv I 't t' alld tor vanous reasons, prove t le SI ua 1011" " "Approved" Codes of Practice on thiS tOpIC have to 1'1 ' ft eems to be a danger that the I eal alms appear. lel e 0 en s " f'" h f Hazardous Area Classl Icatlon are of t e exercise 0' I d d b d ' discussion, \Vhile some f Jelds, suc 1 ciou e yaca emlc, '. ..' '11' h' f I tl 'ltectlOn of vehldes, <11 e Stl 111 t ell as, or examp e, le pit " I'. I' d I the protection 01 electnca Items 0 eve opment stages, . I I' ,I d advanced staO'e ot deve ollment, eqlllpment 1as Ieae le ,". , , reliability and range 01 chOice. 1 he baSIC questltln, hcm t \' I'th d ., IfprotectionrequiredforapartJcularloca- er,o e egleec " tion is, a matter of judgement relined by expenence, expertise and logic.
The definitions of Divisions and, more recentl \, Zoncs 0, I and:2 have remained substantially unchangecl for (lvcr years and have, generally, been limited in applic<ltit)J1 to the of electrical equipment for a giH'n ancl c1elllH'eI ha zardous area, Regretlabh, Coeles of Pract ice c()nta i ni llg IT commended seized upon, often (lut ()ic(ll1tcxt. as "tablets ofstllne", \\hilst their preambles cuntaining pro visos about the reduction of emissions, the zUl1i 1112. 1)\ ,lgn't' lllent between clillert'l1t disciplines, and thl' Ilt'l'cl tu regarcI
such distances as minima, are all virtually ignored in the haste to obtain a classification of area so as to order electrical equipment, in contrast to the real aim of plant protection and consquent safety.
Attempts to develop universal Codes, such as BS 5345, on the basis of distinguishing clearly between Zones 0, 1 and 2, may have bedevilled and obscured the true objective of overall safety. The distinctions are artificial and subject to not only considerations of physics and chemistry, but also to those of economics, of scale and maintenance. In reality, the Zones, as defined, shade into one another and the boundaries are matters of individual and detailed consideration.
It may be time, constructively, to challenge this approach and to widen the discussion away from the narrow field?f choosing electrical equipment, important though that IS, and into the area of overall safety. There is, it is suggested, a fundamental issue and that is the reality of danger. The draft of BS5345, Part 2, within its terms of reference, ie, the classification of hazardous areas for the purposes of installing electrical equipment, suggests that a multi-discipline team is involved at the outset to define such areas. The contention of this paper is that such a team, consisting of chemical, mechanical and electrical engineers, among others, should have broader terms of reference and define three regions of a plant:-
A DANGEROUS REGION defined as a volume of space wi thin which flammable gases or vapours are present continuously, or within which a combustible mixture may occur as a feature of normal operation, and from which sources of ignition should be eliminated.
A SAFE REGION defined as a volume or space within which the presence of a combustible mixture is so unlikely that the probability may be ignored and precautions are not necessary to control sources of ignition.
A POTENTIALLY DANGEROUS REGION defined as a volume or space within which a combustible mixture is onl.>' present as a feature of abnormal operation, and within which Sources of ignition should be controlled to take account of such abnormalities.
It is the potentially dangerous region that requires the app!ication of considerable expertise and competent professIOnal judgement. It is this region where the balance has to be found between the hazard, ie, the flammable atmosphere, the risk, ie, the probability of ignition and the conseProcess plants will present unique problems and it IS only to be expected there will be unique solutions. The to "regionalise" a factory si te handling flammable matenals should be a stimulus to the designer, plant operator, safety fr d o Icer, managers and electrical chemical an mechanical en . ' . ' . d h I gmeers, to concentrate their mm son t ere evant. features to ensure plants are designed, operated and mamtaned w'th f . h . I sa ety m mind. For relevant reasons, t e rebe sub-diVided in terms of Zones for the ins(af tahtlOn of electrical equipment when it becomes the duty ) ose s . , st d ,0 mv.ol ved in that decision to ensure the overall an ard of saf t h' h cessar I e yac leved is not impaired and that t e nedca culations and systems of work are detailed and e So that .t d ' . I oes not become impaired m future.
July I
,;. nu views expressed' IlwJf o/the authors thzs paper, and in particular 4, are flllllI Ilm/111 and S· ,F. are not to be construed as necessarz(y those aJety Executive.
The eMS 2000 gauging system is not a 'mechanical dipstick' it is an effective stock control and management system.
eMS gauges based on ac:vanced technology pioneered by Smiths IndustrIes for accurately measuring fuel in some of the worlds most advanced aircraft. It is this technology that the eMS 2000 brings to today's forecourts.
The unique eMS incremental fill method of calibration. involving the use of specially developed eqUipment and sophisticated computer programmes. ensures that the eMS 2000 system is so accurate that it c.an performance of pumps and. for the fIrst proVIde effective forecourt management checkmg on what is delivered into the tanks and what goes out of them.
That.s its in daily use with major oil compames. dIstrIbutors and independent retailers throughout the UK.
The eMS 2000 puts management in control of its liquid assets.
"Ill habits gather by unseen degrees
As brooks make rivers, rivers run to seas"
The number of petroleum licences again fell during the year, with the closure of uneconomic petrol filling stations. This was offset slightly by an increase in paint spraying services. All too often these were discovered, unlicensed, by officers and then had to undertake alterations to confonn with safety requirements. In most cases it would have been cheaper, as well as safer, and not illegal, for advice to be given prior to initial construction.
Inspections were also at a fractionally lower level, primarily due to the illness of one of the petroleum officers in the last months of the year.
Alterations in equipment design and the introduction of new and more advanced types of appliance occur no less frequently in the petroleum trade than in other commercial and technical branches of industry. Accordingly, it is necessary periodically to review the Council's conditions of licence to ensure that they continue to be effective in the light of the needs of modem safety requirements. Since no major changes had been introduced since 1976, it was decided to undertake a comprehensive review of the conditions relating to petrol filling stations and small petrol stores.
This review is presently in course of completion, but certain amendments have been approved in principle:-
1. A more detailed delineation of the boundary of the 'licensed premises', particularly where petroleum storage fonns only one of the activities of a site;
2. A precise definition of the rules relating to the hazardous areas at filling stations, with provision for safety in petrol sales kiosks, where deemed appropriate;
:1. A relaxation of the communication requirements at self-service stations to pennit the use of a one-way loudspeaker system from the attendant to the customer. Experience has indicated that this, coupled with the ability of the attendant to instantly disable any pump on the site, is adequate;
4. A revision of the manning requirement at self-service premises to enable the station to be operated by a single attendant, provided that efficient means of summoning assistance for emergencies is constantly available. This reflects the relative lack of problems in operating this type of site, provided other safety requirements are rigidly observed.
A significant change in the of I.aw occurred in January, 19H2 with the commg IOtO of the Dangerous Substances m R d T k and Tank ContalOers) RegulatIOns 1JH 1. oa an ers I I' . I The new regulations superseded existing egis atlOn 111 re ation to the carriage of hazardous substances by rt:ad tanker or container. Operators of such vehicles are reqUIred to ensure that the vehicles are fit for the purpose, and that con-. tainers are regularly examined and tested. A whole 01 safety requirements is imposed and operators are to be fully aware of the I;sks involved in the carnage 01 a particular product. Tanker drivers must be adequateh trained and instructed and have full knowledge 01 the
dangers involved.
The regulations prescribed a change in that the police became responsible for enforcement where a tanker is on a road or public place. The experience and knowledge of the officers of this Department will continue to be utilised as required by the police. Moreover, these officers continue to supervise deliveries at petrol filling stations and other premises licensed for storage of motor spirit not exceeding 100,000 litres, and also to deal with vehicles carrying the same categories of dangerous substance in cans and drums.
For the past 50 years, with the minor exception of glass bottles in specific instances, metal containers only were approved for the storage of petrol in small quantities. These are required to have screw-caps to ensure safety at all times, since there is a hazard not only when full of spirit but also when empty. Technological developments of other materials and extensive tests have allowed the Health and Safety Commission to approve the use of specially made plastic containers for the keeping of petrol in quanti ties not exceeding 5 litres. Guidance on materials, construction, and labelling is issued by the Commission. Marking must include "Complies with S.1. 1982/630", and "PETROL HIGHLY FLAMMABLE". Vehicle and boat owners and other persons needing small quantities of petrol will be restricted to a maximum of two containers to be kept on a vehicle or in a safe storage place.
Most regular users of petrol are aware of its dangers if proper safety precautions in han?li.ng are not o?served. There has been concern that pennlttmg such plastiC receptacles will lead to the frequent use of unauthorise? containers.1t will certainly pose problems for filling statIOn operators and their staffs, and will mean that steps must be taken, particularly on self-service stations, to ca.ns before pennitting them to be filled. If this is done It unlIke.ly that any increased hazards will become apparent 111 so far as domestic users are concerned.
The new regulations came into force during the summer of 1982.
The increasing cost of petrol has created renewed interest in the use of liquefied petroleum gas (LPG) as an aut.omotive fuel. It has considerable acceptance on the resulting in the development of storage and dispensmg equipment for use at retail outlets.
In the past safety of LPG as a motor fuel suspect: partly because of the necessity to keep It undel considerable pressure. The industry is confident that the comprehensive safety measures 11l1VIi incorporated 111 storage and dispensing svstems make LPG as safe to handle as any other motor fu:l, even in self-service situations. The safety measures include remote control vain's, supervised by the filling station operator, and automatic emergency cut-off valves in the dispenser itself. These lat ter valves are deSigned to operate if damage occurs, for example, due to a collision. Deliveries of LP(; cannot lw made unless the nozzle connection to the \ehide tank correct. Self sealing breakawa\ host' couplings pr!:'\ ent leakage in the event of the vehicie lwing driH'n ,1\\ <1\ \\ hilst still connected. Oppration is b\ a 'dead man's handlt" 01 button, which requirt's the upt'ratt1l" to t"t'rt cOl1tinllall11d Ilual pressure to ('Hert delivt'n.
Because of the legal definition of "petroleum spirit", LPG is not itself licensable under petroleum legislation. However, where a petrol filling station proprietor wishes to keep LPG, the licensing authority may exercise control over storage because of its hazardous properties.
One of the first installations of this type was at Grimsby in 1975, and the conditions which were drawn by the Department for that site, with the methods of construction approved, subsequently formed the basis for others in many parts of the country. Much experience was gained on the problems likely to arise in everyday use.
It is anticipated that more applications will be received for the keeping of LPG on petroleum licensed premises, and a new schedule of special licensing conditions is currently in course of preparation.
"Power when wielded by abnormal energy is the most serious of facts"
Following the downward trend of previous years, 1980 saw a substantial reduction in the number ofinjuries caused by fireworks in Humberside, the total being only six. Regrettably this reduction was not maintained in 1981, the figure soaring to 17, the highest since 1978. Of these, 15 occurred during the three days around the 5th November. One unusual feature was the high proportion of incidents arising at private parties, there being 11 65%, almost all involving either young or teenage children, and including several eye injuries. This suggests that even when adult supervision is available, as it invariably is at private functions, the safety code is not observed.
Although the 'bonfire night' period in 1981 produced better weather than normal, the total injured is still unacceptably high. If we are to continue celebrating the 5th November then pressure must be exerted on parents and older children to observe the firework safety code more strictly. Greater publicity in schools about not only the risk of accidents, but the pain, disfigurement, and disability arising therefrom, may well cause older children to take more care, and hopefully ensure that younger children will follow their example.
Premises Licensed
The number of premises registered for fireworks within the Council fell slightly during the year. Inspections showed an increase on the previous year, and a number of minor infringements of storage rules were recorded, but none were of a serious nature. 1,819 (1,857)
Quantity Licensed Petroleum 3,312,279,600 litres 728,628,640 gallons (3,310,095,675 litres) -(728,293,878 gallons)
Carbide
Fees Received
Inspections
Sites under Construction
Filling Stations
Bulk Installations
Other Stores
Vehicles Tests
Pressure Tests Tanks
Pressure Tests PI'pel'Ines
Ullage rests Tanks
Explosive Atmospher T . e ests
Empty ranks Tests
PREMISES L'IAn.,')() (.[1,!i40) 17
9,411,948 kg 9,263.3 tons (10,169,638 kg) (10,011 tons) £29,000.73 (£25,660) 13 (19) (400)
Correct (-) 695 (717) 59 (71 ) 728 (761) 55 (77) 68 (66) 68 (101) 85 (74) 101 (81 ) 84 (58)
Incorrect (-) 264 (226) 26 (30) 276 (342) 12 (10) 3 (IO) 9 (3) 3 (7) 33 (10) 49 (38)
VISITS
Correct 29 (39) 329 (:-104)
Incorrect :-1 (S) 49 ((j2)
Total 794 (778) 959 (943) 85 (101) 1,004 (1 67 (87) 2,909 (3,002) 71 (76) 77 (104) 88 (HI) 134 (91 ) 13:-1 (96) 4(H (448) Total 32 (44) :i7H (3h6)
Please address any communication to the undersigned.
Honorary Secretary Eric Brown
Cambridgeshire County Council Hinchingbroke Cottage Brampton Road, Huntingdon Cambs. 048057344
I wish to apply for Membership of the above Association and I enclose the sum of £ 10.00 being the Annual subscription.
Name: Address: Authority or Company:
The completed form should be returned to the secretary with the fee.
Subscriptions: Membership £ 10 per annum.
Membership is open to those persons who are authorised Officers within the meaning of the Petroleum or Explosives Acts, or is open to any body, company or person being otherwise concerned with the handling, storage or transport of substances covered by this legislation.
Technical progress within the industry promoted by Oil companies and large industrial groups during recent years has increased difficulties encountered by Local Authorities in the Administratilln of Petroleum and Explosives Act.
The Association was formed in 19SH and its objects are to further:-
1) The advancement of scientific, technical and legal knowledge in this field.
:2) To supply and interchange information.
:-3) To try and promote uniformity in administration.
-1-) To promote the formation of branc hes
'J) To co-operate with other bodies having similar objects, or who are lltherwist' connected \\ith 1'('(l"ll\t>1I1l1 (l\ Explosives legislation.
Petroleum in the 80s is an expensive commodity. You can 't afford not to know exactly how much you've got.
Normond tank monitoring systems count precisely that -every drop you've got.
Call up the figures on a VDU, a digital indicator or a print-out. They 'll tell you the time, date , capacity and contents of your tanks , instantly. Call them up remotely through the Telecom modem-from the other side of the plant or from the other side ofthe planet. Instant information , accurately, every time; supplied to you by Normond.
If you run a fleet of petrol engine vehicles, the last thing you want is expensive petrol.
Especially when there's a cheaper, better alternative Calor Autogas.
Autogas is a Iiquefied petroleum gas. The big difference between it and petrol is 40 pence or more per gallon.
Put another way, you could save over £ 1 for every three gallons of Autogas you use
And that's only the start of it.
Autogas is a cleaner burning fuel. So the engine, the plugs and the oil stay cleaner, longer. Oil life, for example, can be as much as four times longer. Think what that means in reduced maintenance costs.
With Autogas, you don't need the choke to make a cold start. So costly petrol isn't swamped into the engine to wash away the protective oil film. It's pilfer proof. You can have your own pump installed for fuelling your fleet. Autogas is also available at a growing number of points ?round the country - currently over 300, inclUding some Motorway and self-service
And converting your fleet to run on Autogas doesn't eliminate petrol operation: you can even switch from one fuel to the other while on the move.
So you have the back-up of petrol should you ever need it.
More miles per £1. More miles between plug and oil changes. More miles per vehicle before it needs replacing. What more could you ask for. Get the full, money saving story.
Contact your regional Calor Gas office now.
ScoHish Region , Friarton, Perth PH2 8DQ. Tel : Perth (0738) 25222 Te lex: 76129
Northern Region 171 El land Rood, Leeds LSll 8BU. Tel: Leeds (0532 ) 707193. Te le x: 55479.
North Western Region. Do ckyard Rood , Ell esmere Port, Wirra l, Ches hire L65 4EG. Tel: (05 1) 355 3700. Telex: 629332.
Eastern Region. 63 Th orpe Road, N orw ich , Norfolk NRl 1UF Tel : Norw ich (0603) 27207. Telex: 97151
South Western Region. M illbrook Trad ing Esta te, Mi llbrook, Sou thampton S09 l WE Te l : Southampton (0703) 777244 Tele x: 477442
South Eastern Region , Po int Pleasant, Wand sworth, Londo n SW 18 1NN sites and can be bought on a Calo r Autogas credit card .
Tel : (0 1)870423 1 Tel ex: 928613.