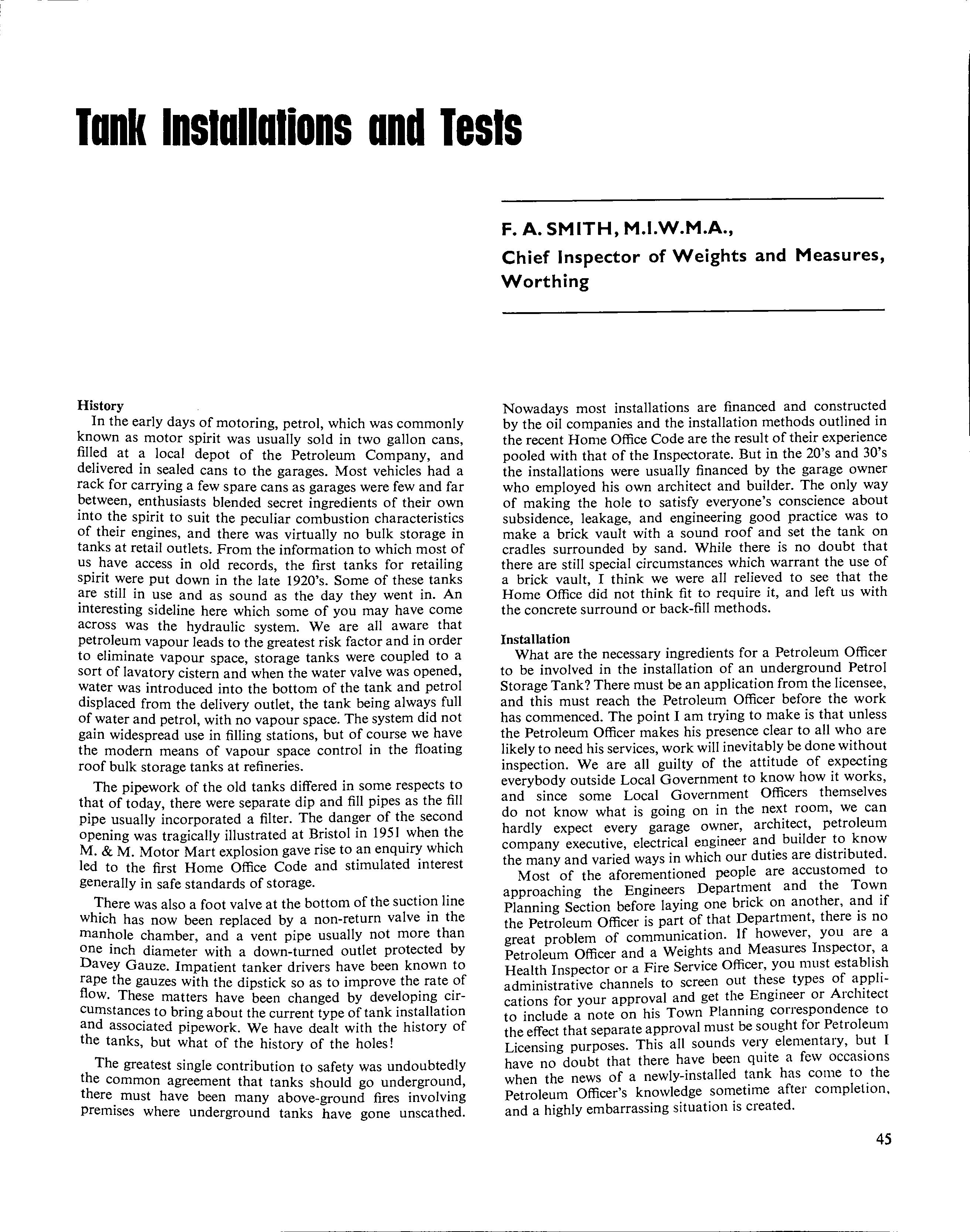
18 minute read
Tank installation and tests
by apeauk
Tank Installations and Tests
F. A. SMITH, M.l.W.M.A., Chief Inspector of Weights and Measures, Worthing
Advertisement
History
In the early days of motoring, petrol, which was commonly known as motor spirit was usually sold in two gallon cans fill~d at ~ local depot of the Petroleum Company, antl delivered m sealed cans to the garages. Most vehicles had a rack for carrying a few spare cans as garages were few and far ?etween, enthusiasts blended secret ingredients of their own mto the spirit to suit the peculiar combustion characteristics of their engines, and there was virtually no bulk storage in tanks at retail outlets. From the information to which most of us. ~ave access in old records, the first tanks for retailing spmt were put down in the late 1920's. Some of these tanks ~re stil~ in use and as sound as the day they went in. An mterestmg sideline here which some of you may have come across was the hydraulic system. We are all aware that petroleum vapour leads to the greatest risk factor and in order to eliminate vapour space, storage tanks were coupled to a sort of lavatory cistern and when the water valve was opened, water was introduced into the bottom of the tank and petrol displaced from the delivery outlet, the tank being always full of water and petrol, with no vapour space. The system did not gain widespread use in filling stations, but of course we have the modern means of vapour space control in the floating roof bulk storage tanks at refineries.
The pipework of the old tanks differed in some respects to that of today, there were separate dip and fill pipes as the fill pipe usually incorporated a filter. The danger of the second opening was tragically illustrated at Bristol in 1951 when the M. & M. Motor Mart explosion gave rise to an enquiry which led to the first Home Office Code and stimulated interest generally in safe standards of storage.
There was also a foot valve at the bottom of the suction line which has now been replaced by a non-return valve in the manhole chamber, and a vent pipe usually not more than one inch diameter with a down-turned outlet protected by Davey Gauze. Impatient tanker drivers have been known to rape the gauzes with the dipstick so as to improve the rate of flow. These matters have been changed by developing circumstances to bring about the current type of tank installation and associated pipework. We have dealt with the history of the tanks, but what of the history of the holes!
The greatest single contribution to safety was undoubtedly the common agreement that tanks should go underground, there. must have been many above-ground fires involving premises where underground tanks have gone unscathed. Nowadays most installations are financed and constructed by the oil companies and the installation methods outlined in the recent Home Office Code are the result of their experience pooled with that of the Inspectorate. But in the 20's and 30's the installations were usually financed by the garage owner who employed his own architect and builder. The only way of making the hole to satisfy everyone's conscience about subsidence, leakage, and engineering good practice was to make a brick vault with a sound roof and set the tank on cradles surrounded by sand. While there is no doubt that there are still special circumstances which warrant the use of a brick vault, I think we were all relieved to see that the Home Office did not think fit to require it, and left us with the concrete surround or back-fill methods.
Installation
What are the necessary ingredients for a Petroleum Officer to be involved in the installation of an underground Petrol Storage Tank? There must be an application from the licensee, and this must reach the Petroleum Officer before the work has commenced. The point I am trying to make is that unless the Petroleum Officer makes his presence clear to all who are likely to need his services, work will inevitably be done without inspection. We are all guilty of the attitude of expecting everybody outside Local Government to know how it works, and since some Local Government Officers themselves do not know what is going on in the next room, we can hardly expect every garage owner, architect, petroleum company executive, electrical engineer an~ builde~ to_ know the many and varied ways in which our duties are d1stnbuted.
Most of the aforementioned people are accustomed to approaching the Engineers Departn_1ent and the Tow? Planning Section before laying one bnck on another, a?d 1f the Petroleum Officer is part of that Department, there 1s no great problem of communication. If however, you are a Petroleum Officer and a Weights and Measures Inspector? a Health Inspector or a Fire Service Officer, you must estabhs!1 administrative channels to screen out these types of applications for your approval and get the Engineer or Architect to include a note on his Town Planning correspondence to the effect that separate approval must be sought for Petroleum Licensing purposes. This all sounds ver~ elementary, b~t I have no doubt that there have been quite a few occasions when the news of a newly-installed tank has come to the Petroleum Officer's knowledge sometime after completion, and a highly embarrassing situation is created.
45
Where then do we start with a tank installation? Having received, examined and approved the application, adverting to my remarks about inter-departmental co-operation the first thing to ensure is that whoever replies to the applfcant to say his licence has been granted or extended includes the magic words "subject to the work being carried out in accordance with the Council's Conditions of Licence and to the satisfaction of the Petroleum Officer".
Inspection
When the builder has been ascertained, he should be clearly told at what stages he will be inspected it is useful to have a printed hand-out to this effect. First jdb is to inspect th~ excavation. When I do this, if I do not already know the builder! I am also .trying to assess his integrity and impress upon him that specifications must be adhered to. He should be warned that the batch note from the Readymix Company will have to be produced if it is to be a mass concrete job, and asked whether he knows the tank dimensions and whether the de~th. has b~n calculated properly to allow for pipe falls. This is v_ery 1mpo~tant where there is to be a long pipe run. I~ there is any budding nearby likely to be affected by subsidence the Chief Building Surveyor should be warned so that he can call for sheet piling if necessary. Depth indicators can be set to proye the. base thickness, although a skimpy builder can cheat with. this or any other safeguard unless you are resent .at all times. If a builder has deliberately skipped an nstruct1on, a word to the Petroleum Company is usually ~~oug_h to ensure that he gets no more work. If there is much bsod water~ anchorages for straps or cables should be ~ad~ at the time_ of pouring the base. When the tank is on si e ~ should be ~nspected for quality of bitumen coating or rust amage and mstructions given for repainting.
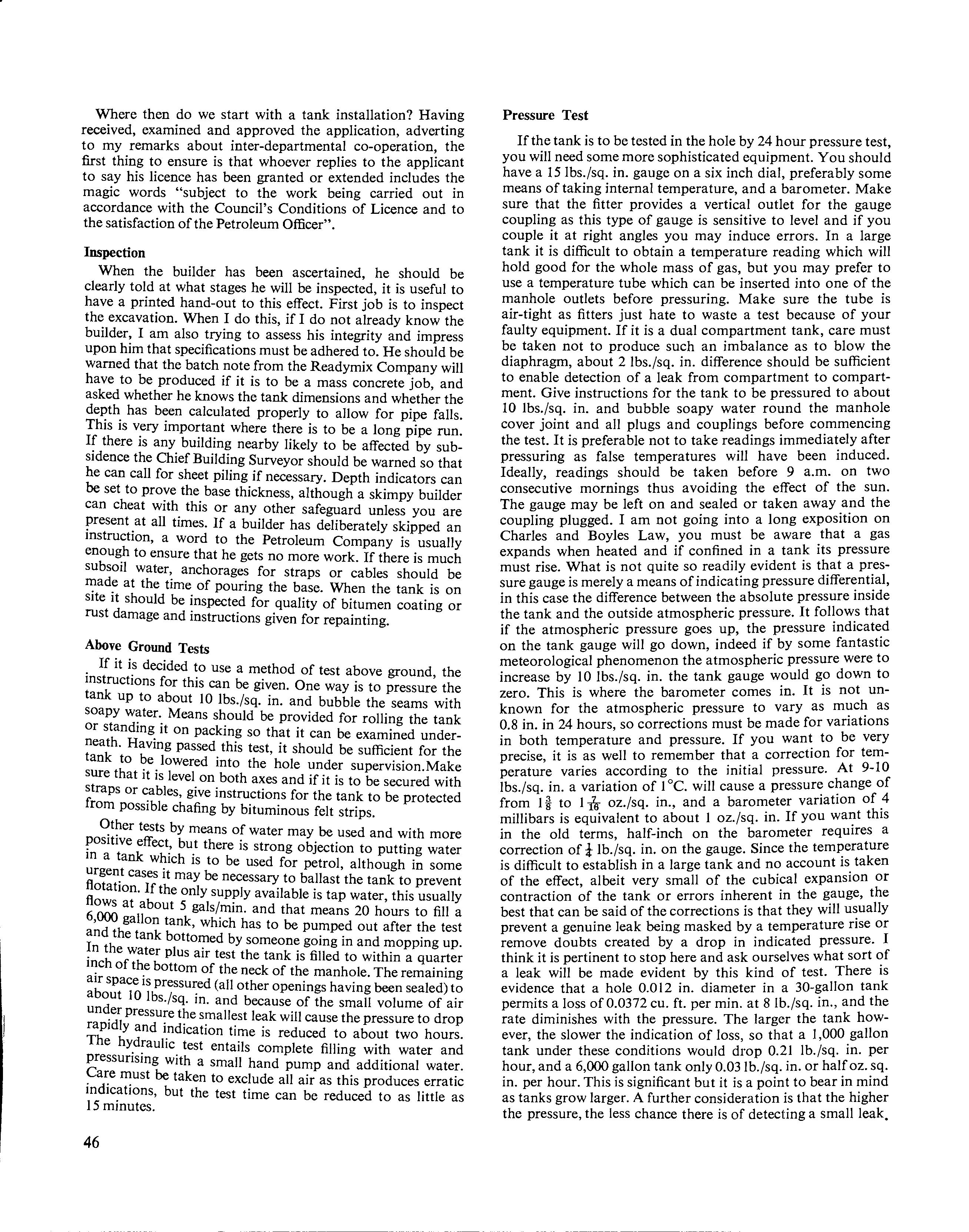
Above Ground Tests . If it i~ decided to use a method of test above ground the mstruct1ons t nk for th · Is can b e · given. One way . is to • pressure the a up to about 10 lbs./sq. in. and bubble the seams with soapy w~ter._ Means should be provided for rolling the tank or standmg 1t on pa k' neath . c mg so h . t at it can be . exammed undert k · Havmg passed this test, it should be sufficient for the san to ~e. lowered into the hole under supervision.Make ~e that it Is level on both axes and if it is to be secured with ~ raps or ~ables, give instructions for the tank to be protected rom possible chafing by bituminous felt strips
Oh
po ·!· er t~ts by means of water may be used . and with more ins~ ~:~ ect? bu~ there is strong objection to putting water ur ent ea w~1ch is to be used for petrol, although in some flo~af s;s It may be necessary to ballast the tank to prevent flows 1 ~~·a: the only supply available is tap water, this usually 6 000 II out 5 gals/mm. and that means 20 hours to fill a a~d th~at
0 ~ ~nk, which has to be pumped out after the test In the w:t~r otto~ed by someon~ going in an~ mopping up. inch of th b plus air test the tank is filled to within a quarter air .e ottom of the neck of the manhole. The remaining ab;~t~~ 1 ~ ?sressu~ed (all other openings having been sealed) to u d ./sq. m. and because of the small volume of air r~i~~ p:essu~e t?e s~allest leak will cause the pressure to drop The Y nd 1_ndication time is reduced to about two hours. P h>:d~auhc test ressunsmg with C a entails complete filling with water and 11 h .. sma and pump and add1t1onal water. . ~e ~ust be taken to exclude all air as this produces erratic 11n5 ic~tions, mmutes. but the test time can be reduced to as little as Pressure Test
If the tank is to be tested in the hole by 24 hour pressure test, you will need some more sophisticated equipment. You should have a 15 lbs./sq. in. gauge on a six inch dial, preferably some means of taking internal temperature, and a barometer. Make sure that the fitter provides a vertical outlet for the gauge coupling as this type of gauge is sensitive to level and if you couple it at right angles you may induce errors. In a large tank it is difficult to obtain a temperature reading which will hold good for the whole mass of gas, but you may prefer to use a temperature tube which can be inserted into one of the manhole outlets before pressuring. Make sure the tube is air-tight as fitters just hate to waste a test because of your faulty equipment. If it is a dual compartment tank, care must be taken not to produce such an imbalance as to blow the diaphragm, about 2 lbs./sq. in. difference should be sufficient to enable detection of a leak from compartment to compartment. Give instructions for the tank to be pressured to about 10 lbs./sq. in. and bubble soapy water round the manhole cover joint and all plugs and couplings before commencing the test. It is preferable not to take readings immediately after pressuring as false temperatures will have been induced. Ideally, readings should be taken before 9 a.m. on two consecutive mornings thus avoiding the effect of the sun. The gauge may be left on and sealed or taken away and the coupling plugged. I am not going into a Jong exposition on Charles and Boyles Law, you must be aware that a gas expands when heated and if confined in a tank its pressure must rise. What is not quite so readily evident is that a pressure gauge is merely a means of indicating pressure differential, in this case the difference between the absolute pressure inside the tank and the outside atmospheric pressure. It follows that if the atmospheric pressure goes up, the pressure indicated on the tank gauge will go down, indeed if by some fantastic meteorological phenomenon the atmospheric pressure were to increase by 10 lbs./sq. in. the tank gauge would go down to zero. This is where the barometer comes in. It is not unknown for the atmospheric pressure to vary as much as 0.8 in. in 24 hours, so corrections must be made for variations in both temperature and pressure. If you want to be very precise, it is as well to remember that a correction for temperature varies according to the initial pressure. At 9-10 lbs./sq. in. a variation of I 0 C. will cause a pressure change of from Ii to 11'f oz./sq. in., and a barometer variation of 4 millibars is equivalent to about I oz./sq. in. If you want this in the old terms, half-inch on the barometer requires a correction of! lb./sq. in. on the gauge. Since the temperature is difficult to establish in a large tank and no account is taken of the effect, albeit very small of the cubical expansion or contraction of the tank or errors inherent in the gauge, the best that can be said of the corrections is that they will usually prevent a genuine leak being masked by a temperature rise or remove doubts created by a drop in indicated pressure. I think it is pertinent to stop here and ask ourselves what sort of a leak will be made evident by this kind of test. There is evidence that a hole 0.012 in. diameter in a 30-gallon tank permits a loss of0.0372 cu. ft. per min. at 8 lb./sq. in., and the rate diminishes with the pressure. The larger the tank however, the slower the indication of loss, so that a 1,000 gallon tank under these conditions would drop 0.21 lb./sq. in. per hour, and a 6,000 gallon tank only 0.03 lb./sq. in. or half oz. sq. in. per hour. This is significant but it is a point to bear in mind as tanks grow larger. A further consideration is that the higher the pressure, the less chance there is of detecting a small leak.
Back Filling and Pipelines
Let us assume that the tank has been satisfactorily tested and permission given to proceed. If the back fill is to be sand then th~re is no problem beyond ensuring that it is river or pit san~ w.1thout salt, but if it is to be concrete, the loading note sp:c1fymg the mix, 1 part cement, 2 parts sand and 4 parts t mch gravel or crushed stone, should be inspected and arrangement: made for all the pouring to be done at one go, ~he tank havmg been secured against movement. If one part is allowed to 'go ?ff' ~nd no precautions are taken to preserve the surface, stratification may occur which can lead to strain ~la~age u?der. sever.ely adverse conditions. A sulphate resistmg mgre?1ent is advisable, and probably cheaper to include on all occas~on~ rather than go into the problems of soil analysis. If by much this time, the better, the suction lines have been as the manhole chamber can connected so be constru~ted to. accommodate them without further 'breaking in'. The bnck chamb~r should be built and rendered with waterproof cement outside and inside, this should prevent ingress of water and help to retain petrol spillage. Where the brick manh~le chamber bears directly onto the tank, some form of corro.s10n pr~tective laminum should be used. All that remams noyv is for pipelines to be tested and the tank to be covered. P!pes may be tested under pressure and joints bubb.l~d with soapy water or filled with spirit under safe con?1tions and examined for leakage. A small hand mirror is advisable for examination under joints and in awkward corners. Put a long level on to ensure fall back to tank and ~ke sure that pipes are adequately concreted where traffic is 1 . ely .to pass. If there are to be offset fills, ensure that provis10n is made for remote stock indication by hydrostatic contents gauges and that there is no separate dipping opening. The tank cover should be graded so as to fall away from manhole cover frames sufficiently to prevent ingress of surface drainage. See that the vent which now needs no gauze and may discharge upwards rises in the place originally approved and is of adequate diameter to cope with the fill rate determined by the diameter of the fill pipe, and that there have been no subsequent alterations to the layout affecting the risk.

Tests on Old Tanks I think that my brief, tank installation be complete without a reference to tests and tests would not to be car~ied out on tanks 20 years old and over in accordance with Home Office recommendations. The first factor to reckon with is that here we have a new situation where the tank, having contained petroleum spirit, is dangerous. If a pressure test is required, then an inert gas such as nitrogen should be used after the tank has been emptied and corrections for temperature and Pressure made as before. I do not want to go too much into the compara~ive merits of ullage and pressure testing, the Pressure test is more expensive and inconvenient to the trade ~~d on c:iccasions reveals or creates leaks in the mahole cover JOm~ which are not very significant and waste tin1e. The ullage te~t is the simplest and some consistent results can be obtained with care. It is important for the spirit to have been in the ~ank for at least 12 hours to reduce thermal effects and also to ave the tank filled almost to the manhole neck but not so hi<>h as to cover the vent outlet. If the spirit covers the vent out~t and ~he tank is not quite level, any trapped air will produce ~rratic readings. First seal the pump nozzle to prevent ma?vert~nt use during the test. There are various ways of takmg dips, good results can be obtained by using a short ullage rod with a T piece to rest on the fill pipe top. The lower end of the rod should have a pair of small prongs to fend it off the side of the pipe, and prevent capillary or meniscus error. Using an indicator paste a clear mark can be obtained in relatively calm weather. If it is very windy and the vent outlet is exposed pressure built up in the vent pipe can cause disturbance in the spirit and the indicator paste will show whether this is happening. A bag placed over the vent will often be a cure. When a true indication is obtained, cover half the width of the rod with sellotape and take the second dip 24 hours later having re-pasted the uncovered half. The temperature of the spirit should also be taken on each occasion and if there is considerable difference the test should be kept on for a longer period, unless the results can be reconciled by using the coefficient of expansion which is 0.00113 per 0 C., and working out the calculated change of volume in terms of the tank dip stick reading at that level. A suspected tank failure can be followed by further confirmatory tests which may include a pressure test. The vent pipes should be traced and probed with a sharpened piece of brass rod where they emerge from the ground. This is a common failure point as pipes rarely get painted down to ground level and there is normally an accumulation of debris around the base which retains moisture and accelerates corrosion. Try the fit of the fill pipe cap and if threads on the fill pipe are worn badly give instructions for renewal. Petrol spillage in the manhole is usually indicative of this fault. Look for tank and dip stick identification in accordance with number 16 of the Conveyance Regulations, 1957. If the sight glass level of a pump is down, instruction should be given for the cause to be found and remedied, this may be due to a leak in the pump system or to a faulty non-return valve or worse still, a leak in the suction line.
Conclusions
It falls to the officer to decide which is the best method of test for his area or for a particular set of circumstances. Whichever method is used, it must be fully understood by those using it and they must have confidence in it. The Home Office Code does not refer to a pressure test on 20-year-old tanks, nevertheless there may be circumstances which justify it. It also suggests the possibility ofreliance upon an inventory check and while I know some highly respected Authorities use this method I would not be happy with it. What will happen when the 6,000 gallon monsters begin to fail. Who is going to relish the purchase of 22 cu. yards of concrete to make them safe! I expect there will be some attempt at relining and somebody will be called upon to give a safe working certificate, or perhaps by that time there will be fuel in jelly-like packs which can be safely stored, like the old cans, in an above ground store, and tanks will be just a memory.
However, so long as there is a system requirin~ ~ periodic test of some sort, the premises are sure to get a v1s1t from an Inspector entailing something more than a cursory glance around the place, the use of the tanks is interrupted and this causes the management to stop and think for a few moments and remember the risks involved with petroleum storage. When one considers these risks and the amount of petrol stored up and down the country, it is reassuring to read H.M. Inspectors' report for 1968, wherein only eight accidents occurred on filling stations and none of these was caused by a leaking storage tank.
47