Journal of the Association tor Petroleum and Explosives Administration
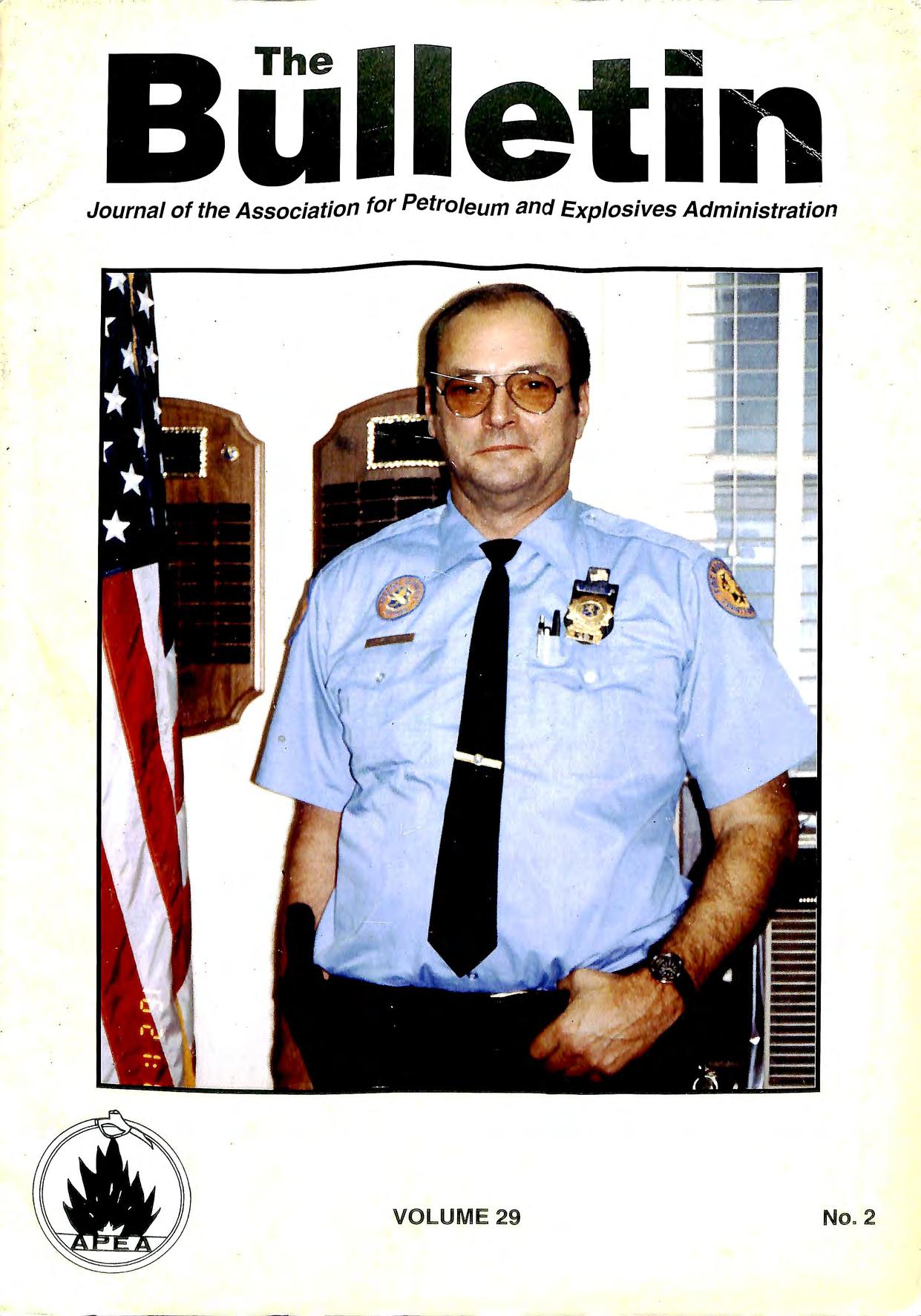
Ameron's Dualoy®3000/L fiberglass piping is li sted with Underwriters' Laboratories for use in undergro und fuel-handling systems. It ha s also been tested and accepted by the Lon don Fire and Civil Defence Authority.
Thi s mean s yo u h ave the ass uran ce that our product h as bee n tested und er the mo s t s tringent conditions a nd is rated for pressures and temperatures far in excess of regu lar petrol s tation requirements .
You can i n s tall a Dualoy sys tem in abo ut one half the time required to put in s tee l In fact, yo u ca n taper th e e nd of our pipe in less time t h an it takes ju s t to put a stee l pipe in a pip e v ise.
Dualoy 3000/L containment systems are also UL listed for alcohol based fuels as well as petrol
But here's the best part: you'll probably find the installed cost of a Dualoy system to b e less than for stee l-as it requires no sulphate resisting concrete surround.
Ameron has a Dualoy system for every underground fuel-handling need: whether it's conventional single-wa ll piping or a comp lete seco ndary containment sys tem.
For more information , write
Ameron Fiberglass Pipe Divi s io n, Prudential Hou se, Wellesley Ro ad, Croy don , CRO 9XY or call us on 081-680 3777
installs twice as fast as steel.
The OPW 66 is the only breakaway connector designed to do its job once, and then be thrown away. It protects your dispenser fro1n dai11age during a driveaway, and gives you peace of mind by protecting you fro1n reassembly errors.
The OPW 66 Breakaway will fit on either the botton1 end or top end of the hose. Placing it on the end may help n1ini1nize possible hose whiplash during a driveaway. In addition, top end installation n1eans less weight and bulk for your self-service customers to handle. Like a fuse , the OPW 66 stays out of sight and out of mind until it 's really ne ed ed .
The OPW 66 Breakaway is the result of OPWs leading position in fuelling c01nponents in the U.S.A., where the world's n1ost stringent safety standards are in force, ensuring that OPW's leading forecourt technology is available here, way ahead of its tin1e.
Specify OPW-your forecourt and equipment will be the greenest and the safest available, without costing you the earth.
The front cover shows Richard Kelner one of the officers responsible for petrol installations in Nassau County, New York State. The Association's Chairman Brian Taylor on a recent visit to New York heard of the successful tank replacement programme in the County, where in a short period all the old steel tanks are being replaced with skin GRP. Brian is convinced that the success of this operation has something to do with the gun Richie carries Richie however stated that the Oil Companies are very cooperative and he has never needed to draw the weapon in anger!
Space will again be available for exhibitors and full details will be circulated to previous exhibitors and others in due course. Meanwhile, if exhibition space is required, provisional reservations can be made by writing to the Advertising Secretary at the address shown on page 1.
The dates for the seminar and exhibition are 23/24 September 1991, and a programme is almost complete.
The following members were elected to the Council of the Association at the AGM at Dunstable
Chairman Brian Taylor
Vice Chairman Jack Sampson
Hon Sec Dave Bucknall
Hon Editor Jamie Thompson
Hon Treasurer Tom Wigfull
Membership Secretary Barry Thompson
Advertising Secretary Jim Luke
Council Members: John Boudry, Gordon Kinnear, William Musgrove, Chris Knight
A licensee in the West Country is taking legal action against a development company and his local petroleum licensing authority for negligence.
An application for a petrol station redevelopment was drawn up by the development company and submitted to the licensing authority. An approval letter for the scheme was issued and work commenced. All works on site were agreed under a certificate of compliance system operated by the licensing authority. At the end of the development work a petroleum license was duly issued.
After opening the site operator found that the pumps would not maintain prime and called in a maintenance company that found:-
1. 300ft suction pipework 1112" runs with Ts off to a series of dispensers had been provided.
2. The pumps were obsolete blenders that did not comply with BS7 l l 7, despite assurances by the contractor.
3. Drainage runs were all plastic.
4. The interceptor had split on installation.
5. An electrical examination indicated serious shortcomings requiring extensive rewiring works.
The licensee was also surprised that at no time had he been asked to have his +20 year tanks tested.
licensing authority have issued a 28 day improvement notice and at this point the licensee has employed legal to take action against both the contractor for m not complying with petroleum regulations and the licensing authority for malpractice. The local authonty ombudsman is now being involved.
Britain's leading forecourt system service oraanisations have formed the Association of Forecou; Systems Contractors.
Cameron Technical Services, Gilbarco, PM Services and Wayne Autocourt have formed the AFSC to study and res?lve_ common relating to health and safet , leg1slat10n and environmental issues Th . . . y bi" · elf aim is to es_ta . ish and promote good working practices and standards w1thm the forecourt service and installation ind try us
A main focus of the Association's activity will b advance safety and uniform standards thro h e. to · f, f · ug poolmg m obrmla 1onh, expenences and research into the potential ems t at personnel face while workina on iorecourts and handling petroleum products. "'
In its first initiative, the Association has developed a code of practice to be followed whenever k · wor 1s undertaken m forecourt manholes. The code lists th f d" ree sets o reqmrements accor mg to the depth of the ma h 1 Where_there_is a depth of no.more than 29 an engmeer is permitted to work on his own with spec"fi d safety-related equipment. For the deepest h . . f es, monitors, ans, safety harnesses and hftmg eqmpment are reqmred together with resuscitati·on eqmpment.
"Forecourt service and installation contractors ar committed to the continual development of uniform saf,e and efficient working procedures and practices,"' Dennis Fox, the Secretary/Consultant to the Association of Forecourt Systems Contractors.
"There can be no competitive barrier when it comes t safety and AFSC members pool resources information and, when necessary, JOmtly sponsor research " he adds. "Safety is our numb.er one priority, both for staff clients and the general pubhc. Such a policy necessar·l ' . . . . d I y involves mvestment m trammg an equipment but it · , expenditure that the AFSC is convinced is essential." IS
In add;t.ion to the will focus on a wide o u _mg tecf mca developments within the mdustry, t e imp 1cat10ns o entenng the Single E . Market and the formulation of industry-wide
In pursuit of its objectives, the AFSC will lia· , d · h f h · · · < ise an work wit a range o ot e1 t1ade orgamsations . h A . . f p l , sue as the ssocrnt1on o etro eum and Explosives Ad · · · h I · f p l · mm1stratmn t e nst1tute o etro eum and, of course th H ' Safety Executive. · ' e ealth and
Membership of the Association is 011 t h . f, · ten o ot er Natmn J orecourt system service oraa111·sat10 h a o< • c ns w o ar ,· ·1 1 committed to safety. · e s11111 ar y
Contact: Dennis Fox A . , · . . C · ssociatmn of Forecourt Syste111s ontractors PO B 64 · · 0737 3527C16. ox . Banstead. Sun-ey SM7 2QH. Tel
The European Promotion Association for Composite Tanks and Tubulars, EPACT, was formed in 1987 by leading European manufacturers of fiberglass tanks, pipes and components used in underground fuel installations. One major objective of EPACT is to create a better understanding of the advantages of Fiberglass Fuel Installations, through pro.motion of the technology and to assure safe mstallat1ons to established procedures. EPACT has recently pr?duced an "European Recommended Practice (ERP) for this as well as a thorough Data Manual, which not only includes the ERP, but also lists the national norms and standards regarding this technology.
are more than thirty members from ten European meet regularly to discuss matters concerning Me of composite fuel storage technology. EPACT Membership fall into three distinct categories: Full ers, Sponsor Members and Associate Members. in Seminars and Training Courses are conducted erent uropean locations annually.
For more info · or pubr rmation on EPACT, Conferences, Seminars, ications, please contact:
General Secretary's Office
A Camden bu · his prem· smessman who stored hazardous products on has been fined by Highbury Corner
In a prosecution b h Defence A th roug t by the London Fire and CIVIi held on th u flonty, the court heard that a weekend market reasons as e 001r above had been closed down for safety a resu t of the offence.
David Cannary I petroleum . P eaded gmlty on March 21 st to keeping a mixture witho t r h Id' premises in St 1 . . u a 1cence at t e 'Motorwe an ey Sidings, Chalk Farm Road, NW 1.
The court w approximat 1 5as told that Mr. Cannary had stored that the e Y O htres of the mixture mainly paint and re Were o _ . ' ' . fittings, gas f ;y cuttmg gear, unprotected hght building wh· heatmg evidence of smoking in the Ic were potential sources of ignition.
The Authority ·d explosion sai there was a risk of both fire and customers. Mr Cannary, his employees and extra risks t f. In the event of a fire, there would be · · 0 Ire 1ghters too.
The magistrate· · s were told that the floor above was used as a market, and the petrol mix below be ser rous threat to 1 h fir 1 11 peop e t ere. If there was an explosion, the s oor would collapse posing a substantial risk to life. f he Authonty had 1 ·ssu d h.b. · · e a pro 1 1t1on notice preventmg its U<.,t' "" <l market.
.1\111 < ;11rnary was fined £500 and The Authority was d\.\ ;infl'd I_ "i() <'OSIS.
The Code of Practice for the Proving of Loading Gantry Meters has been produced by the IP committee dealing with the commercial metering of petroleum products, PM-D-4.
The Code establishes minimum levels of accuracy for the proving and adjustment of loading gantry meters gives guidelines on the traceability of devices. The meter adjustment requirements descnbed m the Code reflect current reasonable practice in the industry. They are practically achievable and represent the minimum. of performance considered acceptable for trade w1thm the industry.
Copies of Petroleum Measurement Paper No. 4 - Code of Practice for the Proving of Loading Gantry Meters are available from:
Price: UK £12.00 Overseas £15.00
The Annual General Meeting of the Branch was held on 13 February 1991 at the Cotteridge Hotel, Woking, Surrey.
The morning started with the formal AGM and Chairman, Secretary and Treasurer gave their respective reports. Each was pleased to report the excellent. progress and enthusiasm which had been evident smce reestablishment of the Branch in 1989.
A summary of past and future Branch activity was by the Chairman. The high attendance levels at meetmgs was especially encouraging and special mention was made of the next meeting to be held in Avonmouth on 1_5 May 1991 when various guest speakers will give presentations on overfill prevention and wet stock control systems.
The following officers were then re-elected:
Chairman Secretary Treasurer
Mike Sewell
Max Cox
Jim Luke
The following members were also elected in addition to the above named to serve on the Branch Development Committee:
Rory Hennessy
Richard Graham
Bob Thompson
and the following two members were elected as Branch Auditors:
Rick Madelin
Keith Holmes
The second part of the morning session was due to be a presentation by John Boudry of Cookson & Zinn on the latest developments in double skin steel tanks and associated leak detection. Unfortunately, however, because of the adverse weather conditions this presentation had to be cancelled.
The Branch was therefore very grateful to Simon Procter and Lewis Glenday of Joseph Ash & Son Ltd who came at very short notice to give a presentation on their double skin steel tank and leak detection equipment.
The afternoon session commenced with a presentation by David Martin of FRP Resins on GRP tanks which included a showing of slides illustrating the installation process for GRP tanks.
The final speaker was Jian Buchan of Esso Petroleum Co Ltd who gave a very interesting insight into his company 's approach to the safe operation of their filling stations; his talk included topics such as the rapidly changing approach in installation methods and testing of underground tanks and of the ever present need to maintain strict wet stock control.
After a short question and answer session the meeting concluded.
N.B. Every effort is being made at present to ensure that all members within the Branch area are circulated with details meetings, site visits etc. If any member 1s not rece1vmg these details , please contact Mac Cox, the Branch Secretary, on 081 -392 1355.
Thank you for allowing me to be your Chairman for the coming year.
I intend to continue to follow the traditions of the past Chairmen in fully supporting the aims and obj ec tives of the Association, and to maintain the Association's standmg.
I am proud to have been one of the team that has assisted in promoting the Association to its present position
I well remember A.G.M. 's not all that long ago , which attracted 20 or 30 members. Today we see an attendance of over 220 members.
Th e Association has a ttempted to provide the memb.ers with information on new technology by promotmg infonna tive sem inars. I will en deavour to continue this objective.
As we proceed into 1992 there are go ing to be many changes in our indu stry, from changing enforcement rol es,. to a greater re spon s ibility by industry in the safe-keep 111g of petroleum s pirit.
Environm e ntal issues are in c reas in g ly being brought to bear o n our indu s try a nd we must take up this cha ll e nge to e nsure that we a ll play o ur part whe re req uired, and have a
greater awareness of other enforcement bodies requirements. Failure to do so could mean others will dictate the path we should take.
There have been .some serious inc idents in our industry recently and these 111c1dents do nothrng to give confidence to those on the outside looking in.
All of us are of public safety, whether you are an Enforcement .officer, Oii Company Engrneer, Contractor or a Manufactunng Company.
we must ensure the. highest standard poss ibl e ll1 the interest of the safe-keepmg of petroleum spirit.
I beli eve that , never in the history of this Asso · t· cia ion , aie the aims and objectives more important as the' d · · · 0 < J a re to ay with the 111c1 eas 1110 technology found 111 our ind t I 1 II h US I y. S 1a attempt to e nsrne t at you are all kept informed of th ese new concepts and one of the ways that we C"' 1· 1 · • • , • < nil ac 11 eve t 11S 1s th1ough the Bull e tm so le t 's giv e o ur Ed itor yo ur support.
To co nc lud e. 1 look forward to visitino yo ur branches during the year to meet you all aga in
Once aga in. thank yo u for you r co nfide nce in e lec tin g me your C hairman .
For over a century petroleum licensing authorities have been involved in regulating the storage of petroleum spirit with the prime objective of ensuring safety and the integrity of storage/delivery systems.
Regrettably some accidents, a few fatal, have occurred, but have given the benefit of hindsight to both the petroleum supply industry and enforcement authorities, enabling safety precautions to be improved beyond all recognition; resulting m present day legislative controls, Health and Safety Executive guidance notes, related British Standards, and petroleum supply industry training/instruction manuals and Codes of Practice.
With the advent of self-service in the 1960s the above ground forecourt revolution began and very soon after that heralded one of the first of the oil companies' "give away" promotions of free petrol from jammed note and coin acceptors! That revolution continues and is an ex_citi:ig/expensive/frustrating/profitable (use self-service cntena) time for all of those involved in it.
We are now witnessing the start of the underground forecou1t revolution in terms of the availability of sophisticated double containment and leak ?etection/prevention systems for storage and pumping This has been brought about by many factors and this article is intended to set the scene and predict the outcome.
Since long before the environment became a maJ·or or. . P itical issue, petroleum officers and the petroleum supply have been striving to reduce, and have succeeded in if not the possibility of leaks or spillages, then the magrn.tude and effect of them. The industry now has the capab11"t t· · d . 1 Y o mstalling double containment and leak systems, and the pressure seems to be mcreasmg for them to do so.
The National Rivers Authority now has very substantial under the Control of Pollution Act 1974 and the Act 1989, and recent Regulations even specifically 1 to water catchment pollution from the storage of agncultur·tl fuel ·1 · c · . . .. ' °' s. ontammat1on of water can now result 111 a fine at Ma · ·t. , C , .· g1s 1ates ourts of £20,000! In my own c1utho11ty soine thi·e f" · e quarters o pubhc water supplies are derived from "r d , o oun water sources. and I am now the owner 01 a "'..RA Aquifer Protection Zone map for the area which 1dentll1cs th I · · · e OCdt1on of bore holes and water sources.
In January this year the Ministry of Agriculture, Fisheries and food published a "Code of Good Aoricultural Practice ft>r the Protection of Water"" which. in :ddition to dealing v. llh hydrocarbon pollution. covers contamination from aµncultural wastes. slurries. fertilisers. pesticides and sheep 1l1p
The Construction Products Directive, due to be implemented in UK regulations to be in force by 27th June of this year, covers the effects of construction products in terms of mechanical resistance, stability and the outdoor environment, (i.e. tanks and pipelines), and requires consideration to be given to the prevention of pollution.
In the USA many states now have made it a legal requirement for double containment systems, and several of our European neighbours have already legislated for similar precautions.
In recent Health and Safety Executive publication, J:IS(G)4 I, dealing with filling stations, specifically refers to licensees operating a system of reconciliation that can identify a leak in a matter of days rather than months.
Friends of the Earth are also showing concern for the let alone safety implications, of hydrocarbon contammat1on caused by leaks/spillages. Additionally, are many other "lobbies" that are showing a growmg concern for the health of our planet in this area.
The desire for double containment can be justified on the grounds of "the ideal world" but consideration has to be given to the implications of the exercise. Mandatory requirements would mean that the small operator/user could be forced out of the "market" because of cost. The outcome of this must be carefully balanced and considered to ensure that t.he economy is not unredeemably affected, but in doing so.' _sight must not be lost of the potential consequences of failmg to act now rather than later in terms of environmental damage and clean up costs.
The. supply industries to the oil companies have had the foresight to recognise the potential long term savings and safeguards t_hat can be achieved by double containment and leak detection/prevention and are flooding (sorry!) the market with new systems almost weekly.
Amongst the innovations now available are double skin tanks with inbuilt leak detection, GRP tanks with va:1ous associated external leak detection systems, double sk.m pipework, tank farm and pipe trench liners (again_ with va:1ous leak detection systems) and several types of mechamcal overfill prevention devices.
The have already grasped this nettle. and from January of this year have required that all new steel tanks are double skinned, and that GRP tanks are installed with leak detection equipment located in the tank farm.
It would therefore seem that if the supply industry docs not go "green" voluntarily (and many have already taken very positive steps in this direction) then it will not be long hefore it is a legislative requirement.
A revolutionary new concept has been designed to facilitate the removal of the existing IOOmm aluminum internal fillpipe fitted to the underside of the existing tank lid on both direct or offset filled installations fitted with a I OOmm equal tee-piece on the top of the tank lid in a completely acceptable, safe and accurate procedure on operational "LIVE" storage tanks on garage forecourts to allow for the installation of either the Emco Wheaton or OPW ove1fill prevention valve.
Until now this operation has only been achievable by the storage tank having to be taken out of use for the period of time required to carry out the bottoming out of the remaining product, water filling of the tank and the necessary works associated with the breaking down of the tank access chamber and disconnection of the pipework connections to allow removal of the tank lid to gain access for the removal of the internal fillpipe, followed by the reversal of this procedure to reinstate the storage tank connections and access chamber including pressure testing and water removal on completion, before the storage tank can be put back into operation.
The only restriction that we must enforce at all sites while the retrofit procedure is in progress is that under no circumstances can tanker deliveries take place. Otherwise apart from any restrictions that may be required by the local licensing authority, we shall only interrupt the normal forecourt operation for adequate traffic management and safety procedures around the work area at any location across the country.
Our fully trained staff will coordinate the complete operation from the time of concept of the customers order through to all neces sary liai so n with both the local area licencing authority and site management on the co ordination of the programme.
Following aiTival of our installation team on site and their introduction to the site manager they will proceed to cordon off the work area and place warning signs, both at the offset filling position and around the immediate work area, ready for the removal of the access chamber cover and reducing of the water table if so required, the plug in the top of the teepiece is then removed and the existing hexago n nipple. and internal fillpipe are checked for dimension and s uitability. after which th e plug is temporarily replaced 111 the top of the fittino while the equipment is set up. 0
The operating rig is then raised onto it s wheels and pushed back from the tank access chamber ready lor resett 111g over th e next tank pos ition or break ing down for removal as appropriate at the time.
The working procedure of the cutting ri g and ov e rfill in sta llation is des ign ed as a two man operation. wi th va riou s sect ion s of th e above operation req uirin g both ope rati ves in
atte nclance , however parts of the process only requ·. · · · I· · 11 e one urnt operator, 1t 1s at t 11s time that th e other opei· it· c 1v e would be engaged 111 the assembly of the overfill prev e r· j'· I c1· " k . . n ion valve 1om tle 1mensions ta en at the t1111e of initial _ checks on both the existing internal fillpipe and and of the storage tank. iameter
Once the operating rig is clear of the tank c . plug can again be re moved and the i· 11 ·t· _hamber, the se1 ion ol th -r· prevention valve earned out and be _ t . e ove1 Ill 1e amed 111 p the lockmg cage screwed into th os1t1on by cl e tee-pi ece be! I sealmg plu g, or alternatively lock ed ow. tl e by the fillpipe adaptor on direct fill tanks. into po s ition
What with th e changes in the etro l _ . our conce rn for th e prote ·tio f 1 e um 1eg ulation s and more emp hasi s on , t\ickl n e n v ironn1ent placing ' cont1 o 'tncl syste ms on re tai I forecourts TI l ' ope i at1onal salety an overfill prevention sy t l e t 1 ou g ht o1 ha vi ng to install tanks. will no Ion oe r u yo ur ex ist 111 g s ite storage tl d c cive you cduse tor co nc e rn. w hat w ith 1e own time on tl · d· · 1e 111 iv iclual tank s and disp e nsino equ ipm e nt. A lso w ith tl , · c c _. _ · 1e 111t e 1i upt1on to your normal IOI eco u1 t op e ration caused b' th , th 1 1 · · j e o e1 ty pe ol rec t1 hcation WO!' le1110 l" lr1·1 erl l l I c- ' c nu l Y t 1e prese nt m e thods.
A h ydraulic powe r unit driven from a small diesel e ng ine complete w ith spark an-estor fitted to the exhaust system is positioned outside of the hazard zones, with forty foot hoses for connection to th e power drive at the work area.
T.he fillpipe extraction unit is constructed to operate on a trailer mounted assembly which is stood on encl in an upright position when in use , a ll rotating parts of the cutter, w ith the exception of the cu ttin g edge are m anufactured in a ll oy o r bras s m aterial s. Small adjustable wheels are fitted at eac h co rn e r of the working platform to facilitate easy maneuverability and acc urate positioning of the compl ete unn ove r the storage tank and in alignment with the ve rtica l plane of the internal fillpipe. Once this is correctly pos iti o ned adju stab le o utri gge rs are locked into position and the w hee ls rai sed up off the g ro und forming a completely s tab le working ri g
Fo ll ow in g remova l of the plug from th e top of the teep1 e c e a g uid e tube is in serted thrmwh and into the internal l'illpipe Th e tube in co rporates rubb e r seals positi o ned at hi gh and lo w lev e l, w hi c h w he n com pressed from the top ex pand o nto the internal a rea of the a luminum tube thu s co mplete ly sea lin g off the work ar ea. Thi s tube a lso acts as a g uid e for the c utte r, w hi c h ha s a n eye on the top for w ith draw in g the comp lete pipe asse mbl y by w in ch on c omp le ti on or the c ullin g ope rati o n. Jn add iti o n the upp e rmo s t rubber sea l traps a ll of the co ntamin atio n drop s into the s torage tank al any tim e . T he lower seal is drilled w ith a se ri es of b leed hol es whi c h all ow s an y produ ct tra pp ed be twee n th e two se a ls to drai n back into th e storage la nk w he n th e unit comp le te w ith the o ri g inal inte rnal lillpipe w ithdra w n al th e e nd of th e operat io n An y
petroleum product re maining above the top sea l is removed and the cap at the filling e ncl of the offset fillpipe replaced with our special adaptor, the pipeline is then purged through with nitrogen to remove any remaining vapours.
The hydraulicall y driven power drive and control unit is mounted onto the guide rails and suspended by attac hment to the clutch controlled winch cable. The cutter is slid over the guide tube and connected to the power unit and lowered clown ready to commence reaming out. After lock mg the operating personal safety frame into position across the front of the rotating cutter drive , the re a min g o ul of the hexagon nippl e in a clockwi se direction is commenced. Th_e power unit is controlled by a deaclman handl e to e ns ure it cannot operate unattended. As soon as th e hexago n nipple has been reamered throu cr h to its full len g th, th e cutter is withdrawn and re moved. The second c utte r is th e n connected and lowered into position , this cutter th e n in an anti-clockwise direction, this is achi e ved by pushmg the deaclmans handle in the opposite direction to th at in the previous operation As soo n as the aluminum tube has been reamerecl from the aluminum socket, it will be free to be removed. At thi s point the cutter g uide becomes an extension to the aluminium fillpipe, thu s maint a inin g a seal to the tank vapour area
The power unit is then di sco nnected from th e c utter and removed from th e operatincr ricr the winch cable is then b b' connected onto the eye on top of the guide tube , the aluminum internal complete with cutter and all of. the swarf to be withdrawn up through the tank lid a nd tee-piece for its complete removal from the tank, leav in g a clean orifice ready to accept the new overfill valve assembly. The plug is then temporall y reinstated to re-seal the ta nk opening.
James Philpotts, the Chief Executive of Melton Medes Limited and a Director of its subsidiary Fibre Reinforced Products Limited looks at the developments in underground fuel storage tanks from the unique perspective of someone who has been a Director of both GRP and steel tank companies. James Philpotts also considers the changes that have taken place in underground fuel storage tanks since the war drawing on his former experiences as Deputy Group Managing Director of Ash & Lacy Pie and its steel tank subsidiary Joseph Ash.
Early steel tanks will be remembered as very heavy gauge vessels generally of smaller capacity than today's tanks and originally installed in brick lined chambers with a sand infill. Many fire officers still speak fondly of this type of installation although the size and consequent weight requirements of modem tankage make it difficult to use heavy gauge steel and present day labour costs make brick chambers prohibitively expensive.
Reduction in the wall thickness of steel storage tanks for underground purposes occurred when installation within a concrete surround became the norm. The surround of necessity was constructed from a sulphate resistant concrete to reduce the chemical attack upon the steel fabrication.
The problems associated with the inner gauge steel tanks namely perforation and leaking are well known throughout the oil industry. One of those most frequently encountered is that resulting from weak points inherent in most welded structures which are not always apparent to the naked eye and which open up due to the effect of corrosion.
Even leakage say equivalent to a tablespoonful of pet:ol an hour becomes quite a significant additional cost fact.or the context of the final price of a mild steel tank which 1s to remain underground for some years. Perhaps more to the point, how much longer will the public be prepared to tolerate leakage of fuel from underground fuel storage tanks? This is especially the case when the marginal costs of improved tanks are so insignificant relative to the cost of establishing a retail petroleum site.
During the 1980s because of the incidence of corrosion and leakage Shell, Netherlands decided to unearth and replace virtually all its mild steel tanks. The cost was some £8m. Estimates suggest that 70% of all Dutch filling stations were encountering leakage. The Dutch have tried numerous methods to cope with the inherent problems associated with the corrosion of mild steel ranging from Bitumen coatings ( 1950s) to cathodic protection ( 1960s) and single or double epoxy protection. Double epoxy treatments recognise the fact that mild steel tanks also rust from the inside.
something. that has only been appreciated more recently. The first installation of GRP tanks was made by Shell Netherlands in 1989 and they have now become standard. '
installed some experimental GRP tanks in the early s1xt1es when the use of GRP for such purpose was in its infancy. One of these tanks was recently dug up for corrosion evaluation by BP after some 25 years in the ground. BP completed their evaluation of these experimental GRP tanks before moving towards GRP tanks earlier in the year.
It is not surprising to find U.K. oil majors and aware independents either specifying GRP tanks or giving consideration to double walled tanks. Potentially one might expect double walled mild steel tanks to fail at a higher rate than single walled mild steel tanks, given that there is twice as much exposed steel and welds.
However, if the tanks are of mild steel form and not encased in sulphate resistant concrete they may corrode much more quickly than the present single walled mild steel tank with a concrete jacket. Obviously great care is needed in the choice of any aggregate used as infill with double walled steel tanks lest it give rise to much faster corrosion. The logical answer for a steel tank which is not to be encased in concrete would be a stainless steel fabrication. Mild steel tanks whether single or double walled are a corrosion risk and failure can occur within two years.
Aside from the environmental issues it is difficult to see the economic justification in utilising tanks with such an buried the cost of removing and refilling contaminated soil alone exceeds £50/tonne. Closing a prime forecourt site for over a week to replace a corroded tank could. lost revenue of over £50.000. For most 011 maJors in the extraction and refining well t.he sale of lost revenue equals lost profit m the Even independent operators cannot ignore the trends 111 the indt1st1·y bee · 11· · ause msta mg the wrong tan_k now could devalue their business in future One of the 011 maJ·ors has al ·e· d . . .. · , . · '· 1 a Y expended a s1gmhcant amount of management time and hw ers f . , f acquiring a chain of f . . . ' y . d ter 01ecou1 ts with a number ot le-1ki110 tanks. ' e-
GRP tanks are f'" • . . . W now 11 mly established 111 a number ol este1 n countnes :I 1 . · dnl 1ave clommated the USA market for many years whei·"' th ,- · • · .._ t:ll c01Tos1on resistant qualities are both well known .1 I'nc .tpprenated. ln reahtv only stamless steel otters · ·. hi J • · cl Yid e <1lternat1ve albeit at a much mcreasecl cost.
Conder'saim has always been to develop better products and building methods to accelerate the construction process the sooner your forecourt is up and running, the sooner your return on investment. 30 years ago we introduced the prefabricated Canopy, later the GRP Interceptor and most recently the revolutionary Fibrelite Access Covers with their light weight, you don't need a 'feat' of strength to lift them. Now, Conder can offer a complete range of ready-made products designed specifically for the forecourt.
Modular Convenience Store and Car Wash buildings delivered to site ready w ired, plumbed and fitted out for rapid assembly; Access Chambers to contain possible fuel spillage and keep out sub-soil water; Silt Traps to avoid drain blockages and last, but not least, Pump Island Barriers all from one source and delivered to site.
This subject covers 2 distinct areas and I will concentrate on the internal inventory control techniques and why it is a quite complex subject. In the second part of this paper Robert Bridges will look at monitoring of the external area. Leak control and loss control are really the same problems in stock reconciliation and what we are particularly keen to identify are where losses may be occurring and when those losses are a risk to safety and the environment.
The first problem to tackle is the issue of closed management of wet stock inventory control and to do this you need accurate information automatically available on the product input (delivery and contents) and the product output which is th volume delivered through the pumps.
Often operators find it hard to accept that the world is not ideal and that the volume in the tank is not exactly what the tank gauge says and that the through-put of fuel indicated by the pumps does not equate exactly to the differences between the opening and closing gauge level readings. Tank and book stock vary and it is this shrinkage we are trying to define in or loss detection. Pump sales less gauge sales equals variance. Sounds very easy, but liken it to this simple algebraic equation.
We know A is 25 but what is C? impossible to define. Inventory reconciliation suffers from exactly this problem.
Unless we get a handle on these variances, we have no hope of proper stock reconciliation or of identifying whether a threat exists to the safety of the environment through a leak. W?rse perhaps is over simplification. For instance, just companng tank gauge readings to pump sales can lead to dangerous conclusions for example a serious leak being masked by counteracting effects.
Inventory control is at the heart of leak or Joss detection but .it is by no means easy to achieve without the correct equipment and automation.
A _filling station on the South Coast of England is currently having a problem reconciling its wet stock. The extent of the problem is 20,000 litres a year. A loss to the site operator of on the bottom line. Theoretically at least, that 20,000 litres could he going into the ground cumulatively.
If this were the USA. where average site remediation is running at a quarter of a million dollars but can be up to 25 million dollars. the costs implication could be alarming. Fortunately perhaps for UK operators. remediation at filling stations is rare and legislation is sparse.
I shall refer often to the States in this paper, simply because ir is where !he mos! practical work regarding leak detection 1Jn underground storage tanks and their lines has taken place. 11 is an extremely high visibility issue. primarily because so many parries are involved. There are regulators from lhe
Environmental Protection Agency and State Agencies and they are putting together somewhat conflicting and often overlapping regulations and performance standards. There are tank manufacturers and equipment vendors who are busy stressing the benefits of their own products and the down sides of competitors' products. The insurance industries watching on the side lines are reluctant to get in the game. Insuring boats, cars and people is easy and infinitely more predictable than leaking underground storage tanks. There are real estate executives, bankers, lenders and the lawyers representing these parties who once may have had a wry smile at the acronym LUST which now has turned to another meaning "Leaking Underground Storage Tanks". These people are all pressing for indemnification and guarantees against leaking tanks before they close their property transactions. I can assure you that there are many beds in the States where the prospect of contaminated collateral is keeping a lot of people awake at night.
But what about the 20,000 litres, where exactly is it? Well, this site has approximately 4 deliveries a week and there is no vapour balancing on site. A typical delivery, given the size. of tankage on site, will displace a vapour equivalent to 50 htres of petrol. 50 litres x 4 deliveries a week x 52 weeks a year accounts for half the 20,000 litres.
How about the other 10,000 litres? As you will already have heard, we only need I degree C difference between the temperature of the delivery and the tank sale temperature to account for most of the other 10,000 litres that is the extent of the_ compensation problem. If we fail to reconcile dehvenes by 20,000 litres in a year, what chance do '!le _have of locating leaks as low as 0.2 gallons per hour which is the US EPA standard? It would be like having one's bank failing to reconcile by £20,000 for some unexplained reason and then trying to notice a discrepancy over and above that of £4.80 a day.
If deliveries are ~omplicated then what goes on in the tank horrendous. Typically, product delivered may differ widely m temperature the temperature of the product already in the tank 1t may have other differences too. (My understan~mg is that on over 40 occasions in one major city last year, it not even the same product going into the tank.) Once m t_he _tank, the process of equilisation takes place. The equalisation is the new product mixing with the old by a complex process of convection and conduction, or ?therwise. by turbulence in the tank caused by the relative with which product enters the tank through the fill pipe. One site in the Midlands. on which have been done, shows a wave on filling of 170mm which takes over 3 hours to die to 1mm remember tank gauges measure height, in the first instance.
The process.of equalising is that of the product in the tank with that of its surroundings through the conductive medium of a wall steel tank or alternatively through the relevant msulator of a double wall steel tank or fibreglass. The ground temperature. of course. is itself varying and the product temperature is therefore often chasing a moving target. The rate of conduction depends on
a whole vaiiety of factors. Heat loss or gain to or from ground water is likely to be quicker than to dry soil which in turn is quicker than heat transferred to an airspace in the manchamber.
Fuel in tanks also stratifies, so where do you measure it? In recent tests it has been interesting to note that in the stratified layers the surface temperature is the most stable band and this closely follows the average temperature in the tank. The most widely fluctuating temperatures are at the bottom and edges of the tank, naturally enough.
The result is that the temperature at which the level is gauged, paiticularly on a simple probe perhaps averaging 2 or 3 sensors will inevitably be different from the temperature of product being drawn from· tank and a failure to reconcile may result. Remember thAt the e1rnr is 0.12% to 0.15% per degree C, a relatively enmmous figure.
The next effects of temperature are felt in the lines as product is sucked or pushed up to the dispenser and it either loses or gains heat from the surroundings, depending on the nature of those smToundings. Relatively speaking the lines are near the smface and the effect of the weather on the forecourt smface has a marked effect on the lines just underneath. On a very hot day the product will heat quickly in the lines although the problem is obviously less acute on a high through-put site. The effect is even more marked if we look at how much of the fuel is the subject of that temperature change. If you look at an average site where the feed pipe is I O metres long and l 'h" in diameter connected to a pump holding about a gallon and with 4 hoses fed from the tank in question you have a total fuel in the pump and pipes of some !JO litres. These pipes, of course, being smaller m volume and nearer to the ground surface, are more prone to temperature change than the tank. It is quite possible to experience wide temperature changes. One test we recently ran actually represented a volume change of somewhere in the order of I litre. This sounds small but in fact it is about 1.2% of the volume in question.
Even this is not the end of the story, as on passing through the the product changes its temperature again. 11 can be seen that the temperature at which the product is metered, will be substantially different from the temperature at which the product is drawn from the tank.
In tests, we have conducted on a site in Kent we measured a 7. degree C difference between the produc't entering the vehicle _at the dispenser and the average temperature of product_111 the tank. Such figures are not presented as typical merely ll t · · · ' 1 us iat1ve of the problem. Suffice to say that if you cannot measure temperature at a number of levels in the tank you take. account of temperature variations in the ab1hty to reconci_le wet stock by reference to tank and pu.mp ales alC?ne critically weak. Temperature is an important issue, certamly 111 the short tenn.
at other variances which affect wet t ·k reconc1hat10n and pump calibration. Pumps are th b· t. nearly ·ill · 1 e as1s o ' measu1 ements o product on the f()r 1 therefore essential that they are calibnted ·1. ecott111l. t is . l"b d ' c<.:curaey and 1e1i:ia111. ea 1 rate accurately. The pump that <>oes · cahbrat1on can be highlighted on a manag.ement s.>'.stem (which I will describe a little later but this. system. of course. a pump that sliahtl overstnkes may look exactly like a pipework leak. '=" y
Water can enter an under<>round l'lnk tl1i-oucrh a h I h h e- ' e- ' () c. t condensata~n or deliberately. Being heavier than the rest of product. 1t will sink to the bottom. Now. althouah 1_11 th.e tank does not in any cdlculat1on. 1t 1s important to know If the level is rising or
falling as any rapid cha11ge in overall level will indicate a problem. On most modem tank aauaes there is a water detection system incorporated anl'on° some you can even measure the height of water.
Evaporation has already been mentioned but it is worth looking at the effect again. When a 10,000 litre tank is filled, vapour may be exhausted through the venting system and the amount lost would be approximately 0.16% of the delivered volume. So taken to its extreme, without vapour balancing tallk. o! product is lost for every 625 used. Imagine this mult1phed b;y all the tanks in the world. Of then:: are other pomts of potential loss in the tank itself of vanous potential discharge points both in the depot through to the car.
What. should be taken into account to effect good stock reconc1hat1on?
Weights and Measures tests are frequently caITied out a11d often the taken from one tank through the pump is put. mto an?ther tank and therefore unsolicited dehvenes occur. It 1s extremely difficult to detennine what effect this may have on the stock inform~tion being provided unless you have a system that can recogmse it.
Theft can be a discrepancy in varying proportions a11d it could be quite sporadic. If every other source of error has been eliminated or quantified, theft could be the only explanation. It is important to know that regular theft follows a particular pattern and a modem wet stock management system is capable of tracing this.
The next effect is the vibration of the liquid in the tank from passing heavy motor traffic or, trains for example, creating wave or ripple effects which have been identified and provide some difficulties to all tank gauges measming height. This is possibly one of the reasons why the electronic hydrostatic gauges which ai·e not effected by surface turbulence due to their mass measurement perfom1 well in the market place.
Now we come to the thorny issue of the accuracy of tank oauaes. All tank gauges measure height and are based on fonn of probe (even the dipstick) all of which have 3 impmtant parameters: height accuracy, repeatability and resolution.
A high specification tank gauge will be accurate to something in the order of plus or minus I mm of height. That might be seen to be poor if you consider that to be in the centre of the tank where a volume level variation may be plus or minus 14 litres per mm, that is a spread of 28 litres and is why the issue of repeatability is so important. If the repeatability of the measurements are neai· pe1tect. the height eJTor becomes no more than a one time off-set and therefore should never feature in future calculations. Repeatability is the ability of the probe to show the same reading each time it passes through a pm1icul<U" height. Looking at the normal accuracies of modern tank gauges. the error in this area n<!rmall7 reflects plus or minus 0.3mm which in the centre 0 1 a typical tank equals +/- 4.2 litres.
final parameter is resolution. Resolution is the gauge's t<'. notice changes in the level. that is. its modern tank gauges have a resolution of approximately plus or Imm which in the centre of the t·ink 1 I . . ' wou l equate ot a volume change oJ about +/- 1.4 litres.
So far we have only considered the measurements of product in the tank as a function of the height readings from the tank gauge but to be meaningful to the forecourt system this has to be converted to volume and there are many ways of doing this. My own company operates 5 different calibration systems, ranging from copying dipsticks dimensions through to incremental or decrimental fills using water proving or flow meter calibration techniques.
All are available according to the budget and the brief set by the customer. The most accurate methods are almost certainly the flow meter or water proving techniques. So you see that there is gauge accuracy and there is calibration accuracy. Both must be taken into account if we are to use the tank gauges, as a comer stone of our reconciliation policy.
There is another variance and that is site plumbing. We really do not have a hope at all of wet stock reconciliation if we do not know which pipe is connected to which tank and what sort of run exists. It is surprising how many times we have been called in to investigate stock reconciliation problems to find that the tank numbering or the connections are not as they were specified when the sites were first fitted with the equipment. (Delivery variances have already been covered.)
If you take into account all or most of these variances you are left with the one that we are perhaps most interested in the leak. There are 3 main areas where product can leak on The tank, the delivery pipes and the d1spensmg u_mt. If you have a very tight inventory control system and ideally an automatic system linked to the tank the pump controller which is also taking the data m real time and taking account of the variances as we have already discussed, through a wet stock management system, then ':"e are a long way towards good site control and effective leak detection.
The output of a modern sophisticated wet stock programme takes the form of up to 8 daily reports. This totals the gauge and pump sales of the day and for the differences that occur between them. It categonses the differences into temperature, evaporation and pump cal"b · . 1 ration effects, thefts, leaks and other anomahes. It also lists deliveries automatically.
A typical report might be:
Gauge sales Pump sales Total variance Temperature Evaporation Pump calibration Theft Leaks etc Deliveries
1044.6 !021.4 23.2 + 9.6 1.7 + 1.5 0.0 32.6 5000
Note that the total variance in this case 23.2 litres in fact involved leaks and other anomalies of 32.6 litres.
In order to ¥ain this kind of output such a system takes 111Jormat1on from an in-tank probe, giving height and ll·111pcrature. from the pump controller and from various ,. 11 , 11• <11mental sensor<., providing information on ground or i1-1i.-111 IL'lllperaturc .1 JI
The system takes the information it requires every time its polled, which is typically every vend. When the nozzle is replaced, all the other sensors are instantaneously polled, irrespective of any other actions going on at the filling station. From this information, the wet stock management programme generates a data base comprising both raw and processed data, taking into account the effects of pump offset of evaporation rate, of product temperature and of surrounding temperatures. The system compounds information on an hourly, daily, weekly and monthly basis to provide historical data in varying levels of detail, depending on age. The system uses this information to produce reports, audible and visible alarms and screen information, both automatically and on demand.
The report possibilities, about 40 in number, might include delivery, theft, leak, activity, tank event and a daily loss report. As such a system is dynamic, taking frequent information, it is able to make "considered" judgements taken over a period to predict leaks with a high degree of certainty.
The EPA regulations which have been referred to, demand that a leak detection system is capable of noticing 0.2 gallons per hour loss but do not provide a maximum to the time window for doing this. However, if the legislation does not provide a time window, practicality does and a busy service station may well not have a sufficient time window for any meaningful results to be produced on leak detection.
It goes without saying that a sophisticated wet stock management programme is capable of autocalibration by p_erfecting or improving on a given strapping table by a pass ?f vends from high to low level. It also goes without saymg that such a process is only meaningful if temperature effects are noted during the process.
However, the detection of leaks is not always just a question of in_ventory control. Many countries outside the UJ<: protection, backed by legislation which ms1sts on peripheral leak detection methods or secondary containment, or both. This is particularly true where fuel is in danger of polluting water supplies, sewer networks or getting into hazardous areas such as railways or housing. A leak may constitute just a tmy mventory loss element but over a period of time it may have disastrous and expensive consequences. To give you an example: If a tank were leaking at the rate of 0.2 gallons per hour and it was undetected for say 6 months, gallons would have escaped. On a high throughput site, 10 the same 6 months 520,000 gallons would have passed through the leaking tank. The leak constitutes only 0.168% ?f the volume and could easily be ignored, but 870 gallons mto the ground cannot.
We have seen that a sophisticated wet stock management system can explain any variances betwe.en pump crauge readings categorising the anomalies and quant1fymg ""1 k Th" i·s n'ot however the way that leaks are usually ea s. is ' ' . . t t k d . d d w1·11 not be until automatic we s oc 1scovere an I · t d leak detection become the norm. t 1s more mana cremen an · h d "" I th human senses of sight and smell wh1c etect ;resence of It is at this stage .that · g turns to media coverage and reputat10ns Public awareness · · h h bi f d I t this conspmng wit t e pro ems o are made an os ' · . ted collateral ment10ned earlier. contamma
The wornes that tank usually revolve around the systems external to . tion It is likely that a site operator of that but in a different way to spills will want to react to h will certainly not wish to have and overfills. He or s .e ting contamination in the ground, 'false' alarms due !0 around is of course a potential although product m t e what its origins. It is environment hazard ful to be able to distinguish therefore extreme.ly at alf ossible, and there are systems between To pdistinguish between an overfill, which can final stages of commissioning of a spill or leak dunng t I difficult. site is, though, extreme Y
However tank leaks are considered potentially more serious to the volume at risk at any one time and this risk depends on the age of the tank, at least in the case. of steel tanks. If, as it has been suggested, there were a policy adopted to test all tanks at 20 years, 25, 30, 32, 34, 36 years and so on, 58,000 tanks in the UK would need testing today and close on 20,000 would fall into a test band each year. These statistics are well known to Normond's tank testing companies.
Line leaks may be due to faulty workmanship on installation, the action of continual hydraulic shocks due to valve closures or pipe fractures caused by mechanical damage at installation or post installation. Our evidence is that plumbing leaks at installation have a very high incidence and suggests that continuous monitoring for leaks during commissioning can be used as a tool to ensure that the pipework contractors have done a good job.
Leak monitoring devices can be categorised in a number of ways according to whether they:
I. respond to liquid or vapour
2. measure or quantify leaks
3. locate the source of a leak
4. have adjustable sensitivity and what levels of sensitivity can be achieved or not achieved
5. distinguish between free and residual product
6. detect spills or leaks or both
7. can be readily retrofitted
In addition to the use of leak locating cable and pressure sensing systems covered earlier, there are vapour monitoring, water/product monitoring and interstitial monitoring methods.
reventable. The latter can be
of a site a spill can cause a . I operat10n ' · k Dunng leak detecting sensors may I_JIC up. problem which some commonly used in the dispenser The permeable. to penetrate quickly and thus area, allow spilled. P of volatiles. In Holland are inhibit the able pavements and gullies to experimenting caused by motori.sts and they ensure the collectJOn 1 P 1000 litres per site per year. h tota ovei · · I ak estimate that t ese uch spills are capable of Potentially, at s der the dispenser area. detection devices un h ver will contain only heavier contamination on site, ·ii either not detect these or fractions and some. sensors without causing alarm will indicate their presenc conditions.
Spills and overfills are p Electronically controlled rfil l preventers. prevented by ave 1 h . 1 overfill preventers, can valves as opposed to mec to ensure that they ' · sly 1110111 · k" themselves be contrnuou 1. · made without ns mg . b f ·ea de ivery is k operate effectively e 01 f failure to operate. Lea s, environmental consequences o bi and therefore the need ·1 preventa e · though, .are less Y. more important. The. 1s to for contmuous is t the site cond1t10ns and install the equipment which best sui s environment.
. f I ak and how can the)'. be But what are the sources 0 e tai1ks or from Imes . ·ther from · h momtored? Leaks are ei llated st·itistics, bot ( 1 d. d.. , ) We have co · ' · , me u mg the 1spenser · 1 h h these somet11nes from the UK and the USA and. a t generally conflict. it is probably true to s<1y thal b th sides of the outnumber tank leaks by at least 4 to on ° · · Atlantic.
A summary of one US tank testmg · 1 ticrht that 25% of existino UST systems are found to be no; d f 1r and 84%, of these tfohtness test failures were e l t "" , Wh"l ·t It does no by loose tank fittincrs or faulty p1p111g. 1 s . [" f reduce the of the problem it is probably a ie · , h · l l ns aie to 01! companies to note that most of t e pw_J ei ·. h caused by faulty connections rather than corrosion of t e systems within the ground.
Vapour monitoring which is more commonly used for protecting the storage tank systems rather than the lines although the latter is possible. It is capable of detecting small leaks very quickly depending on soil type because vapour travels through the ground 50 times as fast as liquid product. It should, however, be noted that an alarm from a vapour monitor does not necessarily indicate a tank '\:problem, the results must be carefully interpreted and analysed to differentiate between spills and leaks. The vapour monitoring system consists of vapour monitoring device or sensor and a vertical well but this may be angled or horizontal. The monitor works according to the p1inciples of volatilisation of the from liquid to gas and the subsequent d1ffus1on or spreadmg of the gas through the substrate.
The volatile components of the stored fuel set off the vapour .if the threshold of measurement, usually in parts pe1: million (ppm): a certain predetermined level. It is often the sub.1ect of discussion as to what level this threshold should be but. 1500 ppm would be typical. only lookmg for trends can readily between spills an? leaks and can even provide as to the source .ot the problem. The sensor may be sited m a vadose well or 111 the kiosk.
!here are a number of factors which affect the sensitivity ot vapour wells: temperature. soil characteristics. water conditions. climate. product characteristics. site location and Well construction. ()f tht'sC soil characteristics. \Valer conditions ancl product characteristics arc particularlv important. ·
The installation of vapour monitoring systems comprises a number of stages. The first is site assessment to make sure vapour monitoring is indeed appropriate to the site characteristics; that the soil is permeable to the flow of vapour, that the water level is low and so on. The second stage is to choose the particular form of transducer or monitor in the vapour well. The third stage is to design the lay-out of vapour wells around the site. Where a tank farm is protected for example it is typical to drill vapour wells at the comers of the tank farm area and to sink those wells to perhaps 450mm below the bottom of the lowest tank. The fourth stage is the construction and installation of the vapour well. The fifth is the operation and maintenance, calibrating the sensors and beginning the monitoring. The last and most important stage of course is in the analysis of the results and readings made by the vapour well. A well installed system will give very fast and sensitive leak detection.
Retrofitting such a system is also very easy although there are ducts required for the cabling from the vapour wells to the monitoring point, usually in the kiosk. If the vapour wells are used on the comrs of the tank farm area it may only be necessary to cut ducts from the vapour well position to an adjacent manchamber, since there are probably ducts from tank gauges which can be sensibly used. Like most leak detection instrumentation, the most crucial stage is not the installation of equipment but in the collection and analysis of information it provides and the resulting action taken.
Free product in the ground can be detected continuously using free product monitors. There are several types but I will describe just one of them. There are two parts to a product monitor, one is the vadose well which is a well that operates between the ground water level and the forecourt surface. The other part is the monitor itself.
The well is mounted in pea shingle and typically comprises a I OOmm diameter, rigid walled, perforated vertical tube.
consists of a float running on a braided wire is anchored on the bottom with a weight and lightly tens1o_ned on top. The float must be able to run freely on the wire and m the tube. Contained within the float are two electrodes separated by distance of 80mm and a reed switch. A small electrical potential is applied across the electrodes through the reed switch via a fan fold cable which allows the float to move up and down, some 2.5m if necessary.
In an empty the float sits on a magnet at the bottom of the, well an_d "dry". If water or product raises the float,. the ability. of the surface liquid to pass a small is tes.ted (water conducts, product does not). th!.s means the eqmpment is able to record either "wet" or leak . In the latter case an alarm sounds.
The system is to understand, to install, to interpret and the level of floatmg product detected can be adjusted from well. n:im to SOn:im. The system is easily retro-fittable and is ?est smted to a situation where the ground water table I el nses abov t· k b ev · · . e an Repeater indicators at each well show the status of mdividual wells.
It should be noted that p · d II · · · ro uct we s are less sens1t1ve to installa!ron. than wells. The water content and the 1ype of sorl are still impo11ant but the temperature of the prodL'.ct. the th_e volatility of the product. are not. The construction. pos1tronmg and the depth of the well are cnlrcal. though.
1n1ers1i1ial monitors are additional to secondary L." 11 1wnr11cnl. Morntored clouhle skinned tanks and lines have till' added rnmplexrry that the interstitial space can have pr"dtH"f ll'akmg in. water leaking in or monitoring fluid <if
used) leaking out. The monitoring fluid can be brine, ethylene glycol, diesel oil etc but should be chosen not to embarrass car petrol tanks or be potential pollutants . If they are hazardous, do not float on water or are miscible in water, they may be more dangerous than motor spirit.
Monitoring for interstitial fluid is usually achieved via two level switches, one detecting ingress and one detecting outflow. Alternatively, an electronic sensor may be used in the interstitial space. Such sensors might include vapour sensors, water/product detecting cable or product/water sensors. Vapour sensors can monitor a large space effectively but would not detect failure of an outer skin. Water/product detecting cable can detect both water and product and can discriminate between them. A third alternative is hydrocarbon detecting cable which can detect failure of just the inner skin. Finally a product/water sensor such as described earlier can be used at a sump connected either to the manifolded interstices of Jines or to a tank wall space. Such a sensor can detect ingress or out-flow and act as a site for recovery of free product.
In summary there is a range of techniques for checking oil Joss at a filling station:
Tank gauging
Tank and line tightness testing
Wet stock management
Vapour monitoring
Product/water monitoring
Interstitial monitoring
Hydrocarbon detecting cable
Pressure sensors
Most of these can be used for continuous monitoring S can quantify leaks. Some can suggest the extent or" 1 Orne Some can leaks. Sm:ne can leaks. All right conditions to function effectively and all need the appropriate expertise to interpret the results. The No the approach is to provide a range of solutions to the leak detecti?n with to of associated diagnostic and remediat1on act1V1t1es. all
Finally, most of the systems described can be re monitored. Each remote monitored site carries a mod motely a dedicated telephone line. The on-site computer em and routinely once a day to a central computer in when an alann condition occurs. The diagnostic or on the screen can pro_vide a valuable tool fo ation engmeer and can not only obviate the first site visit b r the !n some remove the necessity for one at all. Theut can mformat1on. can be to the equipment su rsarr.ie case of eqmpment failure or where additional exp/P ier required. Remote monitoring can firstly, therefore is fast response and low down time at a site and ' provide ·11 ·f ' secondly prompt sp1 response 1 necessary. •
To summarise the benefits of continuous · leaks are: momtoring for
The obvious protection of the environment
The avoidance of legal proceedings which m from leaks ay result
The avoidance of clean up costs
The avoidance of third party claims
The protection of the company reputation
The of local harmony
The avoidance of retaliatory action from custom ..
The t. f · e1 s preven ion o mventory losses
The mamtenance of real estate value
More generally. continuous monitoring. whether usina t stock management systems. line sensors or external can make economic as well as environmental sense b t, 11s. ·t· · · · u on y 1 appropriate and prompt follow up action is taken
INSTALLATION, CAL1BRATldN MONITORING AND MAINTENANCE i
Normand Environmental Systems is at the forefront of supplying the most appropriate products and services for .environmental protection within the retail petroleum market.
Each site hos on individual risk profile. Normand is able to evaluate them and provide the most appropriate products and solutions for protecting these sites and their environment from the consequence of undetected losses or spillage.
The products and services provided by Normand Environmental Systems include con.sultoncy, advisory and risk assessment surveys, as well as a range of leak detectors and monitors, supplied and installed to suit site conditions.
When 0 leak is detected or suspected, Normand will provide high.precision tank and line integdty testing services to confirm the site status This service con also be used on old or ageing tanks to confirm the security of the system
With the introduction of 0 site audit and investigation facility, and 20 methods. for dealing with a contaminated site, Normand Environmental Systems is well placed to advise you on oil your environmental needs Our complete approach will give you complete protection.
Hydrex House, Garden Road, Richmond, Surrey TW9 4NR, UK Tel: 081 392 1355 Telex 919193 Fax 081 878 6642
Corroshield have been lining petrol storage tanks for over a decade endorsing o ur quality of specificati on and experience in this spec ialist field
Corroshield System 80 tank rehabilitation is not a repa ir or temporary solution· (it is new tanks for oldi backed by our guarantees extended for as long as you require
So what do you do when your tanks fail (0949 21032) They could be rehabilitated and returned to service w1th1n 14 days without disruption
In any forecourt operation tank protection be paramoun'., as t.ank failure and subsequent replacement could wipe out years of profits and impose 1mmed1ate financial burden.
DON'T WAIT UNTIL IT HAPPENS: now for details on how we can provide protection for your underground storage facility at very little cost.
CORROSHIELD LIMITED
Unit 1, Hackers Close, East Bridgford, Nottingham NG13 8PG Telephone: (0949) 21032
COMMERCE HOUSE, THE MALTINGS, STATION ROAD, SAWBRIDGEWORTH, HERTS. CM21 9JX Telephone: 0279 723448
At a brand new petrol filling station with overfill prevention devices, one major Oil company did not have to wait long before reaping the benefit of installing these devices
The A PEA. Bulletin. August 1990At one delivery the road tanker driver noticed that the tanks could not be filled as the OPD had operated. The gauge was checked and it was noticed that according to the reading there was still room to install more product. The hose was drained however and the remaining product was returned to the terminal The manager had thought that something had gone wrong with the overfill prevention device. However, On investigation it was noticed that the numbering of tanks to gauges was incorrect, the gauge that was supposed to refer to the tank in question referred to another tank. The fitting of the overfill prevention device saved product loss, possible danger from fire and explosion and of course environmental damage. / /
The simple fact is that the forecourt in question was fitted with an OPW 61 SO Overfill Prevention Valve Wisely specified by a major multinational it was simple, quick and easy to install (even in existing sites) and soon proved itself in the field.
Needless to say the OPW 61 SO Overfill Prevention Valve is an example of OPW's ongoing commitment to reducing environmental and safety risks on the forecourt, backed up by OPW's leading position in the USA, where the world's most stringent forecourt safety standards have been in force for some ume.
If, like the wise multinational, yo would like to know more about OPW products, contact OPW Fueling Components Europe .
It will save you being wise after the event.
The OPW 61-SO overfill prevention valve is designed to be a simple, low cost solution to positive shut-off of product fill for underground storage tanks. The shut-off valve is an integral part of the 4" drop tube used for submerged filling No extensive or expensive excavation is required The OPW 61-SO can easily be retrofit into most existing locations. No special manholes are required Installing the OPW 61-SO is as simple as changing drop tubes.
The OPW 61-SO is a two-stage shut-off valve. When liquid level rises to approximately 95% of tank capacity, the valve mechanism is released and the valve closes automatically with the flow This reduces the flow rate to approximately 5 gpm through a bypass valve The operator may then stop the filling process, disconnect and drain the delivery hose. As long as the liquid level exceeds 95% of tank capacity the valve will close automatically each time delivery is attempted.
If the storage tank is overfilled to an unsafe condition and the liquid rises to about 98% of tank capacity the bypass valve closes. No additional liquid will flow into the tank until the level drops below a reset point.
* Simple, easy and quick Installation no excavation or special manholes required.
* Economical costs a fraction of expensive, complicated and difficult to install valves.
* Completely automatic operation no pre-checks to perform, no resets, no overrides to be broken or abused
* Works at all flow rates operates directly from liquid level.
* Will accept a dipstick for gauging.
* Retrofits directly for existing tanks and 4" riser pipes. * Automatic hose drain for operator convenience.