THE BUL L ETIN
Journal of the
Petroleum and
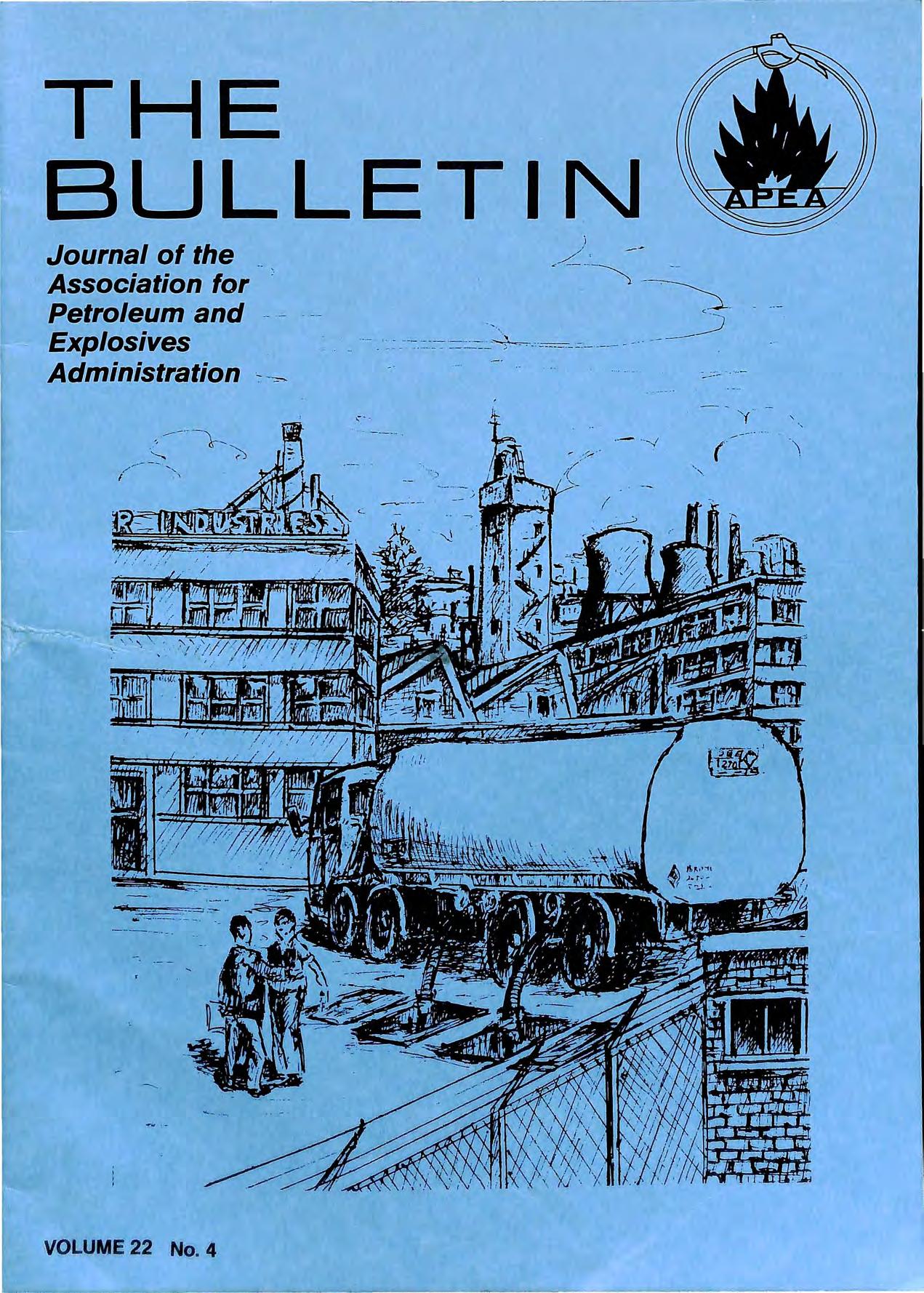
Explosives Administration

Journal of the
Petroleum and
During the past 2 years a different type of drive belt has appeared on forecourt petrol dispensers. The name is Tab-Link, and its unique polyester/polyurethane construction enables this belt to last a minimum of six times longer than conventional V-belts
It's easier to service, as one reel enables the service engineer to make up any length of belt to suit all pump assemblies, thereby greatly reducing the stock carried
When it comes to the manufacture of pump equipment a simpler design is possible using' Tab-Link, as the tensioning and sliding adjustment systems used with conventional drive belts aren't needed " Tab-Link is in successful use in petrol I dispensers throughout Britain. including those serviced by Pump Maintenance Limited, and built by Avery-Hardoll Ltd Tokheim Ltd. and Ferranti Ltd
Suprabloc covers have been specifically designed for use where frequent access is required to part of a chamber within a block paved petrol filling station forecourt.
The system presents the minimum of metal to the general layout yet provides easy, lightweight access.
The solid bottom covers and frames are offered with 300 x 300mm lift-out section available as recessed or solid chequer top which can be fitted centrally or offset over chamber
All units are hot-dip galvanised after
manufacture to ensure long-life resistance against corrosion and are fitted with nitrile sealing gaskets.
Detailed and illustrated technical handbook available to speclflers. Solid top peephole
Recessed peephole
NOTES
Published
Honorary Editor: Mr. GA. Edney, 22
Honorary Secretary: Mr. E. Brown, Cambridgeshire County Council,
There has been a number of rumours about how the new Flammable Liquid Regulations will do away with Licensing and replace it with a system of notification and sUIVey.
In this edition is published just one example of how important the powers of licensing are, especially when the general public are involved.
Self-regulation MAY be effective where only the safety of people-at-work is at risk. As soon as that unwieldy animal, the gets pious hopes about people actrng senSIbly out of enlightened self-interest tend to become laughable. As long as the public get involved with flammable liquids (and gases) definite legislation firmly enforced will be needed.
Gosling of Calor Autogas, interviewed in the recent edition of "Company Car", rejected any doubts about the future of auto gas. With improvements in carburrettion and fuel injection and more attractive car-conversions he felt that the is growing and announced that is busily LPG for business car use. It is also trying hard to mcrease number of retail outlets, and is aiming to have LPG available at one in three motorway service areas within the next 18 months.
The Freight Transport Association has introduced a new inspection service for tankers involved in the transportation of flammable liquids to meet the requirements of Regulation 7 of the new conveyance Regulations, which comes into force at the beginning of next year.
The service, based on the FPA's Vehicle Inspection Service at Tunbridge Wells, will comprise of an examination of the tank, a check on tank fittings and ancilliaries, a wet-test for leaks, a survey of the electrical equipment and a check for compliance as regards design, construction and marking.
Elf-Aquitaine, the French oil company, has discovered an unusual use !or the tank container the intermediate storage of crude 011 extracted from marginal oil fields d . Such operations are only VIable If mobile storage facilities of varying ca 't' bY 'd d h paCi les can e provI e on t e actual production sites.
the early stages of production, the tank containers are utilised to shuttle oil to the refin Wh . . f II fi ery. en operatIons are m u swmg, Ixed storage tanks ar' II d . e msta e and the tank con tamers moved onto the next'ng site.
An experimental new im B' ., been launched b T age or ntam s service stations has y exaco at a north London site.
The new image is called "S and black c I h ystem 2000". It consists of a red o Our sc erne 11" d design of canopy d a le to. a .much sleeker overall identification sign bUildmgs. The "goalpost" mcorporatmg ele t . . b particularly striki c romc pnce ox is ng and features th "T S" which is the trademark of T ,e tar logo exaco s operatIOns world\\ide.
A Code of Practice , h electrical apparatus c Oi t e repair and overhaul of Ex lOr use atmospheres has been bl' 111 potenlially explosive pu Ished '.' tl b I Electrical Equipment M f .Jum y y t le BntIsh anu acturers A d h Association of Electrical M. 'h' ", ssoClalion an t e ae mery I rades.
The Code of Practice is available f' RF Street Iond(JIl W'("')H -DN lom MA, H Leicester " '- In or AFMT 4- 'I I I S" 'I ' U AB ' ,:) S wen Lane .onc on. vv -+
On 21st August 1984, Trusthouse Forte Service Stations Ltd were convicted at Atherstone and Coleshill Magistrates' Court, Warwickshire, for contravening a condition of their petroleum licence. On 19th February 1984, at 01.20 hrs, a Petroleum Officer from the County Trading Standards Department, attended an incident at Corley Service area on the M.6 at the request of the Fire and Rescue Service. The was a strong smell of petrol in the sales kiosk and the Southbound Services had been closed. This was reduced by opening doors to increase natural ventilation. On examining the manholes, the officer found eleven tank caps were not fitted. Although it was unclear to what degree this was responsible for the vapour build-up in the kiosk, the missing tank caps formed the basis of the charge. The company were fmed £250, £ 132 costs were awarded to the Council. Condition.Number 7 of the Council's licence conditions requires petroleum spirit tanks, together with fittings to be efficiently maintained. Breach of this condition was contrary to Section 1(3) of the Petroleum Act, 1928, which is an existing statutory proviSIon for the purposes of Section 33(3) of the Health and Safety at Work, etc., Act, 1974.
From Cambridge comes the following cautionary tale.
The Chairman of a scooter club was instructed to purchase .sufficient petrol to enable twenty members to travel to Bourges, France. The object of the exercise being to allow the members to re-fill their scooters en route from the stock.
A 4S gallon drum was obtained and taken in the back of a Ford Transit van to an attended self service station. When the drum was about half full the automatic cut out operated and a request was made to the console operator for more petrol. The operator saw the drum being filled yet authorised more petrol to be placed in the drum.
The van complete with drum, which was leaking and only had a cloth stuck in the top, was then driven off. The driver left the van outside a house for about an hour and on his return found the van awash with petrol. The Trading Standards Officer, police and fire were called and the van washed out, taken to a place of safety and the petrol burned. The petrol had become contaminated by the contents of the ilium (bitumen of some sort) and was useless as fuel.
The driver of the van was fined :2 x £50 with £25 costs for conveying petroleum spirit in a container ",:as not securely closed and not marked with, any 1I,ldlcatmg contents. The garage were fined L 100 .L 75 costs fOl dispensing petroleum spiIit into a vessel which was not of cU1 approved type.
(any further instances of idiocies of this nature would be gTatefuIIy received -Editor)
New procedures for the of f1ameproof enclosures have been p.ubhs.hed by BASU<,}':'-. They cover both the component certIficatIOn or lor empt y flameproof enclosures and the 01 enclosures having component certification to fully certIfied f1ameproof apparatus.
As a result of a re-organisation \\ithin the department, tht' fm'mer BASEEFA Newsletter will now beconw a part of an Electrical Equipment Certification Service (EEl'S) Newsletter, which is a\'ailable from the EEl'S, Harpm 11ill, BuxtOIl, Derbvs SK 17
It is with regret we report the death on the 14th May, 1984, at the age of 72 of Mr. John Beer, fonner ChiefInspector of Weights and Measures for the City of Worcester. His Authority was a founder member of the West Midlands Petroleum Acts Administration Group in 1958 and John was Chairman of the Group in 1961. He remained a valued member of the Council of the Association until reorganisation in 1974.
John contributed considerably to the success of the Association in its fonnative years, presenting papers at district meetings and lecturing on a number of occasions to students, the school at Attingham Park.
He was a keen sportsman and photographer and was Chairman of the Institute of Trading Standards Administration in 1975, the year of his retirement.
Our condolences go to Mrs. Beer and her family.
A comp h ' re enslve new and uniform system for the packaging and labelling of dangerous substances designed to mcrease health and safety protection for both workers and the general bl"' " pu IC IS contamed m regulations which came into operation on 12th September, 1984,
The were drawn up by the Health and Safety Commission, follOwing extensive consultation with industry trade ' ' unions, local authorities and other relevant organisations,
regulations have been designed to provide a standard agamst which the potentially dangerous properties of substances in I d' , ' , c u mg preparations and other rruxtures can be assessed and th d 'b d" ' , , en escn e m a consistent way on labels, By re I ormatlOn a out the substances and making provldmgmo 'nf ' b sure that the ' bI ' Y are sUlta y packaged nght from the point of manufacture, through the distribution chain including conveyance b dd' , th h Y roa ,an eventually to the shopfloor or mto d e they offer greater protection for industrial and h omestJc users alike as well as helping minimise the risks to t e emerge ' ncy services and general public should an incident occur on the highway,
The new ruI '11 h es WI ensure t at a package used to supply and convey a dange b h drum f rous su stance, wether it be a commercial the or a small bottle or paint stripper for potential cl Will carry an eye-catching label showing the m t' anger of the substance together with advice on the os Important safety precautions,
The operational d t £ h 1984 alth h a e or t e regulations is 12th September full a transitional period, for the provisions to addif IY mto effect, is given to 1 January 1986 with an Iona one-year 'd C litres, peno Ior certain packages ofless than 25
In the main the regul' , and Safety E ,atJons Will be enforced by the Health xecutJve or ' " authorities, except in th m certam clfcurnstances, by local e case of supply to consumers where
A range of industrial and domestic sized containers to demonstrate typical forms of labelling for supply, for conveyance and for both supply AND conveyance,
enforcement will be by the local weights and measures authorities or the Pharmaceutical Society of Great Britain Ltd,
Two approved codes of practice, to be used in conjunction with the regulations, on classification and labelling of dangerous substances and on packaing for conveyance by road, will be published shortly by the Health and Safety Commission together with more detailed guidance on the scope, interpretation and application of the regulations ,
Last month the Commission also published the Authorised and Approved List showing those dangerous substances for which it has approved particulars to be shown on labels when supplied and/or conveyed by road in packages,
The Classification, Packaging and Labelling of Dangerous Substances Regulations 1984, SI 1984 NO: 1244, available from HM Stationery Office or booksellers, Price: £4.50. ISBN 0 11 047244 6.
The flexibility ofthe new fe[m latZ·07 ·ll b- lIS Z ustmted b th' lab both the supply and conveyance int, .' 'Y, IS elon which ':I07matwn are dISplayed ,
Herr Dopner was, before his retirement, with Deutsche BP AG, and was, until last year, the Chairman of the DAbF (the German Committee for Flammable Liquids).
This is the fIrst in a series of articles which, it is hoped, will explore the situation in storing and handling petroleum in various countries of the world.
The directions (law, regulations and technical rules to the regulations) concerning storage and handling of petroleum products in Germany are very extensive, therefore only those, which in the view of the author are of some importance, can be mentioned.
In Germany the law is very comprehensive: storage and handling of flammable liquids require permission for the construction and design of the plant, which must also be controlled before starting operations and then every 5 years by the officially acknowledged experts (TUV). The authority granting these permits has to consider the demands of 3 areas of law:
1. Gewerbe-Recht (Industry-law), to protect against fire and explosions, and more recently to fulfil the clean-airregulations,
2. Wasserhaushalts-Gesetz, Lager-V erordnungen (Water- protection law).
3 Bau Recht (Building- and construction- law).
As protection against fire and explosions, the first regulations were issued in 1883 (and 1882) and since that time have been continuously adapted in accordance with technical developments, the latest in 1980. For this purpose, the Government has appointed (since 1925) an advising committee, the DAbF (Deutscher Ausschul3 fill brennbare Fliil3igkeiten, German committee for flammable liquids) which consists of coming from the authorities, from industry and the TUV.
Essential resolutions of the DAbF (ie. tanks must be liquid-tight and remain liquid-tight and must be controlled every 5 years) require the consent of 1.) the Federal Government and 2.) the Bundesrat (second chamber of the Parliament) to become a "Re,l,'1llation", interpretations and details of these "Regulations" are decided by the DAbF and published by decree of the Federal Minister of Labour as TRbF (Technical Rules for flammable liquids) (ie. how tanks have to be built wall-thickness, steel-quality, welding-procedure, corrosion-protectIon Essential demands of the Water-protection- and the BUlldmgand Construction-laws are sometimes in conformity with those of the Industry-law (ie. liquid-tight tanks), others are contrary (ie. spill ages of motor-gasoline shall, according to the Water-protection-law, in no case cause pollution whereas 111 the Industry-law the major importance is the avoidance of fire (Ir explosions). In order to find generally accepted solutions to such diverging questions, thp DAbF have established (since J ()(,4) a good co-operatioll with the experts of thp Water fJI"IJtection and the Building administration by them as full members of the DAbF. Since that time the I Rbf llIvolved tllP demands otall .i areas of law and every operator
is entitled to permlsslOn for storage and handling of flammable liquids, as long as he accepts and fulfills the conditions of the TRbF. Alternative solutions need an exceptional permission, only granted if adequate safety is proved by expert evidence.
The presently valid rules shall now be explained with 2 examples:
1. Installation for storage and handling of flammable liquids, and
2. Refuelling station for road vehicles (filling-station)
1. Installation: The products are generally stored ground, at smaller depots in underground tanks. The aboveground tanks must be constructed according to DIN -standard 4119. In the past few years, permission was generally granted only for double-bottom tanks, where the intermediate space between the bottoms is (for example) vacuum-controlled for the indication of any leak in one of the bottoms.
The above-ground tanks must be installed in bunded areas impervious to liquids, which have to be tested before starting operations and thereafter every 5 years. The capacity of the bund must be equal to the largest container, but the bund area 0 should not exceed 7.000m ,in case of only one tank 10.00 m. Otherwise special fire-fighting equipment (ie. separationwalls and remote foam-nozzles) will be demanded. For fireprotection and fire-fighting reasons the distances between tanks within one bund-wall as well as the distances of tankgroups from another are fixed. Likewise fixed are the distances from the tanks to buildings dependant on the tankcapacity and the danger-class of the products.
Storages of flammable liquids must be sun-ounded by a "safety-belt" (respectively 10 to 30m) according to the capacity and construction (ie. floating blanket) of the tanks and the danger-class of the stored product. The purpose of the safety-belt is to protect the neighbourhood against the consequences of a fire in the installation as well as the installation itself against the dangers of an ignition from outside.
on of the stored product and operatIonal conditIons (ie. pump capacity) zones (0, 1 and 2) .are defined, where according to the probability of the of dangerous explosive atmosphere graduated protectlOn measures are fixed. These zones exist· . I d m partIcu ar aroun the of the tanks and at filling- and dlscharge-pomts, around pumps valves flang t E ." es e c. very machine or part of eqUIpment that shall be used withi h ' t h th n t ese zones mus ave an au ontatIve permit for the use in the zone concerned and / or must not become a source f. . h . II 0 IgnItIon nelt er operatIOna y nor m case of a disturbance II be expected. So vehicles are only allowed in zo no r1m a'y to ne le. a road-tanker loadmg rack for gasoline if th hi I . e ve c e IS authontatlvely permItted for this operation.
For the and. the filling- and dischargea.n-angements of an mstallatJon definite demands are I ·d down in the TRbF, of which the follOWing may bE'
I. Only pipes with a quality-certificate are admitted.
2. Plastics pipes a.re onlv pennitted from ' th . d . / au onse matenals.
3. Hoses of tested (]ualityare only permitted for temporary connectIons, le. for fillmg a container.
4. The pipework must be in such a condition, that dUling operatIons the accumulation of dangerous static electricit y is not possible.
.). Thp demand of double skinned pipework especially for unclergnJuncl installation is increasing.
6. The floor of the filling- or discharge-points must be lmpermeable and constructed in such a way, that spillages in any case are observed and may be removed.
7. Overfilling, of the storage-tanks as of any kind of transport, of barrels etc. must be excluded by approved safety-equipment such as automatic shut-off valves, quick-acting valves with dead-man's handles or operational measures including volume pre-setting.
8. In some cases the clean-air-administration tried to enforce vapour-return for all loading procedures. In any case above-ground tanks for volatile products must be equipped with a floating blanket and be painted in bright (white) colours.
On prin.ciple the underground storage is only permitted in skinned tanks, with an alarm-equipment, which shall mdlcate an eventual leak in one of the tankwalls. All other demands are similar to those for above-ground storage but with smaller danger-zones and safety-belt. '
FO.r both of I once again stress the obligation for mspectlon by TUV before starting operations and subsequently every .5 years, with the main aim to maintain safe and to prove the tightness of the installation at any pomt.
2. Filling station. Storage is generally only permitted in und.erground, double skinned tanks with approved alarmexactly as in depots. Only quantities up to 1000 litres are permitted above-ground as well as m t - 1- fill" h 0 or cyc e 1 mg-eqUlpment Wit a total capacity up to 200 litres.
If venting of the tanks during discharge by road-tankers is not possible without any risk, vapour-return has to be used. Recently the clean-air-administration has tried to demand vapour-return for ALL refuelling-procedures at fillinO"stations.. This presently is the subject of delayed along With the demand for vapour return while filling motorcars.
Dispensers must be approved by P.T.E. (= V.- eights and Measures Authority) and must be fit for service or self-sef\ice. Self-service without supervision ("ghost-station") is onhallowed with slot-machine-dispensers, which are operated either by input of money or credit-cards etc. ""ith a ma..'<dmum delivery of either 90 litres or 3 minutes pumping-time.
All dispensers must be fitted with approved automatic nozzles, which shall prevent spillages on the fore-court. The area, where the nozzle can be moved \\ith horizontalhstretched hose plus 1 metre must have a solid and impermeable base, where spillages can be recognised ,Uld removed.
The rules for the pipework are similar to those of the depots. On filling-stations too, double skinned pipes are demanded. with the alternative of plastic-coated steel-pipes installed \\ith such a slope towards the tank, that in case of a leak onh minimal quantities can cause pollution.
The filling-stations must be inspected before operations and subsequently every 5 years by Tt\' '
Storage and handling of auto-gas is only pernlitted. if considerable safety measures are applied.
For both, the filling-stations and the installations the waterprotection-administration has in the 70's asked for the same safety standards for existing tanks, as is achieved with double skinned tanks. Mter long discussions and tests the single-shell underground tanks could be refmbished by
TOv inspection, to establish that the state of internal corrosion is not dangerous and subsequently a
-coating with approved plastic anti-corrosion material, plus
-cathodic protection of an approved type, unless a TOVtest has proved it to be unnecessary.
For above-ground flat-bottom tanks, discusssions are going on for the approval of alternative solutions to the fitting of a second internal tank-bottom.
In its Annual Report 1983/84, the Humberside Trading Standards Department reports that the year in question again saw the closme of a number of filling stations, the total number of licensed storage sites in the county having dropped from 17b!) to 1672, with a reduction in the quantity licensed to below 1,000 million litres. The most dramatic change over the decade has been the removal or improvement of many sites which were inadequate from a safety viewpoint.
In explOSives, the number of registered premises, primarily the storage of fireworks, declined sharply from 394 to 286. I he report suggest that this might have been due to the large in registration fees.
Inspection levels were broadly maintained and although numbers of tank tests increased slightly, the report recognises there is still considerable backlog of testing in certain areas.
The report describes the use of a new type of ullage rod for the testing of storage tanks. This rod, which was developed by the Department, incorporates fibre optics and in use is proving a distinct advantage over the previous dipstick method.
It also discusses developments ·in improving the efficiency of service and sales on filling stations, and remarks that while these modem systems do not directly affect the safe-keeping of petrol, any system which reduces public activity on petrol station forecourts also improves safety standards.
1st APRIL, 1983 to 31st MARCH, 1984
Trade
Petroleum Retailer Petrol Site Manager
Garage Proprietor
Motor Dealer Shop Proprietor Statute
Nature of Offence
PETROLEUM CONSOLIDATION ACT, 1928
Failing to comply with petroleum licence conditions Failing to display notice before the storage tank cover plate was removed Failing to secure that a competent person was in charge of the storage tank for delivery purposes. Failing to keep a constant watch on petroleum spirit storage tank during delivery Failing to submit an Electrical Test Certificate
Making false entries in documents to the effect that he was (a) Electrical Engineer and (b) Chartered Electrician
Section 1(3) as amended; Health & Safety at Work etc. Act, 1974, Sections 33(3) & 33(1}(c)
Health & Safety at Work etc. Act 1974, Section 33(1}(c) , Section 1(3)
Health & Safety at Work etc. Act 1974, Section 33(1}(L) ,
EXPLOSIVES ACTS, 1875-1976
Keeping frrworks which were not stored safely
Section 22 & 39 Order in Council No. 16
CASES IN WHICH PROSECUTION WAS NOT UNDERTAKEN BUT WHERE A FORMAL WRITTEN WARNING WAS ISSUED
Petroleum Consolidation Act, 19:1H
Non-compliance with licence conditions
Non-compliance with conveyance conditions Storing without a licence
No. of Cautions 4 :l
Fines £200 £40 £50 £100 £250
Fire caused by the ignition of a petroleum spirit! air mixture is recognised as a major potential hazard at the service station. This is reflected in the conditions and specifications attendant to the design, siting and layout of the premises and plant installed. Standards are set for the management of the site and maintenance of equipment. All these measures are directed towards the safety and health of the staff employed, members of the public and those living or working nearby.
Hazards and potential dangers arise not so much through the absence of proper and adequate standards and behavioural codes, but through their non-observance. This suggests that risks to health and safety are not anticipated or recognised when they take place. The reader who questions this has but to review past volumes of this Association's journal containing numerous accounts of dangerous conditions together with conclusive reports of findings.
The removal of a used petrol pump from the service station starts a series of processes under a wide range of conditions able to margins of safety. Generally the processes cover repair, modernisation, storage or refurbIshment (even just destruction) in practically every possible combination.
at the service station specific legislation is for complIance, the handling of used pumps that contain petroleum spirit is subject undoubtedly to law(s} but these are
usually implicit rather than explicit. Certainly considerations regarding safety are prone to local interpretation. For example, police halting a vehicle carrying old petrol pumps that are leaking, would certainly fmd a place for the alleged offence within a welter of motoring law. (Markedly less effort would be needed if the vehicle had no fuel fill pipe cap). Without explicit guidance or legislation it follows that whatever are the standards (or lack of) towards safety, these reflect the policy and practical outlook of the contractor.
Numerous contracting organisations carry out off-site work for the petrol retailers and their suppliers, ranging from the self employed individual to the international manufacturing and service company. Thus there must be a wide band of opinion and practice towards the place and nature of health and safety. ranging from safety illiteracy to defmitive policies and tightly bound systems and policing mechanisms. But care is taken to stress that this does not imply that the smaller the operating concern, the lower the safety standard or record. Irrespective of company size and worth, every service engineer is his O\m safety master for most of the time, therefore the industry is served in this sense, by hundreds of individuals and not by several major contractors. Yet it is a valid and relevant fact that contracting companies of stature and having a union represented workforce are more likely to have an active and serious address to safety as an identifiable component of work responsibility.
The article that follows shows approaches to health and safety commensurate with the size and of 0u: its environmental location and the industnal actiVIties that take place within it. All is consistent with the objectives of the corporate safety policy. No suggestion is contained here that our policies and procedures should stand as a model beyond the fact that many have introduced themselves as consequences of past error or mishap. For a s.afety strategy to work effectively, use must be made of expenence where controls may be introduced to counter repeated nS.k and others relaxed as circumstances allow. Therefore safety 1S a dynamic element at work, manifesting itself daily in almost unimaginable guises: observing the of an electrical distribution board, weighing the 10catlOn for a new test tank in relation to logistic needs on the one hand and fIre escape routes on the other.
The off-site work on used pumps is a continuous process throughout much of Britain. The scale of this can be gauged by linking together some reasonably accepted statistics and business line trends.
March 1984 summary totals of the number of retail service stations ("Petroleum Review" The Institute of suggest there were during 1983 some 23,000 operatmg s1tes. Excluded are the commercial distribution centres operated outside the retail sector. At broadly 5 per cent a year, the population of supplied service stations contracts. Using a mean number of pumps for the typical site, we can estimate therefore the total population of pumps, excluding the commercial centres. The noticeable growth in the number of newly installed autodiesel pumps is unlikely to disturb or arrest the temporarily continuing decline in pump population.
The most recent information relevant to the annual rate of production of new equipment for the U.K. market, expressed in relation to sites population, suggests that between 10 and 11 per cent is replaced annually, therefore some 10,000 13,000 used pumps are displaced. Many of these are refurbished and are "cascaded" down the retail chain, themselves displacing much older equipment. And so on.
The number of pumps handled "off site" is swollen further by those taken away for the repair of damage caused by vehicles. Transhipments are not just common place: a high proportion of used pumps are transhipped after temporary storage. Therefore, there is a substantial traffIcking going on involving different forms of transport to and from an assortment of premises for a variety of reasons. Britain's pumps are on the move
The Company's statement opens:
"It is the Company's policy that so far as is reasonably practicable all possible steps will be taken to ensure the health, safety and welfare at work of all employees ......"
There follows
Roles of employees, generally and where appropriate, specifically, for the hierarchy and otherwise.
Df'finitions of duties for named titleholders and committees, their composition, objectives etc.
Chains of responsibilit y.
All IS ((Jllvf'V('d in plain words and in slIch terms so that:-
Every employee may feel that safety at work is a durable and tangible element of work.
Unsafe practices cannot develop and remain in being.
Safety cannot be usurped by profIt motives or overly cost consciousness.
Without the written safety policy backed by a commitment to uphold it, no basis would exist for an effective and harmonious discipline. One man's hazard would be another's safe practice. Financial interests would intercede and conceivably triumph. Expertise would not emerge, and who should be trained? Important people or the less important? Everyone? Is the hierarchical chain of command capable of the analysis of a safety problem, the contemplation of possible solutions then the implementation of the selected remedy?
EVidently parliament and the draughtsmen of the 1974 Act thought otherwise and for once implanted into industrial philosophy the proposition that "safety is everyone's business". The working committees that were founded within the Company area as the legislators so designed, composed so that no single contra interest Can bear with oppressive force on this subject. And so it is that the standards and disciplines we have are to substantial measure directly traceable to the agreed views of individuals representatives of management and the managed.
There are three separate areas within the Basildon plant perimeter. Pumps containing petroleum products are not put elsewhere.
1. A temporary storage compound
2. A dismantling and cleaning area
3. Repair workshop.
Each area and part thereof is classifIed according to a safety system modelled upon the electrical safety zones defIned m BS 5345 pt 2. Safe areas are unclassifIed. The zone classes are:
Zone 0
A wne in which an explOSive vapour/air mixture is continually present or present for long periods.
Zone 1
Awne in which an explOSive vapour/air mixture is likely to occur in normal operation.
Zone 2
A in which an mixture is not likely to occur 10 operahons, and if it occurs it will exist onl for a short hme. Y
Where a location can fall within two classifications the senior applies. '
One usefulness of this system of claSSification is that repair fitters normally working in the plant, do not face dissimilar standards when occaSionally working on the service station forecourt.
Therefore, a used pump containing petrol is itself Zone (0) during the time there is an outflow whilst being dismantled.
As shown by figure (I) this is a covered fenced compound, isolated fi'om any working area. NOlmally locked.
Zone
Smoking Signs
Fire Extinguishers
:2
: Prohibited
: "NO SMOKING"
: None
Access for Fire Applicances : Always available
Having an effective working area 110 square metres, this has a covered shelter as shown in figure (2). The concrete has a pr?nounced gradient to afford rapid drainage. . ng capaCIty is 4 pumps at one time. An adjacent bwlding has vapour detecting apparatus and fire alarms (automatic and manual). Hypothetical maximum outflow of liquid 4 is about 50 litres Ordinarily, most of the pumps holdmg capacity is released before that unit is stripped, outflow usually not exceeding 4 litres per pump.
Pumps ?eing are allowed to drain having been WIth a high pressure hot water/detergent mixture. As dramage occurs the surface area is hosed continually until traces of petrol eum product are removed. (Once it was the to dram petroleum spirit from the pump hose and systems mto containers, accumulating the product untIl enough was available to make disposal worthwhile. This was stopped because of the difficulty of controlling the number, type and whereabouts of a miscellany of containers of petrol).
Cleaning is done in an area 8.8 sq. metres part of which is beneath a high ca '. ,_call Surf dr' nopy g1Vmg shelter from direct rallue ace amage is afforded by a drain along one flank of the area then running b h h b d eneat the centre of the canopy area. At t e oun arv of the w ki I dr" d d or ng area t le am IS covere an dIscharges mto at' I np e stage petrol interceptor of conventIOnal design and c t .
Zones
pump drain interceptor working area Smoking
: "PETROLEUM SPIRIT" "NO SMOKING"
"DANGER"
"NO ENTRY"
: 3 x 4.5 kg dry powder. Cleaner (see below)
: hand or pneumatically operated only.
: vehicles ordinarily prohibited
The high pressure hot water cleaner is capable of use as a fire extinguisher. A diesel powered engine pumps water at 70 bar, delivered through a 9m hose and hand held lance. The cleaner is normally 7 m from the working area. Effectiveness of the cleaner in a fire extinguishing role is good provided the jet does not disperse burning liquid and material. Most effective when directed to the seat of a small fire.
Major hydraulic units are not inlmediately stripped, but temporarily stored and petroleum liquid/vapour dispersed to atmosphere. Unwanted hydraulics are partially dismantled to accelerate drainage. (Such units, potentially valued as scrap metal only are shipped to a local scrap merchants premises, the consigement being covered by a release certificate absolving the Company from all consequential liability in respect of any damage or injm-y arising from the merchants' handling of products containing petroleum fuel. Once signed the certificate is retained by a Company representative who hands over the consignment. He is obliged to then witness the spectacle of seeing his company's products (or that of others) being hurled into a furnace. Such is the spiritual gratification that can be aroused by this sight that "trips to the scrap-man" need not be ordered, rather bestowed as a mark of favour.
There is a commercial rather than safety component in this arrangement, for audit requirements stipulate that pumps belonging to others and authorised for disposal as scrap, must be seen to be beyond any further use as a petrol pump. The process followed is _ __ r'-"--
011S ruchon.
: 0 for radius 4.25 m
: 1 (upstream)
o (cleaning site)
: 0 : 1
: Prohibited
'Figure
There are two classification areas, the two test ligs (Zon e 2) and general fitting area (unclassified). Each volumetlic abov e ground test tank contains odourless keros e ne Th e admi x tur e of small volwll es of autodiesel and petrol and ge n eral sediment causes th e drainage and repl enishm e nt or the t es t product several tim es a ye ar.
Petrol is not used for the testing of pumps within the buildings, but if specially required can be carried out at the research and development station.
Fire Extinguishers
Rig 1 2 Rig 2 2
Prohibited
Ix9llitre Ix9kg dry powder mobile foam 2x9 litre water (Fire Station 8 is adjacent to both test rigs and is equipped with mains supplied water hose reel)
Despite all reasonable precautions taken to guard petroleum spirit entering the workshop, from time to time this does happen when a pump has not completely drained, even when the major hydraulic units have been removed. But never is the volume more than a part of a litre. Should this occur, the pump concerned becomes a Zone 0 unit as previously The fumes released spread rapidly and widely and 'it IS expedient to test the atmosphere for L.E.L. using an "Explosi-meter" to ensure that reaction to the smell IS not overly ambitious in the nearby factory and office areas. Two "Explosi-meter" are retained on the premises, one in the custody of the manager responsible for health and safety within the plant perimeter, the other held by the writer.
Access Workshop Zone
Smoking Signs
Fire Extinguishers
Main gangway, two fire escape doors.
: U nclassmed
: Permitted
: None
1 x 5 kg CO2
Figure (3) shows one test rig is use Mains electrical supply is controlled through a 20A switch, a 25A rated circuit breaker and industrial type plug and socket equipped with emergency ON/OFF buttons
Under this heading I review conveyance of used pumps on the public road (external) and within the perimeter of the premises (internal).
Where transportation on the public road is a responsibility of the Company, two forms of vehicle are permitted. The lorry with closed driving cab and hydraulically operated taIl lift, or vehicle drawn open trailer.
With both forms of transport the pump is carried upright. There are no circumstances permitted for the carriage of the pump in a horizontal fashion, for even when the pump inlet connections are blanked off drainage of fuel from the vent outlet can take place.
A battery powered fork lift truck is used for moving pumps from deli:ery vehicles to storage and from storage to process areas. It IS recogrused at the outset that this vehicle is not constructed to other than conventional industrial standards and feasibly, spirit fumes entering the electrical switch boxes could Igrute when Switching action takes I hi k . . db' pace. T 's ns IS appraIse as emg extremely Unlikely dUring normal and proper operatIOn of the machine and great k' erns IS attendant to when a load IS being transported. The risk of careless driVIng causIng damage and personal" d b I · Il1Jury IS considere to e more re evant, Irrespective of load . hil h d . call1ed. Therefore tfhe fP d YTtotwhiar s dsafety IS directed towards the value 0 sa e nVIng. 0 s en , each driver' t S IS ested and subject to exammatJon. uccessful candidates dri · I' d nI I' receive a written vmg Icence an 0 y Icence holder k I 'f k T s are permitted to drive a for I t truc. wo employees ki . I R . W k h Wor ng m the Mechartica epalr or s op are so authorised.
But unnecessary use of the fork lift mac L d IUne IS not allowe and e very effort made to mll11mlse movements
Whil st fire may appear to be the dominant po tential dang er, space IS now gwen to th e Importance of indi vidual's health, in indu stJial occ up a ti o ns hith ert o umesearched. Th e possibilit y th a t empl o yees co uld suffer from th e effec ts of inhcl led spirit va po ur was exam in ed in a qu as i sc ie ntifi c a ppro ac h in th e fi e ld a nd throu g h medi cal res ea rch pe rfo rm ed by a hygi eni St.
Men empl oyed in th e di sma ntlin g clI1d repair of use d p umps a re ex posed to inh a la ti o n of pe tro le um spirit vapour, bu t f( JI' limited pe ri()d s ()nl y. Th e di sm a ntlin g area is a ir y and go()d fac iliti es ex ist f( JI' th e flushin g aw a y () f li q uid pe trol e um fro m till' surfacc o f the a rea.
Exposure can be at a higher level and for longer periods for pump service engineers, for, irrespective of pump faults investigated, the drawing off of test volumes by open measure is an aspect of practically every service visi t. Some res each has been done to assess whether or not such exposure carried with it an avoidable risk to health.
Persistent inhalation occurs not when the service engineer is working at the site, but whilst driving the service vehicle. A totally unventilated panel van containing incompletely drained test vessels, saturated industrial clothing and exchange scheme major hydraulic units can produce a virulent and overpowering atmosphere within the vehicle.
Tests were carried using a volunteer group of employees in which concentration levels were measured under different conditions vehicle type volume and disposition of liquid petroleum states of vehicle ventilation. Samples of body waste matter, gleefully donated by the participants were laboratory examined.
Findings produced at the conclusion of the experiments suggested a discernable risk to health could exist under operating conditions that could be encountered in everyday work. Concisely, standards were then introduced and protective materials procured to reduce as fas as practicable the vapour in a service vehicle.
Extra care is warranted when pumps are fire damaged and returned to the works for restoration, not as regards the health and safety of the workers involved but in connection with the extent of the repair. Fire damage can be unseen. In view of this the first line of defence in ensuring that a pump is inadequately repaired is the policy that all such equipment returned to works is beyond repair. A managerial decision is taken a pump is accepted for repair. Correspondingly the deCISion to proceed is qualified by his identification of the parts to be replaced.
Guidance in this stems from assessing the location of the seat of the fire, its duration and scale. A fire developing within the lower, hydraulic portion of a pump is more than likely to damage repair all in that area. An external fire may be less as the cladding of the pump may form an effective shield. The discolouration and deformity of are useful clues about heat intensity. The general view IS a fire damaged pump in which the fire started and was within its casing, irrespective of brevity of the IS beyond repair. In such an instance, no parts Within the casing would be regarded as unscathed and fit for reuse.
The repairer who processes a used pump prior to field installation, acting commercially as a contracting party to a retailer or petroleum supplier, places himself as a specialist in this calibre of work. Perhaps the contract explicity stipulates sigrrificant standards of repair or refurbishment for attainment. Most likely the contract is a simply and shortly worded order. In any event the future licensee has an expectation that the equipment, irrespective of age and type will be constructed to the standards required for the granting of a storage license. Licensing provisions do not have devalued terms to compensate for older equipment, and therefore it follows that the recycled pump should exhibit the standards required of contemporary equipment.
During the years we have participated in pump recycling and repair, repeated examples have arisen where a sharp conflict emerges between the necessity to preserve and maintain such standards in a market place where many buyers place exclusive interest in price.
Many a small volume dealer is interested in cheap, second hand pumps of the early generation of self computing pumps to replace expiring mechanically driven pumps of the late sixties and early seventies.
Our response to the economic and safety contrasts is spelled by facing the question:
"would this repaired/recycled pump pass test if submitted to B.A.S.E.E.F.A. examination?"
The obvious answer ensures our safety policy remains self fulfilling.
An example of practical expression towards safety is the rejection of electrical enclosures which were once generally approved, ego junction box constructed to BS 229, another, IS the replacement of currently approved enclosures having British electrical threads in favour of metnc threads. (A drawback here is the risk that the site may use a standard ETIMetric adaption when connectmg field m.I.C. cable fittings with metric forms).
The electronic repair workshop, in our of BA SEE F A standards mean, meets every reqUIrement. ot . it . . .h' "cal shop in so far as intricate work is concerned. P so t e amecycled or repaired may thus be partly handled umps emg r in both shops.
Staff training in safety, for example, the exercise of fire d part of the general address to health and safety proce ure, IS a d k at work, but not detailed here. Better minds an wor's are available for information.
The B.A.S.E.E.F.A. Certificate is neither lightly or cheaply earned. Acceptanc 't" . t d e cn ena covenng pump component pm' s an assemblies of . t· h' h 'fi' par s are stnngent, outmatc mg t e speC! IcalIons and t d d . d . s an ar s employed in the deSign an constructIOn of apF) ardt· us used 111 non-hazardous apphcatons. It may not be gener' 11 I' . I I d Y rea Ised in our industry t 1at t le mterest o( RA S F F F A I I (" 1 d f •. •. stops not wit 1 t 11' 1111S 1(' manu actu1"l'd l>llllll) St· 1 I' . '. .. <lll( arc s (or nlll1pilance cover manu(adunng l)rtl("('SS('S t 1 1 ,. d I " , 00 s, 1I1111an quallflcatlolls an t ll' IJrenllses wlth111 whicll . d 1 plO lids are put together under t H' Certificate's warrant.
This article portrays one contractor's demonstration bl ' tions beneath Company and statute law. Others wlth111 o Iga ., h . d' ). th 1dustry may incline to the Opl1110n t at 111 omg so, ell" . h . zealousness is no sounder than "common sense 111 w at IS generally a safe activity. a view J"l'mains unchallengeable. Until the first mishap.
The first of two articles by R.J. Wigfull BSc., MSc., C.Eng, MInstE, director of John Wigfull & Co Ltd., Member of the Association.
These articles are intended to give an introduction to static LPG (Liquified Petroleum Gas) installations The fIrst part is an introduction to LPG and the storage vessel. Following sections will cover the installation, maintenance and testing of the installation. There will be some changes in requirements for installation and maintenance in the near future when the proposed Flammable Gases Regulations and the Pressurised System Regulations come into force. There will also be revised LPGITA Codes of Practice covering Installation and Maintenance, which should be published in early 1985. Much has been made of the draft copies of the revised Codes of Practice to prepare this article, but the opinions expressed are not necessaril y that of the LPGITA.
SpecifIcations for the majority of activities involving storage and use ofLPG are covered b y the LPGITA Codes of Practice.
These are prepared by members of the industry who work closely with the Home Office, Health and Safety Executive, Fire Service College and other Authorities.
The Codes are voluntary but members of the Association are committed to follOwing them as one of the conditions of m embership.
In addition to the Codes, installations having a total capacity of 25 tonnes have to be approved by the Health and Safety Executive and installations on sites covered by the Petroleum R egulations by the Petroleum Officer.
LPG usually refers to commercial butane and propane whose properties comply with BS 4250. For most installations LPG is stored as a liquid under pressure. At 15°C the approxatmte saturated pressures are 2 bar (30 psig) for butane and 8 bar (116 psig) for propane.
Liquid LPG is colourless, odourless, has about half the mass of equivalent volume of water and, importantly for the mamtenance of the vessels, is non corrosive.
When LPG liquid is vapourised, or evaporates, a single volume of liquid produces about 230 volumes of butane or 2?0 volumes of propane vapour. This vapour is heavier than atr and may travel along the ground to lower levels or into drains. In still air the vapour is slow to disp erse. This can lead to ignition from a distant source travelling back to any leak.
To assist detecting any leaks LPG is usually given a smell before distribution by the addition of an odourant such as ethyl mecaptan. This enables the gas to be detected by smell at of about 1/5th of the lower explosion limit. mdustries, noteably those using LPG for aerosol fillmg,. use LPG without the addition of an odourant. Special attentIon must be paid to this type of installation and further details can be found in the Codes of Practice.
LPG can also contain impurities usually from the final production process. These can include lubricating oil, water and caustic soda. Whilst it is not usual to fmd these in significant quantities their possible presence must be considered at the design stage and during maintenance.
Vessels can be installed above ground, underground or mounded. Mounded vessels are those that are at ground level or partly underground which are covered with a layer of soil, or similar material. Unless otherwise indicated this article refers only to above ground vessels. not be installed in a bunded area, in pits or under bUildings. They should not be installed adjacent to liquid oxygen tanks or tanks containing flammable liquids.
The Codes specify minimum separation distances between vessels, LPG equipment, other equipment, buildings and boundaries. Separation distances are intended to protect the LPG facilities from the radiation effects of fires outside the LPG installation area as well as to minimise the risk of an escaping LPG being. before being disperseJ separatlon dIstances are listed at the end of this article, but these can be reduced in certain circumstances by the use of radiation walls or fixed water drenching systems.
LPG should be stored in pressure vessels made to a recognised design code. The current British Code is BS5500. There are vessels in service designed to a variety of Codes, e.g. BS1500, BSI515 and ASME VIII. The minimum design parameters used with the current Code are listed below:
Maximum 14.5 bar (210 psig) 38"C (IOO"F)
Minimum Zero bar (0 psig) -40"C (-40"F)
Butane:
Maximum 4.8 bar (70 psig) 38"C (100°F)
Minimum 0.48 bar abs (-7.6 psig) -IS"C (_18°F)
All vessels are hydraulically tested after manufacture and should be leak tested before entering service.
Some earlier butane vessels were not vacuum rated and the installation should be modified to protect the vessel under the coldest service condition.
Vessels with diameter greater than 1500mm are fitted with a man way to assist during construction and to allow for internal inspection. The number of COlmections fitted to a vessel depends on the size and proposed service. All vessels should have connections to allow at least the following fittings to be installed:
Pressure relief valve coupled into the vapour space.
Drain, or other means of removing the liquid.
Ullage (Fixed maximum level) gauge.
Preferably a contents guage.
Pressure gauge.
Fill coupling.
Outlet valves vapour, liquid or both.
All the connections larger tharI l.4mm diameter with the exception of those for relief valves must be fitted with either excess, flow or back check valves.
Excess flow valves are fitted into, or onto, the connections and are designed to close automatically in the event of a pipe These ar:e valves which are held in the open postion by an mternal spnng. If the flow exceeds the flow rating of the valve, the valve closes and remains closed until the pressure on the downstream side equalises with that upstream. Back check valves are non return valves.
Vessels over I Tonne should be earthed against the static build up and there should be the facility to earth the tanker before and during unloading.
The dissipate static the standard of earthing does not need to be as high as that required for electrical installations.
The resistance to earth should not exceed 1 x 106 ohms. Supports.
The design of the vessel supports shall take into account the vessel shell stress and the transmission of the maximum loadings to the ground. They should preferably be designed to take the mass of the vessel when fIlled with water.
The exterior of the vessels should be suitably prepared and protected from corrosion. One method is by grit blasting followed by metal spraying and painting. The vessels should be finished in a light gloss colour to increase reflection and minimise temperature rise of the contents.
When installed, the vessel should have signs fixed saying "Highly Flammable" Butane (or Propane).
The area under smaller vessels need note be concreted but can be compacted. The area under, and around the vessels, must be kept free from weeds and flammable material.
If unauthorised access is prevented to the valves arId fittings, e.g. by the fitting of a lockable cover, then further protection may not be needed. In all other cases, and when pumps, etc., are installed, the storage vessel(s) should be surrounded by an industrial type fence, at least 1.8mm (6') high which has :2 means of exit and which is not closer than 1.5m (5') from any of the vessels. The fence should be fitted with signs complying with the Safety Signs Regulations, 1980.
To try and make the description of the fittings easier, they have been put in an alphabetic order with a brief definition.
This is a connection that is made to the vapour space of the vessel. This is then connected to the delivery tanker by hose. It allows the vessel and tanker pressures to he equalised and speed up delivery. It is used on most butane and the larger propane installations.
There are several types, but :2 systems predominate. The first is the magl1etic type. A float in the vessel moves a magnet, this rotates on one side of a stainless steel t1ange set in the vessel.
• Training for forecourt staff at your own location.
• Properties & Hazards of LPG Training at your own location.
• Management Training in the New Regulations etc.
• Driver Training to meet the Requirements of Regulation 21.
• Practical Fire Training for oil & LPG at Norwich, Blackpool etc.
•
On the other side of the flange a second magnet is fastened to a pointer and rotates follOwing the internal magnet, indicating the level in the vessel on an external scale.
The second type are bleed gauges which use the fact that when a stream ofliquid LPG is released into the atmosphere it normally expands and forms a visable liquid fog.
When vapour is released it is normally colourless. A moveable tube, having a narrow bore and an exterior valve is fitted into the vessel via a suitable gland. The tube is moved with the valve open until the colourless vapour changes to a visible fog, this shows the end of the tube is at the liquid level, and the level is read off an external scale. The 2 types of bleed gauges are rotogauges which are rotated and the level read off a dial and slip gauges where the gauges are moved in a straight line and the level is measured directly. Other methods of gauging that are used include:
Differential pressure gauges
Sight gauges --:...direct reading and magnetic Load cells
The scales used on contents gauges can vary. Therefore when reading a gauge the scale should be checked to see if it is %total (water) capacity, %rated LPG capacity, or actual contents in litres, tonnes etc.
These are used in drain points of smaller vessel h h SWente dram IS only expected to be used infrequentl It. combination excess flow/isolating valve which.Y· tItS d a IS ac ua e by screwmg m an msert complete with valve into the Checklok outlet. Mter the liquid has been removed the insert is removed which allows the internal valve to close. The Checklok must not be used as a permanent outlet connection.
All vessels should be fitted with a method of removing the liquid contents in the event of the vessel having to be emptied before removal from site or for maintenance. The connection is usually in the bottom of the vessel but can be in the top if an internal pipe is fitted. The drain points can also be used to remove any contaminates that may accumulate, espeCially in vessels used on vapour service only.
LPG is delivered by road tanker and transferred to the vessel using a vehicle mounted transfer pump. antistatic hose on the tanker is connected to a fill couplmg, either on the vessel or on an extended fill line. The hose/fill coupling thread sizes are gradually becoming standardised. The most common thread for butane is 31/'1" ACME and for porpane 1%" ACME. The fIll coupling should be protected from the vessel pressure by an isolating valve and a check valve. The latter is to prevent loss of vessel contents m the event of a hose burst. The internal fill pipework usually ends in the vapour space of the vessel. This causes the liquid to expand when entering, giving a cooling effect and helps to reduce the rate of pressure rise.
This is usually taken to refer to a relief valve manifold with 4 valve connections and is also known as a Polyvalve There is also a 2 valve manifold known as a Duoport. The manifold contains a internal valve and exterior bleed valves for each relief valve connection. The internal valve can be moved to isolate each valve connection to enable the relief valve to be remov ed Multiports are usually fitted to the larger vessels to enable the relief valves to be exchanged without having to depressurise the vessel.
This is a combination valve often fitted to the top of smaller vessels The valve is used to reduce the number of connections on the vessel. There are several different types and they can be used to carry out one, or all, of the services listed below:
Fill
R elief valve
Offtake vapour
Offtake liquid
Pressure gauge
Contents gauge
Ullage
This connection is usually in the bottom of the vessel. An isolating valve should be installed directly downstream of the excess flow valve. The isolating valve is usually threaded on smaller vessels and flanged on larger ones.
This connection is usually on the top of smaller vessels and can be either on the top or bottom, with an internal pipe, of larger vessels An isolating valve should be fitted directly to, or combined with, the excess flow valve
This is fitted to the vapour space of the vessel to indicate the internal pressure. The usual range for a butane gauge is -1 bar (-14.5 psig) to 7 bar (approx 100 psig) or 10 bar (approx 150 psig) and for propane 0 bar (0 psig) to 15 bar (approx 215 psig) or20 bar (approx 290 pSig) . The dial sizes vary but should be selected to enable the gauges to be read at ground level. Weatherproof gauges should be considered.
These are connected directly to the vapour space of all storage vessels to protect against excess pressure conditions. The relief valve capacity must be sufficient to limit the pressure rise to within the design code requirements during a bnormal conditions. This is usually assumed to mean that the vessel is subjected to external heat, the worst condition being a liquid pool fire The heat that would be absorbed under these conditions is a function of area of the vessel, ie. the larger the vessel the larger the number and/or size ofthe relief valves. There are several formulae for calculating the size of the valve and calculations are included in the LPGITA Codes.
The valves used are direct spring loaded, tamper proof, type. Valves on v essels 2 tonnes should be fitted with vent pipes to carry an y discharge a way from the top of the vessel. The tops of the valv es, or of the vent pipes when fitted, should be closed with loose protective caps.
These are fitted on the larger vessels to give an indication of the liquid temperature. They should be fitted into blind pockets which are welded into the vessel.
Any vessel must not be filled to a level so that it becomes hydraulically full at the maximum temperature. If the vessel becomes hydraulically full any additional temperature rise causes a significant pressure rise. This would lift the relief valves and discharge liquid LPG. To ensure that this does not happen a tube is inserted to the depth of the maximum fill level allowed for normal filling. The tube has a valve on the outside and works in the same way as a bleed type contents gauge. The external valve is opened frequently during filling and if liquid is seen to jet from the valve, filling is stopped immediately, irrespective of the level shown on the contents gauge. The ullage gauge valve should be easily visible from the filling point and for external fills this often means installing an extended ullage point.
The maximum fill level can either be defined by the %of the total volume of the vessel or by the filling ratio.
The % of the total vessel that can be filled depends on the size of the vessel and the product. For butane it is about 90% and for propane about 86%.
The filling ratio is "the ratio of the mass of gas introduced into a container to the mass of water at 15"C that fills the container as fitted out for use". Figures for filling ratios at various reference temperatures can be found in BS 5355.
Any valves that are fitted should be suitable for use with LPG and for the maximum pressure that could be reached in service. It is now becoming more usual to use firesafe ball valves conforming with BS5351. This type of valves are designed to provide a shut off even when the valve has been exposed to fire.
Details of installation standards, maintenance and testing will follow in a future edition of the Bulletin.
We acknowledge the assistance received from the LPGITA and their permission to include details of their separation distance tables.
STORAGE MINIMUM SEPARATION DISTANCE (METRES)
Maximum Water Nominal Maximum Total From Site Boundary, Buildings, Between Vessel Capacity L.P.G. Water Capacity Fixed Source of Ignition, etc. Single Vessel Capacity of all Vessels in a Group in a Group Above Below Ground or Mounded Above Below (litres) (tonnes) (litres)
Ground Buried Valve Assembly Ground Ground Portion Filling Point, and etc. Above Mounded Ground
500 to 2500 0.2 to 1.0 7,500 3 3 3 1 1.5 2500 to 10,000 1 to 4 30,000 7.5 3 7.5 1 1.5 10,000 to 150,000 4 to 60 450,000 15 3 7.5 1.5 1.5
Table 2
1 2 3 4 5 L'p.G. STORAGE L.P.G. L.P.G. VEHICLE STORAGE VESSEL PUMP DISPENSER L.P.G., VESSEL FILLING FILLING CONNECTION CONNECTION
I. L.P.G. Storage Vessel Nil Nil but 3m 3m not under
2. Storage Vessel Filling Connection Nil Nil 3m 3m 3. L.P.G. Pump Nil but Nil Nil Nil not under 4. L.P.G. Dispenser 3m 3m Nil Nil 5. Vehicle L.P.G. Filing Connection 3m 3m Nil Nil 6. Underground petrol As 3m 3m 3m 3m tank, manhole or filling point separation distances between tanks in Table I 7. Above ground Flammable 6m lim lim (im 6m Liquid Stage Tank S. Ditto to bund 3m 3m 3m 9. Petrol Tank Vents (in plan) 3m 3m 3m 10. Petrol Pumps/Dispenser 3m Nil Nil Nil 3m 11. Diesel Fuel pump, flameproof 3m Nil Nil Nil 3m 12. Ditto non flameproof As Table 1 Fixed Source Ignition I:l Parked Cars I.Sm 3m I.Sm l.Sm I.!im 14. Site Boundary, As Table 4.Sm 4.2Sm 4.2.'im bUildings, fixed sources of ignition I I.'). L.P.G. Cylinder Storage Srn 1 Srn Hm Hm Hm
FIRST HANGING . BLABY ROAD ENDERBY . LEICESTER . LEg 5AQ
INSTALLATION AND TESTING OF PETROL AND FUEL TANKS.
INSTALLATION, MAINTENANCE AND ROUTINE INSPECTION
LPG EQUIPMENT PURGING, 5 AND 10 YEAR TESTING OF LPG VESSELS.
MEMBER A.P.E.A. L.P.G.I.T.A.
In anticipation of a change in legislation, a prototype Driver Contro lled Unatte nded Delivery Control Box has been developed. Operators can simply add it to their existing tank gauges, or it can be installed as a complete system. The manufacturers have attempted to encompass all the aspects of the draft code of practice.
The manufacturers would like to hear from all interested parties, and are wi lling to arrange demonstrations, by appointment, at their premsies
Further details from: Normond Instruments Ltd., 205, Kew Foot Road, Richmond, Suney TW9 2SW
A synthetic absorbent capab le of dealing with almost every kind of spillage from hazardous chemicals to printing inks and lubricants has bee n introduced. It will even it is claimed, de a l with o il spillages on water by penetrating the oil layer down to the water leve l, a ll OWing it to be scooped up safely.
C a ll ed "Rench Rapid", the absorbent has a very low bulk densit y, so that the weight of a SO litre bag is only 4 kg, but a ve ry hi g h absorp tIon rate, whi ch ca n be as much as J 00%of it s uwn v () l ume o r between S and I S times it s own weight.
Further detai ls from: GOlee T rading Ltd , Gotee HOLlse, lkdll)rd R ()ad , I ,()Jld()n qDE
T7ze use of "Rendl Rapid" on a spillage of dangerous chemical
Roncol's Commercial Pump with new or refurbished hydraulics, new frame plastic coated panels, hose and automatic nozzle.
Suitable for Diesel or Petrol.
Standard or High Speed pump units. Capable of accepting fuel monitoring systems.
Measurement and precise recording of individual and cumulative dispensing of fuels.
Basic Price (inclusive of 12 months warranty on parts and labour)
Optional Extras
High capacity (fitted with 1" delivery hose and nozzle)
Petrol (fitted with limiter)
Lighting Single side