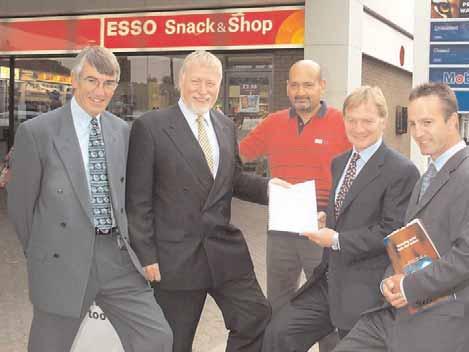
26 minute read
APEA2006
Once an initial review of the document has taken place it is important to run the document past legal representatives from both parties to ensure any ambiguity is resolved prior to signing.
Regularity of meetings should then be agreed along with the normal administration duties including, minute taking, suitable communication channels and venue.
Advertisement
Special attention must be paid to the resources required to make an agreement work. At times partnerships can involve quite a lot of work and energy on both sides so again it is important that decision makers understand the complexities and support these relationships fully.
If the agreement is going to succeed it is vitally important to appoint a suitable representative who possess the skill set necessary to build a fruitful relationship. The most crucial part of the partnership is the relationship between both party’s representatives.
It is very easy to list the skills necessary for a successful relationship but how on earth do you measure if someone is open minded? (Unless you send them to a 3-day Assessment Centre!)
I feel the skill set necessary comprises of many facets. However, as a prerequisite it is imperative that the representatives are knowledgeable about the industry/PLA’s roles and have experience within this field. I say this because the reduction in Local Authority budgets has meant many more multitasked /skilled officers who may not have sufficient knowledge to allow them to be confident within such a relationship as LAPS?
Being able to listen to each others views and being open minded are also important attributes along with reliability and being able to deliver on your action points/promises.
Once confidence in each other’s performance is established trust can begin, and with it a more fruitful relationship.
It should go with out saying that partners should know their boundaries but this does not mean that a relationship has to be sterile or frigid. In my 25 years experience of dealing with people from all walks of life I have found it a rewarding experience in both personal and business terms to get to know people a little more than their first impression might give you.
In any relationship there are potential weaknesses and conflicts and LAPS partnerships are no different.
I have tried to make our relationship with ESSO a little more democratic as I feel this is a potential weakness of LAPS. One authority could decide on a national issue with their partner without consultation to other PLA’s who may not share the same views.
The almost inevitable accusations of ‘getting too close’to your LAPS partner Can be avoided by being professional and keeping good records especially around the rational for decision making.
Succession planning is another potential issue for LAPS partnerships, especially as organisations ‘down size’ and employees seek other opportunities. LAPS relationships are normally formed by partners with long standing experience that academic qualifications cannot replicate.
Lack of resources can also negatively affect a partnership, especially if one partner is far better resourced than the other. Fragmentation can occur and the whole benefit of a partnership can be called into question.
In summary I feel LAPS play a useful role within the industry, from knowledge sharing, consistency and continuity of enforcement to efficiency savings.
As someone who is passionate about relationships I believe that while the constructs of Lead Authority Partnership are important they are not as vital as the actual relationship formed between the two representatives.
By Martin Rackley, Global Alliance
Introduction
The Global Alliance was formed from a partnership between BPand Bovis Lend Lease in 1997. We construct and maintain the BPRetail Filling Station network in the UK, USAand 11 countries throughout mainland Europe.
From the beginning we have maintained a firm belief that proactive Health & Safety Management is not just good for business, it’s a moral obligation. Together with our supply chain partners we have developed systems and procedures that over the years have delivered real improvements including a reduction in accidents. But although the frequency reduced, accidents continued to happen. We came to realise that management systems were only part of the answer to reducing accidents and improving site safety. Several years ago we embarked on our Incident & Injury Free workshops which focus on behaviours and attitudes towards safety and how to improve them. The key component is the responsibility of every individual that works on our projects. The most important message is “It’s ok to say No!”
Training of both our staff and contractors is under constant review. In addition to ensuring ALLour contractors have current UK PIASafety Passports we have also formed a partnership with our training provider SMTS whereby Alliance Contactors can access EU and Central Government funds for NVQ and CSCS training. We have worked closely with APEAto provide bespoke courses for our Project Managers and continue to provide specific training each year for staff and contractors including Confined Spaces and Safety Netting Inspection.
Great efforts have been made to improve our communications. Our quarterly HSSE Newsletters have been well received and provide a useful tool for contractor feedback and lessons learnt from accidents and near misses. We also highlight good practise and individuals who have made a real difference. Our annual contractor HSSE awards are well established and guest speakers have included APEA Chairman Brian Baker. We have recently issued our 3rd edition HSSE DVD to outline the particular hazards that continue to kill and injure in the construction industry and how they relate to operational service stations and are currently working on a 4th edition.
HSSE Systems, Procedures and Initiatives
All GA Contractor Companies must successfully pass our HSSE accreditation which has just been revamped to include behavioural safety programmes, reward / recognition and communication of lessons learnt.
We have developed a Health & Safety Plan template for our Principal Contractors to ensure there is a consistent approach across all our projects and to make auditing more straightforward. Contents include permits, emergency contacts and registers.
All our construction projects have Global Alliance pre-start and works execution risk assessments completed by our Project Manager and HSSE Manager which are issued to the Planning Supervisor and Principal Contractor prior to works. In addition to being incorporated in the Stage One and Construction Phase Health and Safety Plans, they provide the opportunity for us to specific particular procedures or equipment.
PPE is strictly enforced on all our projects. In addition to hard hats, safety
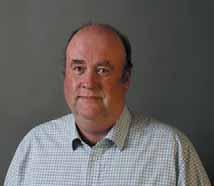
Martin Rackley footwear and high vis vest we insist on safety glass’s and gloves for ALL contractors. The type of glove will vary depending on the task and high-risk tasks including breaking concrete and drilling still require high impact protection goggles.
The Global Alliance adopts the Bovis Lend Lease Falls Mandate across all our projects, which was developed in response to the new UK Working at Height regulations. The focus is on elimination wherever possible. If we don’t need to work at height we shouldn’t.
•We have had particular success this year on erecting forecourt canopies at ground level and lifting into place. The remaining works including the underside sheeting are conducted via scissor lifts. The system has been witnessed and endorsed by specialist
HSE Inspectors. •The need to access the top of fuel tanks during installation has now been eliminated. Working closely with our supplier Cookson & Zinn, we have developed a grillage system that allows the tanks to be lowered direct into the excavation and secured before hand. Even the lifting tackle is attached at the factory prior to delivery and its left in place until backfill is completed.
•Hinged vent stacks have been jointly developed with D. Berry & Co to eliminate the need to access stacks via towers or mewps.
•During 2006 we have started a roof plant removal programme. If we have older type BPsites with roof plant where maintenance works rely on
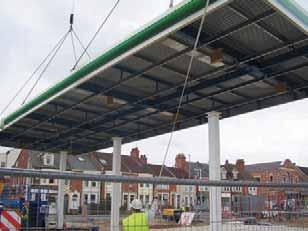
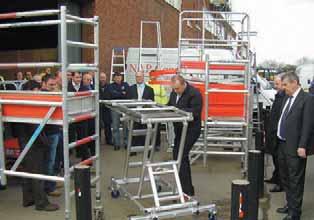
•Traditional type stepladders have almost been eliminated on our construction sites and approximately 70% of our maintenance contractors have sourced more modern alternatives including sherpamatic ladders and podium steps. We have held several workshops with national suppliers and our contractors to highlight the most recent alternatives.
Training
•All GAcontractors must have valid
UK PIASafety Passports. This includes our staff and BPwho need to visit sites.
•We have a close relationship with
APEAand view their courses as essential for our Project Managers. Bespoke courses for the GAhave been held by Brian Baker and Paul Craven and we regularly put staff through the Audit and Inspection a n d Electrical Installation courses. All GA staff have to attend a min 1 day HSSE training each year.
•·Together with SMTS we have been successful in getting EU and Central
Government grants to fund training programmes for our contractors.
SMTS have a dedicated training coordinator who works closely with each contractor. Following the GA application, several of our partners including Broham Forecourts and
Xmo Strata are receiving full funding to put staff through NVQ and CSCS training. They are also being advised on how to receive additional CITB grants. We have held introduction presentations with our supply chain with many due to be added to the scheme later this year.
Incident & Injury Free (IIF)
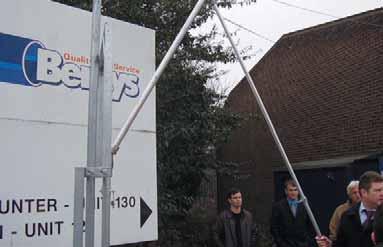
IIF has become a core value with the GA. All our staff have attended commitment workshops and from the beginning we ran Senior Management sessions for our contractors. We had to get the understanding and buy in from our Contractor Owners and Managing Directors before we started a full roll out programme. To date over 90% have attended our 1-day workshops, which were held monthly at Milton Keynes National Hockey Stadium. We now offer bespoke courses on request at contractors’offices / depots across the UK.
IIF is a behavioural safety approach to improve attitudes towards health and safety at work and at home. The workshops provide practical advice on how to talk and communicate with colleagues and others. Tips on how to tackle difficult situations and the need to recognise / praise safe working is of particular importance to site supervisors. We have been delighted by the progress over recent years as our accident rates continue to reduce. Our near miss reporting is up, serious incidents and accidents are down and the fear factor when things go wrong has been very much reduced. Contractors are now less likely to cut corners and take risks to finish the job. We regularly highlight those who have informed BPSites that they cannot do their works unless the safety measures
Communication
•The GAHSSE Newsletter is issued every quarter and was started in 2005. Following the success of our IIF courses contractor feedback has increased and we needed a more effective way to communicate good practise and lessons learnt. The format is fluid and reflects the issues from the last three months. It has proved very successful in influencing the behaviours of BPSite Staff. Managers are not pleased to see their site highlighted for safety concerns raised by contractors. We have also highlighted BPStaff who have been proactive and prevented accidents. Every contactor and supplier receives electronic versions with hard copies issued to our construction sites and maintenance contractors with requests to post on notice boards and include in toolbox talks.
•Reward & Recognition is an area we strongly support. Guidance has been issued to all GAstaff on what should be recognised. The rewards vary and range from a formal appreciation letter to an individuals employer, GA branded clothing (fleeces, tee shirts) or gift vouchers. Our annual
Contractor HSSE awards are held each February. Nominations are received from all GAStaff and categories include Most Proactive
Company, Most Proactive Individual and Best Application of IIF. The awards dinner is preceded by our
Contractors Forum and the guest speakers have included APEA
Chairman Brian Baker.
•We issued our 3rd edition HSSE dvd earlier this year. Our first edition was a site induction film featuring Ian
Whittingham MBE who described the ongoing problems he faces being confined to a wheel chair following a fall at work that left him paralysed from the waste down. Ian was awarded his MBE for his ongoing work with the HSE and their safety campaigns. Our second edition supported our IIF message and encouraged contactors to challenge unsafe working. The 3rd edition features the traditional hazards that continue to kill and injure construction workers and how they relate to operational service stations. We have also included re-enactments of real accidents / incidents that occurred on our sites.
Conclusion
We are convinced that accidents cannot be eliminated by policies and procedures alone. Behavioural safety programmes that create and support a deep rooted safety culture are essential in influencing the various works that take place on our sites every day. It’s about people feeling empowered and choosing to work safe. If this approach is supported by clear and simple procedures and regular review of existing methods to constantly challenge best practise we may achieve an IIF workplace.
Will we abandon IIF if we don’t achieve zero accidents? No. It’s important we keep trying every day. Will we ever achieve an IIF workplace? I’m not sure. But if you truly believe that its unacceptable for people to be harmed at work is there any alternative?
Articles Controlling Electrostatic Ignition Hazards during Fuel Delivery at Forecourts
By Graham Hearn1, Ulrich von Pidoll2 & Jeremy Smallwood3 1 Wolfson Electrostatics 2Physikalisch -Technische Bundesanstalt (PTB) 3Electrostatics Solutions Ltd
Editors Comment This technical paper has been written for the APEAby Europe's leading experts on static electricity and the Association is most grateful for the contribution their paper makes on the safety of fuel handling at petrol filling stations. It confirms that plastic pipework properly installed is safe to use in all fuelling situations.
The use of electrically insulating synthetic materials, such as plastics, for fuel pipelines and other fuel handling components is now becoming widespread. In the case of buried pipelines in filling station forecourts the use of these materials offers superior corrosion resistance and increased longevity. This in turn reduces the risk of pollution due to fuel leakage. It is well reported that the flow of fuel under certain conditions in both metal and plastic pipes can produce significant levels of electrostatic charge on the fuel. Pipe systems in modern filling stations generally contain both plastic pipe lengths and metal components such as in-line valves and couplings on which electrostatic charge can accumulate. Non-conductive pipework properly installed with grounded metal fittings and capped electrofusion coupler terminals should not create electrostatic ignition hazards.
Over the last year or so a small number of fires have occurred around offset fill pipes at various petroleum forecourt refuelling sites in Europe. Initially these were blamed on either static electricity or thermite reaction. A joint investigation by Exxon and Wolfson Electrostatics [1] has shown the most likely cause to be an electrostatic discharge between an electrofusion coupler (EFC) and nearby metal flange. Measurements performed during a repeat of the delivery operation at the site however produced no significant readings of static electricity.
Work undertaken independently by the three authors of this article has highlighted a number of factors influencing the levels of electrostatic hazard and these are discussed in this article. The influence on electrostatic ignition hazards due to the introduction of new alcohol-based ‘biofuels’such as E85 is considered. This article analyses the conditions necessary for electrostatic ignition and draws important conclusions with regard to the parameters influencing the degree of hazard present.
Hazard Analysis
There are five general conditions necessary for an electrostatic ignition hazard to be present:
1.Sensitive flammable atmosphere 2.Generation of electrostatic charge 3.Accumulation of charge 4.Electrostatic discharge (ESD) 5.Sufficient discharge energy for ignition
If all of the above conditions exist, an ignition hazard will be present, if any of the conditions are removed, the hazard is obviated. As a ‘belt and braces’ approach attempts are often made to remove more than one of these conditions, however the extent to which any mitigating measures can be applied in practice often involve other considerations which will inevitably include cost and practicality.
Is a flammable atmosphere present?
Petroleum spirit vapour has a flashpoint of around -43C and is flammable within the range of about 16% by volume with air. At most times within a pipe system and storage tank, there is insufficient oxygen to support combustion ie the atmosphere is overrich. During tanker delivery, a flammable atmosphere may be established around the end of the fill pipe. Similarly flammable petrol vapour concentrations may exist due to fuel spills and within fill-boxes and chambers. This of course applies equally to metal and plastic systems.
E85 which is 85% ethanol and 15% petrol has a reported flashpoint of < 20C [3]. It has a wider flammable range than that of petrol of around 2-26% by volume [3]. Due to the fact that the gas phase of E85 contains much more petrol vapour than ethanol vapour, its upper explosion point is strongly dependent on the filling level of the tank (the so called “effect of ullage space”). An almost full tank of E85 has a non flammable gas atmosphere above its liquid phase at temperatures higher than 0C, this temperature raises to 18C when the tank has become 99% empty [3,4]. Because of this effect E85 may produce flammable atmospheres in a wider set of circumstances than petrol.
Diesel which has a flashpoint in excess of 60C will not produce a flammable atmosphere under normal conditions and is not considered at risk from static electricity at any time during delivery. However mixing diesel with small amounts of petrol, for example when filling diesel into a road tanker containing residual petrol from the last filling, may produce an explosive atmosphere even in a diesel tank.
For all fuels the sensitivity to (spark) ignition varies significantly over the flammable range and is easiest to ignite at a concentration roughly midway between the upper and lower flammable limits. At or near this concentration, the ignition energy is very low and vapour ignitions may occur as the result of sparks from charged, ungrounded metal or electrostatic brush discharges from highly-charged insulating surfaces.
Charge generation due to fuel flow
During fuel delivery it has been estimated that 4500-6000 litres is transferred in 10-12minutes. This corresponds to fuel flows of between 7 and 9 litres per second and moderate velocities in the pipe of around 0.3 metres per second.
The electrostatic charge that is generated in fuel being pumped along pipes arises from the presence in parts per million (or billion) of ions in the fuel.
Positive or negative ions selectively attach themselves to any interfacial surface in contact with the fuel, such as the inner wall of the pipe, due to selective chemical adsorption (and possibly ionic injection from the pipe wall) [2]. As a consequence, the inside surface of the pipe acquires a unipolar charge and ions of the opposite polarity in the fuel are attracted to it. Acharged layer then extends from the wall into the fuel of a thickness that increases with decreasing fuel conductivity, the net charge in the pipe being zero when the fuel is at rest.
When the fuel flows, the ions in the boundary layer tend to be carried along, while the opposite charge on the wall dissipates to earth at a rate depending primarily on the pipe material's conductivity. This implies that there will be a significant difference between charging behaviour in metal and plastic pipes. Any filters, valves and elbows will generally increase the amount of charge, due to greater interfacial charge separation, higher fuel velocities and increased turbulence. Similarly, the presence of free water in the fuel can also increase the charge concentration, again due to the charge separation arising from the large interfacial area of the emulsified mixtures.
Petrol and Diesel are known to produce high levels of charging under certain conditions.
The conductivity of market-place petrol can vary from 5-500 pS.m-1 [3]. Experiments have shown that the highest charge generation occurs at a conductivity of 5-50 pS.m-1[5]. Being alcohol-based, the conductivity of E85 is several orders of magnitude higher than traditional fuels and is unlikely to generate hazardous levels of static electricity due to flow through plastic pipes.
The presence of filters and flame arrestors in the pipe may increase static charge generation and charging levels are likely to increase if the filter or flame arrestor becomes partially blocked with particulate materials and impurities. Entrained air and immiscible impurities could also increase electrostatic charge generation.
According to CLC/TR 50404 [6] typical charge densities of 10 μC.m-3 in liquid due to flow in a pipe can be increased tenfold to around 100 μC.m-3 by a blocked strainer. This level of increase would correspond to a similar tenfold increase in voltages induced on ungrounded metal parts such as electrofusion couplers.
In addition to the electrostatic charging mechanisms associated with fuel flow, there is also the possibility of electrostatic charge generation by friction with the external pipe wall and other components of the system, such as the walls of plastic chambers and sumps. In such cases, the charge generation mechanism could be frictional contact with a maintenance workers clothing.
Charge accumulation
With plastic pipe systems, as with metal pipework, the primary source of charge generation is due to the flow of fuel through the pipe, as discussed above. With metal systems the charge on the metalwork will normally be conducted safely to earth. With plastic systems, electrostatic charge can accumulate on the pipe wall and associated ungrounded metallic components, such as the heating coils in electro-fusion couplings, metal valves and other metal fittings. This represents the principal difference between plastic piping systems and earthed metal systems from an electrostatic point of view.
Totally buried insulating plastic pipes usually do not create dangerous discharges inside and outside of the pipe. However, in an excavated, unburied or partly buried system extra care must be taken. In chambers and fill boxes, small sections of the pipe are not buried. The metal components present in a fill box (e.g. valves and other fittings) usually have enough capacitance, to produce incendive sparks when charged by influence of fuel flowing through insulating pipes. For this reason, all conductive objects in chambers and fill boxes should be sufficiently earthed and the surface of
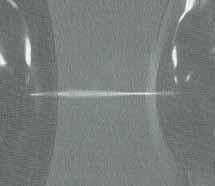
(a) charged objects should not exceed the limits given in [6]. Furthermore, the electrical connections of electrofusion couplers should be tightly closed using plastic caps [6].
The forecourt ground surface of a filling station is normally made of a dissipative material with a leakage resistance to earth of less than 108 Ohms, e.g. concrete [6]. As tyres are usually sufficiently conductive to provide a leakage path to ground, the delivery road tanker parked on the forecourt is normally earthed via its tyres. Faults in the manufacturing process of modern tyres however can occasionally lead to highly insulating tyres. As a consequence, the leakage path to earth of the road tanker cannot be guaranteed [7].
Electrostatic discharges
There are essentially two types of electrostatic discharges (ESD) that can occur during fuel delivery: spark and brush discharges. With regard to ignition hazard the characteristics of these two discharges are very different.
Figure 1 (a) shows a spark between two metal objects at different potential.
Figure 1 (b) shows a brush discharge between a highly charged dielectric and an approaching earthed electrode.
Figure 2 compares the discharge waveforms for the two. The spark discharge current in (a) looks like a damped sine wave whereas the brush discharge current (b) is a single broad pulse. It is important when comparing the waveforms in figure 2 to note that the y-axis for (a) has been compressed and that the spark current is 20 times greater. Generally sparks produce a
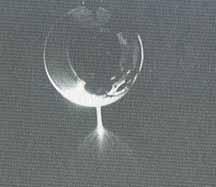
(b)
Figure 1 (a) Spark discharge between a charged metal object and a grounded metal electrode (b) brush discharge from a grounded metal electrode to a highly charged dielectric sheet.
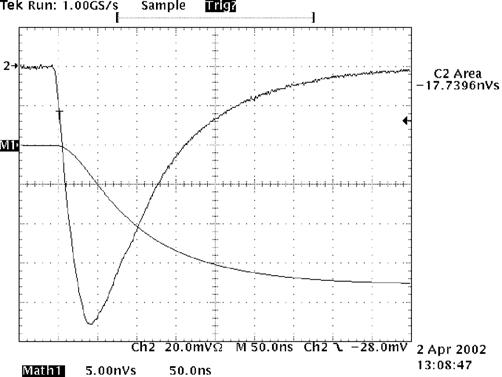
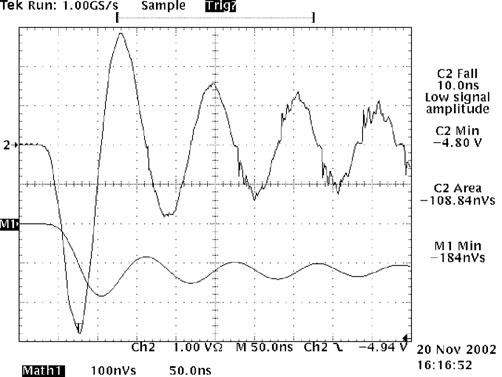
(a) (b)
Figure 2 (a) Waveform of the current and its integral of a spark discharge between a charged pulse capacitor (93,3 pFat 7 kV) and a grounded metal electrode (b) same for a brush discharge from a grounded metal electrode to a highly charged dielectric sheet.

Grounded metal flange Flame arrester Measurement wire
Possible site of spark?
Electrofusion coupler
Summary of conclusions
higher current density than brush discharges resulting in higher temperatures and are therefore more likely to cause ignition.
Ignition of fuel vapour
Spark discharges from charged, isolated metal components constitute a strong ignition hazard if they have sufficient energy. Metal components in a fill-box are generally earthed. Any unearthed items such as EFC heating coils and clips can only store small amounts of electrical energy and need a high potential to have sufficient energy to ignite an optimum fuel-air mix. Even if these conditions are met, a nearby ground is required to provide the spark gap.
To constitute an ignition source a brush discharge will require not only a highly charged electrically-insulating surface but a grounded metal electrode to initiate the discharge. Figure 1 (b) illustrates how the energy of a brush discharge is concentrated close to the
ground electrode and it is this region of the discharge most capable of providing the source of ignition. Afew millimetres away from the ground, the discharge becomes diffuse and nonincendive. Brush-like discharges inside pipes have been recorded, especially for fluorinated pipes, but they are normally not incendive because of the over-rich or too-lean atmosphere inside pipes. These discharges may be hazardous if an optimised fuel-air concentration were to exist [7]. 1. Static electricity has been blamed for fires that have occurred around offset fill Figure 3. All the conditions necessary for ignition? Flammable atmosphere due to residual vapour in the fill box; charge generation due to fuel flow; accumulation on the heating coil of an electrofusion coupler; spark to nearby grounded metal flange. pipes during tanker delivery. Non-conductive pipework properly installed (grounded metal fittings and capped electrofusion coupler terminals) should not create electrostatic ignition hazards. 2. If static electricity is the cause of these fires it is almost certain to be the result of sparks from ungrounded metal fittings or electrofusion couplers igniting residual fuel vapour in the box outside the pipes. If air is present in the pipe, brush discharges may present an ignition hazard. Brush discharges from a buried
Ground Wire
Capped Terminals
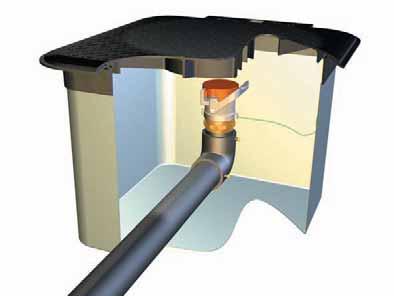
Figure 4. Properly installed underground fill pipe with grounded fitting and caps fitted to electrofusion coupler terminals.
plastic pipe surface are unlikely to produce sufficient current density in the discharge to cause ignition. 3. Incidents of fire have also been blamed on thermite reactions between aluminium fittings and corroded steel but like static electricity this ignition source has not been ratified.
4. Within a normally-functioning pipe system (plastic or metal) there is insufficient oxygen present to support or propagate combustion.
Furthermore. air does not enter the inlet pipe of a fill pipe in modern
European installations. The installation is under pressure (35mbar) causing vapour to come out of the fill after disconnection rather than air going in. This will tend to leave an explosive atmosphere just outside the pipe rather than inside.
5. The alcohol-based fuels E50 – E100 have a much higher electrical conductivity than petrol and Diesel and will not generate hazardous static potentials in pipe systems assuming they are in contact with an earth point somewhere in the tank system.
6. Flame arresters similar to those in place at the site of the incidents in
Hungary [1] (Figure 3) may increase the level of charge generation during fuel flow and may therefore increase the ignition risk.
Fire prevention
The precise cause of the recent flash fires during fuel delivery cannot be considered certain on the basis of the available evidence. However some recommendations of preventative action can be considered. The ignitions were probably caused by an electrostatic discharge external to the fill pipes. Fuel or vapour may well have been present due to spillage or vapour release. It was found that some vapour leakage could occur from the Stage 1 and fill connections on opening, and through a connection that was not vapour tight.
If the possibility of fuel or vapour in the vicinity of the fill pipes can be excluded then the risk of fire from this cause may be eliminated. Reliable exclusion of fuel vapour would be perhaps the best way of removing the risk of ignition outside the pipe. There appears to be little if any risk of ignition inside the pipe if it is either buried or air intake is avoided.
It has been suggested that filling the box with sand to above the pipes and sealing the top layer against fuel ingress. This may be one way of successfully removing the possibility of a flammable mixture near the pipes. This procedure would have added benefit in effectively grounding electrofusion couplers in contact with the sand, in all but the driest conditions. Furthermore, if by some chance vapour did accumulate and a spark could ignite it, the sand would prevent the propagation of flame.
In any location where a flammable atmosphere can occur, it is important to ground all conductive objects of significant size. Electrofusion couplers may be significant in this context. Additionally it is important that a long term reliable earth connection to these items is achieved.
Another approach is to electrically insulate the heating coil terminals in the coupler by some means to prevent electrostatic discharge. This is likely to be effective if a reliable seal is obtained for example by a tight fitting cap or peg. Figure 4 is a photograph of a properly installed underground fill pipe, with grounded metal connectors and capped electrofusion couplers. In this situation, steps 3 and 4 of the five hazard conditions (charge accumulation and ESD) are removed.
With alcohol based fuels E50-E100 it is postulated that fuel flow will not result in significant electrostatic potentials. However with existing installations the presence of a sensitive flammable atmosphere may still exist. Furthermore due to their wider flammable range and different ignition properties, these fuels may be somewhat easier to ignite. With this in mind, precautions against electrostatic discharges from other sources e.g. relating to the grounding of the vehicle and personnel must be in place.
References
[1]Wolfson Electrostatics report
R436/JMS for Exxon Mobil dated 1
February 2006
[2] Feleci, N. J., (1984). J.
Electrostatics, 15, 291-7.
[3]Brandes, E., PTB Braunschweig, section 3.41, Safety data of E50,
E60, E85 and E>85, unpublished datasheet dated 25.7.2006.
[4]Vaivads, R. H., Bardon, M. F. Rao, V. K. and Battista, V., Flammability Tests of Alcohol/Gasoline Vapours, SAE Technical paper 950401, 1995.
[5]von Pidoll, U., Krämer, H. and
Bothe, H., Avoidance of electrostatic hazards during refuelling of motorcars, J. of Electrostatics 40&41 (1997), 523-528.
[6}CENELEC Technical report
TR50404, Code of practice for the avoidance of hazards due to static electricity, 2003.
[7]von Pidoll, U., Electrostatic ignition hazards in motor cars – occurrence, detection and prevention.
Proceedings ESA/IEEE Joint
Meeting on Electrostatics, 2427.6.2003, University of Arkansas,
Little Rock, 78-89.