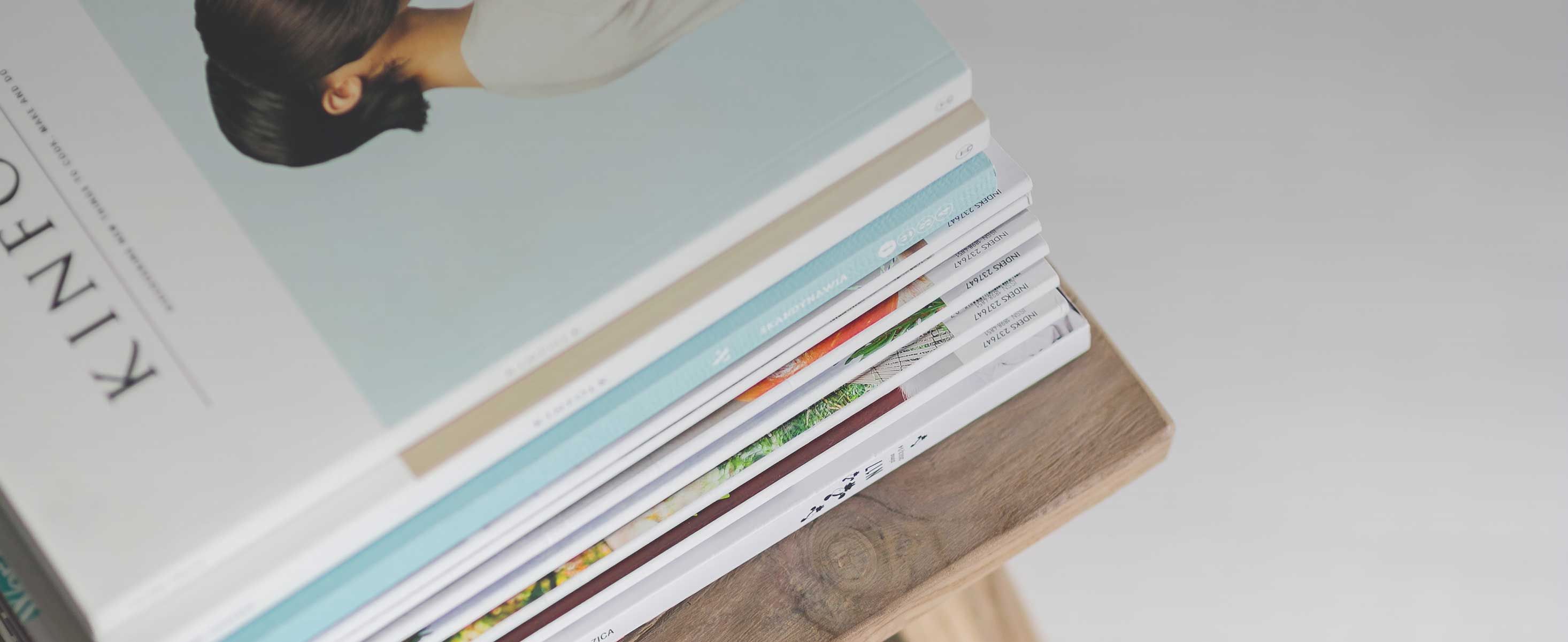
10 minute read
Press Releases
protection afforded by the coating system, increases the structure design life, and prevents deterioration of the structure. Cathodic Protection therefore prevents there being any loss of product caused by external corrosion, avoiding environmental damage and safety implications.
• Permanent
Advertisement
To guarantee freedom from corrosion the coating must completely separate the metal surface from the ground water (or electrolyte). Coatings alone cannot entirely eliminate corrosion, because they can never, in practice, be applied and buried without any defect or damage. However, a correctly designed and maintained cathodic protection system can guarantee to stop corrosion at a fraction of the cost for replacement system.
• Well Established
The application of cathodic protection to prevent external corrosion on new buried steel storage tanks is a well-established technique. It is routinely specified as a method of protecting thousands of LPG vessels in the UK, it is widely used in the US and in some EU countries it is mandatory to protect buried petrol storage tanks with cathodic protection.
Cathodic protection has been accepted in the US by the Environment Protection Agency as a method to prove that underground storage tanks remain structurally sound, as required by Federal Law.
• Verifiable
Buried storage tanks cannot be easily inspected once they are buried, but when fitted with cathodic protection they can be monitored, to assess the tank's corrosion status and the level of cathodic protection applied.
So what are the limitations on using CP?
• Evaluation
Not all buried storage tanks are suitable for upgrading by cathodic protection. Tests on the t a n k s condition should be carried out prior to the application of • Maintenance
Cathodic protection is an electrical system that will need regular inspection & maintenance by suitably qualified personnel (see Section 8.0)
• Design
Each petrol filling station will have different safety and cathodic protection design considerations that should be assessed by a competent individual.
Frequently Asked Questions:
Q. Is it safe? A. Yes - it uses very low voltage/current and installation techniques are regulated by established industry codes.
Q. Is it proven? A.The principles were established by Sir Humphrey
Davy in 1820's. Routinely used on pipelines and used on underground LPG vessels it is well established. Tanks protected by CP are given same status as new tanks by US Environmental
Protection Agency.
Q.Is it economical to install? A.Typically 1/10 cost of replacement and only 2% of new tank installation.
Q.What are the running costs? A.Typical power consumption equates to one light bulb. Annual Monitoring/Maintenance is quick, simple and cheap.
Q.How long do these sacrificial anodes last? A.Ground conditions determine the amount of sacrificial anode material required and this would be decided at the design stage. The life of the anodes will be dictated by the output, which relates to the coating condition of the tank.
Typically sacrificial anodes will have a life of 10 15 years. Replacement is normally possible with minimal disruption utilising a small drilling rig.
Q.Can an operator save money by checking the anodes themselves? A.Specialists should be used to monitor cathodic protection systems. The checks are carried out annually, they are inexpensive (typically less than 20% of a precision tank test) and do not affect site operation.
For more information please contact the author: Martin McTague of Ecotech on 01325 316081.
CP Anode ready to be inserted
Articles Modern Fuel Delivery
By Alec G. O'Beirne PTF Training Limited
HSG 146 clearly identifies that one of the higher risk events in the operation of a petrol filling station is the process of receiving fuel from a road tanker.
This article will have a look at the delivery vehicle and the delivery process.
Petrol tankers have come long way since the days of horse drawn vehicles and 'can boys'. The old 2 gallon cans embossed with the company logos cans now make entertaining collectors items.
The rapid introduction of the internal combustion engine resulted in the core of the market changing from heating and lighting oils to petrol.
Initially the powered tanker ran on petrol engines with tanks of around 1000 gallons,
As illustrated by the Shell Mex and BP Dennis tanker (Picture 1.) fitted with a 3 compartment 1000 gallon steel tank manufactured by
Thomson's at Bilston. This company is still building petrol tankers as part of Heil Trailer International Ltd.
Powered by a 4 litre 4 cylinder petrol engine the 'Flying Pig' was used for inner city deliveries, and latterly as a training vehicle. Anyone who could master the crash gearbox could drive anything.
Petrol engines gave way to diesel and over the years the size of the trucks gradually increased until we are now operating at the EU norm of 44 tonnes.
This article will focus on the full weight vehicles used to deliver petrol and diesel fuel to the larger filling stations.
These vehicles predominantly operate at 44 tonnes and are capable of carrying a maximum load of around 43,000 litres depending on the fuel being carried. Since diesel is heaver than petrol a full load of diesel will equate to around 37,000 litres.
Designed as articulated units they are mounted on 6 axles ( 3 on the trailer and 3 on the tractor unit). This
assists in spreading the load and the use of air suspension also helps to minimise road damage. (Picture 2)
Most oil companies now employ a specialist contractor to deliver product to their filing stations although the requirements of the smaller sites are often met by one of the vehicles operating for a distributor. These trucks, many of which are designed to meet the requirements for petrol are usually much smaller since the bulk of their work is in the delivery of heating oils
to domestic and agricultural customers. (Picture 3.)
Full size trucks are mostly manufactured from aluminium alloy ( picture 4) to keep the unladen weight to a minimum whilst maximising the payload.
All road tankers require to conform to a large number of specifications both national and international.
In 1996 the UK enacted the provisions of the European Agreement for the International Carriage of Dangerous Goods by Road, known by the acronym 'ADR'
There are also the national requirements such as UK 'Approved Tank Requirements' and Approved Vehicle Requirements as well as the Institute of Petroleum code 'Petroleum Road Tanker Design and Construction' .
Theses various codes and regulations ensure that the vehicles are constructed to recognised standards and maintained and operated in a safe manner. In addition the major UK Participating Oil Companies have developed a 'Safe Loading Pass Scheme' to ensure that tankers loading out of oil company premises meet the recognised standards and do not introduce safety problems when loading at another company's facility.
Picture1 - 1935 Dennis 'Pax' with Thompson tank, 3 compartments 1000gallons. Picture 2 - 2003 Heil ADR trailer. 6 compartments 42,800 litres.
Picture 2 - 2002 Distributor vehicle constructed to petroleum standards
Loading a tanker.
Tankers can be loaded in two ways.
1. Top loading
Since the introduction of bulk liquid tankers top loading has been the standard way of filling the vehicle.
The first task before any other is to connect the bonding lead. This wire ensures that any electrostatic charges that exist on the vehicle, or build up during the loading process, are dissipated to earth and do not provide an ignition source for vapours.
Each compartment is provided with a lockable man lid which allows the driver to place the loading arm into the tank.
The loading arms are counterbalanced usually by means of a spring and it is important that the drop pipe goes fully to the bottom of the tank compartment to prevent splash filling, a known generator of static charges in fuel.
The amount to be loaded can then be pre-set on the meter and the driver stamps the loading ticket before opening the loading valve. Once the pre-determined quantity has been loaded the meter shuts off the flow automatically, the driver shuts the valve on the loading arm and moves it to the next
2. Bottom loading.
All tankers constructed for the delivery of petrol have been designed and constructed as 'bottom loading' vehicles since January 1996 in line with the VOC regulations.
The process involves first unlocking the guard bar which protects the loading/discharge adaptors, known as API's after the American standard to which they are manufactured. This process also opens the internal valves in each compartment, known as the 'foot valves' as well as the vapour transfer valves in the top of each compartment. Since the API is also a valve there is effectively a double valving of each compartment outlet.
The driver can then connect the overfill protection system. This system is linked to the loading meters by a multi core cable and
Picture 5 - Overfill Prevention System and Vapour Recovery Hose
plug (Picture 5)
Each truck compartment is fitted with a probe which senses the presence of the liquid surface. Before the system will allow the truck to be loaded it runs a check on all the probes and also ensures that the vehicle is bonded to allow static dissipation.
The probes must indicate that they are dry and the control unit must recognise that the truck is bonded to the loading pipework before the control unit will give the meters a 'permissive signal' to allow loading to commence.
The driver can then connect the vapour recovery hose to the vehicle which enables vapours displaced during loading to be recovered in the terminal vapour recovery unit.
Finally the bottom loading arms can be connected to the truck adaptors, the self sealing coupler valves opened, the API's opened and the meters set to fill the compartment. Rotating grade indicators are provided for each compartment, usually adjacent to the API valves which the driver must set to show the product loaded in each compartment. (Picture 6)
In the event of an overfill the probe in the compartment senses the high level and shuts down the loading process to the entire vehicle. Until the overloaded compartment has product removed the system will not allow the rest of the vehicle to be filled.
Once the loading process is complete the driver can then collect a 'bill of lading' prior to leaving the terminal.
Picture 6 - API Outlets, Vapour adaptor, overfill plug and grade drums
En route
Vehicles carrying hazardous goods are required to be fitted with a number of safety features such as speed limiters which prevent the vehicle exceeding 56 mph.
In addition they are provided with anti lock brakes as well as a secondary retardation system to reduce the strain on the truck brakes during long hill descents.
Wiring installations, usually in flexible conduit must be firmly fixed to the chassis to prevent chafing.
Fire extinguishers must be carried on board, both in the cab (2kg minimum) and externally for a load or tyre fire. (6kg minimum).
Spill kits are also provided for the drivers use in the event of minor spillages.
The truck electrical system must be capable of isolation by means of an external master switch which must be switched off during loading and unloading.
In addition there should be a facility to allow the driver to isolate the electrical system from the driving position.
Cab materials must be fire resistant to a recognised standard and any windows in the rear wall of the cab must be hermetically sealed and made of fire resistant glass.
The vehicle exhaust system should discharge to the offside of the vehicle and be routed in such a way as to avoid any likelihood of fuel coming into contact with it.
In addition a fire screen, usually metal, is called for to the rear of the cab. This is to prevent spilled or leaking fuel reaching hot engine components and additionally isolate an engine fire from the main cargo tank.
Vehicle Marking
All tankers carrying hazardous goods are required to be fitted with placards indicating that they are carrying a hazardous load.
At the front a plain reflective orange rectangular panel will be found .
On both sides and at the rear of the tank are Hazard Warning Panels which advise the emergency services of the load being carried.
A typical set of panels are shown below.
Five pieces of information are provided. 1. The emergency action code which advises the fire crews of the appropriate equipment necessary to tackle a fire or spillage. This is contained in the code 3YE,3Z, etc. 2. The UN number of the product being carried, 1202, 1203, 1223 etc. 3. The telephone number for specialist advice on the load, 4. The hazard warning label for class 3 product (flammable