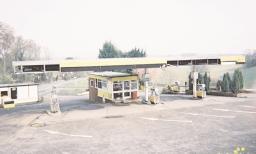
12 minute read
Microbes and fuel systems - The overlooked corrosion problem
By Bob Pillar, Petroleum Officer/Enforcement Officer (Safety), Devon County Council
A Devon filling station owner has finally made his redundant site permanently safe, after 3 years, 2 prosecutions and 1 meeting with the Environment Agency.
Advertisement
The garage is in a rural location near to Exeter, and on the main trunk road from Newton Abbot to Exeter and is passed by thousands of vehicles every day of the year, and also by holiday traffic leaving South Devon. It
apparently had been closed recently and there was a licence still in force on the premises, which was issued by Devon Fire and Rescue Service, who were the licensing authority up to July 2000. The garage dates from the early 30's and has five tanks on site, four 13,500 litres tanks used for petrol and one 22,500 litre tank used for diesel for the whole of its life. It was set up for self-service use and also had an HGV facility on the premises.
The whole saga started for me in February 2001 when, as the Petroleum Officer, I visited the site. From that first visit it was clear that the site had been abandoned although no work had been done to make it even temporarily safe. The tanks were unlocked, and still contained product, the dispensers were still in place and unlocked, and there was evidence of leakage on the site. One dispenser had a novel safety feature where one of the hoses had been removed; the hole had been capped with a Coca-Cola bottle top! Apparently not an approved modification!
This then started the ball rolling and after numerous letters and thinly veiled threats to the licensee and then the owner of the site, who was one and the same person. No correspondence was ever answered, even that which was delivered by hand to his home address. Finally the threat of issuing an Improvement Notice was carried out on the 20th December 2001, giving the owner until the end of March 2002 to make the site permanently safe, by filling the 4 petrol tanks and removing all other equipment associated with the petrol installation.
Surprisingly no work was done at the
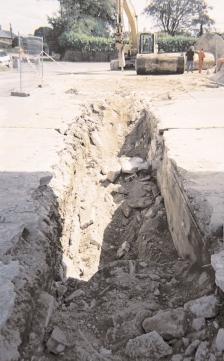
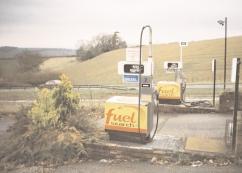
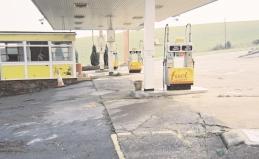
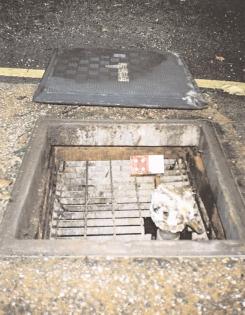

site and the legal process started. This seemed to have some effect as letters were now answered, but only to request that the site be licensed again! Sadly, this request was turned down and a prosecution ensued, which went to Court in February of 2003. The owner of
the site pleaded guilty to the charge, despite apparently not realising what he had to do on the site. The Magistrates obviously didn't believe him, fining him £8,000 with £1,000 costs, and instructing him to comply with the Notice by the end of May 2003.
At the beginning of June 2003 a return visit was again made to the site, to find that some work had been done, but none that was specified in the Notice.
Therefore the whole legal process was started again, but this time the owner wanted to talk to me. However, he was unwilling to be interviewed and the case finally went to Court in December 2003, with him again pleading guilty. This time the Court felt a little bit more sorry for him as they fined him £3,000 with £1,262 costs. Again they gave him until the end of January 2004 to do the work. This second case seemed to have the desired effect, because the owner now became more co-operative, and came forward with plans to convert the site to diesel only storage in order to supply his other premises when they needed it. Unfortunately as the site is within a water abstraction area the Environment Agency declared an interest, and at a subsequent meeting between themselves, the owner and myself a plan of action was drawn up for the
owner to comply with everybody's needs. This included tank tests before any product was stored in the tanks in question, and monitoring of the diesel stored on site. The owner then went away to think about what he had to do.
At the end of January I received a call from the owner informing me that he had decided, finally, to have the tanks permanently filled with resin generated foam on the 16th February and would that be all right. After I had got over the initial shock I said it would be and put the phone down, thinking of numerous questions I would have liked to ask him only then and not before, the main one being "Why now".
Being of a somewhat disbelieving nature as far as this gentleman was concerned I vowed to visit the site on the 16th, and lo and behold there they were, RGF of South Wales, doing the deed and filling the tanks as I had been advised. The certificate of filling was in my hand later that date and finally I could put the file away.
So after 3 years, numerous letters and phone calls, visits to the site, two prosecutions, £13,262 in fines and costs, and boring colleagues about the whole sorry saga the site has been finally made safe. Why it could have been done at the beginning of the process I cannot say, perhaps he thought I would go away and forget him. Perhaps its an example of the old adage that persistence pays in the end. What his ultimate plans for the site are I don't know but as far as I am concerned, I've achieved what I set out to do.
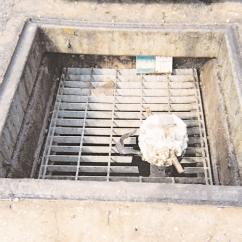
By Annie Risbridger
After 82 years production in leafy Stychens Lane, Bletchingley, the factory has been relocated to the Holmethorpe Industrial Estate in Redhill, four miles away.
All of the staff have relocated with the company and are delighted with the extra space and facilities in the new building. They will miss the rural location, but the parking and materials handling problems will be solved! They are pictured below at the old factory a few days before the move started.
The Stychens Lane factory evolved over many years from a modest
workshop at the bottom of William Risbridger's garden. After winning a large contract William designed a larger workshop and the company built it themselves in four weeks. This has been the machine shop for many years. There were no concrete mixers or other labour saving devices and they used horse and cart to transport the building materials from local quarries! It still only took four weeks, and it is interesting to wonder whether it would be possible to build something that quickly nowadays??
During the war the machine shop was busy 24 hours a day, run by a female workforce using gas powered belt driven machinery which was very noisy and quite dangerous! The company made parts for munitions and for machine tools, as part of the S o u t h e r n Industries Group, and there were also several teams of Installation Engineers working on airfield fuel tank installations all around the country. After working on imported USA made petrol pumps William then set about making his own. At the time he was manufacturing pumps there were over one hundred and thirty petrol pump manufacturers in the UK!
Although the factory is now too small for Risbridger this is not because the staffing levels have increased, in fact it has decreased over the years, as at one stage there were 35 machine operators. In recent years the company has invested in Computer Numeric Controlled (CNC) machine tools. Over the last ten years the products designed and made by Risbridger have tended to increased in value and physical size. The industries Risbridger serve require that there are larger stocks held to service their Just in Time requirements, so more space was a must.
Although the family are in some ways sad that their business is leaving it's historic site in Stychens Lane, it is the end of an era and an exciting time. The new building has many facilities, including meeting rooms and a training & showroom for products. The building has been refurbished over the last four months, and it is now ready. There are spacious office areas including a conference room and ITroom, a staff canteen and it is planned that there will be a trade counter for Forecourt Products.
Recently Annie Risbridger Hind took over as Managing Director with Gerry retaining a role as Chairman. Risbridger are currently enjoying a full order book and are working on a number of promising projects for the future both in the Forecourt business and in Aircraft Ground Servicing equipment. We are looking forward to welcoming our customers and suppliers to our new offices and to continuing to do business with them.
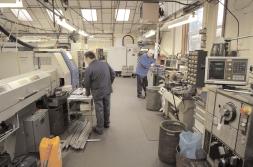
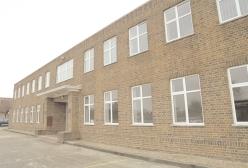
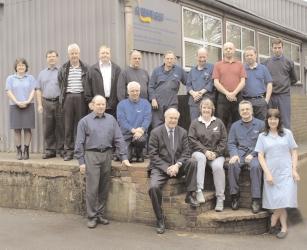
By Roger Marris, Senior Petroleum/Explosives Inspector, West Yorkshire Fire & Rescue Service
Acting on a complaint made by a member of the public, an Explosives Inspector and a Fire Officer of the West Yorkshire Fire and Rescue Service visited the Leeds premises of a seasonal fireworks trader on 20 October 2003. The member of the public had expressed concern at the large quantity of fireworks that were stacked in and around freight containers at the multi occupied premises.
The trader was known to the Explosives Inspector as he had registered a Mode 'A' store at the site for a number of years and had also been previously warned for the overstocking of fireworks.
When the Inspector arrived at the premises he found that in addition to the registered freight container, 2 other freight containers were being used for the storage of fireworks. The Inspector also found a quantity of fireworks stacked on pallets in the goods yard. It was estimated that the quantity of fireworks in the non-registered containers and on pallets in the goods yard was in the region of 5 tonnes. The fireworks trader agreed with the estimation, but insisted that they were 'goods in transit'. Although the Inspector did not accept the trader's explanation of the status of the fireworks, he was precluded from taking any enforcement action as this would have involved him seizing the fireworks for exact quantification (to satisfy the burden of proof) and he could not immediately find a licensed storage facility with spare capacity to keep the fireworks or a haulage contractor to move the goods.
The trader believing that he was at risk of being prosecuted for the unlawful storage of the 5 tonnes of fireworks in the unregistered containers was cooperative with the Inspector when it came to quantifying the fireworks in the Mode 'A' store, that were clearly in excess of the 1000kg permitted under the rulers of registration. After being cautioned by the Inspector, the trader admitted that he was 50% over-stocked and this figure was proved correct by a stock check that revealed the total quantity in the Mode 'A' store to be 1,526kg.
The supposedly 'goods in transit' fireworks were returned to the importer's licensed magazine before the end of the working day.
Due to the trader having received two previous written warnings for exceeding the permitted quantities, a decision was taken to charge him with 'keeping fireworks in excess of the maximum weight permitted by the Keeping of Fireworks Order 1959 and in breach of the general rules for registered premises thereby committing an offence contrary to Section 22 Explosives Act 1875'.
At a hearing before the Leeds Magistrates on 2 February 2004, the trader pleaded guilty to the charge. The Magistrates imposed a fine of £1,500 and awarded £500 costs to the Fire and Rescue Service.
Petrol Filling Stations - Stage 1b Vapour Recovery Safety Concerns when diesel tanks are manifolded with petrol tanks - issued by HSE
Introduction
This circular informs petroleum licensing officers of the safety implications arising when a diesel tank is connected to a stage 1b vapour recovery system. The information will also be of interest to environmental health officers who issue authorisations under the environmental protection act 1990 and the scottish equivalent and environmental health officers who enforce the hswa at petrol filling stations
Background
With the continued decline in the sales of leaded (4*)/lead replacement petrol, a number of filling station operators have converted 4* tanks to the storage of auto-diesel or have rearranged their storage capacities to meet their changing trading requirements by keeping diesel in a tank formerly used for petrol.
It is evident in some cases these changes (to the approved arrangements) have taken place without the consent of the PLA and without any consideration being given to the safety implications where the change involves a tank connected to a manifolded Stage 1b vapour recovery (VR) system.
The following text explains the safety problems that can arise where a diesel tank forms part of a Stage 1b manifolded VR system.
In addition to implementing the necessary control measures, the site operator will need to consider his duties under the Health and Safety at Work Act and will also need to notify the local Environmental Health Department or in Scotland, the Scottish Environmental Protection Agency (SEPA) as the inclusion of the diesel tank in the VR system could invalidate the authorisation under the Environmental Protection Act 1990.
The Safety Concerns
There are essentially three stages in the operation of a diesel tank manifolded to a vapour recovery system: the quiescent stage; the delivery stage; and the maintenance stage.
The quiescent stage of the tank is the time of normal site operation between deliveries. In this stage diesel is drawn from the tank through the dispensers: petroleum vapours will be induced into the ullage space from the manifold, although the concentration of these vapours may decrease between deliveries. It is possible that the absorption of petroleum vapours could alter the specification (composition) of the diesel, but of greater concern is the possibility that a leak on the diesel tank at the tank lid or its fittings could release petrol vapours into an area which could