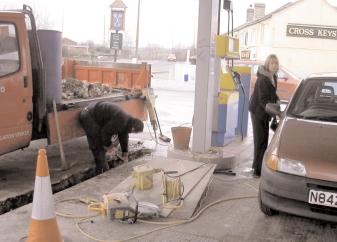
16 minute read
APEAAGM
By Tony Jenner, Cameron Forecourt Ltd
The accompanying recently taken photograph clearly shows the scant regard which, regrettably, some contractors in this industry are paying to Health & Safety! good, safe practices are maintained!
Advertisement
What the photograph does not show is the unprotected mains electrical cables snaking across approximately 10 metres of forecourt before entering
It must be assumed that the engineer in the picture has either had no Health & Safety training or that he has no regard for the safety of himself or that of others. It must be also assumed that the employer does not operate an active Health & Safety management system which would involve carrying out regular audits of his employees to ensure that the pay kiosk door where it was plugged into a wall socket. Irrespective of the obvious danger of flexible mains electrical cables in the hazard area no attempt had been made to secure the cable so as not to present a trip hazard to the many members of the public using the facilities of the service station. Other than positioning their van beside the pump no other attempt had been made by the operatives to cordon off and protect the work area.
Whilst I can accept that some of the actions shown in the photograph are a result of ignorance and a general disregard for Health & Safety, one further consideration is that these corners were being cut purely on financial grounds! To carry out this work safely it would have been necessary to fence the work area off completely and to use compressed air cutting tools rather than the electrically powered equipment shown in the photograph. Also, the engineer should be wearing personal protective equipment such as a high visibility vest or jacket. As a rough estimate I would say the health & safety cost cutting on this job saved the contractor between £300-£400.
In this instance, they got away with it and nobody was hurt, next time they might not be so lucky. It is essential that all of us within this industry strive to uphold the generally good standards of contracting that prevail and prevent the "cowboys" such as those shown in the photograph from behaving in such a cavalier fashion. If we fail to achieve this the next bulletin article may be reporting the tragic consequences of these foolish actions.
Pizza and Fireworks
By Roger Marris, Senior Petroleum/Explosives Inspector, West Yorkshire Fire & Rescue Service
In late October 2003, a customer waiting for a pizza at a take-away shop witnessed what she thought to be some fireworks being sold to a child from the back door. She reported the incident to the Police and Trading Standards Service. The Police were the first to respond to the complaint and after interviewing the proprietor, seized a quantity of fireworks that were stored in the food preparation room. The seized fireworks were subsequently passed into the custody of the West Yorkshire Fire & Rescue Service so that a full investigation could be carried out into the suspected unlawful storage of fireworks and the sale of fireworks to children.
Enquiries by an Explosives Inspector revealed that it was common knowledge in the high street where the take-away was located that fireworks were being sold at ½ price. There was no record of the premises being registered with Fire Service for the storage of fireworks.
When Explosives Inspectors interviewed the proprietor, he admitted to selling fireworks to selected customers but at the same time denied selling any fireworks to children. Unfortunately the witness who made the complaint refused to make a statement in fear of retaliation from certain elements of the local community, which meant that no further action could be taken against this allegation.
At a hearing before the Dewsbury Magistrates on 31 March 2004, the proprietor pleaded guilty to an offence of keeping fireworks in an unauthorised place contrary to section 5 of the Explosives Act 1875. He was fined £200 with an order to contribute £200 to the prosecution costs.
By Jeremy Kennett, Kent Trading Standards
On 20th August 2003, a woman set light to herself after having a petrol pump authorised for use, on a petrol forecourt in Canterbury, Kent.
She had arrived on the premise in a taxi, and was herself using a wheelchair. She first went to the forecourt shop, where the attendant sold her a lighter. She then went across the forecourt to the car showroom, where she spent a short time speaking to a friend who worked there.
She then left the showroom, and went to a pump, in her wheelchair, where she stood up, and after lifting the nozzle the pump was authorised by the attendant. It was later established that the attendant had not had a clear view of the pump, as there was a large 4x4 vehicle at the pump in front of where the woman was. He had not established whether she had a suitable fuel can to fill, or was about to fill a vehicle. Unfortunately there were no working CCTV cameras covering the forecourt, only dummy ones, so no tape was available showing the incident.
Once the pump was authorised, the woman proceeded to douse herself in petrol, but was spotted by another member of staff out on the forecourt assisting another customer. He shouted for the attendant to close off the pumps, and started to clear other customers from the forecourt. The woman threatened to set light to herself, but did not do so immediately. The Fire Brigade and Police had been called, and arrived quickly from their stations about 300 yards away!
By this time, the woman had moved away from the pumps, towards the back of the forecourt. At this point, some six metres from the nearest pump, she flicked the lighter, and was engulfed in flames. She was quickly jumped on by a waiting firefighter with a fire blanket, and the flames doused. She was taken to the local hospital, from where she was transferred to the East Grinstead Burns Unit. She was treated there for about four weeks, but was found to have suffered only 20% burns to her face, arms and body. She was extremely lucky not to have suffered worse burns.
APolice investigation established that the woman was an outpatient at the local psychiatric unit, and had previously injured herself in an attempted suicide, hence her wheelchair.
The attendant gave a statement to the Police, and we interviewed the Forecourt Manager about the training and experience of the attendant. The company (part of a national chain of car dealerships) was found to have adequate systems in place, and the attendant was suitably experienced in petrol retailing.
After some consideration, it was decided that we would not persue any legal action, as the incident was of a type that could not reasonably be foreseen, and the circumstances of the authorisation of the pump were a matter that is a daily occurrence on petrol forecourts, whether or not the practice is seen as wholly acceptable. Clearly the incident has shaken the staff and management of this site, and they have implemented refresher training and reviewed their operating procedures.
This incident raises the profile of campaigns such as those carried out in Suffolk and Milton Keynes last year, where officers took apparently unapproved cans to petrol sites and had pumps authorised for use at a surprisingly high number of the sites. A similar campaign has recently been carried out in West Kent, where nine out of sixteen premises authorised the dispensing of petrol into a plastic bag! No fuel was dispensed by the officers, but this only serves to support the findings of officers in various parts of the country. This is an industry-wide problem, which probably comes down to staff awareness and other pressures on their time and concentration.
Dangerous Fireworks
By John Brooks, Essex Trading Standards
In January 2003, 485Kg of shop goods fireworks which were being incorrectly stored at the rear of a Brentwood High Street newsagents shop, were seized by officers of Essex Trading Standards. The occupier of the premises, Mr. N. Vallabhji was subsequently fined £1000 for exceeding the permitted quantity on a mode B store, fined £500 for not keeping 292 Kg of shop goods fireworks in closed metal containers. £1000 costs and the Court also ordered that the fireworks be forfeited for destruction.
On 16th January 2004, the fireworks were destroyed under controlled conditions. The following photograph shows the destruction of the fireworks and in within seconds of ignition. Astark warning to all who store fireworks.
One can only imagine what it would have been like should these fireworks have ignited within a premises or vehicle.
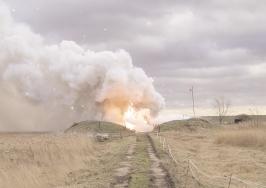
Articles Dangerous Substances and Explosive Atmospheres Regulations 2002 and the Implications for Service Station Operators
(Reprint of a powerpoint presentation to the North West branch of the APEA) By John Hazeldean, HM Principal Specialist Inspector, Flammable Liquids Section, HSE, Bootle
Aims of presentation
1.To explain the background to the Dangerous Substances and Explosive Atmospheres Regulations (DSEAR)
2.To detail the requirements of DSEAR
3.To discuss how DSEAR applies to Petrol Filling Stations and fits in with other relevant H&S legislation
Relevant European Directives covering F &E Risks
Directive
Atex Equipment (94/9/EC) Title
Equipment &protective Systems intended for use in potentially explosive atmospheres Required Implementation
July 2003 (Voluntary March 1996)
Atex User 137 (99/92/EC)
Chemical Agents Directive (98/24/EC) Minimum Requirements for improving the Safety & Health of Workers Potentially at Risk from Explosive Atmospheres
Protection of the Health & Safety of Workers from the Risks related to Chemical agents at Work July 2003
May 2001(Actual Dec 2002)
Implementation of the Directives
CAD and ATEX (137)
COSHH Amendments
CAD (Health)
Asbestos Lead DSEAR
CAD (Safety) and ATEX (137)
Repeal old legislation
Requirements of DSEAR
To ensure that the risks from Dangerous Substances are either eliminated or reduced SO FAR AS IS REASONABLY PRACTICABLE
Framework of DSEAR (Main Principles)
• Assess the risks of work activities involving DSs
• Eliminate or reduce risks sfairp • Classify places where explosive atmospheres may occur into zones
• Provide information, instruction and training
• Provide systems, equipment and procedures for emergencies
General Guidance on DSEAR
HSE BOOKS L138
Scope of DSEAR (Reg. 2, 3 & 4)
• Dangerous substances include: - Materials classified under CHIP (flammable, highly flammable, explosive etc) - Substances because of their properties and the way they are or used create a F&E risk - Dusts that could form explosive atmospheres
• Applies to all workplaces (some ATEX related exemptions)
• Covers risks to employees, self-employed, contractors, visitors and the public
Summary of the Regulations
• Reg. 5 Requirement for a suitable and sufficient assessment of the fire and explosion risks arising from dangerous substances. - Extension of MHSWArisk assessment
• Reg. 6 Apply safety measures to eliminate or reduce risks sfairp. - Includes control and mitigation measures
• Reg. 7 Specific requirements where explosive atmospheres may be present, e.g. - Hazardous Area Classification - Specification of equipment and protective systems for use in zoned areas - Verification
• Reg. 8 Systems and procedures to deal with accidents, incidents or emergencies
• Reg. 9 Provide employees with information, instruction and training
• Reg 10. Identify the contents of containers, tanks and pipes
• Reg 11. Duty of co-ordination between employers of explosion protection measures
Repeals /Revocation arising from DSEAR
• Factories Act Section 31
• HFLand LPG Regs 1972
• Some Petrol legislation
• Sector specific legislation - Shipbuilding - Harbours - Magnesium Grinding Regs - Testing of aircraft engines - Celluloid film
Enforcement of DSEAR
• HSE and Local Authorities as per normal arrangements, but:
• Petroleum Licensing Authorities for all workplace (retail and non-retail) petrol dispensing - Plus other automotive fuels dispensed at PFS
• Fire Authorities for general fire precaution aspects
5 Step model for Risk Assessment
Step 1 Identify fire and explosion hazards
Step 2 Consider who could be affected
Step 3 Evaluate the risks
Step 4 Record findings and action taken
Step 5 Keep assessment under review • Gather information about the site and its surroundings.
Consult others on possible hazards.
• Take a fresh look at your site, how it operates, its surroundings and the age, make and type of equipment installed.
• Look for areas where petrol vapour may accumulate - ie. Hazardous Area Classification
• Adopt a systematic approach by considering the different activities carried out on the site. - ie. Deliveries, storage, dispensers, maintenance
Step 2 - Consider what could go wrong and who may be harmed
• For each activity decide how petrol could escape.
• Consider the amount of petrol that could be spilt or leaked and where it might go.
• Look for possible sources of ignition.
• Consider what could go wrong. Ask 'What if ?'
• Take account of human error and the fact that people do not always follow instructions.
• List your findings and the measures that are already in place to deal with the hazard.
Step 3 - Evaluate the findings and decide whether further precautions are necessary
• Have you done all the law requires? • Consider the requirements of Reg 6. and ACoPs • Compare your facilities against the 'yardstick' of good practice ie. guidance and accepted industry standards • Assess whether you have done enough or whether more should be done: - Have you got rid of the hazard altogether - If not, how can you control the risks so harm is unlikely
Step 4 - Record the Findings
• Must record the significant findings if you have 5 or more employees. The record should detail: - Hazards which pose a serious risk to workers or the public if something goes wrong. - Existing control measures & the extent to which they control the risk. - Any deviations from good practice and the details of any alternative control measures. - Hazardous area zoning diagrams
• Good practice to review at regular intervals, but also
• If you suspect the assessment is no longer valid. ie following an incident or near miss; or
• When new equipment is installed; or
• if changes to the site layout; or
• if changes in the use of adjacent premises.
Further Advice on Risk Assessment
• Petrol Filling Stations Guidance on Managing the Risks of
Fire & Explosion, by West Yorkshire Fire Service, www.westyorksfire.gov.uk
Control Measures specified in Reg 6
• Preventative Measures (in priority order) - Reduce quantity of DS to a minimum - Avoid or minimise release of a DS - Control any release at source - Prevent formation of Explosive Atmospheres - Containing any releases of DS - Avoid ignition sources - Avoid adverse conditions - Segregate incompatible materials
• Mitigation Measures - Reduce number of employees exposed - Avoid propagation of fires or explosions - Provide explosion pressure relief - Provide explosion suppression - Provide pressure resistant plant - Provide personal protective equipment
Schedule 1 - General Safety Measures
• Reg 6(8) requires where appropriate - Workplaces to be designed, constructed and maintained to reduce risks. - Work processes to be designed, constructed,
assembled, used and maintained to reduce risks. - Appropriate systems of work, including written instructions and permit-to-work procedures.
So Far as is Reasonably Practicable
• DSEAR requires risks to be controlled SFAIRP(but not in
CAD)
• Allows factors such as time, trouble and cost to be set against the risk. If the balance between these factors and the risk is grossly disproportionate then additional measures would not be reasonably practicable.
• Whether an individual employer can or cannot afford the measures is irrelevant.
• Burden of proving SFAIRPlies upon the employer.
ACoPs and Guidance supporting DSEAR
L133 L134 L135
L136
Status of ACoPs
L137
• Special legal status " If you follow the advice you will be doing enough to comply with the law. You may use alternative methods… but if you are prosecuted you will need to show that you have complied with the law in some other way or a court will find you at fault."
Status of Guidance
• "Following guidance is not compulsory & you are free to take other action. But if you follow the guidance you will normally be doing enough to comply with the law. Inspectors seek to secure compliance with the law and may refer to this guidance as illustrating good practice."
• General ACoP - Provides background & interpretation but 90 pages long
• Tanker ACoP - Relevant to all sites
• Storage ACoP - Includes controls for leak prevention, separation, ignition sources & security
• Design ACoP - Includes controls for containment, location, mitigation, redundant plant
• Maintenance ACoP - Relevant to all contractors and those carrying out or overseeing maintenance or repair work
Verification (Reg 7)
• What parts of the site require verification? Those parts that need to be considered are where explosive atmospheres may occur (ie designated as hazardous areas). It will also be necessary to take into account any equipment or facilities that may give rise to hazardous areas or are needed to limit their extent.
• When should verification be carried out? Verification should be carried out before a site is put into use, ie. during commissioning, but it will also be necessary to verify that any significant changes or any new equipment will not give rise to an unacceptable explosion risk. A like-for-like replacement or repair, however, should not require further verification.
Verification Checks will include
• Inspection of records to show tanks & pipe work are leak tight.
• Hazardous area drawings have been prepared and equipment is the correct type & category for the zone.
• Confirmation that equipment in the hazardous areas has been installed correctly and has been tested.
• All warning and information notices are in place.
• All electrical and other ducts from hazardous areas are properly sealed.
• Vapour emission control systems have been tested and operate correctly.
• Gauging and leak detection systems operate correctly. Verification - Competent Person
• The site operator has the duty to ensure that a competent person carries out the verification.
• The site operator may be the competent person but he may need to enlist the help of others such as the site designer, the installer of the equipment, test companies or an independent person or organisation.
• The person or persons involved must have practical & theoretical knowledge of the fire & explosion hazards arising at petrol filling stations, which may have been obtained, from experience and/or professional training.
Concluding Comments
• Goal setting but comprehensive legislation that provides effective controls for PFS.
• Places duty for controlling risks firmly with the employer.
• Risk assessment important as it requires site operator to identify and understand the hazards and take into account any site specific issues.
• Can sit along side Petroleum Licensing but Licence
Conditions could be challenged with a site specific risk assessment.
Further Information
• DSEAR 2002 www.legislation.hmso.gov.uk/si/si2002/20022776.htm
• ACOPs and guidance (HSG146, L133 to L138) - Available from HSEBooks or HSEDirect
• WYFS Web page - www.westyorksfire.gov.uk
• PETELCirculars www.hse.gov.uk/lau/lacs/m_s.htm#65
• APEA/IPGuidance
• UKPIA 9 Kingsway, London WC2 B6XF (price £15)
• Petrol (Technical) john.hazeldean@hse.gov.gsi.uk
• Petrol (Policy) stewart.mcewen@hse.gov.gsi.uk
• Guidance for the Design, Construction and Maintenance of
Petrol Filling Stations - www.apea.org.uk