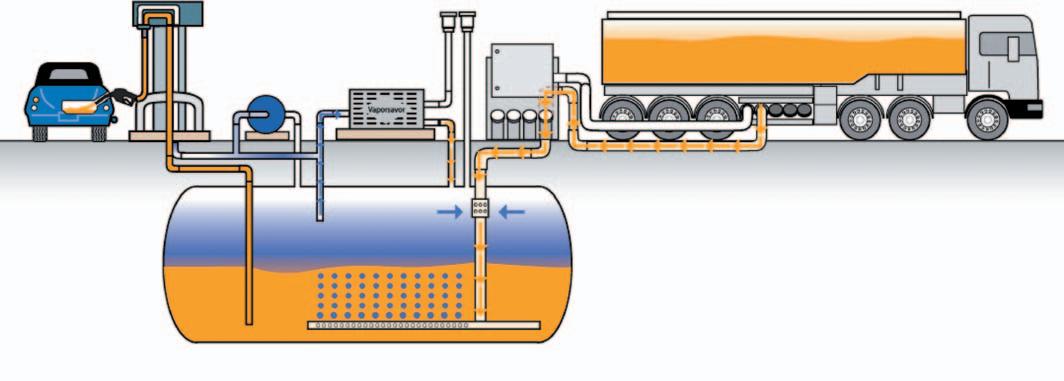
17 minute read
US Experiences with Biofuels
sold onto the customer) and it is the efficiency of this system that has made it possible to bring higher levels of vapour management onto the forecourt, with increasing levels of environmental protection and most importantly, hugely improved levels of profitability for the site operator.
Total Vapour Solution (TVS)
Advertisement
All elements are now in place to make it possible to manage wet stock reconciliation to much higher levels of accuracy. It also allows any shortages incurred during deliveries to be flagged up more rapidly as well as more importantly, leak detection.
Collecting and managing the vapour from fuel deliveries means that there is minimal return to the delivery tanker, whilst the vapour is being controlled within the storage tanks and retained by the retailer. The larger the ullage space after a delivery the more vapour there is stored to be processed. It is therefore easier to quantify product losses or variations, in tens of litres as opposed to hundreds or thousands of litres.
With all the vapour now being processed within the tank farm it is possible to calculate wet stock losses far more definitively, as there is much more information available with Total Vapour Recovery and Processing.
• The delivery of vapour/air from the dispenser nozzle is a tested and legislatively set measurement of efficiency of between 95 – 105 %.
• The closing stock recorded from the tank gauges will include vapour returned to the tank farm as processed liquid and this can be calculated using the following conversion rate of vapour into liquid.
• (667 litres of vapour per litre of product dispensed (1.5 litres of liquid /1,000 litres of vapour)
With the above conversion factor it is possible to calculate and allocate losses, so we have to give consideration to the indirect delivery of product via the dispensers.
D u r i n g n o r m a l operations the processor will be working during the delivery and after to process the retained vapour from the delivery. Once this has b e e n completed it will operate as and when the pressure rises to 3 mbar and switches off at 2mbar. Therefore, a total time of two hours daily with a delivery or with no deliveries thirty minutes daily. Seasonal variations have to be taken into account but we believe this will give a life of fifteen years before major maintenance need be considered. With larger sales sites of seventeen million litres upwards we recommend two processors to achieve the best efficiency. With this reliability it is possible for us to offer the client a three year warranty on all the equipment.
The running costs are very dependent on the clients own situation but these have been calculated to be between £0.65 to £0.95 per day depending upon the number of deliveries. There are three and single phase versions all with ATEX approvals. We try to utilise existing pipe work, so as to avoid disturbance on the forecourt, but some installations do offer higher processing efficiencies due to the sites pipe work.
These performances have been achieved and recorded, with independent stock control companies, and have we little reason to believe that it will not be possible on every site subject to the sites infra-structure.
In the British Isles and Southern Ireland the Total Vapour Solution (TVS) is being marketed by Petroman Environmental Services Ltd based in Stoke on Trent, Staffordshire. Worldwide sales are being handled by OPW from their offices in Europe but should you require any further information please contact Petroman on the details below: -
Unit 5 Sneyd Green Business Park, Stoke-on-Trent, Staffordshire. ST6 2NP Tel: +44 (0)1782 200750 Fax: +44 (0)1782 200755 Website: www.petroman.ltd.uk Email: info@petroman.ltd.uk
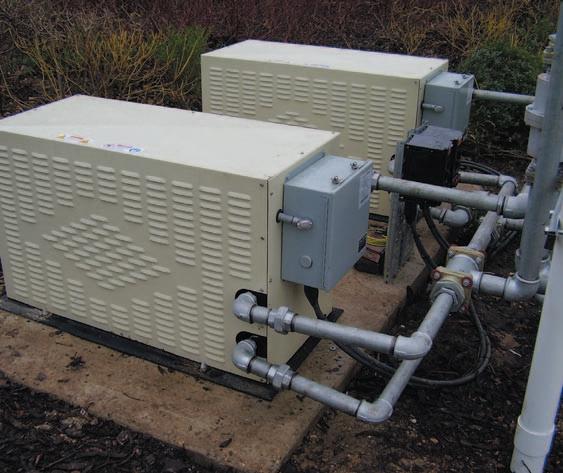
By Jamie Thompson
The first container used to both store and distribute fuel was the 2 gallon can. The oil industry imported barrels of fuel from the US into the docks where the fuel was then transferred into these cans and then distributed to the “filling stations” which were in fact petrol cans stored inside brick stores. In London, (the first city in the UK to import this fuel) most of the brick store “filling stations” were in the many Mews premises where the horses were still being stabled. The early cars had spare cans strapped to the running boards as a venture far from the capital would not guarantee the driver seeing another filling station.
Eventually the industry realised that the laborious filling and emptying of 2 gallon cans was not viable and the move to storing larger amounts of fuel underground was made.
One company in London that designed and provided such a service in 1914 was F. Braby and Co Ltd of Euston. They offered a storage tank and dispensing system with the added incentive that it had been “examined and approved of by the London County Council”. The tank was steel, rectangular by design and riveted. The filling point had a filter in it, it had a contents gauge, a vent and a hand pump and measuring cylinder to allow filling of the car. The tank was surrounded by concrete as early as that date.
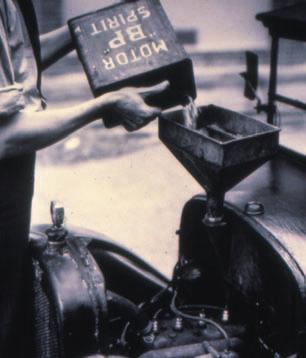
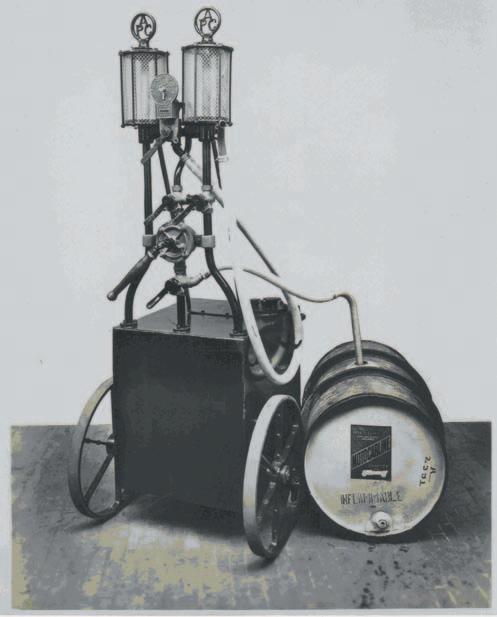
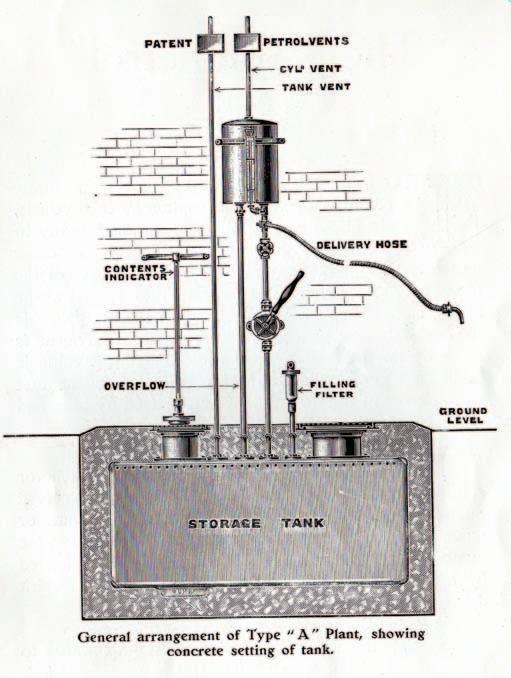
Early deliveries of fuel to the storage tank were via horse drawn road tankers and later by motorised tankers.
1900 to 1950
The very early sites had small storage tanks: 250, 500 or 750 gallons and as the larger sites were developed there was a move towards 1000 to 2000 gallon tanks. These sites were then redeveloped as the site sales rose and tanks from 4000 to 6000 gallons were more common. The tanks were generally steel construction, cylindrical in shape with dished heads, and were installed in puddled clay, sand vaults or concrete in London. In 1957 the first guidance of how sites were constructed was issued by the Home Office and it included underground tank and pipe advice.
1960 to 1980
During this period the tanks became much larger and many of the sites were redeveloped to take into account the demand for self service. Tanks of 10,000 to 12,000 gallon capacity were often used. Many tanks were built with multi-compartments to accommodate the blending of fuel which was going on at that time. The steel tanks were manufactured to BS 2594, were all single wall and were painted with a black bitumastic paint. The tanks were really poor quality compared to tanks manufactured today and built down to a price.
In the late 1960’s the first GRP tanks were installed in the UK. After some early problems the first successful installation was operated by BP in West London from 1970 to 1992 when the tanks were eventually replaced.
1980 to 2000
This period proved to be the one with the greatest change for storage tanks.
The main reason for this was that tanks and pipes which had been in the ground for some time started to leak, and although concrete was placed around the tanks to try and afford some protection from corrosion, many leaking tanks and lines disproved this theory.
In the USA major oil companies were getting sued for leaking product into drinking water and the word “environment” was mentioned in the
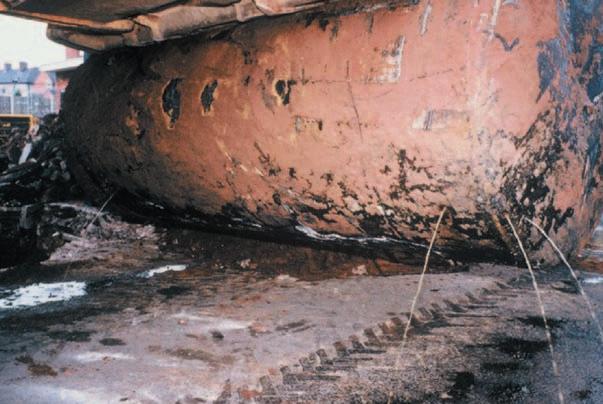
had a much improved quality about it from steel quality and thickness, quality weld, surface preparation and coating. We went a l m o s t overnight to a quality tank with built in safety which
context of petroleum storage. In London during this period the petroleum inspectorate would have dealt with 120 to 130 leaks of petrol a year into the ground and on five occasions petrol leaked into the underground railway network: a serious problem.
It was a case of “out of sight - out of mind” as the buried equipment was not considered by the marketers as important as that equipment which could be seen above ground.
GRP tanks also became an option and while there were some successful installations the number of problems that occurred during and after installation caused the industry in the UK and indeed Europe to lose confidence in the product and although still permitted by regulators there have been no GRP tanks installed in the UK
on retail sites for over 11 years.
The biggest change came about due to work on the European standard for underground tanks which developed the double wall steel tank standard. It was clear that there was a need for a new approach to petrol storage which would suit the next century with both safety and the environment in mind.
The new standard (BS EN 12285-1) years the development of a standard in the USA for tanks providing a fire resistant surround to the tank has been successfully used in the US and more recently in the UK.
The standard the tanks are protected to is UL 2085 which requires the tanks to go through a series of fire tests to ensure integrity and make certain they will not explode. These can be either 2 or 4 hr fire resisting. The main users of such storage tanks have been the utilities, golf clubs or car manufacturers but due to some environmental concerns these tanks are not being considered for retail sites.
Pipework
When the first petrol stations were built with underground pipe it was steel with screwed joints and as time progressed the steel was galvanised to add protection.
Like tanks the steel pipe work was also covered by concrete.
What we appeared to have overlooked during this process was that by attaching galvanised steel pipe to a steel tank we were in fact providing the tanks unintentionally with a sacrificial anode and the galvanised pipe worked
suited both the regulators and the site operators.
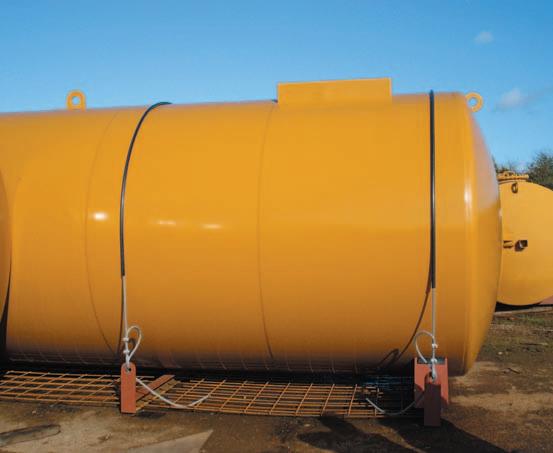
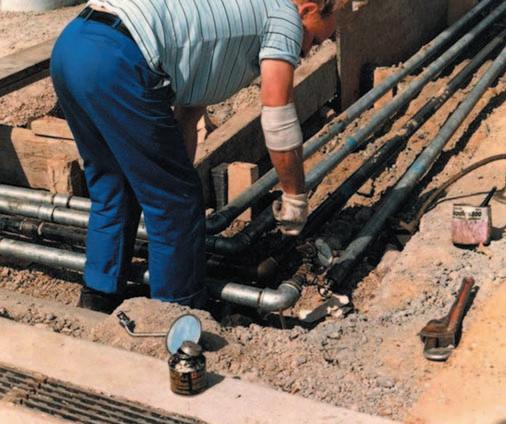
The London Fire Brigade in 1990 decided they would no longer allow single wall tanks for storage of fuel and in future would require all storage to be double wall. These tanks had leak detection covering both skins of the tank to ensure product would no longer enter the environment as once the alarm sounded fuel could be removed from the tank. It was soon adopted by all petroleum authorities, the Environment A g e n c y , industry and is of course included in the
Blue Book.
The above ground storage of petrol has usually been restricted to special bunded areas inside compounds with distance being the main criteria for safety.
In more recent

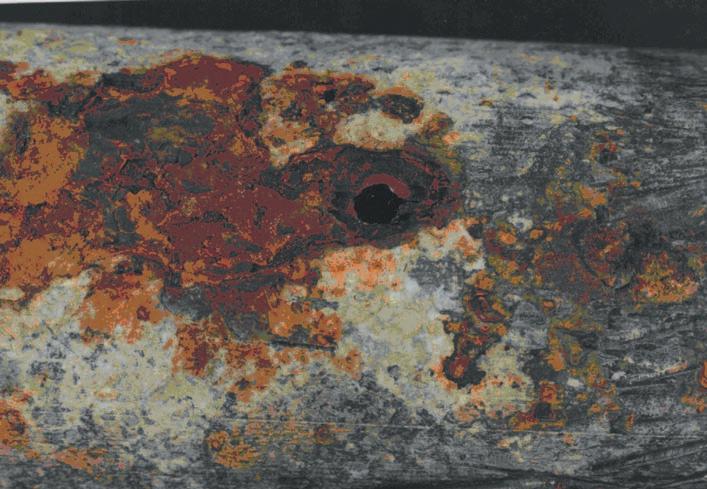
problems of corroding metallic pipes underground and were using Polyethylene in high pressure gas and water mains.
The oil industry first used GRP pipe as an option but eventually as other types became available it is no longer used in Europe
A number of options followed and while some US manufactured flexible pipes were used by some operators, failures of those piping products across the Atlantic caused some doubts and the general trend was towards using the High Density Polyethylene Pipe which is now the industry norm in Europe and indeed many parts of the world.
The use of double wall pipe has also increased with its use mandatory on pressure lines. The operators can also see the benefits of providing such equipment which offers excellent protection at low cost.
What the change has meant is that as sites have been built and pipes have been replaced the number of leaks dropped drastically - the buried part of the plastic pipe will not corrode and steel is now only used above ground or in manhole chambers where it can be regularly inspected.
The changes that started to occur 20 years ago in this section of the industry have been for the better and safety and environmental protection of groundwater has been vastly improved by using these tanks and pipes.
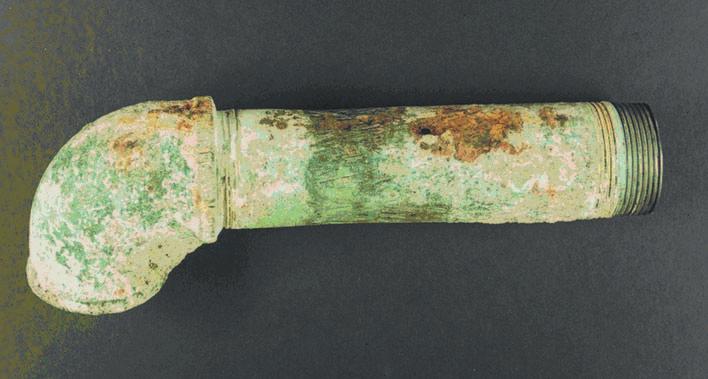
as such and therefore we had lots of leaks on lines, in fact over 75% of the leaks from petrol stations at that time came from lines. While underground pipe work had been the same for over 70 years it too proved a time to change.
The installation of steel pipe took some time; apart from the handling of this heavy pipe the threads were cut on site, a jointing compound mixed up and the joints then set. On completion the petroleum inspector would observe the air pressure and soapy water test over the joints. In one period in the 1980’s the jointing compound failed on a number of newly constructed sites. Once fuel ran through them they had to be dug up and the pipe work replaced.
On looking back we can see that the water and gas industry had already recognised
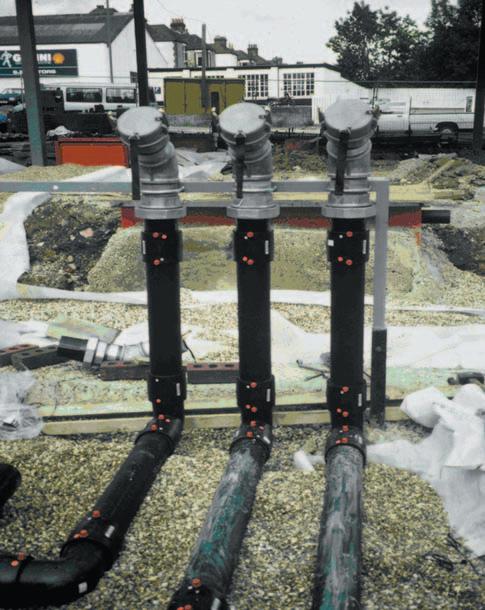
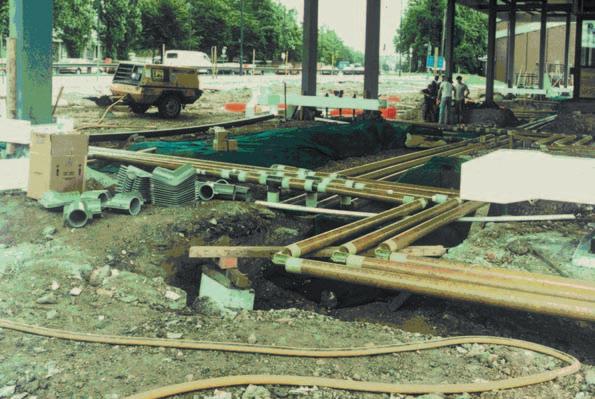
Eastern
APEA Eastern Branch Meeting and AGM held 10th March 2009 at Duxford
The APEA eastern branch met at Duxford . Duxford has one of the finest collections of aircrafts as well as restoring historical aircraft. There is a fine collection of tanks, military vehicles and naval exhibits. This famous heritage site began as an airfield in the First World War and also played a vital role in the Second World War. The film “The Battle of Britain” was also shot on location there and the story is that more damage was caused to the place during the making of the film than during the war.
Our meeting was based on a new and fresh format designed by our active Committee who meet regularly. There were several short presentations of 1015 minutes giving speakers the opportunity to talk about their equipment and technologies with time for question and answers. The short presentations were intended to reflect the busy and demanding times we live in and also our continuous endeavour to keep the meetings interesting and relevant. It also recognises how much time is often dedicated to the preparation of these events. More than 50 people attended and audience participation was lively. It was also a pleasure for us to see and welcome members from our friends of the Southern branch too. We hope you will all come again.
The following people presented for their companies:-
Cookson & Zinn, Geoff Lee talked about the features and benefits of the “Base frame Storage Tank” with prefitted cradle and hold down straps. This was their APEA award winning product. containment system.
Flammer Gmbh, Mirjam Maiberger expanded on the perceived issue of disadvantage of an orifice plate. Now there is a new solution available. Before opening the storage tank, the tanker driver or station manager can release the tank pressure by a hand valve through a bypass. BS EN 12874 is a new standard for flame arresters and has superseded BS 7244.
Flame arresters on forecourts have to be in accordance to new BS EN 12874.
Gilbarco GVR Mike Jennings talked about Globalisation on standards. The
complexity and wide range of standards and approvals and the interpretation of these requires the mind of an expert and Mike did not disappoint.
Elaflex Ltd, A n t o n Martiniussen talked about the new ZVA Slimline 2 and vapour recovery nozzle and the considerations behind the features of this new family of ZVA nozzles to the market.
Risbridger’s Piers Gibson, talked about the RIS-FLANGE modular tank lid system, outlining the key features, benefits, and savings, always good to se a quality British equipment manufacturer.
Hytek’s Adrian Holyomes, gave a short history about Hytek and his role in the business and the range of products they supply to the industry, from the
London Fire Brigade LFEPA Jean Fincken talked about the role of the Petroleum Officer and gave an “overview” of what a petroleum officer does.
PFS fueltec Trevor Mason talked about their production of a Response unit to handle road tanker spill incidents. This seem to be an essential piece of equipment in the event of a serious incident for any authority. These can be towed behind a trailer.
Milton Keynes CC Brian Baker A regulators update: Brian talked about Environment agency Ground water policy, the myth of Stage II VR permits, Above ground storage tanks, Fire Safety order, Impact of Ethanol and guidance issue by Energy Institute. Brians updates are a must for all local authorities. Comprehensive as always. The summarised details are at the end
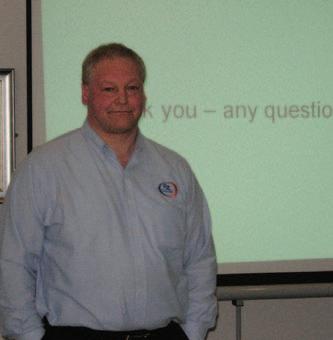
Geoff Lee Alex and John Boudry
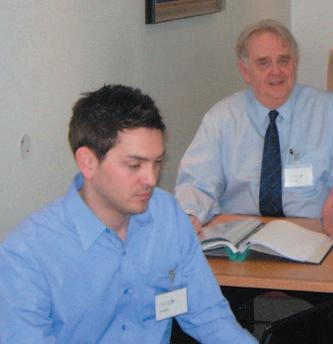
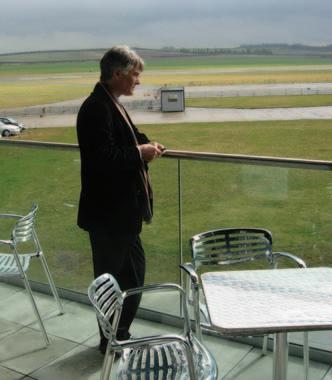
Mike Jennings Anton Martiniussen
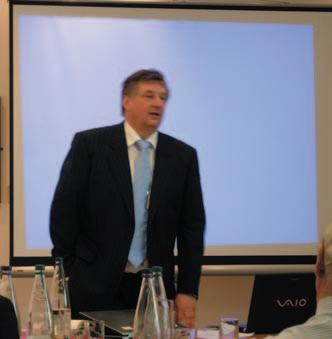
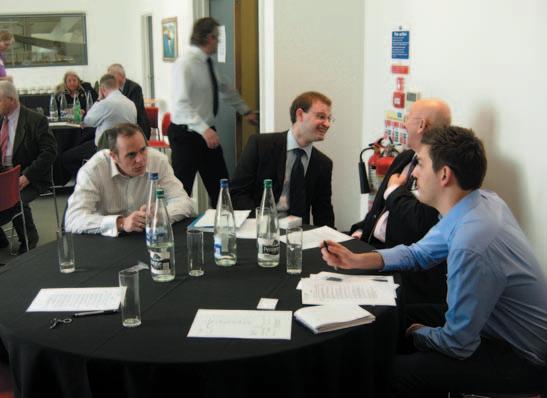
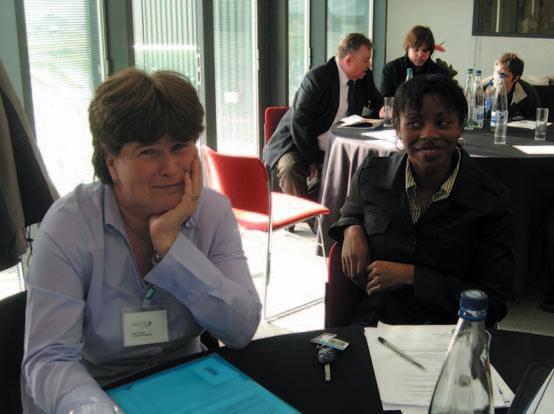
Jean and Audrie
of this note A most sincere thank you goes to all our speakers who made it such an excellent venue.
In line with the requirements of our AGM the following were elected for the eastern branch:
Chairman John Boudry
Vice Chairman Jacquie Holt
Secretary & Treasurer Anton Martiniussen
Committee member John Brooks
Committee member Jamie Thompson
Committee member Alex Boudry
Committee member Jean Fincken
Branch Rep Adrian Holyomes
Auditor Mike Alston
The accounts have been duly audited and approved by members. I would like to thank all those that served in the past year and for the interest and contribution. We would also like to thank Hytek for their hospitality to us during the past year.
Brian Bakers update
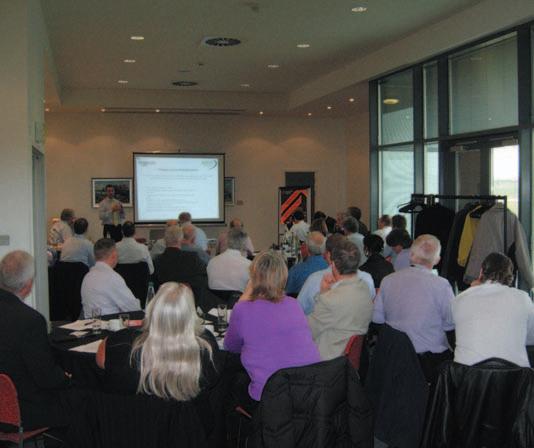
Audience
1.Environmental Damages Act 2009
Coming into effect April 2009 and enforced by the Local Authority that will cause more higher potential fines for pollution
2.Health and Safety Offences Act 2008
Coming into effect later in the year that sees the levels of Fines increase for certain contraventions of health and safety law
3.Review of Fire Precautions Design Guides
Many of the usual fire design guidance is being revoked inn favour of a single guidance publication known as BS9999 that is effective from April 2009 and the former BS588 series is being withdrawn
4.DEFRA Guidance on Stage 2
Vapour Recovery
This has now been published on the
DEFRA Web Site www.defra.gov.uk/vapourrecovery
The Guidance is some 169 pages long whilst the Application Forms are at the back of Part C guidance a separate document. Both downloads are free
5.Environment Agency’s New
Groundwater Policy
Most controversial guidance this published for many years where the
Agency are going to insist on new tanks being above ground due to the risk of groundwater pollution. This will cause major disruption and design issue for all Operators. Despite request from UKPIA the Agency remain adamant about its new policy being followed and it is expected there will be a lot of challenges to it.
6. A b o v e Ground Tanks –Fire Rating
As there is likely to be an increase in the installation of above ground storage tanks, account needs to be taken that the British Standard BS EN 1285 Part 2 2004 does not specify a standard fire resistance rating whilst the American comparable standard Underwriters Laboratories 2085 does stipulate 4 hours. This becomes an issue as the surrounding risk should be assessed from the prospect of direct heat impinging on the surface of an above ground tank wall and Regulator’s are encouraged to pursue such a rating before Approving its location.
7.Energy Institute Guidance on Bio
Fuels E5 and B5
This was published recently and contains useful advise on preplanning and prior switching to a bio grade fuel and what the operator must do before hand. Brian is looking at doing an article for the next Bulletin issue on this subject and guidance.
8.Blue Book Update
Gareth Bourhill (APEA Chairman) and Jamie Thompson (Technical
Committee Chairman) have made the initial approached to the Energy
Institute regarding the revisions to the
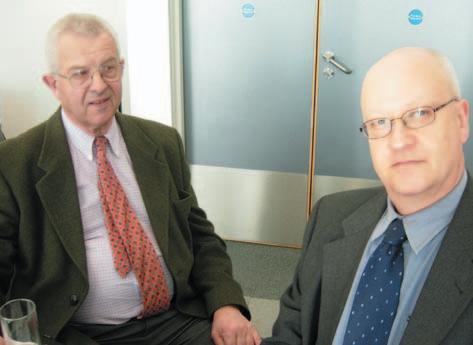