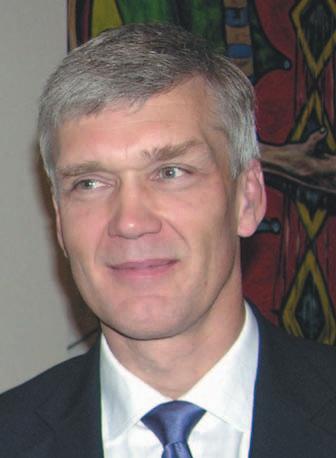
20 minute read
Press Releases
By Brian Baker
As part of the Interviews series we turn north to Scotland and an area that has a lot of rural area bringing their own peculiar problems and on this occasion I was able to track down Gordon Robb who is the Petroleum Officer for Highland Council. I was able to put a few questions to him in his role.
Advertisement
Gordon; It is good to speak and we are very pleased to see you and your colleagues from Scotland at the 2008 APEA Conference. Was this the first time you have been able to get to the Annual Conference?
Hi Brian, I have been lucky enough to get to two previous events, but I agree that it was excellent to see so many of my colleagues from the Scottish Branch there in Telford, thanks of course to the support we received from the APEA executive.
How long have you been in your current role as a Petroleum Officer? Have you always worked for a Local Authority?
Although having had some peripheral involvement in licensing enforcement from my early days working first as a trainee and then as a Trading Standards Officer in Glasgow and the West of Scotland, I only became fully active in my Petroleum Officer role in about 1990 while working in Highland. It’s also at this time I was dropped in at the deep end with explosives storage, so with everything that was going on in these areas in the early 90’s, it was shall we say “interesting”.
My career, with only a short break in the 1980’s, when I was in the police, has been wholly within Trading Standards in local government.
Whilst my knowledge of Scotland is poor tell me what your “patch” is like? How many licensed sites have you?
Currently we have just under 100 active retail filling stations, and something like 30 non-retail sites including a number of farms and estates.
I guess you must travel long distances to get round to inspect your sites. What is the furthest or remotest site?
I think the retail filling station at Uig on the north-west coast of the Isle of Skye is probably the farthest away at about 130 miles and over 3 hours driving, but with a land area equal in size to Belgium and still some single track roads, there are quite a few that are over a hundred miles and/or 2 hours plus driving time from Inverness where I’m based.
Travelling through some of the best scenery in Britain is of course a bonus, but sometimes when the roads are full of tourists and you are trying to get home it doesn’t always feel that way.
What would you say has been the biggest change you have seen in the last 10 years?
Like everywhere else in the UK we have seen the continued decrease in site numbers, but the arrival of the major supermarkets into some of the council’s more rural areas over the last 10 years has had a huge impact. There has been a rise in the closure rate of what in some cases were our better sites and those sites that stay open often struggle to maintain acceptable standards in the face of increased competition. This makes it all the harder to regulate these businesses and at the same time to recognise their importance to the sustainability of rural communities.
Do you manage to get to the Scottish Branch Meetings of the APEA? What particular subjects interest you?
I try to get there when I can, but not as often as I would like. Driven by the problems that are particularly relevant to small rural sites, I take a keen interest in issues such as aboveground storage, unattended self-service solutions (and up here that doesn’t APEA tel/fax 0845 603 5507
always mean supermarket run sites); tank relining; electrical maintenance and wetstock control.
Have you got any unusual sites? Do you have many farms that have a licensed installation?
Other than being old and remote, (or maybe that’s me I’m talking about) most of the permanent sites are pretty standard, but we have had had some temporary installations over the years which were interesting.
The refuelling installation for last year’s Round Britain Power Boat Race, which others will no doubt be aware of was one of the most recent, but I can also remember another temporary aboveground installation (see photo), put together by Esso up at Skibo castle back in the 1990’s for Jaguar’s launch of a new model that certainly caused a bit of head scratching before we could agree on an acceptable solution.
What is your pet hate? What irritates you the most when doing your job as a Petroleum Officer?
Probably being presented with electrical certificates for filling stations which don’t address the hazardous area requirements, from contractors who should know better. I’ll say no more!
When was the last time a new filling station was built in your area?
The last new retail development was in 2005 in Wick, but there are at least two if not three new supermarket sites currently being planned.
Are you a lone PO or is the role covered by colleagues, whom I presume are Trading Standards Officers?
No thank goodness Brian. My role as Principal Trading Standards Officer involves amongst other things, leading a team of 8 officers, 4 of whom have within their wider remit some responsibility for Petroleum. The geography in Highland does not lend itself to single topic specialisation.
Ok, what is the funniest moment you have had as a PO?
I’ll deviate just a little from your question here Brian, if you’ll forgive me as it’s probably more on the explosives side of things that has produced the situations that have made me, or
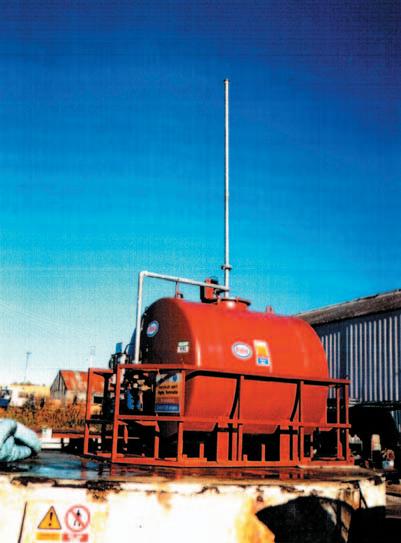
Esso Jaguar Skibo Aboveground filling station sometimes others, laugh.
The incident that comes to mind was being presented with a ferry bill, coincidentally by the prospective licensee, to take me and a police inspector in a small open boat in winter across a sea loch on the west coast to inspect a proposed explosives storage site.
It hadn’t been the most comfortable journey, given that the sleet was horizontal and the water distinctly choppy, but to be then confronted immediately prior to our return trip, by a bill which funnily enough exactly matched the licence fee caused me and certainly others subsequently, to chuckle somewhat.
Do you have any interests or hobbies when not batting for your Council?
When I get the chance, having recently completed converting an old steading and now only have what seems like an awful lot of stone walls to point and the bidding of the head gardener (my wife Lesley) to do, I like to play golf badly, ski, get out on my motorbike and the odd bit of scubadiving.
Where do you want to be in five years time?
Well Brian I’d certainly like to have finished the pointing, but apart from that I’d like to think that I have played my part in securing a viable filling station network in the Highlands, which with all the challenges being presented by the introduction of E85 into an aging infrastructure is at this stage not guaranteed.
Thanks for talking Gordon. I hope you can get to our Conference in Coventry this year. Maybe just maybe I may even come up to you if you can recommend a peaceful quiet location!
Are We Stabilising Our Market?
By Brian Baker
Having got my copy of the excellent publication entitled Retail Marketing Survey produced by the Energy Institute the numbers of Retail Petrol Forecourts saw an INCREASE of 8 sites in 2008, the first rise in numbers since 1997 but represents a mere 0.13% rise. The Oil Companies continue to dominate the market with 5,646 forecourts out of a total of 9,283 sites in the UK. The table reads as follows; (2007 figures in brackets)
Oil Companies Company No of sites Self Service Nozzles No’s
BP 1,200 (1,146) 1,198 9, 380 Texaco 1,061 (1,018) 1,040 7,289 Shell 932 (880) 932 6,819 Esso 872 (880) 872 7,417 Total 835 (855) 835 6,392 Jet 408 (408) 408 2,935 Murco 338 (342) 338 1,860
Total 5,646 (5,549) 5,623 42,542
Main Retailers Company (x18) No. of Sites Self Service Nozzle No’s
1,173 (1,131) 1,009 4,877
Supermarkets Company No. of Sites Self Service Nozzle No’s
Tesco 441 (428) 441 4,981 Morrison’s 288 (283) 288 3,025 Sainsbury’s 247 (246) 247 3,253 Asda 173 (170) 173 1,698 Others 66 (61) 63 377 Somerfield*(Co-op) 30 (35) 30 276 Waitrose 14 (14) 13 140
Total 1,259 (1,237) 1,255 13,750
Other Retailers Companies No of Sites Self Service Nozzle No’s
13 small businesses 128 (105) 114 384
GLOBAL-MSI plc is the European leader for the supply and installation of structures to the fuel station forecourt industry.
To take advantage of the strength of the Euro against Sterling, GLOBAL-MSI plc seeks a sales professional with a proven track record to develop this area of the business, meet Company sales objectives and expand on new opportunities that have emerged.
This is a varied senior sales role and will include dealing with Oil Companies, Forecourt Building Contractors, Design Consultants, Private ‘dealer’ Companies and Local Authorities.
The ideal candidate will have a thorough understanding of sales strategies and fluency in at least one other European language. In addition the right candidate would be highly motivated with excellent communication skills and able to present our leading product and organisation at management level within the industry. Experience in construction would be highly regarded.
Excellent salary and benefits are provided with this position. Interested candidates should forward their CV to:
GLOBAL-MSI plc, Cannon Lane, Tonbridge. Kent TN9 1PP For the attention of Martin Steggles Director & General Manager, Email: martin@global-msi.com
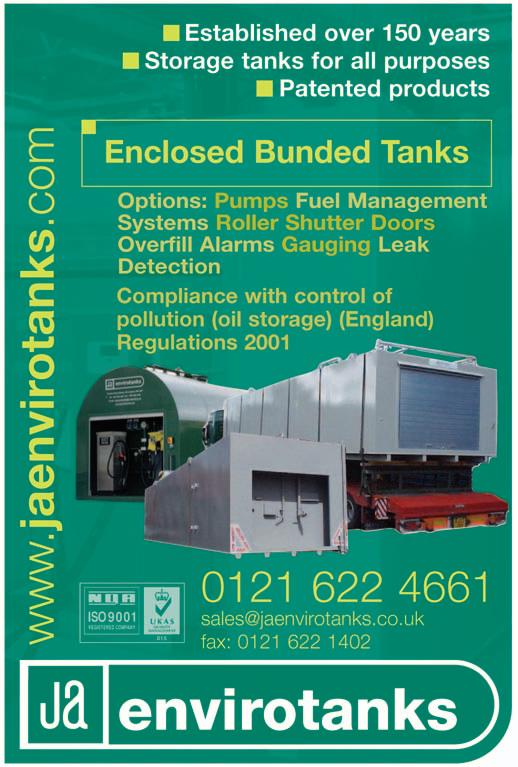
Stage 2 Vapour Recovery - Working safely on tanks and pipe work
By Andy Kennedy, UK Maintenance Manager, BPGlobal Alliance

Ullage pressure
BP has been installing sites with stage 2 vapour recovery since 2000. In the course of operating and maintaining these sites we were early identifiers of issues associated with the build up of pressure in ullage spaces. This usually manifested itself in vapour problems in access chambers and some problems when connecting the tanker vapour recovery hose which resulted in a national program of vapour checking and tank testing on stage 2 sites in 2005. Working with several specialists in their field, we found that vapour pressure could build up in tanks even when the stage 2 systems on the pumps were correctly calibrated and operating correctly.
Safety Concerns
Having noted the problem instructions were issued to all our contractors stating that they must presume all vessels and pipes to be under pressure unless it could be proved otherwise. Recent review with our contractors found there was very little consistency on how engineers on site were preparing for and managing vapour releases when working on tanks, vapour recovery and vent pipes with consequent gaps in safety method statements and risk assessments on clearance certificates.
We were also aware that this additional risk was not being covered in either the UKPIA training or in the inhouse training being given to contractor’s staff. When speaking to other companies and facility managers, they had similar concerns, but no clear answer to the problems.
Workshop
To try and get some consensus on how to reduce the risk when working on stage 2 sites, we organised a workshop at BP Pangbourne with a number of our key contractors and other expert and interested parties from the industry including lead Petroleum Officers, oil company representatives, facility management specialists and contractors. At this meeting the group discussed the safety issues and risks of managing vapour releases safely on a petroleum forecourt. Various options were discussed following presentations from several delegates including proposed methods, vent design
changes and how to carry out on site risk assessments.
The main points from the meeting captured below, covers the main actions agreed by those attending.
It was agreed that in general forecourt work practices have not taken into account the additional risks of pressurised spirit tank ullage spaces. This risk has increased due to the implementation of stage2 and vapours being returned to the tanks under pressure.
Releasing pressure at low level on the forecourt is not recommended due to the risk of ignition and health issues to workers on site. Method statements should identify the means of achieving dilution and dispersion of vapour and identify risks of vapour collection in low lying areas.
Where possible, systems should be checked for pressure readings of the ullage space and pipe work. If this is not possible the system must be approached as if it is under pressure.
Safety method statements supplied for this type of task must take into account how these checks will be made. They should also take into account the likely changes of hazardous areas and how this should be managed.
On site risk assessments must be carried out and specific attention paid to vapour releases and the likely hazardous areas. These risks and how they will be eliminated must be recorded on the clearance certificate. This should be done by walking round the site assessing the zones and the hazards.
It is recommended that a temporary vent is connected to a modified vapour recovery cap via a suitable hose and vented at high level using a temporary vent before work starts and during the work. This temporary vent must be fitted with a flame arrester.
The hazardous area around this temporary vent must be suitable to manage the vapour release safely. If this cannot be maintained then the site should be closed and suitable measures put in place.
The operation of Stage 2 vapour recovery systems needs to be suspended while works to tanks and connected pipework is carried out. This can be achieved by:
• switching off the stage 2 at the dispensers (generally a pump technician needs to be called out to do this)
• all spirit nozzles can be locked in (or isolated) before and during the work so they cannot operate.
• Site closure (Post meeting note: The output pressure of a stage 2 vapour pump can be up to 1.5bar.)
Gas monitors must be used to monitor the vapour levels at the point of venting and the workplace.
Any changes in the hazards or risk must be recorded and changes made to the clearance certificate.
On new installations, methods should be built in to safely vent the ullage space.
Additional training is required for people working on forecourts who may be affected by this type of activity.
Engineers should not release the ullage pressure via the vapour return point, by depressing the check valve in an open vapour return fitting. It has been found from this meeting that not all of these valves have a flame arrester fitted. The gauze installed in these fittings may only be a filter for collecting debris.
The risks associated with uncontrolled vapour release is increased when sites move to E5 due to flammability of ethanol vapours.
Future
The problems associated with working on service station fuel systems with excess vapour pressures affects everyone in the industry. It clearly makes sense to develop a common approach to the procedures to be followed and measures to be carried out by those working on tanks and pipes.
Total Oil have shared their safety notice on this issue and this has been used by the BP Global Alliance as the basis of the BP control measures document. Further work is needed by the various industry associations to develop common procedures and ensure these are uniformly applied at all facilities. Discussions have been initiated with the Energy Institute Service Station Panel, APEA, PEIMF and FEF and it is hoped these bodies can work together to pull together some consistent advice for contractors and operators.
BP’s Stage 2 control measure document is available through the APEA web site at http://www.apea.org.uk/
Design of future sites can be modified to reduce the risk with changes in the venting system and the planned revision of the Blue Book should incorporate these. For now it is up to all of us to ensure that we plan ahead to reduce or eliminate all risk from vapour releases and put in place the processes to ensure we do what we say we need to do.
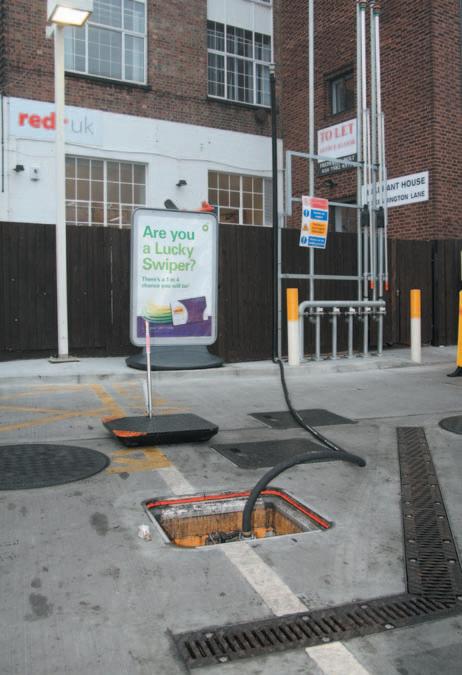
Temporary vent and modified cap courtesy of E&S Environmental
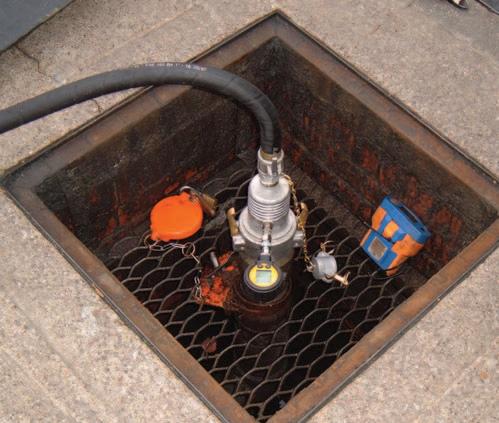
By Rodney Carter, Petroman Ltd
Total Vapour Solutions (Accounting for Stage 1B and Stage 2 combined with TVS)
We are now approaching the deadline of 31st December 2009 for sites that qualify to be fully operational Stage 2 Vapour Recovery systems on sites that qualify in the UK and heralding a new era of controls and safety. To fully understand what is happening, a step backwards is first required.
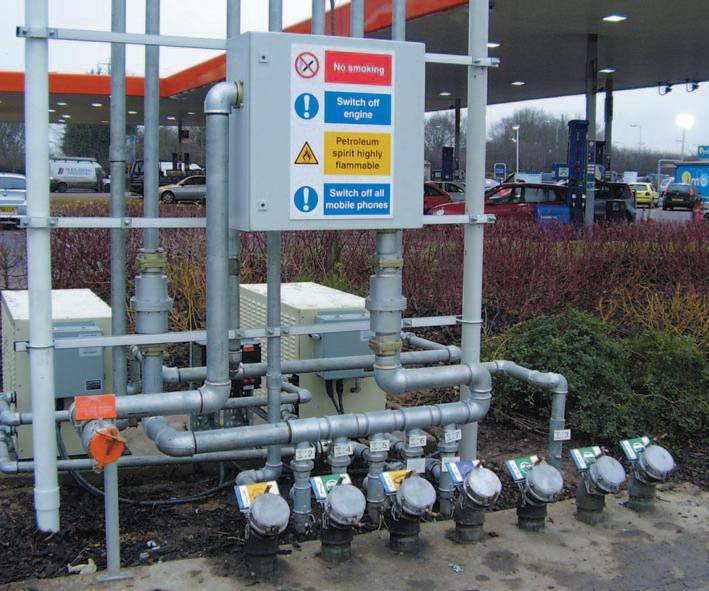
Stage 1b has now been enshrined in legislation for the past eighteen years or so and this is required to control the vapour when off-loading petrol from a road tanker. The efficiency of this system has always been very much dependent on the efficiency of the delivery tanker, working on the old adage that more often than not an efficient delivery tanker will very often overcome the short comings of a poorly operating Stage 1b system. There will unfortunately come the day when a less efficient tanker will arrive on site to deliver to the same system, and that’s when the potential for a serious problem will arise.
The importance of a vapour tight site cannot therefore be over emphasised. The principle of being vapour tight includes the sealing of the over fill prevention valves, the drop tube and pressure/vacuum valve. With this having been done and site sealed, deliveries from the less efficient tanker can still be offloaded safely with virtually no risks at all. This does accentuate the need for testing the Stage 1B system and it is particularly useful to do so with a delivery tanker on site to artificially promote the conditions of a problem
and ensure the system copes satisfactorily under these ‘worst case’ conditions.
The introduction of Stage 2 brings with it a completely different situation to the site in respect of delivering vapour back into the tank farm from all the pump nozzles. In fact, rather than treat Stage 1B and Stage 2 as two separate and distinct systems on the same forecourt, we must now treat them as one complete system, both being fully integrated into a Total Vapour Recovery system and very much interdependent upon one another.
Within the Total Vapour Recovery system there is the possibility of many situations occurring within the tank farm that otherwise would not have occurred if Stage 2 had not been introduced. For example, vapour expansion due to temperature differentials between the temperature of delivered product and the temperature of the collected vapour via the Stage 2 system. This also means that the infra-structure connecting the dispensers back to the tank farm has to be tested as well.
With vapour being collected from the dispenser nozzles, a higher level of concentrated vapour will be present throughout the venting system and therefore new methods of working within this environment will have to be instigated to ensure a safe and emission free environment. The advantages of introducing Total Vapour Solutions well outweigh the few disadvantages, as well as making it possible to operate the site better commercially; it also ensures better and far more accurate control of wet stock reconciliation. This gives the benefit of a more rapid alert to leakages within the system and, perhaps more crucially at a far earlier stage, thus giving the operator valuable extra time to accurately assess the situation and proactively deal with it.
With Total Vapour Recovery, the site has to manage and control vapour created by both the deliveries from the road tanker and vapour being collected via the dispensers and that in its self can produce unwanted problems. The tank farm is now in a different condition due to vapour being “delivered” from the dispensers on the forecourt. Delivered vapour from the dispensers becomes a very important part of wet stock reconciliation.
With a sealed system and vapour being returned to the tank farm, via the underground pipe work the Total Vapour Recovery system should be kept in balance. As the product is dispensed from the tank farm, it is replaced with vapour/air collected from the motorists’ fuel tanks. Under most normal operating conditions this works very well and the Total Vapour Recovery system remains in balance, that is until there is a disparity in the temperature of the vapour in the ullage space and the temperature of the incoming vapour from the Stage 2system.
This temperature differential causes a rapid expansion of the air/vapour mixture to such an extent that the pressure/vacuum (p/v) valve is released (emitting vapours out to atmosphere) and only reseats when the two temperatures resume equality (within the permitted range) in the Total Vapour Recovery system (which can often take quite some time to balance out). This situation is more problematical during the winter season when temperature differentials can be quite high.
To achieve the full advantages of Total Vapour Recovery a number of issues have to be resolved.
1)Control of the Delivery Tanker effects.
2)Managing the delivery of product into the tank farm.
3)Control of the environmental conditions of the delivered vapour from the dispensers to the tank farm.
4) The processing of the air/vapour mixture into liquid, returning that back to the UST’s and releasing the air back out to the environment.
Controlling the delivered product to the Tank Farm Controlling the environmental conditions of the collected vapour from dispensers
There is often a significant differential in temperature (either positive or negative) between the vapour/air collected from the vehicles via the dispensers and the actual temperature of the fuel being dispensed (being determined by the temperature within
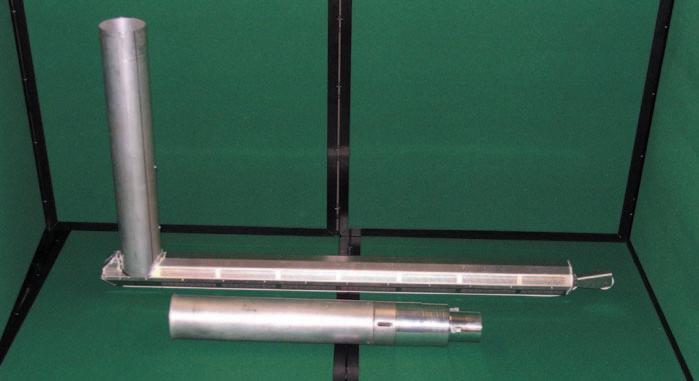
Controlling the effects of the delivery tanker
This is achieved by installing control valves onto the vent pipes (System VR). If the tankers vapour recovery hose is connected to the site when offloading
Turbulence of the delivery product must be prevented during off loading when the product enters the UST’s as this will significantly reduce the generation of vapour, together with balancing the temperature differentials. This is achieved by using a distribution beam to smoothly deliver the product along the bottom of the storage tank, in conjunction with a vacuum generator within the fill pipe to
draw the vapour out from the ullage space and permeating it through the delivered product as it enters the tank via the distribution beam (Softfill + Accumulus).
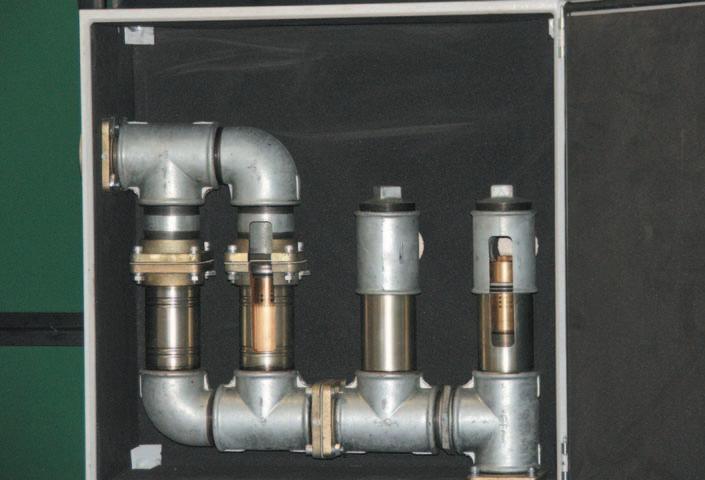
diesel, these control valves will neutralise the effect of the tanker which would otherwise draw off petroleum vapour from the tank farm whilst off loading diesel.
The control valves will also distribute the petrol vapour as it is displaced from the UST’s during off loading, as well as retaining the vapour within the tank farm at a prescribed pressure, rather than allowing it to be returned back to the tanker.
the tank farm). In winter, the vapour/air collected from the vehicles may often be lower than the temperature within the tank farm (and in summer vice versa). If these two temperatures are not equalised or acclimatised, this could promote rapid expansion and significant rises in vapour pressure within the system. It is important therefore, to control as far as possible manage and stabilise the temperature of the vapour/air mixture returning from the dispensers and to regulate it (up or down) to bring it into line with the temperatures within the tank farm. We harness the temperature of the stored product to cool or warm the incoming vapour before entering the ullage space so that a balance is created between the two conditions.
Processing Vapour into Liquid
The OPW (Vaporsaver) device is used to process both the air/vapour collected and generated during deliveries as well as the air/vapour mixture being delivered back from the dispensers.
Using membrane technology, an advanced form of vacuum pump and compressor, any air within the system is purified before safely venting out to atmosphere. All the vapour within the system is processed into the super saturated vapour and liquid (that is then returned to the UST’s where it can be