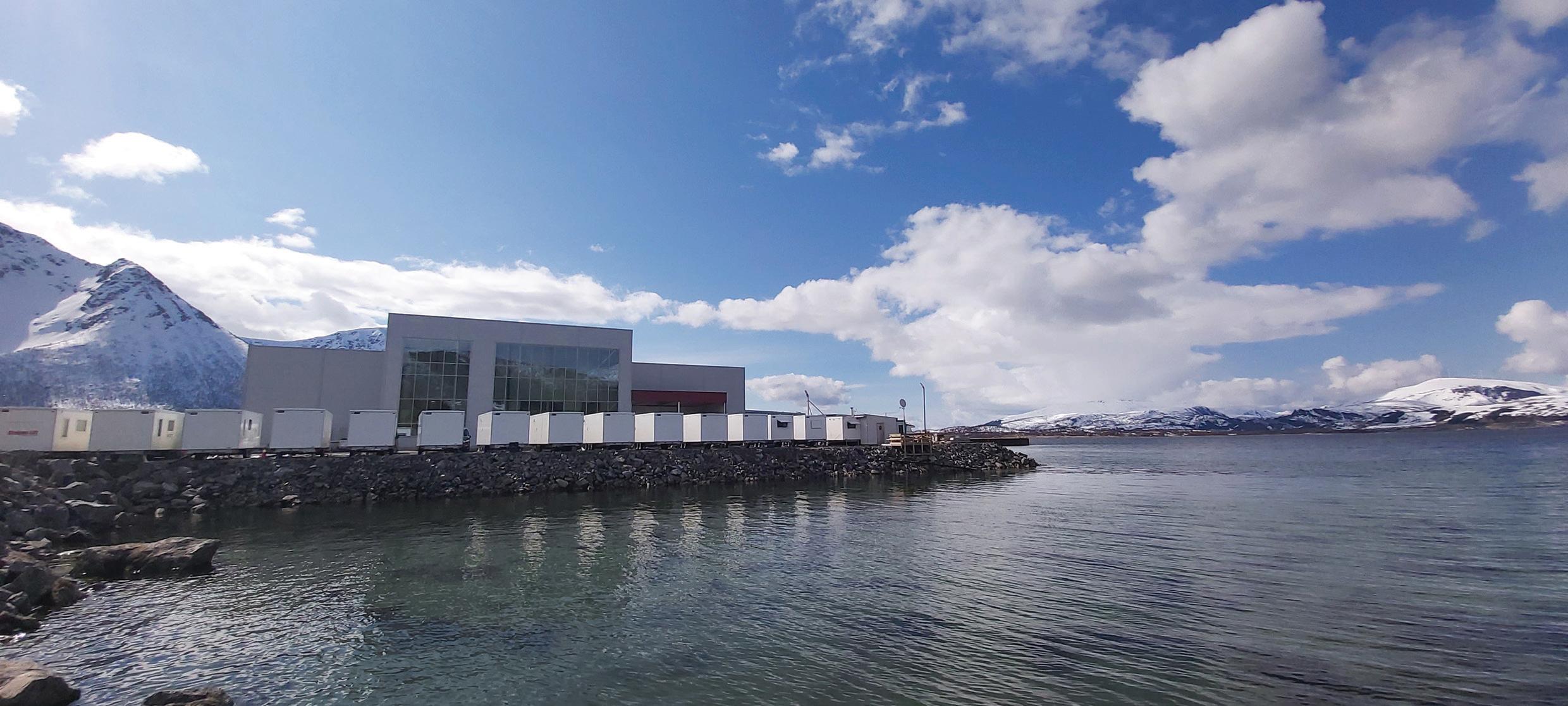
4 minute read
The world’s first industrial plant for processing of the
Isak Bøgwald and Hogne Abrahamsen, Calanus AS
The plant is located above the Arctic circle, in the city of Sortland, Norway.
The Norwegian company Calanus AS is currently building the world’s first full-scale industrial plant for processing of the marine copepod Calanus finmarchicus, located above the Arctic Circle in the city of Sortland in northern Norway. The project was triggered by the decision of the Norwegian government’s Ministry of Trade, Industry and Fisheries to open for commercial harvesting of the species, along with an increasing demand for the company’s products. This decision provides predictability for further investments and puts the company in a good position to supply an increasing number of customers with our health and nutrition products derived from C. finmarchicus. The plant project has a total investment budget of €18 million, of which €7 million is to be financed with equity, and will have an annual processing capacity of up to 10-12,000 tons of raw material.
Sustainable harvesting
Considering that the annual biomass production of Calanus sp. is larger than all fish and mammal species combined in the Norwegian Sea (approx. 300 million tons, Skjoldal, 2004), and the development of new technology to minimize bycatch, harvesting the species is deemed sustainable by both scientists and the government. The annual commercial quota is set at 254,000 tons. This is less than 0.1% of the annual production and a statement to the precautions that are taken to ensure sustainability. Most of the quota is to be harvested outside of the 1,000 m bathymetric contour line (oceanic region), which has incited the company to develop state-of-the-art oceanic harvesting technology for C. finmarchicus. Calanus AS is certified for MarinTrust (previously IFFO RS) for its commitment to responsible practices in the areas of raw material procurement and food and feed safety.
The viewing corridor with CTO Kurt Tande and product manager Alice Marie Pedersen of Calanus AS.
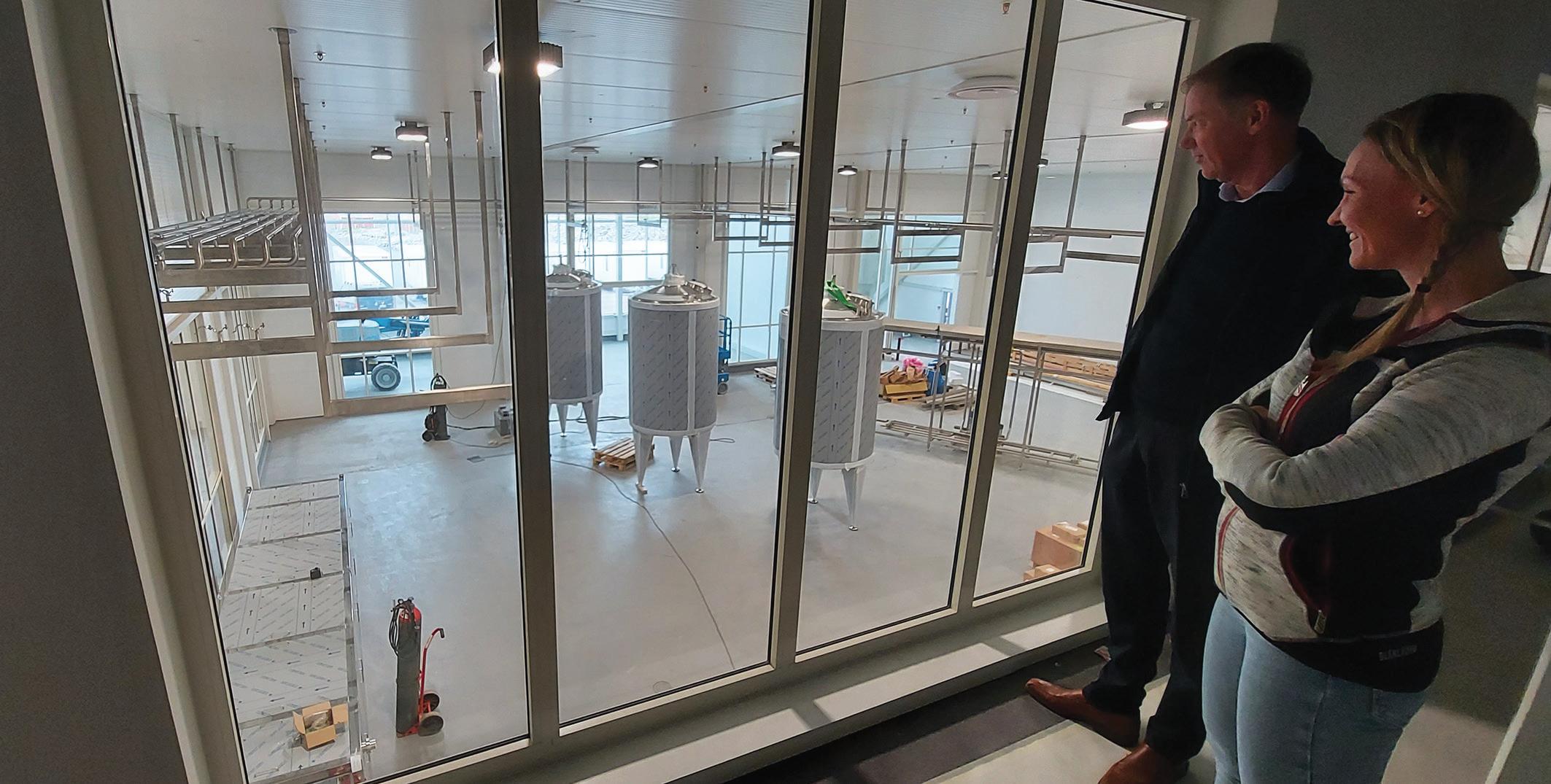
Clean and energy-efficient production process
The manufacturing process developed by the company allows for the extraction of both oil and proteins without the use of solvents and additives, thus nothing is removed, and nothing is added to the natural products from the copepods. The raw material is frozen immediately on the vessels after harvesting and stored at Holmen Industrial Area, right next door to the processing plant. With process technology in the plant customized to handle frozen raw material, the results are minimal oxidation and deterioration of the products. Renewable energy generated by wind farms and hydropower plants in the area will power the processing plant, and energy used in the manufacturing process will be recycled and reused, e.g. by using heat exchangers. The plant is designed to collect every component of the copepods during the manufacturing process; unique wax ester oil for human consumption, and protein hydrolysate and a powdered meal containing lipids, protein, and chitin for aquaculture feed. This leaves only the water contained in the copepods as waste, most of which is evaporated in the process and run through treatment systems that collect particles and sludge, securing that almost no organic material is released to the environment.
An eco-friendly location
The processing plant will be a part of Holmen Industrial Area, and building it on the shores in northern Norway has several advantages for green and environmentally friendly production; i) The proximity to the harvesting areas, vessels and raw material storage facilities reduces transport and thus the carbon footprint of the whole value chain; ii) The access to seawater reduces the use of freshwater in the manufacturing process. Seawater will account for 75% of the water consumption in the process, which is employed mainly for cooling and purification purposes; iii) The proximity to the aquaculture industry and customers. The processing plant is in a central industry hub containing notable feed producers such as Skretting and Biomar, major salmon farmers and other established biomarine companies.
A continuous process
The processing plant is designed to run 24/7 with continuous processing. In addition to the process equipment, control rooms and laboratories, the plant also contains all the necessary elements to function as a “miniature society” including living quarters, wardrobes and dining rooms. There is even a viewing corridor running through the whole plant where visitors
and guests can observe the process without the risk of contamination. The building project involves two major parties; Total Bygg og Anlegg AS for the construction of the building itself and Skala is responsible for all the process equipment within the plant. Skala is a process solutions provider with expertise in foodgrade technology in terms of sterile production and maintenance, and as a total supplier they will set up the best possible option for each of the processes involved in the production.
Up and running in Q1 of 2021
According to the schedule, the processing plant will be ready for production in Q1 of 2021. The company will obtain feed and food approvals of the Norwegian Food Safety Authority and the Food and Drug Administration (FDA) for the new plant and will renew its ISO 9001:2018 and MarinTrust certifications.
As Calanus AS will increase its production capacity 12-fold following the completion of the new processing plant, the company is in a position to broaden the customer base and are now in a process of branching out to several relevant markets for the aquaculture feed ingredients Calanus® Hydrolysate and Calanus® Powder.
References
Skjoldal, H. R. (2004) The Norwegian Sea Ecosystem, Tapir Academic Press.