
6 minute read
Leading down the road of sustainability
Leading down the road to sustainability
Nigel Lindley, NLC-ECO
Courtesy of Ever Extruder and Dedoussis Control systems.
“You cannot be serious!!!” For many who read this, these words may have little meaning. But for my generation and the one before it, these words spoken in 1981 by Wimbledon’s number one player and world tennis champion John McEnroe make perfect sense. John was challenging the referee’s decision as to whether the ball was on the line or out. Hawk eye or video replay came later! For tennis, as with many sports with professional players earning large amounts of money, these decisions were critical for a win or lose.
So how serious are aquafeed companies when they use the word sustainability? How important is sustainability, and how can we, as process technologists, move the industry forward? Ultimately, there is no choice. Sustainability is here to stay. It is of
unprecedented importance wherever production takes place. Sustainability must be part of the DNA of each aquafeed facility. So yes, we have to be very SERIOUS.
Having being involved in the aquafeed industry for over 25 years, I have seen many changes, but today, I still visit plants where poor energy recirculation and outdated technology abound. The purchase price remains the determining factor and long-term energy savings or sustainability are forgotten. I see extrusion systems running on technology of more than 30 years, dryers without recirculation and manual control of high capacity systems where the implementation of new technology could give a return on investment within six months of introduction while reducing costs by up to 35%.
Ever Extruder shaft stabiliser system.
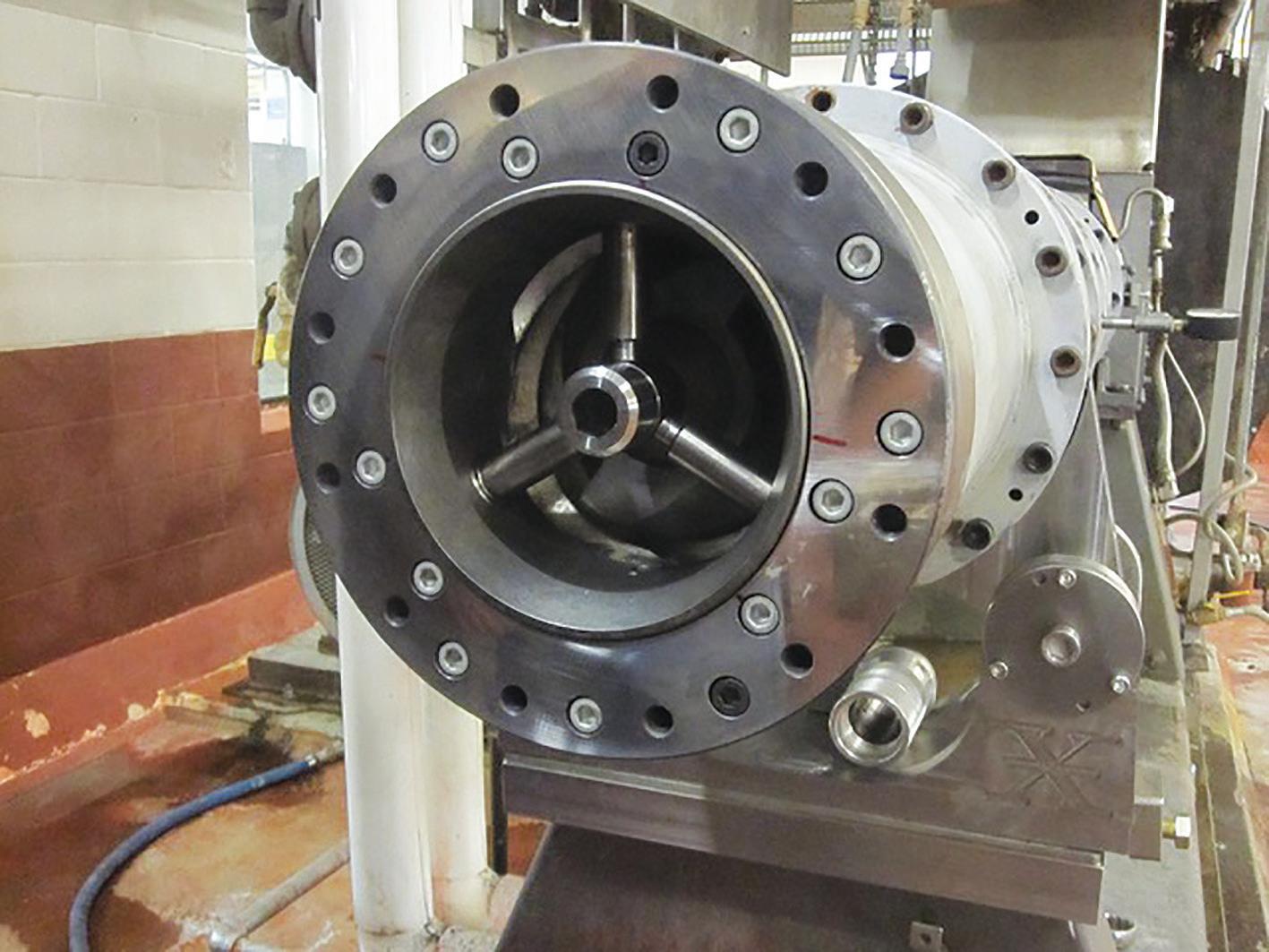
I was fortunate in my career to work with two of the world’s leading extrusion system manufacturers that changed the extrusion process beyond recognition, and within that environment had mentors whom I still respect. Unfortunately, I lived in a cocoon and I didn’t realize it at the time, until starting my own consultancy business six years ago. In my opinion, not all the answers come from Kansas but in many cases, it comes from other industries, other applications and through travel and the internet. Stretching that extra mile is possible. We are a truly global industry.
So, let us be SERIOUS and look at three main areas in the aquafeed production. There are other important steps such as particle size reduction, but today let’s concentrate on immediate and long-term savings in energy, labor and consistency of product and production leading us down the road of sustainability. I am concentrating on single screw extrusion systems, their being by far the main work horse of production in aquafeed, drying and control systems.
Extrusion system. Upgrades and updates
Of course, no one expects that established systems will simply be discarded and replaced by what may be regarded as the latest trend, which could cost several million dollars today. So what simple potential upgrades are available that give instant results?
Most aquafeed process technologists realize the effectiveness of preconditioning. It has been around for many years and is undoubtedly a major processing cost reducer. What is potentially the next most critical attribute associated with maintaining production capacity and quality? The answer, of course, is the stability of the extruder. The possibility of creating the most effective pumping system on single screw systems ensures the required constant die pressure, thus maintaining the production capacity and optimal operating conditions, leading to consistency of product quality. The centralization of the extruder shaft is a key and critical factor to meet stability and consistency. As any engineer appreciates, extruder shafts loaded with screws has a dip point, where some older technology may be applied. For example, some systems apply a type of stationary shear lock consisting of a spider-type accessory that in turn contains a bronze bushing, acting as a bearing and stabilization control. Of course, from the first day the bushing wears, there are no adjustments and performance drops.
Shaft stabilization
Let me introduce you to the retrofit that will change your extruder performance from day one. The adjustable shaft stabilizer and carriage package, utilizing Carbide technology. This package using laser alignment on installation will fully centralize the shaft and barrel as one component on single screw systems. This will have immediate and long-term gains.
The extruder will not only operate under optimal conditions, optimum capacity and reduced wear costs, but also will result in higher standards of quality and, of course, in a more sustainable process.
Advanced die and cutter technology
Let’s take a look at another low-cost update that not only delivers higher quality feeds but that vital requirement, consistency. Which operator appreciates the unenviable task of setting up a cutting system with 16-20 knives and which two operators can set up the knives the same way? The answer to both these
New generation of hybrid batch dryer utilizing both electricity and gas as the heat mediums. Courtesy of Geelen Counterflow.
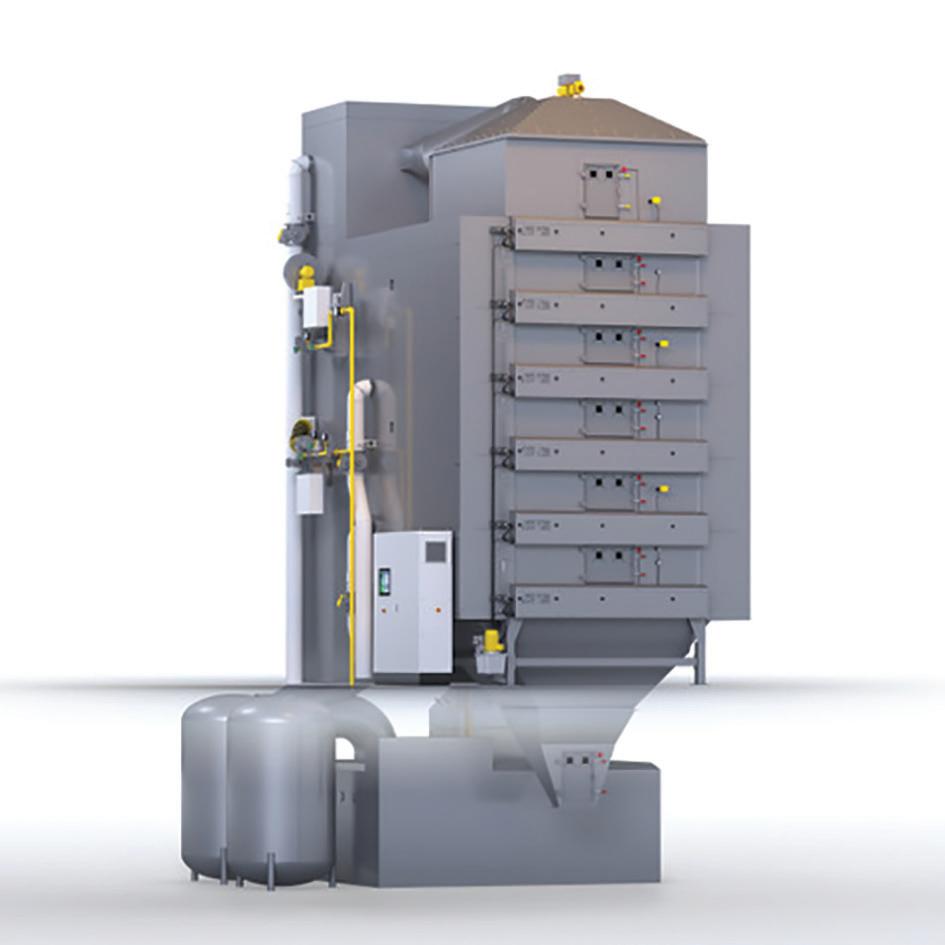
questions is none. How can any system still promote throwing away blades as a sustainable option? Multiblade, reversible and resharpenable cutter assemblies, reduce downtime and in combination with a selfadjusting hub assembly, offer ease of installation, one single screw fixing in place, and consistent set up each time by all technicians day and night. The result is less tails, less fines and a cut of the highest quality.
Combining this cutter technology with Carbide die options (lasting 5-10 times longer than standard hardened steel dies) with unique characteristics of diameter maintained throughout the die life, results in no expansion change.
Advances in drying technology
Anyone involved in the production process of aquafeeds immediately recognizes the importance of efficient and effective drying technology, arguably the most expensive energy-consuming process in the production flow. Effective drying is no longer like searching for the holy grail.
Early, horizontal dyers were expected to have plusminus 2-3% moisture deviation. This results in overdried feeds and more energy usage to ensure that the final moisture does not exceed 9-10%. This approach is not exactly energy or sustainability effective.
Now we can seriously analyze moisture deviations of plus-minus 0.5%. We are seeing drying technology advanced by leaps and bounds since the introduction of the vertical counterflow dryer, where airflow and zone control are paramount to utilize energy consumption with 70% of moisture being extracted from the product in the first two zones. The final moisture of the core can be evaporated in a controlled zonal process, significantly reducing energy consumption.
The revolution. Computer control systems
I started my introduction in the extrusion technology in 1988 and at that time we were all just beginning to visualize the era of technological advancement.
Little did we know what was to come, changing our lives both from a personal and business perspective. This tool we call the computer has provided the aquafeed producer an opportunity to revise all process parameters, reduce energy consumption, utilize a wider range of raw materials and analyze a complete and comprehensive range of data. It’s a teaching tool with remote access to any part of the world that has an internet connection. Instant payback!
Sustainability opportunities at the touch of a key. Traceability programs that detect any abnormal occurrences that can lead to quality challenges in the field together with vital online analysis to predict these challenges and make real-time, live changes to ensure specifications both nutritionally and physically are optimized. We can share online operations, share potential maintenance issues remotely, trend charts to analyze optimum operation of the process. This is a very serious tool!
In conclusion, these three areas will bring consistency into your process flow, reduce costs and most importantly assist the operator interface with production and product quality, resulting in energy savings, lowering production costs and sustainability as a bonus. In this day and age, stimulated by a growing environmental concern and awareness with regards to sustainability we all need to be SERIOUS.