
26 minute read
Usinagem
Paulo Sérgio Martins, José Rubens Gonçalves Carneiro, André Bragança Carvalho França, Leonardo Dutra e Pedro Paiva Brito
Com o desenvolvimento de novas ferramentas de corte, as velocidades empregadas nos processos atingem valores inconcebíveis. Nesse contexto, o aço e o ferro fundido vêm sendo gradativamente substituídos por materiais de menor densidade e melhor usinabilidade. Neste sentido, os autores deste trabalho avaliaram a furação de uma liga Al-Si fundida sob pressão, com o uso de uma broca de aço rápido VK5. O ponto de vista principal foi a tolerância do produto e o desgaste da ferramenta.
Paulo Sérgio Martins desenvolveu este trabalho pela Pontifícia Universidade Católica de Minas Gerais (PUC Minas) e pelo Centro Universitário Una, ambos de Belo Horizonte (MG). José Rubens Gonçalves Carneiro, André Bragança Carvalho França, Leonardo Dutra e Pedro Paiva Brito o fizeram pela Universidade Católica de Minas Gerais (PUC Minas). O artigo foi originalmente apresentado no 8º Congresso Brasileiro de Engenharia de Fabricação (Cobef), realizado de 18 a 22 de maio de 2015, em Salvador (BA). Reprodução autorizada.
A geometria de furos usinados com brocas de aço rápido VK5, em peça de Al-Si
As ligas de alumínio são cada vez mais utilizadas, dada a sua resistência mecânica, baixa densidade e boa usinabilidade.
A adição do silício ao alumínio diminui o seu ponto de fusão e melhora a resistência ao desgaste dos componentes. As ligas Al-Si, por exemplo, são usadas na fabricação de componentes de motores de combustão, que exigem fluidez e baixa tendência de contração; propriedades alcançadas na fundição sob pressão.
Para a produção de uma peça em Al-Si, a exemplo de cabeçotes de motor, diversas operações de usinagem são empregadas, a citar a furação, alargamento, rosqueamento, mandrilamento, fresamento e lavagem.
Posteriormente, o acabamento é feito, neste caso, sem a necessidade de retificação ou polimento.
Devido à boa condução de calor da liga Al-Si, as forças de corte usadas e a taxa de desgaste da ferramenta são consideradas baixas.
Estima-se que em torno de 15% a 20% de todo o aço produzido no mundo seja transformado e removido por usinagem, na forma de cavaco.
A usinabilidade de um material é definida como uma tecnologia comparativa, ou seja, que expressa, por meio de um valor numérico, o confrontamento de um conjunto de propriedades de usinagem. Esse indicador pode ser obtido levando-se em consideração o número de componentes produzidos por hora, o custo de produção do componente ou a qualidade final da superfície trabalhada.
O processo de usinagem é não linear, envolvendo fenômenos como a deformação plástica, fratura, impacto, pontos de contato intermitentes e desgaste. Caracteriza-se, ainda, pela geração de calor e elevada temperatura de corte.
Em razão da complexidade do procedimento, muitas vezes não é possível obter uma descrição matemática da sua dinâmica, o que pode ser superado com o uso de sensores de medição.
Em altas temperaturas, a ferramenta de corte pode perder a sua forma rapidamente ou sofrer desgaste, resultando no acréscimo da força de corte, baixa exatidão dimensional do produto, redução da vida útil, e dano mecânico e químico da superfície acabada.
Essa elevada temperatura pode ser controlada por injeção de fluido lubrificante e refrigerante na interface cavaco-ferramenta.
Dentre os processos de usinagem tradicionais, a furação é uma das operações de corte de metal mais

Fig. 1 – Diagrama do modelo de uso de três fases de desgaste de uma broca de aço rápido Fig. 2 – Microestrutura da liga Al-Si, evidenciando a fase clara, rica em alumínio, e o eutético
importantes, consistindo em 33% de todas as operações de usinagem. Ela é responsável por aproximadamente 40% de toda a atividade de remoção de metal na indústria aeroespacial, por exemplo.
O grau de calor na interface cavaco-ferramenta tem uma influência importante no desgaste da ferramenta e na microestrutura da região de deformação.
A temperatura cresce com o aumento da profundidade do furo, para a mesma velocidade de avanço e do eixo.
Outra teoria é que seu valor máximo na face de corte da broca é uma função crescente da velocidade de corte e de avanço.
A velocidade de corte, avanço e profundidade são indexadas, respectivamente, por v c, f n e a p; as variáveis mais importantes neste processo.
A velocidade de corte (v c) é a velocidade instantânea do ponto de referência da aresta da ferramenta, segundo a direção e sentido de corte. Para os processos com movimento de rotação, a velocidade de corte é calculada por:
(1)
O diâmetro da peça (mm) ou da ferramenta (N) corresponde ao número de rotações por minuto.
Neste caso, a medição é empregada para monitorar, controlar ou investigar o processo. O resultado alcançado é uma faixa de valores associada a uma unidade de medida, sendo o valor verdadeiro compreendido nela.
A qualidade, a segurança e o controle de um processo são assegurados pela medição. As imperfeições contidas em uma superfície podem ser mensuradas com equipamentos apropriados. A importância do acabamento superficial aumenta quando a precisão de ajuste entre as peças sobe.
Deve-se salientar que as superfícies reais de engenharia são compostas de forma, ondulação e rugosidade, podendo ser filtradas em cinco estágios.
Os desvios de forma das superfícies reais, com relação aos parâmetros macro e micrométricos, são a circularidade, cilindricidade e rugosidade.
A rugosidade média (R a) pode ser vista como o desvio médio de um perfil da sua linha ou a distância média de um perfil, desde a sua linha média sobre um comprimento médio.

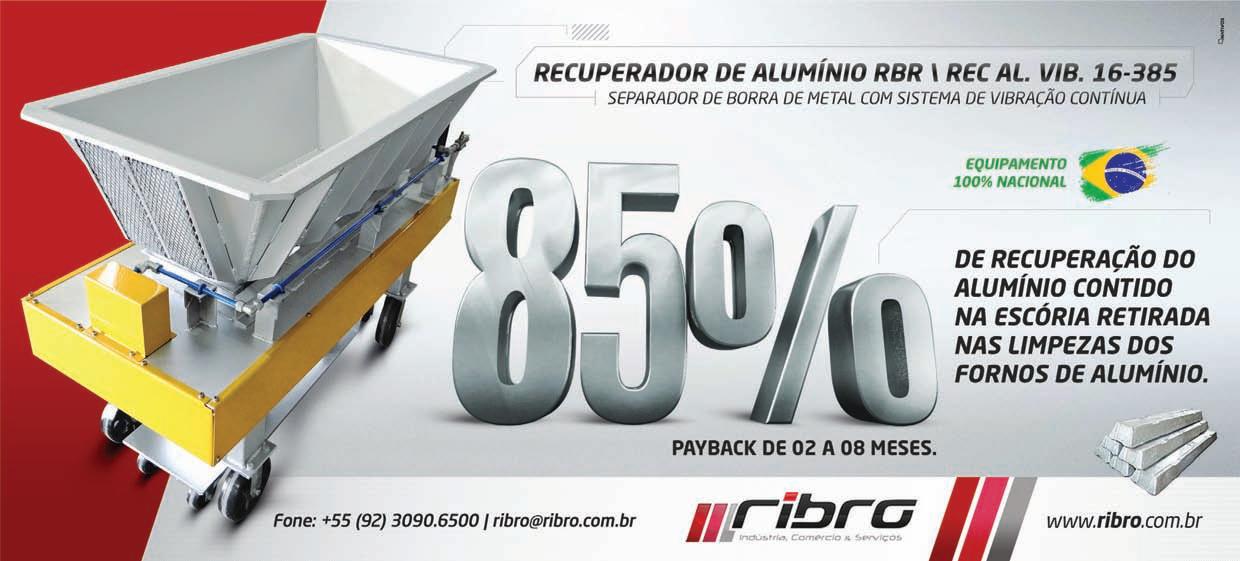
Tab. 1 – Composição química média da liga Al-Si, em porcentagem e peso.
Elemento (%) Al Si Cu Mg Mn Ti Fe Zn Ni Pb Sn Peça 86,8 7,76 3,11 0,36 0,4 0,02 0,74 0,56 0,03 0,05 0,02
O avanço (f n) é o percurso em cada rotação (mm/rot) ou em cada curso da ferramenta.
A profundidade de corte (a p) é a profundidade ou a largura de penetração da ferramenta na peça, a qual é medida em direção perpendicular ao plano de trabalho (NBR6162/1989).
Na furação com brocas helicoidais, os esforços atuantes estão ligados à geometria da broca e às condições de corte do processo, tais como o avanço, velocidade de corte e rigidez do conjunto peça/máquina-ferramenta.
O uso da ferramenta de aço rápido é limitado pela baixa velocidade de corte relativa, na qual este parâmetro é inferior à velocidade econômica de corte dos materiais de ferramentas mais resistentes.
No desenvolvimento do próprio aço rápido, é reconhecido que somente a adoção de um método de modificação da superfície e do revestimento da ferramenta é capaz de alcançar uma melhora significativa.
Foi avaliada a aplicação de cinco categorias diferentes de DLC, para brocas de aço rápido em usinagem de alumínio sem o uso de fluido de corte para remoção do cavaco.
O alumínio é particularmente difícil de se usinar a seco, em razão da sua aderência à ferramenta em altas temperaturas.
Na furação, a medição do desgaste não é importante somente nos seus estágios finais, que precedem falhas catastróficas, mas também por meio da vida da broca. O progresso do desgaste de flanco na furação segue um modelo de três estágios. No primeiro, o desgaste resulta em uma rápida elevação, já nos primeiros segundos de corte, ao passo que no segundo essa taxa é constante. No último estágio, o desgaste avança por um mecanismo adesivo, a
Fig.3 – Sistema hidráulico de fixação da broca VK5
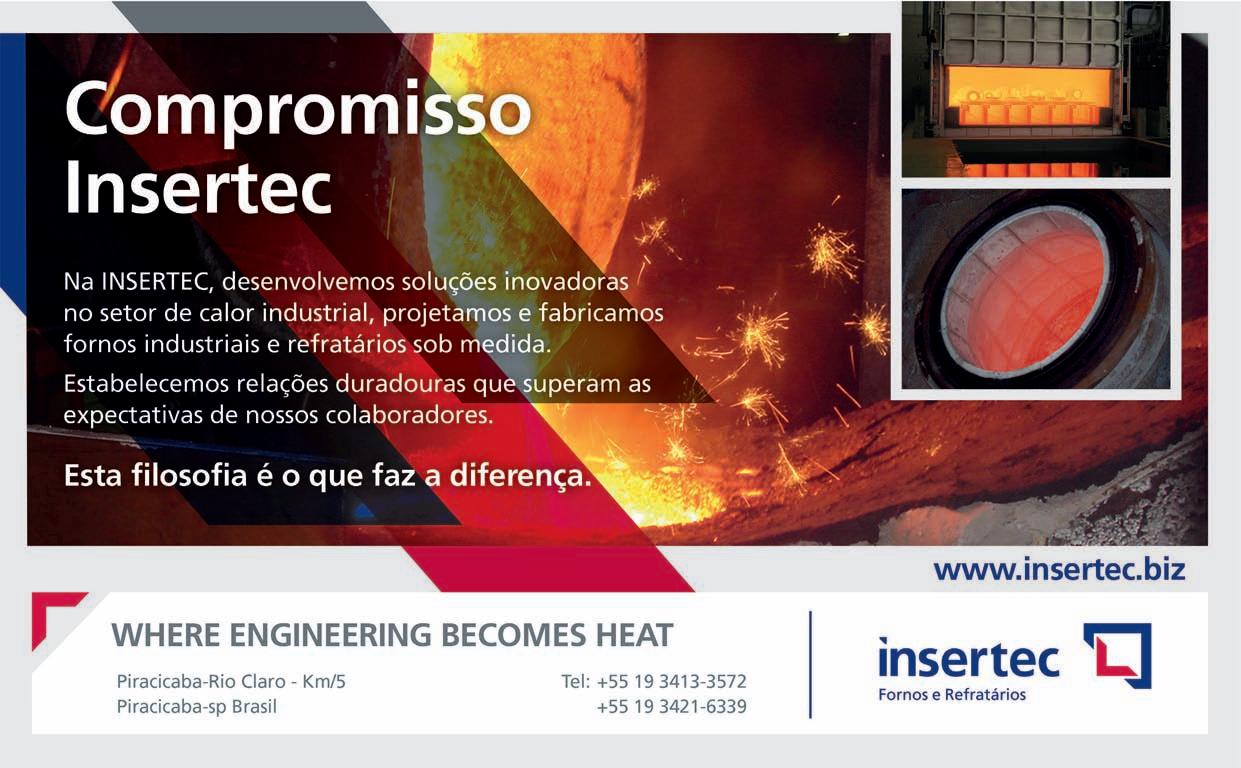

Fig. 4 – Cilindricidade pontual e suas médias em relação ao número de peças, utilizando broca de aço VK5 e velocidades de corte de 340 e 380 m/min
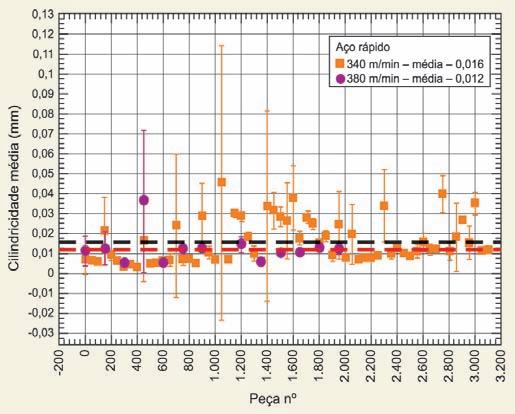
Fig. 5 – Circularidade pontual e suas médias em relação ao número de peças, utilizando a broca de aço VK5 e velocidades de corte de 340 e 380 m/min
uma taxa linear com o tempo de corte (figura 1).
O aquecimento para a têmpera do aço VK5 é feito em banho de sal fundido. Inicialmente, realiza-se um aquecimento preliminar até 500°C em forno aberto ou dotado de circulação forçada de ar, para a eliminação da umidade e dos resíduos de óleo ou outros contaminantes.
Em seguida, as peças são removidas para um banho de preaquecimento, o qual é mantido a cerca de 860°C a 880°C, onde permanecem até a equalização da temperatura.
No caso de peças com grandes seções e Fig. 6 – Análise da superfície R a (A), Rt (B) e R z (C) geometrias comdos furos gerados pela broca VK5 plexas, recomenda-se mais uma etapa Procedimentos de preaquecimento a cerca de 1050°C. experimentais
O presente trabalho avaliou o desempenho da broca VK5 quanto à re- A matéria-prima utilizada foi uma sistência ao desgaste, quando da liga Al-Si fundida sob pressão, na forfuração de peças fundidas em ligas ma de placas retangulares. de Al-Si, a uma velocidade de corte Foi fundido um corpo de prova de 340 e 380 m/min. representativo da corrida, o qual foi
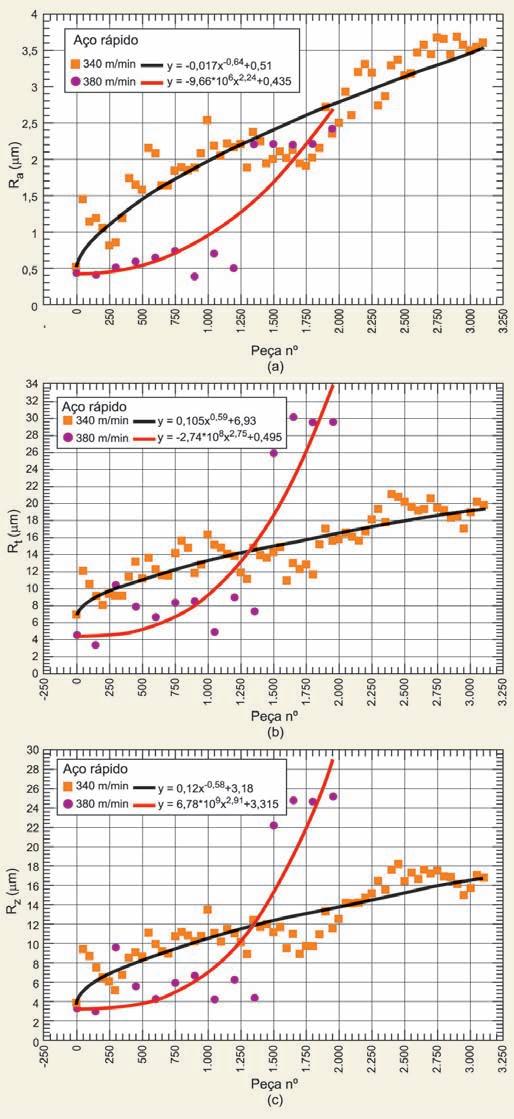
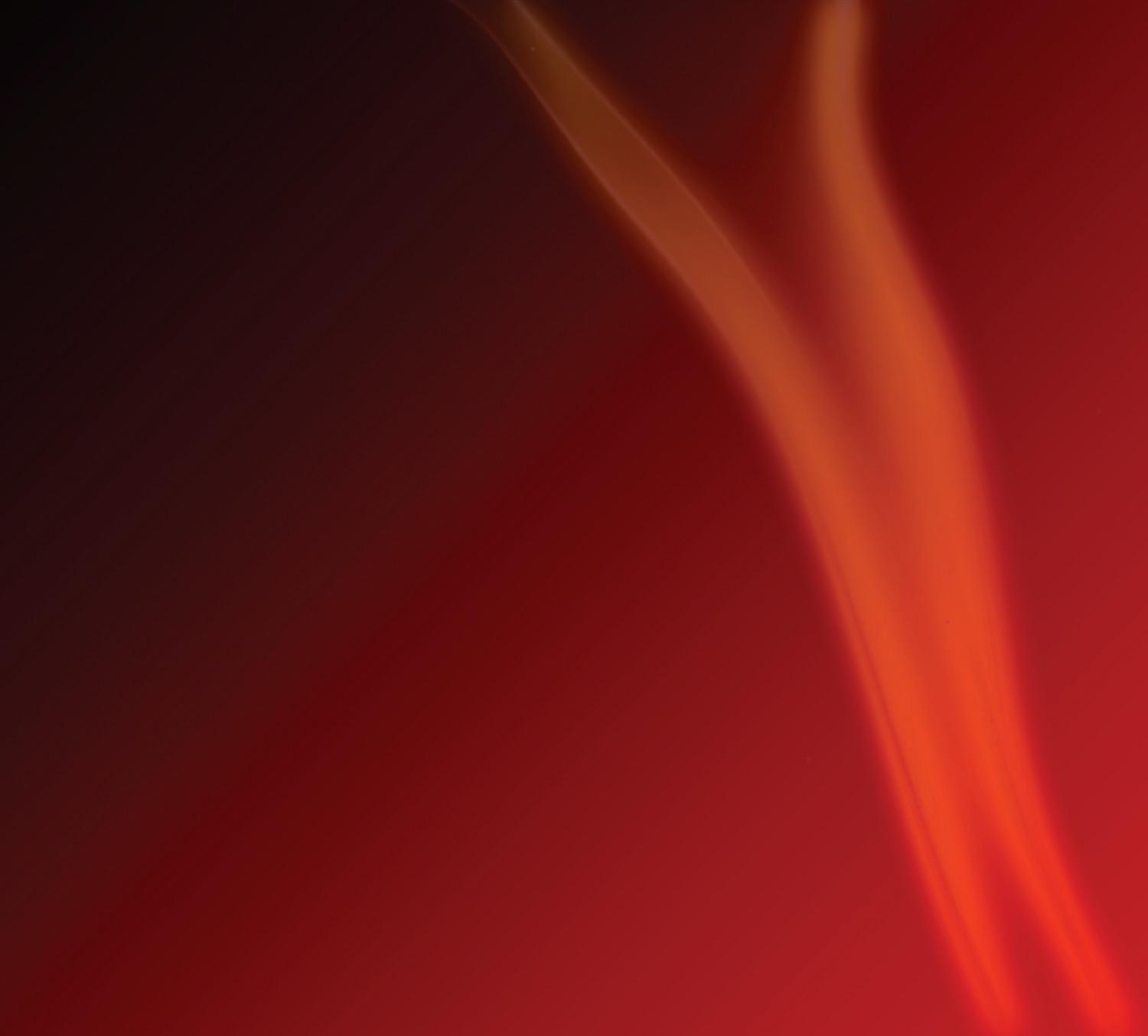
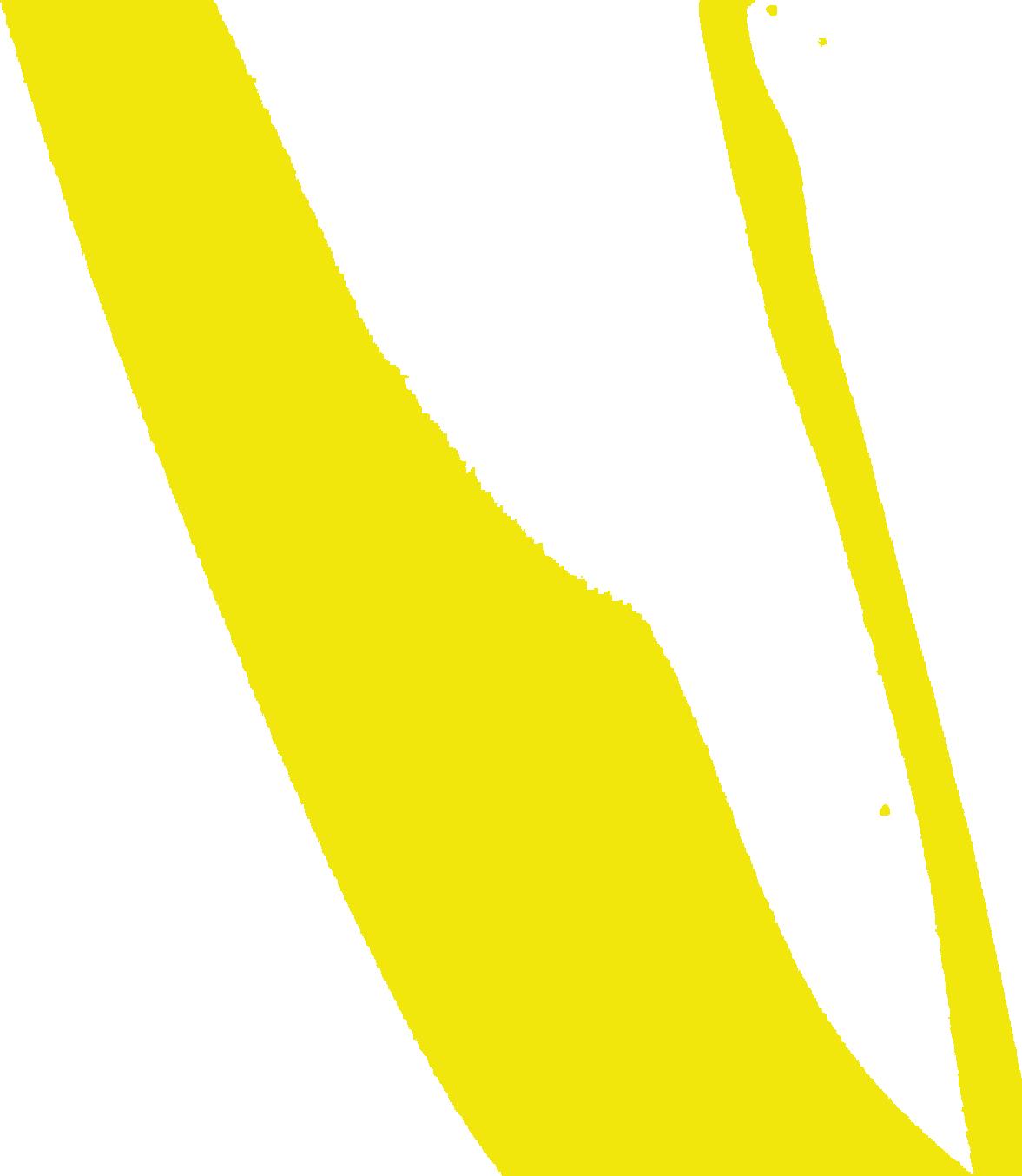
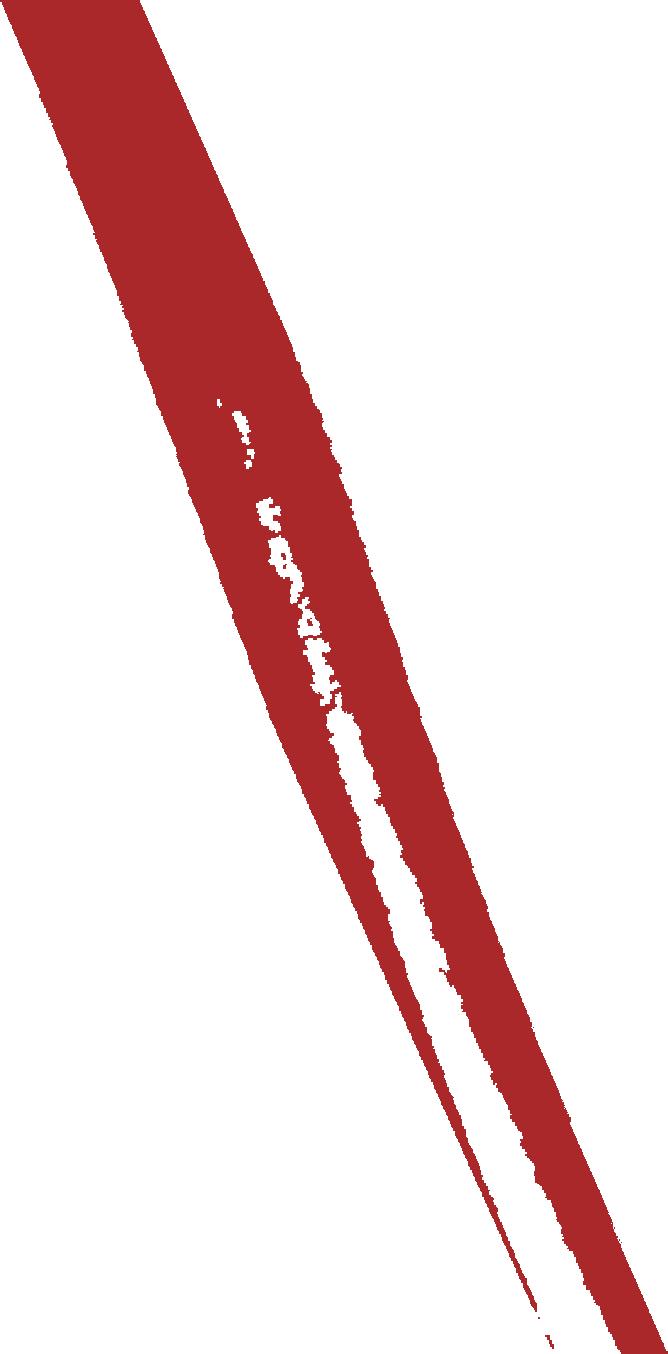
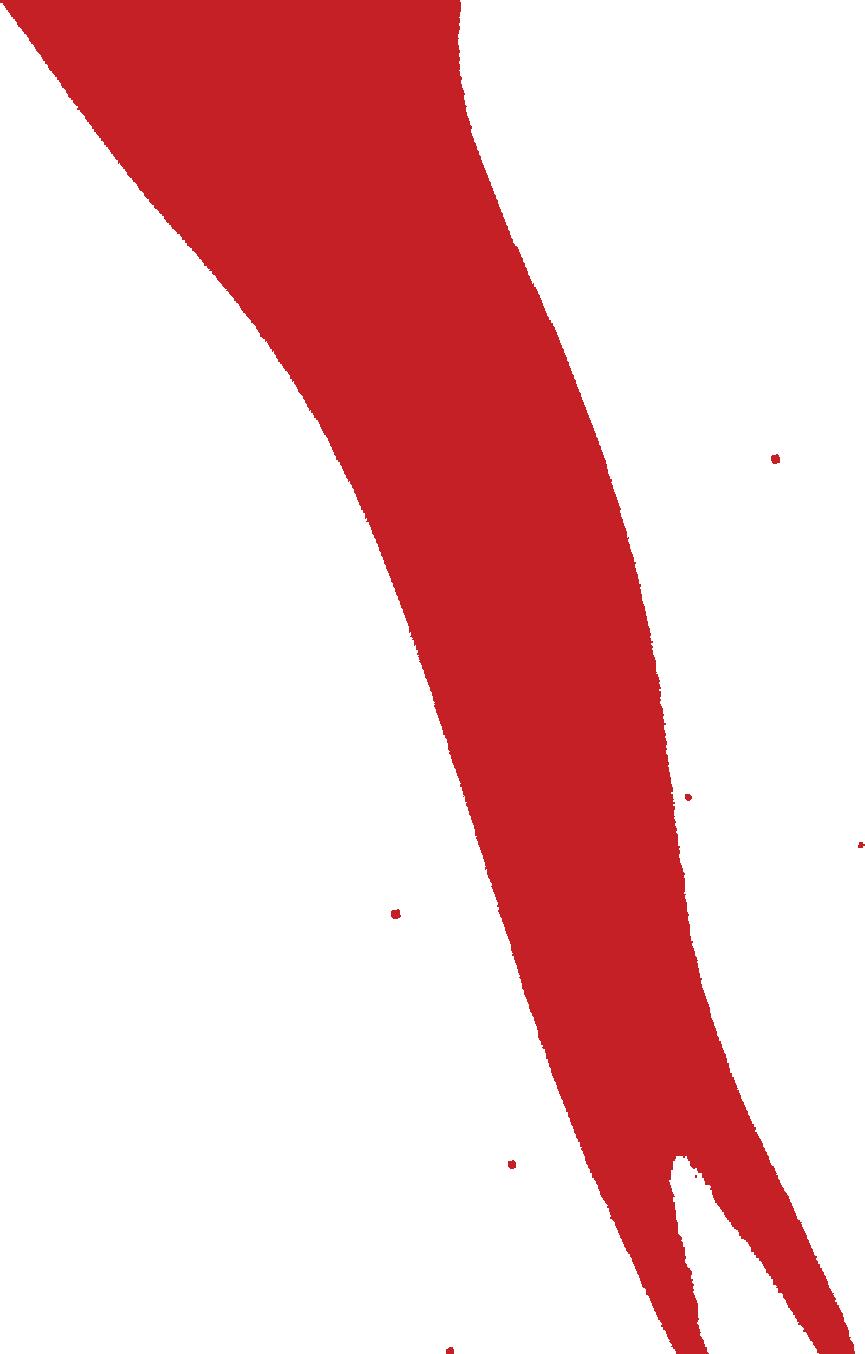
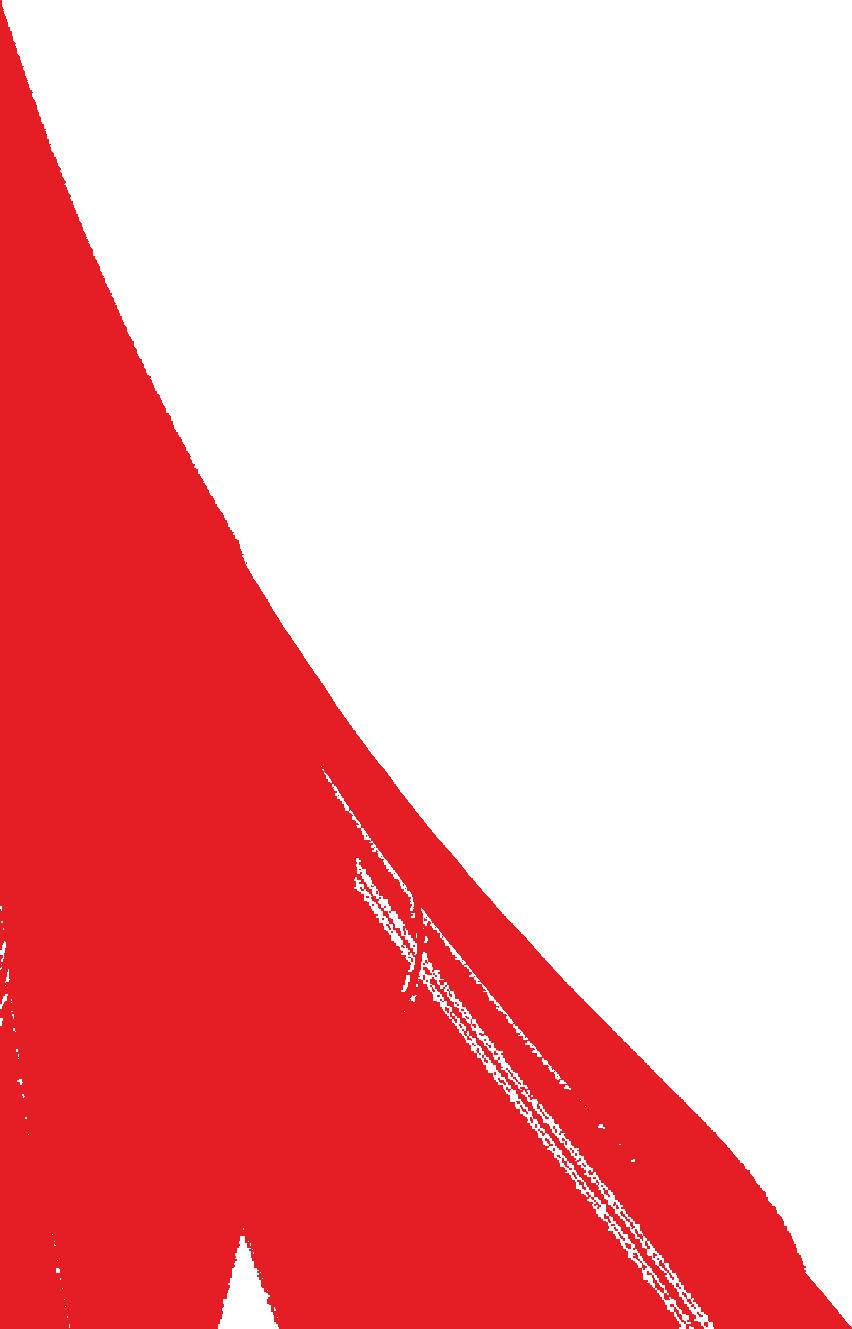
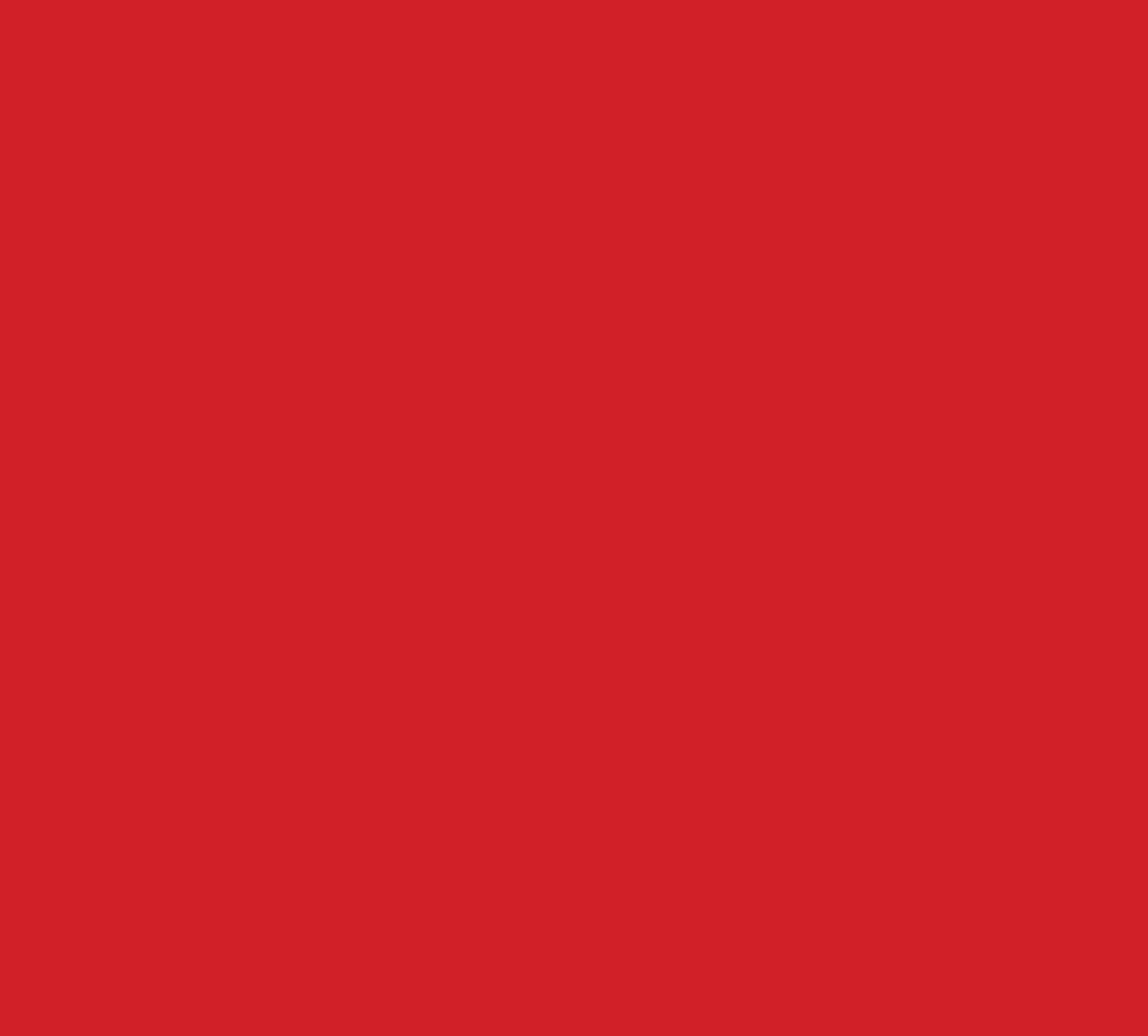
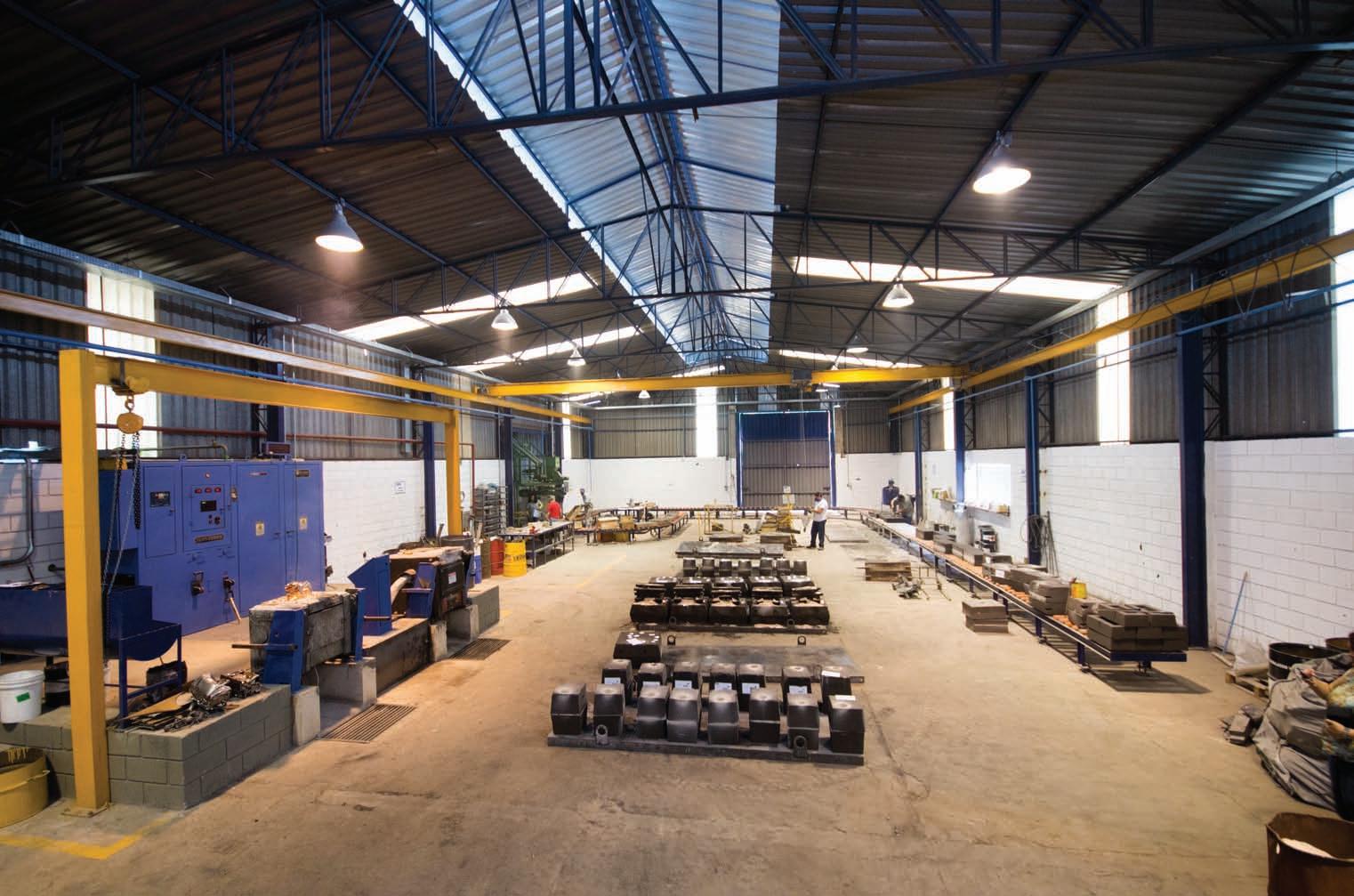



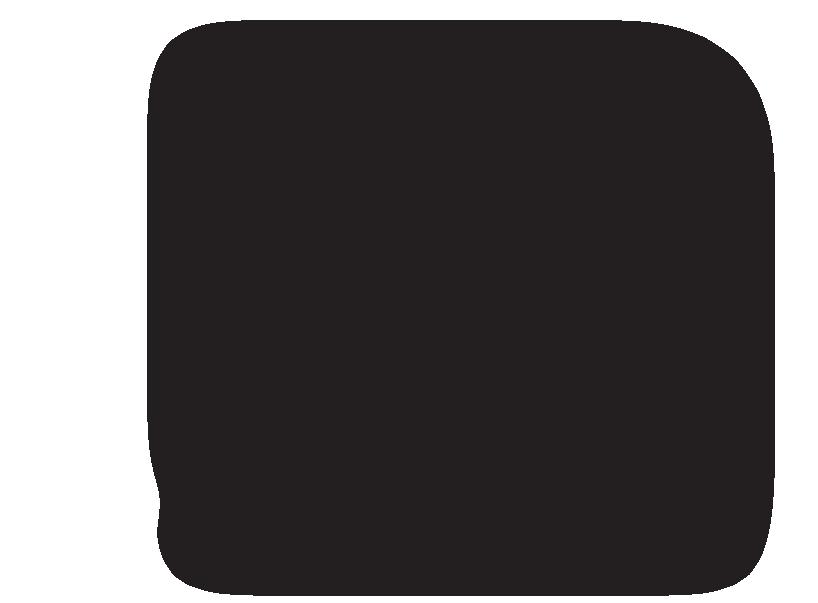
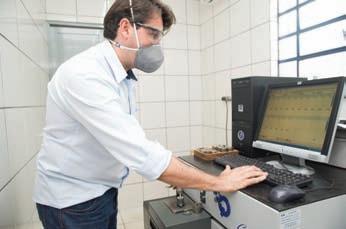
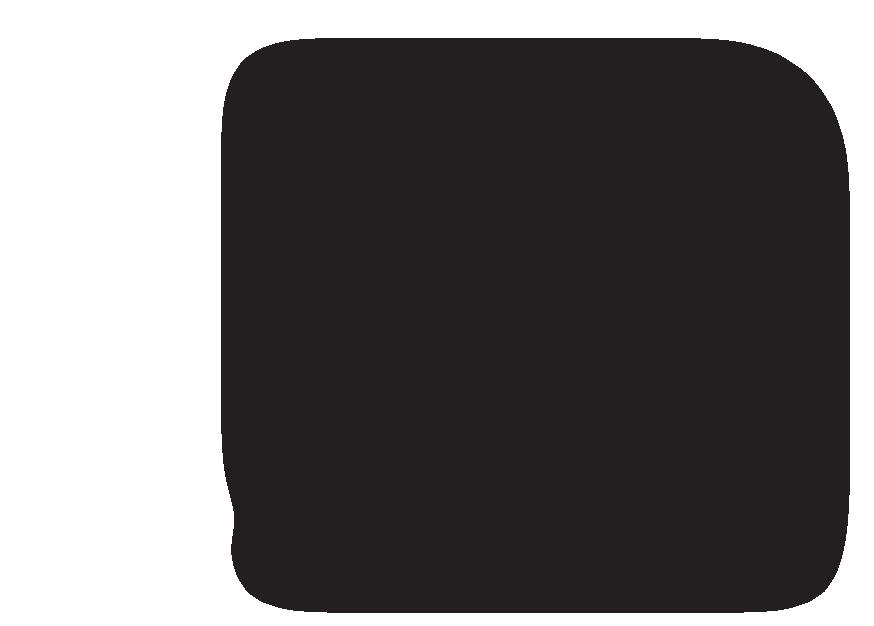

posteriormente fresado e cortado para a retirada de amostras de 30 x 30 mm, para análise química e metalográfica.
Elas foram analisadas em um microscópio óptico da Leitz, com capacidade de aumento de 200 vezes.
Para a análise da microestrutura, as amostras foram atacadas durante 5 h com água destilada com volume de 95%, 1 ml de ácido fluorídrico (HF), 2,5 ml de ácido nítrico (HNO3) e 1,5 ml de ácido clorídrico (HCl).
Foi realizado um ensaio de microdureza Vickers em um aparelho da Leitz, com carga de 100 gf.
A tabela 1 traz a composição química da liga Al-Si fundida sob pressão em lingotes.
A utilização do cobre melhora a usinabilidade das peças injetadas, facilitando ainda a sua solidificação em temperaturas mais baixas, além de reduzir descontinuidades internas na peça fundida.
A presença do ferro nas ligas AlSi é considerado um fator de fragilização, reduzindo o tempo de desmoldagem. A microestrutura consis-
tiu de fase alfa rica em alumínio e o eutético. A fase intermetálica do eutético foi Al5Cu2Mg2Si6 ou Al15(FeMn)3Si2. O teor de silício da liga significa que ela contém partículas primárias, que promovem o desgaste da ferramenta via abrasão, quando comparado a outras ligas de alumínio. Fig. 7 – Diâmetro em do rela furo ção pa ao ra nú as me duas ro de velocid peças ade de corte, Foram utilizadas brocas de VK5 com haste paralela, tolerância de 12,20+ 0,0 0,1 mm, ângulo de ponta a 145° e ângulo de folga a 10° , as quais foram montadas em um mandril hidráulico (figura 3). As velocidades de corte aplicadas foram de 334 e 380 m/min, enquanto a rotação foi de 8.800 a 1.100 rpm, o avanço de 0,36 mm/rot e a profundidade de corte de 6,1 mm, devendo-se

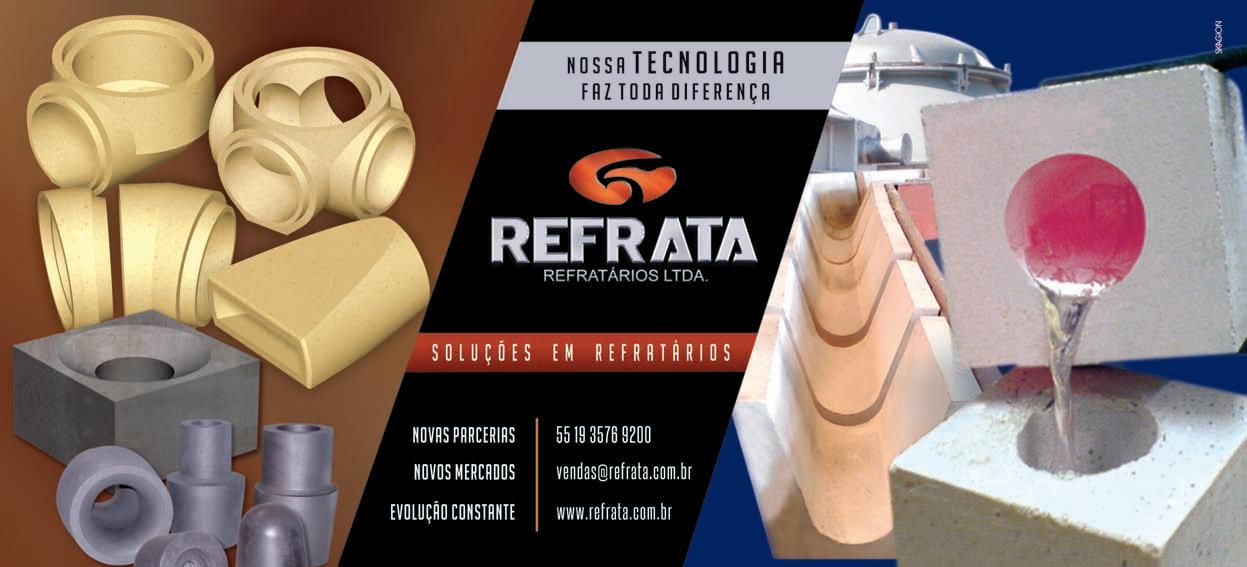
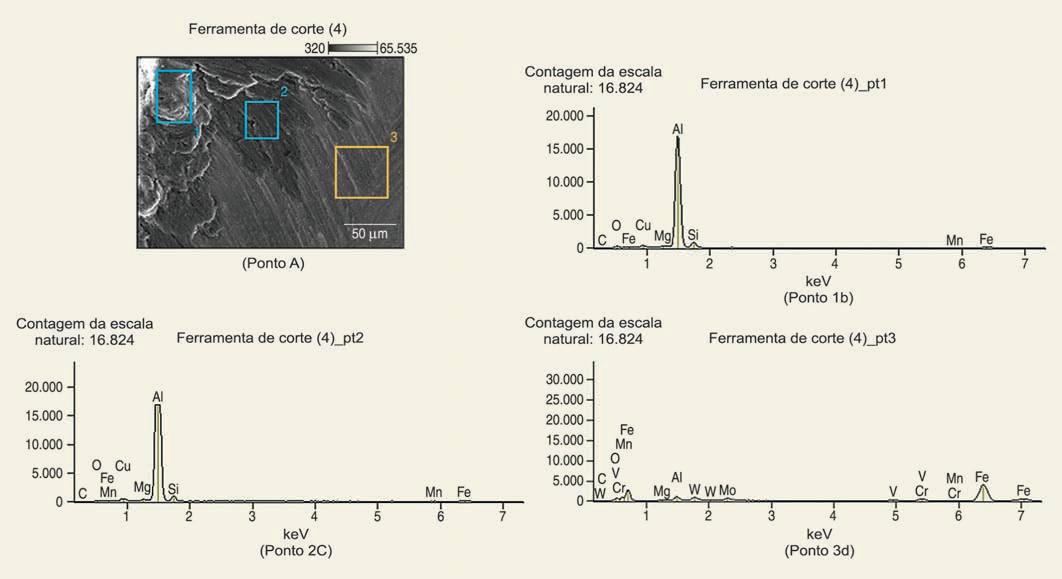
Fig. 8 – Análise feita em microscopia óptica e EDS da aresta de corte da broca VK5, a 340 m/min
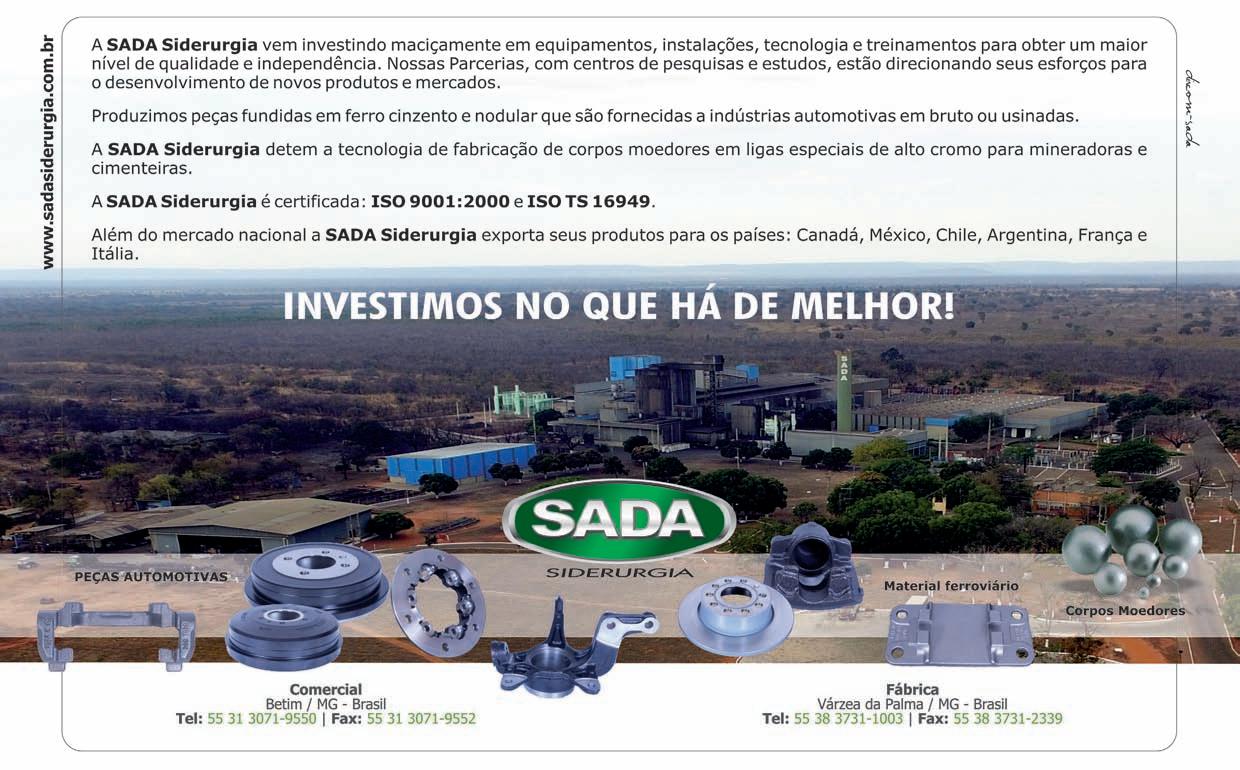

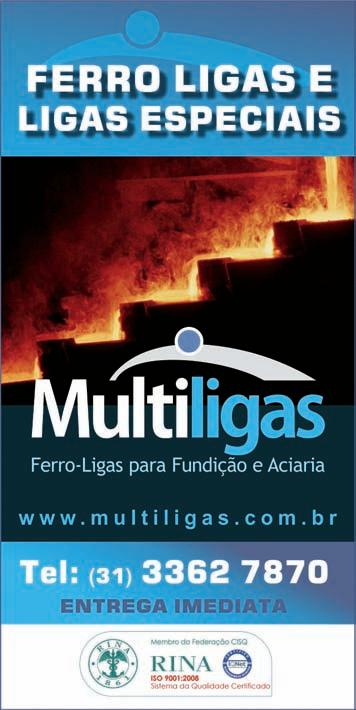
considerar que a broca tem diâmetro nominal de 12,2 mm.
Os ensaios realizados com ligas de alumínio e alargadores monocortantes não apresentaram variações de rugosidade, erros de forma ou equívocos dimensionais do furo com a variação da velocidade de corte.
O fluido de corte utilizado foi o Hocut B 205D, com a concentração de 6% a 8% em volume de água e 30 bar de pressão.
Os furos tinham 8 mm de profundidade.
Após os testes de furação, as peças foram resfriadas até a temperatura ambiente e medidas no laboratório de metrologia.
Foram retiradas as peças de número 1, 150, 300, 450, 600, 750, 900 e 1.050 até 3.100, para a medição dos parâmetros geométricos de cilindricidade, circularidade e diâmetro do furo.
Foi medido também o erro de batimento para o sistema hidráulico, nesta mesma sequência.
Os parâmetros de superfície R a, R z e Rt foram avaliados para as peças 1, 150, 300, 450, 600, 750, 900 e 1.050 até 3.100, utilizando-se um equipamento da Taylor Hobson (Form-Talysurf series) e um filtro gaussiano para a análise da aspereza, com cut-off de 0,8 mm e comprimento de 4,8 mm.
A tolerância de 3,2 μm (R a) da superfície do furo foi controlada com o auxílio de um software desenvolvido especificamente para esta análise.
Resultados e discussões
A figura 4 mostra a evolução da cilindricidade dos furos com o número produzido pelas brocas de aço VK5.
Os valores médios deste parâmetro entre as velocidades de corte mostram que as dispersões são semelhantes nos pontos 500 e 1.200, para velocidade de corte de 380 m/min.
Os demais valores foram abaixo de 0,02 μm, em comparação àqueles obtidos a 340 m/min.
A média geral de cilindricidade para 340 m/min foi de 0,019 μm. Para 380 m/min, foi de 0,018 μm.
A figura 5 mostra a evolução da circularidade em função do número de furos para brocas VK5, além dos valores médios e a dispersão obtida na circularidade dos furos produzidos com as velocidades determinadas (340 e 380 m/min).
A média dos valores para duas velocidades manteve-se linear, mas o desvio padrão para 340 m/min foi maior entre as peças 1.000 a 2.200.
A figura 6 mostra a evolução da textura da superfície, em função do número de furos usinados.
Os valores médios e a dispersão da superfície analisada (R a, Rt e R z) para as velocidades de corte de 340 e 380 m/min apresentaram variações acentuadas de furo para 0, 2, 3 e 4 μm.
Percebe-se que o valor médio da rugosidade obtida a 340 m/min foi maior, quando comparada com a outra velocidade (380 m/min).
Os valores médios e a dispersão da superfície analisada (Rt e R z) para os dois tipos de velocidade apresentaram comportamentos diferentes entre os furos de número 1.500.
A partir do furo 1.750, a rugosidade média dos parâmetros Rt e R z aumentou para as duas velocidades de corte, o que se deve ao desgaste gerado na aresta de corte.
A figura 7 apresenta a evolução do diâmetro dos furos com as peças 1 a 3.100, nas duas velocidades de corte (340 e 380 m/min), mostrando diferenças significativas.
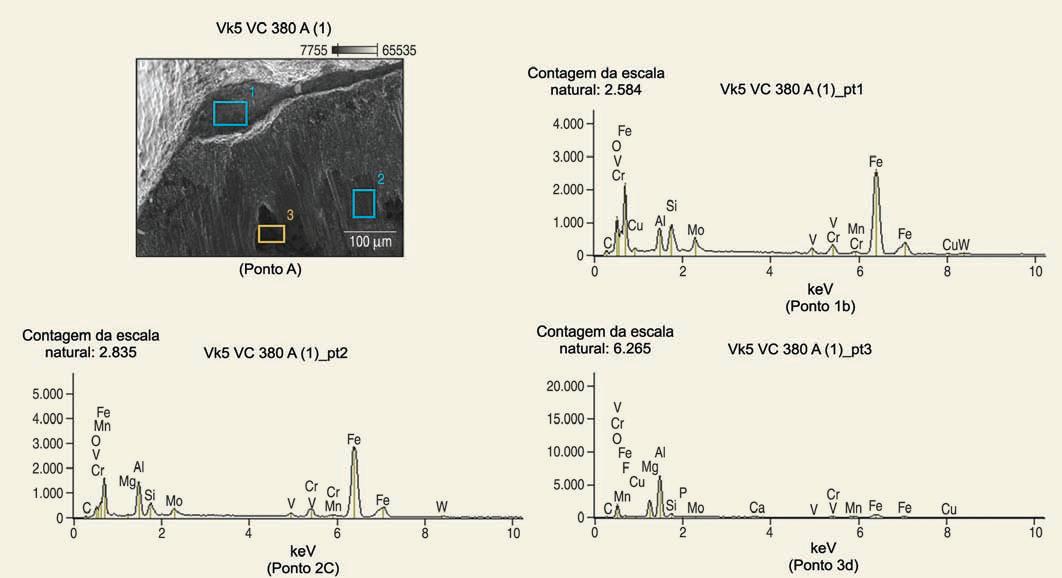
Fig. 9 – Análise feita em microscopia óptica e EDS da aresta de corte da broca VK5, a 380 m/min


É possível justificar este resultado pela natureza do desgaste que ocorre no flanco da broca, e também na adesão deste material à broca.
Para este número reduzido de furos, a adesão é física e não química, o que torna a retirada do material facilitada ao longo do processo de usinagem.
A figura 8 apresenta uma análise feita em microscopia eletrônica de varredura. Nela, nota-se a presença da aresta postiça de corte (APC), fenômeno que ocorre ao longo do processo de usinagem, principalmente em baixas velocidades.
No ponto A, foram demarcados os três pontos de análise, sendo os pontos 1b e 2c na análise em EDS, no microscópio eletrônico de varredura (MEV).
Observa-se a presença de APC aderido na aresta de corte.
Já no ponto 3d, percebe-se a presença de elementos da broca VK5 em maior proporção.
A figura 9 traz a análise da superfície da broca utilizada na velocidade de 380 m/min, após a usinagem de 1 a 2.100 peças.
Com o aumento da velocidade de corte para 380 m/min, a presença da APC foi menor na aresta principal de corte no ponto A, quando foram marcados os três pontos de análise.
No ponto 1b, aparecem valores menores de Al-Si, em comparação ao ponto 1b da figura 8.
Para os pontos 2c e 3d, os valores foram semelhantes.
Conclusão
Os valores de cilindricidade e circularidade comportaram-se de forma semelhante com o aumento dos parâmetros de corte (velocidade de corte).
A média e o desvio padrão dos valores responderam mais positivamente na velocidade de corte de 380 m/min, o que se dá pelo fato da aresta de corte da broca permanecer menos tempo em contato com a parede do furo.
Os parâmetros de superfície (R a, Rt e R z) obtiveram médias semelhantes, sendo que a 380 m/min foram obtidas somente 2.100 peças. Isso porque, com essa velocidade, os valores dimensionais dos furos foram reduzidos.
A altas velocidades, os valores de diâmetros foram piores.
Em comparação com a baixa velocidade, esse fenômeno ocorre devido ao aumento do atrito da aresta da ferramenta ao material usinado.
Mariana Landim Silveira Lima, José Renato Santos do Amaral Cardoso, Rosemar Batista da Silva, Luciano José Arantes, Antonio Vitor de Mello, Fabio Martinho Cezar de Freitas
A retificação normalmente é uma opção de usinagem, nos casos em que são exigidas elevadas precisões dimensional e geométrica, além de um excelente acabamento superficial, a exemplo dos blocos e cabeçotes de motores. Este trabalho apresenta os resultados de ensaios realizados em amostras de ferro fundido vermicular, após uma retificação plana com rebolo de carbeto de silício.
Mariana Landim Silveira Lima, José Renato Santos do Amaral Cardoso, Rosemar Batista da Silva, Luciano José Arantes e Antonio Vitor de Mello desenvolveram este trabalho pela Universidade Federal de Uberlândia (UFU), e Fabio Martinho Cezar de Freitas pela Saint Gobain Abrasivos, de Vinhedo (SP). Ele foi originalmente apresentado no 8º Congresso Brasileiro de Engenharia de Fabricação (Cobef), realizado de 18 a 22 de maio de 2015, em Salvador (BA). Reprodução autorizada.
Qualidade superficial do FoFo vermicular FV450, após retificação plana tangencial
Em geral, o processo de retificação é a última etapa da produção de uma peça, de modo que qualquer desconformidade pode significar a perda do produto e gerar grandes prejuízos.
No entanto, ainda há poucos estudos que avaliam de maneira estatística as relações entre os parâmetros de corte e os resultados desejados, pois são muitas as variáveis envolvidas neste ciclo e os ensaios experimentais demandam tempo. Ademais, na maioria das vezes eles são mais onerosos que os processos convencionais de usinagem, com a ferramenta de geometria definida.
Dessa forma, torna-se necessário identificar as variáveis do processo que mais afetam a integridade da superfície e os desvios dimensionais das peças. Assim, um trabalho investigativo nesta área é de grande importância.
As principais grandezas físicas envolvidas nas operações de retificação plana tangencial são apresentadas a seguir e ilustradas na figura 1:
vs
= velocidade periférica do rebolo (m/s) v w = velocidade periférica da peça (mm/s ou m/min) a p a e = penetração de trabalho (mm)
lc
= comprimento de contato rebolo/ peça (mm) H eq = espessura de corte equivalente ou espessura da camada de material arrancado pelo rebolo (mm)
No que se refere à penetração de trabalho, quando ela aumenta, provoca um acréscimo no número de grãos ativos e no tempo de contato. Isso faz com que cada grão abrasivo remova uma quantidade menor de material, resultando em cavacos mais alongados e finos.
Ressalta-se que há uma maior parcela de atrito e riscamento, desde o início da formação do cavaco até a sua expulsão, o que eleva a temperatura na região de corte e, consequentemente, deteriora o acabamento.
Embora a maioria dos trabalhos aborde a retificação de aços, ainda são poucos os estudos que tratam dos ferros fundidos. Estes são os principais materiais utilizados na fabricação de componentes de motores de combustão interna, como blocos, cabeçotes, eixos de comando de válvula e virabrequins.
Suas propriedades mecânicas são definidas pela microestrutura, mais precisamente pela forma em que o carbono encontra-se combinado.
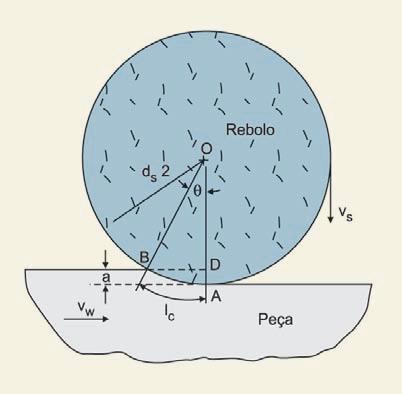
O ferro fundido é definido como uma liga terciária de ferrocarbonosilício, com teores de carbono geralmente acima de 2%, em quantidade superior ao que pode ser retido em solução sólida na austenita.
Além disso, o carbono resultante pode se apresentar parcialmente livre, na forma de veios ou então em lamelas de grafita.
A maioria dos ferros fundidos contém silício, entre 1% e 3%, e enxofre, podendo ou não apresentar outros elementos de liga.
Até a década de 1990, os ferros fundidos eram divididos em quatro classes: cinzento, maleável, branco e nodular.
A partir de 1999, uma nova classe começou a ser produzida: o ferro fundido vermicular.
Ele vem ganhando cada vez mais espaço na indústria automobilística, sendo atualmente utilizado na produção de blocos de motores, discos de freio, cabeçotes de cilindros e coletores de escapamento (figura 2).
Nos ferros fundidos vermiculares, a grafita apresenta-se predominantemente na forma de vermes, sendo interconectada com as extremidades arredondadas na forma de nódulos. Isso confere ao material uma boa resistência mecânica, tenacidade, resistência à fadiga, amortecimento e condutividade térmica.
O ferro fundido vermicular reúne propriedades intermediárias em relação ao ferro fundido cinzento e nodular (tabela 1), tendo mais vantagem em relação ao primeiro, com destaque para o aumento de 75% no limite de resistência, 40% no módulo de elasticidade e 80% na resistência à fadiga.
Nesse sentido, este trabalho apresenta os resultados da rugosidade e as imagens da superfície de amostras de ferro fundido vermicular, que foram retificadas com rebolo de carbeto de silício em várias condições de corte.
Ressalta-se que o acabamento superficial exerce um papel importante no comportamento dos componentes mecânicos, estando relacionado com a precisão de ajuste da máquina, condições de usinagem e tolerâncias de fabricação, que são especificadas de acordo com a aplicação da peça usinada.
Assim, fica clara a importância de se identificar o acabamento que
Fig. 1 – Grandezas físicas na retificação plana tangencial
Fig. 2 – Materiais fabricados em ferro fundido vermicular: bloco de motor a diesel (a); coletor de escapamento (b); disco de freio (c) e cabeçote (d) pode ser proporcionado em um material que ainda não conta com muitos dados de retificabilidade.
Materiais e métodos
Neste trabalho, foi usada uma retífica plana modelo P36, com 2.400 rpm, 3 HP e resolução no eixo Z de 5 µm (figura 3). A ferramenta de corte utilizada foi um rebolo convencional de carbeto de silício (SiC), com especificação 39C46KVK (da Saint-Gobain
Abrasivos) e as seguintes dimensões: 254 x 25 x 76 mm.
Foi selecionado o fluido de corte sintético de base vegetal ME-3, em solução aquosa na proporção de 1:20.
O bocal foi posicionado de forma tangente ao rebolo, a uma vazão de 545 L/h (figura 4).
A peça foi fabricada no ferro fundido vermicular FV450, em formato de barra retangular, com base quadrada e dimensões de 49 x 18 x 19 mm.
Na tabela 2, são apresentadas algumas das principais propriedades do ferro fundido vermicular.
Foram empregados os seguintes parâmetros de corte: velocidade periférica do rebolo (v s) de 32 m/s, velocidade longitudinal da peça (v w) de 10 m/min, profundidade de dressagem (ad) de 10 µm, e dois valores de penetração de trabalho (a e): 15 e 30 µm. Foram realizados quatro ensaios, incluindo a réplica. O critério para o fim de cada ensaio foi um volume de material removido de 55,86 mm3 . As variáveis de saída utilizadas foram os parâmetros de rugosidade (R a e R z) e as imagens das superfícies usinadas. A medição dos parâmetros da rugosidade foi realizada com o
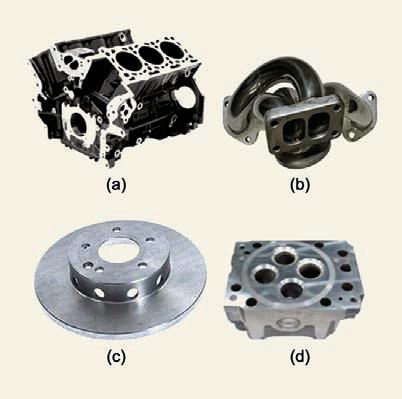


Fig. 3 – Retificadora plana tangencial com o sistema rebolo-peça Fig. 4 – Posicionamento do bocal com o fluido de corte
auxílio de um rugosímetro portátil, modelo SJ201P (da Mitutoyo), com resolução de 0,01 µm.
Foram utilizados um comprimento de onda do filtro (cut-off) de 0,8 mm e um de avaliação de 4 mm.
As medições foram realizadas perpendicularmente à direção do avanço longitudinal da peça, sendo a primeira medição a 4,5 mm da aresta e as demais equidistantes de 10 mm, conforme a figura 5.
Após o processo de retificação, todas as amostras foram submetidas a procedimentos metalográficos, para verificar se houve danos na superfície. Elas foram devidamente limpas e preparadas para a avaliação das superfícies retificadas, a qual foi feita em um microscópio eletrônico de varredura.
Resultados e discussões
A seguir são apresentados os resultados da rugosidade e as análises realizadas das superfícies obtidas após a retificação do ferro fundido vermicular, em diferentes condições de corte.
Rugosidade
Os resultados médios para os parâmetros de amplitude, rugosidade aritmética (R a) e rugosidade total (R z), são apresentados nas figuras 6 e 7, respectivamente.
Estes valores foram obtidos após quatro passes, com penetração de 15 μm, ou dois passes, com 30 μm, totalizando 60 mm ao final de cada ensaio.
Na figura 6, nota-se que há um crescimento da rugosidade R a, com a penetração de trabalho a e . Essa tendência está relacionada com o aumento da espessura de corte equivalente, a qual é consequência direta do aumento da penetração de trabalho.
Isso implica em cavacos com dimensões maiores, os quais, com a progressão do corte, se agrupam e podem causar o empastamento do rebolo.
Sabe-se que dependendo da estrutura do rebolo, os seus poros não são capazes de alojá-los. Assim, o cavaco alojado no rebolo diminui a eficiência na retificação, aumenta os esforços de corte da ferramenta sobre a peça e, consequentemente, compromete a superfície retificada.
Tab. 1 – Comparação entre as propriedades físicas e mecânicas dos ferros fundidos cinzentos, vermiculares e nodulares.
Propriedade Resistência à tração (MPa) Módulo de elasticidade (GPa) Alongamento (%) Condutividade térmica (W/mK) FoFo cinzento FoFo vermicular FoFo nodular 250 450 750
105 145 160
0 48 1,5 37 5 28
Capacidade relativa de amortecimento 1 Dureza (BHN 10/3000) 179-202
Resistência à fadiga (MPa) 110 0,35
0,22 217-241 217-255 200 250
Tab. 2 – Características do ferro fundido vermicular.
Matriz
Forma Nodular Partículas (p/mm²) Grafita
Tamanho (%) 8 7 6 5 4 Dureza Brinell Microdureza (5/750) na perlita (HV 01)
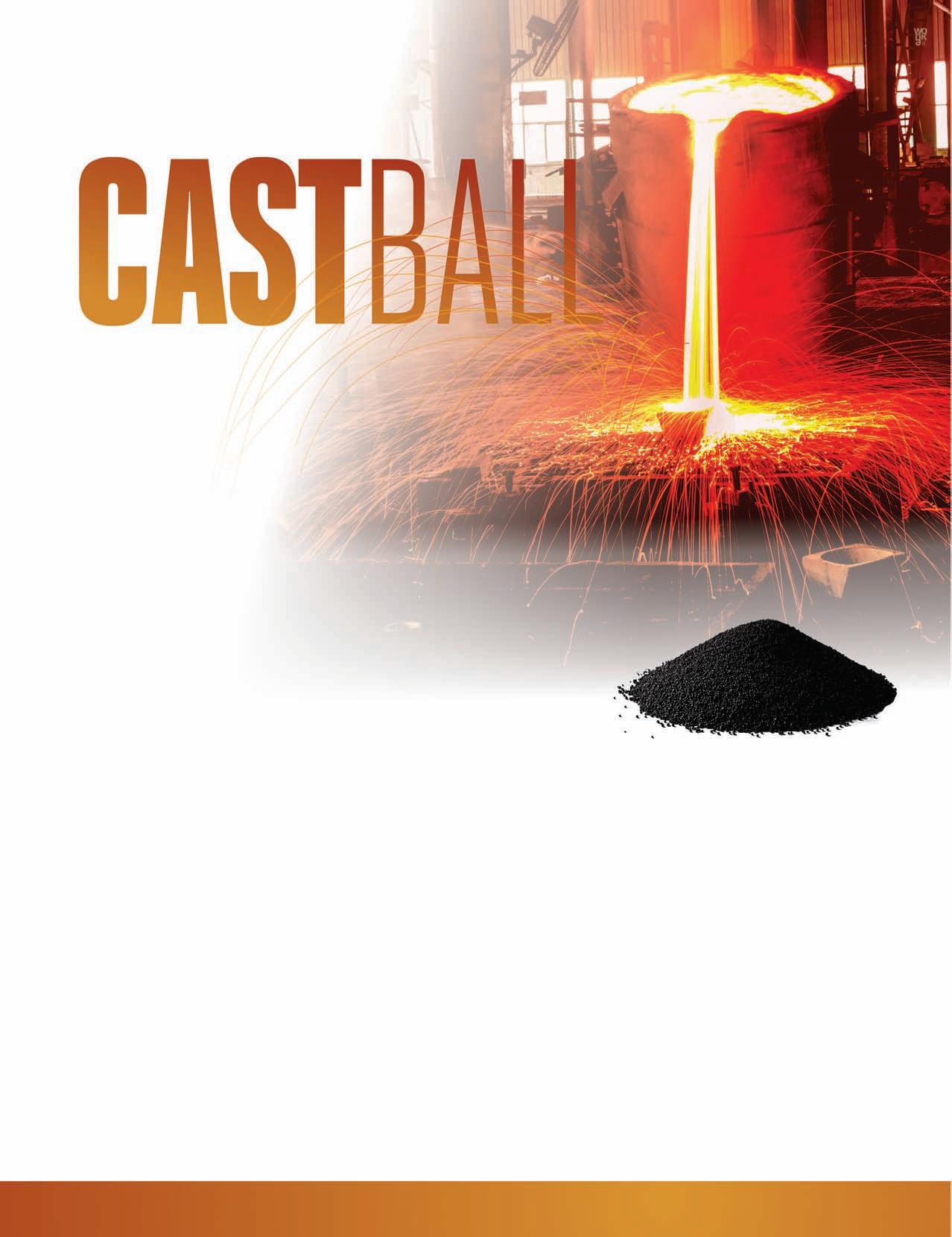
Além disso, a penetração de trabalho possui relação direta com a área de contato entre a peça e o rebolo, ou seja, com o seu aumento, cresce também a área de contato e, consequentemente, as forças de corte, afetando ainda a qualidade da superfície retificada. Esta pode ter sido a causa da elevação de ambos os
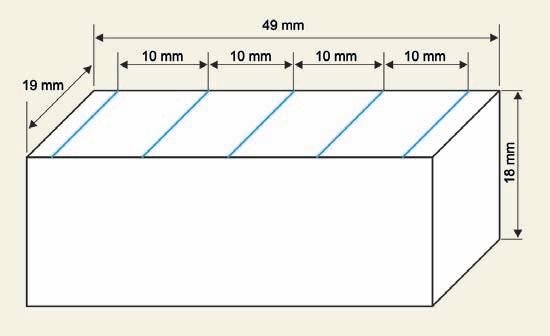
Fig. 5 – Regiões de medição da rugosidade na superfície da peça
Fig. 6 – Valores médios da rugosidade R a, obtidos com a variação da penetração de trabalho Fig. 7 – Valores médios da rugosidade R z, obtidos com a variação da penetração de trabalho
parâmetros de rugosidade estudados neste trabalho.
No entanto, mesmo com a elevação da rugosidade R a, os valores obtidos ficaram abaixo de 0,30 mm, os quais são bem inferiores ao limite máximo de R a = 1,6 mm (valor de referência usualmente adotado para processos de retificação de semiacabamento).
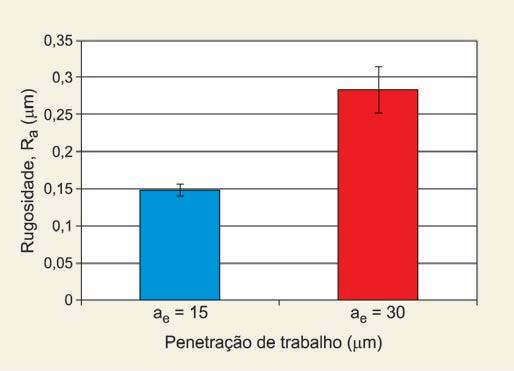
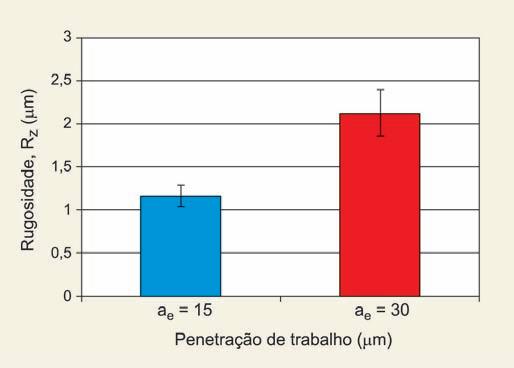
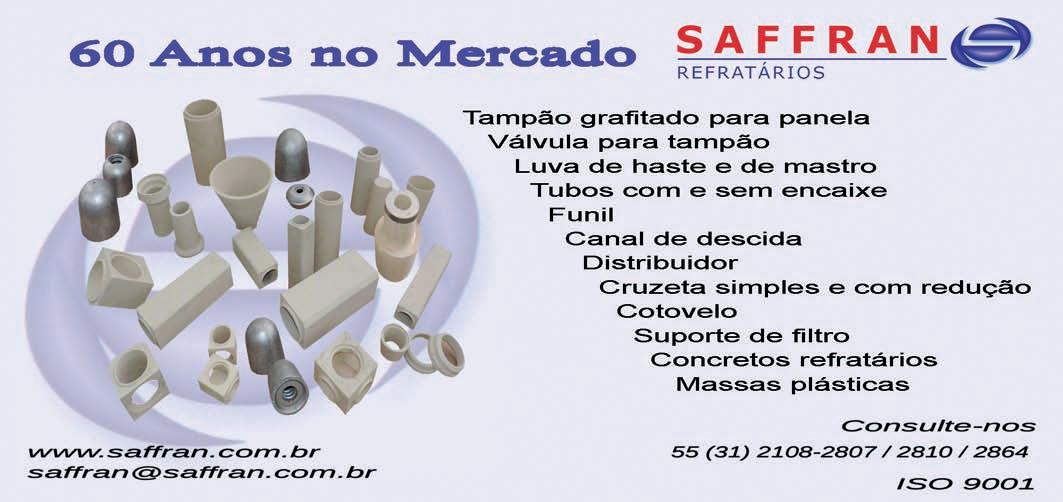
Estes valores indicam que as condições de corte empregadas nessa pesquisa (velocidade do rebolo, velocidade da peça, penetração de trabalho, rebolo e fluido de corte) foram adequadas para a retificação plana do ferro fundido vermicular FV 450.
Na figura 8, são apresentados os valores de rugosidade (R a) obtidos em cada uma das cinco posições em que o apalpador do rugosímetro foi colocado durante a medição, tanto para o ensaio principal quanto para a réplica, utilizando-se os dois valores de penetração de trabalho descritos anteriormente.
Nesta mesma figura, observa-se que nos ensaios principais, para cada penetração de trabalho, praticamente não houve diferença entre os valores de rugosidade obtidos. Entretanto, a diferença foi significativa para a réplica.
O aumento da rugosidade entre os ensaios 1 e 2 pode ser atribuído à superfície do rebolo resultante da operação de dressagem realizada.
Não é tarefa fácil garantir a uniformidade das dimensões de um grão abrasivo, mesmo adotando um procedimento rigoroso de dressagem, pois de uma para outra pode-se variar o número de grãos expostos, assim como a quantidade de ligante que pode atritar com a peça.
A réplica de cada ensaio pode ter sofrido influência da dressagem e isso refletiu no acabamento da superfície em relação ao ensaio principal.
Análise da superfície usinada
Na figura 9, são apresentadas as superfícies do ferro fundido vermicular retificadas para as diferentes condições de corte. Essas imagens se referem ao ensaio principal e réplica, para a menor penetração de trabalho.
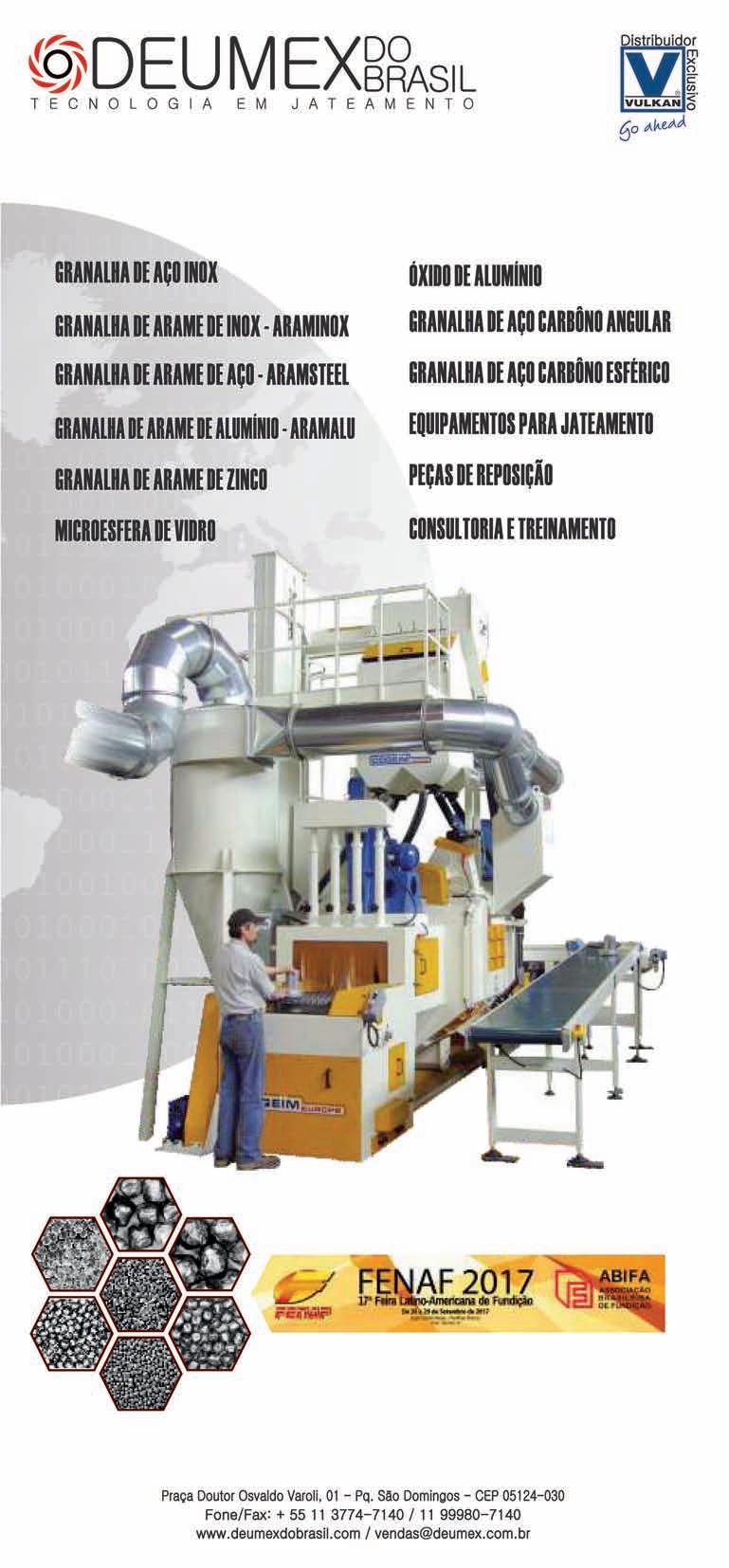
Fig. 8 – Valores da rugosidade R a, de acordo com o posicionamento do rugosímetro
Observa-se que as marcas de avanço dos grãos são semelhantes.
Nota-se também a presença de algumas áreas com deformações plásticas e de fluxo lateral de material, causado pelos abrasivos, mas que ainda assim não elevaram a rugosidade para valores acima de 1,6 mm.
Além disso, é importante ressaltar que não foram observadas trincas perpendiculares à superfície nas amostras, nem a presença de queimas de aspecto visual.
A figura 9 mostra ainda o ensaio principal e a réplica, para a maior penetração de trabalho. De forma análoga para a menor penetração, as marcas de avanço nos dois ensaios são bem parecidas, com riscos visíveis ao longo da direção de avanço da ferramenta. Ao comparar as duas imagens da figura 9 (cujas escalas são as mesmas) é possível observar que as marcas longitudinais nas superfícies das primeiras são mais largas e não apresentam a mesma continuidade, como aquelas após a usinagem com a menor penetração de trabalho. Esta diferença já era esperada, pois à medida que se aumenta a penetração de trabalho na máquina-ferramenta, os grãos também penetram mais na peça, refletindo na rugosidade.
O parâmetro R z foi mais sensível a esta alteração, que detecta os vales mais profundos em todo o comprimento de amostragem selecionado.


Conclusão
As seguintes conclusões podem ser tiradas deste trabalho:
Com o aumento da penetração de trabalho de 15 para 30 µm, os parâmetros de rugosidade R a e R z também aumentaram, conforme esperado. Todos os valores de R a obtidos foram menores que 1,6 µm e, portanto, ficaram dentro da faixa de rugosidade aceitável para o processo de retificação de semiacabamento. No que se refere à superfície e topografia da peça, foram observadas regiões com deformações plásticas e fluxo lateral de material, causados pela passagem dos grãos. Porém, não foi observada a presença de trincas ou queimas de aspecto visual.
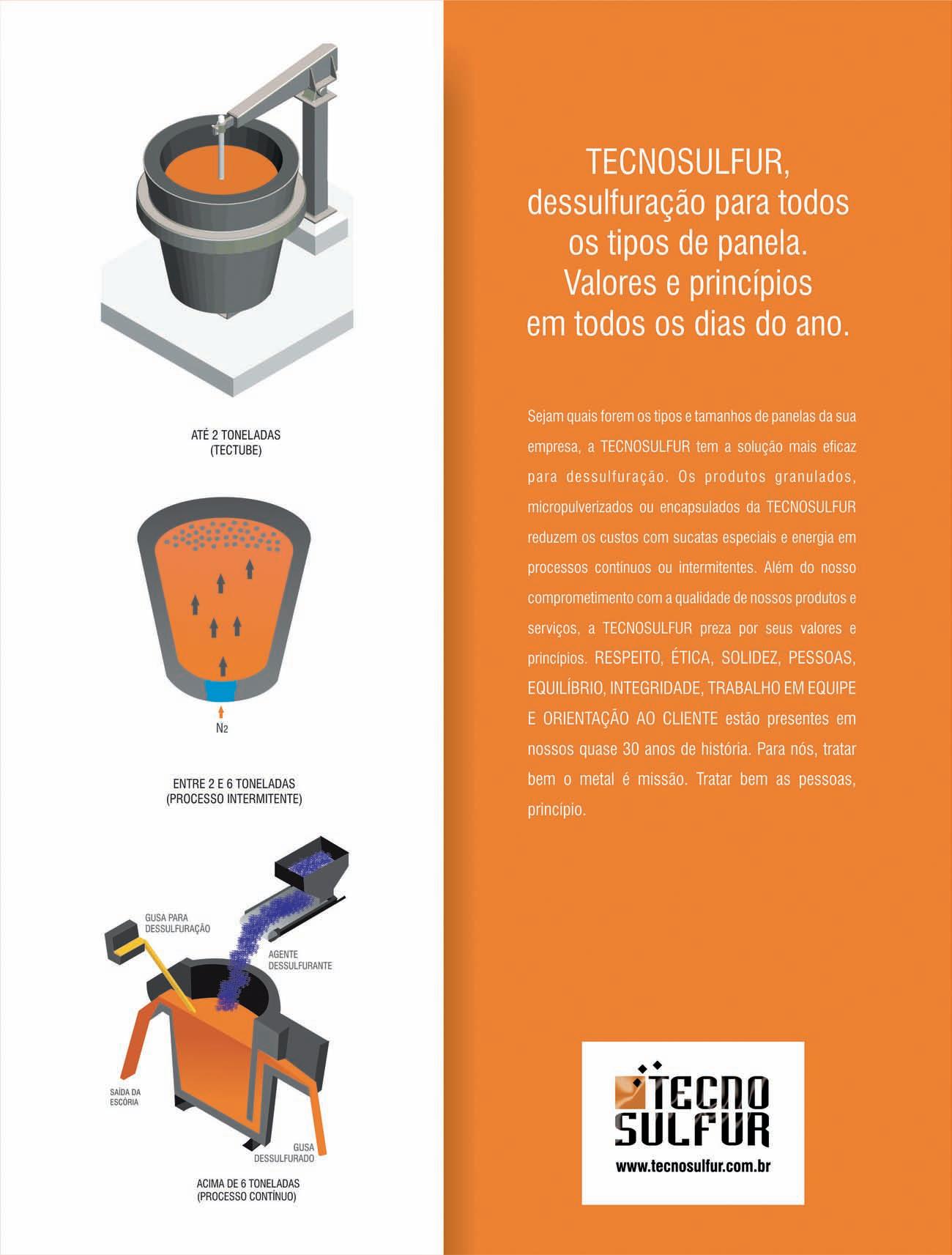