
16 minute read
Pandemic Fuels
Pandemic Fuels Data Center Growth
With employees working remotely, school being held virtually, and everyone being entertained via the Internet during the COVID-19 crisis, growth of these mission-critical facilities accelerated and will continue to do so.
By Dave Fanning, Executive Managing Director and Practice Leader, Data Center Advisory Group, Cushman & Wakefield
In a year full of turmoil and strife caused by an unexpected pandemic, data centers were quickly recognized for their crucial presence in all lives, for maintaining communication and knowledge during a period of sudden change for humanity.
Data center operators and major services held fast throughout the troubled, early days as they were identified as truly mission critical. Companies large and small rapidly scaled up workloads with cloud service providers so employees could access their normal applications; schools and universities moved online as students attended classes remotely; and all people looked to the Internet for entertainment as they stayed home for days at a time.
Several trends that were beginning prior to the year accelerated rapidly throughout 2020. Businesses were forced to continue their IT transformation with a suddenly fully remote workforce, and many moved workloads straight to major cloud services. While most of this will remain in the public cloud environment, costs and regulatory concerns may lead to some moving to a colocation or even on-premises situation. As a result, increased cloud adoption and hybrid IT scenarios are fueling growth in the data center sector for both established and emerging markets.
Development Pipeline
An active development pipeline is a useful indicator of market strength, as it signifies continued local demand leading to the creation of ever-greater supply. Development under way shows that local authorities are willing to approve new builds, that power and fiber were obtainable at the site, and that project financing is available.
Few developments in the data center realm are launched speculatively. More often an anchor tenant has signed on for a significant portion or all of an initial phase. Signing a major hyperscale, corporate or government tenant also assists in the creation of the local ecosystem, as entities with similar requirements often follow.
While the recent pandemic has caused construction difficulties across all sectors of commercial real estate, data centers have been less affected than most, as their early designation as essential operations indicates. Construction continued at most locations, and although supply chains occasionally tightened, most projects saw minimal disruption. This is reflected in the overall increase in construction from our previous study to this year.1 Our 2020 report tallied 1.6 gigawatts in progress across the 38 markets re-
350
300
250
200
150
100
50
ACTIVE DEVELOPMENT (MW) TOP TEN
Northern Virginia Singapore London Sydney Silicon Valley Frankfurt Dublin Chicago Atlanta Nashville
DC-Northern VirginiaSingaporeLondonSydneyBay AreaFrankfurtDublinChicagoAtlantaNashvilleSeoulTokyoMumbaiLas VegasJakartaBeijingPortlandAmsterdamTorontoQueretaroHong KongShanghaiParis JohannesburgSalt Lake CityOsakaSao PauloDallasPhoenix NYC-Northern NJZurichMelbourneMunichLagosMarseilleMilanBerlinMadridWarsawLos AngelesDenverSeattleMontrealColumbusBostonVancouverOslo Reykjavik 0
Source: Cusman& Wakfield Research
viewed, while this edition totals 2.9 gigawatts across 48 markets. Organizational needs and the move to modernize information technology have pushed both operators and hyperscalers to action.
Markets leading the charge in terms of active development include many of the global primary markets: Northern Virginia, Singapore, London, Sydney, and Silicon Valley round out the top five, with Frankfurt, Dublin, and Chicago following. Several of these markets are experiencing shortages of potential sites (London, Sydney, Silicon Valley), power (Frankfurt, Dublin), or both (Singapore), and it remains to be seen if local concerns over further builds will lift throughout 2021. Of note are the number of secondary markets where the colocation sector continues to blossom, including Seoul, Mumbai, Jakarta, Portland, and Queretaro. These fast-growing regional hubs are emblematic of the smaller market expansion that began in earnest in 2020, and expectations are high for similar growth worldwide.
Access to the Internet has now exceeded half the global population with no end in sight. Between increasing demand from existing users, the increase in corporate cloud demand, and new geographies adding access, we expect strong demand to continue for data centers around the world. n

Challenges of Moving Manufacturing Out of China
When moving manufacturing out of China, there’s a lot to consider, e.g., employment contracts, retrieval of tooling and molds, IP protection, and taxes and fees.
By Rosemary Coates, Executive Director, The Reshoring Institute; and President, Blue Silk Consulting
There is plenty of manufacturing capability around the world for consumer goods, PPE, testing equipment, medical devices, consumer goods, and other industrial products. So why are companies reshoring their manufacturing operations now?
The Tax Reform Act of 2017 helped. The 301 China penalty tariffs gave a little push. But the global pandemic made executives acutely aware of their global supply chain risks and vulnerabilities and provided an opportunity to rethink their global manufacturing strategy. New strategies typically include at least some capacity for manufacturing and sourcing critical goods in America.
Pharmaceutical manufacturers were among the first to consider reshoring in an attempt to reduce America’s dependence on basic ingredients coming from China and India. Other industries are now actively following, including automotive, plastics, and machinery. But how easy is it to extract your manufacturing from China or end your relationships with suppliers and contract manufacturers?
It’s not so easy.
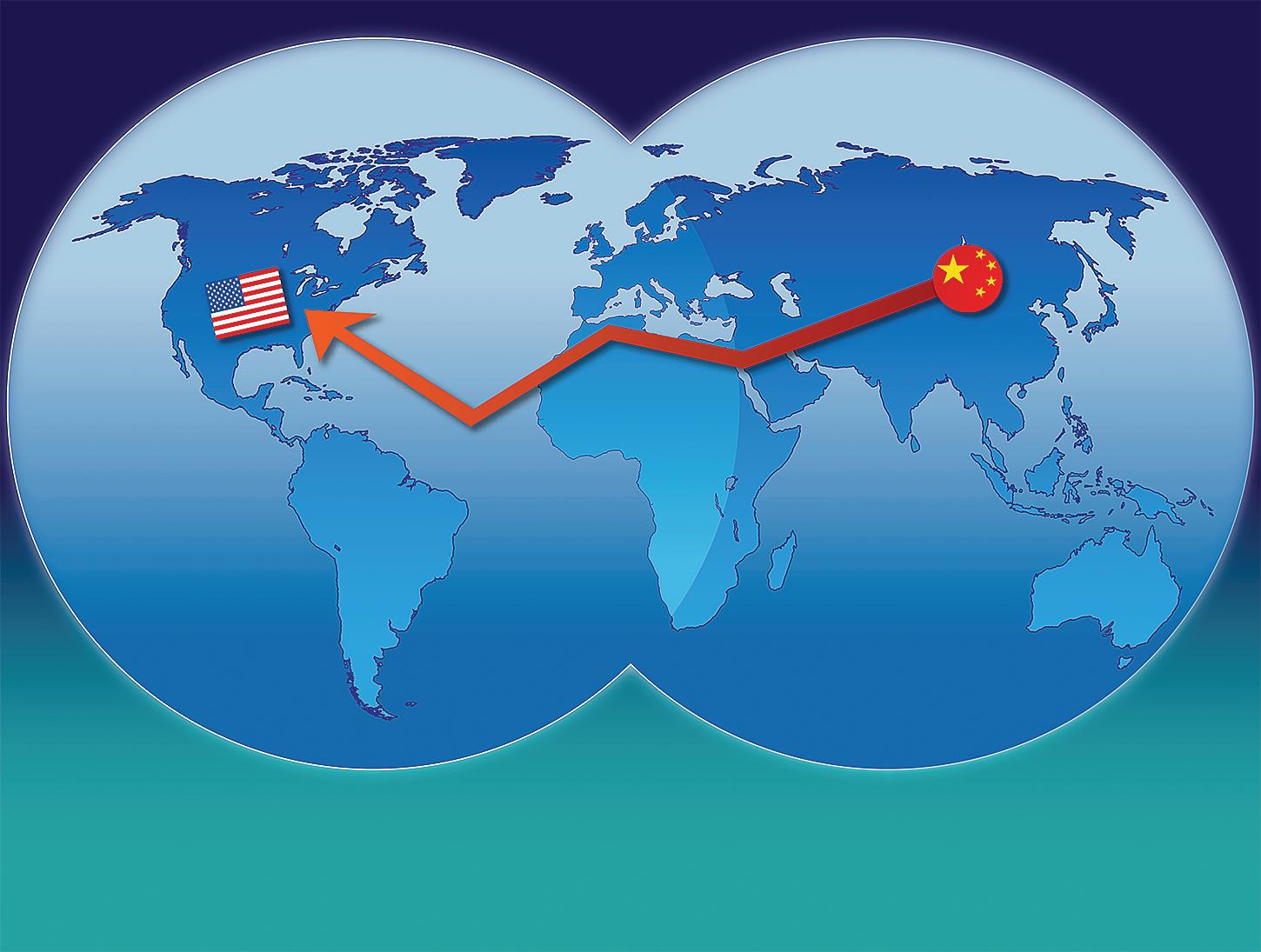
Global Supply Chains Sourcing from China
China includes consumer products, finished goods, and parts that go into other finished goods around the world. This is because, over the past 20 years or so, China has become the low-cost production leader, particularly for high-touch, high-laborcontent processes such as electronics assembly and sewing. This production cost profile (high-touch, high-labor-content) is well suited to low-cost countries such as China, Vietnam, Bangladesh, Mexico, and others.
From a market economy perspective, this is appropriate. But strictly economic decisions have not served the markets very well in this pandemic emergency, with so many human lives at stake. Having no capacity for producing products such as PPE, medical devices, and pharmaceuticals in our home country leaves us vulnerable and completely dependent on China.
The pandemic has been a wakeup call and a catalyst for reshoring, or at least for considering a multicountry manufacturing strategy. The U.S. government has also started to consider an industrial policy that supports critical industries and may even offer incentives for reshoring. But leaving China to return production to the U.S. is likely to be complicated and expensive.
Leaving China
Even if some industries are deemed critical and incentives are
provided, there are still difficult hurdles in leaving China and redirecting supply chains to a third country or toward reshoring to America. Companies cannot expect to simply pack up shop, lock the doors, turn out the lights, and move back to the U.S. It’s complicated.
The decision to leave China isn’t an easy one. With nearly 350 million people in China’s middle class and growing, China is likely to be a company’s biggest target market over the next 20 years. As the Chinese middle class grows, so do its disposable income and the desire for all kinds of products, particularly those with Western brand names. To serve this market, many manufacturers are deciding to leave at least some of their production in Asia.
Further, America’s relationship with China has deteriorated significantly over the past four years. Not only has the anti-China rhetoric ramped up in America, but also the anti-America rhetoric is equally as bad in China. The Chinese government and the Chinese Communist party have made no secret of their unhappiness with American trade and sanctions policy. They aren’t going to make it easy for companies to move manufacturing out of China.
Let’s examine the various facets of the Chinese operation:
• • The Chinese Employees — In China, most workers are hired under employment contracts lasting one to two years. If a company closes its factory in China, the expectation is that all employees will be paid until the end of their contract. This is often a costly surprise to Western companies. Before deciding to leave China, companies should carefully check their responsibilities outlined in their employment contracts.
It’s best to consult with an attorney familiar with Chinese employment law — perhaps one with offices in the U.S. as well as China. In-country local Chinese law firms may not have your best interest in mind. It’s best to use a multinational law firm with deep China experience.
• • Tooling and Molds — Packing up and shipping or trying to retrieve tools and molds from a Chinese manufacturing site can also be problematic. In the past, a Western manufacturer would send machine tools or molds to a Chinese original equipment manufacturer (OEM), or to their own Chinese manufacturing site. These tools and molds, sometimes worth hundreds of thousands of dollars, are needed to produce products.
If a company does not take steps to clearly identify ownership — and signs an agreement to that effect, including serial numbers positively identifying each item — it may never see the tools and molds again. This is because the Chinese believe that they have been given the equipment, and it becomes part of the plant’s assets and infrastructure. The Chinese government may not allow the machines, tooling, and molds to be exported. Your contract, that you thought clearly defined ownership, may not be honored in a Chinese court.
Blueprints and molds that are made in China for your production line are yet another issue to consider. If a Chinese manufacturer has your blueprints and they outsource the mold-making to a subcontractor, it’s a sure bet that they will continue to produce your goods long after you are gone. The Chinese mold-maker is likely to claim ownership of the mold, even though you paid to have it made. In fact, the Chinese company may have registered your brand and logo in China without your knowledge.
• • Manufacturing Methods Intellectual Property —
When a company leaves China, it also leaves behind its manufacturing intellectual property if the Chinese have been taught confidential production methods. We’ve all heard the horror stories about IP protection, copying, and counterfeiting in China.
To protect their IP, most Western companies now register their patents and brands in China. But production methods and raw materials aren’t always as well protected. A company may have taught the Chinese factory how to make its product — methods the Chinese factory is likely to continue to use to produce the same product under a different name. In addition, the Chinese factory now knows all of your raw materials and parts suppliers and potentially could source the same materials from the same suppliers after you are gone.
• • Taxes and Fees — In addition to paying out employment contracts, there may be other regulations that must be considered. China’s Commerce Department has issued guidelines for withdrawal from China by foreign investors. China’s law requires that foreign investors inform creditors of the closing, settle all outstanding taxes, pay all pending debts, liquidate property, and de-register the business. In addition, companies may be required to pay closure taxes. All this takes time and money, and often comes as a surprise to Western companies in the process of reshoring.
Obtaining a permit to leave may be yet another hurdle. Depending on your industry, the Chinese government may not want you to leave the country. High-tech companies, in particular, may be subject to extended exit permit times. Anything that would be considered a strategic industry or strategic technology is likely to experience delays in the permitting process.
Cultivate a Second Life for Decommissioned Power Plants
As the need for industrial development grows and requirements for coal-fired decommissioning increase, land repositioning can offer a mutually beneficial solution.
By Courtney Dunbar, Site Selection and Economic Development Leader; Jeff Pope, Facility Decommissioning and Demolition Services Manager; Burns & McDonnell
The generation landscape for utilities is in a state of constant change. The decarbonization movement is driving difficult decisions as coal-fired power plants close amid the transition to renewable generation. But there is opportunity within that disruption.
Decommissioned power plant sites offer industrial developers a great deal of opportunity — specifically, decades of well-maintained assets. The majority of these facilities were built more than 50 years ago with access to everything they needed to operate — connections that would require extensive time and capital investments to put in place today. Rather than seeking greenfield locations, industrial developers should take a closer look at repositioning these sites.
Revealing Exceptional Value
Coal-fired power plants are sprawling sites, teeming with invaluable assets. To establish a buffer between facilities and the communities served, these plants were often placed on hundreds of acres with distribution lines and substations installed to transmit the power generated. Infrastructure to accommodate water and wastewater needs was constructed, and multimodal transportation connections were established to bring materials in and out of the plant.
Industrial developers can take advantage of these well-maintained, high-value assets and breathe new life into their purpose. For example, distribution lines that sent power out can be reversed to bring power into a new industrial facility, and a rail or barge connection that brought coal to the plant can be used to take products and materials in or out of a facility. Developers can take advantage of the permitting and regulatory hurdles that had been overcome by the utilities in years past, generating a potential savings today in both time and money.
Repositioning of expansive decommissioned sites also offers multiuse possibilities. Most industrial facilities don’t require the hundreds of acres that former power plant sites offer. Therefore, a campus arrangement could position several viable solutions within one site, such as a solar field for the utility or developer as well as multiple locations for different facilities — offering load gains for the utility and a costeffective green approach for industrial developers.

Mapping Out the Possibilities
To optimize a property and its correlating repositioning benefits, a utility should develop a master plan for a future industrial campus on its site before any decommissioning begins. This approach would commence with an assessment of the site to determine what should remain after decommissioning, and what may be lacking when complete. It is then advised to undergo a thorough analysis of both natural and built-environment attributes to achieve a vision of property diligence and any potential impediments to development.
Once existing conditions are understood, a general regional market review can determine local- and statelevel tax advantages, industrial cluster presence, and any high-level property assets that might align within specific markets. From there, the property can be decommissioned to meet the design requirements through development of a master plan to directly position it to specific industrial audiences.
This robust review and flexible development plan is thorough and granular in its details, which is essential. After all, not every asset will appeal to every industry, and not every industry that needs a certain asset exists in a region. For example, grain unloading in agricultural areas would use the site differently, and require different assets, than a sand and gravel mining area. Therefore, a thoughtful master plan can cast the widest net based on the site location, assets, and market.
Including the master planning upfront in the decommissioning process can also help pinpoint potential challenges and adjust the design or business case accordingly. For instance, aging plant facilities might require asbestos or subsurface remediation or be located on protected wetlands — situations that could increase liabilities and costs that could exceed the value of the property. Or an existing rail connection might be viewed as an asset but is so outdated that the rail line no longer serves the area. By identifying these possible limitations early in the process, a utility can have confidence in the direction of its approach, making decommissioning more cost-effective and focused on its end goal.
Due to the broad potential markets and industries for repositioning, a utility should involve its economic development staff — either internally or from the local and/or regional level — to discuss the goals and targets for the site. It wouldn’t be surprising for the site development to include a marriage of public and private investments; thus, economic development insight is vital. The utility should also consider partnering with a full-service firm to provide preferably both the decommissioning and master-planning services. If a firm can offer guidance and continuity from site and facility assessments, environmental remediation, design, construction, and more, the utility will be able to secure the optimal solution.
Establishing Benefits for Everyone
Repositioning of decommissioned power plant sites is a win-win for utilities and industrial developers. Utilities can convert unused sites, with their potential safety and environmental hazards, into increased load capacity and a boon for their local communities. Doors closing on coal-fired power plants are eliminating jobs nationwide. By bringing established assets like these sites to market, utilities can be part of generating industrial growth in their regions and reinvigorating their communities’ labor opportunities.
At the same time, industrial developers can streamline cost-effective site development by utilizing existing sites that boast valuable assets. Already ideally positioned efficiently for operations, decommissioned power plant sites allow industries to start fresh — but with the most essential connections already in place from the start.
Repositioning offers a unique, mutually beneficial opportunity for utilities, developers, and communities alike. Rather than removing everything during decommissioning, take the time to understand the value of existing assets and put them back to work. n
Challenges of Moving Manufacturing Out of China – Continued from page 69
The Way Forward
There is a lot to consider when designing a new global manufacturing strategy. Many things are now in flux, including the global trade wars, domestic industrial policy, and incentives. With the U.S. presidential election of Joe Biden and Kamala Harris, changes in policy will affect global relationships. Katherine Tai has been nominated as the next U.S. Trade Representative, and with her significant background in China relations and negotiations, the U.S. relationship with China is likely to improve. But so much damage has been done during the past four years that improving and changing the ChinaAmerica relationship now is a daunting task that will surely take time.
So many companies make the mistake of simply comparing labor costs when determining their reshoring pathway. But there is so much more to a reshoring decision, especially within the context of a global pandemic and the resulting global recession. There is no sweeping correct answer applicable to all enterprises in all countries. Microeconomics of the firm will drive the final decision to reshore or not. n
Advertiser Page Advertiser Page Advertiser Page
ALABAMA Alabama Department of Commerce 11 contact@madeinalabama.com www.MadeInAlabama.com
FLORIDA Enterprise Florida, Inc. tvanderhoof@EnterpriseFlorida.com www.FloridaTheFutureIsHere.com/ Freedom 45
GEORGIA Georgia Department of Economic Development 15, 17 www.Georgia.org IDAHO Emsi 72 www.EconomicModeling.com KENTUCKY Kentucky Cabinet for Economic Development 39 www.BuildReadyKY.com CED.ky.gov MARYLAND Maryland Department of Commerce 29 Commerce.Maryland.gov open.maryland.gov/innovation MISSISSIPPI Golden Triangle Development Link 67 info@gtrlink.org www.GTRLink.org Mississippi Development Authority 5 jrounsaville@mississippi.org www.Mississippi.org/Opportunity MISSOURI Missouri One Start Department of Economic Development 7 www.MissouriOneStart.com
NEVADA NV Energy www.NVenergy.com/EconDev www.NevadaSiteLocator.com
NORTH CAROLINA Economic Development Partnership of North Carolina www.edpnc.com Person County Economic Development swilborn@personcountync.gov www.PersonCountyEDC.com C3
9
63
OHIO JobsOhio www.OhioIsForLeaders.com C4 SOUTH CAROLINA Santee Cooper wmccall@SanteeCooper.com www.PoweringSC.com TENNESSEE Tennessee Department of Economic & Community Development www.TNecd.com 35
51
TEXAS Lubbock Economic Development Alliance carolyn.rowley@lubbockeda.org www.LubbockEDA.org Tex Americas Center Eric.Voyles@TexAmericasCenter.com www.TexAmericasCenter.com 53
61
OFFSHORE Invest Puerto Rico info@investpr.org wwwInvestPR.org C2, 1
Invest Turks and Caicos Islands 23 info@investTurksandCaicos.tc www.InvestTurksAndCaicos.tc
US Virgin Islands EDA www.InvestUSVirginIslands.com 20, 21
The world has changed. The importance of data hasn’t.
WHATEVER YOUR SITUATION, EMSI DATA IS HERE TO HELP.
FOR SALE
COMMUNITY BROKER
EXECUTIVE helping businesses recover adapting to a new market assessing location needs and options