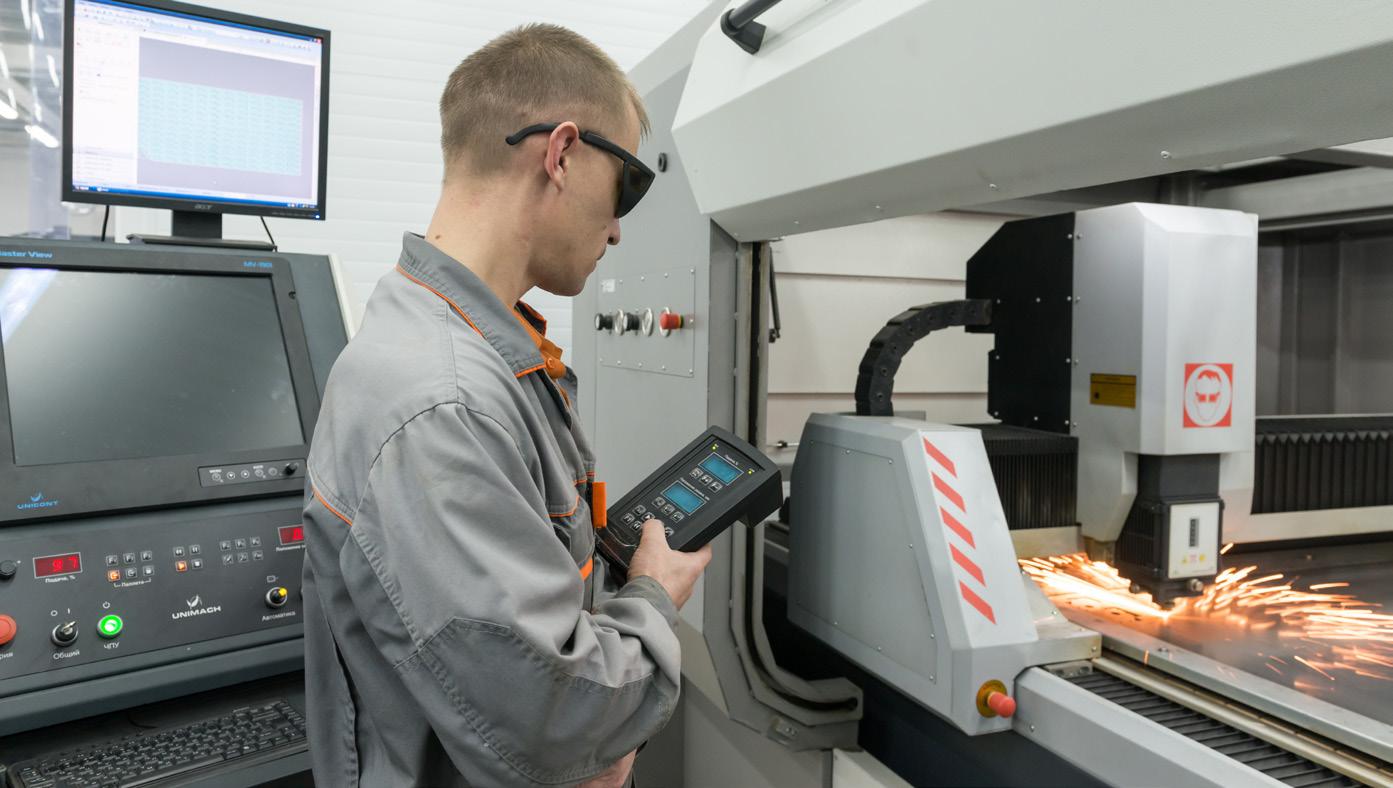
13 minute read
Companies, Organizations Get Creative in Workforce Development
from Blueprint 2022
Arkansas companies that rely on skilled labor have been working overtime to attract help. Increasingly, companies have partnered with local schools and community colleges to provide advice and expertise to training programs. This ensures students learn the most in-demand skills, virtually guaranteeing them a job after graduation.
Here are a few companies and organizations that are setting the pace in worker training and development, both internally and externally.
ABC ARKANSAS
As president of Associated Builders and Contractors, Bill Roachell hears from his member companies all the time about the challenges of finding good help to accommodate their growth and to replace workers who are retiring.
The demand is so great, ABC has implemented its own apprenticeship and training programs to help boost the number of hirable workers coming out of twoyear colleges and those headed straight for the workforce after high school. And they’re always looking at new and faster ways to get people looking to change careers the basic instruction they need to get into the job market.
“We’ve got a new program coming online that we call fast-track training,” he said. “Over an accelerated timetable, we can get people OSHA 10 trained, we can get them their CPR first aid, we can get them their basic core construction. Maybe a little bit in electrical, a little bit in plumbing, and then get those people moving into the workforce.
“There’s a ton of opportunity out there right now. For people who maybe were displaced by COVID who are looking to get back into the workforce, this will help them get a better job than they had before.”
Roachell said he’s been impressed with the shift many Arkansas high schools and community colleges have taken to emphasize skilled career training in recent years, measures that ABC has partnered with several schools to provide throughout the state.
“These programs are helping us recruit new and better talent into the construction workforce,” he said. “A lot of these kids are in rural communities and they
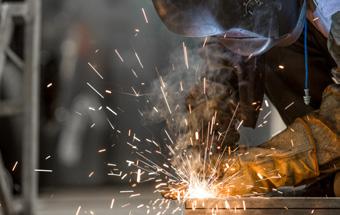
FOUR FAST FACTS
WELDING • One of the foundational skilled careers, welders are in demand across a wide range of industries. • Demand for welders in Arkansas expected to outpace the national average. • Train in school or through an apprenticeship program. • Construction, manufacturing and utilities are just three areas desperate for welders. INTERESTED? See Page 47 for more.
really can’t see outside of that to know the opportunity that is out there. These education programs do a good job of bringing industry to those kids and saying, 'Here’s what you can do.'
“When these kids come out and they get an apprenticeship, they’re working. They’re not accruing all the debt they would get if they went to a traditional four-year school. It’s just a great model and I think it will just continue to grow in popularity.” ETHAN CASH
ENTERGY ARKANSAS
AGE: 17 EDUCATION: Senior, Vilonia Pathways Academy SNAPSHOT: As part of the inaugural class at VPS, Cash is getting a head start on his career through
As utilities become more sophisticated and cus- skilled training and exposure to tomer expectations have changed, the demand for various job opportunities. front-line workers with advanced technical skills is high. So says Michael Considine, vice president of distribution operations for Entergy Arkansas. “Entergy Arkansas in particular, and Entergy as a whole, is making tremendous investments in people WHY DID YOU CHOOSE TO FOLLOW THE ACADEMY COURSE OF STUDY? WHAT’S DIFFERENT ABOUT IT? and infrastructure around grid modernization,” he I have always thought about doing said. “We are almost done with the installation of something in construction, and this 3 million advanced meters across all of Entergy’s was a great opportunity for that. I footprint, and with the type of data we now have have the goal of becoming an elecon customer usage and the systems that are put in trician and making that my career. place, we can start to respond to unplanned outages much more quickly. “Along with that comes a lot of distributed automation and distribution automation that really helps us plan for the future around a self-healing WHAT TECHNICAL SKILLS ARE YOU LEARNING OR HAVE LEARNED THROUGH THIS PRO GRAM? grid. We’re installing equipment on our grid today We are learning about BIM (buildthat will help us transfer the electricity demand of ing information modeling) in the customers around and it will start to anticipate a construction industry. I’m also problem before it becomes an outage.” learning all kinds of hands-on
Training programs have had to keep up with skills that will help me in the these technical advancements. For this, Entergy future. created the H-VOLT Academy in partnership with UA Pulaski Technical College in North Little Rock, and also sends new hires to lineman boot camp VILONIA PATHWAYS ACADEMY IS SET UP VERY DIFFERENTLY THAN THE SCHOOLING YOU HAVE HAD THUS FAR. HOW HAVE YOU ADJUSTED TO THE CURRICULUM? before putting them to work in the field, initially I was a little nervous about it because I didn’t know how everything would work. But as time went on, in an apprentice capacity. everything started connecting. We take the lessons we learned in class and apply them to hands-on
“A lineworker’s job is no longer just manual activities. work,” Considine said. “It’s much more a technol- We visit job sites and companies; we get to talk to the owners and management to learn about ogy company than it is a poles and wires business. what their company has to offer. This helps me see where I can be in 10-15 years working for one of We electronically dispatch work to vehicles when these companies. ADVICE FROM A PROWHAT ADVICE DO YOU HAVE FOR HIGH SCHOOLERS WHO ARE STILL TRYING TO FIGURE OUT WHAT THEY WANT TO DO FOR A CAREER? our employees are out in the field every day. There is an incredible amount of data that we push to the tablets they work off of to communicate with the customer about their outage. They also have a lot Trade jobs are a great opportunity and you can make good money. I would recommend that you purof web-based training and learning they do to keep sue this field if you are willing to work hard. their skills sharp.
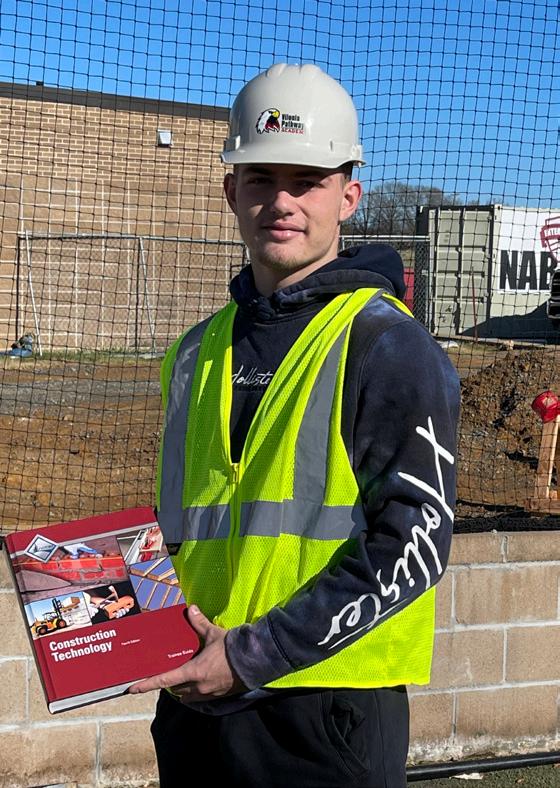
Looking for more information on other educational and career opportunities in Arkansas?
TRAINING FUTURE...
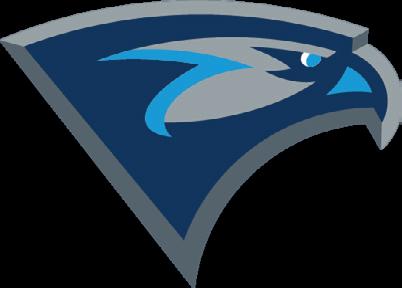
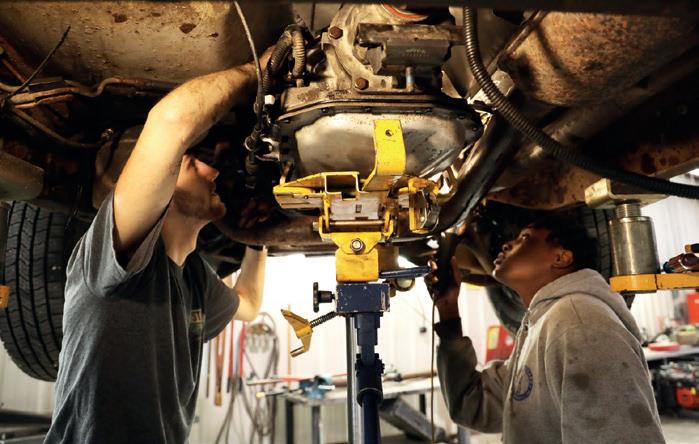
CNC Machine Operators Electricians Industrial Mechanics Machinists Structural Technicians Welders
Scan to view BRTC programs!
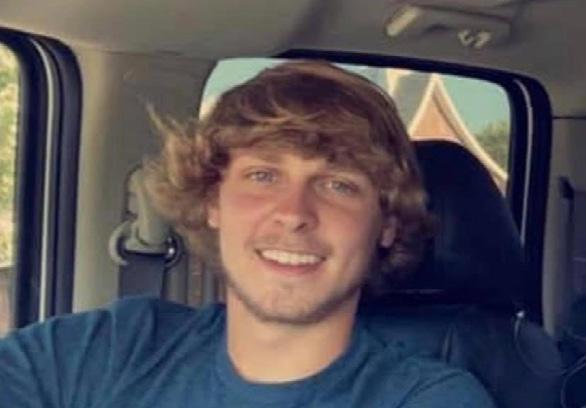
TYLER WINCHESTER
AGE: 20 EDUCATION: Arkansas Northeastern College JOB: Shift electrician, Big River Steel SNAPSHOT: A family member’s steel-working career laid the path for the Missouri native to follow. Now he’s starting his well-paying career at an age when many of his peers are still piling up student loan debt.
HOW DID YOU GET INTO THE STEEL INDUSTRY? My dad works at the steel mill where he’s a mechanic. I was in the steel tech program at ANC for one term, then I got a job offer at a different steel mill, Big River Steel. I’m a full-time electrician there now.
WHAT DOES THAT ENTAIL EVERY DAY? You go in in the morning and you take over for the guy who worked over the nighttime. He tells me what kind of issues he had, if he had any standing issues, what you need to jump on right away. If there’s nothing to jump on, you kind of hang around till you get a call.
I’ll be working on machinery as issues come up or I might be working on a larger project within the plant itself. There’s something different every day. You’re not looking at the same exact thing every day, so you get the chance to learn something new every day.
WHAT OTHER SKILLS DO YOU NEED ON YOUR JOB OUTSIDE OF THE TECHNICAL STUFF AND KNOWING ABOUT ELECTRICITY? The most important skill is communication. If you don’t have communication, you’re not safe. If you don’t know what somebody’s doing around you, you don’t know what could possibly harm you.
WHAT HAS IT BEEN LIKE BEING THE NEW GUY? I’m just going in and soaking up as much information as I can. I tend to get with the older guys so I ask a lot of questions. They know a whole lot more, so I try to be their sidekick and get all the information I can out of them.
WHAT ARE YOUR LONG-TERM GOALS? I’ll start off as a shift electrician, but eventually I want to be a day electrician or a lead man. Starting out at my age straight out of high school, there is a great opportunity to be promoted where I work.
I’m actually getting sent to a class in about two or three months and the company will continue to send me to different trainings. Those will be good learning opportunities for me to help keep the mill running and advance my career.
“The equipment that they’re installing is also very high-tech. We’re deploying IPO reclosers, which are basically automated circuit breakers. Those have a computer inside of them and lineworkers are expected to understand those and work on those. Ten years ago, we didn’t have any of those, and today we’re deploying hundreds every year.”
NABHOLZ CONSTRUCTION
As one of the oldest general contractors in Arkansas, Nabholz Construction has for years left its mark on the state through one high-profile project after another. The company has put the same attention to detail in its apprenticeship and continuing training programs, both internally and in partnership with external schools, colleges and organizations.
“Our carpentry apprentice program was the first private program in the state. It goes back to 1972,” said David Nabholz, executive vice president. “Our apprenticeship class will generally get eight to 12 new candidates every year here in Central Arkansas and then that’s a three- or four-year training program, depending on if they have any previous experience.”
Nabholz said that while not all who start the program finish it, the ones that do generally stay with the company over the long term.
“They become our craftsman carpenters, they become our foremen, they become our superintendents and some of them even become project managers,” he said. “Either way, between the benefits and the 401K and their career growth, they’re here for their whole career.”
Nabholz has also been an active partner in creating training programs through Arkansas high schools, most recently with the Vilonia Pathways Academy, where the company not only serves as advisers, but provides field trip opportunities to job sites and leads other training to help steer interested students into a skilled career.
“We brought students here to our company to meet with our human resources department,” Nabholz said. “It’s a pet peeve of mine that people don’t understand many companies in the construction industry have really great benefits. So, we did about two hours with them, and for the first time they started seeing that we have health insurance, we have a 401K that pays very well and we have all the other benefits, holidays and vacations. They started seeing this as a career where they can excel.
“We show them that you come here unskilled and we have apprenticeship programs that you can go through. We’ve got a management training system you can go through. We show them it’s a great career path.”
ABB
ABB in Fort Smith, part of a global manufacturing company, is a familiar partner with job skills training in area K-12 school districts, UA Fort Smith and Western Arkansas Technical Center. In fact, the company was instrumental in bringing key educational stakeholders to the table to discuss ways to expand job training into career planning among Fort Smith’s youth.
“About five years ago, we started rethinking our approach to career and technical education,” said Jason Green, head of human resources for ABB’s Nieman Motors Division. “We reached out to UA Fort Smith, the Fort Smith Public Schools and the Fort Smith Chamber of Commerce to reengineer the entire career and technical education model.”
Those discussions resulted in new programs that help technical education stand out to students much earlier and educate them on the opportunities available in manufacturing, health care and information technology.
Along with the new training and education programming has come new facilities, such as the PEAK Center, set to open in 2022, which extends the work of the Western Arkansas Technical Center in training both young people and adults.
ABB has also led the way in providing paid internships providing high schoolers real-world exposure to skilled positions.
“For the 2020-21 school year, we hired six apprentices who were trained in partnership with UA Fort Smith,” Green said. “They went through a 40-hour-a-week summer session for eight weeks spending the morning in class at UA Fort Smith and the afternoon working in the manufacturing facility. Once school started, they worked for us three hours a day, four days a week, all paid.”
Of those six interns, four joined the company after graduation. ABB hired them part time to allow them time to finish their associate degree, which they did thanks to ABB’s tuition reimbursement program. Green said the company’s internships are a model for others to follow.
“We’ve aligned training programs with demand,” he said. “As students walk across that stage at graduation, whether it’s high school or post-secondary, they’re walking with two things: a viable career plan and relevant skill sets so that they’re employable.”
LITTLE ROCK WATER RECLAMATION AUTHORITY
As a public utility, Little Rock Water Reclamation Authority is responsible for serving thousands of households, and it fulfills this responsibility through the talents of many different skilled employees. The organization provides ongoing training programs for these employees to keep their skills up-todate and customer service at its peak.
LRWRA employs electricians, plumbers, HVACR and general carpentry workers, as well as machinists and tool-and-die crafts people. All of this skill is at work in the field daily, as are more entry-level positions from which workers can begin their careers and move up.
The most entry-level positions — utility workers — require only a high school diploma, but the company encourages employees to improve their skills to create a career path. In fact, after one year of service, LRWRA offers employees educational reimbursement, which allows people to train for a skilled career, earn a certificate or even finish an associate degree, thus moving up and commanding a higher wage. The organization also pays outright for any mandatory training or continuing education required of employees in a given role, along with affording them paid time off to complete it.
Little Rock Water Reclamation Authority pays competitive wages, as well as offering a full slate of benefits from health and wellness, to retirement, to paid time off that accrues from day one of employment. All told, benefits make up about 40 percent of employees’ total compensation package.
Another benefit that’s hard to put a price on is job security. Given the local nature of the work, Little Rock Water Reclamation Authority’s jobs aren’t going to be relocated out of state or offshore. In fact, even a global pandemic didn’t affect operations much; as an essential service, the majority of skilled positions worked straight through the COVID crisis of 2020 and 2021 to ensure water kept flowing to homes and businesses alike.
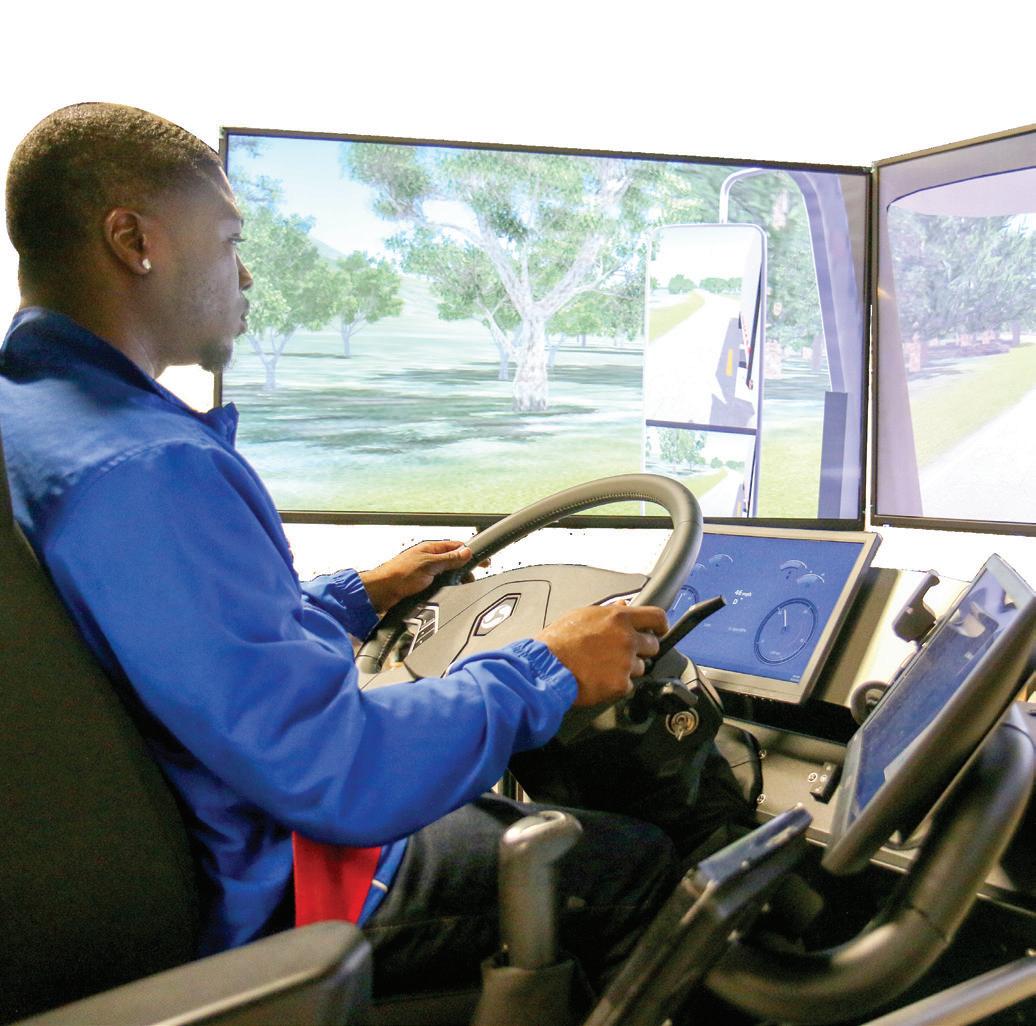