A REVOLUTION IN STEEL
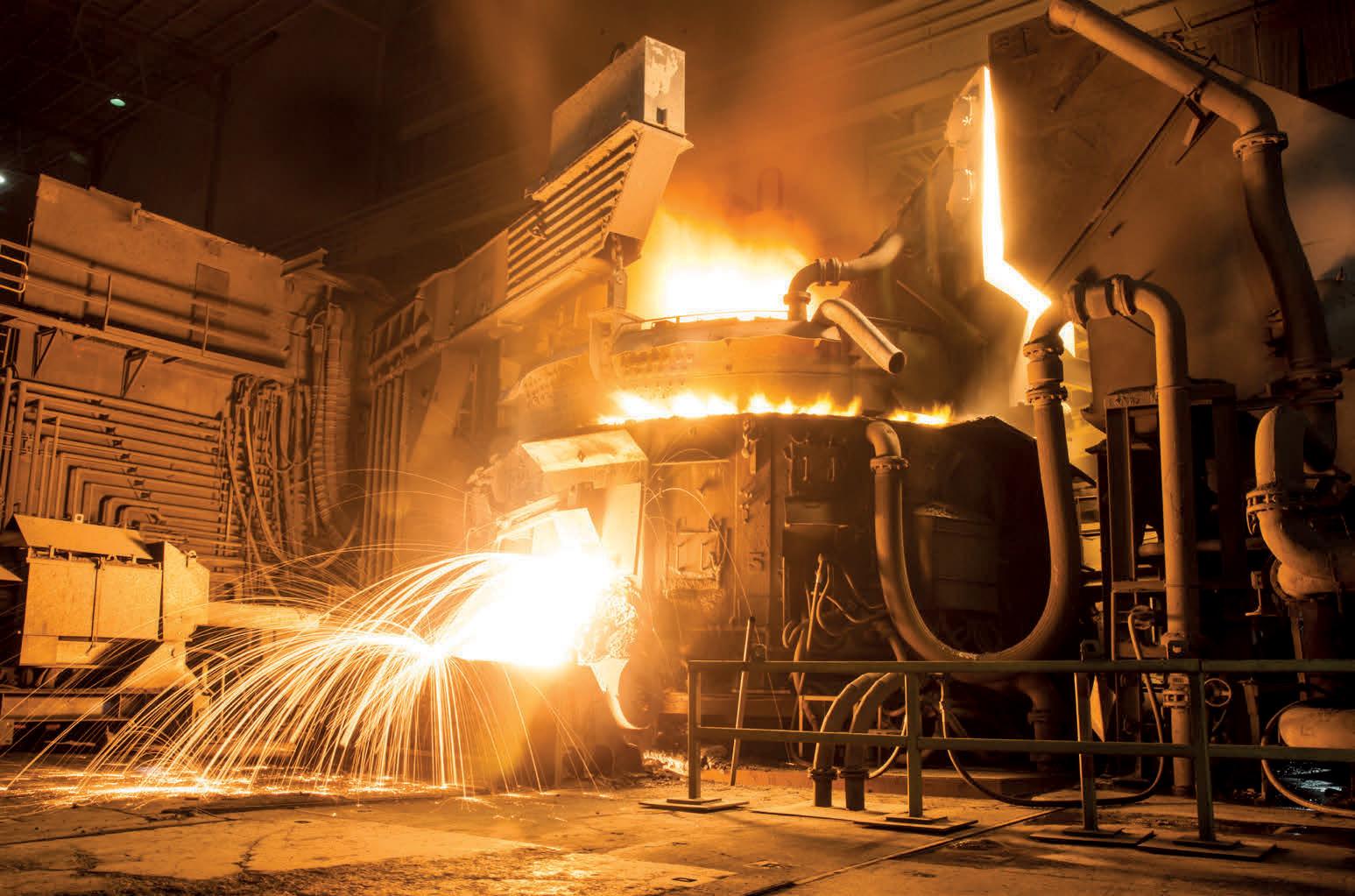
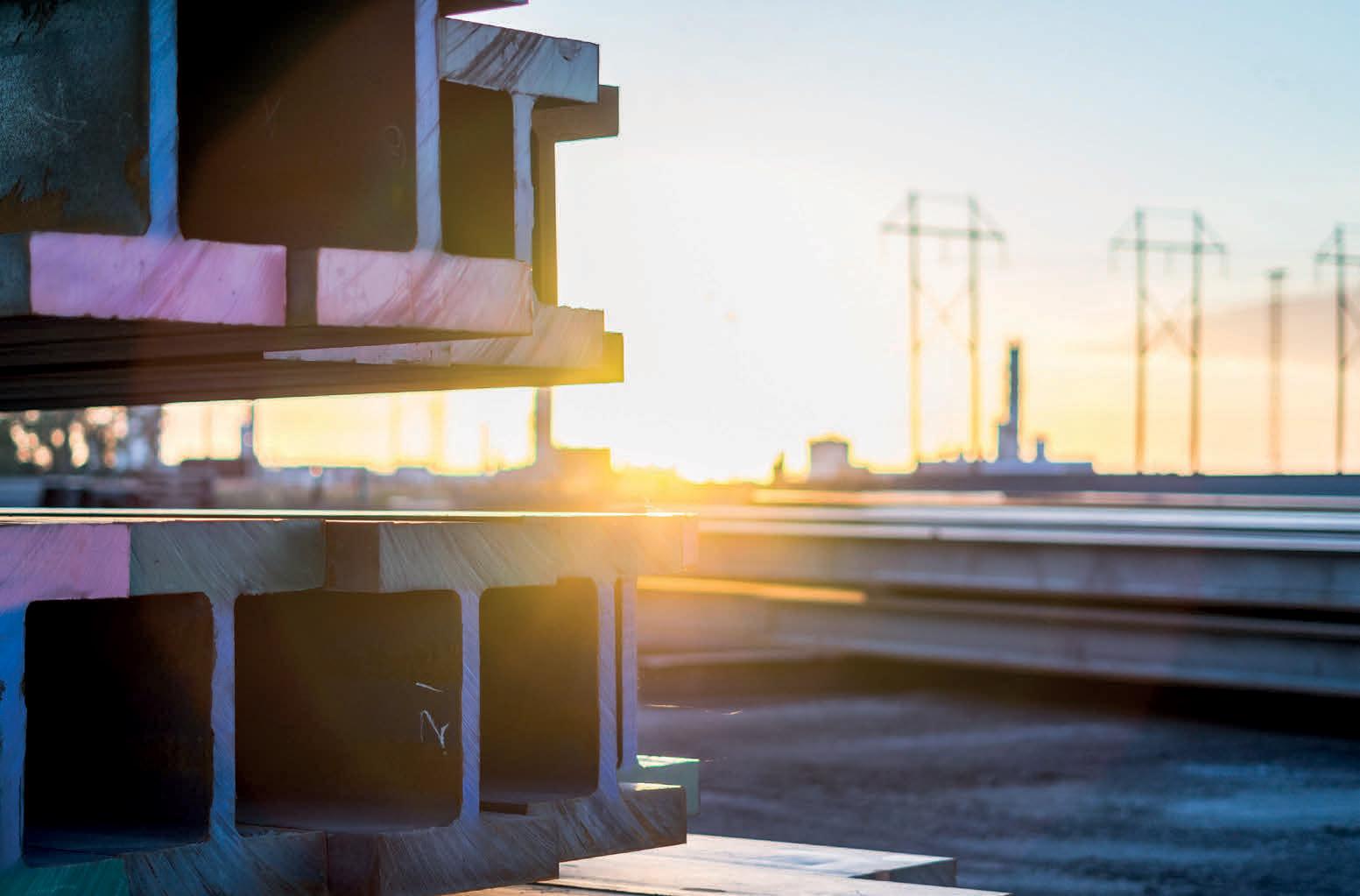
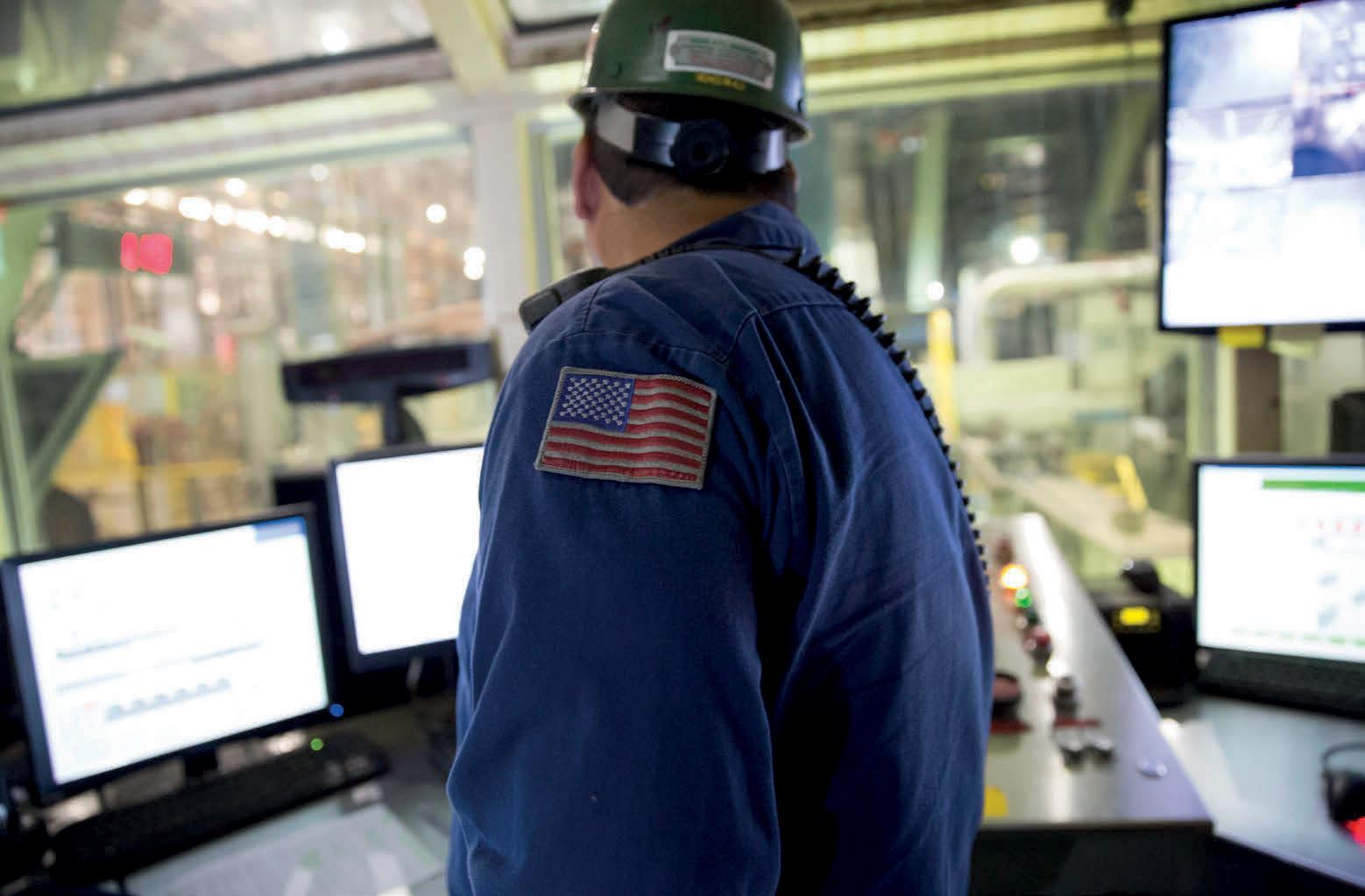
DISCOVER THE OPPORTUNITIES
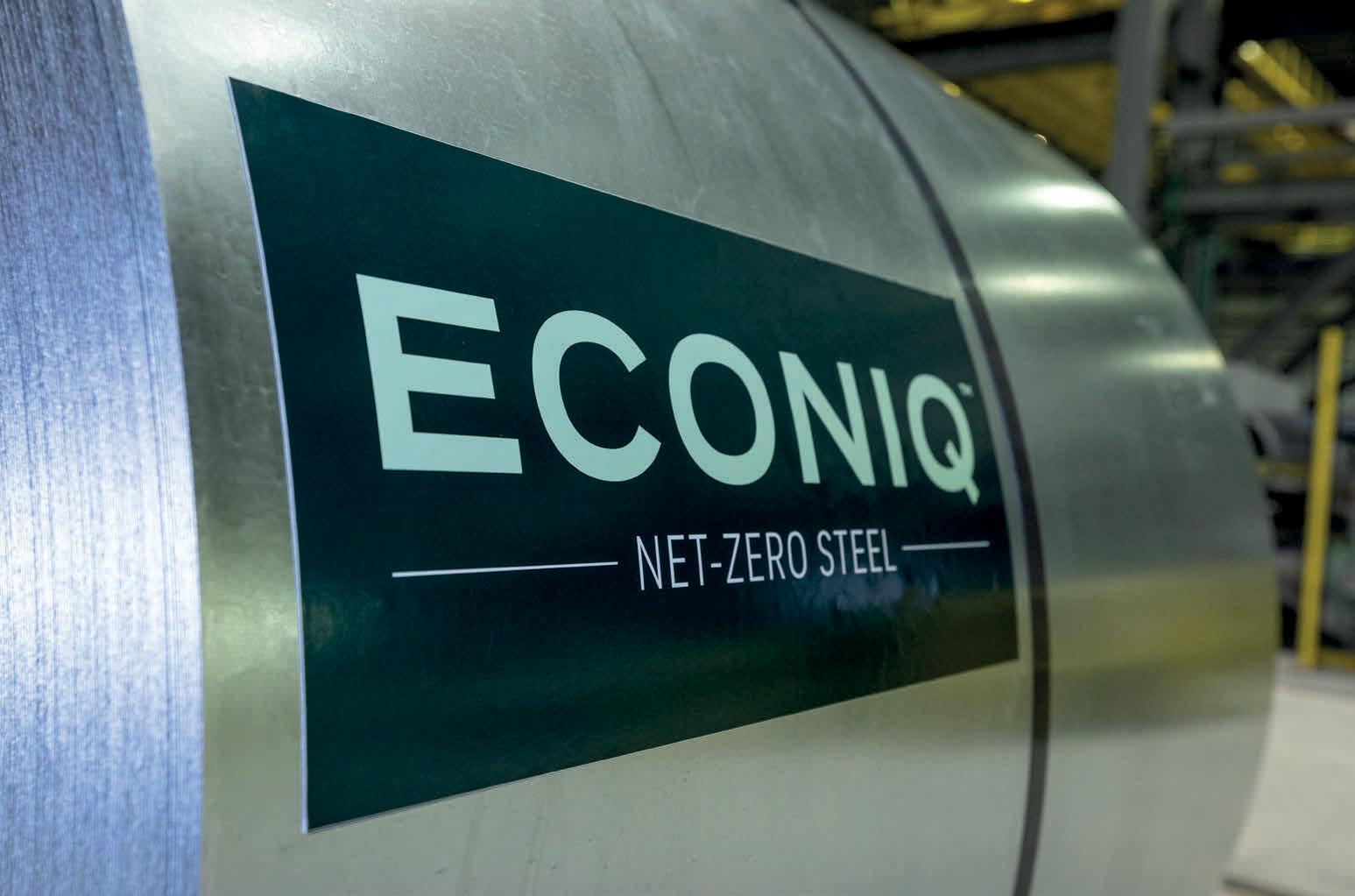
LEARN YOUR TRADE
• MAKE THE TEAM
• BUILD YOUR CAREER
NUCOR: A REVOLUTION IN STEEL
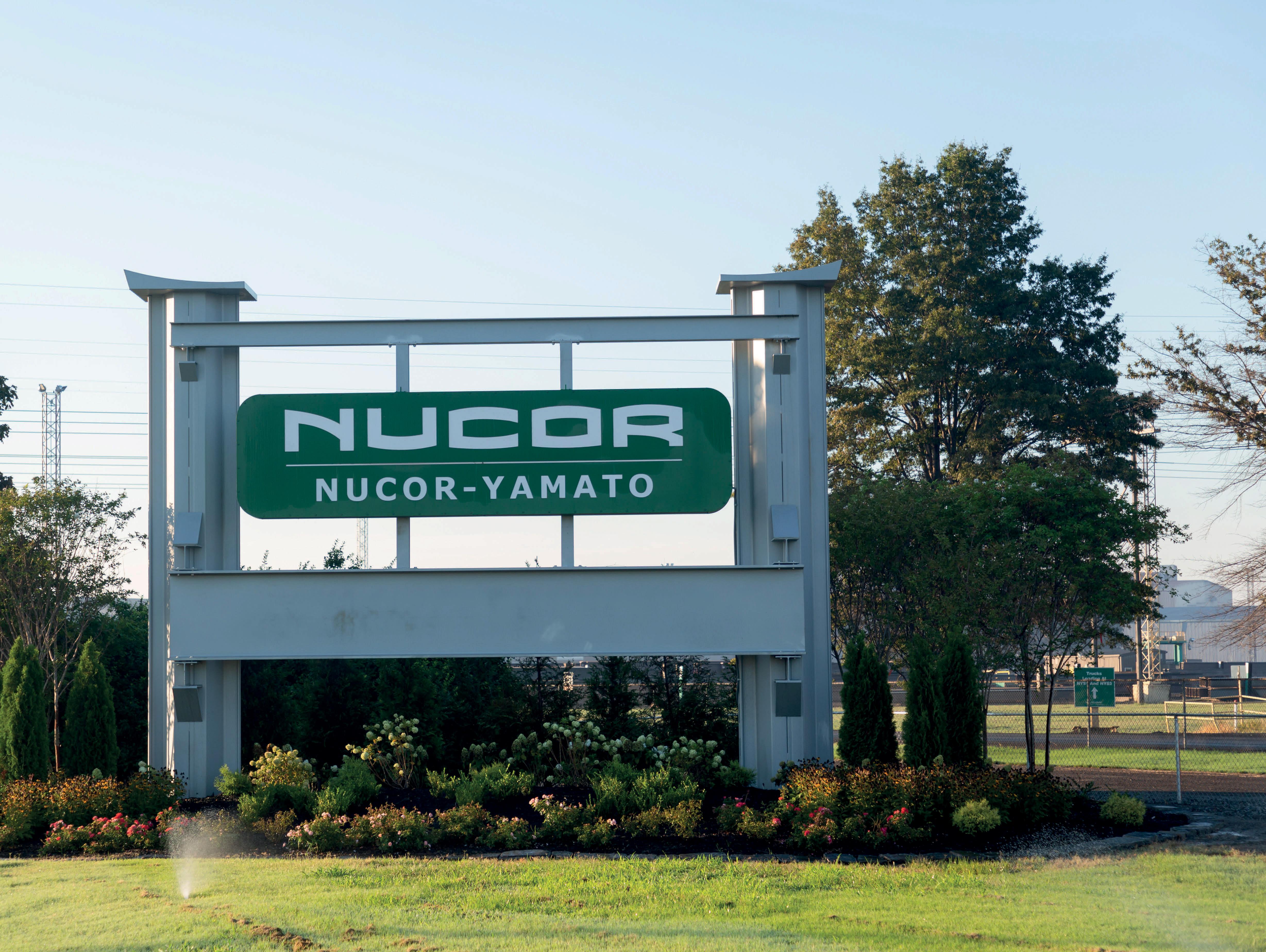
DISCOVER THE OPPORTUNITIES
LEARN YOUR TRADE
• MAKE THE TEAM
• BUILD YOUR CAREER
Northeast Arkansas is home to the second-largest steel producing county in the entire country, Mississippi County. As the U.S. enjoys a manufacturing boom that shows no signs of slowing, the steel industry in the U.S. – and in Mississippi – will continue to grow.
The industry got its start in northeast Arkansas back in 1987 when the Nucor-Yamato Steel Company (NYS) began operating a mill that produces steel beams used to build skyscrapers and other structures. Five years later, in 1992, sister division Nucor Steel Arkansas began producing steel sheet used to make cars, appliances and other products. Since then, these two Nucor mills have invested billions of dollars to grow, creating thousands of high-paying jobs with generous benefits and plenty of opportunities for teammates to advance their careers.
Nucor’s two Arkansas steel mills are some of the biggest and most technologically advanced manufacturing facilities in the country. They each have developed innovative high-strength, lightweight steel products for the construction and automotive industries, and they are both world leaders in sustainable steel production. All Nucor mills recycle scrap metal into new steel products, which makes the company a world leader in low-carbon steel production. And the company continues to find ways to lower its environmental footprint. It has made a commitment to reduce its greenhouse gas emissions intensity by another 35%, is supporting the development of renewable and other clean energy sources, and recently introduced the world’s first line of net-zero carbon emission steel products, called Econiq.
Today, Nucor’s plants are the model for the steel industry and the company is one of the most important corporate citizens in The Natural State. This advertising section in Blueprint will highlight the company’s many benefits, as told directly by the teammates of NucorYamato Steel Company and Nucor Steel Arkansas, who are building their futures as they help build America.
• 2,300 – Nucor Steel Jobs in Arkansas
• $100,000 – Median pay for Nucor teammates, excluding executives
• $36 billion – Net sales in 2021
• 23 million – Tons of ferrous scrap recycled into new steel annually
• $4,000 – Annual scholarship amount available to each Nucor teammate and their dependents
• Largest steel and steel products producer in North America
• Largest recycler of any type of material in the Western Hemisphere
• #1 Most Admired Metals Company (Fortune Magazine, 2021)
• Named one of Fortune Magazine’s 20 Best Large Workplaces in Manufacturing and Production, 2021
EAF Helper, Nucor-Yamato Steel
Hometown: Memphis
Age: 32
Years with Nucor: 7.5
BLUEPRINT: What is your educational background and what were your career plans?
WILLIAM SANDERS: I went to the University of Arkansas at Pine Bluff and received a bachelor’s degree in industrial technology management as applied to engineering. I wanted to apply for a job in manufacturing and Nucor was offering an internship through UAPB. It was the perfect opportunity to put my educational skills to work.
BP: Why manufacturing? Do you enjoy working with your hands?
WS: Yes, I learned to work on cars, build fences and work on houses with my dad and uncle when I was younger.
BP: Was there a big learning curve once you joined the company?
WS: We get a lot of training on the job both directly for our role here and for other jobs, such as cross training. Nucor also offers educational reimbursement for college courses we may be interested in to continue learning.
BP: What is your schedule like?
WS: I work twelve-hour shifts, four days on and four days off, rotating shifts from days to nights, seven days a week.
BP: What do you like best about working for Nucor?
WS: The pay and the benefits that come with the job are great! I really enjoy the people I work with and know they are looking out for my safety. We refer to each other as teammates because we get to know each other and form a real bond.
Safety Coordinator, Nucor Steel Arkansas
Hometown: Brookland, AR
Age: 42
Years with Nucor: 23 years
BLUEPRINT: What’s your background?
BETH WREN: Before Nucor-Yamato, I was a nutritionist for a hospital. I started as a contractor doing diabetes education and health and wellness programs for health and safety, and it ended up turning into a full-time position.
BP: What does your job entail now?
BW: I work with the new-hire processing, training them for the safety department.
BP: Are there opportunities for new teammates to have an immediate impact on safety?
BW: The new teammates bring in a new set of eyes. If they see something unsafe, Nucor culture lets them ask the question, ‘Why are we doing that? Can we do this differently?’ It empowers and helps new teammates to know they are just as much a part of our safety culture as teammates who’ve been here for 30 years.
BP: What have you learned by working for Nucor that everyone should know?
BW: The career possibilities are endless.
BP: What would you say to someone who thinks they lack the training for a job at Nucor?
BW: Nucor really wants to be proactive instead of reactive when it comes to training. Using our department as an example, we train new hires with a 10-hour class. After they are hired, we continually train people to meet the needs of the business. We just got certified in mental health first -aid because we have seen mental health as a growing issue. We also have first responder training; we have multiple teams for emergency response and high-angle rescue, and we do that training onsite. That training is a huge opportunity for teammates because when we get these certifications it’s not just a Nucor certification, it’s something teammates can take with them for the rest of their career.
What I tell people is yes, the pay is wonderful, but what you gain from here and how you grow here is even more valuable.
One of the most important aspects of having a vibrant, healthy, productive and satisfying workforce is to ensure its diversity: diversity of background, diversity of thought, diversity of experience and diversity of ability.
Companies across the country are paying greater attention than ever to the makeup of their labor force, motivated by a combination of public relations, a response to the increased labor shortage, and customer demands.
At Nucor Steel Arkansas and Nucor-Yamato Steel (NYS), the production floor and offices are populated by men and women of various ages, races, ethnic backgrounds and countries of origin. In short, they reflect the communities of which they’re so proud to be a part. Their common denominator – what binds them all together – is a desire to build a career, look out for the safety of their fellow teammates, and support the company that makes it possible.
“As far as diversity goes, I see a lot of people of color here,” said Tyrone Dodd, who joined Nucor-Yamato Steel right out of high school last summer. “We all want to do a job and be safe doing it. It doesn’t really matter where you come from or what you look like -we’re all just one team.”
Nucor’s success in recruiting from a diversity of backgrounds has become almost self-sustaining, with members of our vibrant Arkansas community attracted to the company based on what they see in the faces of Nucor teammates.
“I think it’s like the old saying, ‘You can’t be what you can’t see,’” said Randy
Henderson, Safety Coordinator with Nucor Steel Arkansas. “When I think about the dynamics in this area, I think about leadership. You’ve got to have people of all backgrounds in leadership positions, which I’m proud to say we do. That way, students and people in the community see these people and know there’s a pathway for them.”
Nucor teammates know, once a new teammate joins the company, they will have an incredibly broad range of people in varying departments stepping up as mentors to assist in fulfilling career goals.
“I was blessed with the way things worked out for me here,” said James Jones, a lab crew leader who has worked at Nucor-Yamato Steel for 13 years. “Nucor runs on the abilities of its teammates more than anything. We have people who have worked here a long time, people who helped me move up at an accelerated rate. I was always well-received and was taken under someone’s wing to teach me how to be part of the Nucor leadership team.”
Almost everyone at a Nucor mill has a story about how the working environment and all-for-one mentality elevated their work life and inspired them to want to move past a job into a career. Despite being on the job less than a year, Mayra Gonzalez, a single mother of two originally from Mexico, has one such story. “I am a coil wrapper and handler; I prep the coils according to their packaging code and ship them out either by rail or truck,” she said. “My advice for others is to never give up. Everything is possible if you set your mind to it. I never really had a role model, so I became one to my daughters.”
Nucor teammates from all backgrounds work and succeed as one.
FRENZEL MORALES
PC Tech, Nucor Steel Arkansas
Country of Origin: The Philippines
Age: 27
Tenure with Nucor: 9 months
BLUEPRINT: How did you get interested in your career field?
FRENZEL MORALES: Growing up, I leaned toward technology, and I was a very curious person. Any toy I had, I broke it apart just to see how it functioned and how it worked. I took my first phone apart to see how it worked.
BP: What would surprise people about the level of technology at work in the steel plant?
FM: At Nucor, our biggest thing is safety. Some of the technology we’ve engineered works to take a person out of a dangerous position. Some of what we do is baseline work, but there’s a lot that’s more complicated. Last week I had to work on a computer that had specialty software just for that specific manufacturing area.
BP: Is all your work on PCs or do you work with the manufacturing equipment?
FM: We do a lot of what’s in-between, depending on where the equipment is out at the mill. It could be a computer, it could also be a printer, it could be a label printer that we print out labels to put on finished coils. If any of this equipment isn’t working, we swap it out and change it. And we have to work fast to get back up and running so it doesn’t stop production.
BP: What do you like about working at Nucor?
FM: Where do I start? I have a great team and my team always has my back. We’re working in an environment where there’s a lot of hot metal, and it can be somewhat dangerous. But at the same time, it’s all well thought out.
BLUEPRINT: How did you learn about opportunities at Nucor?
TYRONE DODD: During my senior year at school, I was selected for a Nucor pilot program, NuPath, that offers graduating Seniors the opportunity to interview for an entry level job at one of the Nucor Arkansas divisions. It was a great opportunity. After going through the interview process and graduation, I got hired on and learned even more while I was in training. I’ve learned something every day since I’ve been here.
BP: Now that you’re working at Nucor, what are your long-term goals?
TYRONE DODD
Buildings & Grounds, Nucor-Yamato Steel
Hometown: Blytheville
Age: 19
Tenure with Nucor: 6 months
TD: Right now, I am working with the building and grounds crew for a year to familiarize myself with the steel mill. After that, I can bid on an open job in another department where I want to work. So, I can go to the melt shop, shipping, anywhere I think I want to go.
BP: In your job today, is it a lot of solo work? Do you have a mentor? Do you work on a crew?
TD: The building and grounds crew consists of five people – me, three other men and our supervisor. They’re all my friends, they take care of me and have from day one. They are my mentors, teaching me everyday skills needed for my job. I see NYS as a diverse place to work. Everybody’s nice, everybody treats everyone the same, and everybody is a teammate on the same team.
BLUEPRINT: Does working on heavy equipment run in your family? How did you get to work a crane?
JULIE PELTS: I originally set out to work in the office, but one day my manager encouraged me to get a feel for what is available at Nucor, so I rode in the crane for a bit and watched the guys run it. I thought, maybe I could do that.
BP: What’s the formal training like?
JP: Training runs between 60 and 90 days. You get in the crane, and you have a trainer in there with you to explain everything about how to operate the crane. They eventually let you run for a little while, but they are always in the crane with you.
Crane Operator, Nucor-Yamato Steel
Hometown: Cooter, Missouri
Age: 45
Years with the Company: 16
BP: What do you do during a typical shift? In the bloom yard we stack the steel. We cast it, we pick it up and put it in the yard and then we give it back to the roll mill for them to reheat and roll it.
BP: Have you had the opportunity to mentor other women in the same job?
JP: We have had a few other women come over here and I trained them. We also have Bloom Yard I and Bloom Yard II cranes and there have been women over there that I’ve helped train.
BP: Is it unusual for women to be crane operators? How were you accepted early on?
JP: Actually, at the time I started, we had quite a few women crane operators. And there’s another woman on our crew right now. In fact, I’ve been doing this for 13 years now. The guys were great and still are.
Lab Crew Leader, Nucor-Yamato Steel
Hometown: Blytheville
Age: 42
Years with Nucor: 13
BLUEPRINT: You have quite the connection to the Nucor plant, don’t you?
JAMES JONES: My dad was one of the first people who helped to implement the design of the Nucor plant in Blytheville; he was a fabricator. When Nucor came to town my dad was one of the people who reviewed the plans and made the adjustments for real-time operation.
My dad was one of the first teammates at Nucor Yamato Steel. From the very beginning, he was able to provide our family with a good living and provided us with a lot of things that he could only dream of.
BP: What has been your experience working at Nucor?
JJ: The people here care about you and treat you well in times of need. When my father was dying, my team said, “You do what you’ve got to do, and we’ll take care of everything else. You don’t have to worry.” I was able to spend time with him during his last days. Nucor wrapped me in an envelope of friendship and family so that it didn’t hurt as bad when I went back to work. So, yes, I have a little bit of heritage with this company and working here, it’s a personal thing for me.
Safety Coordinator, Nucor Steel Arkansas
Age: 53
Years with the company: 26
BLUEPRINT: Where did you grow up?
RANDY HENDERSON: I was born and raised in Mississippi County, Arkansas.
BP: What brought you to Nucor?
RH: Like some in this area, I had a strong work ethic and limited skills. Nucor was willing to take a chance on me. I was hired in an entry level position, and I basically worked my way up from the bottom. Once I established myself within Nucor, my manager began to help push me out of my comfort zone to help me grow.
BP: Where did you start your career at Nucor?
RH: I started out as a shipper loader in the shipping material handling department. Before I knew it, 26 years had passed. I have held many different positions within Nucor, each a step up from where I started. I have also been involved in promoting and recruiting for Nucor within our hometown, as well as at many twoand four-year colleges. I am where I am today because Nucor allowed me the opportunity to grow, not only as a person, but as a leader for Nucor and our state.
BP: What helped you advance over that time?
RH: First and foremost, I had great Nucor mentors, people who took the time to help me and provide guidance. Second, the company presented me with a clear pathway to getting an education and reimbursing me for college courses. I went back to school and got my Associate of Art degree in technology and then, a year later, I got my undergraduate degree in technology. When I graduated, I had zero college debt; Nucor funded that 100 percent.
BP: Now that you’re a supervisor, what are some pieces of advice you give to new teammates about working here?
RH: I tell them the most important thing is your attitude. Attitude determines everything. With the right attitude, Nucor offers unlimited possibilities. That’s part of the Nucor brand, and I talk about that all the time. That is what I think makes Nucor stand out from the rest!
MAYRA GONZALEZ
Coil Wrapper/Handler, Nucor Steel Arkansas
Country of Origin: Mexico
Age: 38
Tenure with Nucor: 5 months
BLUEPRINT: Tell me about your background. MAYRA GONZALEZ: I’m a 38-year-old single mother of two teenage girls. I was born and raised in Mexico, but I have been living in Missouri for the last 23 years.
BP: What did you do before you joined Nucor?
MG: For 12 years I worked as a case manager for a federally funded nonprofit through the Department of Labor. One day I decided that I no longer had the passion for it and resigned. Shortly after that, a contractor company was needing a toolbox person to work during outages at various steel mills and keep inventory of tools. I obtained the job and worked my way to learn the proper tool names and got familiar with the steel mill environment.
BP: What do you like about Nucor?
MG: I like the learning opportunities. The company pays for your training and pays you while you train. In a short period of time with Nucor, I’ve taken advantage of the training and opportunities the company provides. I became a First Responder and a cab crane operator, and I got the opportunity to visit two Nucor plants in Kentucky for a Redline Audit.
BP: What would you tell someone looking to forge a career at Nucor?
MG: My advice for others is to never give up. Nucor encourages you to explore other jobs within the plant and move up and if you want to relocate to a different plant on another state, that is an option too.
DIVISION: Nucor-Yamato Steel and Nucor Steel Arkansas
AVERAGE STARTING SALARY: $83,000+
WHAT DOES THE JOB DO?
A port crane operator is responsible for port activities including river barge loading, equipment and port car repairs and oversight of all port personnel.
WHY IT’S IMPORTANT: Port crane operators are responsible for operating a crane to lift and move heavy objects in and out of barges. They are often tasked with moving large pieces of equipment or materials into place, but they may also be called upon to remove debris or clear an area of any obstructions that might get in the way of their work. Successful crane operators have extensive knowledge of how the crane operates, how to inspect the equipment for safe operations, as well as an understanding of hoisting mechanisms, rigging and load control. This includes knowing how to operate all of the various components as well as how these components interact with one another during normal operations. Most importantly, the port crane operator is responsible for the safety of the individuals within his or her area of operation.
SKILLS, EXPERIENCE AND ATTRIBUTES: Skills for success in this role include experience working a crane over the river, loading and unloading barges, rail cars, and/or trucks and previous rigging experience. Successful applicants must pass a depth-perception test.
WHAT MAKES THIS POSITION IN HIGH DEMAND?
The scarcity of crane operators with experience loading and unloading barges on the river makes this job in very high demand.
HOW DO I LEARN MORE? Please visit Nucor.com/careers to learn more about this opportunity.
DIVISION: Nucor-Yamato Steel and Nucor Steel Arkansas AVERAGE STARTING SALARY: $110,000+
WHAT DOES THE JOB DO?
Process control engineers and technicians are highly trained maintenance personnel tasked with making the steel manufacturing process as efficient as possible. This means they help Nucor make steel safer, faster, at a lower cost and with higher quality.
WHY IT’S IMPORTANT: Making the steel process more efficient allows the company to sell steel to customers at a lower price. In the competitive steel market, having the lowest cost is essential for doing business. Accelerating the process automation helps make on-time deliveries.
SKILLS, EXPERIENCE AND ATTRIBUTES: Some of the skill sets for success in this role include database work, control systems, web development and mathematical modeling.
WHAT MAKES THIS POSITION IN HIGH DEMAND? Level II and Level III skill sets are exceedingly rare. Most of these positions are held by electrical engineers or technicians with equivalent experience. There are plenty of positions in this job area that require only a two-year degree, and with Nucor’s policy of promoting from within and its programs to assist teammates with education and skill development, these jobs often lead to rapid advancement.
HOW DO I LEARN MORE? Please visit Nucor.com/careers to learn more about this opportunity.
Nucor promotes continuous skills learning for teammates.
Few manufacturing jobs in Arkansas carry as many perks and benefits as working for Nucor Steel Arkansas or Nucor-Yamato Steel (NYS). From high pay to generous benefits, the compensation offered here is well known. But ask anyone who works here, and they will also point to the personal growth and skills development they have achieved as a result of the company’s mentality of continuous improvement.
“They are eager to send you to training and that’s probably one of my favorite things about working here,” said Ethan Green, an industrial electrician who’s been on board for 18 months. “If you want to learn something, they are willing to teach it or send you to a place that will teach you.”
Like a lot of new hires, Green didn’t have well-developed technical experience coming out of high school. But thanks to a steel tech internship, an educational partnership between Nucor and Arkansas Northeastern College in Blytheville, he was able to learn quickly.
“My internship definitely helped a lot, plus working out here in the mill,” he said. “The stuff in the book is great, but you can’t really do much with it until you apply it out there in the field. I worked with the day guys and the shift guys seeing what their job roles were. They helped me with questions I had from school and showed me what the job was really like.”
Tyler Avery, project electrical automation technician for NYS, knows the value of the internship well. A decade ago, the 28-year-old was the very first electrical intern to go through the program.
“When I was in high school, I knew college wasn’t for me,” he said. “So, I chose to get a skilled trade and with Nucor’s help, I’m doing right now what an electrical engineer typically does.”
Avery said he’s not anti-college; in fact, he’s gone back to school to finish his degree, paid for by Nucor.
“Now that I’m mature enough to take it seriously, Nucor is paying for me to go back to school to get my four-year education,” he said. “I’ve done the electrical side, I’ve done the automation side and now I’m getting into the supervision side, so I’m learning about leadership roles. That’s definitely given my career a head start.”
As robust as the formal training programs are here, some of the best training comes outside the classroom, shared on the job and handed down from one generation of Nucor teammate to another. Charles Casey, Cold Mill 2 Supervisor at Nucor Steel Arkansas and a 31-year veteran of the company, said it’s been this way for as long as he can remember.
“Our guys on the floor are really good about taking their time to train newer folks and show them what needs to be done, how to work safely,” he said. “How we approach and talk to our leads out on the floor, that is us extending a helping hand to our new guys. There’s a lot of mentorship.
When a new teammate shows up, before they do the job that they’re hired to do, they work with a veteran teammate who’s doing that job, and they will not be released to do that job on their own until their mentor thinks they’re ready to go.
“I tell young people all the time that Nucor is a place where what you’ve got to do is have a desire to come to work and put your head down and work hard and work safe. You are in control of your entire career here. If you’re here on time and do a good job, the sky is the limit for you.”
BLUEPRINT: Did you have an idea of what you wanted to do when you were growing up?
ETHAN GREEN: My father and my grandfather were industrial electricians, and my dad actually works at the Nucor-Yamato steel mill. So, I did have a pretty good idea., I just wasn’t sure how I was going to get into it. I heard about the steel tech program at Arkansas Northeastern College, and I decided to do that. I landed an internship and here I am.
BP: Did you do any advanced training when you were still in high school knowing you wanted to get into electrical work? Or did it all start in college?
Industrial Electrician, Nucor Steel Arkansas
Hometown: Gosnell
Age: 21
Years with Nucor: 1.5
EG: Not so much electrical. I was taking some welding classes at the college, but that was it. I just kind jumped into electrical when I got into the steel tech program.
BP: How did you combine what you learned in the classroom with what you were learning on the job?
EG: I worked with the day guys and the shift guys seeing what their job roles were. They would help me with questions I would have from school, and I would get to work alongside with them and troubleshoot, go on calls and kind of see what was going on and what life was like at the steel mill.
BP: What are your job responsibilities, generally speaking?
EG: My responsibility as a shift electrician is to take care of the line, make sure it stays running. We do anything from wiring all the way to the programming.
BP: How have you, as a new employee, gotten up to speed quickly?
EG: Working alongside my teammates and just putting my hands on the equipment were the biggest things. I get to work with mechanics and other electricians and production folks, and we work as a team be really effective.
ASHLEY KROLL Environmental Coordinator Management Rep/Nucor-Yamato SteelHometown: Manila, AR
Age: 30
Years with Nucor: 12
BLUEPRINT: You started with Nucor at a pretty young age. How did that come about?
ASHLEY KROLL: I started when I was 18 in a two-year steel industry technology internship with Nucor, a month after high school graduation. An engineer from Nucor came to talk to our physics class during my senior year. I was undecided about what I wanted to do, and when she told us about the internship program, I was like, sign me up.
BP: Was college an option for you at that point?
AK: I was definitely not looking forward to racking up debt. I was struggling to figure out how I was going to make college work. I wanted to have a good career and start my life.
BP: How did that internship help you make that happen?
AK: I worked part time while I was going to college. The internship required that you had to keep good grades, to be at work on time, to have a positive attitude and most importantly, to make sure you were following the safety rules and doing your job duties as well. At the end of the two years, they offered me a full-time job.
BP: Did you have any experience in manufacturing or the trades prior to getting this internship?
AK: No, and honestly, I did not know a thing about the steel industry. When I stepped foot out here for the first time – and this place is huge, a lot of moving equipment, so many cranes and Taylor forklifts – I was just astonished and a little intimidated. It was amazing.
BP: You must be very proud of what you accomplished.
AK: I am extremely proud. And I’ll tell you this: I think Nucor is proud too. The teammates I work with, I think they’re proud of where I started and how far I’ve come. A lot of them have helped me along the way. I would say my hometown of Manila, AR, is very proud to have produced a young woman from that small town and that small high school who has accomplished so much.
“IF YOU WANT TO LEARN SOMETHING, THEY ARE WILLING TO TEACH IT, OR SEND YOU TO A PLACE THAT WILL TEACH YOU.” —ETHAN GREEN
Cold Mill Electrician Lead, Nucor Steel Arkansas
Hometown: Senath, Missouri
Age: 39
Years with Nucor: 11 years
BLUEPRINT: Growing up, did you have a good idea of what you wanted to do?
JOSH PAYNE: My story is a little different than many of my teammates. I went to college to study early childhood education. But after I graduated with a bachelor’s degree, I realized education was not really what I wanted to do. I wanted to come to work for Nucor. They offered me an electrical apprenticeship; it’s a two-year program, and I finished it in eight months.
BP: What did that program entail?
JP: In the electrical apprenticeship program, they put me to work, and they moved me around to different departments. I worked in the cold mill, then the metal shop, the caster deck, and then with the electrical team. They were training me and teaching me on the job at the same time I was taking college classes that Nucor paid for.
BP: What was that like?
JP: I worked areas that were completely foreign to me. It was all new. The guys I worked with were all veteran electricians, and they were able to help me pick up on things and learn the electrical aspects of it.
BP: What advice do you have for a young person who doesn’t have a plan for what they want to do?
JP: I did the same thing. I got here having process knowledge that I could apply enabling me to troubleshoot things, because I knew what the equipment was supposed to do. I use my background in the education field every day to train people, to talk to people and to help people understand.
BP: Why would you recommend Nucor?
JP: Coming into Nucor, you have the opportunity to move in any direction you want. If you want to do something at Nucor, everything is laid out and it’s there for you to go and get it.
NUCOR: A REVOLUTION IN STEEL
NUCOR: A REVOLUTION IN STEEL
DIVISION: Nucor-Yamato Steel and Nucor Steel Arkansas
DIVISION: Nucor-Yamato Steel and Nucor Steel Arkansas
AVERAGE STARTING SALARY: $64,000+ based on experience
AVERAGE STARTING SALARY: $64,000+ based on experience
WHAT DOES THE JOB DO? Support safety, environmental compliance and outreach efforts while promoting the mission of the organization within the division and community. Implement and manage the ISO 14001 Environmental Management System.
WHAT DOES THE JOB DO? Support safety, environmental compliance and outreach efforts while promoting the mission of the organization within the division and community. Implement and manage the ISO 14001 Environmental Management System.
• Build relationships with governmental, industry and community organizations.
• Build relationships with governmental, industry and community organizations.
• Oversee internal and external audits.
• Oversee internal and external audits.
• Ensure environmental objectives are met.
• Ensure environmental objectives are met.
• Develop and conduct environmental training.
• Develop and conduct environmental training.
• Facilitate community outreach programs.
• Facilitate community outreach programs.
• Engage the plant-wide team to identify and assist in continual improvement initiatives.
• Engage the plant-wide team to identify and assist in continual improvement initiatives.
• Take a lead role in safety initiatives.
• Take a lead role in safety initiatives.
• Maintain required emergency contingency plans.
• Maintain required emergency contingency plans.
WHY IT’S IMPORTANT: There are many environmental laws that govern industry and businesses, laws created to protect our air, water and land. Environmental engineers design, build and operate equipment and systems that give industry the ability to operate while staying within environmental laws. Some of the equipment and systems used in industry are wastewater treatment plants, baghouses, fume exhausts, fume
WHY IT’S IMPORTANT: There are many environmental laws that govern industry and businesses, laws created to protect our air, water and land. Environmental engineers design, build and operate equipment and systems that give industry the ability to operate while staying within environmental laws. Some of the equipment and systems used in industry are wastewater treatment plants, baghouses, fume exhausts, fume
DIVISION: Nucor-Yamato Steel and Nucor Steel Arkansas
DIVISION: Nucor-Yamato Steel and Nucor Steel Arkansas
AVERAGE STARTING SALARY: $70,000 + based on experience
AVERAGE STARTING SALARY: $70,000 + based on experience
WHAT DOES THE JOB DO?
WHAT DOES THE JOB DO?
Design, configure, secure, maintain and troubleshoot networks and networking systems. Work with users in full life-cycle software development including gathering requirements, designing solutions, developing full-stack applications and supporting those applications in production. Collaborate with individuals both in IT and across the organization
Design, configure, secure, maintain and troubleshoot networks and networking systems. Work with users in full life-cycle software development including gathering requirements, designing solutions, developing full-stack applications and supporting those applications in production. Collaborate with individuals both in IT and across the organization
WHY IT’S IMPORTANT:
WHY IT’S IMPORTANT:
Advancements in technology enable manufacturers to safely streamline production processes, innovate at a faster pace, reduce cost and deliver higher-quality products to meet customer demand. Systems and network engineers are crucial to installing, configuring, maintaining and securing the technology that enable these processes to run.
Advancements in technology enable manufacturers to safely streamline production processes, innovate at a faster pace, reduce cost and deliver higher-quality products to meet customer demand. Systems and network engineers are crucial to installing, configuring, maintaining and securing the technology that enable these processes to run.
SKILLS, EXPERIENCE AND ATTRIBUTES FOR SUCCESS:
1. Experience in an IT environment administering and supporting systems and network infrastructure or a bachelor’s degree in information systems, computer science, TSM or related field.
1. Experience in an IT environment administering and supporting systems and network infrastructure or a bachelor’s degree in information systems, computer science, TSM or related field.
2. Knowledge of TCP/IP, sub-netting and VLANs.
2. Knowledge of TCP/IP, sub-netting and VLANs.
3. Experience managing Active Directory, DNS, DHCP and Windows servers.
3. Experience managing Active Directory, DNS, DHCP and Windows servers.
scrubbers, thermal and catalytic oxidizers, cooling towers and landfills. An environmental engineer applies the correct technology to ensure compliance with state and federal environmental laws.
scrubbers, thermal and catalytic oxidizers, cooling towers and landfills. An environmental engineer applies the correct technology to ensure compliance with state and federal environmental laws.
SKILLS, EXPERIENCE AND ATTRIBUTES:
SKILLS, EXPERIENCE AND ATTRIBUTES:
• Bachelor’s degree in environmental engineering, related discipline or equivalent experience.
• Bachelor’s degree in environmental engineering, related discipline or equivalent experience.
• Previous experience in environmental engineering or equivalent field.
• Previous experience in environmental engineering or equivalent field.
• Environmental compliance experience.
• Environmental compliance experience.
• Permitting experience (Title V, PSD, NPDES).
• Permitting experience (Title V, PSD, NPDES).
• Knowledge of pollution control equipment, CEMS, drinking/ wastewater systems and ISO 14001 Environmental Management Systems.
• Knowledge of pollution control equipment, CEMS, drinking/ wastewater systems and ISO 14001 Environmental Management Systems.
• Experience with ISO 14001 or related systems.
• Experience with ISO 14001 or related systems.
WHAT MAKES THIS POSITION IN HIGH DEMAND?
WHAT MAKES THIS POSITION IN HIGH DEMAND?
Environmental laws are becoming increasingly more stringent because protecting the environment is even more of a priority in society. At the same time, there’s a worldwide demand for more complex products. The technology used in the environmental field is therefore becoming more complex, and new technologies are being created every day to minimize and control waste. Environmental engineers are at the forefront of creating and operating these new technologies.
Environmental laws are becoming increasingly more stringent because protecting the environment is even more of a priority in society. At the same time, there’s a worldwide demand for more complex products. The technology used in the environmental field is therefore becoming more complex, and new technologies are being created every day to minimize and control waste. Environmental engineers are at the forefront of creating and operating these new technologies.
HOW DO I LEARN MORE? Please visit Nucor.com/careers to learn more about this opportunity.
HOW DO I LEARN MORE? Please visit Nucor.com/careers to learn more about this opportunity.
4. MCSA certification or equivalent.
4. MCSA certification or equivalent.
5. Net+, CCNA certification or equivalent.
5. Net+, CCNA certification or equivalent.
6. Experience in the following areas:
6. Experience in the following areas:
• Cisco switches, firewalls and wireless LAN controllers
• Cisco switches, firewalls and wireless LAN controllers
• VMWare • PowerShell scripting
• VMWare • PowerShell scripting
• VPN technologies
• VPN technologies
• VOIP technologies
• VOIP technologies
• Microsoft PowerApps
• Microsoft PowerApps
• Fiber optic termination
• Fiber optic termination
• SharePoint administration
• SharePoint administration
• SAN administration
• SAN administration
7. Project management experience8. Customer support/help desk experience.
7. Project management experience8. Customer support/help desk experience.
WHAT MAKES THIS POSITION IN HIGH DEMAND?
WHAT MAKES THIS POSITION IN HIGH DEMAND?
Systems and network engineers play an essential role in any organization. Due to the growth and expansion of Nucor, this position is even more essential to support not only the existing and expanding infrastructure, but to provide the tools and technology to help the company become the safest steel manufacturer in the world.
Systems and network engineers play an essential role in any organization. Due to the growth and expansion of Nucor, this position is even more essential to support not only the existing and expanding infrastructure, but to provide the tools and technology to help the company become the safest steel manufacturer in the world.
HOW DO I LEARN MORE? Please visit Nucor.com/careers to learn more about this opportunity.
HOW DO I LEARN MORE? Please visit Nucor.com/careers to learn more about this opportunity.
Project Electrical Automation Technician, Nucor-Yamato Steel
Hometown: Blytheville
Age: 28
Years with Nucor: 9
BLUEPRINT: You were part of the Nucor internship program, is that correct?
TYLER AVERY: I was the very first electrical intern in the Nucor internship program between Nucor and Arkansas Northeastern College. I was kind of like a guinea pig. Now that internship program is one of the most successful programs with Nucor and ANC.
BP: Did you have any role models in the skilled careers growing up?
TA: I knew about skilled trades from the get-go. My dad is a welder and I’ve always worked with my hands with carpentry, working around the house, helping my dad. I ended up wanting to be an electrician.
BP: There are a lot of stereotypes about skilled careers. What’s the reality?
TA: As long as someone is willing to work, willing to challenge themselves, the opportunities at Nucor are endless.
CHRISTIAN WILLIAMS
Melt Shop Mechanic, Nucor Steel Arkansas
Hometown: Paragould
Age: 20
BLUEPRINT: What’s a typical day like?
CHRISTIAN WILLIAMS: On a typical day I check my emails, do my inspections, and walk around the mill and make sure everything is running well. I talk to my operators and then I’m on call for anything that goes wrong. I assist with mechanics, helping them with their projects.
BP: What’s your schedule?
CW: I work four-on/four-off rotating nights and days. I work 12-hour shifts and during that 12-hour shift I’ll be on call. If our boss needs us, we’ll go in and take care of what we need to do.
BP: What do you like about your job?
CW: It’s something different every day.
BP: What soft skills are most important?
CW: Being on time and communication skills are important, but safety is the number one factor.
A couple of generations ago, working in a steel mill was among the dirtiest, most physically demanding and potentially dangerous careers a person could have. But times have changed, as has the steel industry itself.
Today’s mills bear little resemblance to the fire-breathing factories of old, as computerization, robotics, artificial intelligence, and the Internet of Things help to run the show.
It’s a bold new chapter in manufacturing, demanding that employees with wide-ranging skill sets operate, troubleshoot and maintain high-tech equipment and the network backbone behind it.
Logan Nielsen, IT Leader for the Software Development team with NucorYamato Steel, has been with the company for five years.
“The software my team writes generally creates dashboards and interfaces for users to work with data,” he said. “Our customer is everyone out in the mill. I get a request every week for an application that needs to be written to display data or work with data to make the job out there easier.
“We create analytics and program a lot of reporting applications to show how well a crew is working, and if there were any issues or downtime. Probably the most fun part of my job is creating interfaces and dashboards that are easy to use as well as useful.”
Katie Behrendt, Sales Metallurgist with Nucor Steel Arkansas, said the massive amount of data captured continuously in the mill feeds even more sophisticated technology to keep the plant running at peak proficiency, right down to individual machines.
“The big things in technology we’re using and trying to make more use of are data analysis, machine learning and advanced automation techniques,”
she said. “That could be something like an electric vehicle company needing a higher-strength steel or a thinner steel to build a new car. We can use the data we’ve collected from our mills here to design and develop new processes and new materials to meet our customers’ needs.”
Technology is also leveraged throughout the plant to help the company maintain its strict safety standards in an environment featuring furnaces that reach almost 3,000 degrees Fahrenheit, said Damilola Balogun, Plant Metallurgist for Nucor-Yamato Steel.
“We use a lot of robots in safety,” he said. “We don’t want teammates close to the furnace while working. I don’t have to go to the front of an electric arc furnace to take temperatures, we have a robotic hand that goes into the steel, takes temperatures and comes out.”
Managing this new, highly advanced workplace requires a different set of skills than steel teammates of the past might have had, but it’s not all keyboards and coding that Nucor leadership is looking for. Soft skills, such as the ability to work as a team and the ability to communicate well, are equally critical.
“The old stereotype of the IT person sitting and typing away on a keyboard doesn’t exist here,” said Nishant Varadachari, IT Lead for business process for Nucor-Yamato Steel. “We get requests all the time from the mill, and we have to be able to follow up on that and ask questions so whatever we’re producing makes their lives easier. At every stage, our teammates have to be able to communicate, both in-person and over the phone, to ask questions, gather feedback and explain things. “In our company, skills can be taught, but it’s those natural communication skills and people skills that are truly valuable. They are what’s at the heart of Nucor.”
Plant Metallurgist, Nucor-Yamato
Home Country: Nigeria
Age: 26
Work Tenure: 6 months
BLUEPRINT: How did your professional journey lead you to Arkansas?
DAMILOLA BALOGUN: I have been in the United States for four years. I went to school at Missouri University of Science and Technology in Rolla, Missouri to obtain my doctorate in Metallurgy.
I’ve always wanted to work in a very big steel mill. Nucor is the largest steel manufacturer in the United States and our division, Nucor-Yamato Steel, is the largest manufacturer of beams in the United States.
BP: What do you like best about working at Nucor?
DB: Nucor is a company that really takes care of teammates. We are not even called employees, we are called teammates, we are called family. I have seen Nucor go out of their way to take care of their teammates. That’s why teammates typically always give their all to make sure everything runs smoothly.
Another very good thing about Nucor is that there is no hierarchy. What I’m trying to say is, you can start from entry level and end up as the CEO.
BP: What have you found to be important skills aside from your technical skills and how have you developed those?
DB: One of our challenges as a steel company is to be the world’s safest. To do that, we are held accountable in how we perform our work. To do that you need excellent communication skills.
In the six months since I joined Nucor, I have improved my communication skills thanks to training that involved going out into the plant to ask my teammates questions and get to know them on a deeper level.
DIVISION: Nucor-Yamato Steel and Nucor Steel Arkansas
AVERAGE STARTING SALARY: $80,000-$100,000 based on education and experience
WHAT DOES THE JOB DO?
A metallurgist is a highly sought-after manufacturing professional who can work in many different industries, including steel, aluminum, petroleum, automotive, aerospace and more. A metallurgist’s duties include:
• Review steelmaking and rolling processes to improve their metallurgical characteristics, yield and cost.
• Provide technical expertise for process development and continuous improvement of steelmaking processes.
• Engage in new product and grade development through analysis, experimentation and implementation of new raw materials, chemistries, equipment and manufacturing practices.
• Utilize engineering, physical metallurgy and steelmaking knowledge to help the company optimize process variables and improve the quality of its products, lower production costs, improve mechanical properties of low carbon steels and improve process efficiency.
• Implement and monitor testing practices as per required specifications so metallurgical requirements are met.
• Review, purchase and install new metallurgical equipment for upgrading of in-house testing capabilities.
• Provide support in the maintenance and proper operation of testing and analytical instruments.
• Utilize statistical process control tools to direct continuous improvement activities.
• Develop, revise and update standard operating procedures for special manufacturing projects.
• Develop and coordinate quality and safety training programs for operations, maintenance and quality-assurance laboratory teams.
• Review and process customer claims, which requires providing metallurgical technical support to the company’s sales and marketing departments.
WHY IT’S IMPORTANT: A metallurgist is responsible for the success of the company’s efforts to continue its development of innovative steel products, improve existing steel production practices which creates a safer product for our customers, and continuing efforts to make operations greener.
SKILLS, EXPERIENCE AND ATTRIBUTES: A metallurgical engineering degree from an accredited university is highly desirable as is prior work experience in the field of metallurgy. Data acquisition and analysis skills are also key to this position.
WHAT MAKES THIS POSITION IN HIGH DEMAND? Metallurgists are in scarce supply as there are currently only a small handful of universities in the United States offering a degree in metallurgical engineering. Metallurgical engineers are therefore in high demand; a newly graduated metallurgical engineer will typically command as many as a dozen job offers.
HOW DO I LEARN MORE? Please visit Nucor.com/careers to learn more about this opportunity.
BLUEPRINT: What misconceptions do people, including people in IT, have when it comes to technology and steel mills?
NISHANT VARADACHARI: If you’re looking from the outside, you’re thinking, “Okay this company just makes steel, so it probably doesn’t involve a lot of technology and computers.” That is absolutely wrong!
personal experience, a degree is good and it will be really helpful, but it’s not like you have to have a degree.
Country of Origin: India
Age: 38 Years with Nucor: 6
This technology was what I was used to seeing in my graduate studies and the places that I worked in California prior to coming to work for Nucor. When you go from school to the workplace and then come to Nucor, you see that the technology here is advanced. If you really have an interest in computer science, yes, you can make a good living at Nucor.
BP: Does it require the kind of college degrees you have in order to find opportunity at Nucor?
NV: Definitely not; there’s a home for pretty much anyone at Nucor. Speaking from
Being in IT in Nucor, you are mostly customer service. We are supporting the teammates out in the mill, because they are the ones who are actually rolling and casting and making the things with steel. So, if you come in with that mentality, there’s a place for you here.
BP: There’s a big focus on diversity across the board in workplaces, something IT has traditionally lacked. What’s the Nucor workplace like in terms of diversity?
NV: We have men and women from all different ethnicities. NYS’ IT department consist of 16-17 people; consisting of males and females, older and younger, as well as different ethnicities; everybody is really happy working, getting along. And, if you go around in the mill, it’s a pretty diverse environment out there as well.
Sales Metallurgist, Nucor Steel Arkansas
Hometown: Waukesha, WI
Age: 36
Years with Nucor: 3
BLUEPRINT: What does a sales metallurgist do?
KATIE BEHRENDT: I’m part of Nucor’s tech services group. I help our sales team and our customers who have new inquiries for the mill, asking if we can make this or that. I help ensure we understand what they need and that we’re giving them what they need. And then, if they have issues, of course I’ll get involved as well.
BP: Did you come to Nucor straight from college?
KB: Right before here I was at a U.S. Steel mill outside of Detroit. Right out of college I started in a wire mill in Milwaukee, and I was there for eight years.
BP: What is something about this job that might surprise someone?
KB: I think that a lot of people have this view that being an engineer or getting into a technological field starts with being really good in math and science. We definitely use a
lot of math and science, and I wouldn’t want anyone to think that they can avoid that, but I don’t think that’s required to become an engineer or a technological leader. I think it’s really just curiosity; it’s liking to take things apart and put them back together, it’s wanting to understand how things work. If people have that mindset, if they just have the curiosity and desire to understand, we can work with people and give them the technical part.
BP: What’s one characteristic that’s essential in this field?
KB: Being someone who asks, “Why? Why does this happen?” and then asking, “Why not? Why can’t we do it differently? Why can’t we do it better?” Those are really the people we’re looking for.
“IT’S REALLY JUST CURIOSITY ... LIKING TO TAKE THINGS APART AND PUTTING THEM BACK TOGETHER.” —KATIE BEHRENDT
Hometown: Rapid City, South Dakota
Age: 27
Years with Nucor: 5
BLUREPRINT: You have a degree in computer science which can be applied in a lot of places. Why work at Nucor?
LOGAN NIELSEN: Nucor-Yamato has a good relationship with Missouri University of Science and Technology, where I went to school. They did a recruiting event on campus one spring, and I applied for a co-op when I was a secondsemester junior.
I did a seven-month co-op with the IT team and fell in love with everybody here. And really fell in love with the idea of development in the manufacturing world as opposed to the tech industry. I got a full-time offer before I finished my co-op contingent upon successful completion of my degree, and I accepted it.
BP: What’s the difference between a co-op and an internship?
LN: Generally, an internship lasts over the summer; Nucor’s co-op spans a summer and a semester, so you get an extra four or five months, which also allows you additional time to learn and work on your own.
BP: What opportunities are in your department for someone without a four-year degree?
LN: We have a position called a technical analyst and they do a lot of things;, they’re the jack-of-all-trades in IT. A technical analyst is the frontline to our IT department, interfacing with customers a lot more than a software engineer. They are always on call.
If somebody calls our IT hotline, they’re the people who answer the call. That’s critical because if a monitor goes out in the middle of a crane, someone has to go replace that because they use those screens to keep people safe. If there are administrative issues – the technical analyst handles it; if there’s access right issues – the technical analyst handles that. That’s a job you only need an associate degree for, but it is really one of the most important jobs that we have in IT because it interfaces with customers all over, all the time.
Hot Mill Process Control
Lead/Nucor Steel Arkansas
Hometown: Steele, Mo.
Age: 45
Years with Nucor: 15
BLUEPRINT: What classes did you take in high school that prepared you for a career in manufacturing?
BRIAN ABBOTT: I went the vocational route. I took shop and electronics classes at a vocational-technical school my junior and senior year.
BP: Knowing what you know now, what classes would you recommend someone take to prepare for a career like yours?
BA: Physics and any type of programming class like Python, C++ would be helpful. Also, PLC programming classes would be very beneficial.
BP: What’s been your career progression at Nucor?
BA: I was originally hired as a shift electrician and then moved on to the process control group where we complement what the electricians do. We look at quality, reliability, performance, things like that. Basically, I’ve taken ownership of an area, the hot mill. I get
calls all the time. I’m on call 24/7 if something breaks. I’m kind of the last line of defense; if the electricians can’t fix it, they call me
BP: What are you most proud of in your career thus far?
BA: In our manufacturing process, material goes through the mill and is supposed to run up and make a nice, pretty coil. But if something happens in the process where it doesn’t make it to that, we call that a mill wreck. Part of what a process control engineer does is you investigate, get down to the root cause, define what happened, and then implement solutions to keep that from happening again.
The process control group, since I’ve been here, has reduced those from 500 to 600 a year down to 50 a year or less. That’s something I’m really proud of.
“I WENT THE VOCATIONAL ROUTE. I TOOK SHOP AND ELECTRONICS CLASSES AT A VOCATIONAL-TECHNICAL SCHOOL MY JUNIOR AND SENIOR YEARS.” —BRIAN ABBOTT
Roll Mill 1 Lead, Nucor-Yamato Steel
Hometown: Goshen
Age: 31
Years with Nucor: 10
BLUEPRINT: What was it like the first time you walked into the steel mill?
CODY MACE: I remember the first day like it was yesterday – walking in and being overwhelmed. Everything was so big, the equipment, the atmosphere.
BP: Where did you get your start at Nucor?
CM: I started in shipping, learning how to load rail cars, run cranes and run a tailer a little bit. Then I moved on to work in safety and in finishing steel in a roll mill a little bit as well. In finishing, you’re actually working on the inspection bin where the steel goes across the bed, and you look for any kind of defect.
BP: You were part of the steel tech internship program. What did that teach you?
CM: The great thing about being an intern is that every day you do something different. You may go, for instance, to the finishing bay or pulpit where you’re in the hot saws and you cut the steel, or you stack steel. It’s a great opportunity when you’re 18 or 19 years old to go in there and get an idea of what you really want to do as a full-time employee. And you make good money while you’re there.
BP: Did you have any mentors along the way?
CM: Mentoring happens every day out here, and it’s happened to me multiple times. I’ve got two or three guys I go to all the time with questions and any issues at all. That’s one of the things I like best about this place, the relationships you can build and the people you can trust.
BP: What do you like about the job you’re doing now?
CM: What I like about it is every day I come in and do something different. Some days are slower and other days are faster, but there’s always something going on.
BP: What’s your best advice for the next generation of workers?
CM: Stay hungry and stay motivated every day you’re out there. Never let up. If you’re an intern and people see you coming in on time every day, they see you take direction and see you’re willing to learn and they see that you like to work hard, supervisors will fight over you. Maintain that can-do attitude; positivity goes a long way out here.
BARBARA HOPKINS
Traffic Clerk, Nucor-Yamato Steel Hometown: Blytheville
Age: 47
Years with Nucor: 14
BLUEPRINT: When you were in high school, what was your goal career-wise?
BARBARA HOPKINS: My mind was pretty much made up that I wanted to be a secretary, working in an office. Two weeks after my high school graduation, I moved to Dallas and enrolled in Executive Secretarial College for legal assisting and that’s where my corporate career took off. From 1994 to 2007 I was in Dallas until the company I was working for started outsourcing and that was my opportunity to come back home to Arkansas.
BP: How did you get on with Nucor?
BH: Nucor was hiring a clerk; I came in with the quality department as a temp and six months later I was offered a position in the finance department as a temp. I did that for a couple of years, and then I got hired on.
BP: How have you improved your skills over the time you’ve worked at Nucor?
BH: I’ve had plenty of opportunities to do a little bit of everything. I started in finance, then went to the metal shop. The metal shop clerk position is something that is totally different from a finance clerk. And I was in the melt shop for almost seven years and that was brand-new for me.
Nucor gives you the opportunity to cross-train and learn the process. They can teach you everything you need to know if you’re willing to learn.
Nucor has also allowed me the opportunity to continue my education beyond the training they offer. Nucor reimburses you for college courses taken to improve yourself; this allows you to grow as well as help the company grow as you learn and share your knowledge.
BP: What’s something you want people to know about working at Nucor, especially young people just starting out?
BH: Nucor isn’t a cookie-cutter organization. They want you to bring in your own ideas to improve things or to make your job better. When I went through course certification in Human Resources and payroll, I’d pick up new training. I realized, OK, this is something useful.
BP: What’s the best advice you have for a new teammate?
BH: The main thing is don’t be afraid to step up and try something different. When you say “manufacturing,” you think big machines, but there’s so many other intricate parts that make a finished product. Don’t be afraid to ask questions. Sometimes we don’t know what we really want until someone tells us about it.
DIVISION: Nucor-Yamato Steel and Nucor Steel Arkansas
DIVISION: Nucor-Yamato Steel and Nucor Steel Arkansas
AVERAGE SALARY: $67,000+ based on experience
AVERAGE SALARY: $67,000+ based on experience
• Work closely with Nucor Steel Arkansas teammates, contractors and leadership to drive continuous improvement in Nucor’s safety culture, performance and safety systems.
• Work closely with Nucor Steel Arkansas teammates, contractors and leadership to drive continuous improvement in Nucor’s safety culture, performance and safety systems.
• Have knowledge of and participate in OSHA compliance, safety management system, workers compensation and ergonomic compliance.
• Have knowledge of and participate in OSHA compliance, safety management system, workers compensation and ergonomic compliance.
• Perform field industrial hygiene monitoring, as necessary.
• Perform field industrial hygiene monitoring, as necessary.
• Work with the team to develop and administer safety training.
• Work with the team to develop and administer safety training.
• Participate in and or lead safety focus groups.
• Participate in and or lead safety focus groups.
• Maintain safety, health and incident records.
• Maintain safety, health and incident records.
• Establish safety policies to promote team member safety at all levels.
• Establish safety policies to promote team member safety at all levels.
• Track safety data and use analytical tools to identify opportunities for improvement.
• Track safety data and use analytical tools to identify opportunities for improvement.
• Work with the team to maintain Safety Management System, programs and compliance issues
• Work with the team to maintain Safety Management System, programs and compliance issues
• Interact with all teammates to ensure plant-wide understanding of and compliance with federal, state and local regulations.
• Interact with all teammates to ensure plant-wide understanding of and compliance with federal, state and local regulations.
• Develop, organize and deliver safety training.
• Develop, organize and deliver safety training.
• Conduct safety inspections and audits.
• Conduct safety inspections and audits.
• Compile, review and report injury and illness statistics and OSHA 300 logs.
• Compile, review and report injury and illness statistics and OSHA 300 logs.
• Assist with the coordination of first responders and emergency response teams.
• Assist with the coordination of first responders and emergency response teams.
• Audit and monitor contractor safety programs.
• Audit and monitor contractor safety programs.
• Spend time in the mill to obtain understanding of production operations.
• Spend time in the mill to obtain understanding of production operations.
workplace not only means taking care of our team but it also creates financial stability by limiting our costs. The safety coordinator focuses solely on taking care of team members and regulatory compliance, making it one of the most important positions in the company.
workplace not only means taking care of our team but it also creates financial stability by limiting our costs. The safety coordinator focuses solely on taking care of team members and regulatory compliance, making it one of the most important positions in the company.
SKILLS, EXPERIENCE AND ATTRIBUTES:
SKILLS, EXPERIENCE AND ATTRIBUTES:
• Associate degree in related field or 4+ years’ experience in a safety position managing and presenting safety training and programs.
• Associate degree in related field or 4+ years’ experience in a safety position managing and presenting safety training and programs.
• Knowledge of OSHA, NFPA, ANSI and other regulatory standards.
• Knowledge of OSHA, NFPA, ANSI and other regulatory standards.
• Ability to prioritize and organize several projects effectively.
• Ability to prioritize and organize several projects effectively.
• Ability to analyze data and think strategically.
• Ability to analyze data and think strategically.
• First responder and EMT certification or willingness to obtain.
• First responder and EMT certification or willingness to obtain.
• Industrial hygiene and behavior-based safety experience.
• Industrial hygiene and behavior-based safety experience.
• Safety training experience and certifications.
• Safety training experience and certifications.
• OSHA Voluntary Protection Program experience.
• OSHA Voluntary Protection Program experience.
WHAT MAKES THIS POSITION IN HIGH DEMAND? Safety coordinators are in high demand partially due to their overall impact on teammates and the business. Successful individuals in this position have a desire to serve by taking care of others. The safety field’s technical needs are wide as far as standards and policies are concerned. It takes someone with a breadth of knowledge, an interest in researching and understanding multiple laws and regulations, as well as the ability to translate that information for individual teams and the company as a whole.
WHAT MAKES THIS POSITION IN HIGH DEMAND? Safety coordinators are in high demand partially due to their overall impact on teammates and the business. Successful individuals in this position have a desire to serve by taking care of others. The safety field’s technical needs are wide as far as standards and policies are concerned. It takes someone with a breadth of knowledge, an interest in researching and understanding multiple laws and regulations, as well as the ability to translate that information for individual teams and the company as a whole.
HOW DO I LEARN MORE? Please visit Nucor.com/careers to learn more about this opportunity.
HOW DO I LEARN MORE? Please visit Nucor.com/careers to learn more about this opportunity.
WHY IT’S IMPORTANT: Safety is a core part of our business; having a safe
WHY IT’S IMPORTANT: Safety is a core part of our business; having a safe
DIVISION(S): Nucor-Yamato Steel and Nucor Steel Arkansas
DIVISION(S): Nucor-Yamato Steel and Nucor Steel Arkansas
AVERAGE STARTING SALARY: $97,000 +
AVERAGE STARTING SALARY: $97,000 +
WHAT DOES THE JOB DO?
Our team is expected to demonstrate safety-minded support of our entire maintenance team while seeking to provide world-class reliability for our customers. We support our maintenance and production teams via mechanical and some electrical troubleshooting in a given area of the mill. Our team is responsible for interpreting drawings and manuals for the installation, repair and maintenance of complex equipment systems and machinery such as pumps, valves, cylinders, compressors, conveyors, overhead cranes, etc. Our department uses various pieces of equipment such as forklifts, man lifts, mobile crane, etc. in order to safely operate during routine mechanical operations. Troubleshoot and repair water systems, hydraulic systems, alloy systems, DRI system and mechanical components, plus participate and lead in all preventive and predictive maintenance programs. Mechanics are responsible for the continuous process of steel manufacturing. These highly trained technicians are responsible for complex hydraulic/pneumatic systems and installing and maintaining industrial precision equipment.
Our team is expected to demonstrate safety-minded support of our entire maintenance team while seeking to provide world-class reliability for our customers. We support our maintenance and production teams via mechanical and some electrical troubleshooting in a given area of the mill. Our team is responsible for interpreting drawings and manuals for the installation, repair and maintenance of complex equipment systems and machinery such as pumps, valves, cylinders, compressors, conveyors, overhead cranes, etc. Our department uses various pieces of equipment such as forklifts, man lifts, mobile crane, etc. in order to safely operate during routine mechanical operations. Troubleshoot and repair water systems, hydraulic systems, alloy systems, DRI system and mechanical components, plus participate and lead in all preventive and predictive maintenance programs. Mechanics are responsible for the continuous process of steel manufacturing. These highly trained technicians are responsible for complex hydraulic/pneumatic systems and installing and maintaining industrial precision equipment.
WHY IT’S IMPORTANT: Maintaining the large industrial machinery at a steel manufacturer is essential for safety, productivity and efficiency. Keeping machinery running smoothly allows Nucor to meet production deadlines and work at top efficiency.
WHY IT’S IMPORTANT: Maintaining the large industrial machinery at a steel manufacturer is essential for safety, productivity and efficiency. Keeping machinery running smoothly allows Nucor to meet production deadlines and work at top efficiency.
SKILLS, EXPERIENCE AND ATTRIBUTES: Skill sets for success in this role include knowledge of welding, cutting, hydraulic, pneumatic, alignment, big hammers, print reading, boilers, gear boxes and bearings. This position also requires excellent troubleshooting skills and the ability to make timely decisions to meet company goals.
SKILLS, EXPERIENCE AND ATTRIBUTES: Skill sets for success in this role include knowledge of welding, cutting, hydraulic, pneumatic, alignment, big hammers, print reading, boilers, gear boxes and bearings. This position also requires excellent troubleshooting skills and the ability to make timely decisions to meet company goals.
• Experience using engineering and maintenance principles
• Experience using engineering and maintenance principles
• Industrial mechanical maintenance experience
• Industrial mechanical maintenance experience
• Experience interpreting drawings and manuals for complex equipment and machinery
• Experience interpreting drawings and manuals for complex equipment and machinery
• Formal mechanical maintenance training and/or degree
• Formal mechanical maintenance training and/or degree
• Metal fabrication skills
• Metal fabrication skills
• High school diploma or GED equivalent
• High school diploma or GED equivalent
WHAT MAKES THIS POSITION IN HIGH DEMAND? Industrial mechanics have a larger array of skill sets than a mechanic, welder, machinist or lubricator. It takes a well-rounded knowledge of all the listed trades. The good news is, individuals can begin a highly rewarding career in this job area with as little as a high school diploma and advance as they add to their education, experience and job skills.
WHAT MAKES THIS POSITION IN HIGH DEMAND? Industrial mechanics have a larger array of sets than a mechanic, welder, machinist or lubricator. It takes a well-rounded knowledge of all the listed trades. The good news is, individuals can begin a highly rewarding career in this job area with as little as a high school diploma and advance as they add to their education, experience and job skills.
HOW DO I LEARN MORE? Please visit Nucor.com/careers to learn more about this opportunity.
HOW DO I LEARN MORE? Please visit Nucor.com/careers to learn more about this opportunity.
BLUEPRINT: What jobs have made up your career at Nucor?
JEFF ROBERTSON: I’ve been with the company for over 27 years, and all of my time has been in shipping.
BP: What attracted you to Nucor in the first place?
JR: What originally attracted me to this company was the pay. I come from a not-so-rich family, raised by my grandparents. I had an opportunity once I got out of college to come out here to interview. I wanted to provide for my family in the way that I didn’t have when I was growing up. I saw this as a great opportunity to do that. I was planning for my future.
BP: As someone who worked from the bottom up, what advice do you have for young people looking to get on here, or who are just starting out with Nucor.
JR: Don’t be afraid to step out of your comfort zone. Make a plan where you can see yourself five years from now. Set some goals, both short term and long-term, things that are attainable. I know at 17, 18 years old you are not always thinking that way, but you’ve got to get your game plan together.
BP: How have things changed since you were that new hire?
Hometown: Wilson
Time with the Company: 27 years
JR: It takes a little more coaching to get new teammates in the right mode. We do set expectations once you’re hired. We set expectations of what we require, and we give evaluations every 30 days to let new hires know where they’re at, where they stand and where we think they need to be or where they should be. This is a great company with lots of opportunity, if you’re willing to learn and work for it.
Intern Supervisor, Nucor Steel Arkansas
Country of Origin: East Africa
Years with Nucor: 1.5
BLUEPRINT: What brought you to the United States?
KENNEDY OGWAMBO: I came to the United States in 2006. I went to Union University in Jackson, Tennessee, and then I transferred to Williams Baptist in Walnut Ridge, Arkansas.
BP: How did Nucor enter the picture?
KO: It was something different, a different opportunity. It’s a great industry to work in and a great company to work for.
BP: Where did you start with Nucor?
KO: I started out working in shipping and receiving. My role was getting the trucks in, unloading trucks, making sure my area was clean, that everybody was safe. After about three or four months they gave me another opportunity with the maintenance department. My new role was trying to see if we could save money by doing more maintenance ourselves, so we did a lot of construction.
BP: Did you have a background in that kind of work already?
KO: I worked for myself for a while on houses and I have a few rental properties. I had to teach myself quickly and figure out how to do what I needed to get done. I learned as I went, building stuff up.
BP: Even though you’re relatively new, is there something about Nucor that stands out to you?
KO: I’ve worked in different factories, and they talk about safety, but it’s just talk. When I was interviewing here, everybody was speaking the same language and I thought, “This sounds scripted.” But now I’m speaking the same language too. Safety, man, safety is really, really big. And that, to me, means that someone cares. I’m not just a number. I’m a person.
I mean, the money is great, but making sure you go home to your family, that’s just the biggest thing. I preach that now; even when I’m at home, I’m thinking about safety.
BP: What’s your advice for new people thinking about applying here?
KO: You have to be positive. Be positive and humble and hungry and everything else will fall into place. There are so many opportunities here, you just have to have the right direction and the right people around you to push you. I have great mentors and great leaders around me and those are the people who I listen and talk to, every day.
Shortly after his 18th birthday, Jim Shelton was hired for an entry-level job at a Nucor steel mill in Utah. He landed in Arkansas in 1988 as a roll mill operator, and today he’s the roll mill manager for Nucor-Yamato Steel (NYS). He has done it all on hard work, company training, and the can-do attitude embodied by every teammate at Nucor.
As impressive of a career as his has been, Shelton said the longevity in his work life comes down to a few simple elements.
“Integrity, teamwork, optimism, those are Nucor’s core values,” he said. “I can’t imagine working for anybody else, and a lot of that is because of the opportunities offered here. We empower our teams. We encourage them to make decisions, because the men and women on the floor make things happen more efficiently. It’s not necessarily the manager or the supervisor that makes things happen, it’s the teammates on the floor.”
“Limitations are often what teammates place on themselves; those who are preparing and really taking advantage of the opportunities, see the payoff when the opportunities come.”
Nucor’s corporate culture moves intentionally to help teammates map out a career plan while preparing them for the next step through training and feedback.
“I started off as a temporary employee. I was hired as an entry level production teammate in the hot mill,” said Sammy Sanchez, Nucor Steel Arkansas Cold Mill 1 Coil Bay Supervisor at Nucor Steel Arkansas. “In six months, I got a promotion to a Burner Bander and then I got another promotion to a Furnace Tech and another promotion to a Coiler Tech and then I did an Interim Lead role in the Hot Mill.
“Everybody here is striving to be better and always looking for the next step. I was in production, then I bid on an entry-level Maintenance Utility position, figuring if I have two backgrounds, two skill sets, maybe that’ll set me up for a supervisor role.”
Sanchez said at each step of his 16-year career, teammates and training opportunities helped him master new skills and develop a broader view of the overall work process. But like Shelton, he said the fundamentals of building a career don’t change, even if job titles do.
“When you have goals, are energetic, have the right attitude and mindset, and are eager to learn, the leadership team sees it,” he said. “They see you have a passion to get better. Those are the teammates they look to for promotion.”
Ashley Kroll is another example of a teammate who has leveraged her opportunities over 12 years with Nucor-Yamato Steel, where she’s recently been promoted to Environmental Coordinator Management Representative. From being the only woman in her steel tech internship to tackling every professional challenge placed in her path – including relocating for work to Texas for nine months with a small child in tow –Kroll has taken “can-do” to another level.
“Don’t be scared. Don’t be intimidated,” she said as advice to the next generation. “I didn’t know how to work a Microsoft Excel spreadsheet when I came here. Nucor paid for the class and I came back knowing how to work Excel, Microsoft Word and Microsoft Project. The point is, there’s always someone here ready to help, but you’ve got to be willing to figure out what you want to do and then give it your all to go do it.
“Be coachable, be open-minded and have the drive. Because if you have the drive and are coachable, that’s going to lay the foundation for everything else.”
BLUEPRINT: Did you grow up working with your hands?
SAMMY SANCHEZ: All my life, I’ve always worked with my hands. In Chicago my family had a mechanic shop, so I was always around tools. My dad was always working on trucks or fixing things. I love doing those type of things. I love fixing things.
In school, I took wood shop. I also took mechanics because I wanted to know how to troubleshoot problems with equipment and the tools used to fix them. Also, in the summer when I was growing up, I’d work at the golf course running the tractors, front-end loaders, backhoes.
Cold Mill 1 Coil Bay Supervisor, Nucor Steel Arkansas
Hometown: Chicago
Age: 39
Years with Nucor: 16
BP: How have you improved your skills since you have been at Nucor?
SS: Out here, you learn skills that you wouldn’t think you would use. I learned how to weld from teammates who are certified welders.
I took classes and learned how to operate heavy equipment.
BP: What’s the Nucor culture like?
SS: Continuous improvement is promoted here. It doesn’t matter who you are; you make your own career path. It’s here if you want it. If a teammate has that drive to advance, we help them with leadership, help them with public speaking, with business acumen to help on the business side, dealing with new teammates and hiring teammates. We put them through the courses to help them get better.
BP: What’s the best advice you could give to someone looking to follow in your footsteps?
SS: This is a great company. If my kids wanted to come here and work, I would promote that because I would want another generation of my family to work here. It takes drive and it takes effort, but your career is all up to you.
Hometown: Armorel
Age: 57
Years with Nucor: 31
BLUEPRINT: Where did you grow up?
CHARLES CASEY: I grew up right here in Armorel. I can look out the door and see the patch of woods where our house sat years ago. I ride on the same roads to work that I rode on the school bus as a kid.
BP: Do you have a college background?
CC: I have training from technical school in machine experience, CNC machines and others like that.
BP: What made you want to come work at Nucor?
CC: Nucor-Yamato was built in ‘85 or ‘86, and I graduated in ’84 so I had heard about Nucor. When I got out of school I went into a vocational/technical school to learn how to be a machinist – which was a highly sought-after opportunity for people. I got into that kind of work and one thing led to another as far as my machine experience.
I worked for Milwaukee Tool, and they sent me to CNC training. I left there and went to BorgWarner and made car parts there, and then I got a call and was asked if I would be interested in interviewing here at Nucor Hickman. I came in for an interview and they offered me a job a few days later. The rest is history. I’ve done very well at Nucor for my family.
BP: Have other family members followed in your footsteps?
CC: Since I’ve been at Nucor, two of my sons came to work for Nucor. One is in shipping at Nucor-Yamato Steel (NYS) and the other one works in the mill. My oldest son works at Atlas right next door. We’re all in the steel business.
“YOU MAKE YOUR CAREER PATH. IT’S HERE IF YOU WANT IT.”
—SAMMY SANCHEZSAMMY SANCHEZ CHARLES CASEY Cold Mill 2 Supervisor, Nucor Steel Arkansas
Roll Mill Manager, Nucor-Yamato Steel
Hometown: Belleville, IL
Age: 55
Years with Nucor: 37
BLUEPRINT: What is your background?
JIM SHELTON: My uncle used to work for a steel company in California that closed down, and when Nucor Utah was built, he was recruited. We used to visit my uncle every year, and the steel industry just interested me. I started with Nucor 15 days after I turned 18. I worked at one of our other divisions in northern Utah for three years and then transferred to Nucor-Yamato Steel (NYS) in 1988 when this division was built.
BP: How did you learn the job skills you needed, starting that young?
JS: Nucor invests time in training new teammates, they are our most important resource. You are not just put out on the floor to figure it out on your own. I had a lot of folks along the way who taught, coached and mentored me throughout my career. We have a training calendar at our division so that the team has access to training that is available. Some training is required annually to make sure everyone is refreshed on certain topics.
Nucor also offers tuition reimbursement for teammates and their spouses who have an interest in furthering their education. We have several different safety ownership teams to get involved with that have different subject matter and offer team building and leadership opportunities without a title.
We also offer cross-training in different areas. If a teammate has an interest in an area, and maybe wants to learn more about it, they sign up on their days off to work in a different area which gives them a look at what it’s like in other areas of the mill and gives that area a look at the teammate. There are a lot of opportunities at Nucor, the sky is the limit, you just need to take advantage of the opportunities when they are available.
BP: What other skills do people need to be successful at Nucor?
JS: To me, attitude, the ability to learn, and getting along with others, those are things you start with. Those are fundamental traits to build a successful Nucor teammate from. From a leadership standpoint, it’s having the ability to create relationships, having the courage to have tough conversations on the front end, and understanding your team.
BP: How does it feel to have created such a long and successful career?
JS: I can’t imagine working for anybody else. We empower our teams at the floor level to be creative and look for safer and more productive ways of doing the things we do. It’s not the manager or the supervisor who makes things happen, it’s the teammates on the floor. You don’t have to have a position in management to be a leader at Nucor. It is very fulfilling to see new teammates join Nucor and watch their careers develop and be successful long-term teammates.
Inside Sales Representative, Nucor-Yamato Steel
Hometown: Blytheville, AR
Age: 37
Years with Nucor: 3 years
BLUEPRINT: Did you start out to go into manufacturing?
SHANNON WOOLSEY: I earned an associate degree from Arkansas Northeastern College in 2009. From there I went to Arkansas State University Tech Center for a cosmetology and cosmetology instructor licenses. I owned a salon and then worked for a salon for a few years.
BP: How did that turn into a career in the steel industry?
SW: As a cosmetologist, I had a lot of clients who worked at Nucor. I had never been out to Nucor, didn’t even know where it was located. I had this one customer in particular who said, ‘I think you would be a good fit for Nucor.’ I enjoyed what I was doing, and the schedule, but one door led to another and before I knew it, I was at Nucor to interview and was hired.
BP: What’s the best thing about working at Nucor?
SW: Something I’ve really enjoyed about Nucor is the chance for advancement. If you’re open to new possibilities, there’s someone there who’s going to push you along and help you along the way. Internal advancement has always been preached and practiced here at Nucor.
BP: What have been some ways you have improved your overall skillset?
SW: I was part of the group that started Toastmasters at Nucor Yamato. I was also part of the Blytheville Leadership Institute which helped me learn more about what northeast Arkansas has to offer. I have completed the company’s Seven Habits of Highly Successful People class and I’m currently going through the Extreme Ownership program.
BP: What advice do you have for the next generation?
SW: Be respectful of leadership and other teammates, be a hands-on teammate, be willing to jump in and help and avoid saying, ‘That’s not my job.’ Be humble and willing to take the trash out if it needs to be taken out.
Communication is another important thing. We do a lot of coaching on communication skills. Someone in New York probably does not have the same personality or mindset that I have as a Southern girl. I have to know how to communicate with customers all over the United States.
DIVISION(S): Nucor-Yamato Steel and Nucor Steel Arkansas
DIVISION(S): Nucor-Yamato Steel and Nucor Steel Arkansas
AVERAGE SALARY: $88,000+
AVERAGE SALARY: $88,000+
WHAT DOES THE JOB DO?
WHAT DOES THE JOB DO?
Our team is expected to demonstrate safety-minded support of our entire maintenance team while seeking to provide world-class reliability for our customers. We support our maintenance and production teams via electrical and mechanical troubleshooting in a given area of the mill. Our team is responsible for planning, installation, programming, testing and troubleshooting of electrical machinery and automation systems. The person in this role must diagnose process and equipment problems and take appropriate measures to resolve issues. Shift electricians are responsible for the continuous process of steel manufacturing. These experienced industrial automation systems technicians are responsible for planning, installing, programming, testing and troubleshooting of electrical machinery.
Our team is expected to demonstrate safety-minded support of our entire maintenance team while seeking to provide world-class reliability for our customers. We support our maintenance and production teams via electrical and mechanical troubleshooting in a given area of the mill. Our team is responsible for planning, installation, programming, testing and troubleshooting of electrical machinery and automation systems. The person in this role must diagnose process and equipment problems and take appropriate measures to resolve issues. Shift electricians are responsible for the continuous process of steel manufacturing. These experienced industrial automation systems technicians are responsible for planning, installing, programming, testing and troubleshooting of electrical machinery.
WHY IT’S IMPORTANT: Electrical interruptions in the steel-making process can be costly. Shift electricians are the first defense against avoidable downtime. They rely on their years of experience and training to solve complex troubleshooting issues, which is essential for an efficient steelmaking process.
WHY IT’S IMPORTANT: Electrical interruptions in the steel-making process can be costly. Shift electricians are the first defense against avoidable downtime. They rely on their years of experience and training to solve complex troubleshooting issues, which is essential for an efficient steelmaking process.
SKILLS, EXPERIENCE AND ATTRIBUTES: Some of the skill sets for success in this role include understanding of electrical theory, process instrumentation, ability to read electrical schematics, troubleshooting skills, programming experience and control systems.
SKILLS, EXPERIENCE AND ATTRIBUTES: Some of the skill sets for success in this role include understanding of electrical theory, process instrumentation, ability to read electrical schematics, troubleshooting skills, programming experience and control systems.
• Understanding of electrical theory, process instrumentation and control systems
• Understanding of electrical theory, process instrumentation and control systems
• Ability to read electrical schematics
• Ability to read electrical schematics
• Ability to troubleshoot electrical systems and equipment
• Ability to troubleshoot electrical systems and equipment
• Proficient in the use of electrical test equipment
• Proficient in the use of electrical test equipment
• Related industrial maintenance and automation experience in a manufacturing facility OR equivalent electrical training OR equivalent military experience
• Related industrial maintenance and automation experience in a manufacturing facility OR equivalent electrical training OR equivalent military experience
• Experience with medium-high voltage
• Experience with medium-high voltage
• Usage and limitations of various electrical troubleshooting tools and instruments
• Usage and limitations of various electrical troubleshooting tools and instruments
Experience with:
Experience with:
• PC, PLC, PID control and visualization programming
• PC, PLC, PID control and visualization programming
• AC motors and drives/maintenance and control of DC motors
• AC motors and drives/maintenance and control of DC motors
• Electrical, pneumatic and hydraulic LOTO
• Electrical, pneumatic and hydraulic LOTO
• Hydraulic and pneumatic troubleshooting
• Hydraulic and pneumatic troubleshooting
• Industrial motor starter circuit layout and troubleshooting
• Industrial motor starter circuit layout and troubleshooting
• Industrial instrumentation
• Industrial instrumentation
WHAT MAKES THIS POSITION IN HIGH DEMAND?
WHAT MAKES THIS POSITION IN HIGH DEMAND?
Industrial shift electricians require experience or equivalent technical training. Individuals with this skill set are in high demand and are being heavily pursued by all industrial facilities. Nucor also offers many job opportunities in this area where people of various skill levels can start potentially leading to high-level career positions.
Industrial shift electricians require experience or equivalent technical training. Individuals with this skill set are in high demand and are being heavily pursued by all industrial facilities. Nucor also offers many job opportunities in this area where people of various skill levels can start potentially leading to high-level career positions.
HOW DO I LEARN MORE? Please visit Nucor.com/careers to learn more about this opportunity.
HOW DO I LEARN MORE? Please visit Nucor.com/careers to learn more about this opportunity.