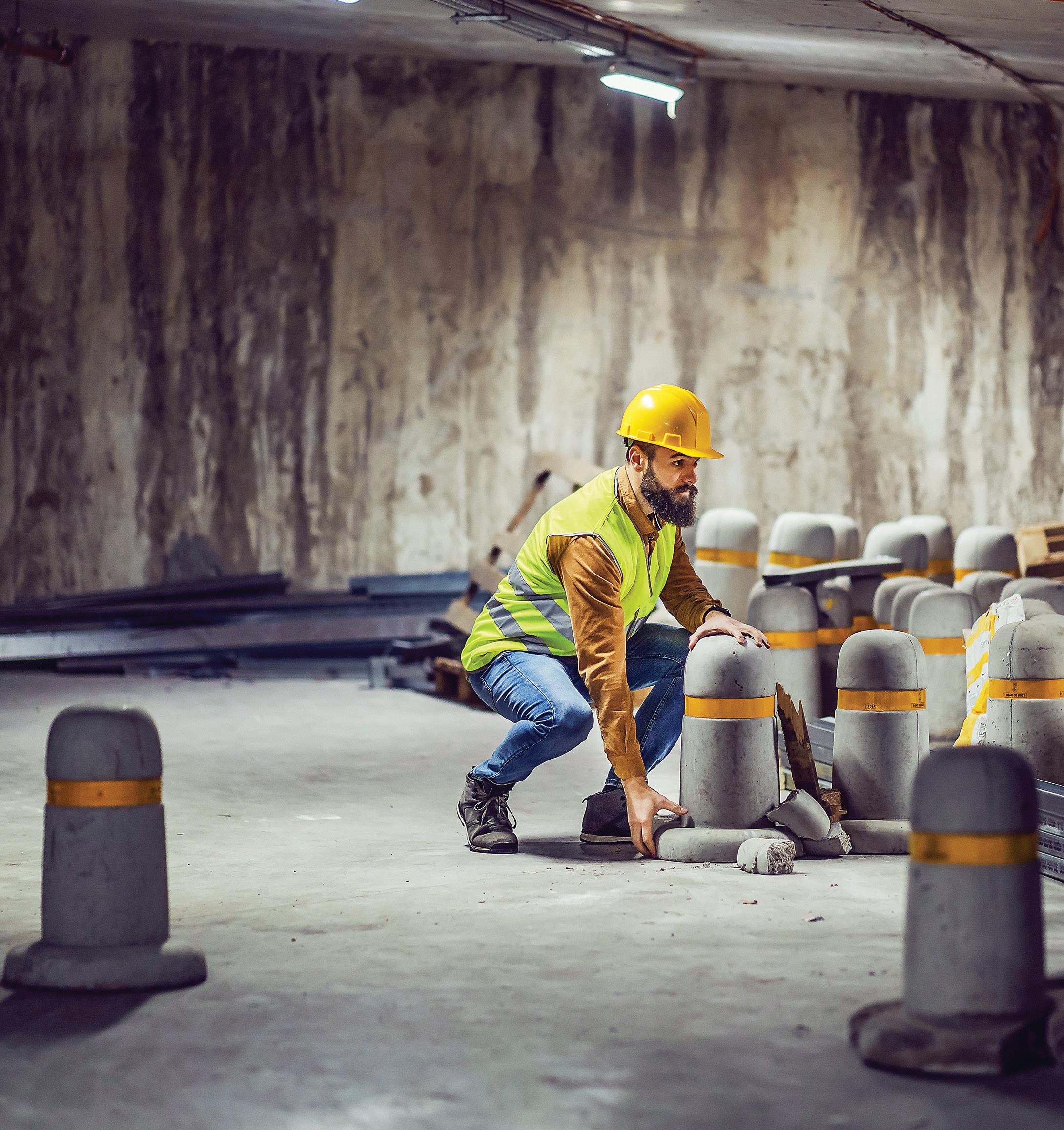
27 minute read
Workplace Manual Handling
The physical and economic cost of Work-Related Musculoskeletal Disorders in Australia
SafeWork Australia indicate that workrelated musculoskeletal disorders (WMSDs) have decreased considerably in the number of compensation claims. Regardless of this, WMSDs still account for the majority of workers’ compensation costs in Australia and continued to be the leading work health and safety issue in 2020 costing the Australian workforce more than $28 billion.1 Further, SafeWork Australia highlighted that in 2015-16 the National Data Set for Compensation-based Statistics: “identified a total of almost 125,000 accepted workers’ compensation claims for WMSDs in 2015–16. Of these 62,420 or 50 per cent were serious claims, meaning the worker had at least one claim-related week of absence from work. Serious claims for WMSD diseases and injuries comprised 58 per cent of all serious claims. The median time lost from WMSD injuries has increased from 5.0 to 5.2 since 2011–12. While the overall rate of serious claims has been declining over time, compensation costs and ongoing issues with lost time both suggest that WMSD claims continue to be
a serious challenge. The frequency rate of WMSDs is highest in those aged 45–64, at more than four serious injuries per million hours worked. Males have a higher frequency rate in all age groups and types of WMSD claims except the female 45–54 group for WMSD diseases.” 2
HAZARDOUS MANUAL TASKS
Hazardous manual tasks are one of the main causes of WMSDs and include injuries such as sprains and strains of muscles, ligaments, tendons and joints. The back, neck, shoulder, elbow, wrist, abdomen and knees are the most commonly affected parts of the body.3 When one or more of the following risk factors are present a manual task becomes hazardous: • repetitive or sustained force • high or sudden force • repetitive movement • sustained or awkward posture • exposure to vibration • mental stress / work pressure4 These six factors are also known as the characteristics of hazardous manual task and being exposed to one or more of them can lead to an injury. The NSW Government has a Code of Practice for Hazardous Manual Handling Tasks, August 2019 detailing how to manage the risks associated with hazardous manual tasks.
LEGAL OBLIGATIONS
In accordance with — Work Health and Safety (WHS) Regulation 2017 – Clause 60:
A person conducting a business or undertaking (PCBU) must manage risks to health and safety relating to an MSD that are associated with a hazardous manual task.
To manage risk, a duty holder must: • identify hazards that could give rise to the risk • eliminate the risk so far as is reasonably practicable • if not reasonably practicable to eliminate the risk, minimise the risk by implementing control measures in accordance with the hierarchy of control • maintain the control measure so that it remains effective • review risk control measures.5
HOW TO LIFT POSITION STATEMENT
Employers often commit both time and resources to the provision of how to lift training for their employees. Such an investment makes good business sense provided the training is designed effectively. To be effective training needs to be tailored to ensure the inclusion of the hazardous manual tasks as detailed below by HWSA. In the how to lift position statement the HWSA state (and NSW Code of Practice Hazardous Manual Tasks) training should cover: • manual task risk management, including hazardous manual task risk factors and sources of risk • specific manual task risks and the measures in place to control them • how to perform manual tasks safely, including the use of mechanical aids, tools, equipment
and safe work procedures • how to report a problem or maintenance issues6
RISK MANAGEMENT PRINCIPLES
HWSA indicates that an employer needs to follow the “risk management principles specific to the hazardous manual tasks” to enable the management of hazardous manual tasks in the workplace. Risk management principles: • Identifying which manual tasks are hazardous (manual tasks that expose a worker to one or more hazardous manual tasks risk factors) • Determining why a task is hazardous • Eliminating the hazard, then controlling any remaining risk by following the hierarchy of control. Control measure(s) should address the source of the risk • Maintaining and reviewing the control(s) to ensure continuing effectiveness Note: these risk management principles must be adhered to as per the NSW Work Health and Safety Regulation 2017 (Part 3.1 and Clause 60). 7
SOURCE OF RISK
SafeWork NSW states the sources of risk are the things that are responsible for a risk factor being present: • Workplace design and layout • Systems of work including organisational and psychosocial factors e.g. work rate, lack of job control • Work environment e.g. poor lighting • The nature, size, weight or number of persons, animals or things involved in the task8 It is not only a legal obligation on an employer to manage risks to health and safety in relation to WMSD that are associated with a hazardous manual task – it also makes good business sense to protect your employees and your company. Mend Services has the knowledge and expertise to assist employers meet their legal obligations. Mend can help the employer identify hazardous manual tasks, and conduct hazardous manual task risk assessments that identify the source/s of risk. Mend can tailor and deliver onsite the appropriate training package to address the risk assessments identified.
6 SafeWork NSW - How to lift position paper – FAQs. 7 Ibid. 8 Ibid.
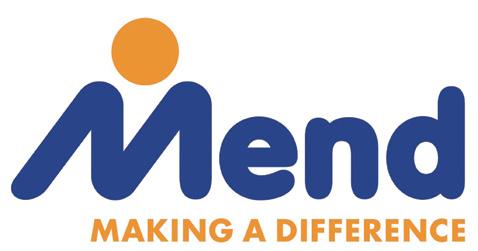
FMC embrace innovation
In this day and age, we are constantly faced with higher expectations, challenging designs, and new method requirements — the Ronald McDonald House in Perth was one such build. As an international charity that helps the families of sick children with support and accommodation during their times of treatment, it was essential that the building be an exemplary design and construction for this type of project and purpose. The building achieved a LEED [Leadership in Energy and Environmental Design] Silver rating and a global recognition and certification for environmentally sustainable buildings — the first of its kind in Australia. Several significant challenges presented themselves at Ronald McDonald House. In particular, the new construction method affected the supporting basement retaining walls by creating gaps in the structure large enough for a small child to squeeze through. As with every unique project, this required a new way of thinking. The Homeguard team at FMC Australasia proudly assisted the HomeGuard Accredited Installer, Termico Pest Management Services, to install a HomeGuard Termite Management System. The solution was HomeGuard termite protection ‘sheeting’ – it provided great flexibility coupled with chemical repellence that could wrap the retaining walls and cover all entry points from subterranean termite infestation with no worries about exposure to residents as it is fully contained in the sheeting’s matrix. HomeGuard is designed, researched and developed in Australia for Australian conditions to last for the design life of the building. So, Ronald McDonald House can rest assured that in the future their limited funds can be spent on the young patients and their families, not on continual termite treatments. Perth’s Ronald McDonald House by Perth Architect Gerry Kho, built by Doric Construction HomeGuard installed by Termico Pest Management Services, and supported by FMC Australia.
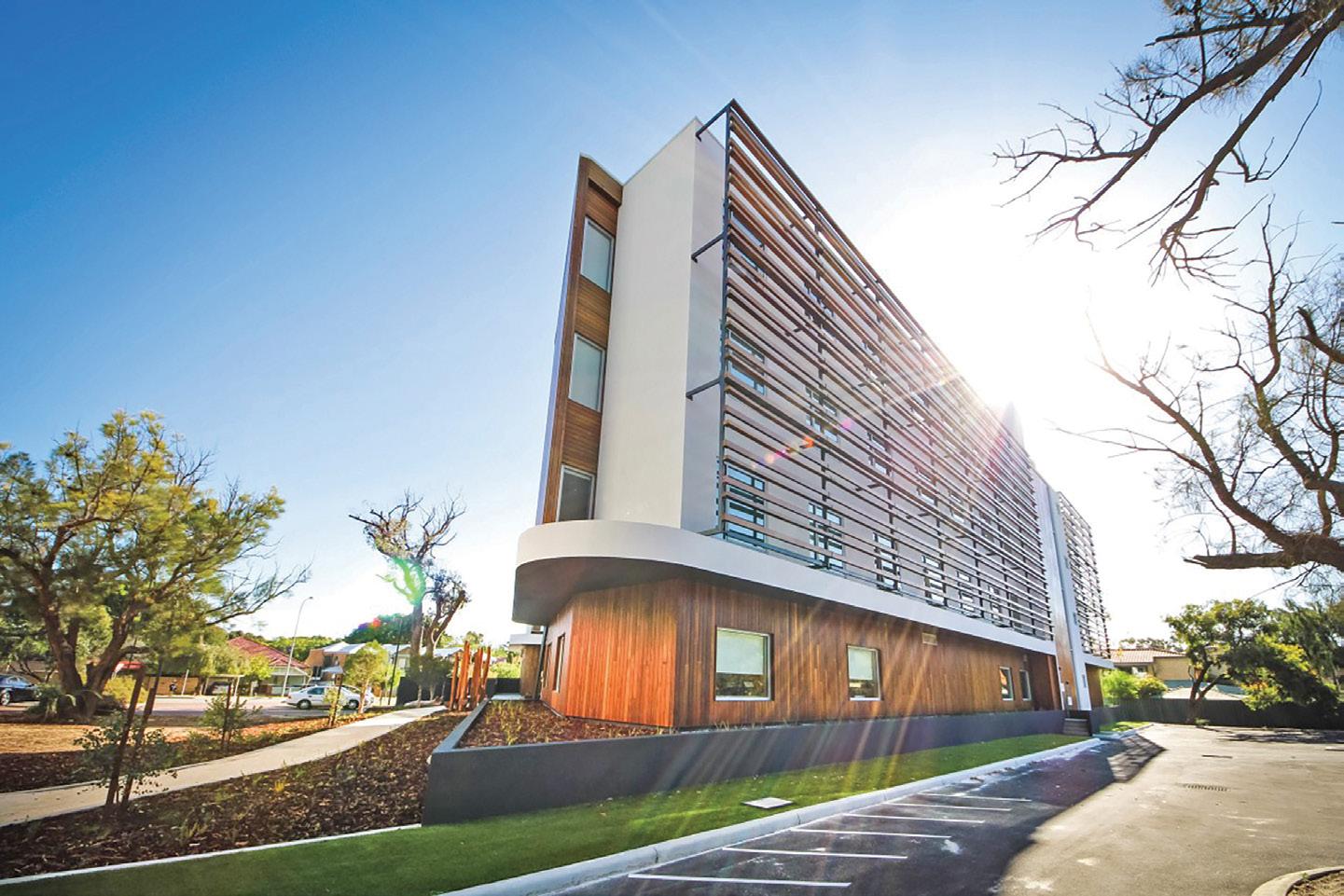
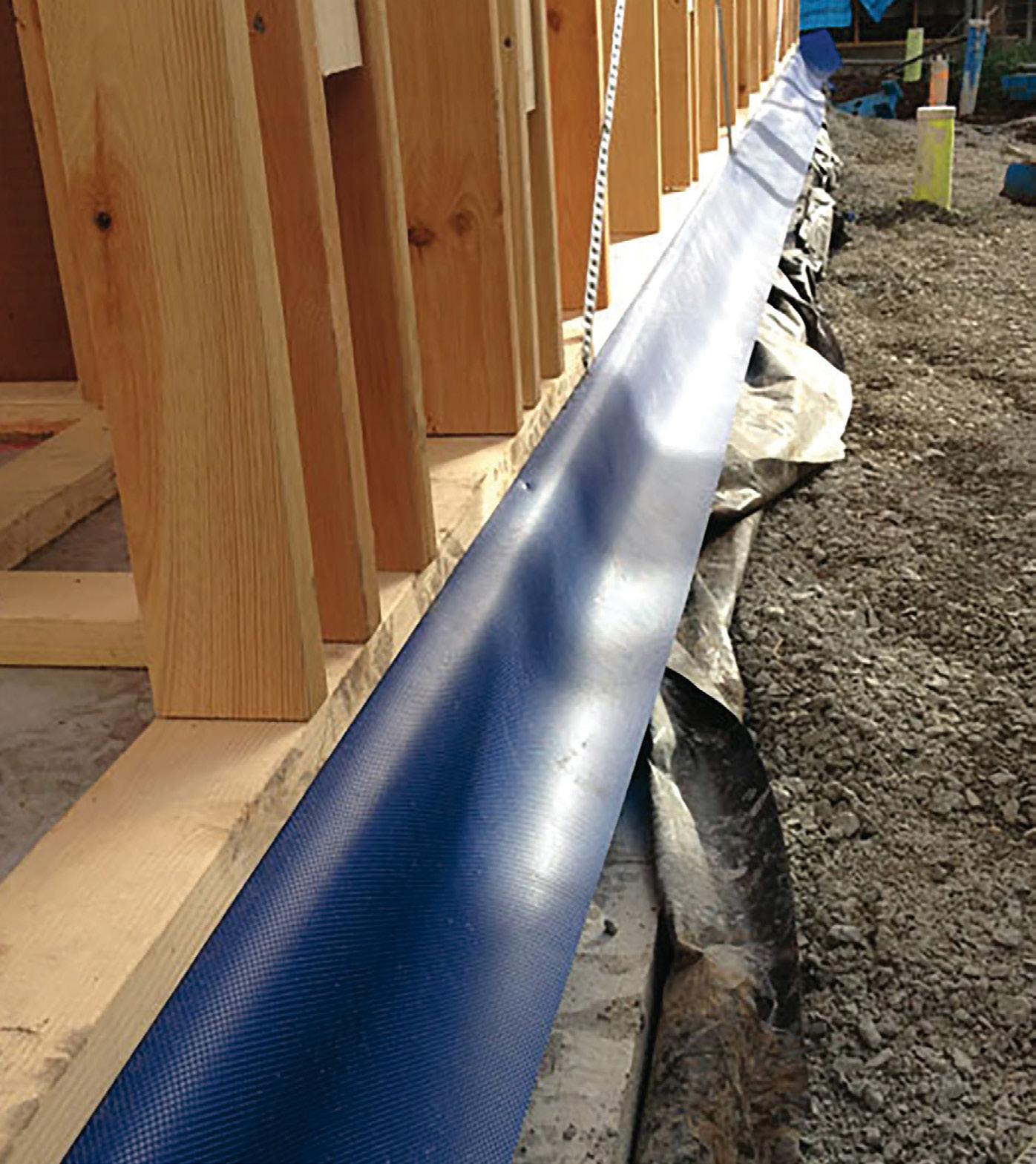
Manufactured in Australia
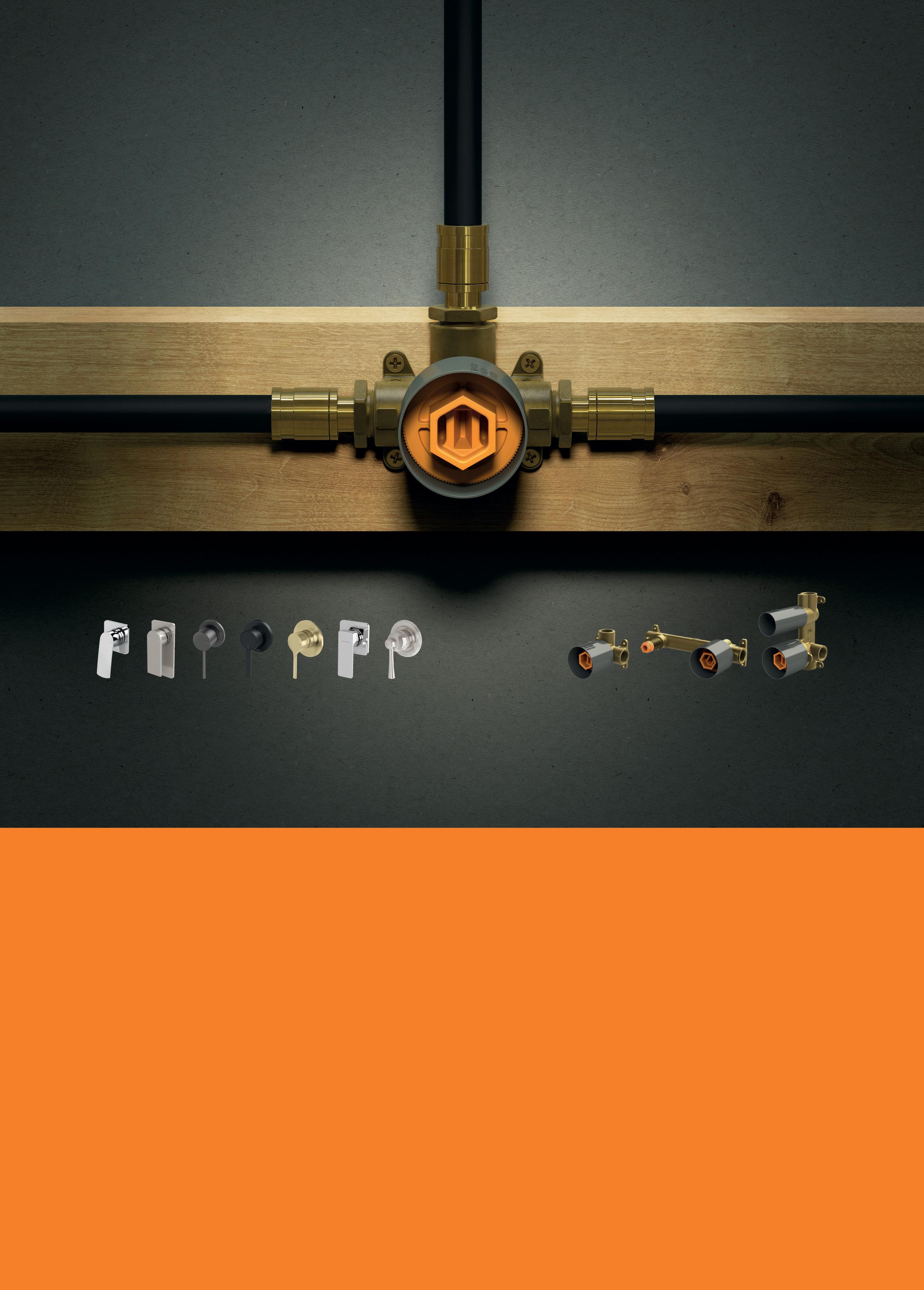
Make the Switch to time and money saving mixer technology
The use of traditional mixer bodies on job sites can often be fraught with issues. The building job timeline can be prolonged due to delays in decision-making, or parts being out of stock. There is also the potential for parts to be damaged, misplaced or stolen during the process of construction. SwitchMix® by Phoenix is a revolutionary innovative technology offering the ultimate flexibility with bathroom fittings. Consisting of two main components, the rough-in kit (in-wall component) and fit-off kit (the cartridge, handle and backplate), SwitchMix® allows more time for your clients to consider design and finish selections without holding up construction as the components can be ordered separately. There are many benefits for those in the building industry to make the move towards this new mixer technology.
Convenience
Compact Rough-In Kits can be carried on hand with ease, are readily available for the next job and there is no risk of damage to the finish.
Low-cost rough-in
Mixer cartridges are supplied with Fit-Off Kits, keeping Rough-In Kits low cost, compact and easy to install.
Time saving
Fit-Off Kit design and finish can be decided and ordered later, preventing expensive delays on the job site.
Pressure Testing
Easy options for testing water lines without the cartridge or a hot water service connection. High pressure testing suitable up to 1500kPa.
Innovative seal
Rough-In Kits are designed with a plastic waterproofing sleeve to ensure waterproof integrity is never compromised, when tapware changes are made in the future.
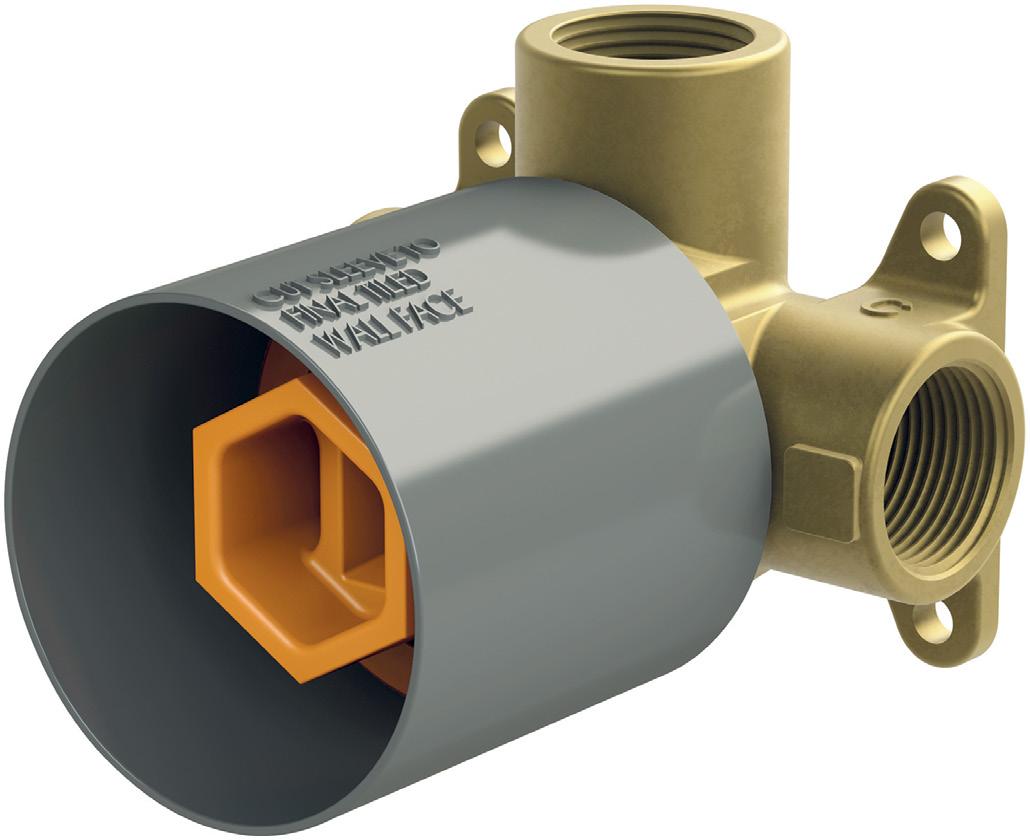
Flexible selections
SwitchMix® is compatible with multiple Phoenix collections, with up to five finishes to choose from. This allows your client to easily select a new design or finish in future without having to remove or damage tiles and compromise the waterproofing, as all the changes are made front of wall. This opens a whole new world of design opportunity, with the flexibility to easily follow trends as they come and go. This presents a great point of difference to give to clients when presenting quotes or when they are making their fixture and fittings selections.
Multi-residential benefits
Building developers can easily create multiple looks in one multi-residential project, offering buyers more flexibility and the opportunity to easily update their tapware in the future. To watch our video explaining the features and benefits of SwitchMix®, simply scan this QR code. Or visit our website https://www.phoenixtapware.com.au/ switchmix-collection
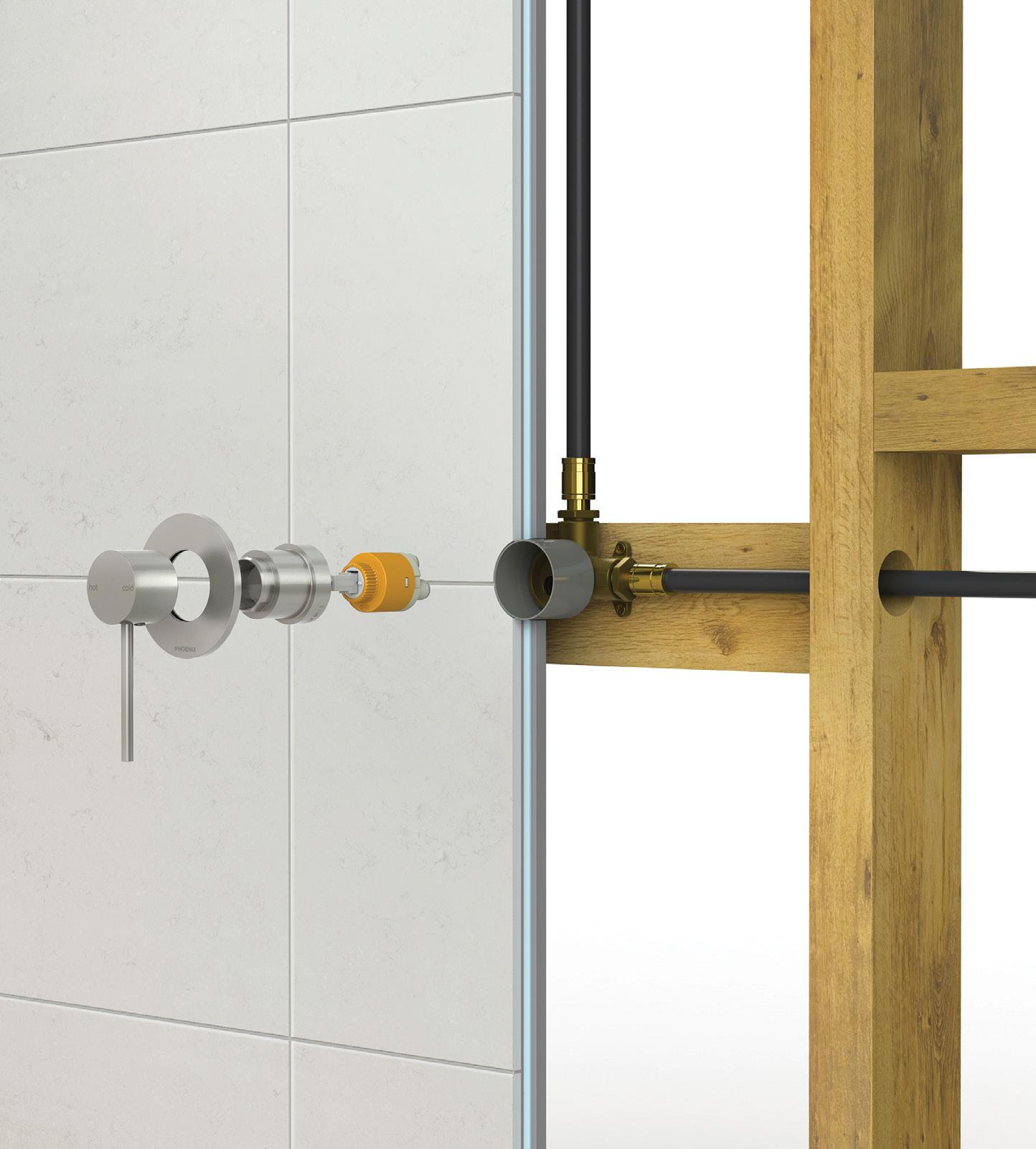
With the phrase ‘net zero’ being bandied around, and the evergrowing public discussion on carbon, climate and cutting greenhouse gas emissions, there couldn’t be a better time to talk about the key role that certified forest management and certified forest products play in combating climate change.
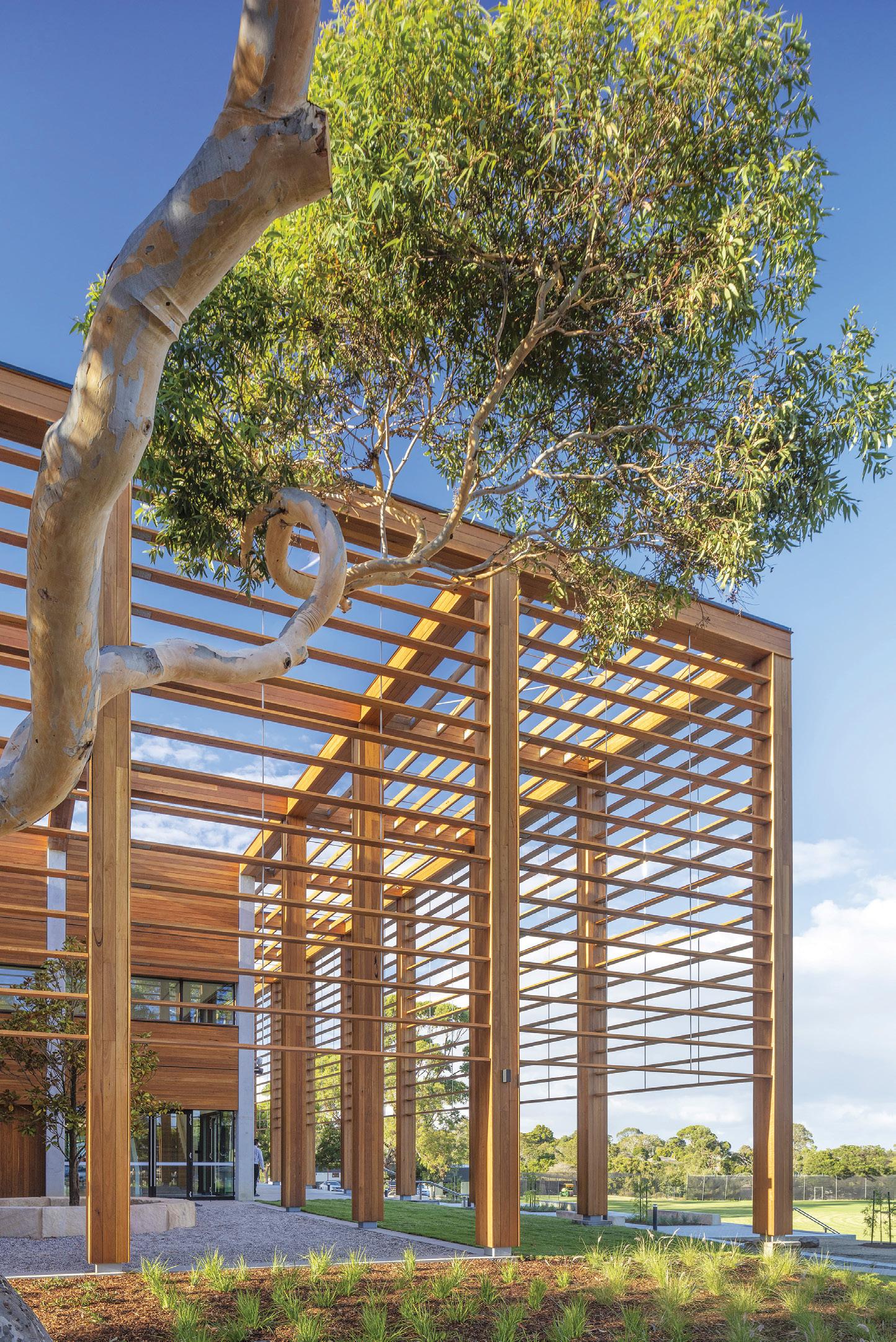
Timber is the ultimate renewable resource and has been used in construction for centuries, but where does it fit inside a circular economy model and how does it contribute to carbon cycles? It is well known that forests are a major component of the global carbon cycle because of the large amounts of carbon they capture in the soil and their biomass. Perhaps less known is that the storage of carbon in harvested wood products gradually increases over time, especially for long-lived products such as electricity poles and floorboards. This was highlighted in a report published by the NSW Department of Primary Industries in 2021 based on research conducted by Dr Fabiano Ximenes et al. Notably, the report also highlights that carbon is effectively stored in products, even beyond their intended use in a landfill. Whilst the relationship between forests and carbon, and timber as a renewable resource might be well known, it is important to remember that not all forests and forest products are managed in the same way. Forests certified through globally recognised standards like the joint Australian and New Zealand Standard for Sustainable Forest Management (AS/NZS 4708 – 2021) are designed to manage forest values and productivity for generations to come. Deforestation and conversion practices are not supported in the standard. Organisations certified to the sustainable forest management standard are independently audited each year against internationally endorsed and science-based, world-class standards. The standard has been designed to create outcomes that are socially just, culturally relevant, ecologically sound, and economically viable. In addition, internationally recognised chain of custody certification standards (like PEFC ST 2002 and AS 4707) promote sustainable forest products through forest product supply chain transparency and traceability. “The forestry and timber industries have a chance to share a compelling story, highlighting the role that their forests and products play in the fight against climate change,” says Jonathan Tibbits, Responsible Wood Marketing & Communications Manager. Mr Tibbits added: “Research has shown that when it comes to product substitution when timber products replace non-renewable alternatives, it results in lower net greenhouse gas emissions.” This year’s Timber Design Awards continues to publicly recognise excellence in the use of Australian Certified Timber and/or timber products which are sourced from certified Australian forests.
Peninsula Grammar’s new creative hub in Mt Eliza. 2022 Entrant: Alatus (creative school hub in Mt Eliza). Architect: FJMT Studio. Builder: 2Construct. Photographer: John Gollings.
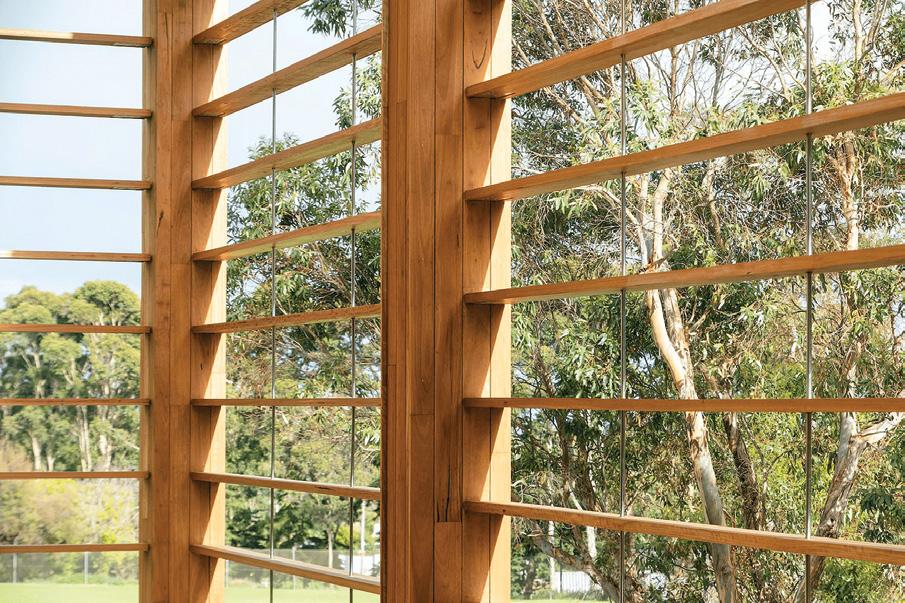
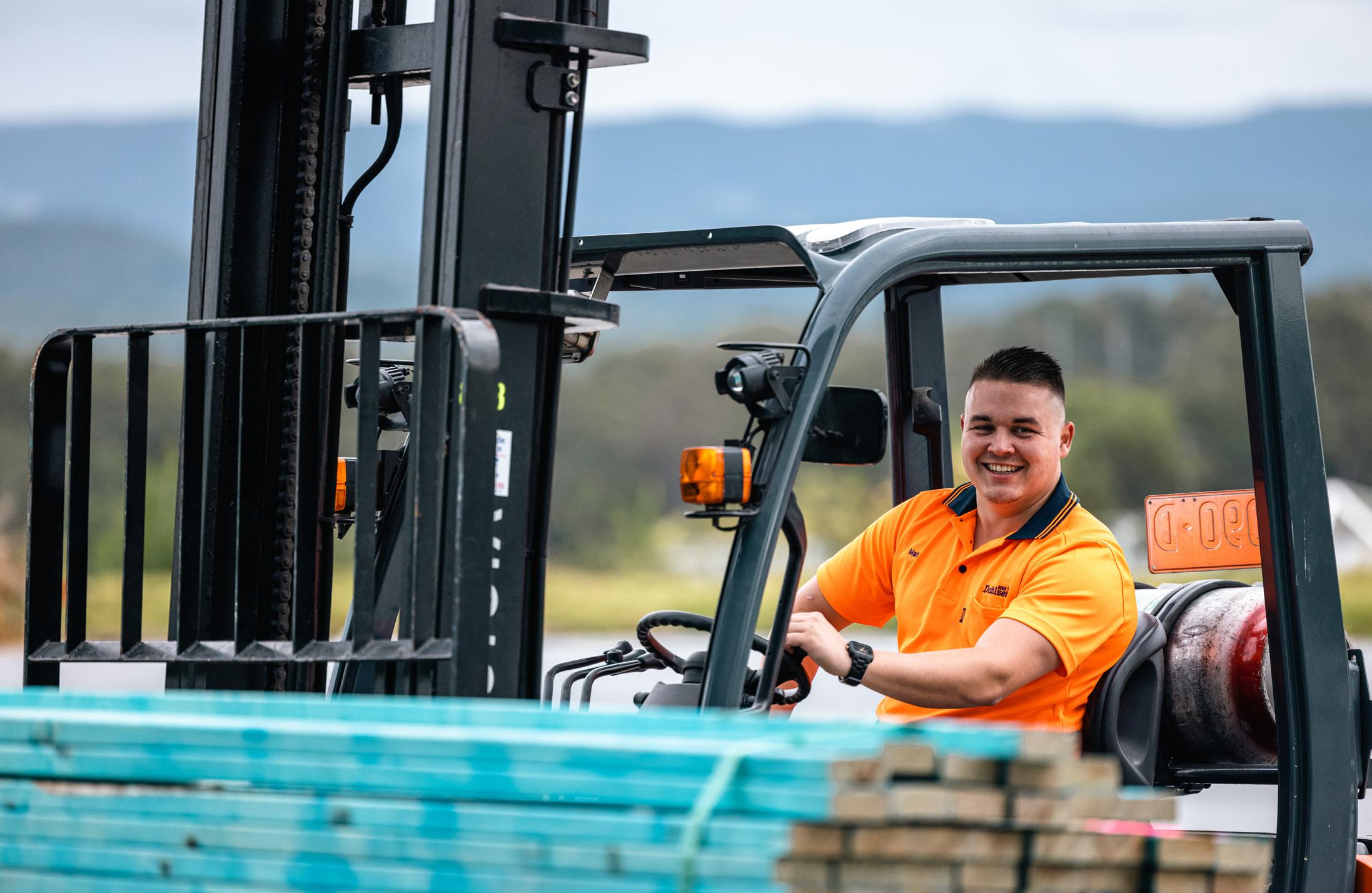
Dahlsens, a rare treasure in the building industry
While it’s rare for an Australian company to have been around for 145 years, Dahlsens is proud to hold this record and to remain 100 per cent family owned. The family legend is that a fortuitous gold find was the start of everything for the company, with founder Johan Christian Dahlsen arriving in Australia 14 years prior to striking gold in 1863. For more than 40 years, Johan worked in the Gippsland gold mining industry, using his earnings to build a newly formed hardware business. In September of 1877, when Johan received a large consignment of timber and advertised his plans of starting up the timber yard business, Dahlsens was born - and the rest, as they say, is history. Fast forward to 2022 and the company is still family owned and operated, marking an impressive six generations of Dahlsens in the business. Today, Dahlsens is the largest builder-focused merchant in Victoria and New South Wales, operating a total of 40 trade stores, truss and frame manufacturing plants and roofing manufacturing plants throughout the two states, all experts in servicing the trade. There are also subsidiaries trading in Far North Queensland under the Cairns Hardware Company, and in the Northern Territory and Broome (Western Australia) as Nortruss Group. In the past 12 months, Dahlsens has invested heavily in its service and network, opening six new trade stores, and acquiring two more truss and frame manufacturing plants in New South Wales, upgrading the (formerly) Midcoast Timber Centre network across the state to better support the needs of the trade. Right across Greater Sydney, the Central Coast and Newcastle, wherever you’re building, you can now access whole-of-house building materials and truss and frame with one phone call. The company has also branched out since the days of Johan’s timber consignments, and now offers building solutions to new home and alteration/addition builders in bulk trade quantities – from foundation to fit-out, wall frames to door handles, roof trusses to bathroom products, cladding to doors, decking to insulation and more, Dahlsens offers a convenient one stop shop for all building materials. A team of trade experts - including account managers, logistics professionals and trade support team - can work directly with you to organise delivery and drive-through pick-up of building materials to meet your project lead
times, as well as the installation of items such as blinds, heating, ventilation, cooling, and insulation. An extension of your team who care about your success, you can depend on your local Dahlsens team and account manager for reliable service and helpful advice. With Dahlsens, you can also get truss and frame manufactured using SpeedTruss by Pryda - an innovative approach to roof truss design and installation that incorporates preinstalled screws which act like an assembly kit, reducing installation time and greatly improving safety. With SpeedTruss you can fix everything into place at, or below, the top plate – a total gamechanger. There is more to come for Dahlsens, as it continues to invest in its people, partners and communities, expanding and enhancing its ability to support builders and trades today and for decades to come. If you’d like to open an account, request a quote or have a general enquiry, visit your local store — which you can find by visiting dahlsens.com.au/store-locator — or contact Dahlsens’ NSW Sales Manager, Shane Selby, by calling 0409 354 592 or emailing shane.selby@dahlsens.com.au Issue Four | October-December 2022 | MBA NSW 31
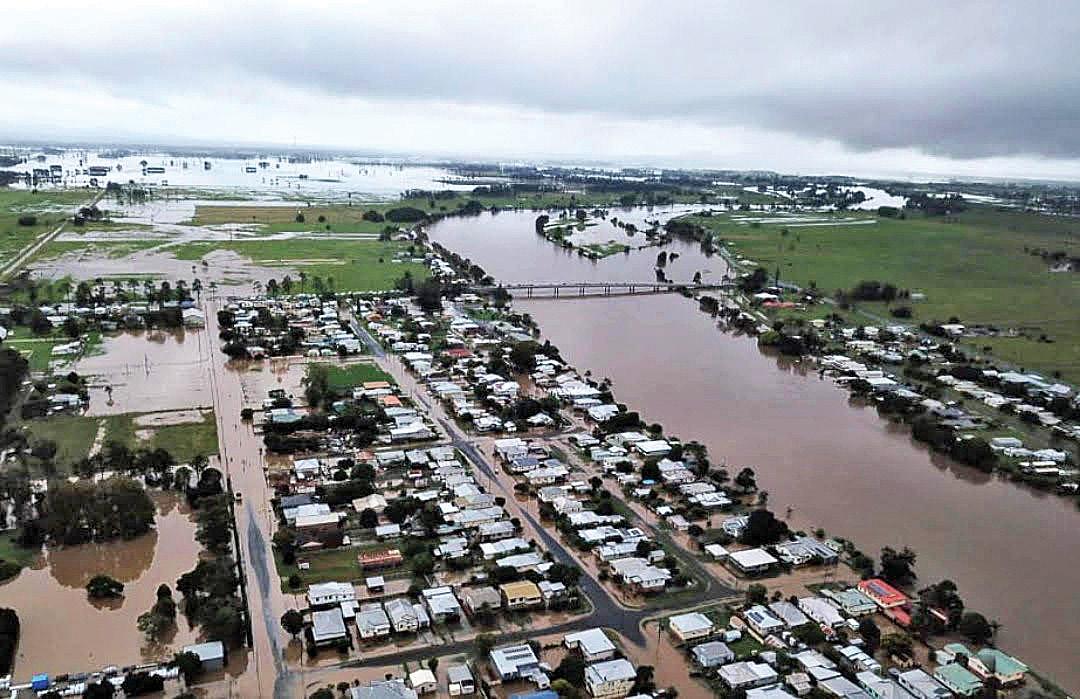
With flooding events becoming more frequent, FloodClad Composite Cladding products offer a range that is strong, durable and extremely resilient.
Revolutionary interior/exterior cladding product
Powerful protection during floods or fires
While Governments strive to meet the challenges of Climate Change, one innovative Australian company has been hard at work, developing specialised composite building and cladding products. FloodClad Composite Cladding products offer a range that is strong, durable and extremely resilient when it comes to the extreme, diverse challenges of the Australian climate. It offers diverse protection from flood, fire, termites, mould, bacteria, impact and sound. FloodClad offers an outstanding range of products in floors, walls, ceilings, roofing, eaves, soffits, decking, etc to suit every need. Finally, we discover a product that protects on multiple levels. This product appears to be the greatest single advance in construction cladding history, when considering multifaceted protection/performance, economic gain and long lasting, low maintenance for dwellings in flood/fire-prone areas. A better choice long term, FloodClad is a resilient and diverse solution. The beauty of FloodClad Composite products is they do exactly what they are designed to do: protect people and property in multiple ways from serious threats, while being kind to the earth… and they last, providing long term peace-of-mind. FloodClad is planet friendly and has a very low carbon footprint. Being an MgSO4 product, FloodClad is a water inert cladding, an MgSO4 product - scientifically developed, it is primarily inorganic composite. It is 100% recyclable. FloodClad eliminates repetitive costs and genuinely delivers - being the most resilient and versatile product available on the market. Owners who proactively choose to make their properties more resilient, will realise not just financial gains, but ensure greater stability and wellbeing for those who occupy them, as well as being kind to the planet.
FloodClad remains inert in water and during flooding - even over long periods - and when correctly water-sealed during installation, can protect timber framing from serious water absorption. After flooding, lightly scrub off water marks and repaint if required. A very inexpensive, easy process, to return things back to some kind of normality. Government Projects Benefit: Agencies involved in procurement of quality construction products would benefit from this product development — particularly where such cladding is used in temporary or emergency accommodation — as well as wherever there is risk of fire, flood, termites or mould. FloodClad is sold direct to builders and construction companies with national supply capability.
More info: visit www.floodclad.com.au, a product of the FireCrunch Group.
Issue Four | October-December 2022 | MBA NSW 33
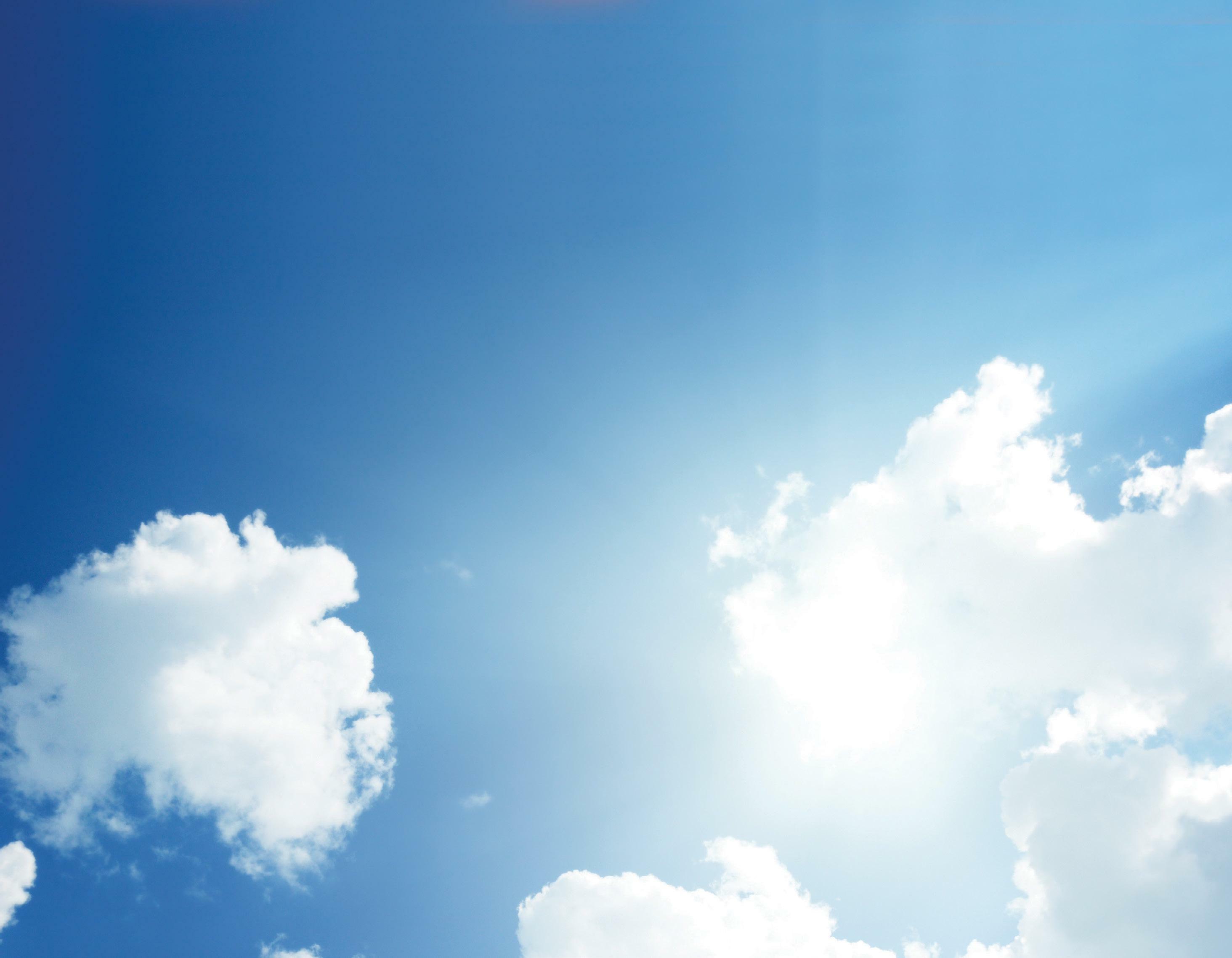
A reroof is the perfect time for VENT-A-ROOF®

Following ongoing water leaking issues with their tiled roof, the owners of this home in Moorooka, Queensland, decided to address the problem by upgrading and replacing their tiles with CUSTOM ORB® steel roofing. The reroofing work was undertaken by IRT roofing, with the owners deciding that as part of the process, they would take the opportunity to also install the innovative VENT-A-ROOF® ventilation system. Having sound ventilation is an important consideration in every home, as it provides many benefits for occupants: in warmer months the hot air escapes the home more freely keeping living spaces cooler, while in colder temperatures humid air can more easily escape, minimising the chance of condensation, and reducing the likelihood of mould and other issues. VENT-A-ROOF® is a concealed and passive system that uses the power of natural airflow to ventilate ceiling cavities. It’s suitable for use in domestic, commercial and light industrial buildings with metal roofs, and is installed under traditional ridges, hips and barges, resulting in a sleek and clutter-free roofline. Along with providing superior performance, the aesthetic benefits of the VENT-A-ROOF® system were particularly important to the homeowners, according to Vent-A-Roof Sales Manager, Chris Cuschieri. “The home sits on a sloping block and as a result the entire roofline is visible from the street,” Chris said. “Given that every part of the roof is on display, the owners wanted to avoid the obtrusive ‘bolt-on’ appearance of traditional systems such as wind-driven rotary ventilation systems. VENT-A-ROOF® is completely concealed, so it maintains the roof’s clean look and the home’s street appeal.” On this project, VENT-A-ROOF® was installed across three of the roof’s ridges, providing a complete ventilation solution for the entire home. To have achieved similar ventilation performance from traditional systems would have required fitment of multiple devices, which could have caused inherent problems according to Chris. “One of the other many benefits of VENT-AROOF® is that the system doesn’t require any penetration of the roof, this avoids leaks and the potential of having ongoing maintenance issues,” he said. “Installed across three ridge sections over approximately 15 metres of roofline, the owners of this house will benefit by having a complete ventilation solution for the entire home; to have achieved a similar outcome using winddriven rotary ventilation system, multiple units would have been needed which is impractical and costly. Another drawback of wind driven systems is that they can be quite noisy – as a passive system with no moving parts, VENT-AROOF® is completely silent. Chris said that a growing number of customers, particularly those who were reroofing their homes, were choosing to install VENT-A-ROOF®
as part of their renovation project. “If a homeowner is considering reroofing, this is the perfect time to install VENT-A-ROOF® as either a replacement to their previous traditional ventilation system, or as their first-time ventilation solution,” Chris said. “While the system is already cost effective compared to traditional systems, if the installation occurs during a reroof, the process becomes even more efficient.” VENT-A-ROOF® is fully compatible with both ZINCALUME® steel and COLORBOND® steel, proven performers in the harsh Australian Climate. The system is also BAL and Cyclone-rated, meets ‘Form 15’ compliance and is compliant with 2019 NCC ventilation requirements. VENT-A-ROOF® is available nationally from Lysaght branches and resellers. For more information visit www.lysaght.com/vent-a-roof. Issue Four | October-December 2022 | MBA NSW 35
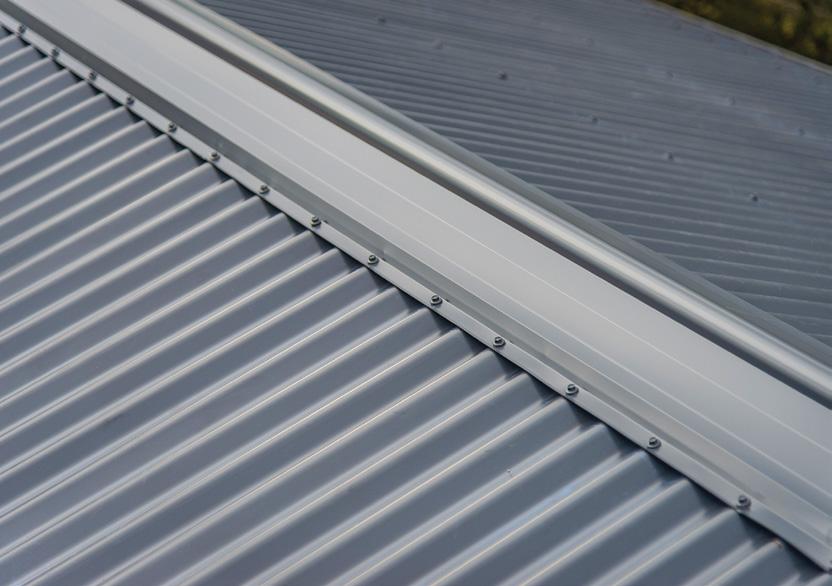
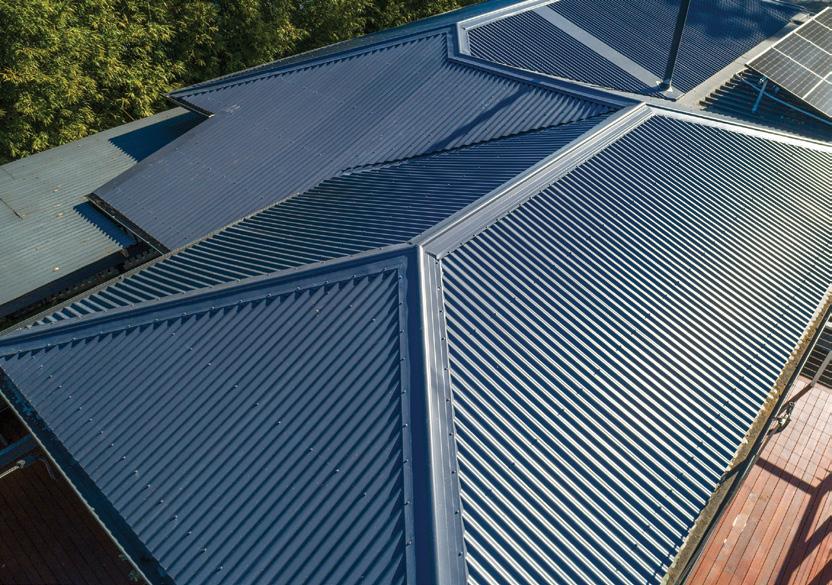
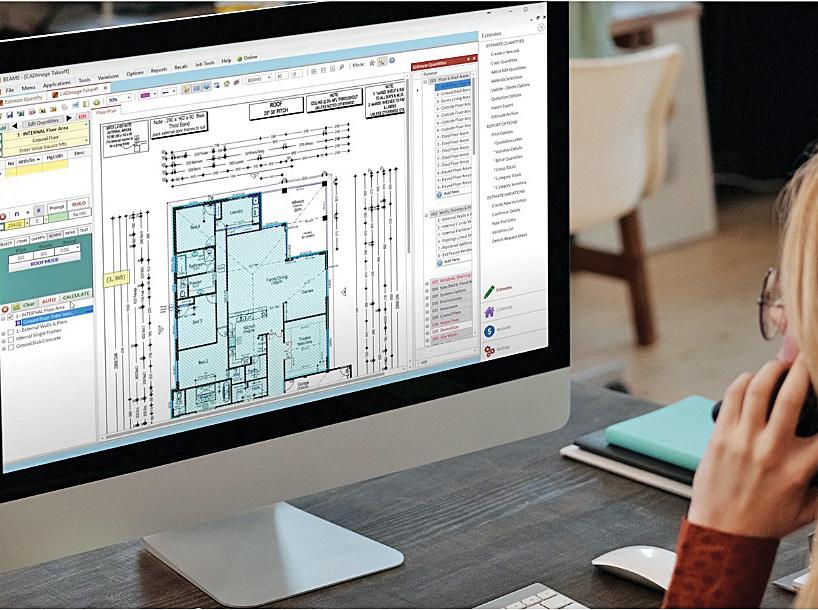
Much more than a building quoting software package, BEAMS easily streamlines all the complex processes
They say necessity is the mother of invention and when it comes to the success story of the construction software, BEAMS – this saying couldn’t be truer. Founded in Perth by director Peter Fonte, the concept for the software came about when, working as a builder himself, he realised the need for an integrated building package. BEAMS was five years in the making and although initially developed for internal use only, the ease and functionality of the software prompted them to make it available for commercial use in 1994. Since then, BEAMS has enabled a greater understanding of what is required to manage and maintain a profitable business thanks to its coverage of the entire building process. Unique in its offering, BEAMS covers web leads in CRM, estimating with CAD Image, scheduling and accounts, plus the addition of mobile functionality. In addition to this, BEAMS is backed by an experienced and dedicated team who are constantly looking for ways to improve the package which is in perpetual development as the market changes and users’ needs evolve. When it comes to setting itself apart from other similar products on the market, BEAMS offers the unparalleled knowledge and understanding of a builder / company director with years of practical, hands-on experience. “BEAMS software was developed by a builder who understands the wants and needs of users within the construction industry,” Peter said. “BEAMS customer support is suited to both the East and West coast, resulting in the longest support hours for our Clients. “We are currently the only software provider that integrates the functions of at least nine separate applications generally required to manage and operate a successful business, such as word processing, document storage, estimating, scheduling, CAD Image Take-off, email monitoring, accounting, CRM & Beams Mobile — to name a few.” And while having a vast offering is a key point of business for BEAMS Software, simplicity and functionality have always been areas in which they endeavour to deliver time and time again. “Users are able to prepare quotes quickly and respond to their clients in a timely fashion,” Peter said. “We offer the ability to maintain accurate cost control which results in better profits, including time-line scheduling. “BEAMS is keeping up with legislation changes including GST, T Par, Super Stream, Single Touch Payroll and provides full financial reporting, including BAS & PAYG.” Backed by more than 28 years in business and a relentlessly dedicated team, it is easy to see why BEAMS continues to lead the way in the construction software industry and with international expansion plans in the pipeline, it seems the sky is the limit for this innovative company.
NEWCASTLE Newcastle Master Builders Apprenticeship Scheme accolades
Newcastle MBA Apprentices were fortunate this year to have three of its apprentices and trainees as finalists in the annual AEN (Apprentice Employment Network of NSW & ACT) Awards in Sydney competing against the State’s Best. Bowen Schmitt (Carpenter 4th Year) won the Downing Pooley Award, whilst Lara-Jane Haggerty (Trainee Admin Cert III) and Nathan Andrews (Plumber 4th Year) were unfortunately pipped at the post! Well done to all the finalists and thanks to their Host Employers (David Compton Building, HL Mullanes Plumbing and Lara was our own NMBA Trainee) for the momentous training and guidance they deliver to their young people in training. So, that event has finished off a big year for everyone for 2022 and Christmas is just around the corner! We at Newcastle MBA Apprenticeship Scheme would like to thank all our Host Employers, Apprentices, Trainees, and suppliers for all your support and wish you a very Merry Christmas and a safe and Happy From left: Nathan Andrews, Lara Haggarty, Bowen Schmidt. Below: Kyran Hancock.
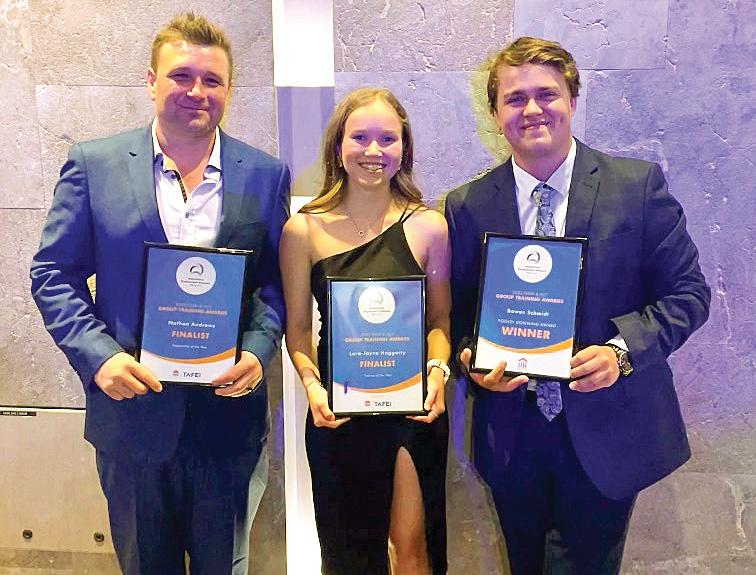
New year! Also remember, if you are looking for a new apprentice for the new year, give us a call and we can show you how easy it is to have an apprentice or trainee in your business! We congratulate Kyran Hancock on being awarded Apprentice of the Month for October. Kyran is hosted with N & D Contracting and has shown an outstanding level of progression and improvement since his last assessment, demonstrating Kyran’s excitement and passion for his trade. Well done Kyran! Keep up the great work! Brett Lester — General Manager GT&P
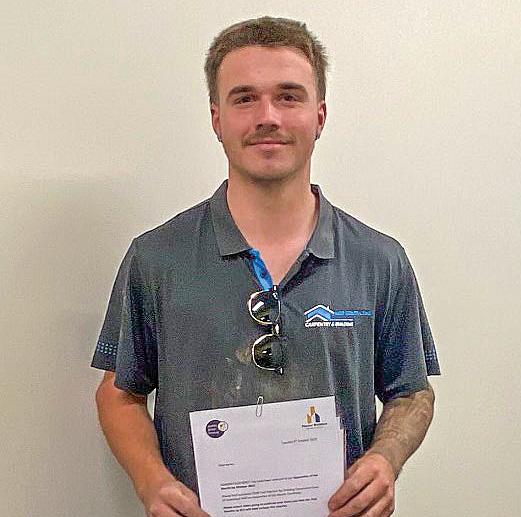
Protection against termites
Still the Australian Standard in Termite Protection
Kordon is a physical termite management system and can be used for perimeter or full under-slab protection. It is quickly and easily installed in all building applications by the Accredited Kordon Network and is certified by the Australian Building Code.
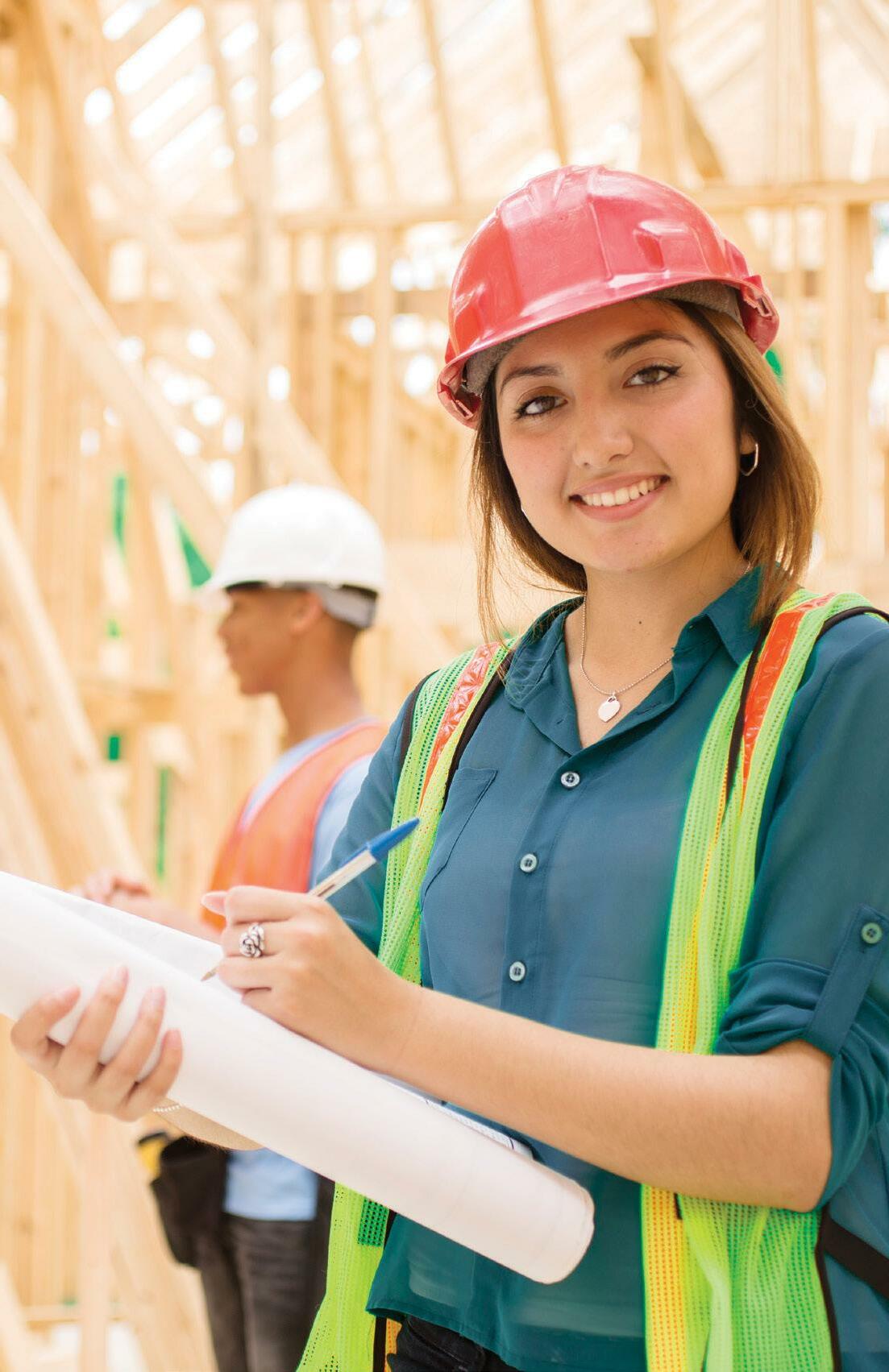
CMA-CM40182
ALWAYS READ THE LABEL BEFORE USE 2022 Environmental Science AU PTY LTD Suite 206, 737 Burwood Rd, Hawthorn East, VIC. 3123 Technical Enquiries: 1800 024 209 + www.au.envu.com Kordon® is a Registered Trademark of 2022 Environmental Science AU PTY LTD Envu and the Envu logo are trademarks of Environmental Science U.S. Inc. ©2022 Environmental Science U.S. Inc.
PASSING OF KEN AUSTIN
On the 22nd of October, our great mate Ken Austin sadly passed away. Ken was a long serving member of MBA for over 37 years. He served on two MBA/NSW Divisions, as an active Committee Member, President and Secretary. Ken also represented the Central Coast/ Hunter Region on the MBA Council of Management for many years. Ken was recognised by the committee in 2019 for his contribution to the Central Coast Division and the MBA. He was awarded the Divisional Gold Medal, an award that is bestowed upon a member, by his/her peers – it is an award that represents the highest recognition by fellow builders on an individual who has contributed to the division and the MBA. Most of all Ken was a very proud family man, who worked hard all his life to provide for and support his wife Faye, children Sally, Scott, Stuart and Stephanie (dec) and all his grandchildren. On behalf of the MBA and Central Coast Committee we thank you for your service and passion for the industry, you will be deeply missed by us all.
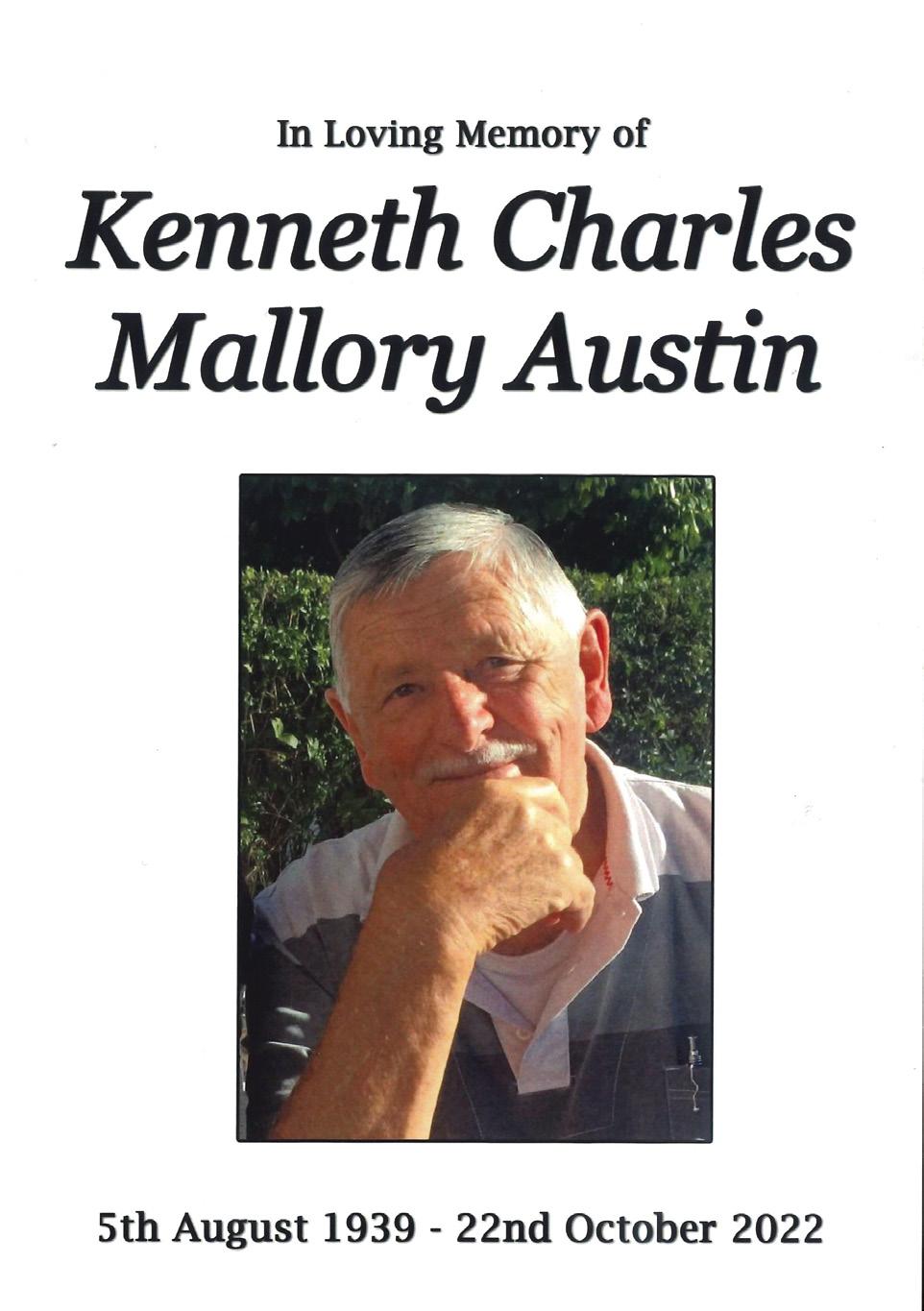
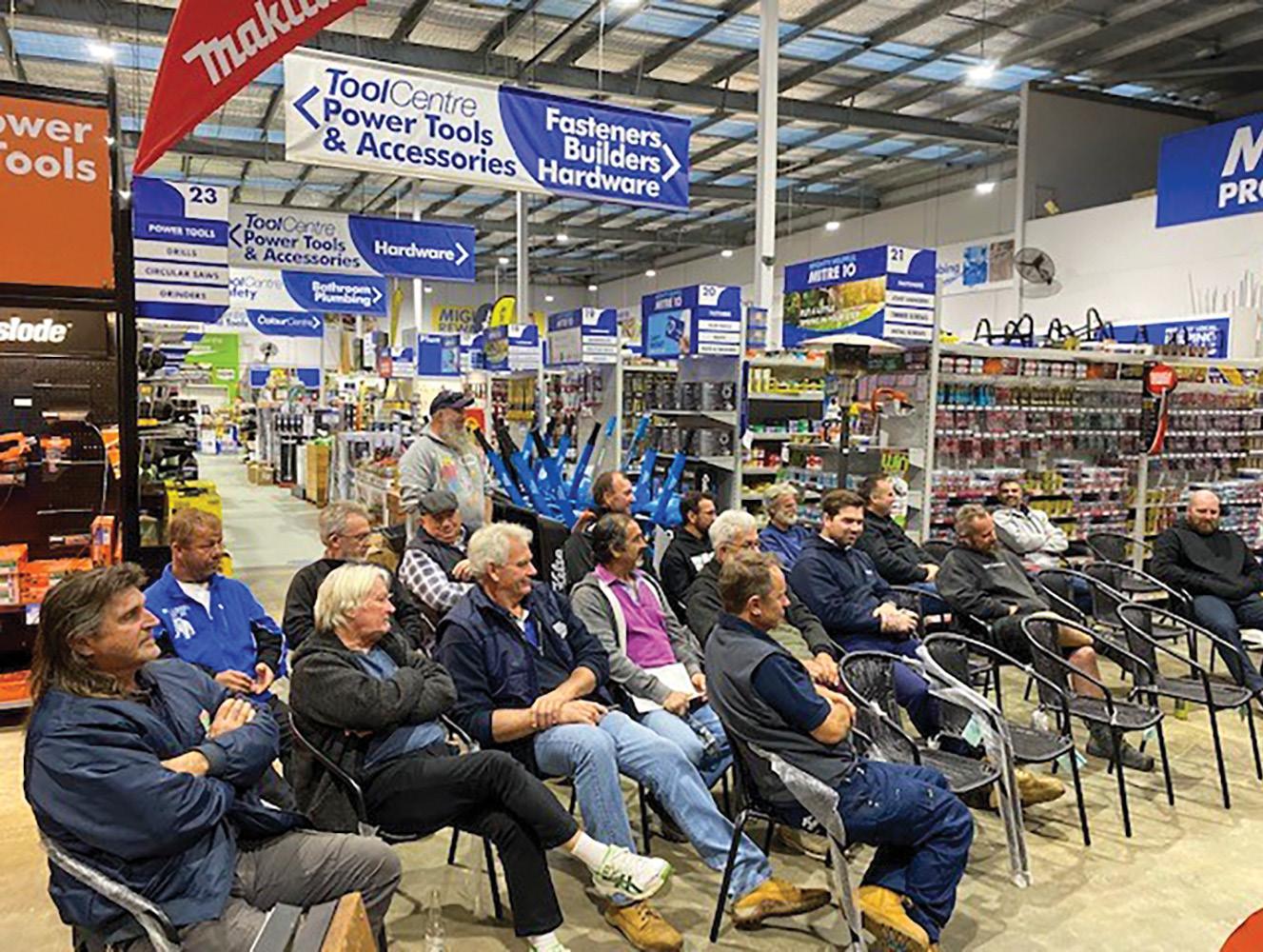
Information Night Mitre 10 Kincumber
On Wednesday 5th October, we held our AGM and Information Night at Mitre 10 Kincumber. Thank you, Matthew and the team from Mitre 10 for hosting the event during some wild and wet conditions. Also, great to have Nick from Outdoor Stair Kits Australia give us a demonstration of his product. The members had the opportunity to look over the Principal Kitchen display with Dianna answering any questions about the range of features and easy installation.
Amber from DoneDeck braved the wet weather to set up her mobile BBQ. The presentation on your new range of accessories and full timber profile range was well received. The AGM went well, with 12 nominations for the 2023 Central Coast Committee.
Are You Balancing Work and the Books? Are You Able to Pay Staff and Bills? Are You Stressed Chasing Payments? Are You Feeling Family or Lifestyle Pressures?
28 Years Experience Knowledge of the Law Over $20M Paid
With passion for the job and compassion for clients, Subbie Assist is a creative problem solver with strong writing ability and communication skills. Subbie Assist has the willingness to listen with healthy scepticism and perseverance to get the job done — giving you YOUR LIFE BACK!
It’s up to you to take the fi rst step ~ it can be done swiftly!
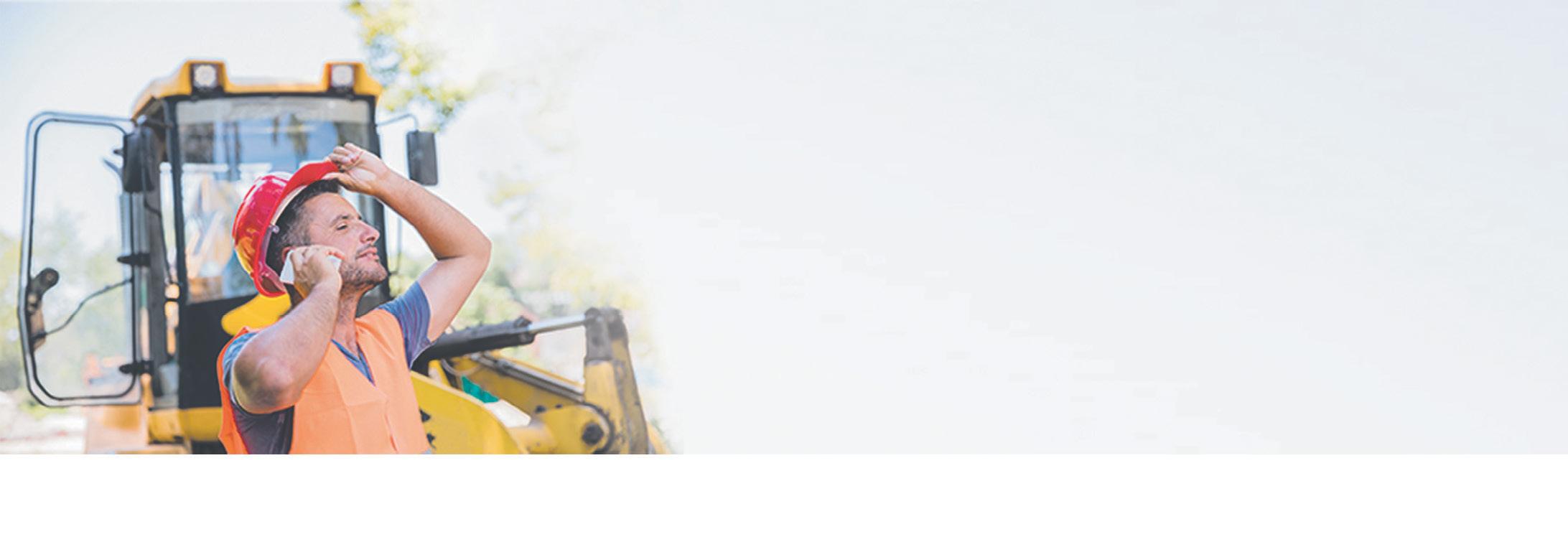
Getting your life back start with one simple phone call 0400 221 360
Newcastle St George Castle Hill Port Macquarie Wollongong Manly Ballina Liverpool Rosehill Wednesday 15 February 2023 Wednesay1 March 2023 Wednesday 22 March 2023 Wednesday 7 June 2023 Wednesday 28 June 2023 Wednesday 19 July 2 2023 Wednesday 23 August 2023 Wednesday 11 October 2023 Wednesday 15 November 2023 NSW Excellence in Housing Saturday 16 September 2023 NSW Excellence in Construction Saturday 4 November 2023 Riverina Murray Regions Friday 31 March 2023 Northern Regions Saturday 27 May 2023 Southern Regions Saturday 15 July 2023 Western Regions Friday 18 August 2023 Newcastle Regions Friday 8 September 2023
Refer A Mate to join Master Builders and receive a $50 eGift card to spend at over 130 retailers.
Scan QR code or go to mbansw.asn.au/refer-mate
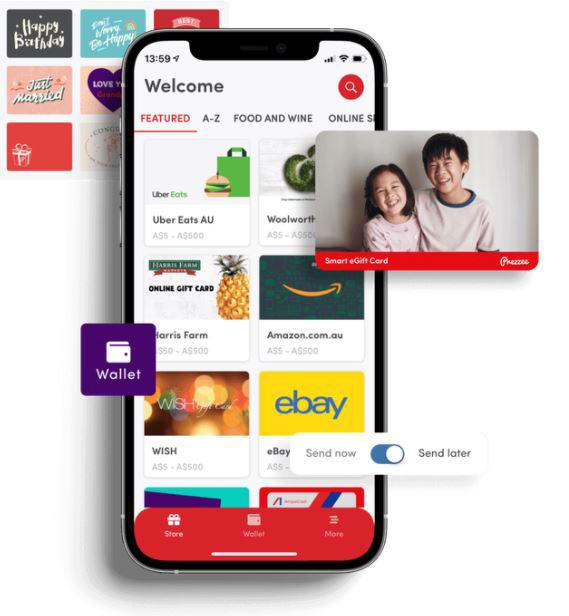
Don’t let mould put your project on hold!
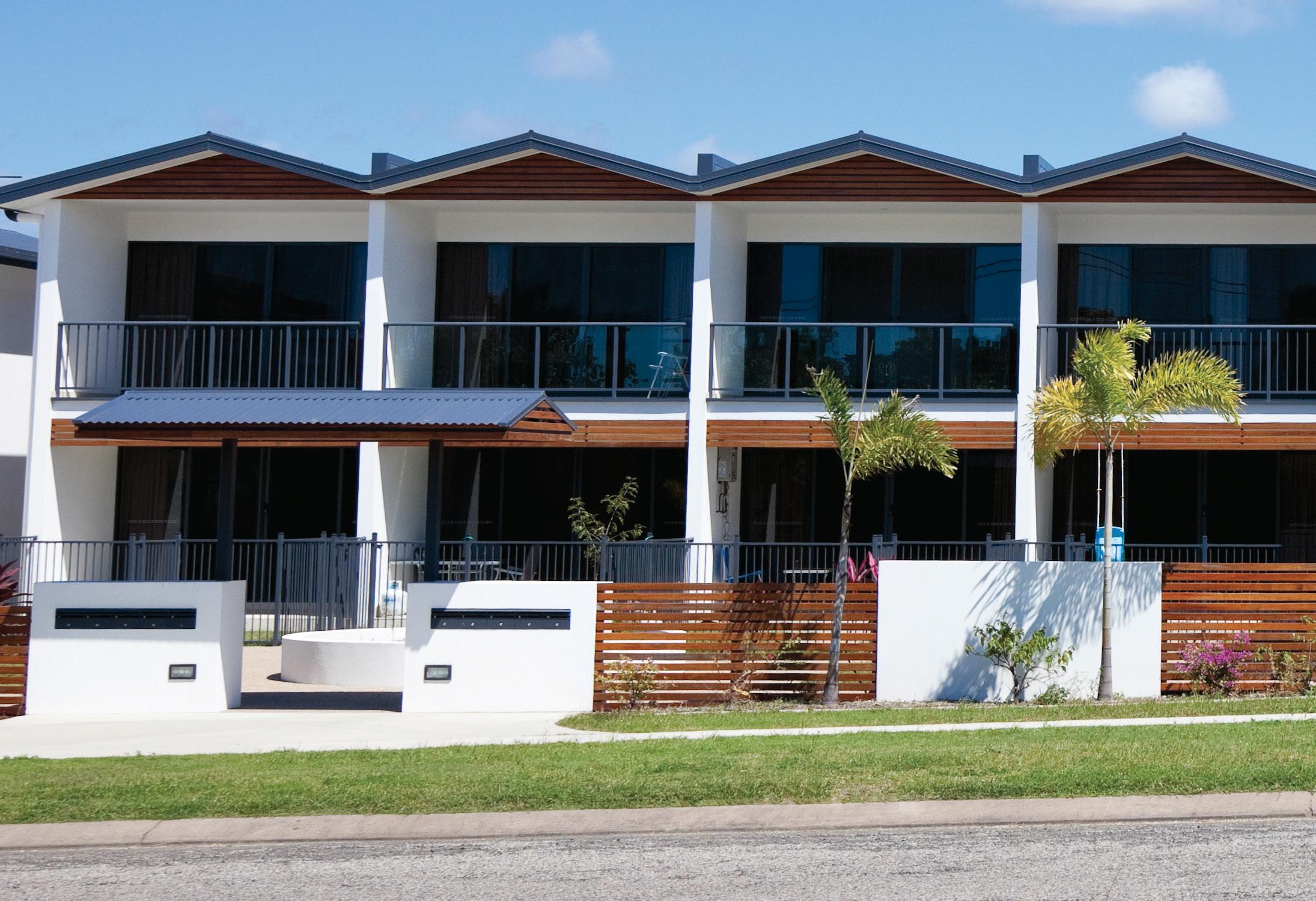
Mould is a serious concern for builders. It results in costly delays while waiting for structures to dry and cleaning the mould further adds to the time and cost. Siniat’s Interhome is a popular separating wall system suitable for duplexes and townhouses, and is well-known for its ease of installation.
Interhome can now offer mould resistance.
By incorporating Siniat’s mould resistant Intershield in the central fire barrier, and mould resistant Multishield in the lamination of the barrier, mould does not have to put your project on hold.
Siniat. Let’s build better together.
siniat.com.au
What the MBA said… March 1990
At the time of writing this, Australians have just seen their seventh consecutive interest rate rise. Our official cash rate is now 2.85 per cent. This has been the most rapid increase in nearly three decades. But spare a thought for those who had a loan back in the late 80s. Throughout that volatile period, interest rates reached a record 17 per cent — an almost inconceivable figure now. In the March 1990 edition of Master Builder Magazine, MBA President Arthur Krust wrote a great column on the effect of high interest rates on housing.
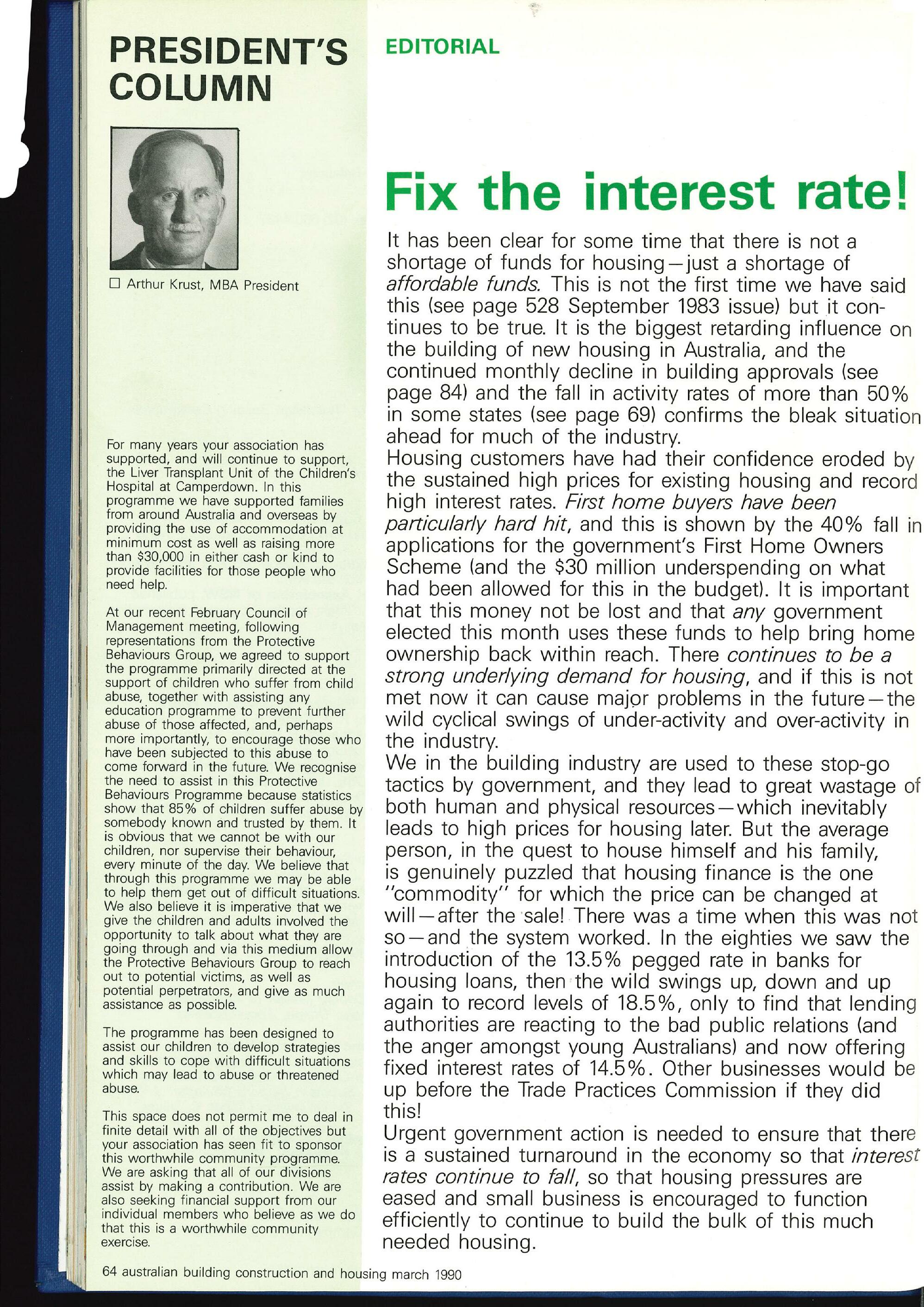