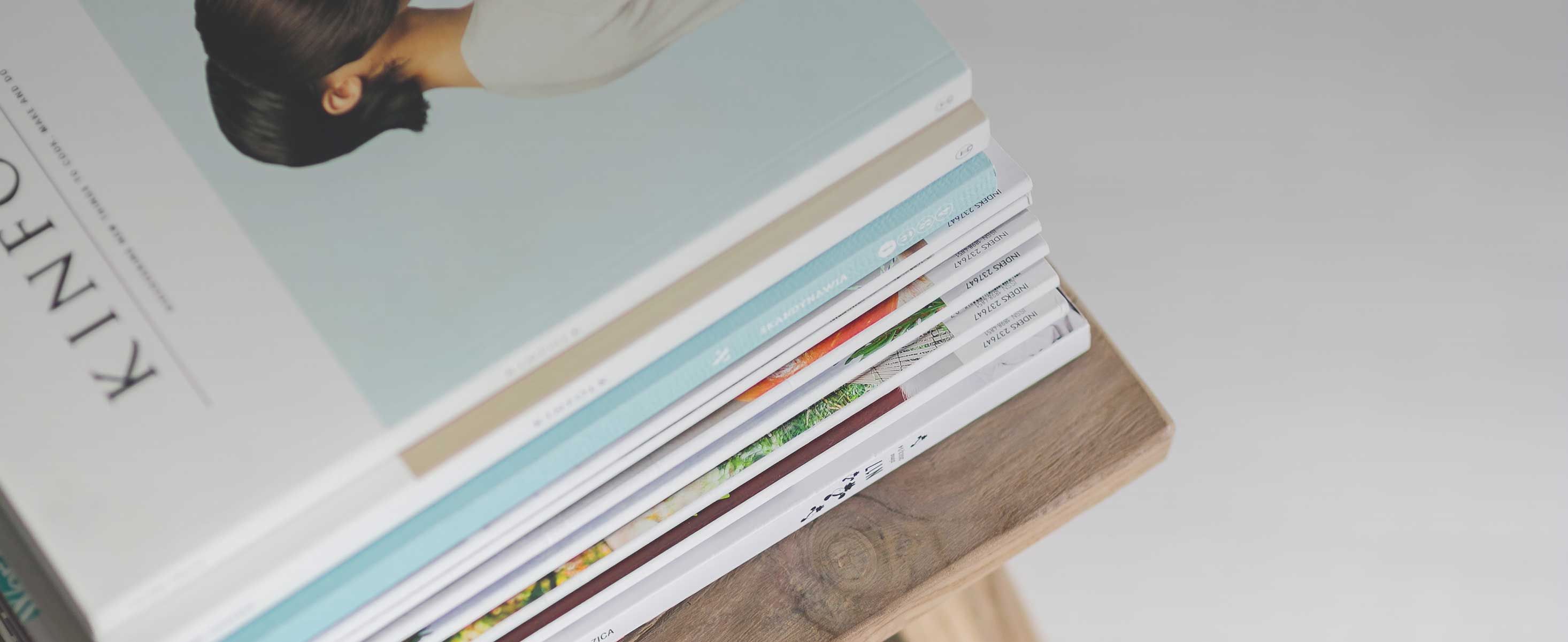
2 minute read
UPgRADing TiTAN
aturnaround (tar) is a planned process of completing maintenance work and safety and reliability upgrades on plant assets. at Methanex trinidad, our 3-year turnaround cycle involves significant forecasting, planning and preparation as we work to improve the reliability and integrity of our two methanol plants.
in the second half of 2013, downstream companies competed for limited resources, local labour and expert competencies, on account of the large number of turnarounds which occurred simultaneously on the Point Lisas industrial Estate, resulting in a historic deployment of manpower and equipment. Midand downstream companies took the opportunity to schedule turnarounds to coincide with upstream maintenance outages by two major gas suppliers owing to limited gas supplies during the period July to October. Collaboration among key stakeholders was key to well-coordinated TARs and the Point Lisas Energy Association ensured communication was a priority.
Advertisement
The planned 30-day turnaround in September on our Titan Plant addressed critical path jobs in the replacement of the Waste heat Boiler (Wh B), structural work on the Cooling Tower, catalyst replacement in the Water Cooled Reactor (WCR) and hydrogenator, and an overhaul of the Titan Flare. Statutory inspections of boilers, vessels and steam drums were also completed.
At a cost of USD 33 million, the scope of this turnaround extended to 36 days, required 390,540 man-hours and projected 1280 individual jobs for execution. Our team of employees and approximately 40 contractor companies, operating under the Titan TAR logo: T.E.A.M (Together Everyone Achieves More) were engaged in delivering on Responsible Care, Quality, Productivity and Budget targets. All departments demonstrated heightened coordination in the months leading up to the turnaround to ensure the timely procurement of materials, equipment and services; development of a comprehensive Responsible Care package which included risk assessments, job hazard analyses, contractor orientation and training; development of communication strategies; and the establishment of a comfortable contractor facility to accommodate a canteen, change-rooms, washrooms, lockers and drug testing facilities.
This turnaround engaged global collaboration from other Methanex sites, including a visit from kevin henderson, Vice President, global Manufacturing and Brad neumann, Director, Responsible Care. Brad observed the implementation of the Responsible Care plan and provided feedback in guiding the team, noting that adjustments are necessary and unique to each turnaround.
Mushtaq Mohammed, Director, Manufacturing, recalled the turnaround challenges and the commitment of personnel to work collaboratively to deliver a safely executed TAR. Michael Wei, Turnaround Lead, also commended the teamwork, adding high praise for the Titan Cooling Tower project which met its targets.
Upon close-out of the turnaround and with no losttime injury, 154 audits were completed and 2600 safety observations were recorded. The lessons learnt will be applied in continuously improving plant reliability.
“In my 27 years of experience in the Oil, Gas and Petrochemical Industries, I’ve never once enjoyed working on Cooling Towers; I’d prefer to work on the Delayed Coker Units! That all changed after observing the Titan Cooling Tower project. I was totally impressed with the team’s attention to detail during the planning phase, the architectural model used to manage execution and the engineering improvements made during this project. This project, to me, should be used as a ‘case study’ on the maintenance of Cooling Towers, a very successful job! Congratulations to the team.”
Luis Lopez, Project Manager, DATSU Unlimited