
11 minute read
What you need to know about formulations Pa

by EndeavorBusinessMedia-VehicleRepairGroup
Brake pad and rotor technology
What you need to know about formulations and legislation to help your customers
By Mike Mavrigian
Today’s brake pad formulations continue to evolve, but the basics include organic, non-asbestos organic (NAO), semi-metallic and ceramic.
Organic pads (even today, some aftermarket pads may still contain a degree of asbestos) contain less than 20% metallic content, so they’re easy on rotors, are relatively quiet and perform best at lower temperatures.
NAO pads are made using so-called organic materials such as f berglass, Kevlar and a host of other materials. Like organic pads, they’re relatively soft and quiet, but the wear rate is low and they create plenty of brake dust. They can include small levels of metals (copper, steel) to help with heat transfer.
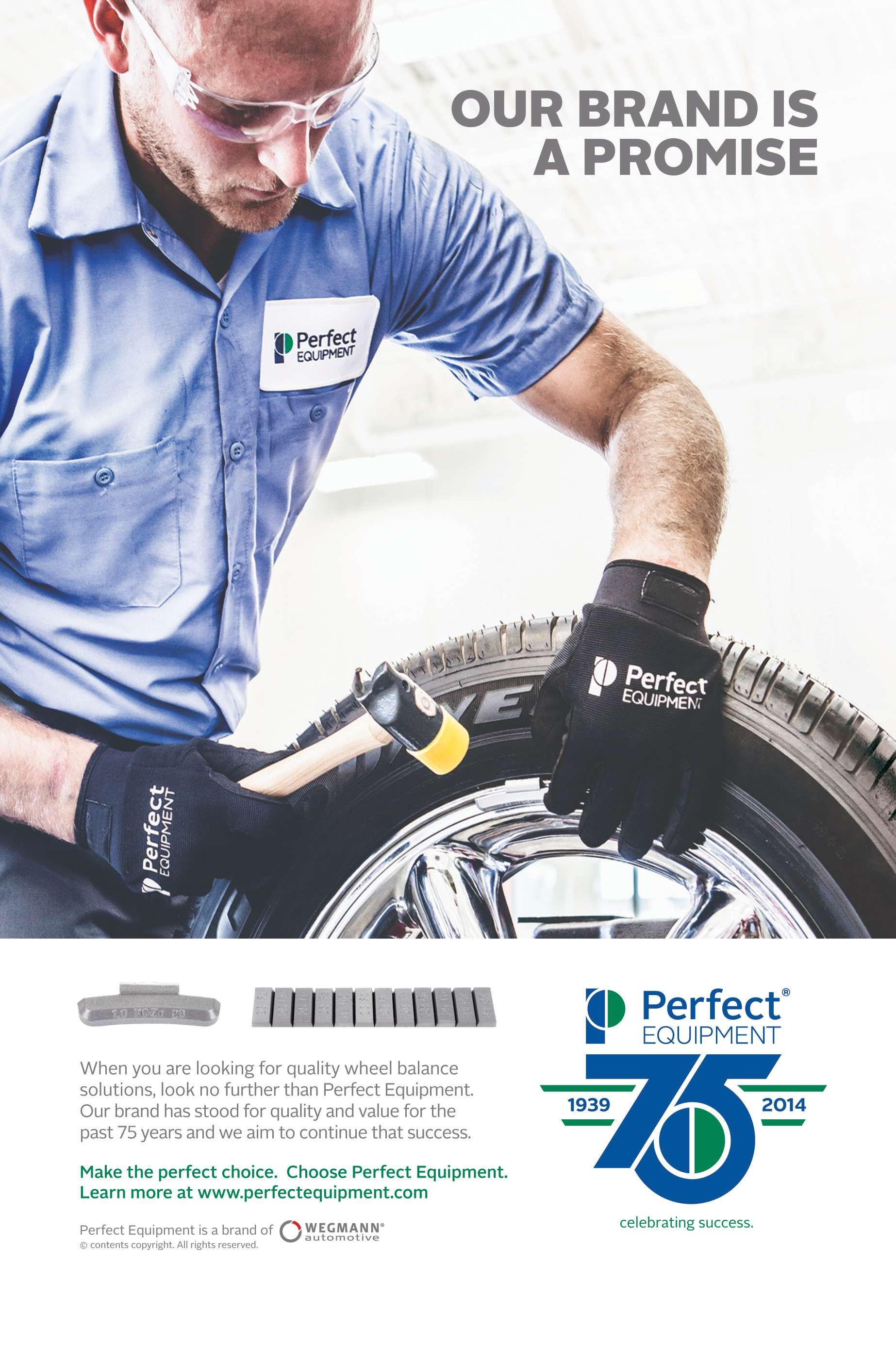
Vented rotor vanes allow heat to escape and are too often ignored. Inspect for any blockage, such as rust scale, dirt, rocks, etc. Isolated vane blockage can lead to disc warping.

Semi-metallic pads contain approximately 30% to 65% metal and are tougher. They last longer and perform better at higher temperatures, but they’re relatively aggressive and can wear rotors faster.
Brake pads that are touted as ceramic are not made of 100% ceramic. Rather, the compound is comprised of ceramic f bers/ powders and manufacturer-specif c binding and f ller materials, often instead of the steel f bers used in semi-metallic pads. The ceramic content (again, this depends on the specif c maker’s pads) is able to handle higher braking temperatures with theoretically less brake fade and faster braking recovery time, and depending on the specif c formulation, may provide reduced braking noise, since the ceramic content tends to dampen noise by generating a noise frequency that’s not discernible by the human ear.
Be aware that not all pads labeled as “ceramic” may actually feature ceramic content. That’s one more reason to always stick with reputable and established brands, and to steer clear of pads of questionable origin.
Ceramic pads, generally speaking, tend to generate less noticeable “brake dust,” due to the lighter color of the friction material compounds. All brake pads will generate dust as they wear, but overall, ceramic pad dust is less noticeable. Many of today’s pads feature a “ceramic-metallic” structure.
A hot topic: copper content
Today, copper content is a hot topic in the brake industry. Copper is traditionally used in brake pad formulas as part of the friction material binding agent, as a highly effective heat transfer material, and is used to help reduce brake pad noise.
The copper content in brake pads (and shoes) has been reduced, due to state and federal mandates. Why? Because of pad dust. All pads release a small amount of dust as they wear. This dust, partially comprised of copper, is released onto the roads, which eventually is washed into the water system (creeks, ponds, lakes, oceans, etc.). Copper is considered a pollutant that can have adverse effects on aquatic vegetation and specif c marine species, such as salmon.
Legislation known as Senate Bill 346 (SB346) dictates that the use of copper in brake pads sold in California must be reduced to no more than 5% by 2021 and further reduced to 0.5% by the year 2025. The state of Washington also passed a similar bill, SB6557, requiring the same reduction, but the deadline for reaching a 0.5% copper content seems to be vague at this time. Both bills were passed in 2010, giving the brake pad industry almost 15 years to meet this goal. Since all states are likely to pass similar legislation at some point, the brake manufacturers have already begun to reduce copper content in their brake pads. The challenge for pad makers is

Always measure disc thickness from the specif ed location. Commonly this will be about 5/16- inch to 3/8-inch inboard from the outer edge. Avoid any un-worn outer lip areas.
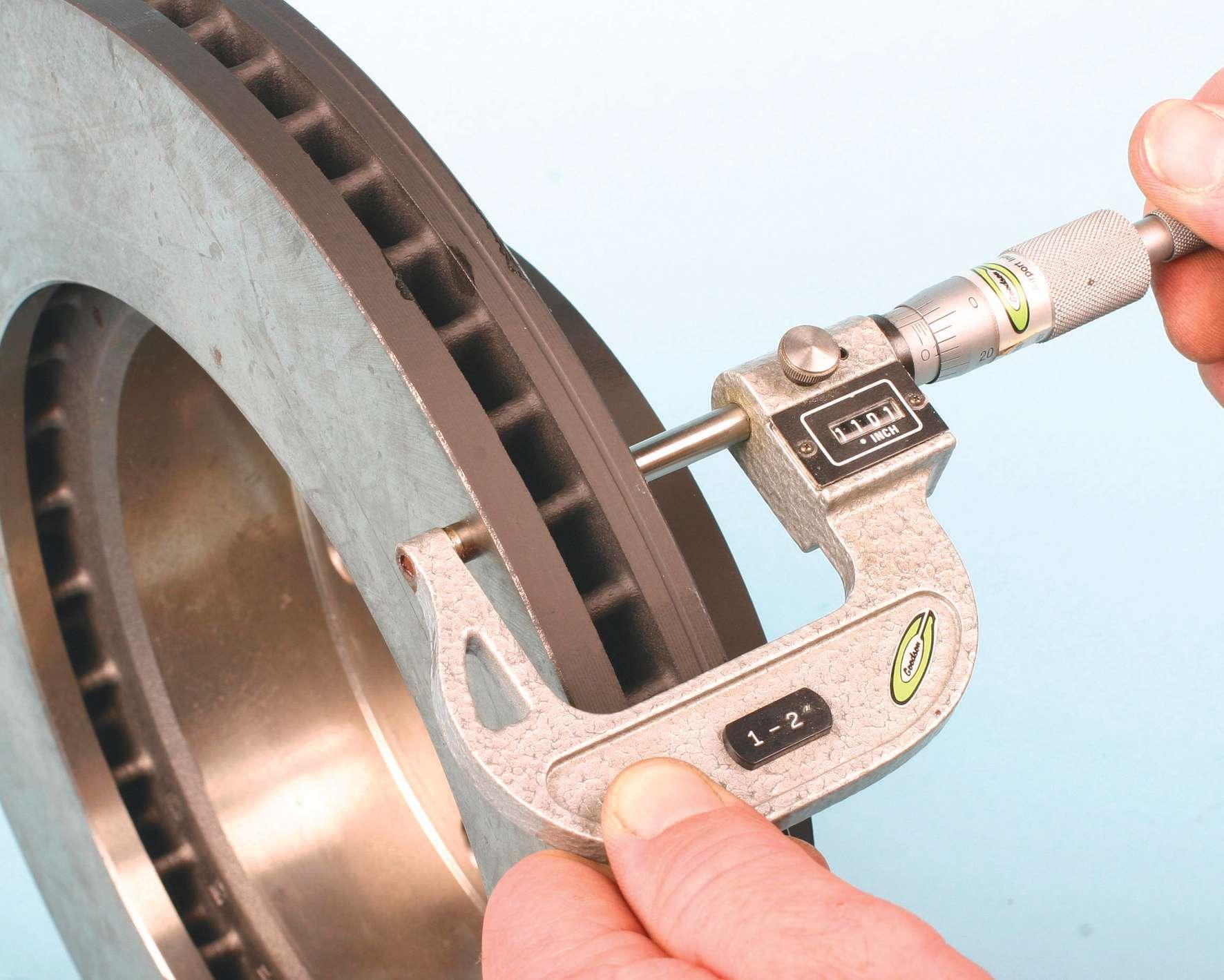
to develop alternatives for copper. Leading pad makers have reportedly already reduced the copper content in their friction material to zero. At this time, the materials being used (and considered) as replacements for copper are tightly held secrets due to the competitive nature of the business.
It’s not as easy as it sounds to simply “replace” copper, which has been a proven mainstay in friction material makeup.
Typically, about a 22% copper content was featured. Unfortunately, there is no direct or easy replacement for copper. A combination of materials must be developed in order to achieve the same performance attributes. Brake pad manufacturers are working diligently to develop formulas to meet the reduced-copper content. Brake pad codes
The edge of a brake pad will feature a list of engineering codes. If you know how to read these codes, you can determine who made them, the composition of the friction material and the pad’s CF (coeff cient of friction) based on SAE standards.
The f rst group of characters indicates the manufacturer. The second group indicates the formulation of the pad composition. The third group indicates the pad’s CF. The CF rating isn’t a guarantee of how the pads will function on a specif c vehicle or application, but will provide a rough idea. Coeff cient of friction (CF) codes: – C.........less than 0.15 – D.........0.15 to 0.25 – E.........0.25 to 0.35 – F.........0.35 to 0.45 – G.........0.45 to 0.55 – H.........over 0.55 – EE.......0.25 to 0.35 at 250 and 600 degrees Fahrenheit. Fade at 600 degrees
F possible.
– EF.......0.25 to 0.35 at 250 degrees F; 0.35 to 0.45 at 600 degrees F. 2% to 44% fade possible at 600 degrees F. – FF.......0.35 to 0.45 at both temps. 0-22% fade possible at 600 degrees F. – GG......0.45 to 0.55 – HH......0.55 to 0.65 carbon/carbon only.
OK up to 3,000 degrees F.
FE pads tend to fade when hot. EF pads may tend to not grab when cold.
Physical pad design
Depending on the vehicle or intended application, pads may feature one or more slots. These slots in the friction material pad help to clean dust out of the rotorto-pad contact area, and provide thermal expansion of the friction material segments, which aid in preventing pad material stress cracking.
Pads may feature chamfers at the leading and exit edges of the pad. This is often used to eliminate or “tune” certain noise frequencies.
Pad bedding/break-in
As the pads mate with the rotor disc surface, and depending on the type of pad formula, a small amount of friction material is transferred to the disc surface, which increases braking eff ciency. If the replacement pads differ from the original pads (in terms of friction material formulation), and are to be used with the original rotors (when changing pads but not the rotors), an initial break-in is recommended.
Drive the vehicle through a few moderate braking exercises in order for the new pads to “wipe” the disc surfaces of the previous embedded friction material. Then continue to drive with moderate braking (at speeds of around 35 to 40 mph) in order to “bed” the new pads to the disc surfaces. However, some brake pad manufacturers note that no bedding-in procedure is necessary with certain pads, so don’t make assumptions. Read the instructions (if provided) that come with the new pads.
Regardless of the type of pad formula, it’s still not a bad idea to perform a few
moderate braking procedures before the need to perform more extreme braking, if for no other reason than to “mate” the pads to the disc surfaces.
A note regarding rotor disc surface preparation is applicable when discussing the installation of any new set of brake pads. The rotor disc surfaces should be clean. That does not mean simply wiping the surfaces down with a rag.
In order to remove residue (dirt and potential oils/grease from used rotors, and packing/shipping rust inhibitors on new rotors), the disc surfaces should be washed and scrubbed thoroughly with a fast-drying solvent, and if time permits, this should be followed up with a hot scrubbing bath with a detergent (Dawn dish washing detergent is a favorite). A hot soapy bath followed by a thorough hot rinse will aid in removing any contaminants that the solvent didn’t remove.
Also, if you do treat the rotors to a hot bath and hot rinse, it’s a good idea to immediately follow this with a cold water rinse (this will reduce the chance of light
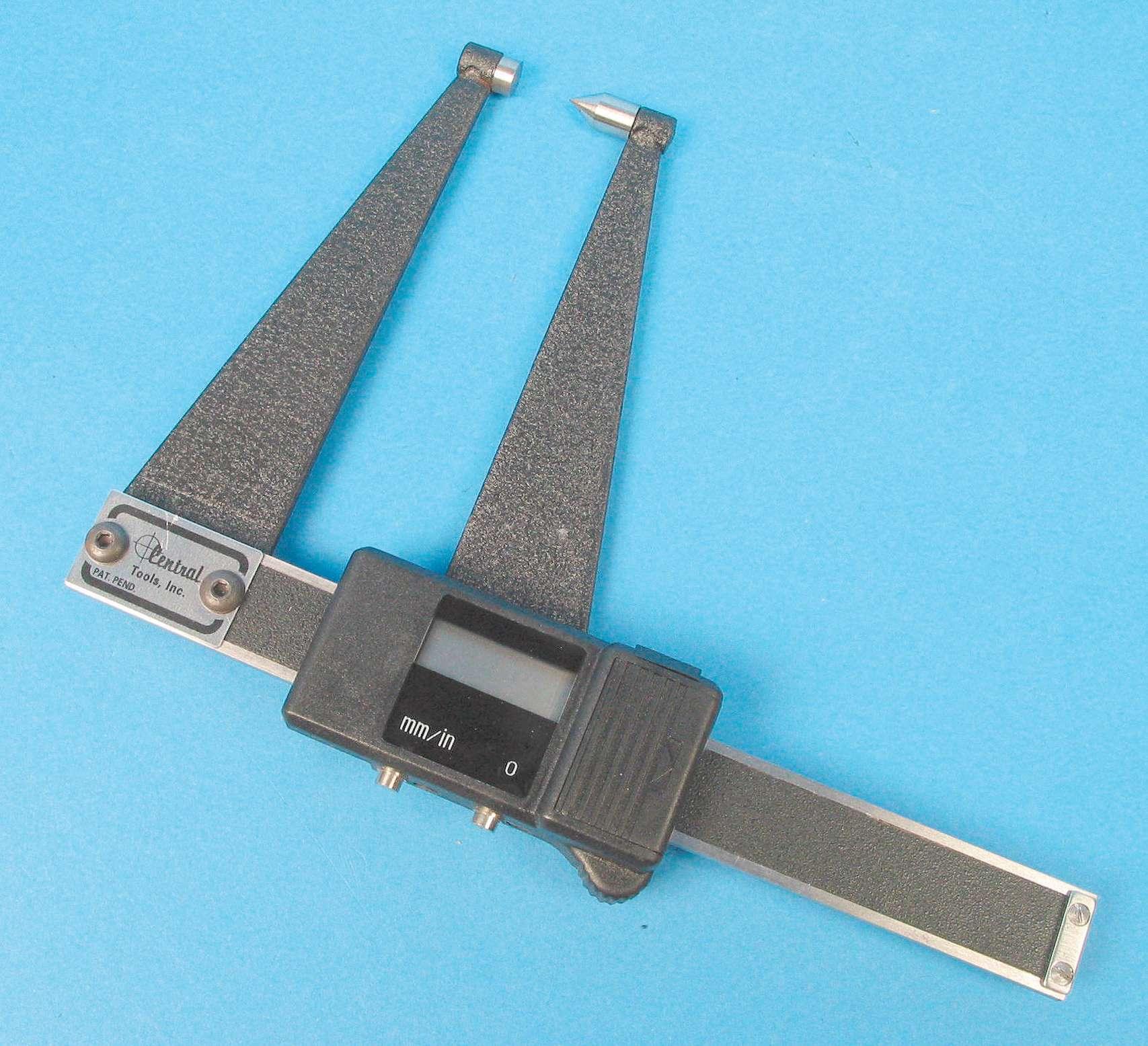
While the use of a generic micrometer with opposing f at anvils will suff ce for disc thickness measurement (as long as great care is used to hold the anvils f at against the disc surface), a dedicated brake disc micrometer is a better choice, as the pointed anvil will allow a slightly more accurate measurement, for more precise contact. surface rusting on the bare metal), followed by blow-drying with compressed air.
Rotor technology
A process referred to as “Ferritic Nitro Carburizing” is gaining in popularity, primarily to reduce or eliminate rotor disc surface rusting, both from a standpoint of appearance and performance. The surface of the rotor is impregnated with nitrogen and carbon, which hardens the surface (increasing the density of the surface with less
To aid in identif cation, the edge of the pad material will feature a code that indicates the manufacturer, the friction material composition and the SAE-rated coeff cient of friction.
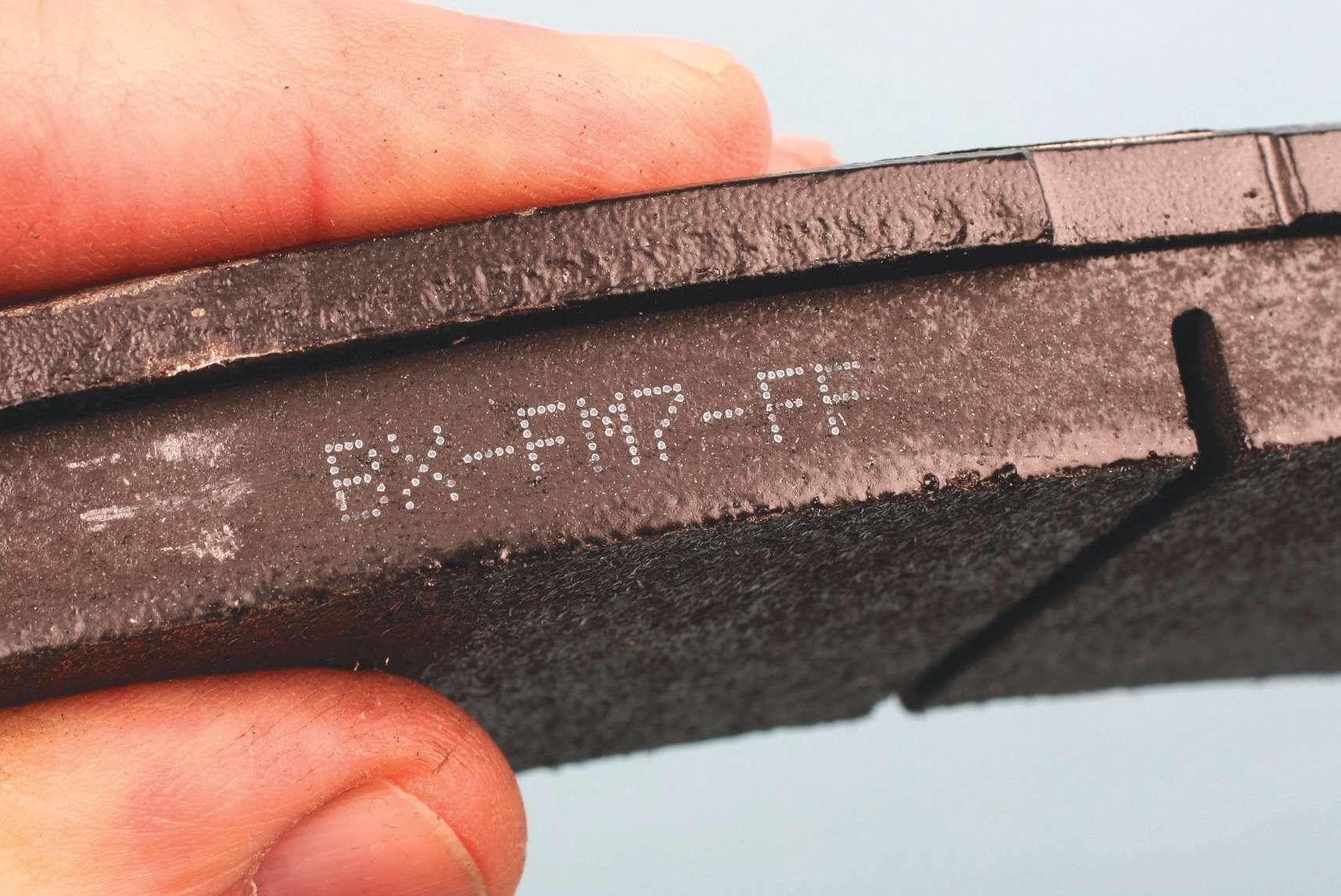
porosity) and prevents surface oxidation/ corrosion. This will appeal to appearanceconscious vehicle owners whose vehicles are equipped with alloy wheels, where the rotors remain visible. From a performance standpoint, the hardened surface provides a more uniform surface for the friction material (partly as a result of reduced or eliminated rust buildup), which offers the benef t of avoiding pad bounce and resulting brake pedal vibration.
In addition to surface hardness treatments for the disc areas, some rotor manufacturers also offer a specialty coating to the rotor hats that prevents or reduces rust buildup on the hat surfaces. This offers both enhanced appearance and more importantly, less chance of electrolysis, reducing the possibility of dissimilar metal bonding (for example, alloy wheels sticking to steel or iron rotor hats). This is what should be an obvious time-saver for technicians during wheel removal. The coating, depending on

the manufacturer, might involve powder coating, Tef on coating, vapor deposition or other non-sticking/rust preventive coating approach (as but one example, Raybestos refers to their rotor hat treatment as a “Black Fusion” coating).
While brake rotor diameters are generally decreasing in size in order to help automakers reduce overall vehicle weight, rotor diameters have, in select vehicle applications, increased over the years, primarily in domestic and import performance cars, trucks and SUVs. Increased surface area of vented rotors results in faster heat transfer, which also relates to the specif c brake pad compound formulation. By increasing disc surface area and increasing heat transfer (removing braking heat at a faster rate), it is possible for the pads to not reach their optimum operating heat range. This is yet another reason to follow brake pad manufacturer recommendations for each application, to ensure that the proper formula of pad is used with specif c type and size of rotors.
Rotor treatments to consider
Cryogenics, in terms of metal treatment, is a tempering process that makes metal stronger by making its molecular makeup more dense and uniform. Cryogenics is a process that involves freezing the component in a bath of liquid nitrogen to (approximately) 300 to 400 degrees below

If a set of pads feature chamfered leading and trailing edges, this is a result of testing and research to reduce unwanted pad harmonics and resulting potential noise.
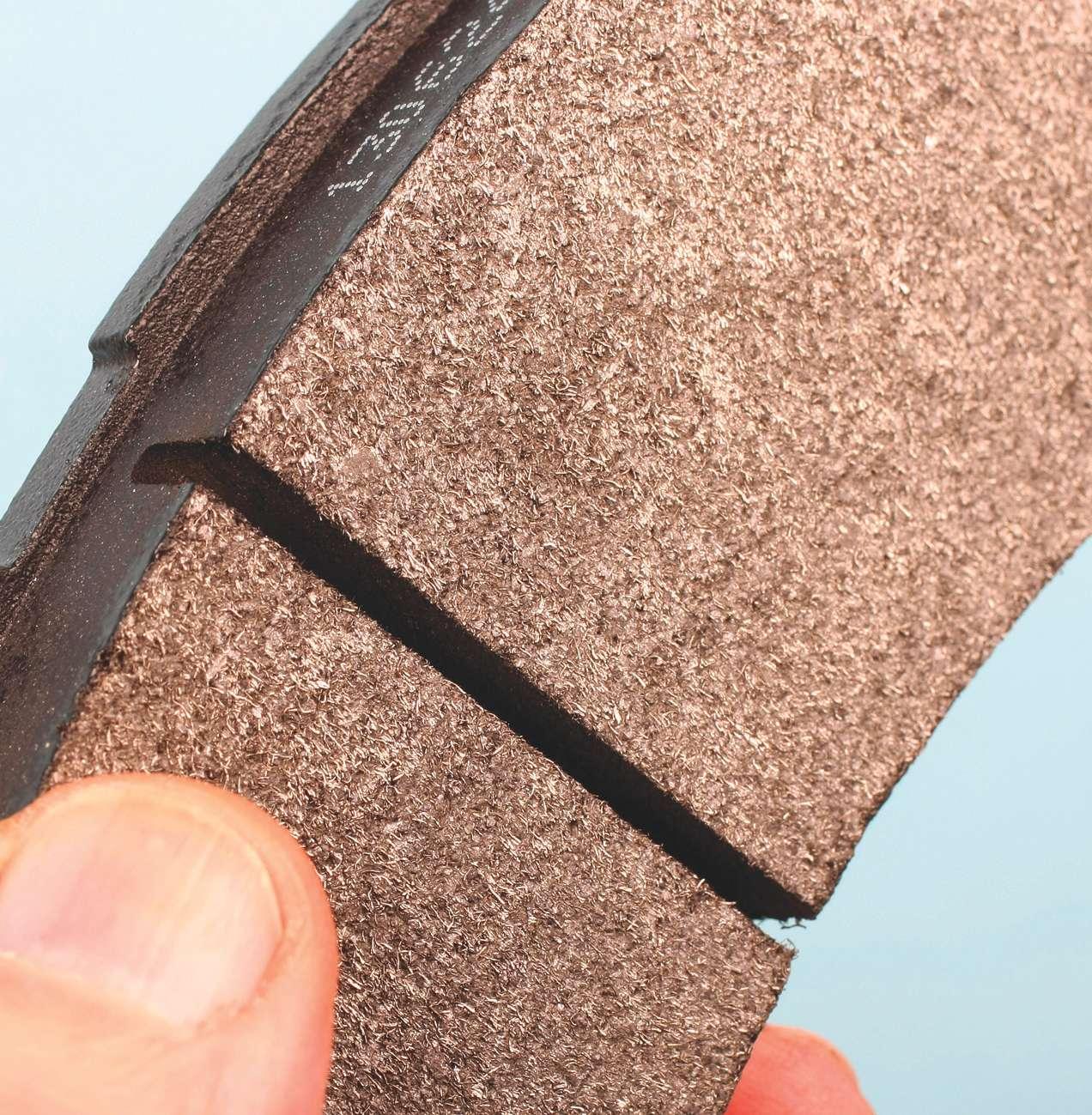
Center slots in the friction material (featured as a result of manufacturer testing and development) are often used to prevent friction material cracking where backing plate def ection is a concern, and to aid in self-cleaning.
F in a controlled manner, and then slowly raising it back to room temperature.
This tempering process changes the “brittle” deposits (called austenites) within the metal to “martensites” which are more uniform. The process results in a metal that is less porous and less prone to warping or cracking. Some manufacturers may employ the use of cryogenics on their rotors. While certainly not a mandatory process for the average brake customer, this process is readily available to treat rotors if the customer so desires. A number of cryo shops throughout the U.S. offer this service. While racers commonly take advantage of cryo treatment for their rotors, this is a service to consider as an add-on upgrade for severe-duty f eet customers as well (police vehicles and other emergency vehicles).
Another process that will achieve the same result (of making the molecular structure stronger and less prone to cracking or warping) is known as vibratory stress relief. This process uses computer-controlled frequencies (vibrations) to remove internal stresses and to increase metallurgical uniformity/stability. Both processes have been used for severe-duty engine, driveline and braking components with great success. ●
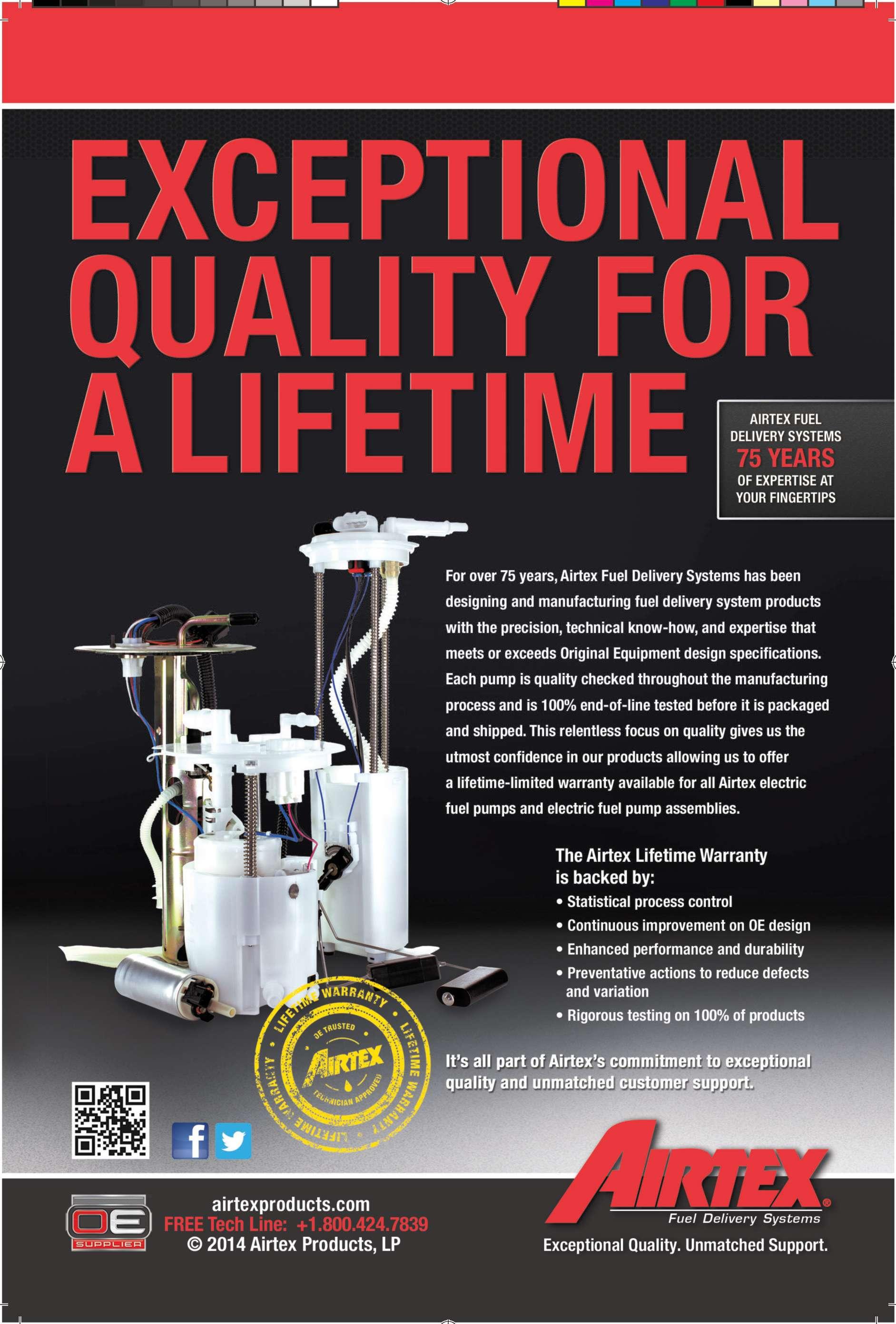