
16 minute read
Stopping customer complaints with

from Auto Service Professional - August 2017
by EndeavorBusinessMedia-VehicleRepairGroup
Avoiding brake job comebacks
Stopping customer complaints with attention to detail
Don’t let this happen to you! You performed a brake job on a vehicle a month ago, and it’s back in your shop with a noise or vibration complaint. Performing a brake job in a busy shop can sometimes lead to overlooking details that can easily result in a comeback. In this article, we discuss areas of concern to avoid customer complaints, including diagnosing and checking wheel bearing condition, rotor lateral runout, stacked runout, surface preparation and more.
By Jeff Taylor
There is no worse feeling for a tech than to have performed a straightforward, uncomplicated brake job and see the vehicle return with a concern or a complaint. The customer can raise his concerns immediately after the repair or in the weeks or months following.
Brake comebacks are common and the range of complaints is huge: dusty wheels, the brakes not working like the originals, etc. The list is long. But I find the most common complaints are brake noises and brake vibrations.
There are many conditions that can cause these comeback situations, including cheap replacement parts, abuse by the customer and manufacturing issues, but several can be created by the tech performing the work.
In my tenure as a tech, I have found that brake job complaints were habitually my number one comeback, but I now take a few more steps in my inspection and repair procedures to ensure that this return number is low and typically caused by a situation that I as a tech could not control.
Brake noises
Sound is created when something vibrates, and these vibrations are transmitted through the air, or another medium (the vehicle’s caliper bracket and spindle assembly, for example) and this vibration is detected by our ears.
Sound is something that we want to hear, noise is something that we don’t want to hear. Either way they are both created by something vibrating.
When a customer applies the brakes and the calipers clamp the pads onto the rotor, or the shoes contact the drums to slow down the vehicle, they are creating the perfect circumstances to create a lot of vibrations that shouldn’t be heard, but if it is, its unwanted NOISE!
All brakes make some form of noise. It happens when the friction material is forced onto the drum or rotor. This friction creates vibrations; not just of the pads or shoes, but the entire brake system. The original equipment (OE) manufacturers and aftermarket parts manufacturers go to great lengths to keep the braking system of our cars
inspection
Any time a customer has a brake issue or a brake concern, a comprehensive visual and hands-on inspection of the base brake system and its components should be the first step, long before any parts are replaced. If simple things are missed at this stage, the result could easily be a comeback.
Looking closely at the wear of the brake materials can be an indication of a sticky caliper, binding/bent caliper pin, binding pads or even a restricted flexible brake
hardware, parking brake cables and all the other crucial parts need a thorough visual examination. For hands-on inspections, I carefully push back the caliper piston to ensure that the caliper and its mounting hardware are all free and able to move properly. If they don’t move they may need some disassembly to properly diagnose what parts are going to be needed to complete a painless brake service. I also make sure that the parking brake cables and their application mechanisms move freely and fully release properly. Corrosion can greatly affect the splash/ backing plates that are designed to prevent road grime from contacting the rotor. But Don’t always assume that the noise the customer that’s not all these backing plates do; in is complaining about just after a brake job is many cases they hold parking brake shoes, something you have done; in this case the whirring noise complaint was a bad hanger bearing. hardware, support ABS parts and provide directional air flow for brake cooling. The and trucks as quiet as possible. The use of visual inspection should include a close look special shims, abutment pads, retainer clips, at these parts as their replacement may be adhesives, friction material components and required to prevent a rubbing or grinding other methods are commonly used to absorb noise complaint or as serious a problem as the vibrations that the brake parts create, or premature brake fade due to inadequate change the noise generated to a level that we cooling. humans can’t hear. Any tech who is working in the Rust Belt The initial brake winter will understand what I’m talking about
where road-clearing agents are used in the hose. The condition of the This backing plate is a noise waiting to happen after new rotor is rotors, backing plates, dust installed. It was replaced to prevent any noises and to protect the shields, brake drums, shoes, rotor from water, snow and road debris.

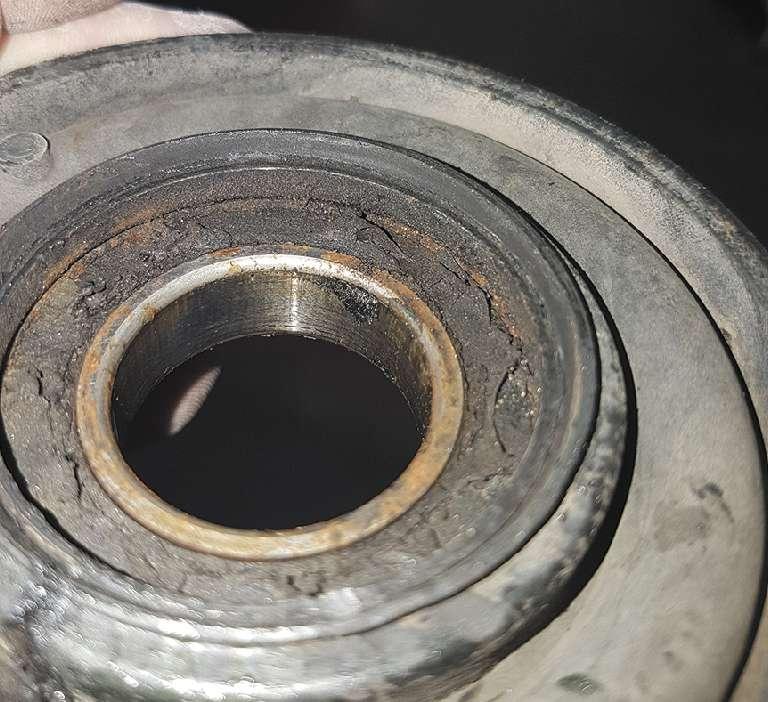
when I say that checking for corroded backing plates is essential.
Many times, I have seen a backing plate that is intact and not causing any concerns, but the corrosion growing under its attaching point, (spindle/ hub) forces it outward on to the rotor surface. Over the life of the brake system the moving parts slowly clear away the rust Abutment pad clips must be installed on a clean surface that’s and excess metal as it builds free of debris and rust, and properly attached so that no small up, but once a new rotor is pieces rub against the rotor, causing a noise. installed those clearances are changed and rubbing noises pad retainers, brake pad shims, anti-rattle often result. clips, the caliper bushings (these bushing
I pay attention to backing plates on a typically last for two sets of pads) and in the number of vehicles; Honda CRVs, GMC/ drum system all the springs and hold down Chevy pickups and VW Beetles (there are hardware. many others) and either recommend backing The reason is simple. The wear may not be plate/splash shield replacement during a brake visible but these parts wear out. This is one repair or warn of the noise issue they may reason many superior quality brake pad sets create if not replaced. now include new abutment pads. Remember, these parts all started out new together and Starting the brake job wore out together.
Pay attention to the simple things from the All the rust, scale, corrosion and road grime calipers to parts inside the drums that can should be removed and the proper brake cause noise and vibration trouble. lubricant (not lithium grease) installed on the
Simple procedures can often be overlooked parts that require lubrication. A brake pad and it can start when the caliper is removed that is binding/seized due to rust or corrosion and allowed to hang by the brake hose. The or flopping around because of worn out abutflex hose was never designed to hold the ments or abutment pads will cause noise. weight of the caliper and a simple wire hook A leading cause of brake comeback noises, or bungee strap should be used to support it. according to a local GM dealership, is either The internal parts of the hose can be damaged improper installation of caliper/pad hardif the weight of the caliper is applied to it and ware or corrosion on or under the attaching this injury may not show up right away, but hardware parts. ACDelco specifically notes the damage may result in a restriction causing that you should never “grind the ears of the a pull or dragging caliper or worse, a brake pad to get them to fit.” fluid leak. It is vitally important to make sure that
Both the OE and aftermarket brake parts the caliper hardware and their brackets are manufacturers will tell you that many of the restored to like-new condition to prevent parts and pieces of the brake system should future issues and comebacks. be replaced when preforming a brake job, not The importance of new quality brake shims just the pads or shoes, to ensure a troubleand their proper installation is also critical free brake job (many companies even show to attaining a noise-free brake job. The shims illustrations on their brake pad packaging that contact the back of the brake pads are indicating what should be changed). And anything but a simple piece of steel to quiet this normally includes the abutment pads, the pads’ vibration. These are very specialized
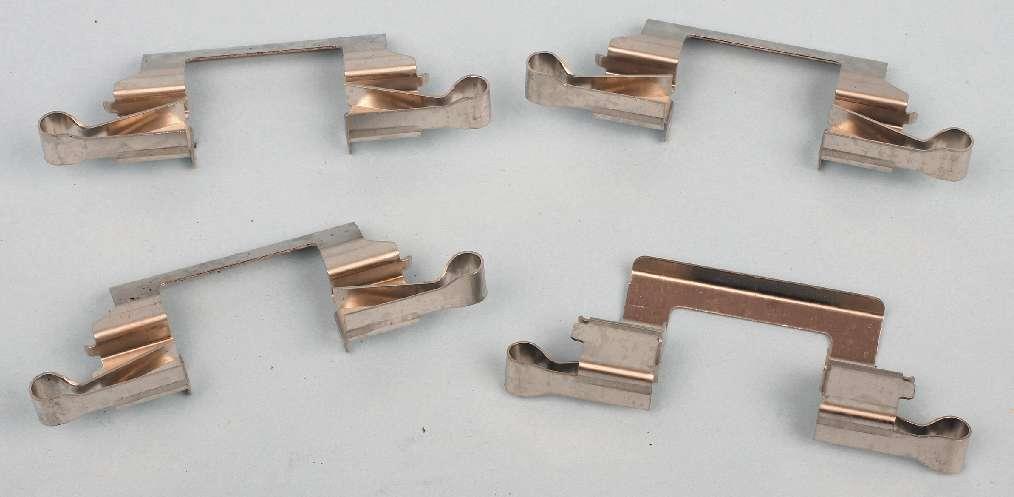

Brake shims should never be reused. Always replace with a small amount of brake lube at the caliper bracket and piston contact points. The corrosion is evident on these examples.
and highly engineered components of multi-layered steel, elastomeric rubbers and other compounds that are bonded together and then bent into the proper shape. The engineers will fine-tune the layers and shape to give the shim the best vibrational damping characteristics for the particular vehicle and braking system. If the shim doesn’t properly contact the back of the brake pad it will not be able to do its job correctly, and may actually create more noise than it absorbs.
If the shims aren’t already attached to the brake pad, you can test their effectiveness by dropping them on a firm surface. They should just make a solid thunk, and not bounce all around. If they bounce around and make a tinny clinking noise, they likely won’t be able to adequately reduce any noise-creating vibrations. This is a common scenario in low price point pad kits and hardware.
Most superior quality brake pads will already have a quality shim installed on the pad when you open the box. There are several reasons for this. The factory is cleaner than most shops and dirt free for proper installation. They can be riveted or peened in the proper position or the adhesive backing can be thermally activated under pressure to ensure the shim stays in place and functions as designed. Inferior quality factory shims have been known to move off the brake pad,

Some pads come with new shims that must be attached. These have an adhesive back and need to be attached to clean, dry brake backing plates. Many manufacturers already mount these shims to prevent installation issues.
create noise and in some cases cut into the brake rotor, something none of us wants to happen.
Before installing the brake pads, a small amount of the proper brake lubricant should be used to add an extra layer of vibration isolation between the pad and the caliper or bracket. If the pads come with two-piece shims, a small amount can be used in between them, but the lubricant must be used sparingly, not in huge blobs that could contaminate the brake material.
Excessive lubricant will melt off and be wasted or attract debris and brake dust and cause other issues and possibly noises. Proper lubing of drum brakes again calls for a dab on the shoes’ contact area on the backing plates and the star adjuster of the self-adjusting mechanism.

A specific, dedicated silicone brake lubricant must be used, not lithium grease, and it should be used sparingly so it doesn’t melt off and contaminate the new brake material.
Proper torquing of not just the wheels but all the parts and pieces of the brake system on reassembly is important. Many parts need to be tight but not just impact gun tight.
The proper torquing of caliper brackets is
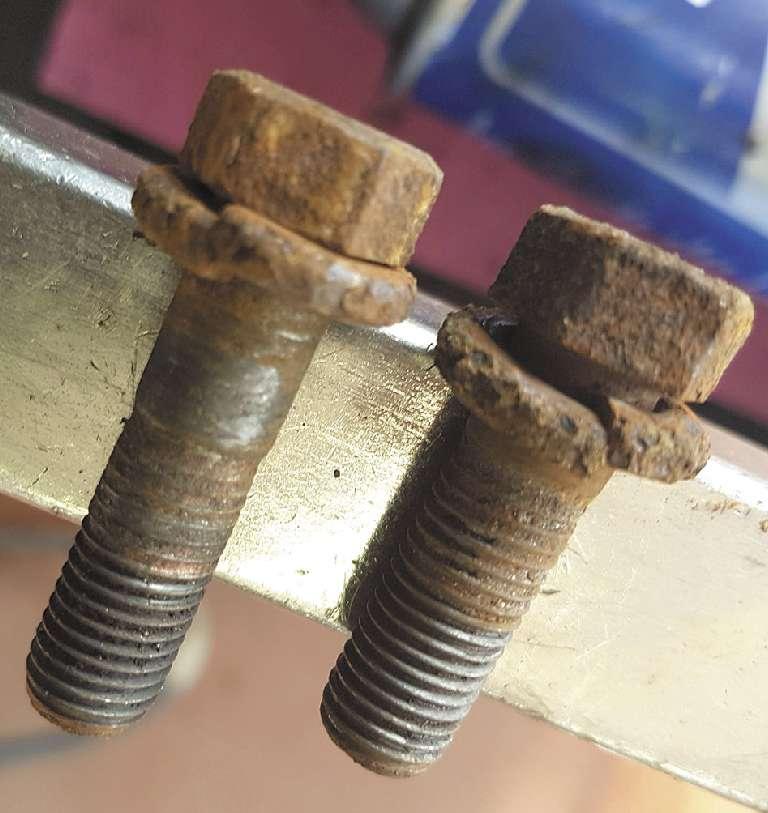
The length and location of the caliper abutment bolts must be noted. Kia, Hyundai and Nissan may use a longer length bolt to attach a support to the caliper abutment bracket on the axle. If the wrong bolt is installed brake rotor failure may result. essential yet not something many of us do. Take the time to look up the specs. You will be surprised how tight many need to be to prevent noises. Citing just two examples, 2014 F-150 caliper bracket torque is 184 ft.-lbs. 2010 Cadillac STS caliper bracket bolts need fresh Loctite and require 96 ft.-lbs.
Rotors/drums as the cause of the noise, vibration or pedal pulsation
If you are machining a rotor or drum, a poor finish can easily create a noise. The rotor’s machined surface finish should be non-directional and of the proper smoothness to allow the pad material transfer that creates the correct coefficient of friction. Improper machining can result in a record player effect on both drums and rotors that results in a slapstick banging noise as the shoes or pads are pulled away and released, so attention must be paid to bit condition, machining speeds and the final machined finish.
When you’re finished machining rotors or drums, they should be washed with hot soapy water (as opposed to brake clean solvents which tend to dry too fast) in order to remove any metal fragments left over from the

On most passenger car applications, rotor lateral runout should be less than 0.002 inch, preferably less than 0.00197 inch. Lug nuts/wheel fasteners must be torqued to specification. machining process. These small particles can impede the pads/shoes bedding process and cause noise or affect the brake pedal feel and stopping distance.
Before the rotor is installed onto the hub flange it should be cleaned to ensure there is no rust or corrosion present that could affect the runout of the assembly. And before the caliper is reinstalled the rotor and hub assemblies’ runout should be checked.
To measure rotor runout: attach the rotor to the flange with all required and properly torqued wheel nuts. Then, using a dial indicator, measure the runout 1/2-inch from the rotor’s edge, by slowly turning the rotor. When performing this test, mark the high and low spots on the rotor and index the rotor location on the flange with a Sharpie. Most passenger car applications will show less than 0.002 inch. If the reading is more than 0.002 inch, remove the rotor and rotate it 180 degrees on the flange and re-measure. If it’s now in spec, you’re all set. If it’s still out of spec the root cause has to be found or a comeback could result. Excessive runout that is greater than 0.006 inch is an indication that either the hub flange, rotor flange or wheel bearing assemble may need replacement.
Why is this measurement so important? Excessive runout could lead to uneven brake pad material transfer to the rotor. Brake pad material transfer to the rotor and drum is essential for proper brake function and feel but unevenly deposited materials affect the coefficient of friction and can create a pedal pulsation. As little as 0.003 inch of runout can easily result in a vibration/pulsating pedal comeback within 5,000 miles or less due to this uneven pad transfer.
On some particularly troublesome rotor vibration comebacks, if the runout is in spec, I recommend measuring the rotor thickness variation (RTV) in six separate locations. The spec for this measurement is typically less than 0.001 inch and in many cases is zero. This procedure is time consuming, but excessive RTV or a combination of runout and RTV together can cause pedal pulsation due to uneven pad material transfer.
The use of ceramic brake materials has made runout and RTV issues much more common due to its pad transfer characteristics. Simply installing new rotors may temporarily fix or hide the issue until the pad material is unevenly deposited again.
Wheel bearings need to be properly torqued to prevent excessive runout and so does the wheel itself. Unevenly or over-torqued wheels can cause rotor distortion and these uneven deposits can result.
In a situation where you find a lateral runout condition (where a stack-up of tolerance between the rotor and hub exists), you may be able to easily correct this without replacing parts by using a tapered correction shim between the rotor and hub. These shims are available to correct problems from initial runout of 0.003 inch to 0.006 inch.
Stopping performance
After all the cleaning, measuring, proper lubing and installing new pads and hardware, a proper road test is the final step needed to ensure a noise and vibration-free brake job that offers the proper “feel.” The pads and shoes need to be properly broken in or burnished to allow the resins in the brake material to set properly. Hard or panic stops should be avoided during this period to avoid glazing the pads by overheating the resins
When measuring for rotor thickness variation, measure at a minimum of six equally spaced locations around the rotor disc. When installing new pads, complaints often arise due to poor rotor conditions. The thickness of the rotor, called DTV (disc thickness variation) needs to be checked.
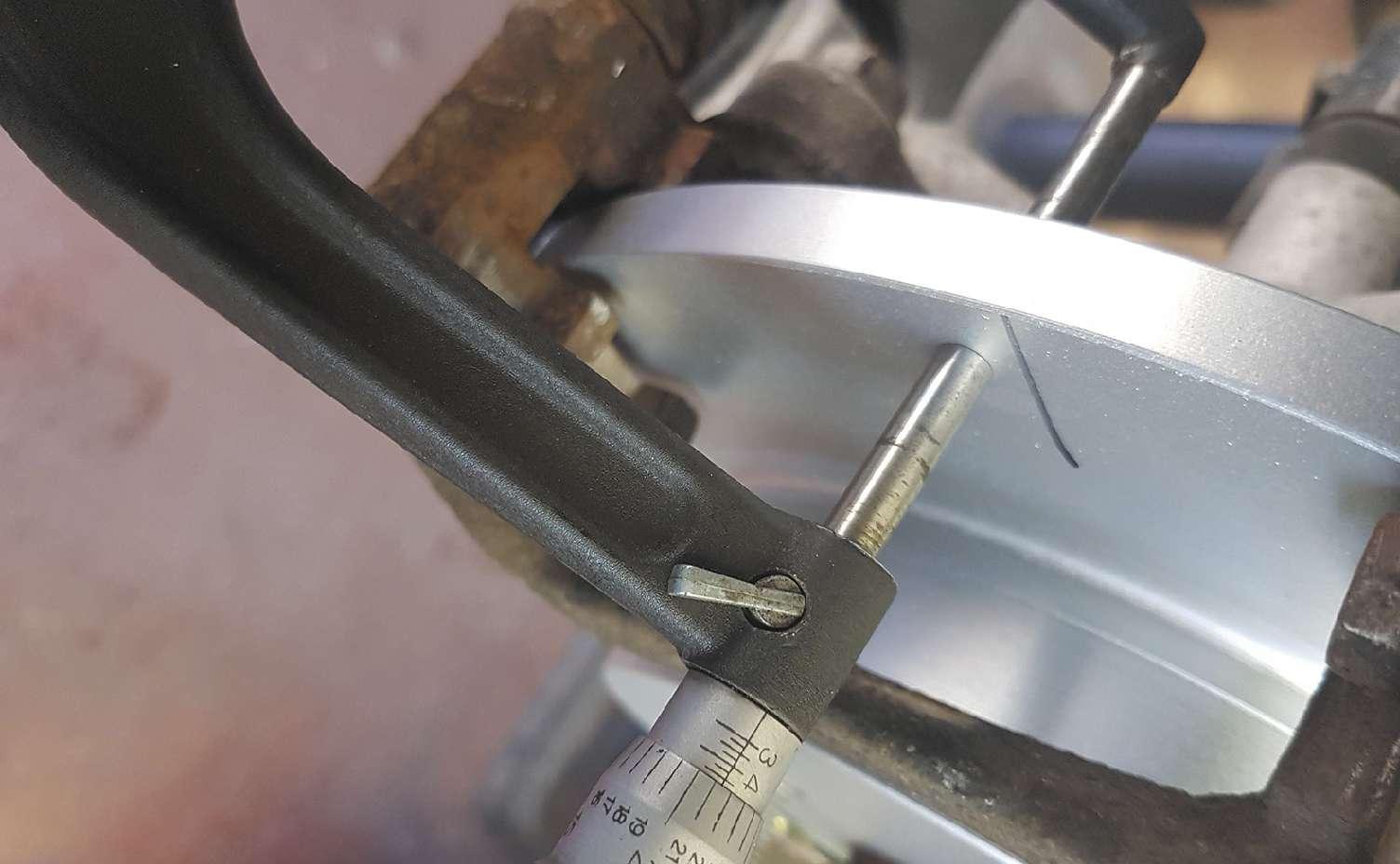
and forcing them to the surface. The typical procedure involves 30 smooth stops from 30 mph, with 30 seconds in-between for the parts to cool. Nice smooth stops will bed the new pads and shoes to the rotors and drums and transfer the needed friction material to provide optimal brake performance, from the first time the customer picks up the vehicle. Don’t rely on the customer to perform this break-in.
Bringing this to a quiet, vibration-free stop
It is easy to blame the pads or the rotors when you have a comeback due to noise or vibration. But when a car owner returns complaining that the brakes are squeaking or vibrating since they had their brakes done, we must drop everything to fix the issue.
“Brake job comebacks are easily avoidable when technicians keep a few best practices in mind. Proper cleaning techniques, correct installation procedures and, most importantly, choosing quality parts,” said Josh Shuck, ACDelco brake product specialist. “Installing poor quality brakes, pads and rotors is a common reason customers return. Customer returns can be significantly reduced by being selective of the products, such as choosing true OEM parts, which ensure quality, durability and exact fit.”
Most comebacks can be averted before they even start, with careful attention to details: from the initial visual inspection, the proper repair and replacement of parts, to the final proper road test.
I would like to thank ACDelco , Nick Viverios of Brake Parts Inc and Marc Stahl of Leggatt Auto Group for their help and contributions.
Jeff Taylor boasts a 32-year career in the automotive industry with Eccles Auto Service in Dundas, Ontario, as a fully licensed professional lead technician. While continuing to be “on the bench” every day, Jeff is also heavily involved in government focus groups, serves as an accomplished technical writer and has competed in international diagnostic competitions as well as providing his expertise as an automotive technical instructor for a major aftermarket parts retailer.