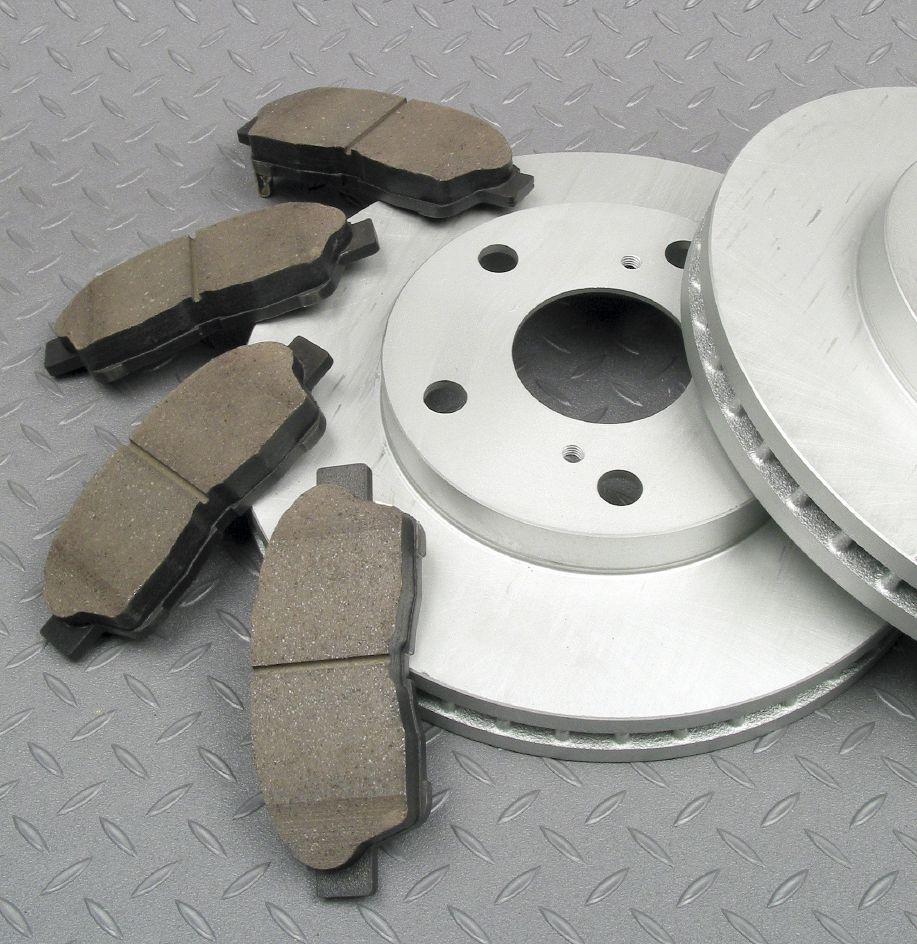
18 minute read
Technical

from Auto Service Professional - October 2019
by EndeavorBusinessMedia-VehicleRepairGroup
The computer module gathers this information to determine the remaining pad life.
Once pads and sensor have been replaced, the brake life service indicator on the dash will need to be reset. Depending on make, model and year, this may be done on the dashboard or with the use of a scan tool.
Electronic wear sensors, in addition to pad friction material, are wear-related items. The sensors should be replaced every time the pads are changed, even if the sensor visually looks OK. Regardless of outward appearance, the wire harness and the sensor may have experienced severe thermal cycle duty and can be prone to failure. The sensors are relatively in-
expensive items and should always be replaced whenever the pads are serviced.
The future of brake pads We asked a number of experts if there have been any recent/impending advancements in brake pad friction material and/or design. Here are some comments.
Centric Parts The following comments were provided by Steve Ruiz, Centric’s vice president of engineering.
First, we look at what the OEMs are doing, as we concentrate on meeting application-specific requirements. As far as brake pads are concerned,
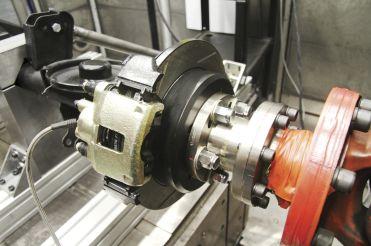
COURTESY OF CENTRIC PARTS
Dyno testing gathers frictional and thermal data during pad and rotor development.


Examples of pad chamfers. Leading and trailing edge chamfers are featured where required to reduce noise.
COURTESY OF CENTRIC PARTS
COURTESY OF CENTRIC PARTS
Brake pad and rotor interface testing is performed at a variety of operating temperature and pressure, in part to evaluate pad compounds and resins.
we toggle between ceramic and semi-metallic, depending on the application, but the trend is moving to ceramics. Semi-metallics are better suited to heavy-duty applications, but for passenger vehicles, we primarily prefer to use ceramics due to superior noise reduction and good release characteristics. We’re always looking for ways to lower braking noise. Shims are an integral part of noise management, usually involving steel/rubber shims that are clipped onto the backing plate or retained with the use of adhesives combined with mechanical retention.
Example of Centric GCX rotors, which feature a Geomet RS200 anti-corrosion coating involving a zinc and aluminum-rich resin to all non-friction surfaces of the rotor.

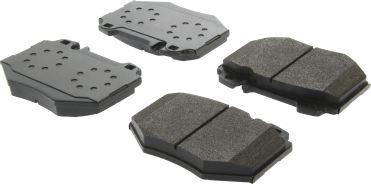
Examples of PosiQuiet pads. Pad-to-backingplate retention is critical to establish a permanent bond between the two materials. A positive-molding approach is used that features a series of holes in the backing plate. During the pad molding process, pressurization forms pad material into these holes, essentially making the pad material an integral part of the backing plate.
Semi-metallic pads have different characteristics in terms of how they react to the rotor. Obtaining a transfer layer is a key element, as a layer of pad material transfers to the rotor for superior braking. Ceramic pads do a better job of establishing this vital transfer layer. Currently, ceramics tend to dominate the industry. They offer good stopping power, are more quiet, offer good release, better pad life and better rotor life. As most technicians are aware, the industry is working to eliminate the use of copper in friction material. In order to maintain good
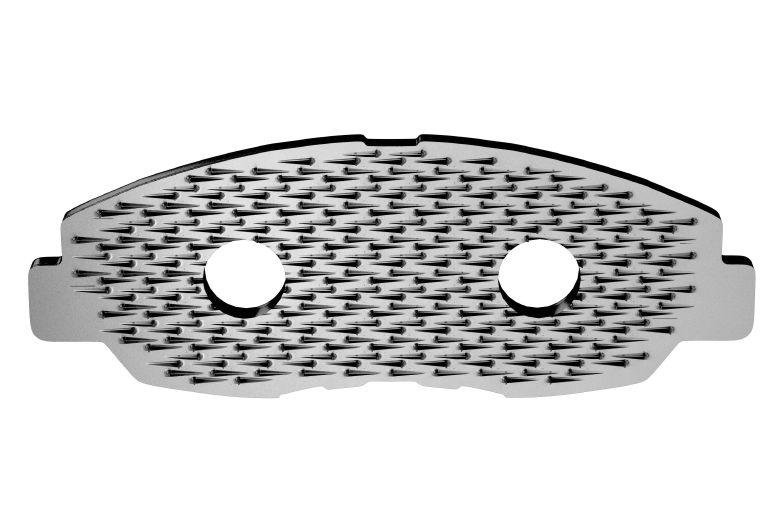
A series of tooth barbs provide a secure friction material to the backing plate anchor.
heat transfer, developing proprietary pad formulations is an ongoing process.
An example is our New 500 pad material which features an added layer on the friction material, with no need to perform a “break-in.” Our PQ Pro also features an added layer and is designed for emergency vehicles such as police and tactical vehicles. This makes the pads ready to use in abusive/emergency situations without the need to perform a break-in procedure. Pad friction surfaces are “scorched” to a depth of about 2 mm, which “ages” the initial surface for superior and immediate layer transfer.
Pad-to-backing-plate retention is critical to establish a permanent bond between the two materials. We favor utilizing a positive-molding approach that features a series of holes in the backing plate. During the pad molding process, pressurization forms pad material into these holes, essentially making the pad material an integral part of the backing plate. This positivemolding process is an OEM-favored approach.
We don’t buy into the notion of reducing rotor weight. We want to retain the OEM design. With that said, depending on the application, we may upgrade the iron that we use, with enhanced tensile strength and low hardness for crack resistance (hardness to tensile ratio). As part of our ongoing development, we continue to mature this ratio, to surpass the OE hardness/tensile ratio.
Rotor anti-corrosion coatings have become increasingly popular. We apply a Geomet RS200 coating on our GCX rotors, involving a zinc and aluminum-rich resin to all non-friction surfaces of the rotor. Depending on the specific OE requirement, we intentionally don’t apply coating 14
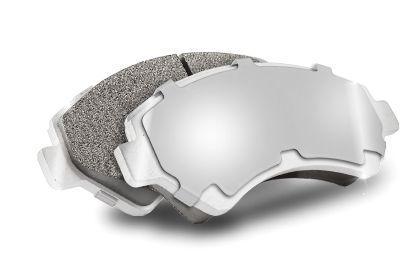
Backing plates are galvanized to prevent corrosion.
to the friction surfaces, as this may hinder pad break-in material transfer. An example of a good combination is our New 500 pad coating coupled with coated GCX rotors.
Brake Parts Inc The following comments were provided by Jerry Forystek , director friction product development, Brake Parts Inc LLC (BPI).
Friction material is moving toward copper free. Also, applications are going to a higher level coefficient of friction. The 2019-20 Chevy Silverado is a good example. This application contains a high friction ceramic material with a much smaller caliper/braking surface area. BPI continues to monitor the changes being made by the OE manufacturers with new formulas that are developed by our own research and development group.
Our biggest advancement here is finding ways to improve on corrosion resistance. The high corrosiveness of the salts and chemicals used on roads today is making it tough on all brakes. Continued improvements in corrosion capabilities of the backing plate assist with this problem.

COURTESY OF BRAKE PARTS INC

Diagonal slots and shims.
The following information was provided by Gary Mical, product manager - rotors and drums, Brake Parts Inc LLC.
Some key material items that we have noticed is more and more OEs are starting to use aluminum rotor hats on their performanceoriented cars. This leads to less unsprung weight and rotational mass, along with better heat dissipation near hub components. Carbon ceramics are another material that is being offered more frequently on high-end vehicles. Some advantages to this are higher thermal stability, improved wear resistance to allow for more aggressive pad compounds and corrosion resistance. Surface coatings have continued to be an important attribute in combating seasonal elements, increasing corrosion resistance while also improving braking wear resistance.
Another common trend that has developed is truck brakes are getting larger on fronts. Larger front rotor with a carry-up rear rotor may not change bias, but the front rotor is more capable for heavy towing. OE may be indicating that overall braking difference is made up by trailer brakes. We have continued to see a decline in drums in recent years. The rear braking systems are moving toward EPB and a caliper-based parking brake, instead of a parking drum.
The industry is seeing an increase in the use of rotor coatings to prevent rust. Some OEM rotors now feature aluminum hats to reduce weight and to increase thermal release.
Dann Ingebritson, senior trainer/technical service, Brake Parts Inc LLC.
Many calipers are aluminum to save weight, but they cannot hold up in harsh environments. This is why new calipers with no core needed is the future. We are seeing more high performance optional brake setups on cars and trucks. There are more multi-piston calipers now than ever. Also, many OE manufacturers are going away from mechanical parking brake calipers and using electronic parking brake calipers. This is reducing the complexity of the caliper itself, but making it much more difficult for non-dealer shops to work on the cars because of special scan tools needed.
On the subject of brake fluids, Brake Parts Inc’s Ingebritson noted that all new vehicles have at least two to three advanced braking systems such as ESC or AEB. These systems operate in milliseconds and rely on the quick operation of the total brake package. The system is only as good as the weakest link, which can be the brake fluid. Brake fluid with too much moisture will boil and have loss of pedal. Fluid that is old may have lost its ability to prevent corrosion causing component failure.
Brake fluids have not changed much in the past few years but fluid maintenance needs to be followed more closely.
COURTESY OF BRAKE PARTS INC
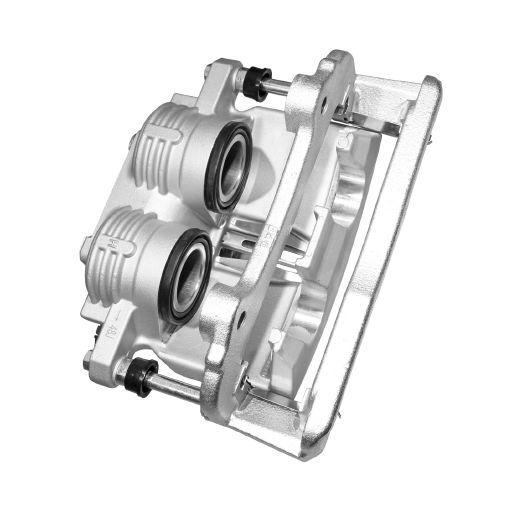
The OEMs are increasingly using multi-piston calipers, with some made of aluminum to reduce un-sprung weight. Since aluminum calipers are prone to corrosion, replacements without the need for core returns will likely be common.
ADVICS The following comments were provided by Greg Ladley, ADVICS manager of friction engineering.
In today’s market, the major complaints involve roughness, squeal noise, creep groan/ grunt, and appearance (re: corrosion), as refinements to occupant comfort and a noise-free environment seems to be the important factors for the average driver. In terms of friction formulation, we don’t use metallic/semi-met, opting for ceramic to create optimum friction between the pad and rotor.
There are two main types of friction, one being an adhesive style (stick and tear) and the other is abrasive style (machining). The adhesive style deposits a transfer layer/film onto the rotor during initial pad contact (burnish), creating a chemical relationship between the two surfaces, while the abrasive style cuts into the rotor much like a machining action.
The ADVICS method of blending the two friction types builds an optimal thickness and evenly distributed transfer layer onto the rotor surface improving lining/rotor life and reducing DTV (disc thickness variation) growth.
We also develop under-layers between our pad and the backing plate first and foremost to maximize bond integrity (shear strength), but more recently we have developed new underlayer technology designed to improve damping characteristics for better noise performance.
At ADVICS, we expose the backing plates to a special nitriding process which provides anti-corrosive properties and allows greater pad bonding integrity with the use of special adhesives. For very large pads, we also consider using our backing plate suppliers patented hook technology along with an adhesive. In addition to backing plate nitriding, we also use a high-heat powder coat for optimum corrosion protection, without compromising plate thickness.
Based on pad size, we employ slots in the pads... in some cases two slots. We try to avoid using diagonal slots, which can create a point wherein friction material volume may be compromised. In some cases, we employ multiple slots to address NVH (noise/vibration/harshness) issues where the specific application requires this.
The use of chamfers at leading and trailing edges are based on the specific application, in order to resolve frequency-based noises. Chamfers are also used in some cases because of caliper design to eliminate unwanted pad drag.
There are different levels of frictional property requirements regarding front and rear brake locations. Naturally, the front brakes are responsible for the majority of braking performance. The front brakes are exposed to higher duty cycles and higher temperatures. The rear brakes experience less braking power, but are responsible for static performance (re: parking brake use), so the pad size and formulations are tailored to suit these different requirements. However, in SUV and truck applications, these may experience higher rear loads due to cargo and towing applications. The duty cycles differences require varying genres of friction materials.
Here in the U.S. another consumer concern involves brake dust buildup from an appearance standpoint, so friction material must be formulated to minimize this. By contrast, historically, in Europe, consumers are much more concerned with stopping power. More recently Europe has concerns about brake dust and the contents within regarding potential health risks.
On the subject of rotors, from an OEM perspective we see a push for changes in design

Based on pad size, pad slots may be employed. ADVICS tries to avoid using diagonal slots, which can create a point wherein friction material volume may be compromised. In some cases, multiple slots are used to address NVH noise/vibration/harshness issues where the specific application requires this. Chamfers are featured where needed to resolve frequency-based noises. Chamfers are also used in some cases because of caliper design to eliminate unwanted pad drag.
and materials in terms of resistance to corrosion. Friction suppliers will need to take a fresh look at pad-to-rotor relationship, developing pad materials to work with FNC (ferritic nitro carburizing) rotors which are surface-impregnated with nitrogen and carbon, which makes the rotor harder, which could require a change in friction logic.
As far as rotor drilling or slotting is concerned, we tend to follow the OEM design. If the OEM design does not involve holes or slots, we don’t add these features. Where these features are required, primarily for performance applications, stopping power is the primary goal, while noise or roughness concerns are not a priority.
Wagner Brake The following comments were provided by Nick Thomas, friction product manager, Wagner Brake.
In the past, “one pad covers all” was the norm in terms of materials. Today, this is no longer true.
Brake pads are now designed, from scratch, for vehicle-specific applications. One of the trends today is to offer pads that are specifically designed for light trucks, SUVs and CUVs, given the growing popularity of this market segment, and another pad technology for passenger cars.
Customers want, and expect, brakes that not 18
only provide good stopping power, but offer quiet operation.
Wagner Brake takes a no-compromise approach in this regard. Given the mandate to remove copper content, special pad formulations have been developed, much akin to a recipe for cake mix, to create a balance of organic materials and resins to provide both consistent frictional stopping power and to provide adequate heat transfer. Ceramic materials have been developed that offer longer life and quieter operation.

Where required based on specific vehicle applications, unique pad slot designs are utilized that assist in removing debris from the rotor surface in a self-cleaning manner. This may involve straight single or multiple or S-curved slots.
In terms of pad-to-backing plate retention, Wagner employs a mechanical retention approach, with raised-edge teeth on the backing plate that secure the friction material during pressurized molding, eliminating the need for chemical adhesives. In order to prevent backing plate corrosion, plates are galvanized, preventing corrosion where the backing plate rubs on the caliper.
While the industry has seen an influx of lower-priced and lower-quality rotors, Wagner Brake insists on offering rotors with premium materials, and design custom vaning to improve cooling for specific applications to enhance airflow and venting. In terms of corrosion prevention, Wagner Brake employs an electronically bonded coating termed E-Shield, to all non-contact rotor surfaces, avoiding coating the friction
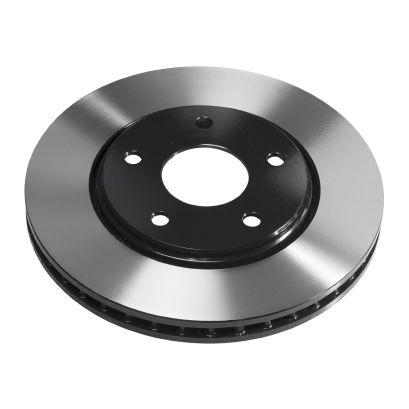
Wagner Brakes’ E-Shield rotor.
surfaces which could gum-up the friction interface between the pad and rotor.
On the subject of pad wear indicators, while the majority of domestic vehicle applications continue to feature mechanical wear indicators, and electronic wear sensors are predominantly used on European vehicle applications, we’re seeing a gradual influx of the electronic sensor systems that apply to domestic vehicles.
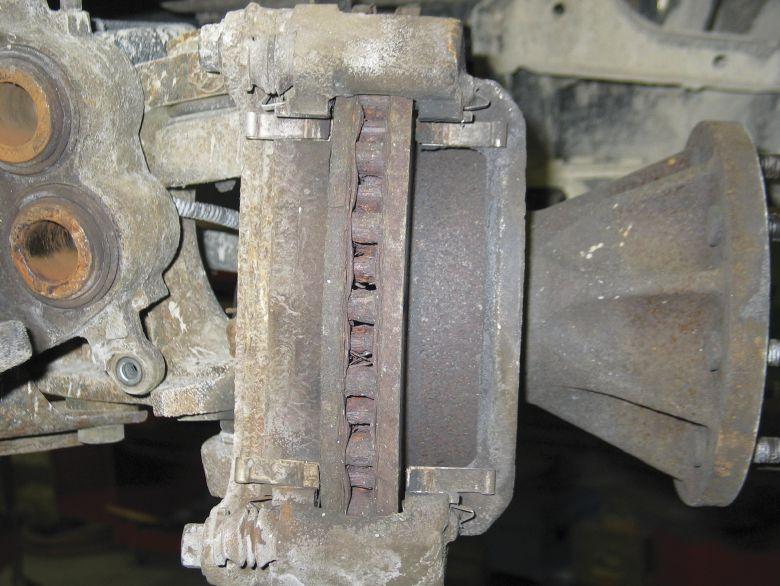

Examples of Akebono pads left to right ProAct, Euro and Performance. Euro pads are equipped with electronic pad wear sensors where applicable.
Akebono Brake Corp. The following comments were provided by Edward Gerhardt, Akebono brake marketing and data services manager.
With the requirement to eliminate copper from brake friction material, there is no simple substitute for copper. This requires creating proprietary compound formulas that provide required heat resistance and durability. Ceramic pad compounds today provide the same benefits of traditional ceramic pads in terms of durability, quietness, heat dissipation and reduced rotor abrasion without using high levels of copper or abrasive ferrous metals.
There are two ways to generate friction: through adhesion or abrasion. Akebono ceramic friction materials work through adhesion by laying down a transfer film onto the rotor surface, with friction achieved by shearing the transfer film. This provides long wear for both the pad and rotor, and very low dust. By contrast, the abrasive method involves dislodging small particles from the rotor surface by using larger and harder abrasive components in the pad formulation. Since these components wear, they need to be constantly renewed. Combined with rotor wear, this generates large amounts of dust.
On the subject of pad backing plates (pressure plates), Akebono applies a phosphate treatment to the plates, which helps to improve the bonding between the friction material and the plates.
Brake fluid notes Brake fluid type and condition is critical to brake system operation. In general, brake fluid should be changed every two years due to ambient air moisture entering the system (as glycol brake fluid is hygroscopic and absorbs moisture, thus lowering the fluid’s boiling point). Below is an overview of the dry and wet boiling point minimums for various fluid grades.
DOT 3 4 5 5.1 DRY BOILING POINT 401 degrees F 446 degrees F 500 degrees F 518 degrees F WET BOILING POINT 284 degrees F 316 degrees F 356 degrees F 374 degrees F
(The above figures represent a minimum standard. Depending on the brand and formulation, some fluids offer higher boiling points.)
Do not confuse DOT 5 with DOT 5.1 fluid. DOT 5 is silicone-based, and is not compatible with glycol fluids. While DOT 3, 4 and 5.1 fluids are hygroscopic (glycol based and absorbs atmospheric moisture), DOT 5 is silicone based and is hydrophobic (it does not absorb moisture).
Fluid life As mentioned, glycol-based brake fluids absorb moisture. Even in a properly sealed brake system, atmospheric pressure eventually allows airborne moisture to enter the system. Generally speaking, moisture contaminates glycol brake fluid at a rate of about 2% to 3% per year. Any glycol-based brake fluid, since it will absorb atmospheric pressure moisture over time, should be changed at least every two years in order to maintain the proper level of its boiling point and resistance to compression. Any container of glycol fluid that has been opened, and then stored even with the cap tightened, should be discarded after 12 months. ■
COOLING SYSTEM
Checking belts, pulleys, tensioners and pumps By Edwin Hazzard
WWhen a vehicle rolls into your service bay for an inspection or any other problem, it’s a good idea to make sure that the vehicle gets a good visual check as well. You want to take care of your customers COURTESY OF NAPA AUTOTECH and give them a good sense of peace of mind so they know you are looking out for their best interests. That’s how you generate a repeat customer. There are many systems on a vehicle that Figure 1: Exhaust manifold, 2013 Ford Focus. should be inspected besides safety critical areas like brakes, tires, etc. The engine has to be oper- still need to be maintained and the mainteating correctly, fluid levels must be maintained nance needed for these systems is just as critiproperly, and all other components need to be cal as before. working as designed. As everyone knows, the heart of a cooling One of the more important systems is the system is the coolant that is used to maintain cooling system. If the cooling system isn’t keep- engine temperature. The type of antifreeze used ing the engine cool then an overheating scenar- is just as important as the condition of the anio will occur and that could get your customer tifreeze. Antifreeze doesn’t last forever and it overheated as well. breaks down just like engine oil does. Cooling systems have become more and This article isn’t going to get into the specifmore complex as modern technology seems to ics of which antifreeze to use or how to test it. creep in with today’s new vehicle technologies. We can save that for a future article. The point It used to be years ago that you had one type I’m trying to make is following the factory recof antifreeze, a water pump, one or maybe two ommended guidelines and specifications that belts, one thermostat, heater core and a radia- your customer’s particular vehicle calls for is tor. Gone are the simpler times. Hello to multi- the best rule of practice. ple cooling systems, an increase of components and the addition of electronics. Inspection Today’s modern cooling systems potentially When performing a cooling system inspecfeature multiple thermostats and may include tion, the first thing that has to be done is a close electronic thermostats to boot! Would you ever visual inspection. Look for any sign of a leak consider an exhaust manifold being a coolant whether it’s an external leak or an internal one. system part? For external leaks, inspect the hoses for A 2013 Ford Focus ST Eco Boost engine has splits around where the hose clamps are, any an integrated exhaust manifold incorporated rubbing or chafing against another component into the cylinder head (see Figure 1). This is an or obstacle (see Figure 2). Pay close attention to example of why it’s more important to stay on the way a coolant hose is routed. It’s possible top of technology. that a hose was installed incorrectly or maybe Today’s vehicles are more efficient in keep- it was an incorrect hose replacement to begin ing the engine at the correct temperature than with. the ones that we’ve seen in the past, but they With the engine cold, give the hose a couple 24
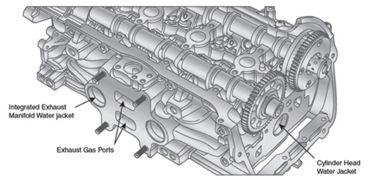