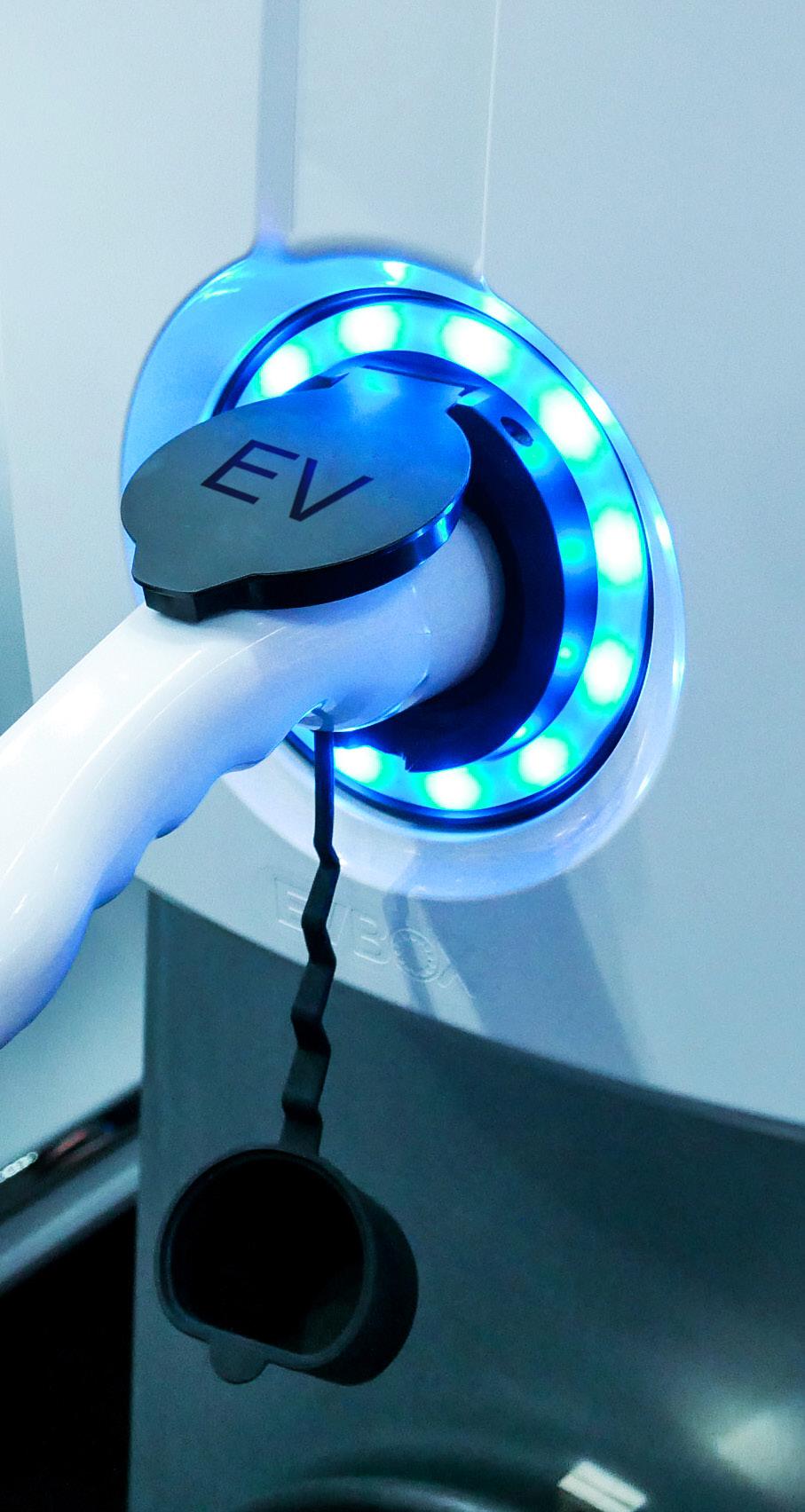
5 minute read
In the driver’s seat
process of the different battery components — improving efficiency, extending their lifespan, and preventing electrical shorts and fire risk.
Structural adhesives provide additional support and protection of battery cells within a battery pack, protecting them from mechanical shock and vibration while the vehicle is in motion. They also ensure the electrically charged cells do not touch, which could cause a fire and significant damage to the vehicle.
“Inside the battery pack, you need electrical isolation, thermal management, and structural strength — all of these things are performed by adhesives,” says Dr. Pradyumna Goli, eMobility Business Development Manager at Henkel.
Sealants also play an equally vital role in ensuring a battery’s safety by completely sealing it from environmental debris or moisture, while also preventing fumes from spreading in the event of a thermal runaway.
Tons of benefits
The construction of the body and interior of a modern vehicle is completely reliant on adhesives and sealants.
Lightweighting is a key advantage over other bonding methods such as mechanical fasteners. A lighter vehicle improves efficiency and extends the life of the engine — whether electric or a traditional internal combustion engine. This is particularly pronounced in EVs though as they prove much heavier than traditional cars, says Goli.
“An electric car is at least three times heavier than the traditional car because of all the metal going into the battery pack,” he says. “Adhesives really help balance that weight out and improve the car’s efficiency.”
Structural adhesives tend to be preferred to welding when constructing the body of the car given their ability to bond dissimilar materials — something that cannot be achieved by any other method.
Separately, adhesive automation through robot dispensing helps speed up production, an advantage valued by any mass car manufacturer.
Adhesives are also a much safer alternative than welding, especially in an electronically sensitive environment.
Noise, vibration and harshness characteristics are also an important consideration. In a conventional vehicle, they limit engine noise entering the passenger compartment. And even though EVs lack such noisy engines, drivers are still subject to excessive road and wind noise. Manufacturers are therefore looking at various ways to block that noise, which presents new opportunities for the adhesive and sealant market.
“Adhesives and sealants will remain key components of modern vehicles as you just can’t beat the tons of benefits they bring, whether they are used together with other joining methods or alone,” adds Benevento.
Gradual acceleration
Adhesives and sealants will undoubtfully be a key contributor to the projected growth of EV consumption in the years to come. There are, however, some doubts as to the speed at which that growth will materialize.
Just under 6% of new U.S. cars sold in 2022 were electric, according to public market data. The number is relatively low compared to the ambitious 2030 target, although it still represents a steep 65% year-on-year improvement.
This positive trend contrasted to a decline in the overall year-on-year number of cars bought in the U.S. in 2022. It also came at a time when the auto sector has been tackling inflation, a stretched labor market, and a supply chain crisis — all of which contributed to a shortage of new vehicles.
The EV sector has been somewhat shielded from these challenges. With electric cars still considered a premium product, their demand was not high enough to be significantly impacted by these logistical challenges. However, the sector has still had its own set of obstacles to overcome.
Among these is their high price point, which keep them at the top end of the market.
“The perception that future demand will be there is driving the specification work around EVs, but for that demand to really materialize cost reduction is necessary,” says James Swope, Chief Commercial Officer at ChemQuest.
While there are a number of tax credits and rebates aimed at U.S. households, there is skepticism over how quickly and easily they will turn to electric cars.
“The key thing is, are consumers in the U.S. ready for EVs? Making the change from early adopter to mass market is typically not that smooth a transition,” says Benevento.
Goli is much more optimistic about the speed at which EVs will penetrate the U.S. market.
“I can safely say electric cars should be a dominant player on the road compared to traditional cars in the next 10 years,” he says, adding that the overall perception of electric cars as a premium product is somewhat misleading as they vary considerably in their model and price range.
“When talking about EVs, the base model to look at is a semi premium model [Tesla Model 3]. We should get out of that mindset and see other EVs like Leaf, Bolt, ID4, etc. that also are available in the market,” he notes.
Limited infrastructure
The current lack of sufficient EV charging stations is another major factor to consider when looking at near future electric car consumption in the U.S.
While there are government rebates aimed at supporting charging network manufacturers, there is some doubt as to how quickly these stations could be up and running.
“My personal opinion is that the headwinds are still quite strong for EVs. There is little charging infrastructure ready to support the projected Battery Electric Vehicles (BEV) growth,” says Swope, adding that current infrastructure is better equipped to support alternatives, such as hybrid electric vehicles (HEVs) and Plug-in Hybrid Electric Vehicles (PHEVs).
Other technologies such as hydrogen generated electric (fuel cell) and hydrogen powered internal combustion engines are still nascent and yet to be fully commercialized, but have enormous potential for the future. Again, adhesive and sealants will be required to enable their deployment.
Suitable infrastructure is particularly important in the U.S. where people rely heavily on long-distance driving.
Benevento believes insufficient charging infrastructure is likely to keep the number of new EVs on the road low despite the fuel economy standards introduced by the U.S. government.
“I think there is still going to be a significant bridge, where in order to meet the fuel economy standards more people are going to go for a hybrid, which is much less expensive than a long-range EV,” he says.
Most of the initial EV offerings have been very expensive due, in part, to the long range capabilities and the batteries they require.
Goli, however, remains doubtful about the future of hybrids as maintenance costs are comparatively high owing to their dual engine architecture.
“If you look at the total ownership cost for five years, EVs will be cheaper than the hybrids. Hybrids are running out of their course and in the next few years we will be seeing either traditional or pure electric cars on the road,” he says, adding that all major U.S. manufacturers are now moving away from hybrid production.
While there is still uncertainty as to how and when consumers will embrace EVs, the market will inevitably enjoy significant growth in the coming years. Adhesive and sealant manufacturers will play an increasingly important role on that journey.
Acouple of years of strong growth in the U.S. residential construction sector looks set to reverse as rising inflation and high interest rates have put a dampener on the housing market, which will undoubtedly impact the adhesives and sealants business.
“We’ve just come off the highest growth in the value of construction that we’ve seen in years within U.S. industry, primarily driven by the residential segment,” says Chris Fisher, Managing Principal at global consulting and M&A company Ducker Carlisle, where he leads the firm’s building and construction industry practice.
“COVID-19 spurred significant growth in residential construction and remodeling, although the non-residential sector did not enjoy the same opportunity. Now we’ve entered into a period of high interest rates that will slow all new construction and major projects, equating to a more challenging time for the construction industry after a few very solid years,” he says.
According to Ducker Carlisle estimates, spending on new homes grew at an average annual rate of 13-15% for the period 2019 to 2021, and residential remodeling expenditures also grew at a near record 9-11%.
And given the increased building activity and economic environment, it is likely that most adhesives and sealants manufacturers have enjoyed some pricing power and been able to achieve higher revenues with lower volumes. In the long run, construction practices continue to evolve which support using more adhesive and sealant content, particularly with panelized construction — and this looks set to continue.
Looking ahead through 2027, Ducker Carlisle is predicting slower growth for new residential construction at an annual average